This article introduces the paper "Corrosion Protection of Joining Areas in Magnesium Die-Cast and Sheet Products."
1. Overview:
- Title: Corrosion Protection of Joining Areas in Magnesium Die-Cast and Sheet Products
- Author: Wenyue Zheng, C. Derushie, J. Lo and E. Essadiqi
- Publication Year: 2007
- Publishing Journal/Academic Society: Materials Science Forum, Vols. 546-549, pp 523-528
- Keywords: Magnesium sheet, die cast, galvanic corrosion, friction-stir welding, adhesive bonding, riveting, fastening, coating, galvanic compatibility
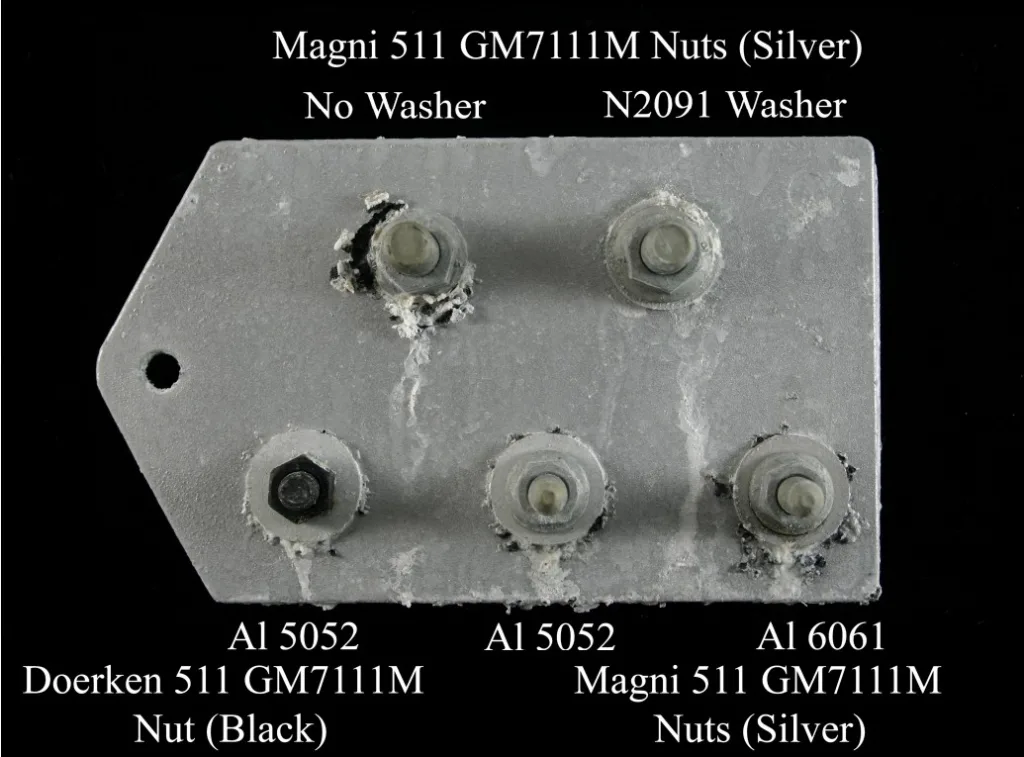
2. Research Background:
- Social/Academic Context of the Research Topic: The increasing use of magnesium alloys in large automotive components and subsystems, such as in DaimlerChrysler's new lightweight body and the 2006 Z06 Corvette engine cradle, has brought the corrosion performance of joining areas into critical focus. In complex multi-material systems, joining diverse materials with sufficient strength is essential. These joining areas become potential sites for galvanic corrosion, especially when exposed to corrosive environments like road salt and sand. Magnesium, being the most reactive metal, makes corrosion a particularly serious concern in automotive applications.
- Limitations of Existing Research: While not explicitly stated as limitations of existing research within the paper, the context implies a gap in comprehensive understanding and effective solutions for corrosion protection in magnesium alloy joints, particularly with the advent of advanced joining technologies. The paper addresses the practical challenges arising from the application of common joining techniques to magnesium in automotive settings, suggesting a need for more focused research in this specific area.
