This article introduces the paper "A computer-aided system for multi-gate gating-system design for die-casting dies" presented at the The International Journal of Advanced Manufacturing Technology
1. Overview:
- Title: A computer-aided system for multi-gate gating-system design for die-casting dies
- Author: Ranjit Singh, Jatinder Madan
- Publication Year: 2018
- Publishing Journal/Academic Society: The International Journal of Advanced Manufacturing Technology
- Keywords: Die-casting, Die-design, Process parameters, Gating-system design, Multi-gates
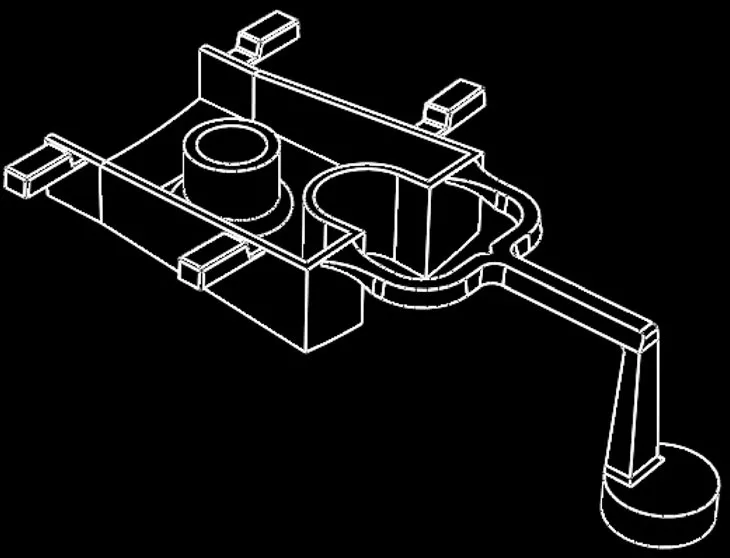
2. Research Background:
The design of gating-systems in die casting is traditionally a complex and time-intensive task heavily reliant on the expertise of die-casting engineers. Current industrial practices necessitate a deep understanding of industry best practices, process physics, and extensive database consultation. This manual approach is described as "very time consuming and cumbersome exercise." The die-casting industry recognizes the need for systems that can alleviate the manual burden on experts, particularly for designing effective gating systems.
Existing computer-aided systems for die-casting die design often fall short in automating the entire gating system design process. Many commercially available CAD systems require significant manual input of process parameters and gating system specifications. Furthermore, these systems often lack the sophistication to handle the complexities of multi-gate gating-system design, which is increasingly necessary for intricate die-casting parts.
This research is therefore motivated by the necessity to develop a computer-aided system capable of designing multi-gate gating systems, thereby reducing the reliance on manual, expert-driven processes and improving design efficiency in the die-casting industry.
3. Research Purpose and Research Questions:
The primary research purpose is to develop and implement a computer-aided system specifically for the design of multi-gate gating systems in die-casting dies.
The key research questions addressed by this study include:
- How can a computer-aided system automate the determination of critical die-casting process parameters?
- How can such a system facilitate the efficient design of gating system parameters, particularly for multi-gate configurations?
- How can a feature library be utilized to automatically generate CAD models of gating systems based on system-determined parameters?
While not explicitly stated as hypotheses, the research operates under the implicit research hypotheses that:
- A computer-aided system, incorporating industry best practices and a feature library, can effectively automate significant portions of the multi-gate gating system design process.
- Such a system can reduce the time and effort required by die-casting experts while maintaining design quality and adherence to industry standards.
4. Research Methodology:
This research employs a system development approach, focusing on the creation and implementation of a computer-aided design tool. The system's design is based on a structured methodology encompassing three key modules:
- Module 1: Determination of Die-Casting Process Parameters: This module automates the determination of parameters such as "cavity fill time, gate velocity, and selection of die-casting machine automatically from the input information."
- Module 2: Computer-Aided Determination of Gating System Parameters: This module calculates gating system parameters like "gate thickness, gate length, runner length etc., by using input information."
