This introduction paper is based on the paper "[JIS ADC12 Aluminum Alloy Semi-Solid Slurry Preparation Technology by Applying Mechanical Vibration]" published by "[Materials Transactions]".
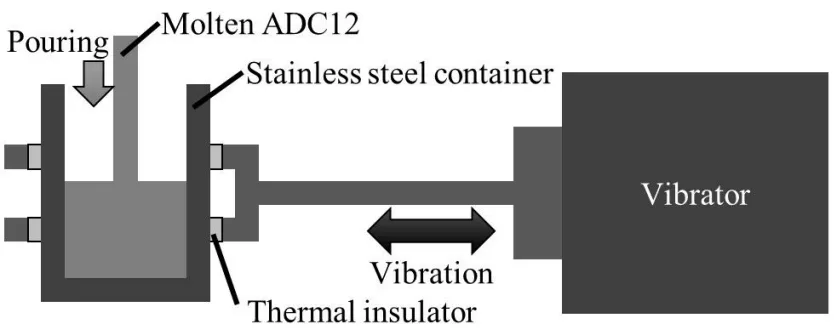
1. Overview:
- Title: JIS ADC12 Aluminum Alloy Semi-Solid Slurry Preparation Technology by Applying Mechanical Vibration
- Author: Yuichiro Murakami, Kenji Miwa, Masayuki Kito, Takashi Honda and Naoki Omura
- Year of publication: 2024
- Journal/academic society of publication: Materials Transactions, Japan Foundry Engineering Society
- Keywords: ADC12 Aluminum Alloy, Semi-solid Process, Semi-solid Slurry, Fraction Solid, Morphology of solid particles, Mechanical vibration
2. Abstract:
Semi-solid high pressure die casting is known as a process capable of forming high quality products. JIS ADC12 aluminum alloy is widely used for high pressure die casting, but this alloy has a narrow semi-solid temperature range, making it difficult to apply the semi-solid process. In this study, the preparation of ADC12 aluminum alloy slurry by applying mechanical vibration was attempted. Mechanical vibration was applied during the solidification of ADC12 alloy from the liquid to semi-solid state, and the effects of parameters of mechanical vibration and pouring temperature on the morphology of slurry have been investigated.
The application of mechanical vibration transformed the solid phase in the slurry from dendritic shape to fine spherical shape with increasing acceleration amplitude and velocity amplitude. As a result, slurry with solid particles dispersed in the liquid phase could be obtained. Moreover, it was found that high frequencies and displacement amplitudes above a certain value are required to obtain slurry with fine spherical solid particles. Fraction solid of slurry was affected by both the pouring temperature and vibration applied time, increasing with decreasing pouring temperature and increasing vibration time. Consequently, slurry with sufficiently fine spherical particles could be obtained by applying mechanical vibration with the frequency of 50 Hz and acceleration amplitude and velocity amplitude higher than 49.0 m/s2 and 0.19 m/s, respectively. In this way, the fraction solid of ADC12 alloy slurry could be controlled by controlling the pouring temperature and vibrations time.
3. Introduction:
Semi-solid high pressure die casting (SS-HPDC) is a forming method that injects metal in a solid-liquid coexisting state into a mold at high velocity. Compared to conventional HPDC which uses metal in a completely liquid state, SS-HPDC can reduce defects caused by air entrainment and smaller solidification shrinkage, leading to improved dimensional accuracy and extended mold life. Furthermore, SS-HPDC is environmentally friendly due to lower process temperatures, requiring less energy compared to conventional HPDC. For optimal fluidity in SS-HPDC, a semi-solid slurry with dispersed solid particles in a liquid state is essential, with finer and more spherical solid particles being desirable for improved general fluidity.
JIS ADC12 Al-Si-Cu-based aluminum alloy, widely used for HPDC in Japan, exhibits a narrow semi-solid temperature range due to its composition close to eutectic. This characteristic, while beneficial for HPDC fluidity, complicates the SS-HPDC process. To mitigate porosity in SS-HPDC, slurries with a 0.3-0.5 fraction solid are preferred, but ADC12 alloy's narrow temperature range (less than 5 deg) makes it generally unsuitable for the semi-solid process. Consequently, SS-HPDC of ADC12 alloy has not been widely adopted.
