This introduction paper is based on the paper "Effects of Trace Variation of Al Content on Microstructure and Properties of HPDC Mg-4Sm-2Al Alloy" published by "Special Casting & Nonferrous Alloys".
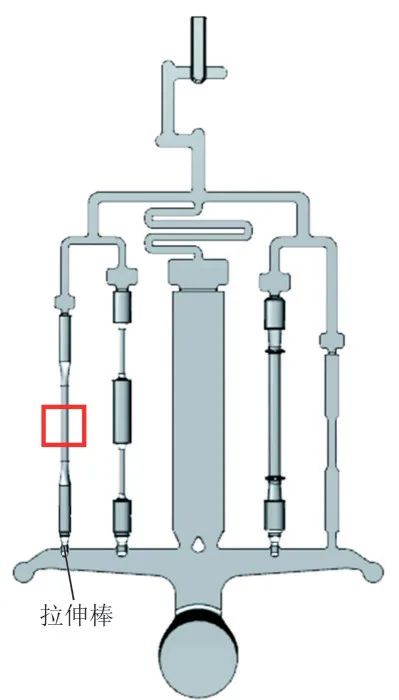
1. Overview:
- Title: Effects of Trace Variation of Al Content on Microstructure and Properties of HPDC Mg-4Sm-2Al Alloy
- Author: LI Zixin¹, CHEN Bin², TONG Shengkun², LU Shiping², LIANG Sheng², HU Bo¹, FU Penghuai¹, PENG Liming¹, LI Dejiang¹, ZENG Xiaoqin¹
- Year of publication: 2025
- Journal/academic society of publication: Special Casting & Nonferrous Alloys
- Keywords: Mg Alloy, Mechanical Properties, Die Casting, Microsturcture
2. Abstract:
SA42 and Mg-4Sm-2.6Al (SA42.6) alloys were fabricated by HPDC process, and influence of trace Al content on mechanical properties was systematically analyzed. The results indicate that with 0.6% Al addition to SA42 alloy, the yield strength and elongation are reduced by 10.2% and 63.5%, respectively, which is attributed to the large quantities of massive Al₂Sm phases generated by reaction between Al and Sm dissolved into the matrix, leading to an approximate 50% reduction in Sm concentration within Mg matrix, significantly diminishing solute strengthening effects. The contributions from secondary phase strengthening as well as grain boundary strengthening provided by formed Al₂Sm can hardly compensate for the loss in solid solution strengthening effect, resulting in an approximate reduction of 20 MPa in yield strength for SA42.6 compared to that of SA42. The substantial decrease in elongation primarily arises from modulus mismatch between Al₂Sm particles and Mg matrix. The brittle and hard Al₂Sm particles induce great stress concentrations during deformation processes, thereby accelerating fracture and failure.
3. Introduction:
Magnesium alloys offer significant potential in the automotive industry due to their low density and high specific strength, finding applications in components like center console back panels, steering wheel frames, instrument panel frames, and LED car lights[1]. With the trend towards highly integrated and high-power components in new energy vehicles, structural materials require good heat dissipation capabilities. Traditional commercial magnesium alloys often have low thermal conductivity. Therefore, developing magnesium alloys with both high thermal conductivity and good mechanical properties is crucial. Mg-RE-Al alloys are common high-thermal-conductivity magnesium alloys. Optimizing alloy composition and element content can reduce solute atoms in the matrix, transforming them into effective strengthening phases, thereby achieving higher thermal conductivity and mechanical properties. High-pressure die casting (HPDC) is a widely used forming process known for its high efficiency, low production cost, and high dimensional accuracy[3-8]. HPDC can effectively refine grains and secondary phases, potentially enhancing the mechanical properties of alloys. Recent trends in integrated die casting ("一体化压铸") are revolutionizing automotive manufacturing, particularly in the new energy vehicle sector, contributing to vehicle lightweighting and production efficiency[9]. This study focuses on understanding how minor variations in Al content affect the microstructure and properties of HPDC Mg-4Sm-Al alloys.
4. Summary of the study:
Background of the research topic:
The automotive industry, especially in the context of new energy vehicles and integrated die casting, requires lightweight materials with both high strength and good thermal conductivity. Mg-RE-Al alloys are promising candidates, but their properties are sensitive to composition.
