The content of this introduction paper is based on the article 'Development of Customized Software for Designing Gating System of Compressor Rotor Dies' published by 'NOVATEUR PUBLICATIONS'.
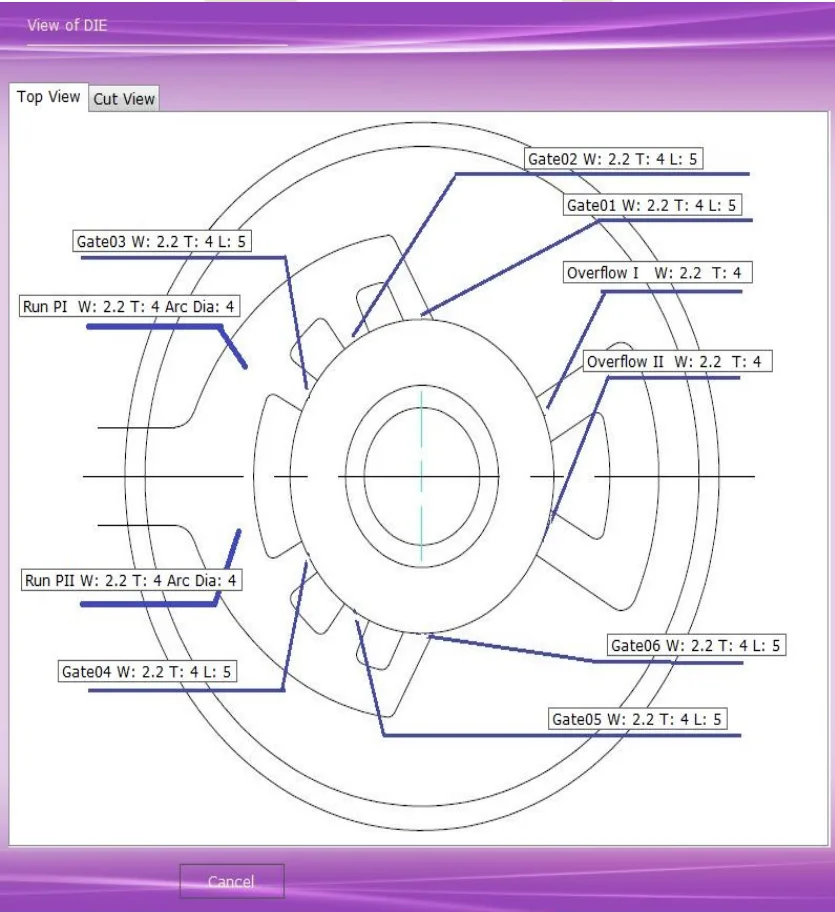
1. Overview:
- Title: Development of Customized Software for Designing Gating System of Compressor Rotor Dies
- Author: SANTOSH RAUT, MARTAND TELSANG, ATUL CHAVAN
- Year of publication: 2015
- Journal/academic society of publication: INTERNATIONAL JOURNAL OF INNOVATIONS IN ENGINEERING RESEARCH AND TECHNOLOGY [IJIERT] (ISSN: 2394-3696, VOLUME 2, ISSUE 4, April-2015)
- Keywords: Gating system, Pressure die casting, Die design, Customized software, Visual C#.
2. Abstract:
An important factor for obtaining defect free pressure die cast parts is good design of the gating system. Gating system is a path of flow of molten alloy during filling of casting. In this project a systematic approach has been developed to design gating system for pressure die casting die. This involved studying current design practices in the industry and translating this into a knowledge base of rules for machine selection, design of gate, gate runner, runner, and overflows. The entire approach has been implemented in a window based program using visual C#. It has been successfully tested on industrial case study. It is perhaps the first attempt of its kind in the area of pressure die casting die design, and is expected to be of significant interest and value to the industry.
3. Summary of the study:
Background of the research topic:
The gating system is crucial for defect-free pressure die-cast parts. It controls the flow of molten metal into the die cavity.
Status of previous research:
Existing design practices rely heavily on experience and established rules, often derived from past performance. No single equation successfully determines optimal gating system design. There's a wide range of literature, but designs are often case-by-case due to variations in casting size and shape.
Purpose of the study:
To develop a systematic, knowledge-based approach for gating system design and implement it in a computer program.
Core study:
The project, named "Diecast," translates industry design practices into a set of rules for machine selection, gate, gaterunner, runner, and overflow design. It's implemented in a Windows-based program using Visual C++.
4. Research Methodology
Research Design:
The research involved breaking down the gating system design process into logical, interdependent steps. Equations and logic for each step were collected and verified.
Data Collection and Analysis Methods:
Data was collected from both literature and industry sources. The system uses a database of material properties and machine parameters stored in a text file format.
Research Topics and Scope:
The research covers the design of the entire gating system, including:
- Computing filling time.
- Selecting gate velocity.
- Establishing gate thickness.
- Determining gate area and its dimensions.
- Calculating runner dimensions.
- Finalizing overflows.
- Machine Setting
5. Key Results:
Key Results:
- A software program ("Diecast") was successfully developed and implemented using Visual C++.
- The software calculates gating system dimensions and machine settings.
- The software was tested on an industrial case study, producing rotors with improved dimensional accuracy and surface finish compared to previous methods.
- The software uses a modular design, with modules for gate, gaterunner, runner, overflow, and machine settings.