- Necessity of the Research: Protecting joining areas in magnesium automotive products is identified as a key task within corrosion research activities at CANMET. The paper emphasizes the complexity introduced by common automotive joining techniques like riveting, friction-stir welding, and adhesive bonding. These methods, while structurally effective, can exacerbate corrosion issues. The research is necessary to address these challenges and provide solutions for ensuring the long-term durability and reliability of magnesium components in automotive environments. This paper summarizes recent research results achieved by CANMET in this critical area of corrosion protection for magnesium joining areas.
3. Research Purpose and Research Questions:
- Research Purpose: The primary research purpose is to investigate and summarize recent findings on corrosion protection methods specifically for joining areas in magnesium die-cast and sheet products. The study focuses on evaluating the impact of various joining techniques, including friction-stir welding (FSW), adhesive bonding, and riveting, on the corrosion behavior of magnesium alloys. The research aims to identify effective strategies for mitigating corrosion in these critical joining zones.
- Key Research Questions:
- How do common joining techniques for magnesium sheet and die cast alloys, such as riveting, friction-stir welding, and adhesive bonding, influence corrosion performance in the joining areas?
- What are the corrosion characteristics of as-cast surfaces of magnesium die-cast components compared to machined surfaces?
- How does surface contamination, particularly from iron-rich particles, affect the corrosion rate of magnesium sheet and die cast materials?
- What is the effectiveness of friction-stir welding and adhesive bonding, both individually and in combination, in improving the lap-shear strength and corrosion resistance of magnesium joints?
- How do different coating processes, such as powder coating and anodizing, affect the corrosion protection and adhesion strength of adhesively bonded magnesium joints?
- What are the galvanic corrosion concerns associated with using steel rivets for joining magnesium alloys, and what types of coatings or washers can mitigate these issues?
- Research Hypotheses: While not explicitly stated as formal hypotheses, the research is guided by implicit assumptions that:
- Surface contamination on magnesium sheet and die-cast products significantly increases their corrosion rate.
- Friction-stir welding and adhesive bonding can enhance the structural integrity and corrosion resistance of magnesium joints.
- Anodizing provides superior adhesion strength retention in corrosive environments compared to conversion coatings for adhesively bonded magnesium joints, but may present challenges for galvanic corrosion in riveted joints.
- Galvanically compatible coatings are essential for steel rivets to prevent or minimize galvanic corrosion when joining magnesium alloys.
4. Research Methodology
- Research Design: The research employs an experimental design focused on evaluating the corrosion performance of magnesium alloy joints under various conditions. This includes comparative studies of different surface treatments, joining techniques, and protective coatings. The study utilizes standardized corrosion tests and mechanical testing to quantify and assess the effectiveness of different corrosion protection strategies.
- Data Collection Method: Data was collected through a combination of quantitative and qualitative methods:
- Weight Loss Measurements: ASTM B117 salt spray tests were conducted on magnesium alloy plates to measure weight loss as an indicator of corrosion rate. Weight-loss data for AM60B plates from two suppliers were collected and compared for as-received and machined surfaces.
- Lap-Shear Strength Testing: ASTM D-1002 type lap-shear samples were prepared using friction-stir welding and adhesive bonding techniques. Failure load was measured before and after salt-spray exposure to assess the impact of corrosion on joint strength.
- Electrochemical Measurements: Galvanic corrosion performance was evaluated using GM9540P test environment for riveted joints with different rivet materials and coatings.
- Microscopic Examination: Scanning Electron Microscopy (SEM) was used to examine corroded surfaces, identify corrosion products, and analyze surface contamination, such as iron-rich particles.
- Elemental Analysis: Energy Dispersive Spectroscopy (EDS) was employed to determine the elemental composition of surface contaminants and corrosion products observed in SEM images.
- Visual Inspection: Visual inspection was used to assess the extent of corrosion on riveted joints after exposure to corrosive environments.
- Analysis Method: The collected data was analyzed using:
- Comparative Analysis: Corrosion rates of as-cast and machined surfaces were compared using weight loss data. Lap-shear failure loads of FSW and adhesively bonded joints, with and without corrosion exposure and different coatings, were compared to evaluate the effectiveness of joining methods and protective treatments.