Status of previous research:
Previous studies on gravity-cast Mg-4Sm-xAl alloys indicated that Al content above 2 wt% yielded favorable thermal conductivity and mechanical properties[2]. Specifically, gravity-cast SA42.6 (Mg-4Sm-2.6Al) showed improved strength and elongation compared to SA42 (Mg-4Sm-2Al), attributed to grain refinement by Al₂Sm particles formed as Al consumed matrix Sm. However, gravity casting produces coarser microstructures than HPDC, which is known to refine grains and phases, potentially leading to different property outcomes.
Purpose of the study:
This research aims to investigate the effect of a minor variation in Al content (0.6 wt%) on the microstructure and mechanical properties of Mg-4Sm-Al alloys produced by the HPDC process. The study seeks to elucidate the strengthening mechanisms and fracture behavior to provide guidance for designing die-cast magnesium alloys.
Core study:
The core of the study involves fabricating SA42 (Mg-4Sm-2.03Al) and SA42.6 (Mg-4Sm-2.42Al) alloys using HPDC. It then systematically compares their microstructures (grain size, phase types and distribution, solute concentration in the matrix) and room-temperature tensile properties (yield strength, ultimate tensile strength, elongation). The study analyzes the contributions of different strengthening mechanisms (solid solution, grain boundary, second phase) and examines the fracture surfaces and cross-sections to understand the reasons for the observed differences in mechanical behavior, particularly the unexpected decrease in strength and ductility with increased Al content in the HPDC process.
5. Research Methodology
Research Design:
A comparative study was designed using two magnesium alloys with slightly different Al contents: SA42 (nominal Mg-4Sm-2Al) and SA42.6 (nominal Mg-4Sm-2.6Al). Both alloys were fabricated under identical HPDC conditions to isolate the effect of the Al variation. Their microstructures and mechanical properties were then characterized and compared.
Data Collection and Analysis Methods:
- Material Preparation: Alloys were prepared using a TOYO/BD-350V5 cold chamber die casting machine under a protective atmosphere (95% N₂ + 0.5% SF₆). Die casting parameters are listed in Table 2. The shape of the casting is shown in Fig.1.
- Composition Analysis: Actual chemical compositions were determined using Inductively Coupled Plasma Optical Emission Spectrometer (ICP-OES, Avio 500) (Table 1).
- Microstructural Characterization: Samples were mechanically ground, polished, and etched (4 mL HNO₃ + 96 mL ethanol, 5 s). Microstructure was observed using a Hitachi SU-70 Scanning Electron Microscope (SEM). Solute content in the matrix was measured using Wavelength-Dispersive Spectrometry (WDS) attached to the SEM (average of at least 10 matrix regions). Grain size and second phase volume fraction were quantified using Image Pro Plus software.
- Mechanical Testing: Room temperature tensile tests were performed on standard specimens (gauge dimensions Φ6.4 mm × 60 mm) using a Zwick/Roell 100 tensile testing machine at a strain rate of 1 mm/min.
- Fracture Analysis: Fracture surfaces and longitudinal cross-sections near the fracture surface (observed via Back-Scattered Electron - BSE imaging) were examined using SEM.
- Strengthening Mechanism Analysis: Contributions from solid solution strengthening (σss), grain boundary strengthening (σgs, Hall-Petch relation), and second phase strengthening (σsp) were calculated using established models (Equations 1-5) based on measured microstructural parameters (solute concentration, grain size, phase fraction).
Research Topics and Scope:
The research focused on the influence of increasing Al content from ~2.0 wt% (SA42) to ~2.4 wt% (SA42.6) in an HPDC Mg-4Sm-Al alloy. The scope included:
- Characterization of the resulting microstructure (phases: Al₁₁Sm₃, Al₂Sm; grain size; Sm solute concentration).
- Measurement of room temperature tensile properties (yield strength, UTS, elongation).
- Analysis of strengthening contributions (σss, σgs, σsp).
- Investigation of fracture mechanisms.
6. Key Results:
Key Results:
- Microstructure: Both SA42 and SA42.6 alloys exhibited fine, equiaxed grains after HPDC. SA42.6 had slightly finer grains (8.2 µm) compared to SA42 (9.1 µm). Both contained rod-like Al₁₁Sm₃ phases at grain boundaries and blocky Al₂Sm phases within grains. However, SA42.6 contained more massive Al₂Sm particles (>2 µm) within the grains (Fig. 2).
