This introduction paper is based on the paper "A comprehensive investigation on various welding facets for FSW of advanced structural AMC" published by "Research Square".


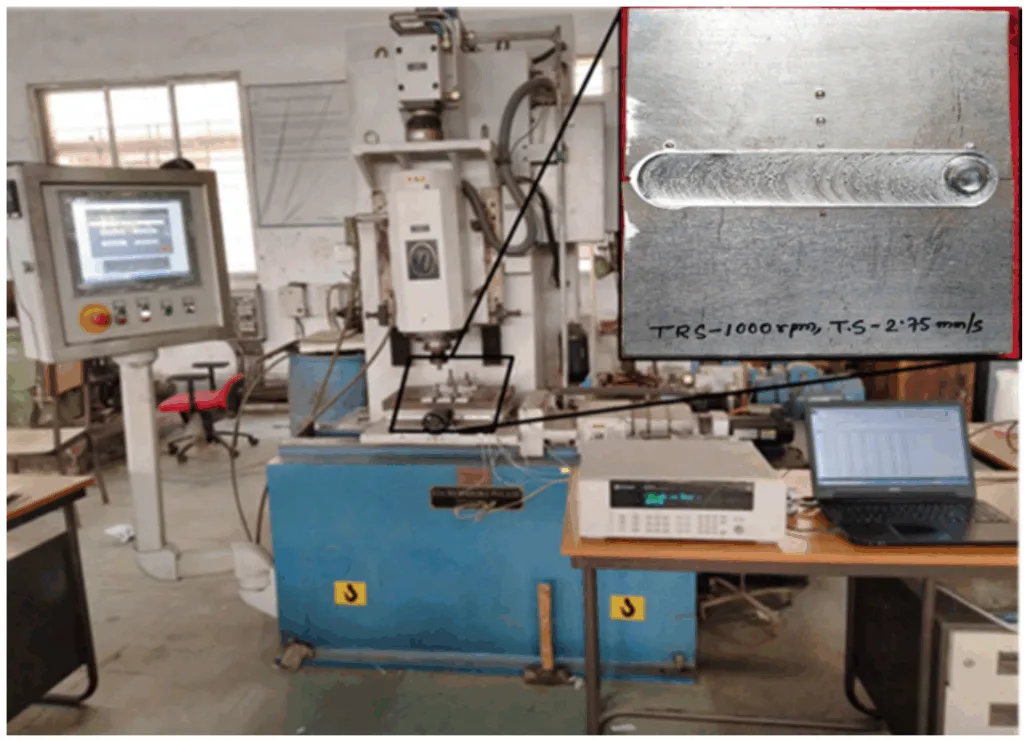
1. Overview:
- Title: A comprehensive investigation on various welding facets for FSW of advanced structural AMC
- Author: Uttam Acharya, Smrity Choudhury, Durjyodhan Sethi, Esther Akinlabi, Kuldeep K Saxena, Barnik Saha Roy
- Year of publication: 2024
- Journal/academic society of publication: Research Square (Preprint)
- Keywords: Aluminium matrix composite, friction stir welding, force-torque distribution, mechanical property, microstructure, thermal behaviour
2. Abstract:
The study comprehensively explores various welding facets for FSW of advanced structural AMC (AA6092/17.5 SiCp-T6) by varying the Tool Rotational Speed (TRS). Thermal variations, force-torque distribution, structural evolution, and joint mechanical characteristics were evaluated. At 1000 rpm, welding temperature increases along the welding direction, contrasting with other TRS. The cooling rate escalates as welding progresses. The temperature gap between the Advancing Side (AS) and the Retreating Side (RS) widens with higher TRS. Increasing TRS leads to decreased spindle torque and Z-force, with X-force fluctuations evident at lower TRS. Additionally, the TRP exhibits a direct linear relationship with the energy input during the welding process. Microstructural analysis reveals diverse SiC particle aggregation in the Nugget Zone (NZ) across all the TRS conditions. Notably, at 1500 rpm, an onion ring width of 80 µm is observed. At 1750 rpm, iron particles indicating tool wear and an Al2O3 mud-cake-like formation is traced out. Furthermore, as TRS rises to 1500 rpm, there is a decrease in the particle size, succeeded by an increase, aligning with variations in the grain size. Welds display lower hardness than the BM, following a 'W' shape profile with the AS-HAZ region consistently showing the lowest hardness across all conditions. Hardness peaks at 1500 rpm, then decreases. The Tensile samples mostly fracture outside the weld zone, except at 1700 rpm. UTS values range from 308 MPa to 358 MPa, with joint efficiency peaking at 87% for 1500 rpm before decreasing to 74%. Welding at 1500 rpm exhibits greater elongation compared to the Base Metal, with fractographic analysis indicating predominantly ductile failure, except at 1750 rpm, displaying a mixed mode of failure.
