This introductory paper is the research content of the paper "Influence of microstructure on the corrosion of diecast AZ91D" published by Pergamon.
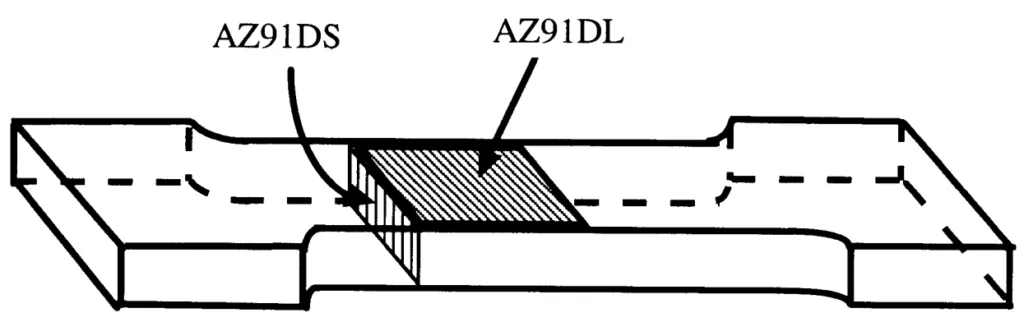
1. Overview:
- Title: Influence of microstructure on the corrosion of diecast AZ91D
- Author: Guangling Song, Andrej Atrens, Matthew Dargusch
- Publication Year: 1999
- Published Journal/Society: Corrosion Science
- Keywords: Magnesium alloys; AZ91D; Diecasting; Corrosion; Microstructure
2. Abstract
The corrosion of die cast AZ91D was studied and related to its microstructure. For comparison and to more fully understand the behaviour of die cast AZ91D, corrosion studies and microstructural examinations were also carried out using slowly solidified high purity AZ91, Mg-2%Al, Mg-9%Al, low purity magnesium and high purity magnesium. Corrosion was studied in 1N NaCl at pH 11 by (1) observing the corrosion morphology, (2) measuring electrochemical polarisation curves and (3) simultaneously measuring both the hydrogen evolution rate and the magnesium dissolution rate. The skin of the die cast AZ91D showed better corrosion resistance than the interior. This is attributed to a combination of (1) a higher volume fraction of the β phase, (2) a more continuous β phase distribution around finer α grains, and (3) lower porosity in the skin layer than in the interior of the die casting. This study showed that the casting method can influence the corrosion performance by its influence on the alloy microstructure. © 1999 Elsevier Science Ltd. All rights reserved.
3. Research Background:
Background of the research topic:
Casting, particularly die-casting, is a common method for producing magnesium alloy components. Magnesium alloy diecastings are used in non-load bearing applications and structural parts in automobiles. Alloy AZ91 is a popular magnesium casting alloy, with high purity grades being corrosion resistant.
Status of previous research:
AZ91 has a two-phase microstructure [1] of α grains and β phase (Mg17Al12) along the α grain boundaries [1]. The detailed microstructure is determined by casting method and heat treatments, varying for different types of casting and regions. The chemical composition and distribution of constituent phases are believed to be responsible for corrosion behavior, but haven't been studied in detail.
Need for research:
It is important to examine the reasons for the corrosion behavior of die cast AZ91, and there is a lack of detailed study on the influence of chemical composition and distribution of constituent phases on the corrosion behavior.
4. Research purpose and research question:
Research purpose:
To reveal the influence of microstructure on the corrosion performance of AZ91 die casting.
Core research:
Investigating the relationship between the microstructure and corrosion behavior of die-cast AZ91D, compared with slowly solidified high-purity AZ91 and other Mg-Al alloys.
5. Research methodology
- Research Design: Comparative experimental study.
- Data Collection Method:
- Microstructural examination using XRD, SEM, and optical microscopy.
- Corrosion studies in 1N NaCl at pH 11:
- Observation of corrosion morphology.
- Measurement of electrochemical polarization curves.
- Simultaneous measurement of hydrogen evolution rate and magnesium dissolution rate using Gas collection and inductively coupled plasma atomic emission spectroscopy (ICPAES).
- Analysis Method:
- Comparison of corrosion morphologies and rates between different samples and regions.
- Analysis of polarization curves.
- Correlation of microstructural features (grain size, β phase distribution, porosity) with corrosion behavior.
- Research materials:
- Die-cast AZ91D, slowly solidified high-purity AZ91 (H.P.AZ91), Mg-2%Al, Mg-9%Al, low-purity magnesium, and high-purity magnesium.