- Solute Concentration: The addition of 0.6% Al in SA42.6 led to a significant decrease (approx. 50%) in the concentration of Sm dissolved in the Mg matrix compared to SA42 (Fig. 3b). This is because the added Al reacted with the matrix Sm to form Al₂Sm.
- Mechanical Properties: Contrary to expectations based on gravity casting, increasing Al content from SA42 to SA42.6 via HPDC resulted in a decrease in mechanical properties. Yield strength decreased by 10.2% (from 160.9 MPa to 144.4 MPa), and elongation decreased drastically by 63.5% (from 13.7% to 5.0%) (Fig. 4).
- Strengthening Mechanisms: The primary reason for the reduced yield strength in SA42.6 was the significant loss of solid solution strengthening (σss) due to the depletion of Sm from the matrix (Fig. 5, Table 3). While the formation of Al₂Sm slightly increased grain boundary strengthening (σgs) and second phase strengthening (σsp), these contributions could not compensate for the substantial loss in σss (Table 3). The grain refining effect of Al₂Sm was found to be less potent in HPDC compared to gravity casting, as the particles often did not reach the critical size (>2 µm) needed for significant heterogeneous nucleation under rapid solidification conditions [15-16]. The calculated yield strengths based on these mechanisms showed reasonable agreement with experimental values.
- Fracture Behavior: The dramatic reduction in elongation for SA42.6 was attributed to the presence of the massive, brittle, and hard Al₂Sm particles. A modulus mismatch exists between the Al₂Sm particles (E ≈ 143.95 GPa) and the Mg matrix. During deformation, these particles act as stress concentration sites, leading to early cracking of the Al₂Sm particles and subsequent crack propagation along particle/matrix interfaces or through the matrix, accelerating failure (Fig. 7b). The fracture surface of SA42.6 showed predominantly brittle features associated with cracked Al₂Sm particles, whereas SA42 exhibited more ductile features like dimples and fractured Al₁₁Sm₃ (Fig. 8).
- Fig.1 Die casting specimens
- Fig.2 Microstructures of SA42 and SA42.6 alloys 162
- Fig.3 Volume fraction of secondary phase and solute atomic con⁃
- Fig.4 Engineering stress-strain curves of SA42 and SA42.6
- Fig.5 Solid solution strengthening effect of SA42 and SA42.6
- Fig.6 The secondary phase strengthening effect of SA42 and
- Fig.7 BSE images of section near fracture surface
- Fig.8 Surface morphologies of fracture of SA42 and SA42.6
Figure Name List:
- Fig.1 Die casting specimens
- Fig.2 Microstructures of SA42 and SA42.6 alloys
- Fig.3 Volume fraction of secondary phase and solute atomic concentration in SA42 and SA42.6 alloys
- Fig.4 Engineering stress-strain curves of SA42 and SA42.6 alloys at room temperature
- Fig.5 Solid solution strengthening effect of SA42 and SA42.6 alloys
- Fig.6 The secondary phase strengthening effect of SA42 and SA42.6 alloys
- Fig.7 BSE images of section near fracture surface
- Fig.8 Surface morphologies of fracture of SA42 and SA42.6 alloys
7. Conclusion:
(1) Increasing the Al content by 0.6% in the SA42 alloy (forming SA42.6) leads to the formation of large quantities of massive Al₂Sm phase during HPDC. This reaction significantly reduces the Sm concentration dissolved in the Mg matrix of the die-cast SA42.6 alloy by nearly 50%.
(2) The addition of 0.6% Al substantially diminishes the solid solution strengthening effect in SA42.6. The strengthening contributions from the formed Al₂Sm phase (second phase strengthening and minor grain refinement) are insufficient to compensate for this loss. Consequently, the yield strength of die-cast SA42.6 is approximately 20 MPa lower than that of SA42. The heterogeneous nucleation effect of Al₂Sm particles is not significant under HPDC conditions.
(3) Adding 0.6% Al causes a drastic deterioration in the ductility of the SA42.6 alloy, with elongation decreasing by 63.5%. This is primarily due to the modulus mismatch between the brittle and hard Al₂Sm particles and the Mg matrix. These particles induce significant stress concentrations during deformation, leading to accelerated fracture initiation and failure.
8. References:
- [1] 刘奇峰, 蓝丽招. 铝、镁合金压铸件在汽车工业中的应用及发展[J]. 汽车文摘, 2024(2): 50-55.