- Module 3: CAD Model Generation: This module utilizes a "feature library" of gating system components to "generate CAD models of the gating system by updating gating system features from feature library" based on the parameters from Module 2.
Data Collection Method: The system leverages "part, process, machine, and material information" as input. It incorporates industry best practices and empirical formulae, such as those outlined in Ward's gating system manual [24], for parameter determination. A feature library of gating system components is also utilized for CAD model generation.
Analysis Method: The system was implemented using MATLAB. The validation of the system's effectiveness was conducted by "testing on example die-casting parts." The results were evaluated by comparing them against "industry practice," indicating a qualitative assessment of the system's output.
Research Subjects and Scope: The research focuses on developing a computer-aided system specifically for "multi-gate gating system design for die-casting die." The scope is limited to the design and CAD model generation of the gating system, with an emphasis on automating parameter determination and utilizing a feature library. "Flow simulation studies are not in the scope of the present work."
5. Main Research Results:
The primary outcome of this research is the development of a functional computer-aided system for multi-gate gating-system design. The system operates in three modules, successfully automating key aspects of the design process:
- Automated Process Parameter Determination: The first module effectively determines die-casting process parameters, aiding in "determination of cavity fill time, gate velocity, and selection of die-casting machine automatically from the input information."
- Computer-Aided Gating System Parameter Calculation: The second module successfully calculates gating system parameters, enabling "computer-aided determination of gating system parameters like gate thickness, gate length, runner length etc., by using input information."