- Samples were prepared with different surface orientations (AZ91DS: cross-section; AZ91DL: flat surface). (Fig. 1)
- Chemical compositions were determined by ICPAES (Table 1).
6. Key research results:
Key research results and presented data analysis:
- The skin of die-cast AZ91D exhibited better corrosion resistance than the interior.
- Corrosion rates (hydrogen evolution and Mg dissolution) varied with applied current density (Fig. 10, Fig. 11).
- Polarization curves showed differences between alloys with varying aluminum content and purity levels (Fig. 12).
- The negative difference effect (NDE) was observed and correlated with corrosion resistance.
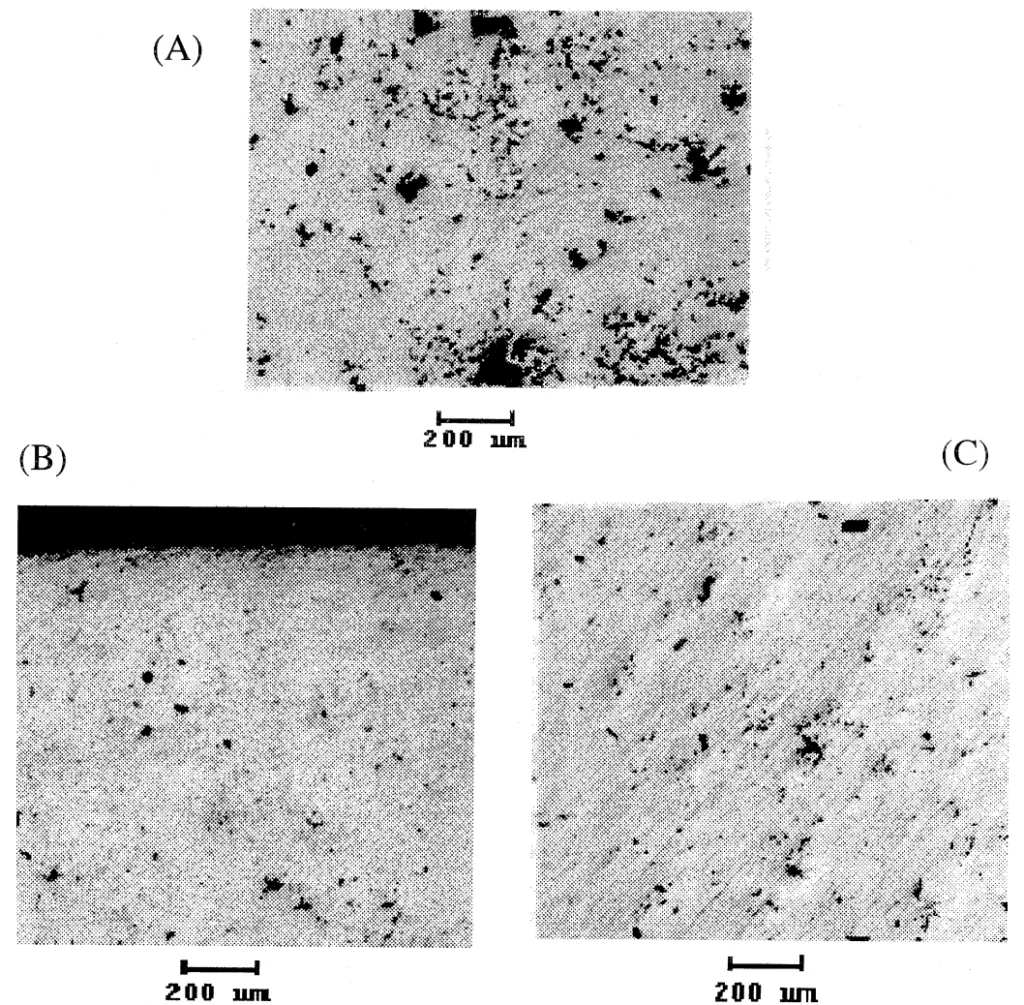
perpendicular to the tensile direction of the tensile sample[ "B# AZ80DS\ edge area[ The surface is
perpendicular to the tensile direction of the tensile sample[ "C# AZ80DL\ central area[ The surface is
parallel to the tensile direction of the tensile sample.