- Statistical Analysis: Although not explicitly mentioned as statistical analysis in the paper, the comparison of average weight loss and failure load values implies basic statistical comparison to determine the significance of observed differences.
- Microstructural Analysis: SEM images and EDS spectra were analyzed to identify corrosion mechanisms, the role of surface contaminants, and the effectiveness of coatings at a microstructural level.
- Qualitative Assessment: Visual inspection results provided qualitative data on the type and extent of corrosion in different conditions, particularly for riveted joints.
- Research Subjects and Scope: The research focused on:
- Materials:
- High-Pressure Die Cast (HPDC) AM60B magnesium alloy plates from two suppliers.
- As-rolled AZ31 magnesium alloy sheets.
- AE44 magnesium alloy for fastener studies.
- Aluminum alloy A6061 for Mg-Al joining and washers.
- Aluminum alloy A5052 for washers.
- Steel rivets (plain, Sn-coated, Zn-coated).
- Coated steel fasteners and nuts.
- Joining Techniques:
- Friction-stir spot welding (FSW) for Mg-Mg and Mg-Al joints.
- Adhesive bonding.
- Riveting.
- Fastening with bolts and nuts.
- Coatings and Surface Treatments:
- Machining to remove surface layer.
- Organic solvent degreasing.
- Fluorozirconate pre-treatment.
- Epoxy powder coating (with and without metallic powder pigments).
- Commercial anodizing.
- Alodine 5200 pre-treatment.
- Sn and Zn electroplating on washers and rivets.
- Testing Environments:
- ASTM B117 salt spray test.
- GM9540P test environment.
- Materials:
5. Main Research Results:
- Key Research Results:
- Surface Corrosion Rate of Mg Sheet and Die Cast Materials:
- As-cast surfaces of HPDC AM60B plates from both suppliers exhibited higher corrosion rates compared to machined surfaces in ASTM B117 tests. The corrosion rate of as-cast surfaces was up to 100% higher in some cases.
- SEM examination revealed the presence of iron-rich particles on the as-cast surfaces, which are likely foreign objects left from the die casting process and contribute to increased corrosion.
- AZ31 magnesium sheets showed a significantly higher corrosion rate for as-rolled surfaces compared to machined surfaces, with the corrosion rate being at least one order of magnitude greater. EDS analysis confirmed the presence of detectable amounts of Fe-rich particles on the as-received AZ31 sheet surface.
- Effects of Corrosion on Lap-Shear Strength of Friction-Stir Weld (FSW) and Adhesive Bonding:
- Friction-stir welding (FSW) is considered a promising joining method for Mg alloys.
- For Mg-Mg joints, the effect of corrosion in reducing lap-shear strength was most dramatic for FSW-only joints. These joints did not resist the corrosion environment well, with corrosion observed around the keyhole.
- Combining FSW with adhesive bonding significantly improved lap-shear strength and corrosion resistance.
- Anodizing as a pre-treatment for adhesive bonding resulted in better retention of lap-shear strength after salt spray exposure compared to conversion pre-treatment plus powder coating. Conversion-coated samples showed a lap-shear strength loss greater than 30% after corrosion testing.
- The effect of corrosion exposure on Mg-Al joints was similar to Mg-Mg joints. However, as-welded Mg-Al pairs tended to be somewhat weaker than as-welded Mg-Mg joints due to the formation of intermetallics in the stir-metal zone.
- Galvanic Corrosion of Fastened Mg Alloys:
- Galvanic corrosion of fastened Mg alloys was studied extensively.
- Using Al-based washers significantly reduced the extent of galvanic attack compared to using no washer with coated steel fasteners.
- The 'N2091' washer, an in-house developed Al-Mg based alloy washer, showed the best galvanic compatibility, having a corrosion potential very close to Mg alloy.
- Joining by Riveting:
- Preliminary study of riveting showed that galvanic corrosion is quite fast on anodized Mg AM60 plates when using plain steel rivets.
- Epoxy powder coating provided better resistance to galvanic action of plain steel rivets compared to anodizing.
- Anodizing is preferred for adhesive bonding due to lap-shear strength retention, but conversion treatment with epoxy topcoat is better for resisting galvanic corrosion in riveted joints.