- Automated CAD Model Generation: The third module demonstrates the capability to "generate CAD models of the gating system by updating gating system features from feature library" using the parameters derived in the previous modules.
Statistical/Qualitative Analysis Results: The paper states, "The system has been tested on example die-casting parts, and the results obtained from the system are as per industry practice." This indicates a qualitative validation, suggesting that the system's output aligns with established industry norms and expert expectations.
Data Interpretation: The results demonstrate the feasibility and effectiveness of the proposed computer-aided system for multi-gate gating-system design. The system successfully integrates process parameter determination, gating system design, and CAD model generation, offering a streamlined approach to a traditionally complex task. The qualitative validation against industry practice suggests the system's practical applicability and potential to enhance efficiency in die-casting die design.
Figure Name List:
- Fig. 1 Illustration of important terms used in the gating-system
- Fig. 2 An instance of multi gate for a part having identifiable segments and gate locations
- Fig. 3 An instance of multi-gate for a part having no identifiable segments
- Fig. 4 A schematic of the distributed flow pattern
- Fig. 5 A schematic of the directed flow pattern
- Fig. 6 A schematic of the shortest path of metal flow
- Fig. 7 Dimensional parameters of a chisel gate (Johal et al. [26])
- Fig. 8 Illustration of the features available in the gating-system feature library
- Fig. 9 Architecture of the system for computer-aided gating-system design
- Fig. 10 Information flow diagram for the computer-aided system for gating system design
- Fig. 11 A snapshot of engine cover case study die-cast part
- Fig. 12 A snapshot of the assembly of the gating-system and cavity of the engine cover case study