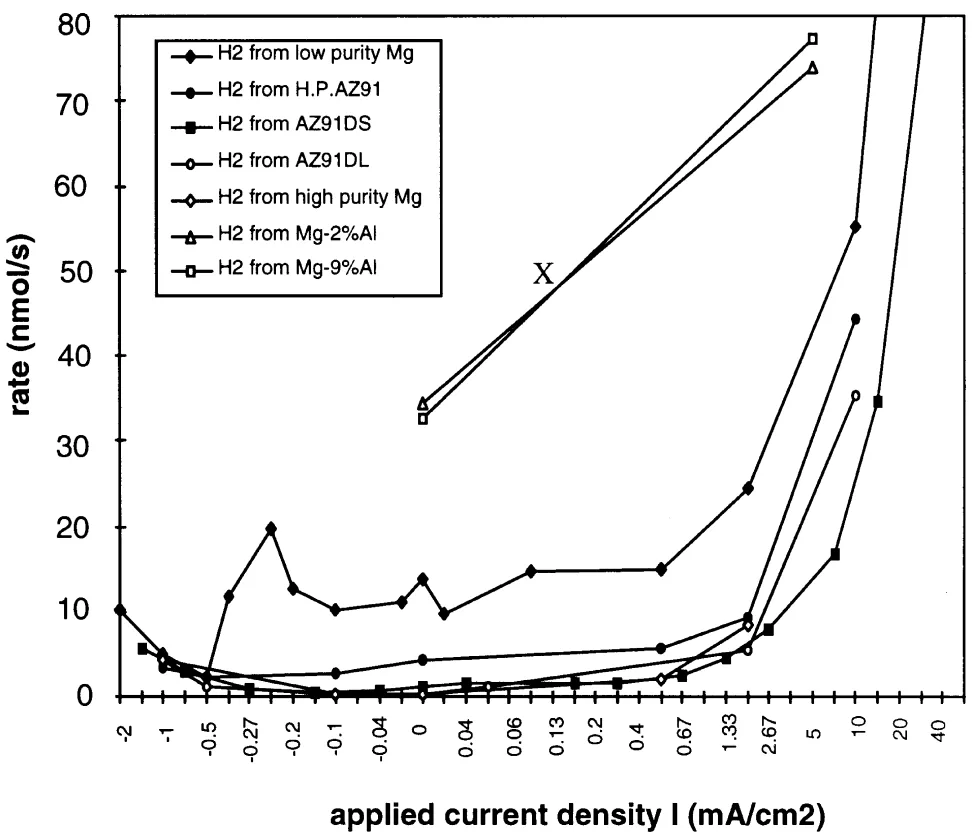
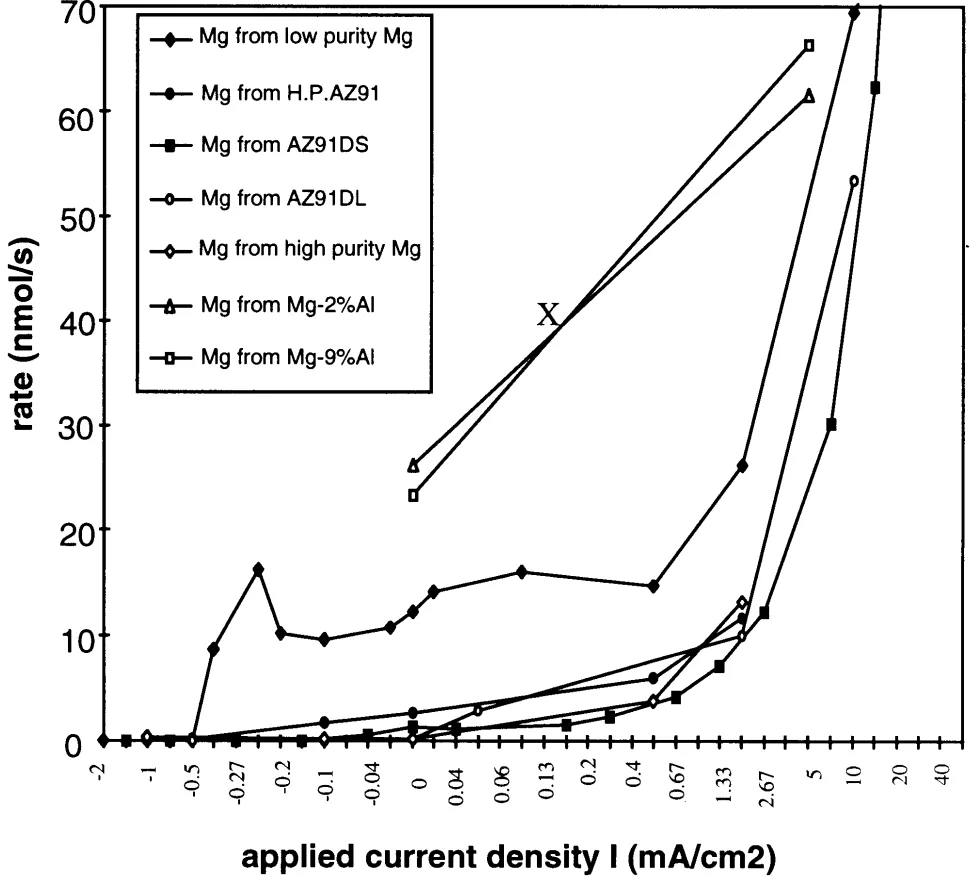
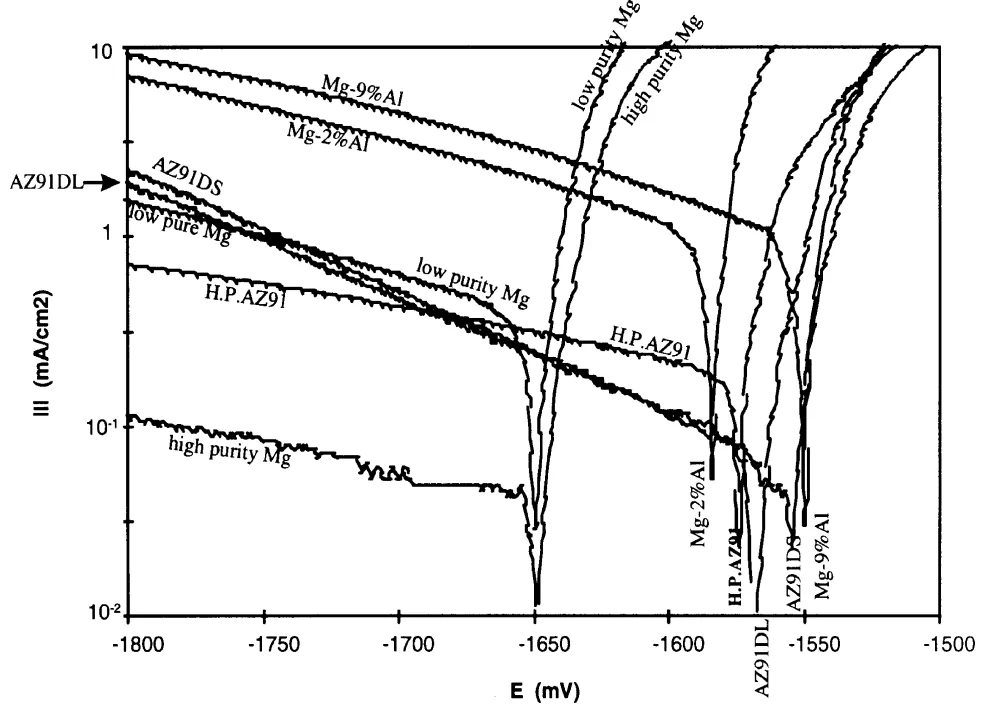
List of figure names:
- Fig. 1. Schematic presentation of the location of samples AZ91DL and AZ91DS taken from the tensile sample.
- Fig. 2. Optical micrographs of die cast AZ91D before etching.
- Fig. 3. Optical microstructures after etching of different sections of diecast AZ91D alloy.
- Fig. 4. Optical mircrostructure of diecast AZ91D alloy.
- Fig. 5. Back scattered SEM images of die cast AZ91D.
- Fig. 6. Back scattered SEM image of H.P.AZ91.
- Fig. 7. Micro-corrosion morphologies of H.P.AZ91 in 1 N NaCl at pH 11 at typical locations A,B,C and D.
- Fig. 8. Micro-corrosion morphologies of AZ91D in 1 N NaCl at pH 11 at typical locations A,B,C and D.
- Fig. 9. Typical micrographs for two different corrosion morphologies of die cast AZ91DS after a few minutes of half immersion in 1 N NaCl (pH= 11).
- Fig. 10. Hydrogen evolution rate for magnesium alloys at different applied current densities.
- Fig. 11. Metal dissolution rates for magnesium alloys at different applied current densities.
- Fig. 12. Polarization curves for magnesium allpys in 1 N NaCl (pH = 11).