To address these challenges, a method for preparing semi-solid slurries by applying mechanical vibration was previously developed. This paper further evaluates the method and conditions for obtaining ADC12 alloy slurry with finely dispersed spherical solid-phase particles using mechanical vibration, investigating the effects of vibration parameters and pouring temperature.
4. Summary of the study:
Background of the research topic:
Semi-solid high pressure die casting (SS-HPDC) offers advantages over conventional HPDC, including reduced defects and improved environmental performance. JIS ADC12 aluminum alloy is a common material in HPDC, but its narrow semi-solid temperature range poses challenges for SS-HPDC applications.
Status of previous research:
Prior research indicates that applying mechanical vibration is a promising method for preparing semi-solid slurries. However, the specific vibrational conditions required to produce slurries with fine, spherical solid phases and stable fraction solids in ADC12 alloy were not fully clarified.
Purpose of the study:
This study aims to investigate the preparation of ADC12 aluminum alloy slurry by applying mechanical vibration during solidification. The primary purpose is to determine the effects of mechanical vibration parameters (frequency, acceleration amplitude, velocity amplitude, displacement amplitude) and pouring temperature on the morphology of the slurry and the fraction solid.
Core study:
The core study involves preparing ADC12 aluminum alloy slurry by applying sinusoidal mechanical vibration during cooling. Experiments were conducted to examine the effects of vibration conditions, pouring temperature (T), and vibration time (t) on the morphology of solid-phase particles and fraction solid. The mechanical vibration parameters, including frequency (f), displacement amplitude (d), velocity amplitude (V), and acceleration amplitude (A), were systematically varied. Microstructural analysis and image analysis were used to characterize the morphology and size of solid particles in the prepared slurries.
5. Research Methodology
Research Design:
The research employs an experimental design focused on the preparation of semi-solid ADC12 aluminum alloy slurry using mechanical vibration. Sinusoidal mechanical vibration was applied horizontally to a stainless steel container during the solidification process. The experiment systematically varies mechanical vibration parameters and process temperatures to observe their effects on slurry characteristics.
Data Collection and Analysis Methods:
- Microstructure Observation: Samples were sectioned, polished, etched with 0.5% hydrofluoric acid solution, and observed under an optical microscope to analyze the morphology of the solid phases.
- Image Analysis: Image-Pro Plus 7.0 software was used to measure particle diameter (dp) and particle roundness (R) of the α-Al phase from micrographs. Area-weighted mean values (dps, Rs) were calculated. The fraction solid was determined by calculating the area ratio of the α-Al phase to the total area in micrographs.
Research Topics and Scope:
The research investigates the following topics:
- Effects of vibration parameters on solid-phase shape: Frequency (f), acceleration amplitude (A), velocity amplitude (V), and displacement amplitude (d) were varied to determine their influence on the morphology of solid particles.
- Effects of pouring temperature and vibration time on fraction solid and shape of solid particles: Pouring temperature (T) and vibration time (t) were varied to assess their impact on the fraction solid and the morphology of the solid particles.
6. Key Results:
Key Results:
- Effect of Vibration Parameters on Morphology:
- Applying mechanical vibration transformed the solid phase from dendritic to spherical.
- Increased acceleration amplitude (A) and velocity amplitude (V) resulted in finer and more spherical solid particles.
- High frequencies and displacement amplitudes above certain thresholds were necessary for obtaining slurry with fine spherical solid particles.
- At constant velocity amplitude (V), higher frequency (f) led to larger acceleration amplitude (A) and smaller displacement amplitude (d), influencing particle morphology.
- Effect of Pouring Temperature and Vibration Time on Fraction Solid:
- Fraction solid was influenced by both pouring temperature (T) and vibration time (t).
