This introduction paper is based on the paper "Strength of oxide skin on aluminum melts" published by "Not specified in the provided text (Authors affiliated with Ural Federal University, Ekaterinburg, Russia)".
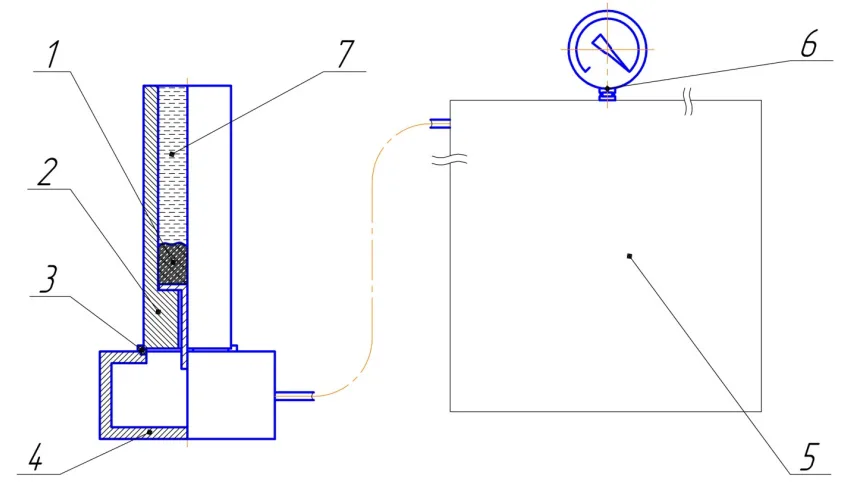
1. Overview:
- Title: Strength of oxide skin on aluminum melts
- Author: Finkelstein Arcady, Schaefer Arseny, Husnullin Dmitry, Mahmud Zoda Muminjohn
- Year of publication: Not specified in the provided text
- Journal/academic society of publication: Not specified in the provided text (Authors affiliated with Ural Federal University, Ekaterinburg, Russia)
- Keywords: Not specified in the provided text
2. Abstract:
Infiltration pressure of the “melt-filler” boundary surface within the replicated aluminum foam technique has been studied on alloys A999, AlMg5Si, and AlSi9MgFe1. It is shown that the infiltration pressure on filler fractions under 0.2 mm in size will be governed by Laplace equation. While the filler fraction size becomes larger, the infiltration pressure stays constant and shall be defined by rupture of the oxide skin on the “melt-filler” boundary. The rupture leads to appearing of a micro crack, and the oxide skin growth rate becomes lower than the leak rate of the melt in the evolving channel. Impurity elements which form defects of the crystalline structure in the oxide skin on aluminum alloys influence formation of the micro crack. The influence of magnesium adding leads to formation of MgAl2O4 in the skin and lowering of its strength. But it is iron that has the strongest impact on the oxide skin strength; when the percentage of iron exceeds 0.8% it forms an intermetallide of laminar type (Al5FeSi), thus ensuring decreasing the minimum infiltration pressure of the oxide skin from 20000 MPa on pure aluminum to 7000 MPa on AlSi9MgFel alloy.
3. Introduction:
Aluminum melts in an oxygen-containing atmosphere get covered with the oxide skins. It is a crystalline structure of spinel type (1). A skin which appears on pure aluminum is, to a high extent, an amorphous structure, while y–phase crystals of cubic form appear after exceeding the temperature of 700 °C (2) It is the y-phase of aluminum skin which is responsible for reduction of strength performance at adhesive destruction of metal matrix composites, plus for absorption of hydrogen (the basic source of gas defects in castings) by the skin due to surface defects/vacancies. The latter are focuses of hydrogen chemisorption (3).
At temperature up to 1000 °C, aluminum y–oxide is formed (2). Dimensions of the lattice correspond to the dimension of aluminum lattice, thus conforming to Dankov-Konobeyevsky's principle, which leads to high cohesion (4). The rate of growth of the oxide skin on the surface of a melt is extremely high. In case of removing the oxide skin from the melt surface, the growth rate of the skin complies with Arrhenius's equation (5). The oxide skin influences greatly the process of a casting formation. It prevents gas diffusion through the phase boundary. Due to its sufficiently high strength the oxide skin influences fluidity.