- Developing an advanced coating system for steel SPR rivets is necessary, requiring hardness for piercing, ductility for deformation, and electrical resistivity or electrochemical compatibility with Mg alloys.
- Surface Corrosion Rate of Mg Sheet and Die Cast Materials:
- Statistical/Qualitative Analysis Results:
- Weight Loss Data:
- Figure 1: Weight-loss data for AM60B plates from supplier A shows that as-received surfaces have higher mass change (g/cm²) compared to machined surfaces across 200 to 800 hours of exposure.
- Figure 2: Weight-loss data for AM60B plates from supplier B also indicates higher mass change for as-received surfaces compared to machined surfaces over the same exposure period.
- Figure 4: Comparison of corrosion rate for AZ31 sheet surfaces (AR, ARM, HT, HTM) shows that received surface (AR) has significantly higher mass change (g/cm²) than machined surface (ARM) and heat-treated samples over test times from 1 to 16 days.
- Lap-Shear Failure Load Data:
- Figure 5: Effects of salt-spray exposure on lap-shear failure load of FSW samples. Mg-Mg FSW-only joints show a dramatic reduction in failure load after 10 days of B117 salt spray. Adding adhesive significantly improves failure load retention after exposure. Anodized Mg samples with adhesive show better performance than conversion pre-treated + powder coated samples with adhesive after exposure.
- SEM and EDS Analysis:
- Figure 3: SEM image shows an iron-rich particle on an AM60 sample, with a 'halo' of corrosion around it, indicating that the particle acted as a corrosion initiation site.
- Figure 6: SEM image shows contamination particles (white) found on a corroded surface, indicating surface contamination related to fast corrosion.
- Figure 7: EDS analysis of a particle from Figure 6 confirms a high Fe level, supporting the presence of iron-rich contamination.
- Visual Inspection of Riveted Joints:
- Figure 8: Appearance of fastened AE44 plates pretreated with fluorozirconate and a metallic-looking epoxy-based powder coat, showing galvanic corrosion around Al washers when electrically conducting ingredients are in the coating.
- Figure 9: Performance of various rivets placed into (Fluorozirconate +epoxy powder coat) after GM9540P test.
- Figure 10: Performance of various rivets coated AM60 plate placed into anodized AM60 plate after GM9540P test, showing faster galvanic corrosion on anodized sample compared to epoxy powder coated sample.
- Weight Loss Data:
- Data Interpretation:
- Higher corrosion rates of as-cast magnesium surfaces are attributed to surface contamination by iron-rich particles introduced during the die casting process or sheet making.
- Friction-stir welding and adhesive bonding are effective in enhancing the structural integrity and corrosion resistance of magnesium joints, especially when used in combination.
- Anodizing provides better adhesion strength retention for adhesively bonded joints in corrosive environments compared to conversion coatings, suggesting its suitability for applications where bond durability is critical.
- Galvanic corrosion is a significant concern in riveted and fastened magnesium joints, necessitating the use of galvanically compatible materials or coatings to mitigate corrosion. Al-Mg alloy washers and specialized coatings for steel rivets are potential solutions.
- The choice of coating for corrosion protection in magnesium joining areas depends on the specific application and joining method. Anodizing is beneficial for adhesive bonding strength, while conversion coatings with epoxy topcoats offer better resistance to galvanic corrosion in riveted joints.
- Figure Name List:
- Figure 1 Weight-loss data for AM60B plates plates from supplier A.
- Figure 2 Weight-loss data for AM60B test from supplier B.
- Figure 3 SEM image showing an iron-rich particle on an AM60 sample.
- Figure 4 Comparison of the corrosion rate of the received surface (AR) and machined surface (ARM) (HT refers to heat-treated sample with original surface, and HTM for heat-treated sample with machined surface. All data are for the same AZ31sheet.)
- Figure 5 Effects of salt-spray exposure on lap-shear failure load of FSW samples with and without the use of adhesives.
- Figure 6 contamination particles (white) found
- Figure 7 EDS analysis of a particle shown in the previous figure, showing high Fe level.
