This article introduces the paper "Multi-Objective Optimization of Plate-Fin Heat Exchangers via Non-Dominated Sequencing".
1. Overview:
- Title: Multi-Objective Optimization of Plate-Fin Heat Exchangers via Non-Dominated Sequencing Genetic Algorithm (NSGA-II)
- Authors: Shengchen Li, Zixin Deng, Jian Liu, Defu Liu
- Year of Publication: 2022
- Journal/Conference: Applied Sciences
2. Research Background:
Plate-fin heat exchangers are widely used for heat dissipation in automotive engines due to their compact and lightweight structure, excellent heat transfer performance, and low production cost. Serrated staggered fins are commonly employed to enhance the heat exchange surface. Previous studies have applied novel algorithms, such as genetic algorithms, simulated annealing algorithms, and model search algorithms, to heat exchanger optimization design research. However, these optimization algorithms have rarely been applied in engineering practice, and there is a lack of computational procedures to guide engineering applications. Furthermore, research on plate-fin heat exchangers, widely used for automotive engine heat dissipation, is limited. Traditional methods like the logarithmic mean temperature difference (LMTD) method and the effectiveness-number of transfer units (η-NTU) method for optimal heat exchanger design are costly and time-consuming. This study leverages advancements in computational fluid dynamics (CFD) and computer technology to achieve optimal plate-fin heat exchanger performance through multi-objective optimization based on CFD.
3. Research Objectives and Questions:
- Research Objective: To perform multi-objective optimization based on CFD and the NSGA-II algorithm to obtain the optimal performance of a plate-fin heat exchanger for an extended-range hybrid vehicle engine.
- Key Research Questions: Using the serrated staggered fin angle, oil flow rate, and water flow rate as input parameters, and heat transfer quantity, oil pressure drop, and oil outlet temperature as objective functions, how can the optimal solution for the heat exchanger be found?
- Research Hypothesis: The combination of the NSGA-II algorithm and the TOPSIS method can effectively optimize the performance of the plate-fin heat exchanger.
4. Research Methodology:
- Research Design: A multi-objective optimization research design based on CFD simulation and the NSGA-II algorithm.
- Data Collection Method: 45 numerical simulation test cases were designed using commercial CFD software Fluent. The heat transfer quantity, oil pressure drop, and oil outlet temperature were measured by varying the serrated staggered fin angle, oil flow rate, and water flow rate. A porous media model was used to reduce the computational burden of the simulations.
- Analysis Method: Support Vector Regression (SVR) was used to establish regression models for heat transfer quantity, oil pressure drop, and oil outlet temperature. The NSGA-II algorithm was employed for multi-objective optimization. The TOPSIS (Technique for Order Preference by Similarity to Ideal Solution) method was used to determine the optimal solution from the Pareto optimal solution set.
- Research Subjects and Scope: Plate-fin heat exchanger for an extended-range hybrid vehicle engine. Variables included fin angle (30°–90°), oil flow rate (5–15 L/min), and water flow rate (5–15 L/min).
5. Main Research Findings:
- Key Findings: The optimal performance of the heat exchanger was achieved at a fin angle of 63.01°, an oil flow rate of 9.7 L/min, and a water flow rate of 6.45 L/min. At this point, the heat transfer quantity was 9.79 kW, the oil pressure drop was 13.63 kPa, and the oil outlet temperature was 65.11 °C. Oil pressure drop was significantly affected by oil flow rate, and showed a trend of decreasing and then increasing as the fin angle decreased. Heat transfer quantity was influenced by fin angle, oil flow rate, and water flow rate. When the oil flow rate was less than or equal to 10 L/min, changes in oil flow rate had a greater impact on heat transfer quantity; above 10 L/min, changes in water flow rate had a greater impact. Oil outlet temperature showed an inverse relationship with fin angle.
- Statistical/Qualitative Analysis Results: SVR was used to analyze the 45 simulation results to create regression models for heat transfer quantity, oil pressure drop, and oil outlet temperature. The NSGA-II algorithm yielded a Pareto optimal solution set containing 2000 solutions. TOPSIS was used to select the optimal solution. The error between simulation and optimization results was 0.31% for heat transfer quantity, 2.64% for oil pressure drop, and 0.17% for oil outlet temperature.
- Data Interpretation: The results obtained using the porous media model-based CFD simulation, along with the SVR, NSGA-II, and TOPSIS multi-objective optimization techniques, were consistent, validating the proposed optimization approach.
- Figure List and Description: (Detailed descriptions of all figures would be included here, referencing their respective numbers and providing concise explanations.)