3. Introduction:
FSW has become increasingly important in recent years as an innovative welding process that operates without melting the materials, showing significant potential across various industries. Originating in 1991 through pioneering work by TWI in the United Kingdom, FSW is an eco-friendly method that achieves solid-state joining. This process relies on a non-consumable rotating tool creating frictional heat while interacting with the workpiece, allowing material flow through the tool stirring action and induced plastic deformation. The constant pursuit of strong yet lightweight materials in the aerospace industry has led to a deep exploration of innovative composite materials for structural components. Aluminium Matrix Composites (AMCs) reinforced with Silicon Carbide particles (SiCp) have garnered considerable attention due to their remarkable blend of lightweight properties and enhanced mechanical characteristics.
4. Summary of the study:
Background of the research topic:
The aerospace industry's constant pursuit of strong yet lightweight materials has led to deep exploration of innovative composite materials for structural components. Aluminium Matrix Composites (AMCs) reinforced with Silicon Carbide particles (SiCp) have garnered considerable attention due to their remarkable blend of lightweight properties and enhanced mechanical characteristics. However, the primary challenge in adopting AMCs within the aviation sector lies in the thermal-related issues associated with traditional welding processes for such materials.
Status of previous research:
While some fragmented studies have highlighted diverse findings across different directions, indicating the promising potential of FSW in joining advanced next-generation materials, a significant research gap remains. Specifically, there is a lack of a systematic approach to comprehensively investigate various welding facets (thermal effects, torque and force dynamics, critical structural examinations, and mechanical properties) and their interrelationships in the context of the high-strength aerospace-grade AA6092/17.5 SiCp-T6 AMC.
Purpose of the study:
The primary objective of this study is to conduct a thorough investigation into the thermal fluctuations, force-torque distribution, structural changes, and mechanical properties affecting the joining process of the advanced structural high-strength aerospace-grade AA6092/17.5 SiCp-T6 AMC using FSW with varied TRS. This systematic approach aims to provide a comprehensive reference point for students, researchers, and industry practitioners, offering insights into the complexities of welding such crucial structural materials.
Core study:
The study conducted FSW on 6 mm thick AA6069/17.5 SiCp-T6 AMC plates arranged in a butt configuration, perpendicular to the rolling direction. The welding process involved sections of 80 mm in length, with variations in the TRS set at 1000, 1250, 1500, and 1750 rpm, while maintaining TTS and TTA constant at 2.75 mm/s and 2°, respectively. Comprehensive investigations were conducted on thermal profiles, force-torque analysis, microstructural examination, and mechanical properties evaluation.
5. Research Methodology
Research Design:
The study employed a comprehensive experimental approach using FSW on AA6092/17.5 SiCp-T6 AMC plates with systematic variation of Tool Rotational Speed (TRS) while keeping other parameters constant. A 3-ton, force-controlled FSW equipment from ETA Technologies was used with a simple tapered pin profile tool made of 56 HRC H13 tool steel.
Data Collection and Analysis Methods:
Thermal data was collected using K-type chromel-alumal thermocouples placed at specific locations. Force and torque measurements were conducted using strain gauge-based load cells. Microstructural analysis was performed using light optical microscopy and scanning electron microscopy. Mechanical testing included Vickers microhardness testing and tensile testing following ASTM standards.
Research Topics and Scope:
The research scope included thermal profile analysis, spindle torque and force analysis, microstructural examination including grain size analysis, hardness distribution assessment, tensile property evaluation, and fractographic analysis across different TRS conditions (1000, 1250, 1500, and 1750 rpm).
6. Key Results:
Key Results:
At lower TRS (1000 rpm), temperature rises as welding proceeds, while higher TRS shows opposite trend. Cooling rate increases at various points along welding direction. AS exhibits higher temperature compared to RS, with temperature difference widening as overall temperature increases. Increasing TRS leads to notable reductions in spindle torque and Z-force. Microstructural analysis reveals dense aggregation of SiC particles in the Nugget Zone across all TRS conditions. At 1500 rpm, onion ring width measures approximately 80 µm. Tool wear evidence and Al2O3 formation observed at 1750 rpm. Particle size decreases up to 1500 rpm then increases. Hardness exhibits 'W' shape profile with lowest values in AS-HAZ region. Tensile samples fracture outside weld zone except at 1750 rpm. Joint efficiency peaks at 87% for 1500 rpm.
