This introduction paper is based on the paper "The High Fluidity (HF) Zinc Alloy: Process-Property and Ageing Characteristics" published by "NADCA 2015 Die Casting Congress & Exposition (North American Die Casting Association)".
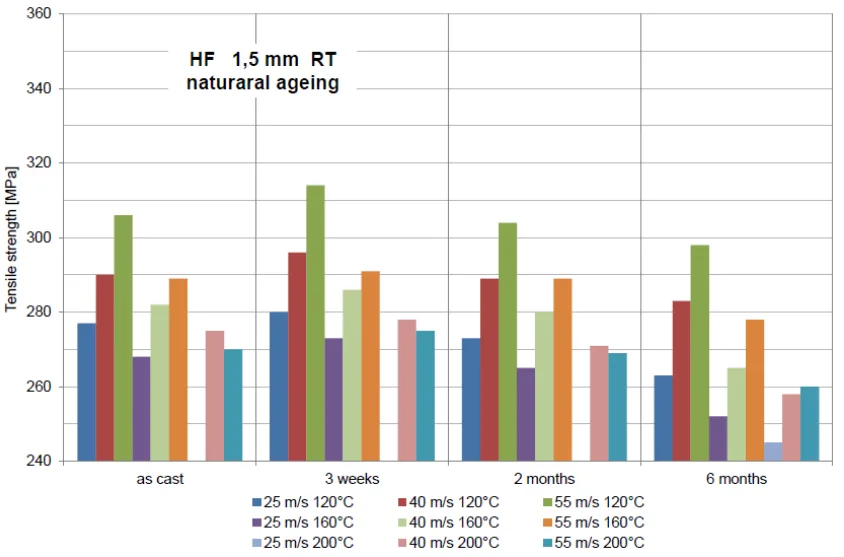
1. Overview:
- Title: The High Fluidity (HF) Zinc Alloy: Process-Property and Ageing Characteristics
- Author: F.E. Goodwin, L.H. Kallien, W. Leis
- Year of publication: January 2015
- Journal/academic society of publication: NADCA 2015 Die Casting Congress & Exposition (North American Die Casting Association)
- Keywords: high fluidity zinc die casting alloys, mechanical properties, die casting process variables, wall thickness, room temperature ageing, artificial ageing (derived from abstract)
2. Abstract:
During the years 2005-2014 a new high fluidity zinc die casting alloys was developed with funding from the USA Department of Energy and the NADCA Technology Administration Group. This alloy has entered commercial production according to the standard specification ASTM B989 and is finding use with wall thicknesses between 0.4 and 3 mm. This paper describes the relationships mechanical properties and most important die casting process variables together with wall thickness. Also, the effects of both room temperature and artificial ageing on mechanical properties are described; behaviors are compared to results previously developed for the traditional zinc die casting alloys.
3. Introduction:
The traditional zinc hot chamber die casting alloys, based on the composition zinc-4% aluminum, have been used to cast both small and large components with wall thicknesses of less than 1 mm (0.04"), thinner than many other competitive casting materials and processes can achieve. During the last few years the HF alloy, based on a composition of zinc-4.5% aluminum, has been shown to exhibit higher casting fluidity than the traditional alloys and has been used to make components with thicknesses as thin as 0.25 mm (.01 inches). Like most other alloys, the HF alloy can be expected to undergo ageing effects after the casting is solidified, because solubility of alloying elements is much higher in the liquid melt than in the primary solid phase. Zinc alloys in particular have the capability of ageing at room temperature because of their low melting point compared with other alloy systems. This ageing is known to be based on diffusion of alloying elements from the primary phase, where they are supersaturated, to existing second phases or to creation of new phases. The rate at which diffusion occurs depends upon the concentration gradient of the alloying elements between the various solid phases and also the distance of the concentration centers in these phases. Past work has given details of ageing phenomena in the conventional zinc alloys. ¹,² The purpose of the current research project, of which the initial results are described in this paper, is to examine the effects of both common die casting process variables on the mechanical properties of the HF alloys, together with the effects of both natural and artificial ageing.