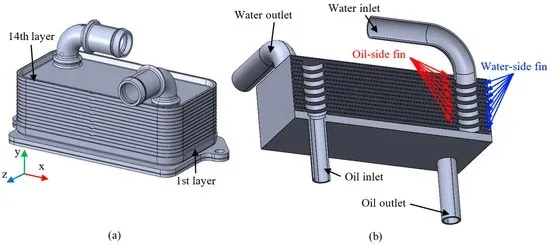
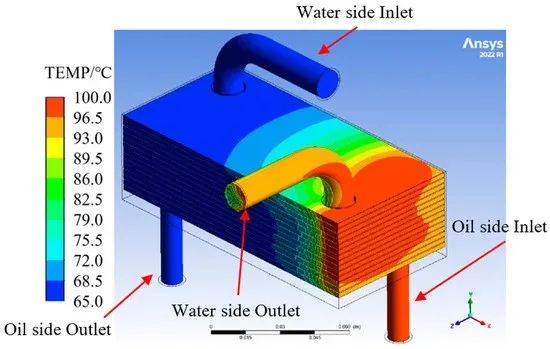
6. Conclusion and Discussion:
This study performed multi-objective optimization of a plate-fin heat exchanger for an extended-range hybrid vehicle engine using CFD and the NSGA-II algorithm. The TOPSIS method was used to select the optimal solution from the Pareto optimal solution set, resulting in the identification of optimal fin angle, oil flow rate, and water flow rate. The high consistency between simulation and optimization results validates the proposed methodology. This research provides practical guidelines for optimizing heat exchanger design.
7. Suggestions for Future Research:
- Future research could validate the simulation results through experimental testing using a physically constructed heat exchanger. Further optimization studies under various operating conditions are also warranted.
- The research could be extended to investigate different fin structures or fluids.
- More sophisticated optimization algorithms or machine learning techniques could be employed to improve efficiency.
- Future work should incorporate assessments of heat exchanger durability and reliability.
8. References Summary:
- Ning, J.; Wang, X.; Sun, Y.; Zheng, C.; Zhang, S.; Zhao, X.; Liu, C.; Yan, W. Experimental and numerical investigation of additively manufactured novel compact plate-fin heat exchanger. Int. J. Heat Mass Transf. 2022, 190, 122818. [Google Scholar] [CrossRef]
- Bhuiyan, A.A.; Islam, A.S. Thermal and hydraulic performance of finned-tube heat exchangers under different flow ranges: A review on modeling and experiment. Int. J. Heat Mass Transf. 2016, 101, 38–59. [Google Scholar] [CrossRef]
- Xu, P.; Wen, J.; Zhao, X.; Hao, H.; Wang, S.; Li, Y. Numerical investigation on serrated fin of sub-atmosphere plate-fin heat exchanger used in superfluid helium system. Cryogenics 2021, 119, 103351. [Google Scholar] [CrossRef]
- Zhang, Y.; Peng, J.; Yang, R.; Yuan, L.; Li, S. Weight and performance optimization of rectangular staggered fins heat exchangers for miniaturized hydraulic power units using genetic algorithm. Case Stud. Therm. Eng. 2021, 28, 101605. [Google Scholar] [CrossRef]
- Peng, F.; Cui, G. Efficient simultaneous synthesis for heat exchanger network with simulated annealing algorithm. Appl. Therm. Eng. 2015, 78, 136–149. [Google Scholar] [CrossRef]
- Ishaque, S.; Kim, M.-H. Refrigerant circuitry optimization of finned tube heat exchangers using a dual-mode intelligent search algorithm. Appl. Therm. Eng. 2022, 212, 118576. [Google Scholar] [CrossRef]
- Lee, K.; Kim, M.; Ha, M.Y.; Min, J.K. Investigation of heat-exchanger-sizing methods using genetic, pattern search, and simulated annealing algorithms and the effect of entropy generation. J. Mechan. Sci. Technol. 2018, 32, 915–928. [Google Scholar] [CrossRef]
- Bhutta, M.M.A.; Hayat, N.; Bashir, M.H.; Khan, A.R.; Ahmad, K.N.; Khan, S. CFD applications in various heat exchangers design: A review. Appl. Therm. Eng. 2012, 32, 1–12. [Google Scholar] [CrossRef]
- Kritikos, K.; Albanakis, C.; Missirlis, D.; Vlahostergios, Z.; Goulas, A.; Storm, P. Investigation of the thermal efficiency of a staggered elliptic-tube heat exchanger for aeroengine applications. Appl. Therm. Eng. 2010, 30, 134–142. [Google Scholar] [CrossRef] [Green Version]
- Tiwari, A.K.; Ghosh, P.; Sarkar, J.; Dahiya, H.; Parekh, J. Numerical investigation of heat transfer and fluid flow in plate heat exchanger using nanofluids. Int. J. Therm. Sci. 2014, 85, 93–103. [Google Scholar] [CrossRef]