Figure Name List:
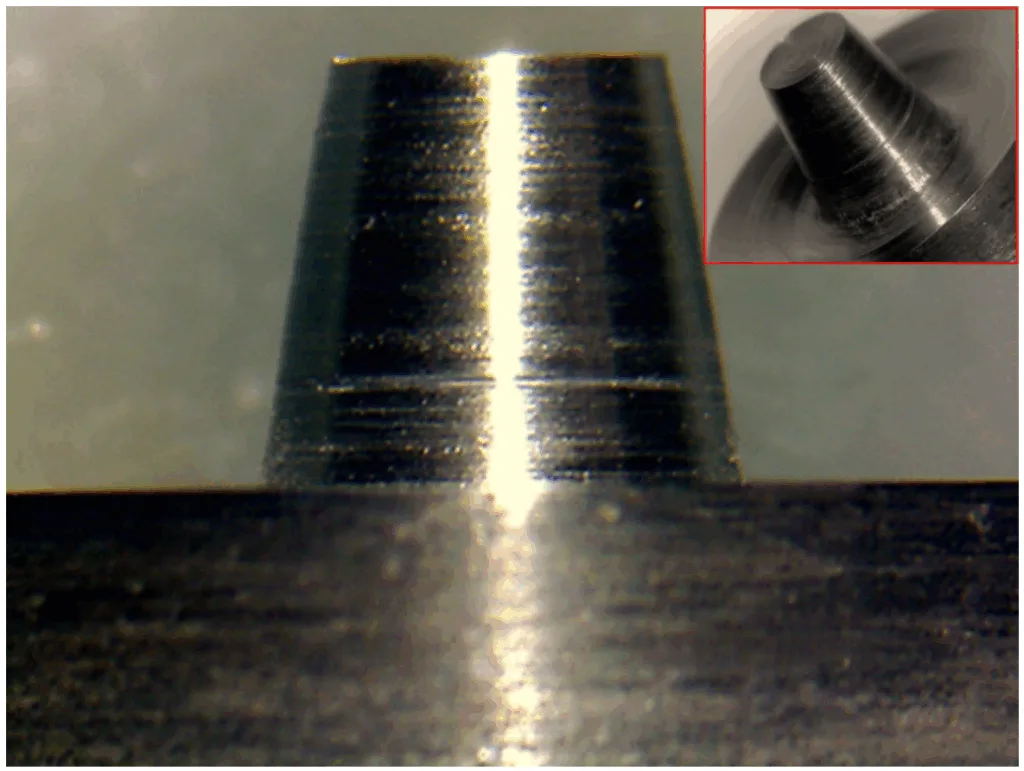
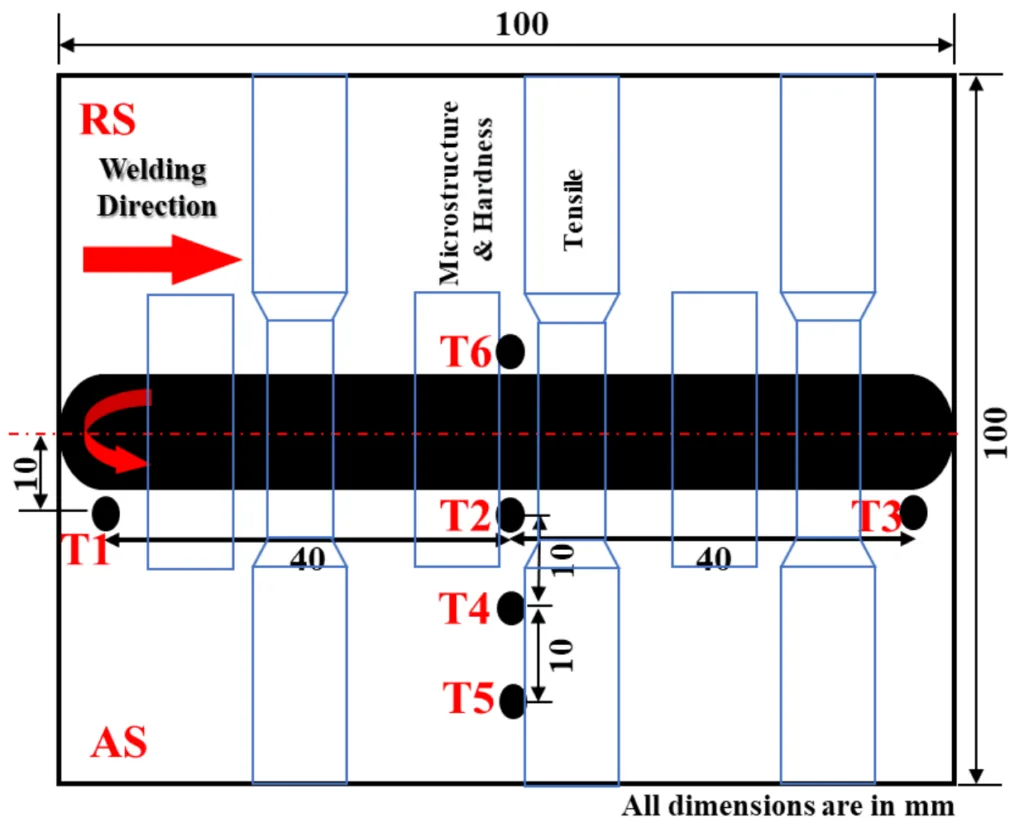
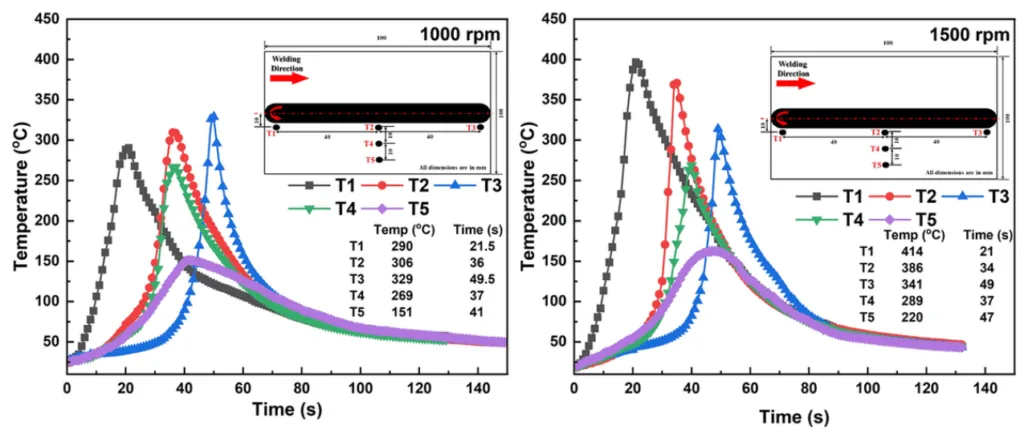
- Figure 1: FSW machine with temperature measuring instrument setup
- Figure 2: FSW tool used for the welding
- Figure 3: Representation of sample collection for the testing
- Figure 4: Comparison of thermal profiles for the TRS of 1000 rpm and 1500 rpm
- Figure 5: Cooling rate vs thermocouple positions for different TRS condition
- Figure 6: Comparison of AS and RS thermal profiles for different TRS
- Figure 7: Comparison of spindle torque and Z-force for different TRS
- Figure 8: Comparison of X-force for different TRS
- Figure 9: Comparison of the averages of spindle torque, Z-force and X-force for different TRS
- Figure 10: Relationship between TRP and energy input for variation of TRS and at constant TTS
- Figure 11: SEM micrograph of BM and the spots selected for EDS analysis
- Figure 12: EDS spectrum of the selected area in the BM
- Figure 13: Weld bead surface for different TRS
- Figure 14: Weld macrostructure at different TRS
- Figure 15: The orientation of particles in weld nugget at different TRS
- Figure 16: Presence of iron particle in the weld nugget at 1750 rpm
- Figure 17: Evidence of the formation of Al2O3 phase at 1750 rpm effecting tensile properties
- Figure 18: Weld nugget microstructure at different TRS
- Figure 19: Weld nugget grain structure for different TRS
- Figure 20: Hardness plots
- Figure 21: Front and side view of tensile fractured samples
- Figure 22: Comparison of the tensile strength
- Figure 23: Fractographic image of the samples at different TRS conditions
7. Conclusion:
The quantitative findings from this study indicate that a TRS range of 1250 to 1750 rpm, maintaining a fixed TRS of 2.75 mm/s, achieves a balance between microstructural refinement and enhanced mechanical performance for this material under the FSW process. At lower TRS (1000 rpm), temperature rises as welding proceeds, while higher TRS shows opposite trend. Increasing TRS leads to decreased spindle torque and Z-force. Microstructural analysis reveals diverse SiC particle aggregation in the Nugget Zone across all TRS conditions. Welds exhibit considerably lower hardness compared to the BM with 'W' shape profile. Maximum UTS of 358 MPa achieved at 1500 rpm with joint efficiency peaking at 87%.