- Decreasing pouring temperature (T) and increasing vibration time (t) generally increased the fraction solid.
- For short vibration times, higher pouring temperatures resulted in lower fraction solid.
- Fraction solid became constant after vibration time reached 20-25 s.
- Optimal Vibration Conditions:
- Slurry with fine spherical particles was obtained by applying mechanical vibration with a frequency of 50 Hz, acceleration amplitude and velocity amplitude higher than 49.0 m/s² and 0.19 m/s, respectively.
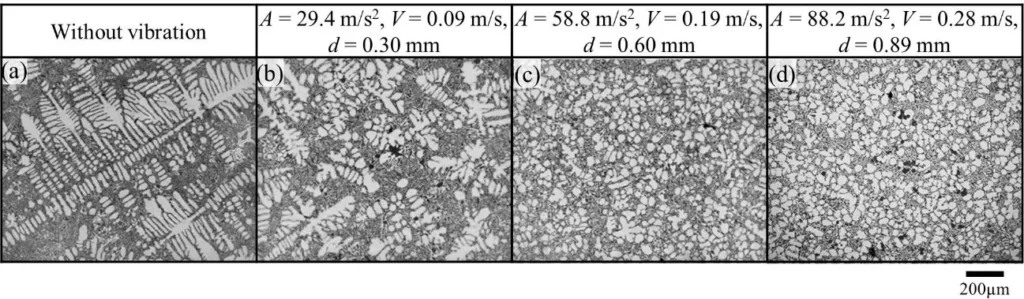
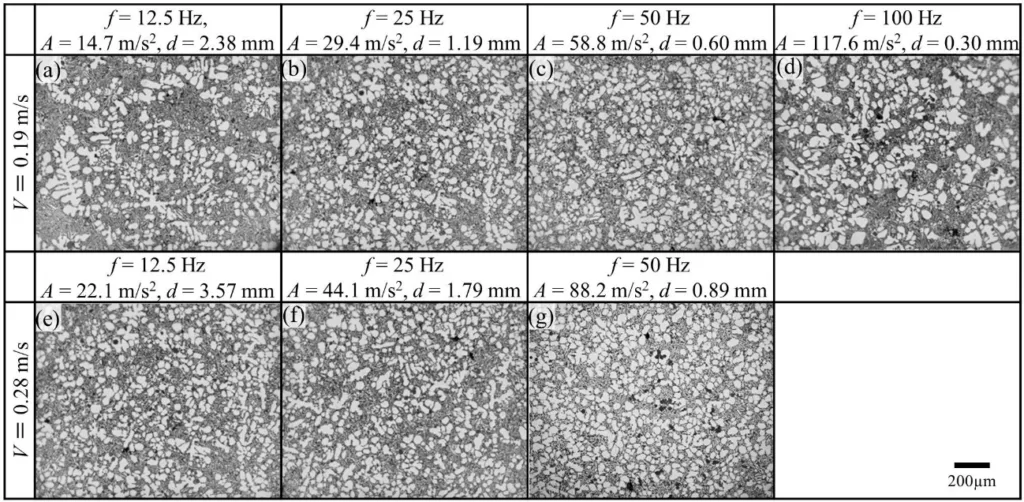
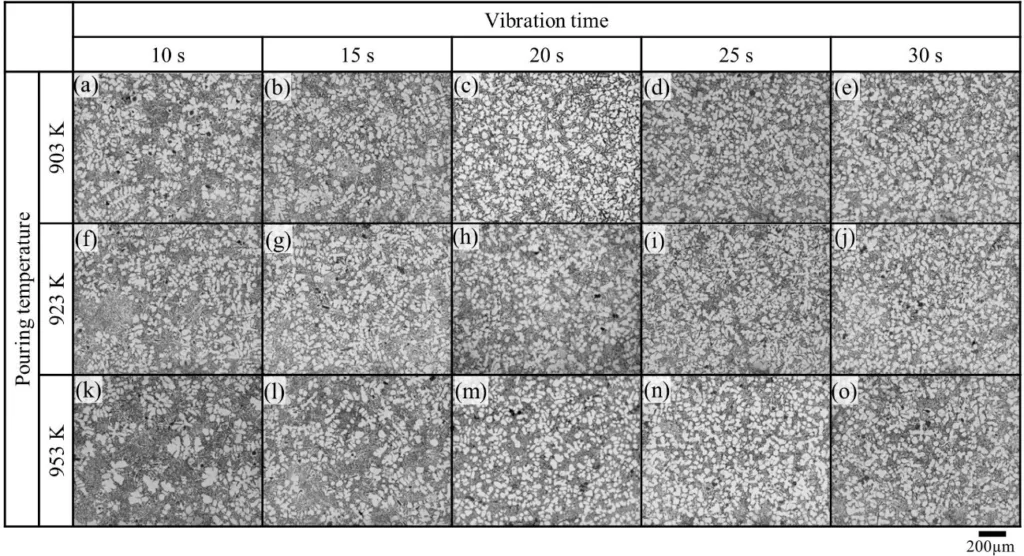
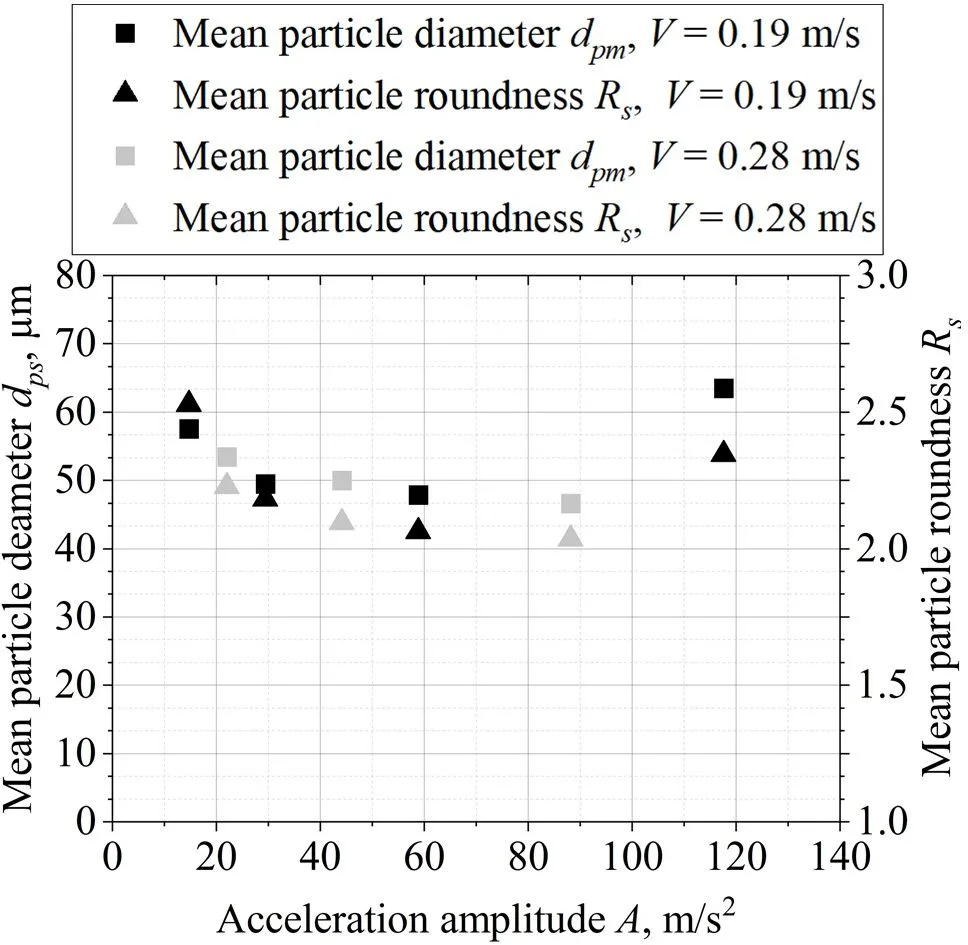