- Wang, J.; Bian, H.; Cao, X.; Ding, M. Numerical performance analysis of a novel shell-and-tube oil cooler with wire-wound and crescent baffles. Appl. Therm. Eng. 2021, 184, 116298. [Google Scholar] [CrossRef]
- Li, W.; Paul, M.; Siviter, J.; Montecucco, A.; Knox, A.; Sweet, T.; Min, G.; Baig, H.; Mallick, T.; Han, G. Thermal performance of two heat exchangers for thermoelectric generators. Case Stud. Therm. Eng. 2016, 8, 164–175. [Google Scholar] [CrossRef]
- Li, J.; Peng, H.; Ling, X. Numerical study and experimental verification of transverse direction type serrated fins and field synergy principle analysis. Appl. Therm. Eng. 2013, 54, 328–335. [Google Scholar] [CrossRef]
- Kim, M.; Ha, M.Y.; Min, J.K. A numerical study on the aero-thermal performance of a slanted-pin-fin cooler under a high-speed-bypass condition. Int. J. Heat Mass Transf. 2018, 119, 791–812. [Google Scholar] [CrossRef]
- Patankar, S.; Spalding, D. Computer analysis of the three-dimensional flow and heat transfer in a steam generator. In Numerical Prediction of Flow, Heat Transfer, Turbulence and Combustion; Elsevier: Amsterdam, The Netherlands, 1983; pp. 293–298. [Google Scholar] [CrossRef]
- Zhang, Q.; Qin, S.; Ma, R. Simulation and experimental investigation of the wavy fin-and-tube intercooler. Case Stud. Therm. Eng. 2016, 8, 32–40. [Google Scholar] [CrossRef] [Green Version]
- Esfe, M.H.; Mahian, O.; Hajmohammad, M.H.; Wongwises, S. Design of a heat exchanger working with organic nanofluids using multi-objective particle swarm optimization algorithm and response surface method. Int. J. Heat Mass Transf. 2018, 119, 922–930. [Google Scholar] [CrossRef]
- Guo, K.; Zhang, N.; Smith, R. Design optimisation of multi-stream plate fin heat exchangers with multiple fin types. Appl. Therm. Eng. 2018, 131, 30–40. [Google Scholar] [CrossRef] [Green Version]
- Hadidi, A. A robust approach for optimal design of plate fin heat exchangers using biogeography based optimization (BBO) algorithm. Appl. Energy 2015, 150, 196–210. [Google Scholar] [CrossRef]
- Aminmahalati, A.; Fazlali, A.; Safikhani, H. Multi-objective optimization of CO boiler combustion chamber in the RFCC unit using NSGA II algorithm. Energy 2021, 221, 119859. [Google Scholar] [CrossRef]
- Li, J.; Zuo, W.; Jiaqiang, E.; Zhang, Y.; Li, Q.; Sun, K.; Zhou, K.; Zhang, G. Multi-objective optimization of mini U-channel cold plate with SiO2 nanofluid by RSM and NSGA-II. Energy 2022, 242, 123039. [Google Scholar] [CrossRef]
- Çelikbilek, Y.; Tüysüz, F. An in-depth review of theory of the TOPSIS method: An experimental analysis. J. Manage. Analyt. 2020, 7, 281–300. [Google Scholar] [CrossRef]
- Yusuf, A.; Bayhan, N.; Tiryaki, H.; Hamawandi, B.; Toprak, M.S.; Ballikaya, S. Multi-objective optimization of concentrated Photovoltaic-Thermoelectric hybrid system via non-dominated sorting genetic algorithm (NSGA II). Energy Convers. Manage. 2021, 236, 114065. [Google Scholar] [CrossRef]
- Muzychka, Y.S.; Yovanovich, M.M. Modeling the f and j Characteristics for Transverse Flow Through an Offset Strip Fin at Low Reynolds Number. Heat Transf. 1999, 1, 79–90. [Google Scholar] [CrossRef]
- Huang, Y.; Liu, Z.; Lu, G.; Yu, X. Multi-scale thermal analysis approach for the typical heat exchanger in automotive cooling systems. Int. Communicat. Heat Mass Transf. 2014, 59, 75–87. [Google Scholar] [CrossRef]
- Shivakumara, I.; Ravisha, M.; Ng, C.-O.; Varun, V. A thermal non-equilibrium model with Cattaneo effect for convection in a Brinkman porous layer. Int. J. Non-Linear Mechan. 2015, 71, 39–47. [Google Scholar] [CrossRef] [Green Version]