8. References:
[References are listed exactly as cited in the paper, numbered from 1-49, including authors, publication years, titles, and DOI information as provided in the original document]
9. Copyright:
- This material is a paper by "Uttam Acharya, Smrity Choudhury, Durjyodhan Sethi, Esther Akinlabi, Kuldeep K Saxena, Barnik Saha Roy". Based on "A comprehensive investigation on various welding facets for FSW of advanced structural AMC".
- Source of the paper: https://doi.org/10.21203/rs.3.rs-3930818/v1
This material is summarized based on the above paper, and unauthorized use for commercial purposes is prohibited.
Copyright © 2025 CASTMAN. All rights reserved.
Paper Summarize:
This comprehensive study investigates friction stir welding of advanced structural aluminum matrix composites (AA6092/17.5 SiCp-T6) with systematic variation of tool rotational speed. The research demonstrates that optimal welding parameters can achieve superior mechanical properties, with 1500 rpm showing the best balance of microstructural refinement and mechanical performance, achieving 87% joint efficiency and predominant ductile fracture behavior.
Key questions and answers about the research:
Q1. What is the optimal Tool Rotational Speed for FSW of AA6092/17.5 SiCp-T6 composites?
A1. Based on the comprehensive investigation, 1500 rpm emerges as the optimal TRS, achieving maximum joint efficiency of 87%, finest particle size (6.86 µm), and highest hardness (121 HV0.1) with predominantly ductile fracture behavior. Source: "A comprehensive investigation on various welding facets for FSW of advanced structural AMC" - Results and Discussion section.
Q2. How does Tool Rotational Speed affect the thermal distribution during FSW?
A2. At lower TRS (1000 rpm), temperature increases along the welding direction from 290°C to 329°C, while at higher TRS (1500 rpm), temperature decreases from 414°C to 341°C along the same positions. The Advancing Side consistently shows higher temperatures than the Retreating Side, with this difference widening at higher TRS. Source: "A comprehensive investigation on various welding facets for FSW of advanced structural AMC" - Weld thermal profile section.
Q3. What microstructural changes occur in the weld nugget with varying TRS?
A3. Particle size decreases from 8.73 µm at 1000 rpm to 6.86 µm at 1500 rpm, then increases to 8.18 µm at 1750 rpm. Grain size follows similar trend, decreasing from 12.23 µm to 9.16 µm at 1500 rpm, then increasing to 14.08 µm. Dense SiC particle aggregation occurs in the Nugget Zone, with onion ring width of 80 µm observed at 1500 rpm. Source: "A comprehensive investigation on various welding facets for FSW of advanced structural AMC" - Critical microstructural findings section.
Q4. How do force and torque characteristics change with increasing TRS?
A4. Spindle torque decreases significantly from 17.2 N-m at 1000 rpm to 8.63 N-m at 1750 rpm, while Z-force decreases from 9715 N to 7126.1 N. X-force shows irregular fluctuations throughout welding, with degree of fluctuation decreasing at higher TRS. A direct linear relationship exists between Tool Revolution Pitch and energy input. Source: "A comprehensive investigation on various welding facets for FSW of advanced structural AMC" - Spindle torque and force analysis section.
Q5. What mechanical properties are achieved in the FSW joints compared to base material?
A5. Ultimate Tensile Strength ranges from 308 MPa to 358 MPa (base material: 415 MPa), with joint efficiency peaking at 87% for 1500 rpm. Hardness exhibits 'W' shape profile with lowest values consistently in AS-HAZ region. Welding at 1500 rpm shows greater elongation than base metal with predominantly ductile fracture behavior. Source: "A comprehensive investigation on various welding facets for FSW of advanced structural AMC" - Effect on Mechanical Properties section.
Q6. What defects or issues occur at higher Tool Rotational Speeds?
A6. At 1750 rpm, significant tool wear evidenced by iron content (41.74%) and formation of Al2O3 mud-cake-like structure with 52.25% oxygen content are observed. This leads to mixed mode fracture behavior and fracture within the weld zone rather than outside it, resulting in reduced joint efficiency (74%) and lower mechanical properties. Source: "A comprehensive investigation on various welding facets for FSW of advanced structural AMC" - Critical microstructural findings and Tensile Property sections.