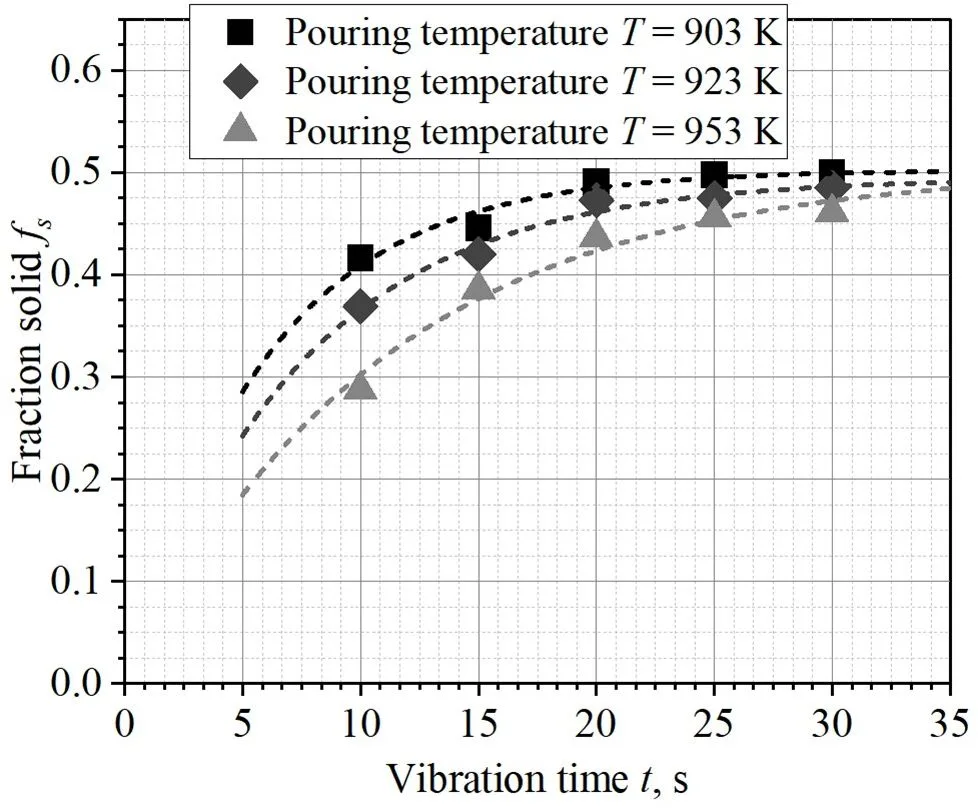
Figure Name List:
- Fig. 1 Schematic representation of experimental apparatus
- Fig. 2 Microstructures of ADC12 alloy slurry. Without vibration and applied mechanical vibration with fixed frequency f = 50 Hz.
- Fig. 3 Microstructures of ADC12 alloy slurry vibrated at same velocity amplitude, but different frequencies and acceleration amplitudes.
- Fig. 4 Microstructures of ADC12 alloy slurry made at various pouring temperatures and vibration times. Vibration frequency and acceleration amplitude 50 Hz, 78.4 m/s².
- Fig. 5 Effects of vibration conditions on mean particle diameter and roundness of α-Al particles at frequency of 50 Hz.
- Fig. 6 Effects of acceleration amplitude on mean particle diameter and roundness of Al particles at same velocity amplitude.
- Fig. 7 Effects of displacement amplitude on mean particle diameter and roundness of Al particles at same velocity amplitude.
- Fig. 8 Effects of pouring temperature and vibration time on area fraction of α-Al particles.
- Fig. 9 Relation between fraction solid and temperature or molar enthalpy of ADC12 alloy.
- Table 1 Chemical composition of JIS ADC12 aluminum alloy used in this study.
- Table 2 Experimental conditions for investigating effects of mechanical vibration on solid particle shape.