- Fig. 13 A snapshot of crank case cover case study die-cast part
- Fig. 14 A snapshot of case study die-casting part with the gating-system
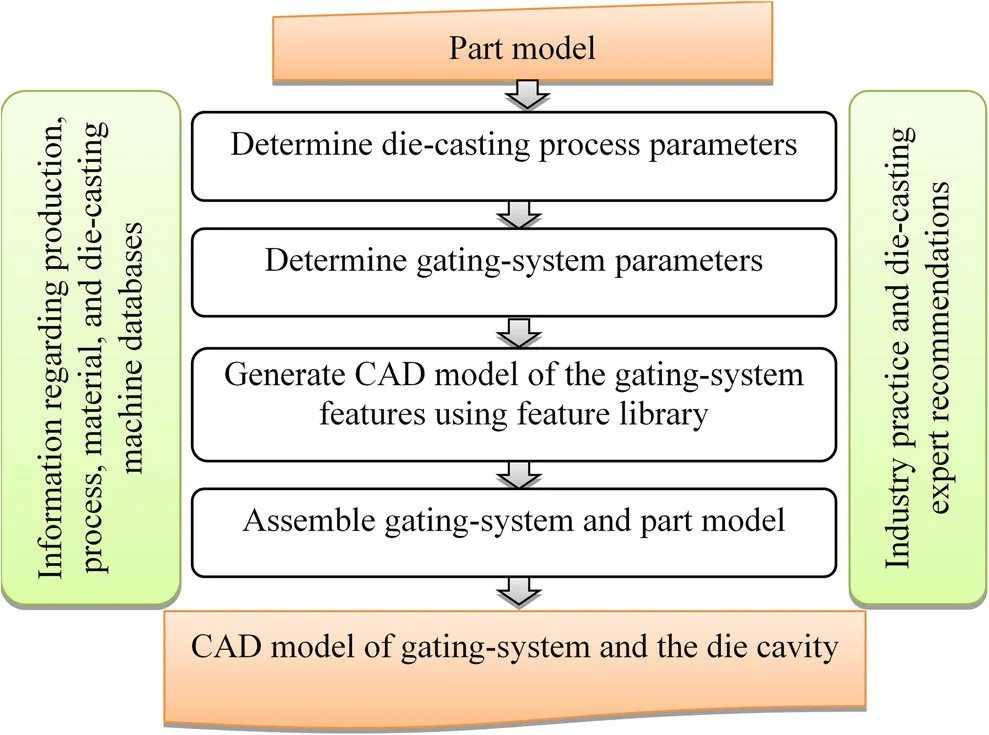
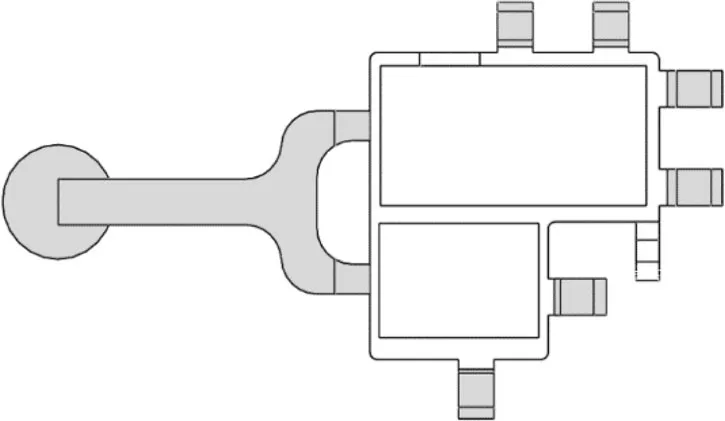
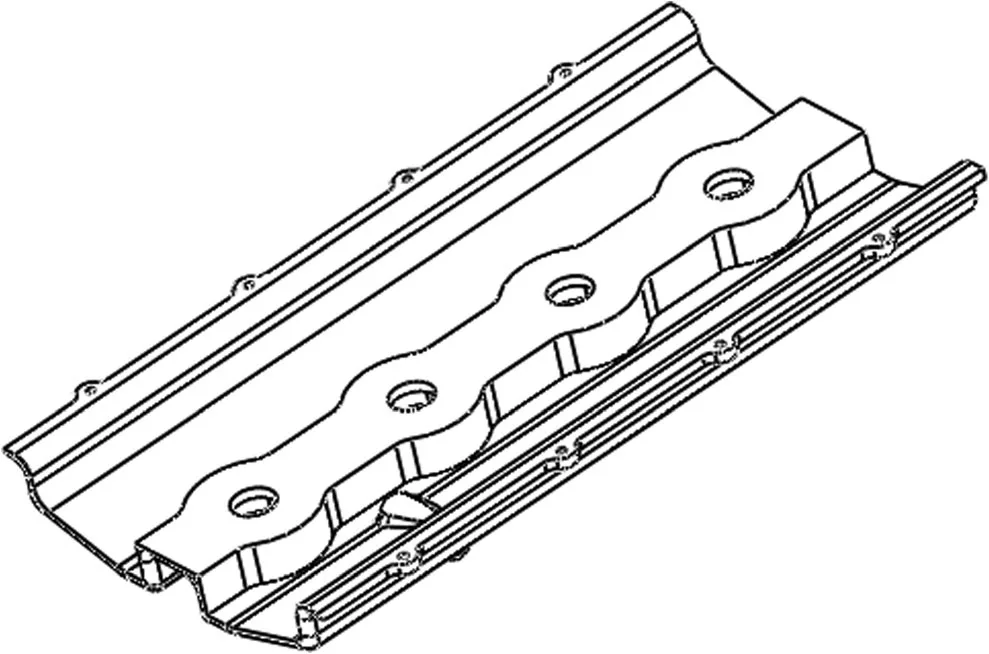
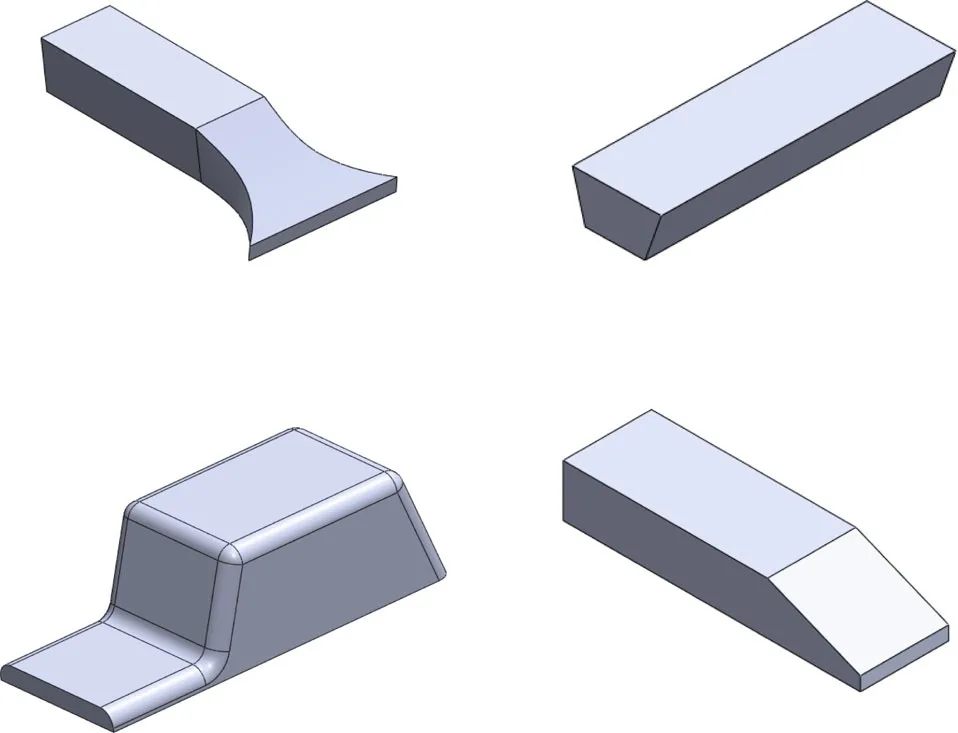
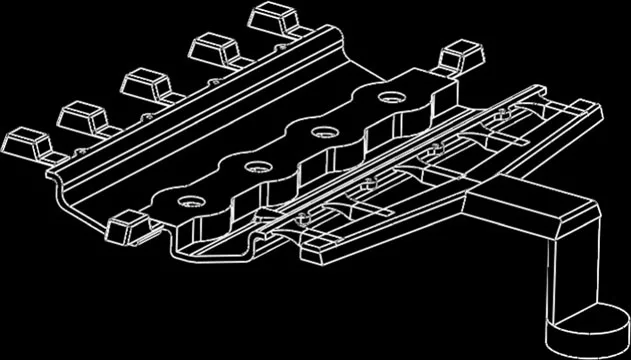
![Fig. 7 Dimensional parameters of a chisel gate (Johal et al. [26])](https://castman.co.kr/wp-content/uploads/image_6-2.webp)
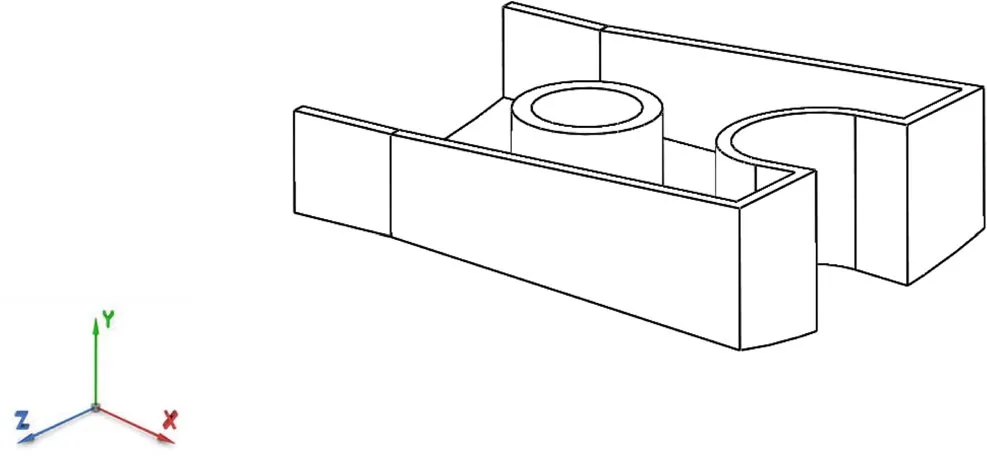
6. Conclusion and Discussion:
Summary of Main Results: This research successfully developed a computer-aided system for multi-gate gating-system design in die casting. The system comprises three modules that automate the determination of process parameters, gating system parameters, and the generation of CAD models using a feature library. Testing on example die-casting parts showed that the system's results are consistent with industry practices.
Academic Significance of the Research: This work contributes to the field by addressing the gap in automated design systems for multi-gate gating systems. It presents a systematic approach that integrates industry best practices and automates crucial parameter determination and CAD modeling stages.
Practical Implications: The developed system offers significant practical benefits for the die-casting industry. It has the potential to reduce the workload on die-casting engineers, shorten design lead times, and improve the consistency of gating system designs, particularly for complex parts requiring multi-gates. The system's ability to handle multi-gate designs is highlighted as a key advantage for industrial applications.