Studying of strength of a skin by modelling thereof as symmetric to the axis of a round plate with fixed edges supported by a compatible foundation showed that the pure aluminum oxide possesses low fracture stress in conditions of the maximum fracture stress intensity. The stress intensity factor showed that very low loads can lead to fracture of the skin, subject to the existence of fine surface defects (6).
According to (7) alloys of Al–Si–Cu system have fluidity differing by 1.5 times when percentage of copper therein changes by 2%. It cannot be conditioned by a change of viscosity, heat conductivity and crystallization interval of the alloy. Increase of copper percentage in Al–Cu system or in more multi–component systems on aluminum basis leads to formation of CuO within oxide skins. Upon a period of holding, CuO transits into Cu2O, thus providing cracks and ruptures in the skin. It leads to decreasing of hydrogen percentage but deteriorates protective properties of the skin. The sharp growth of fluidity is explained by presence of Cu2O within the oxide skin, which is a stress concentrator lowering mechanical strength of the oxide skin significantly (8, 9). Therefore, flowage losses of the melt kinetic energy get lower.
MgO skin possesses loose and porous structure; accounting for high activity of magnesium itself at normal and high temperatures, absorption of oxygen during melting will be very intensive. In aluminum alloys with magnesium percentage up to 1.5%, the oxide skin will contain oxides of magnesium and aluminum and their joint spinel with composition MgAl2O4. Within the melt volume, this spinel will act as a second row conditioning agent thus providing a higher number of nucleation centres. For metal matrix composites, high magnesium content which provides generation of spinel will improve mechanical properties due to lowering of double skins defects (10, 11, 12, 13).
Moreover, a group of alloys containing up to 2% of iron has been developed for die casting (14). In these alloys, from one hand, intermetallides Al5 FeSi formed at cooling will raise the alloy viscosity as per Einstein's equation, but on the other hand, they make the oxide skin softer. For die casting, in conditions of a small wall thickness of the casting and a significant cooling rate of the melt, judging by the chemical composition of the developed alloys, it is resistance of the oxide skin against flowing of the melt which plays the core role.
In course of producing composite castings by the infiltration method, when the wall thickness of a casting is even less than in case of die casting, it is necessary to break the oxide skin on the "melt-filler” boundary for initiation of melt flowing in the filler's porous medium (15). So, the minimum pressure of infiltration will be equal to the pressure of oxide skin breaking, which restricts opportunities of varying the permeability factor of finished products (16).
4. Summary of the study:
Background of the research topic:
Aluminum melts in oxygen-containing atmospheres develop oxide skins. These skins are typically crystalline, with a γ-phase appearing above 700 °C, which can reduce strength in metal matrix composites and absorb hydrogen (1, 2, 3). The oxide skin's growth rate is high and significantly influences casting formation by preventing gas diffusion and affecting fluidity due to its strength (4, 5).
Status of previous research:
Previous studies indicated that pure aluminum oxide has low fracture stress (6). In Al-Si-Cu alloys, copper content affects fluidity through the formation of copper oxides (CuO, Cu2O) in the skin, which act as stress concentrators (7, 8, 9). Magnesium in aluminum alloys leads to MgO and MgAl2O4 spinel formation in the skin, which is loose and porous (10, 11, 12, 13). Iron in die-casting alloys can form Al5FeSi intermetallics, making the oxide skin softer (14). For composite castings via infiltration, breaking the oxide skin is crucial (15, 16).
Purpose of the study:
This research is aimed at studying of certain chemical elements' influence on strength of the oxide skin of aluminum melts. Studying of iron's influence is the most technologically perspective, as iron constantly accompanies commercial aluminum alloys. Using of alloys of Al-Si-Cu system leads to electromechanical corrosion and so is better to be avoided. Thus, alloys of Al-Si–Fe (AlSi9MgFe1) and Al-MSi (AlMg5Si) systems were selected objects of the study.
Core study:
The core of the study involved investigating the influence of chemical elements, specifically magnesium and iron, on the strength of the oxide skin on different aluminum melts (A999, AlMg5Si, and AlSi9MgFe1). This was achieved by using a replicated aluminum foam technique and an experimental setup (Figure 1) to measure the infiltration pressure required to break the oxide skin at the "melt-filler" boundary with varying filler (NaCl) fraction sizes. The study focused on how these elements affect the oxide skin's resistance to melt flow.