7. Conclusion:
This study demonstrated the effectiveness of applying sinusoidal mechanical vibration during cooling for preparing semi-solid slurry of ADC12 aluminum alloy. The key findings indicate that mechanical vibration parameters, particularly acceleration amplitude, velocity amplitude, frequency, and displacement amplitude, significantly influence the morphology of solid-phase particles. Specifically, higher acceleration and velocity amplitudes, along with optimized frequency and displacement, promote the formation of fine, spherical solid particles. Furthermore, the fraction solid of the slurry can be controlled by adjusting the pouring temperature and vibration time. The research concludes that mechanical vibration is a viable technology for producing ADC12 aluminum alloy semi-solid slurry suitable for SS-HPDC, even for skin-forming solidification alloys like ADC12. The study identified optimal vibration conditions (f = 50 Hz, A ≥ 49.0 m/s², V ≥ 0.19 m/s) for achieving desirable slurry characteristics.
8. References:
- 1) M.C. Flemings: Metallurgical Transactions. 5 (1974) 2121-2134.
- 2) M.C. Flemings, J. Yurko and R. Martinez: Solidification Processes and Microstructures (2004) 3-14.
- 3) H.V. Atkinson: Materials Science and Technology. 26 (2010) 1401-1413.
- 4) T. Haga and S. Nishida: PLASTOS. 1 (2018) 39-43.
- 5) H. Fuse: PLASTOS. 1 (2018) 714-718.
- 6) P. Kapranos: Metals. 9 (2019) 1301.
- 7) S. Okano: J. Jpn. Soc. Technol. Plast. 48 (2007) 96-101.
- 8) "Whats diecast". Japan Die Casting Association. https://diecasting.or.jp/diecast/pdf/19-20.pdf, (accessed 2024 01-18).
- 9) Y. Murakami, K. Miwa, N. Omura and S. Tada: Materials Transactions. 53 (2012) 1775-1781.
- 10)Z. Guo, N. Saunders, A.P. Miodownik and J.P. Schillé: Materials Science and Engineering: A. 413-414 (2005) 465-469.
- 11)S. Janudom, T. Rattanochaikul, R. Burapa, S. Wisutmethangoon and J. Wannasin: Transactions of Nonferrous Metals Society of China. 20 (2010) 1756-1762.
- 12)Y. Murakami, K. Miwa, M. Kito, T. Honda, N. Kanetake and S. Tada: Materials Transactions. 57 (2016) 163--167.
- 13)Y. Murakami, K. Miwa, M. Kito, T. Honda, N. Kanetake and S. Tada: Materials Transactions. 54 (2013) 1788-1794.
- 14)Y. Murakami, K. Miwa, M. Kito, T. Honda, N. Kanetake and S. Tada: Materials Transactions. 57 (2016) 168--173.
- 15)Y. Murakami, K. Miwa, M. Kito, T. Honda and N. Omura: Solid State Phenomena. 285 (2019) 333-338.
- 16)H.S. Kim, I.S. Cho, J.S. Shin, S.M. Lee and B.M. Moon: Isij International. 45 (2005) 192-198.
- 17)A. Žukauskas: Advances in Heat Transfer. 8 (1972) 93-160.
- 18)Y. Murakami, K. Miwa, N. Omura and S. Tada: Materials Transactions. 53 (2012) 1775--1781.
- 19)N. Hirata, Y.M. Zulaida, M. Itamura and K. Anzai: Solid State Phenomena. 192-193 (2013) 386-391.
9. Copyright:
- This material is a paper by "Yuichiro Murakami, Kenji Miwa, Masayuki Kito, Takashi Honda and Naoki Omura". Based on "JIS ADC12 Aluminum Alloy Semi-Solid Slurry Preparation Technology by Applying Mechanical Vibration".
- Source of the paper: https://doi.org/10.2320/matertrans.F-M2024810
This material is summarized based on the above paper, and unauthorized use for commercial purposes is prohibited.
Copyright © 2025 CASTMAN. All rights reserved.