- [2] LI Z X, HU B, LI D J, et al. Microstructure-dependent thermal conductivity and mechanical properties in cast Mg-4Sm-xAl alloys [J]. Materials Science and Engineering, 2022, A861: 144 336.
- [3] 罗哲民, 李烈军, 倪东惠, 等. AZ91D超薄笔记本电脑外壳压铸工艺参数优化[J]. 特种铸造及有色合金, 2016, 36(10): 1 057-1 060.
- [4] 张亚琴, 席亚娟, 李远发, 等. 稀土镁合金的散热性能研究[J]. 特种铸造及有色合金, 2015, 35(5): 463-465.
- [5] 陈礼清, 赵志江. 从镁合金在汽车及通讯电子领域的应用看其发展趋势[J]. 世界有色金属, 2004(7): 12-20.
- [6] 李子昕, 张玮宸, 李德江, 等. 真空压铸对LA42镁合金热导率和力学性能的影响[J]. 特种铸造及有色合金, 2023, 43(5): 590-595.
- [7] 付彭怀, 孙启才, 王嘉诚, 等. 真空度对真空压铸镁合金副车架品质的影响[J]. 特种铸造及有色合金, 2023, 43(1): 88-91.
- [8] 王雪杨, 李子昕, 胡波, 等. 真空压铸镁合金减震塔的组织和性能[J]. 特种铸造及有色合金, 2022, 42(4): 467-472.
- [9] 查敏, 顾焘, 马品奎, 等. 轻合金大型一体化结构部件压铸成形技术研究进展[J]. 特种铸造及有色合金, 2024, 44(8): 1 009-1 022.
- [10] YASI J A, HECTOR L G, TRINKLE D R. First-principles data for solid-solution strengthening of magnesium: From geometry and chemistry to properties [J]. Acta Materialia, 2010, 58(17): 5 704-5 713.
- [11] CACERES C H, LUKAC P. Strain hardening behaviour and the Taylor factor of pure magnesium [J]. Philosophical Magazine, 2008, 88(7): 977-989.
- [12] HALL E. The deformation and ageing of mild steel: III discussion of results [J]. Proceedings of the Physical Society, 1951, B64(9): 747-753.
- [13] PETCH N J. The cleavage strength of polycrystals [J]. Journal of Iron and Steel Research International, 1953, 174(19): 25-28.
- [14] CACERES C H, MANN G E, GRIFFITHS J R. Grain size hardening in Mg and Mg-Zn solid solutions [J]. Metallurgical and Materials Transactions, 2011, A42(7): 1 950-1 959.
- [15] QIU D, ZHANG M X. Effect of active heterogeneous nucleation particles on the grain refining efficiency in an Mg-10Y cast alloy [J]. Journal of Alloys and Compounds, 2009, 488(1): 260-264.
- [16] DAI J, EASTON M, ZHU S, et al. Grain refinement of Mg-10Gd alloy by Al additions [J]. Journal of Materials Research, 2012, 27(11): 2 790-2 797.
- [17] ZHANG B, YANG K V, NAGASEKHAR A V, et al. Deformation behavior of the percolating eutectic intermetallic in HPDC and squeeze-cast Mg alloys [J]. JOM, 2014, 66(10): 2 086-2 094.
- [18] SZARAZ Z, TROJANOVA Z, CABBIBO M, et al. Strengthening in a WE54 magnesium alloy containing SiC particles [J]. Materials Science and Engineering, 2007, A462: 225-229.
- [19] TAHREEN N, ZHANG D F, PAN F S, et al. Strengthening mechanisms in magnesium alloys containing ternary I, W and LPSO phases [J]. Journal of Materials Science & Technology, 2018, 34(7): 1 110-1 118.
- [20] NARDONE V C, PREWO K M. On the strength of discontinuous silicon carbide reinforced aluminum composites [J]. Scripta Metallurgica, 1986, 20(1): 43-48.
9. Copyright:
- This material is a paper by "ZENG Xiaoqin". Based on "Effects of Trace Variation of Al Content on Microstructure and Properties of HPDC Mg-4Sm-2Al Alloy".
- Source of the paper: https://doi.org/10.15980/j.tzzz.T20240410
This material is summarized based on the above paper, and unauthorized use for commercial purposes is prohibited.
Copyright © 2025 CASTMAN. All rights reserved.