5. Research Methodology
Research Design:
To study the oxide skin strength, the pattern close to a production one was used (Figure 1) (15). A test charge of metal was melted in a laboratory muffle–type resistance oven SNOL 1,6.2,5.1/9-13. Temperature control was realized by means of a chromel-alumel thermoelectric converter of K type. The KSBM-345 crucible from fine-disperse melted quartz was used for melting and pouring the metal. NaCl as per GOST R 51574–2000 was used as a filler. A cylindrical iron cast mould (fig. 1, pos. 2) with internal dimensions Ø30x180 mm was heated to 250 °C before each filling. Via a gas-tight damper (fig. 1, pos. 3), the mould was connected with an adapter (fig. 1, pos. 4) of a vacuum unit (fig. 1, pos. 5). Suction was created using a vacuum pump (2NVR–01 DM model), and residual pressure was monitored by a vacuum-meter (fig. 1, pos. 6).
Data Collection and Analysis Methods:
Granulometric analysis of the filler was conducted on a laboratory rotap LPzE-2e with use of standard meshes (0.10–0.20; 0.20–0.32; 0.32–0.63; 0.63–1.0; 1.0–1.5 mm; 1.5–3.0 mm). Both the filler and the melt were heated to 700 °C. Upon pouring of the filler in the crucible, the melt was poured in (fig. 1, pos. 7) with simultaneous opening of the vacuum unit valve. Measuring of infiltration pressure was made by gradual decrease of pressure in the receiver until the leakage threshold occurred which was defined visually by beginning of the melt level drop in the cast mould. Mean arithmetic values of fraction intervals were used in the paper, and the obtained results are presented in Figure 2.
Research Topics and Scope:
The research focused on the strength of oxide skins on aluminum melts, specifically studying alloys A999 (pure aluminum), AlMg5Si (aluminum-magnesium-silicon alloy), and AlSi9MgFe1 (aluminum-silicon-magnesium-iron alloy). The scope included examining the effect of different filler fraction sizes (NaCl particles ranging from 0.10 mm to 3.0 mm) on the infiltration pressure required to rupture the oxide skin. The key elements investigated for their influence on oxide skin strength were magnesium and iron.
6. Key Results:
Key Results:
The study found that for filler fractions under 0.2 mm in size, the infiltration pressure is governed by the Laplace equation. However, as the filler fraction size becomes larger (above a critical size of 0.2 mm), the infiltration pressure remains constant and is determined by the rupture of the oxide skin on the “melt-filler” boundary. This rupture leads to the appearance of a micro crack. The phenomenon of oxide skin rupture being largely independent of filler fraction size above this critical point is attributed to the dense crystalline or amorphous structure of the oxide skin (1).
Impurity elements significantly influence micro crack formation. The addition of magnesium leads to the formation of MgAl2O4 in the skin, which lowers its strength, consistent with previous findings (10). Iron demonstrated the strongest impact on oxide skin strength. When the percentage of iron exceeds 0.8%, it forms an intermetallide of laminar type (Al5FeSi). This intermetallide acts as a stress concentrator, significantly decreasing the minimum infiltration pressure required to rupture the oxide skin. Specifically, the pressure decreased from 20000 MPa on pure aluminum (A999) to 7000 MPa on the AlSi9MgFe1 alloy. This reduction in infiltration pressure can considerably increase the infiltration factor of finished products. The results are graphically represented in Figure 2, showing infiltration pressure versus the average diameter of particles for the different alloys.