4. Summary of the study:
Background of the research topic:
Traditional zinc hot chamber die casting alloys (Zn-4%Al) can cast thin walls, but the High Fluidity (HF) alloy (Zn-4.5%Al) exhibits even higher casting fluidity, enabling thicknesses as thin as 0.25 mm. Like other alloys, HF alloy undergoes ageing due to the higher solubility of alloying elements in the liquid melt compared to the solid phase, leading to diffusion from the supersaturated primary phase to second phases or new phase creation. Zinc alloys are notable for ageing at room temperature.
Status of previous research:
Previous work (References 1, 2) has detailed the ageing phenomena in conventional zinc alloys. This study builds upon that understanding by focusing on the newer HF alloy.
Purpose of the study:
The primary purpose is to examine the effects of common die casting process variables (such as wall thickness, gate velocity, and die temperature) on the mechanical properties of the HF alloy. Additionally, the study aims to investigate the effects of both natural (room temperature) and artificial ageing on these properties.
Core study:
The research investigates the process-property relationships and ageing characteristics of the HF zinc alloy. This involves:
- Casting test coupons with varying thicknesses (0.4 mm to 3 mm) under different die casting process conditions (gate velocity, die temperature).
- Evaluating the mechanical properties (tensile strength, yield strength, elongation, elastic modulus) of the HF alloy.
- Studying the microstructure of the HF alloy.
- Analyzing the effects of natural ageing (at room temperature for up to 6 months in this reported phase) and artificial ageing (at 65°C, 85°C, 105°C for 24 hours) on the mechanical properties.
- Comparing the behavior of the HF alloy with traditional zinc die casting alloys (Alloys 2, 3, 5, and ZA-8).
5. Research Methodology
Research Design:
An experimental approach was adopted using a design of experiments (DOE) methodology, specifically applying Design-Expert 7 by Stat-Ease, to minimize casting runs. The DOE included center point conditions of 1.5-mm wall thickness, 160°C die temperature, and 40 m/s gate velocity. Flat test coupons were high pressure die cast with thicknesses of 0.4, 0.8, 1.5, and 3 mm.
Data Collection and Analysis Methods:
- Material Preparation: The HF alloy used was covered by ASTM specification B989. Its composition, along with conventional alloys for comparison, is detailed (Table 1 for standard, Table 2 for actual cast compositions). The Mg level in the trial HF alloy was higher than specification but similar to Alloy 3, not expected to significantly influence mechanical properties or ageing, though it could affect fluidity.
- Casting: Test coupons (DIN 50125 Form E) were produced on a Frech DAW 80 hot chamber die casting machine. Nine casting parameters were used: three each for casting section thickness, gate velocity, and die temperature. Sensors monitored pressure and temperature.
- Ageing: Specimens underwent natural ageing at room temperature (results reported up to 6 months) or artificial ageing (24-hour treatment at 65, 85, and 105°C).
- Mechanical Testing: Tensile tests were performed at -35°C, room temperature, and +85°C to determine yield strength, tensile strength, elongation at fracture, and elastic modulus. Only available tensile test results are reported in the paper.
- Microstructural Analysis: The microstructure of the cast alloy was examined (as shown in Figures 1 and 2).
Research Topics and Scope:
- Alloy: High Fluidity (HF) zinc alloy (ASTM B989). Comparisons made with Alloys 2, 3, 5, and ZA-8.
- Process Variables:
- Casting section thicknesses: 0.4, 0.8, 1.5, and 3 mm.
- Gate velocities: Varied (e.g., 25 m/s, 40 m/s, 55 m/s as per Table 3 and Table 5).
- Die temperatures: Varied (e.g., 120°C, 160°C, 200°C as per Table 4 and Table 5).