- Figure 8 Appearance of fastened AE44 plates pretreated with fluorozirconate and a metallic-looking epoxy-based powder coat.
- Figure 9 Performance of various rivets placed into (Fluorozirconate +epoxy powder coat)
- Figure 10 Performance of various rivets coated AM60 plate placed into anodized AM60 plate
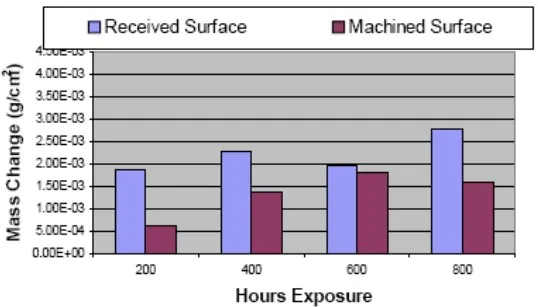
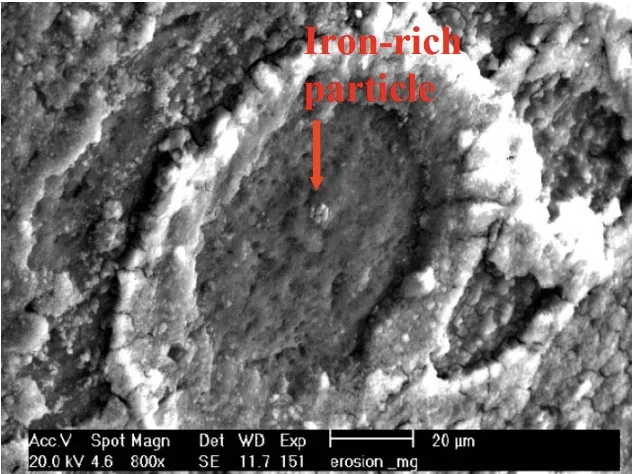
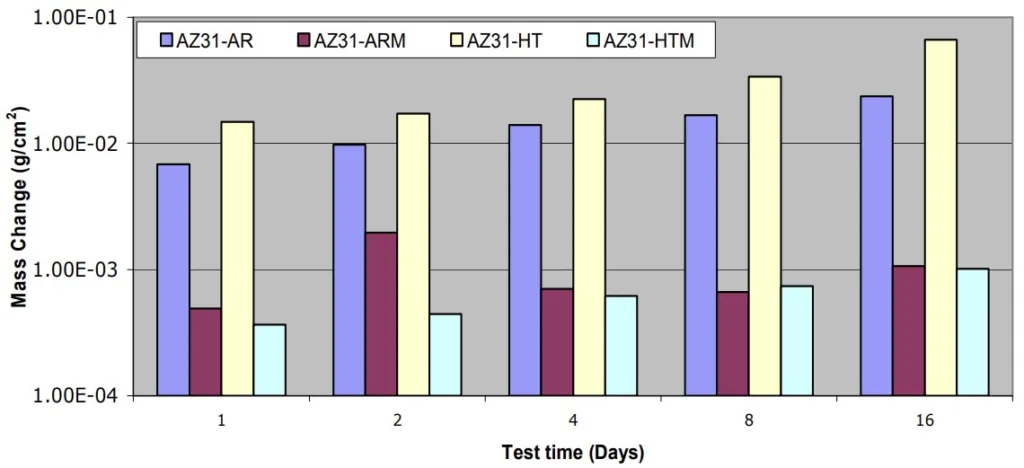
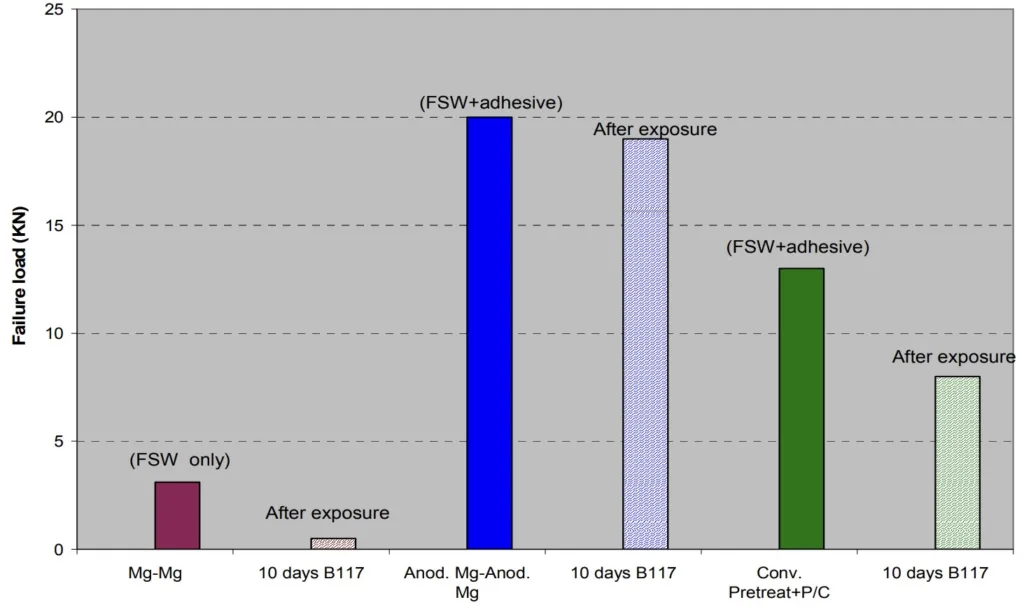
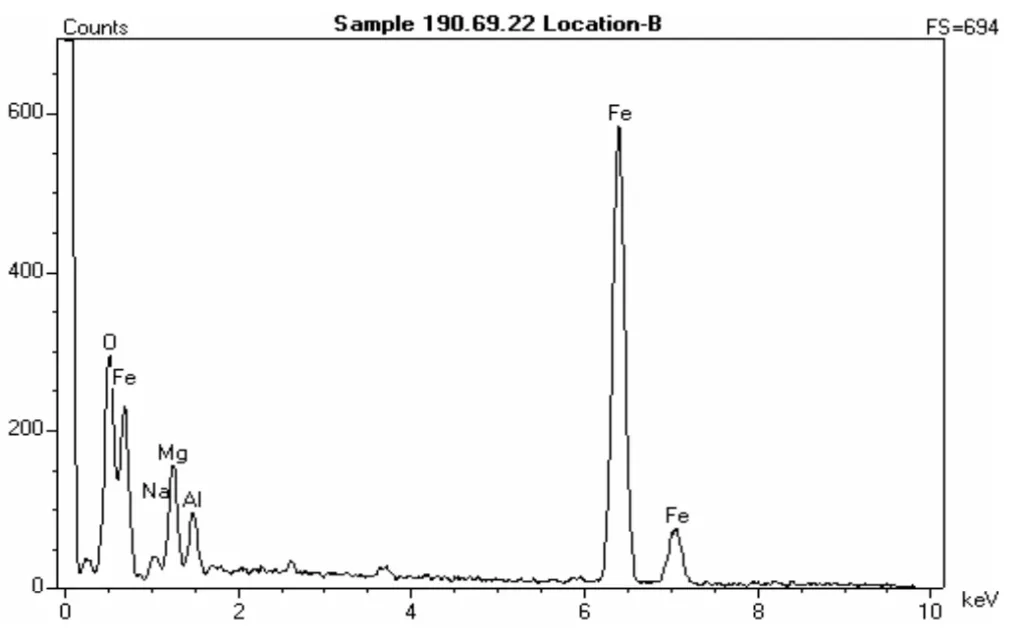
6. Conclusion and Discussion:
- Summary of Main Results: The research concludes that AZ31 sheets are prone to high corrosion rates when contaminated with iron particles from sheet-making. Combining adhesive bonding and friction-stir welding significantly improves the lap-shear strength of Mg-Mg joints. Anodized magnesium samples exhibit better resistance to corrosion attack and retain higher lap-shear bond strength compared to powder-coated samples during ASTM B117 salt-spray exposure. Galvanic corrosion in riveted Mg joints is a significant challenge, and developing galvanically compatible coatings for steel rivets is crucial.