- Sample calculations are provided, demonstrating the software's output. For example:
- Cavity Filling Time (t) = K*T*(Ti-Tf+SZ) / (Tf-Td) = 0.08671 Sec
- Gate Area (Ga) = GA= W/ (g*t*Gv) = 155.9 mm 2.
- Gate Thickness (Gt) = Gate Thickness Factor * Casting Avg. Thickness = 4.0 mm.
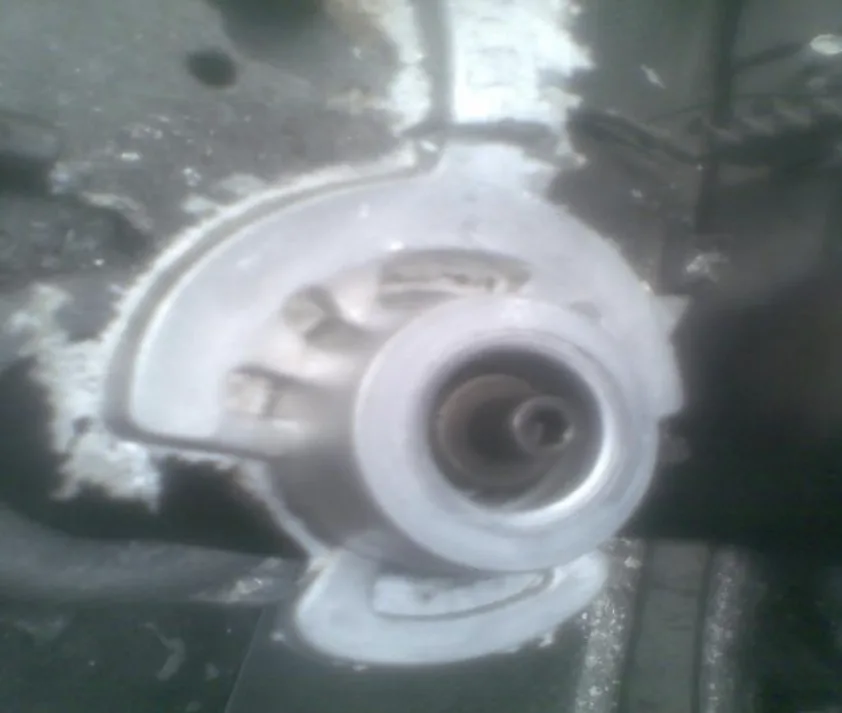
Figure Name List:
- Fig.1. Pressure Die Casting Machine.
- Fig. Different Gating Model Screen
- Fig. Top View Output parameters of software.
- Fig. Side View Output parameters of software.
- Fig. Output parameters of software.
- Fig. Gating System with Rotor.
6. Conclusion:
Summary of Key Results:
The "Diecast" software successfully implements a knowledge-based approach to gating system design for pressure die casting. It uses established design rules and has been validated through an industrial case study.
7. Future Follow-up Research:
- Directions for Follow-up Research:
The paper does not explicitly state any limitations. - Areas for Further Exploration:
The paper does not explicitly state any limitations.
8. References:
- [1] Wallace J F, “Gating of Die Casting”, AFS Transcations, vol 73, 1965, pp 569-580.
- [2] Russ Van Ress, “Gating Diecasting Dies”, North American Diecasting Association, 1996.
- [3] Davis A J, “Tapered runners gating thin gates”, Transcations Society Diecasting casting Engineers, 1979, paperG-T79-052.
- [4] Makelskji M F, “Gating system for Pressure die casting”, Russian casting Production, September 1976, pp 413-416.
- [5] Rodionow E M, “Influence of gating system on quality of pressure die casting”, Russian Casting Production, September 1974, pp No. 397.
- [6] Davis A J, “Some consequences of the relationship between the flow of molten metal in gate systems and the concurrent flow of hydraulic fluid in die casting machines”, Transcation Society Diecasting Engineers, 1975, Paper G-T75-1224.
- [7] Draper A B, “Effect of vent and gate areas on the porosity of diecastings”, AFS Transactions, vol 75, 1967, pp. 727–734.
- [8] Sheptak N, “Water analogy study of fluid flow in the cold chamber”, AFS Transactions, vol 71, 1963, pp 349 – 357.
- [9] Chen C W, “Numerical simulation of filling pattern for an industrial diecasting & its comparison with the defects distribution of an actual casting”, AFS Transactions, vol 102, 1994, pp 139 – 146.
- [10] Hwang W S, “Computer simulations for the filling of castings”, AFS Transactions, vol 95 , 1987, pp 425 – 431
- [11] Estrin Len, “A deeper look at casting solidification software”, Modern casting, July 1994, pp 20 – 23.
- [12] Sloane David J, “Relationship between machine clamp and casting area in aluminum diecasting”, AFS Transactions, vol 70, 1963, pp 442 – 448.
9. Copyright:
- This material is a paper by "SANTOSH RAUT, MARTAND TELSANG, ATUL CHAVAN". Based on "Development of Customized Software for Designing Gating System of Compressor Rotor Dies".
- Source of the paper: [The paper does not include a DOI URL.]
This material is summarized based on the above paper, and unauthorized use for commercial purposes is prohibited.
Copyright © 2025 CASTMAN. All rights reserved.