- Fig. 13. Schematic presentation of the change of surface composition during corrosion for an alloy with nearly continuous β phase over its surface layer.
- Fig. 14. Schematic presentation of the corrosion caused by the galvanic effect between the β phase and the primary or eutectic α.
7. Conclusion:
Summary of key findings:
- The corrosion behavior of diecast AZ91D is determined by its microstructure, including composition, porosity, grain size, and β phase distribution.
- Faster solidification leads to smaller grain size, more β phase, and a more finely distributed β phase.
- The casting method influences corrosion performance through its control on microstructure.
- The skin of die-cast AZ91D has better corrosion resistance due to higher β fraction, more continuous β phase, finer α grains, and lower porosity.
- The β phase can act as a barrier or galvanic cathode.
- The α phase's corrosion behavior depends on aluminum content and local current density.
- Diecast AZ91D showed the negative difference effect (NDE).
- Anodic polarization curves did not show Tafel behavior, while cathodic polarization curves did.
Summary of research results.
- The microstructure of diecast AZ91D alloy is significantly influenced by the solidification rate, which in turn affects its corrosion resistance.
- The study provides a detailed understanding of the relationship between microstructure and corrosion in die-cast AZ91D, highlighting the importance of solidification control.
- The findings suggest that the original surface of a die casting should not be machined, as the casting skin is more protective.
8. References:
- [1] C. Suman, The effects of direct aging on mechanical properties and corrosion resistance of diecast magnesium alloys AZ91D and AM60B, SAE Transactions 99 (5) (1990) 849.
- [2] W.P. Sequeira, G.L. Dunlop, M.T. Murray, Effect of section thickness and microstructure on the mechanical properties of high pressure die cast magnesium alloy AZ91D, in: G.W. Lorimer (Ed.), Proceedings of the Third International Magnesium Conference, The Institute of Materials, Manchester, UK, 1996, p. 63.
- [3] G.L. Maker, J. Kruger, International Materials Reviews 38 (3) (1993) 138.
- [4] J.D. Ganawalt, C.E. Nelson, J.A. Peloubet, Corrosion studies of magnesium and its alloys, Trans. Am. Inst. Mining Met. Eng. 147 (1942) 273.
- [5] K.N. Reichek, K.J. Clark, K.E. Hills, in: Int. Cong. and Exposition, Society of Automotive Engineers, paper No. 850417, 1985.
- [6] J.E. Hillis, S.O. Shook, Composition and performance of an improved magnesium AS41 Alloy, SAE Technical Paper Series #890205, Detroit, 1989.
- [7] W.P. Sequeira, M.T. Murray, G.L. Dunlop, D.H. St John, Effect of section thickness and gate velocity on the microstructure and mechanical properties of high pressure die cast magnesium alloy AZ91D. Automotive Alloys, A Special symposium—TMS Annual Meeting and Exhibition, Orlando, Florida, February 9–13, 1997.
- [8] E.H. Adolf Beck, The technology of magnesium and its alloys, trans. The technical staffs of F.A. Hughes and Co. Ltd and Magnesium Elekton Ltd of Magnesium und seine Legierungen. London, Chapter 3, 1940.
- [9] S.K. Das, L.A. Davis, Mater. Sci. Eng. 98 (1988) 1.
- [10] O. Lunder, J.E. Lein, T. Kr. Aune, K. Nisancioglu, Corrosion 45 (9) (1989) 741.
- [11] G.L. Makar, J. Kruger, K.J. Sieradzki, Electrochem. Soc. 139 (1) (1992) 47.
- [12] G. Song, A. Atrens, X. Wu, B. Zhang, Submitted to Corrosion Science.
- [13] G. Song, A. Atrens, D. St John, X. Wu, J. Nairn, Anodic dissolution of magnesium in chloride and sulphate solutions, Corrosion Science 39 (10–11) (1997) 1981.
- [14] G. Song, A. Atrens, D. St John, J. Nairn, Y. Li, Corrosion Science 39 (5) (1997) 855.
- [15] J. Campbell, Castings, Butterworth Heinemann, 1991.
9. Copyright:
- This material is a paper by "Guangling Song, Andrej Atrens, Matthew Dargusch": Based on "Influence of microstructure on the corrosion of diecast AZ91D".
- Source of paper: DOI: 10.1016/S0010-938X(98)00121-8
This material was created to introduce the above paper, and unauthorized use for commercial purposes is prohibited. Copyright © 2025 CASTMAN. All rights reserved.