- Ageing Conditions:
- Natural ageing: As cast, 3 weeks, 2 months, 6 months (longer periods planned).
- Artificial ageing: 24-hour treatments at 65°C, 85°C, 105°C.
- Properties Investigated: Mechanical properties (primarily tensile strength in reported results) and microstructure. The relationship between fill time, solidification time (Chvorinov equation), and casting quality was also considered.
6. Key Results:
Key Results:
- Microstructure: The HF alloy exhibits a layered microstructure, typical of zinc die casting alloys. Near the surface, a columnar primary phase structure is observed under a microcrystalline skin. The interior shows a zinc-rich primary phase with a dendritic microstructure, along with eutectic. The microstructure is very fine, implying short diffusion distances during ageing (Figures 1, 2).
- Room Temperature Ageing:
- Tensile strength is higher for thinner section thicknesses and lower die temperatures (e.g., 120°C).
- Tensile strength generally decreases with increasing natural ageing time (Figures 3, 4).
- Effects of process variables are less pronounced in thicker samples (1.5 mm) compared to thinner ones (0.8 mm).
- Artificial Ageing:
- The tensile strength of HF alloy is consistently lower than that of Alloy 5, attributed to the higher copper content in Alloy 5 (Figure 5).
- The HF alloy is predicted to age in a manner similar to Alloy 3 (Figure 6).
- For a 1.5 mm thickness, a natural ageing time of around 100 days can be simulated by artificial ageing at 65°C for 24 hours (Figure 6).
- Effect of Process Variables on Tensile Strength (As Cast):
- Section Thickness: Has the greatest effect. Halving the section thickness increases tensile strength by approximately 10%.
- Gate Velocity: Increasing gate velocity from the midpoint (40 m/s) to a higher value increases tensile strength by about 3.5%. Decreasing it to 25 m/s reduces tensile strength by about 3.5%.
- Die Temperature: Increasing die temperature from the midpoint (160°C) to 200°C decreases tensile strength by about 4.5%. Decreasing it to 120°C increases tensile strength by about 4.5%.
- These effects are linked to local solidification time (as per Chvorinov equation), fill time, and heat transfer influencing the microstructure. Good quality castings for 0.4mm thickness were only obtained under favorable conditions where fill time exceeded solidification time.
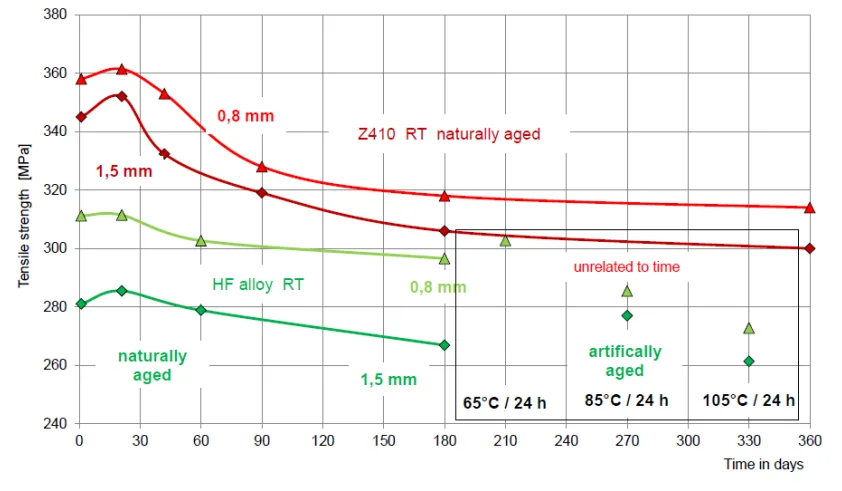
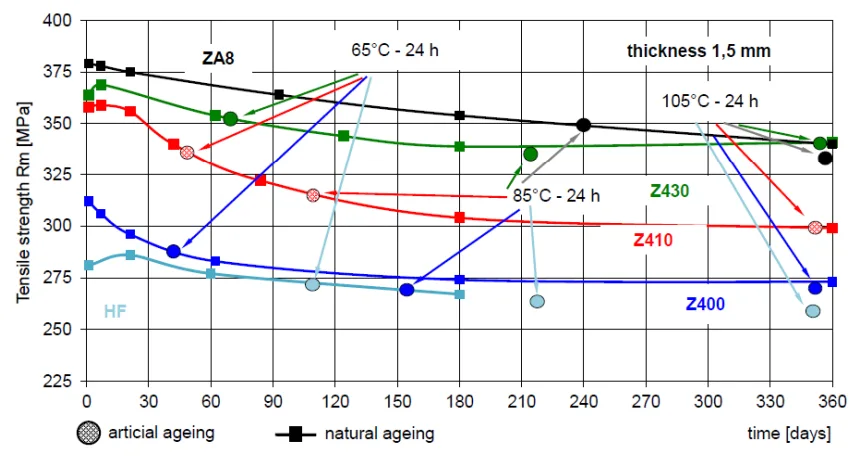
Figure Name List:
- Figure 1. Microstructure of HF alloy at the surface, thickness 0.4 mm, casting conditions 160°C / 55 m/s