Figure Name List:
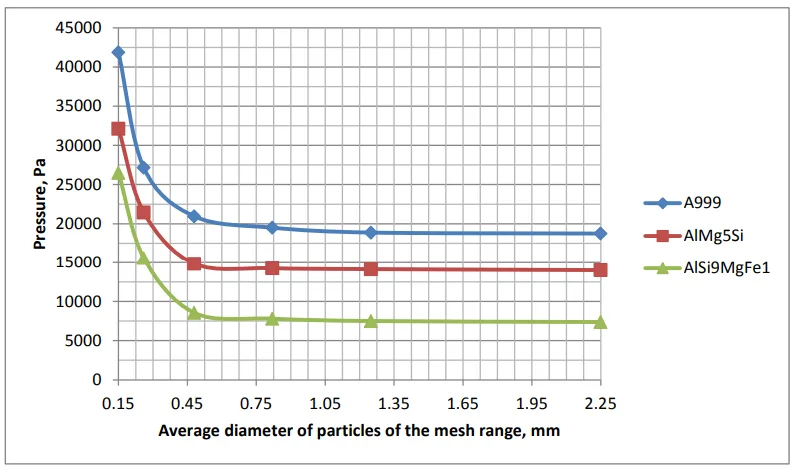
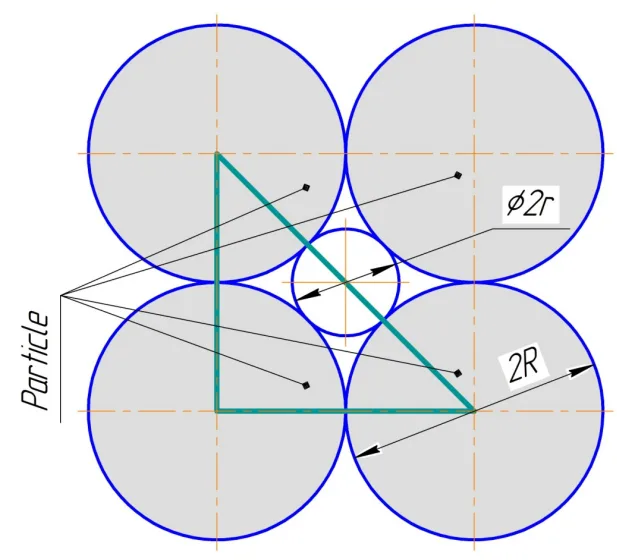
- Fig. 1 - The pattern of studying oxide skin strength.
- Fig. 2 - Infiltration pressure.
- Fig. 3 - Dummy ground model.
7. Conclusion:
In result of studying the issue of strength of oxide skins on aluminum melts surface it was found that use of iron in the alloy renders to the largest lowering of this strength. Iron will form an intermetallide of laminar type (Al5FeSi), which is the most efficient stress concentrator in the oxide skin. Thus, utilization of aluminum alloys with increased iron percentage (over 0.8%) in the replicated aluminum foam technique allows decreasing the minimum infiltration pressure from 20000 MPa on pure aluminum to 7000 MPa on AlSi9MgFel, which ensures a considerable increase of the infiltration factor of finished products, thus expanding the range of their application.
8. References:
- 1. Chalyj VP: Metals' hydroxides (Laws of formation, composition, structure and properties). Kiev, Naukova Dumka, 1972.
- 2. Lepinskih BM, Kitashev AA, Belousov AA: Oxidation of liquid metals and alloys. Moscow, Nauka, 1979.
- 3. Borisevich JuP, Fomichev JuV, Levinter VE: The study of hydrogen interaction with the γ-Al2O3 surface. Journal of Physical Chemistry, 1981, 55 (8), 2149–51.
- 4. Coenen JWE, Linsen BG: Physical and chemical aspects of absorbents and catalysts. London, Academic Press, 1970.
- 5. Finkelstein AB: Replicated aluminum foam, theory and practice – doctoral thesis. Yekaterinburg, Ural State Technical University, 2009.
- 6. Morasch KR, Bahr DF: Nanomechanical testing for fracture of oxide skins. Journal of materials research, 2005, 20 (06), 1490–7.
- 7. Hatch JE: Aluninum: properties and physical metallugry. Cleveland, ASM International, 1984.
- 8. Timofeev GI, Markov VV, Pirjazev VP, Gerasimov AI: Oxidation of aluminum melt upon exposure and casting. Liteinoye proizvodstvo, 1975, 9, 18–9.
- 9. Opie WR, Grant NJ: Hydrogen solubility in aluminum and some aluminum alloys. Transactions AIME, 1950, 188, 1237–47.
- Wang Y, Li HT, Fan ZY, Scamans G: Characterisation of oxide skins in Al-Mg alloy melts. Material Science Forum, 2013, 765, 220–4.
- Mal'cev MV, Chistjakov JuD, Cypin MI: To the question about the structure of the oxide skins in liquid aluminum and it's alloys. Reports of the USSR Academy of Sciences, 1954, 99 (5), 813–5.