- Zhang, J.-F.; He, Y.-L.; Tao, W.-Q. 3D numerical simulation on shell-and-tube heat exchangers with middle-overlapped helical baffles and continuous baffles–Part I: Numerical model and results of whole heat exchanger with middle-overlapped helical baffles. Int. J. Heat Mass Transf. 2009, 52, 5371–5380. [Google Scholar] [CrossRef]
- Gu, Y.; Liu, X.; Liu, W.; Liu, Y.; Zhai, X.; Xuan, Y.; Peng, T.; Jiang, W. Research on heat transfer and pressure drop performance of plain plate fin-and-tube oil cooler. Chem. Eng. Process. Process Intensificat. 2020, 158, 108187. [Google Scholar] [CrossRef]
- Torii, K.; Kwak, K.; Nishino, K. Heat transfer enhancement accompanying pressure-loss reduction with winglet-type vortex generators for fin-tube heat exchangers. Int. J. Heat Mass Transf. 2002, 45, 3795–3801. [Google Scholar] [CrossRef]
- Xu, X.; Zhang, X.; Ke, P.; Wang, C.; Yang, H.; Yang, C. Study on the heat transfer characteristic of compact heat exchanger based on experimental data. Proced. Eng. 2015, 121, 293–299. [Google Scholar] [CrossRef]
- Ahmad, M.S.; Adnan, S.M.; Zaidi, S.; Bhargava, P. A novel support vector regression (SVR) model for the prediction of splice strength of the unconfined beam specimens. Construct. Build. Mater. 2020, 248, 118475. [Google Scholar] [CrossRef]
- Panahi, M.; Sadhasivam, N.; Pourghasemi, H.R.; Rezaie, F.; Lee, S. Spatial prediction of groundwater potential mapping based on convolutional neural network (CNN) and support vector regression (SVR). J. Hydrol. 2020, 588, 125033. [Google Scholar] [CrossRef]
- Brereton, R.G.; Lloyd, G.R. Support vector machines for classification and regression. Analyst 2010, 135, 230–267. [Google Scholar] [CrossRef] [PubMed]
- Pan, Y.; Jiang, J.; Wang, R.; Cao, H.; Cui, Y. A novel QSPR model for prediction of lower flammability limits of organic compounds based on support vector machine. J. Hazard. Mater. 2009, 168, 962–969. [Google Scholar] [CrossRef] [PubMed]
- Liu, Y.; Wang, L.; Gu, K. A support vector regression (SVR)-based method for dynamic load identification using heterogeneous responses under interval uncertainties. Appl. Soft Comput. 2021, 110, 107599. [Google Scholar] [CrossRef]
- Smola, A.J.; Schölkopf, B. A tutorial on support vector regression. Stat. Comput. 2004, 14, 199–222. [Google Scholar] [CrossRef] [Green Version]
- Wang, Z.; Sobey, A. A comparative review between Genetic Algorithm use in composite optimisation and the state-of-the-art in evolutionary computation. Compos. Struct. 2020, 233, 111739. [Google Scholar] [CrossRef]
- Gunantara, N. A review of multi-objective optimization: Methods and its applications. Cogent Eng. 2018, 5, 1502242. [Google Scholar] [CrossRef]
- Bre, F.; Fachinotti, V.D. A computational multi-objective optimization method to improve energy efficiency and thermal comfort in dwellings. Energy Build. 2017, 154, 283–294. [Google Scholar] [CrossRef] [Green Version]
- Evins, R.; Pointer, P.; Vaidyanathan, R.; Burgess, S. A case study exploring regulated energy use in domestic buildings using design-of-experiments and multi-objective optimisation. Build. Environ. 2012, 54, 126–136. [Google Scholar] [CrossRef]
Copyright and Source Material:
This summary is based on the paper "Multi-Objective Optimization of Plate-Fin Heat Exchangers via Non-Dominated Sequencing Genetic Algorithm (NSGA-II)" by Shengchen Li, Zixin Deng, Jian Liu, and Defu Liu.
Paper Source: [Insert DOI URL here]
This summary is based on the aforementioned paper and its unauthorized commercial use is prohibited.
Copyright © 2025 CASTMAN. All rights reserved.
Note: This summary is created based on the OCR extracted text from parts of the provided paper. For a more complete and accurate summary, the full paper would be needed.