- Academic Significance of the Research: This research contributes to the academic understanding of corrosion mechanisms in magnesium alloy joining areas. It highlights the critical role of surface contamination in accelerating corrosion and demonstrates the effectiveness of different joining and coating strategies in mitigating corrosion. The study provides valuable insights into the comparative performance of anodizing and conversion coatings in adhesive bonding and riveting applications for magnesium alloys.
- Practical Implications: The findings have significant practical implications for the automotive industry and other sectors utilizing magnesium alloys. The research underscores the importance of controlling surface contamination during the manufacturing of magnesium sheets and die-cast components. It provides guidance for selecting appropriate joining techniques and corrosion protection systems for magnesium structures. Specifically, it emphasizes the benefits of combining adhesive bonding with FSW for enhanced joint performance and the necessity for developing galvanically compatible coatings for steel rivets used with magnesium alloys. The study suggests that while anodizing is excellent for adhesive bonding, conversion coatings may be more suitable for riveted joints in terms of galvanic corrosion resistance.
- Limitations of the Research: The research is primarily focused on specific magnesium alloys (AM60B, AZ31, AE44) and joining methods. The findings may not be directly generalizable to all magnesium alloys or joining techniques. The corrosion testing was conducted under controlled laboratory conditions (ASTM B117 and GM9540P tests), which may not fully replicate the complex and variable conditions of real-world automotive environments. Long-term corrosion performance and the effects of other environmental factors were not extensively investigated within the scope of this paper.
7. Future Follow-up Research:
- Directions for Follow-up Research: Future research should focus on the development and optimization of galvanically compatible coating systems specifically for steel rivets used in joining magnesium alloys, particularly for Self-Piercing Riveting (SPR) applications. Further investigation is needed to develop advanced coating systems for SPR rivets that meet the conflicting requirements of hardness, ductility, and galvanic compatibility. Long-term corrosion performance evaluation in more realistic automotive environments is also recommended.
- Areas Requiring Further Exploration: Further exploration is needed in areas such as:
- Optimization of coating formulations and application processes to achieve both robust corrosion protection and desired mechanical properties in magnesium joining areas.
- Investigation of novel joining methods beyond FSW, adhesive bonding, and riveting for magnesium alloys.
- Study of the influence of various environmental factors, such as temperature, humidity cycles, and different types of road salts, on the long-term corrosion behavior of magnesium joints.
- Development of cost-effective and scalable corrosion protection solutions for mass production of magnesium automotive components.
8. References:
- S. Logan et al, “Lightweight Magnesium Intensive Body Structure”, SAE paper # 2006-01-0523
- J. Aragones, “Development of the 2006 Corvette Z06 Structural Cast Magnesium Crossmember”, SAE 2005-01-0340.
- J. H. W. De wit, “Inorganic and organic coatings”, in “Corrosion Mechanisms in Theory and Practice, Eds. P. Marcus and J. Oudar, Copy right @Marcel Dekker Inc, 1995.
- P. Su, A. Gerlich, M. Yamamoto And Th North, “Friction stir spot welding of a range of Mg-alloys", paper to be published in the Proceedings of COM/CIM, 2006.
- W. Zheng, C. Derushie, R. Zhang and J. Lo, Protection of Mg Alloys for Structural Applications in Automobiles, SAE Paper # 2004-01-0133, Detroit, USA. SAE, April, 2004.
- Wenyue Zheng, R. Osborne, C. Derushie and Jason Lo, Corrosion Protection of Structural Magnesium Alloys: Recent Development, SAE paper #2005-01-0732, SAE 2005.
- Su Xu, G. Williams, G. Shen, Mahi Sahoo, Richard Osborne, “Bolt-load Retention Testing of Magnesium Alloys for Automotive Applications”, 2006 paper #: 2006-01-0072, SAE,Detroit, MI, USA.
9. Copyright:
This material is Wenyue Zheng, C. Derushie, J. Lo and E. Essadiqi's paper: Based on Corrosion Protection of Joining Areas in Magnesium Die-Cast and Sheet Products.
Paper Source: https://doi.org/10.4028/www.scientific.net/MSF.546-549.523
This material was summarized based on the above paper, and unauthorized use for commercial purposes is prohibited.
Copyright © 2025 CASTMAN. All rights reserved.