- Kurdjumov AV, Inkin SV, Chulkov VS, Grafas NI. Flux treatment and filtration of aluminum melts. Moscow, Metallurgy, 1980.
- Emamy M, Razaghian A, Kaboli S, Campbell J: Statistical analysis of tensile properties of cast A357/Al2O3 MMCs. Materials Science and Technology, 2010, 26 (2), 149–156.
- Data A: NADCA product specification standards for die castings. Arlington Heights, NADCA, 2003.
- Furman EL, Finkelstein AB, Cherny ML: Permeability of aluminum foams produced by replication casting. Metals, 2012, 3 (1), 49–57.
- Furman EL, Finkelstein AB, Cherny ML: The anisotropy of replicated aluminum foams. Advances in Materials Science and Engineering, 2014, 2014.
- Furman EL, Chechulin AV, Finkelstein AB, Kazancev SP: Surface tension of cast aluminium alloys and wetting of inorganic pore-forming fillers therewith. Melts, 1995, 2, 27–31.
- Carman PC: Flow of gases through porous media. London, Butterworths, 1956.
- Furman EL: The creation and improvement of cast composites manufacturing technique based on the study of capillary interaction in the mold – doctoral thesis. Sverdlovsk, Ural State Technical University, 1990.
9. Copyright:
- This material is a paper by "Finkelstein Arcady, Schaefer Arseny, Husnullin Dmitry, Mahmud Zoda Muminjohn". Based on "Strength of oxide skin on aluminum melts".
- Source of the paper: Not available from the provided text.
This material is summarized based on the above paper, and unauthorized use for commercial purposes is prohibited.
Copyright © 2025 CASTMAN. All rights reserved.
Paper Summarize:
Key questions and answers about the research:
This paper investigates the strength of oxide skins on aluminum melts, specifically alloys A999, AlMg5Si, and AlSi9MgFe1, using a replicated aluminum foam technique. The study shows that for small filler fractions (<0.2mm) infiltration pressure follows the Laplace equation, while for larger fractions it's determined by oxide skin rupture, which is largely independent of filler size. Notably, iron content exceeding 0.8% significantly reduces oxide skin strength by forming Al5FeSi intermetallics, lowering infiltration pressure from 20000 MPa in pure aluminum to 7000 MPa in AlSi9MgFe1 alloy.
Q1. What was the main objective of the research "Strength of oxide skin on aluminum melts"?
A1. The main objective was to study the influence of certain chemical elements, particularly iron and magnesium, on the strength of the oxide skin on aluminum melts. (Source: "Strength of oxide skin on aluminum melts", Introduction)
Q2. How does the filler fraction size affect the infiltration pressure in the studied aluminum alloys?
A2. For filler fractions under 0.2 mm, infiltration pressure is governed by the Laplace equation; for larger fractions (above 0.2 mm), it stays constant and is defined by the rupture of the oxide skin. (Source: "Strength of oxide skin on aluminum melts", Abstract, Results and discussion)
Q3. What happens when the oxide skin on the “melt-filler” boundary ruptures?
A3. The rupture leads to the appearance of a micro crack, and the oxide skin growth rate becomes lower than the leak rate of the melt in the evolving channel. (Source: "Strength of oxide skin on aluminum melts", Abstract, Results and discussion)
Q4. What is the effect of magnesium on the oxide skin of aluminum alloys?
A4. The addition of magnesium leads to the formation of MgAl2O4 in the skin, which lowers its strength. (Source: "Strength of oxide skin on aluminum melts", Abstract, Results and discussion)
Q5. Which element has the strongest impact on reducing oxide skin strength, and how?
A5. Iron has the strongest impact; when its percentage exceeds 0.8%, it forms an intermetallide of laminar type (Al5FeSi), which acts as a stress concentrator, significantly decreasing the oxide skin strength. (Source: "Strength of oxide skin on aluminum melts", Abstract, Conclusion)
Q6. By how much can iron reduce the minimum infiltration pressure compared to pure aluminum?
A6. Iron can decrease the minimum infiltration pressure of the oxide skin from 20000 MPa on pure aluminum to 7000 MPa on AlSi9MgFe1 alloy. (Source: "Strength of oxide skin on aluminum melts", Abstract, Conclusion)