- Figure 2. Microstructure of HF alloy in the center of the casting, thickness 0.4 mm, casting conditions 160°C / 55 m/s
- Figure 3. Tensile strength as a function of production parameters through the natural ageing process of HF alloy, wall thickness 0.8 mm, average of 5 specimens
- Figure 4. Tensile strength as a function of production parameters through the natural ageing process of HF alloy, wall thickness 1.5 mm, average of 5 specimens
- Figure 5. Tensile strength as a function of wall thickness through the natural and artificial ageing process of HF alloy, wall thickness 0.8 and 1.5 mm compared with the natural ageing of alloy 5 (Z410)
- Figure 6. Comparison of natural and artificial ageing behavior of the 4 conventional hot chamber zinc die casting
7. Conclusion:
The available results show that the HF alloy responds to ageing in a similar manner to that of the traditional hot chamber zinc die casting alloys. The tensile strength of the HF alloy also responds similarly to changes in section thickness, gate velocity and die temperature. The achievable tensile strength is influenced by alloy content. It can be seen that the lower copper content and high aluminum content reduce the as cast tensile strength regardless of the casting or ageing condition for the HF alloy compared with the traditional zinc alloys. However, this lower strength is offset by the greatly improved castability of the HF alloy, allowing much thinner sections to be achieved. This can be an advantage where reduction of casting mass overrides mechanical property concerns, such as in portable electronics enclosures and similar applications, and also where thin sections are used for other purposes, such as in die cast heat sinks.
8. References:
- 1. F. E. Goodwin, "Ageing Properties of Zinc,” NADCA 2011 Congress, Columbus, OH, September 19-21, 2011.
- 2. F. E. Goodwin, L. H. Kallien, W. Leis, “New Mechanical Properties Data for Zinc Casting Alloys, Proceedings NADCA 2014 Die Casting Congress, Sept. 22-24, 2014, Milwaukee, WI, USA, paper T14-032.
- 3. Friebel, V.R. and Roe, W.P., "Fluidity of Zinc-Aluminum Alloy”, Modern Castings, September 1962, pp. 117-120.
- 4. N. Chvorinov, Giesserei, v. 27, p. 177, 1940
9. Copyright:
- This material is a paper by "F.E. Goodwin, L.H. Kallien, W. Leis". Based on "The High Fluidity (HF) Zinc Alloy: Process-Property and Ageing Characteristics".
- Source of the paper: https://www.researchgate.net/publication/283726224
This material is summarized based on the above paper, and unauthorized use for commercial purposes is prohibited.
Copyright © 2025 CASTMAN. All rights reserved.