Limitations of the Research: The scope of the research is limited to the design and CAD model generation of the gating system. "Thermal aspects and process physics are not included explicitly in this paper," although the authors suggest that "industry best practices used in the paper implicitly take care of the process physics." Furthermore, certain user inputs are still required, such as the selection of gate type, number of gates, and part segmentation. Flow simulation is also noted as being outside the current scope.
7. Future Follow-up Research:
The authors identify several directions for future follow-up research to enhance the system's capabilities and address its limitations:
- Integration with CAD/CAM Software: Developing the system as an add-on application for existing CAD/CAM software to streamline the design workflow and reduce lead times.
- Incorporation of Flow Visualization: Integrating flow visualization capabilities to further aid in gate placement and design optimization, potentially reducing reliance on user experience for flow pattern prediction.
- Expansion to Include Thermal and Process Simulation: Widening the system's scope to explicitly incorporate thermal aspects and process simulation to provide a more comprehensive design solution.
- Automation of User-Dependent Steps: Further automation of steps currently requiring user input, such as gate type and number selection, and part segmentation, to minimize user intervention and enhance system autonomy.
Areas Requiring Further Exploration: Future research should focus on deeper integration of process physics, further automation of user-dependent design choices, and broader validation of the system across a wider range of die-casting parts and industrial settings.
8. References:
[List of references as provided in the original paper, numbered 1-42]
9. Copyright:
This material is [Ranjit Singh and Jatinder Madan]'s paper: Based on [A computer-aided system for multi-gate gating-system design for die-casting dies].
Paper Source: [https://doi.org/10.1007/s00170-018-2980-z]
This material was summarized based on the above paper, and unauthorized use for commercial purposes is prohibited.
Copyright © 2025 CASTMAN. All rights reserved.