This introduction paper is based on the paper "Process Control and Thixoforming of Cu Rotor for High Efficiency Motors" published by "Transactions of Materials Processing".
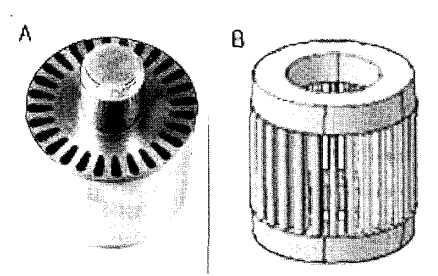
1. Overview:
- Title: Process Control and Thixoforming of Cu Rotor for High Efficiency Motors
- Author: W. S. Jung, S. Y. Lee, P. W. Shin
- Year of publication: 2005
- Journal/academic society of publication: Transactions of Materials Processing (한국소성가공학회지)
- Keywords: Cu Rotor, Thixoforming, Semi-solid Metal Forming, High Conductivity Copper Alloy, SIMA Process, Cu-Ca Alloy
2. Abstract:
Rotor in small-medium induction motor has been usually manufactured by aluminum diecasting. In order to improve the efficiency of induction motors, newly developed Cu-Ca alloys have been investigated. The electrical conductivity in the Cu alloys containing Ca less than 1.0wt% was higher than 80% IACS. Cu-Ca alloy is desirable for the thixoforming process because it has wide semi-solid range over 150°C. In this study, Cu-rotor with thixoforming process was developed to replace the conventional aluminum diecasting rotor. Analysis was performed for the microstructure of thixoforming rotor. Effect of incomplete filling on the efficiency of induction motor was discussed.
3. Introduction:
Electric motors convert electrical energy into mechanical energy via rotor rotation and are widely used in homes and industry. With increasing energy demand, improving motor efficiency is crucial, as 7-25% of energy is lost during conversion, depending on the motor type. Induction motor efficiency is significantly influenced by the electrical conductivity of the rotor. Currently, rotors for small-to-medium motors are commercially produced by die-casting pure aluminum due to its low cost, ease of manufacturing complex shapes, and longer mold life compared to copper alloy die-casting. However, aluminum's electrical conductivity is only about 60% that of pure copper. Replacing aluminum with high-conductivity copper alloys is desirable for enhancing motor efficiency. Copper alloys offer high room/high-temperature strength, fatigue resistance, and creep resistance, enabling the production of energy-efficient, durable, and high-performance motors. However, copper die-casting faces challenges due to copper's high melting point (1083°C), which causes severe mold wear and limits economical mold life [2]. Thixoforming, a semi-solid metal forming process widely used for Al and Mg alloys, offers a solution. Forming occurs in the semi-solid (solid-liquid coexistence) region, at temperatures potentially over 100°C lower than liquidus, reducing mold wear and casting defects compared to die-casting. This study utilizes Cu-Ca alloys, known for their wide semi-solid range, and employs the SIMA (Strain Induced Melt Activated) process to create a globular microstructure suitable for thixoforming. The research focuses on process control for thixoforming high-efficiency motor rotors and discusses the impact on motor efficiency based on prototype testing.
4. Summary of the study:
Background of the research topic:
There is a growing need for high-efficiency electric motors to reduce energy consumption. Standard induction motor rotors are made by aluminum die-casting, which limits efficiency due to aluminum's lower electrical conductivity compared to copper. While copper offers superior conductivity and mechanical properties, conventional die-casting of copper is problematic due to its high melting point leading to rapid mold degradation.
Status of previous research:
Aluminum die-casting is the established method for rotor production. Thixoforming (semi-solid metal forming) is a known technique applied to Al and Mg alloys to reduce processing temperatures and defects compared to die-casting. Research has explored Cu-Ca alloys for their properties, including electrical conductivity and semi-solid characteristics [3]. The SIMA process is recognized as a method to obtain the necessary globular microstructure for thixoforming [4-5].
Purpose of the study:
The study aimed to develop a copper rotor using the thixoforming process with a Cu-Ca alloy to replace conventional aluminum die-cast rotors, thereby improving induction motor efficiency. The research focused on controlling the thixoforming process variables, analyzing the resulting microstructure and filling characteristics, and evaluating the effect of these factors on the final motor efficiency.
Core study:
The core of the study involved:
- Selecting a suitable Cu-Ca alloy (Cu-0.5%Ca) based on electrical conductivity and processability (Table 1).
- Applying the SIMA process (specifically, 15% compressive prestrain followed by reheating to 1050°C) to achieve a fine, globular microstructure suitable for thixoforming (Fig 1.1, Fig 1.2).
- Developing and optimizing the thixoforming process for a 3HP motor rotor using an 800ton press, including billet heating (~1075°C via induction), die preheating (400°C), and forming parameters (Fig 3).
- Investigating and mitigating filling defects like back-filling and porosity observed in initial trials (Fig 4, Fig 5).
- Controlling process parameters, particularly billet heating (temperature uniformity, asymmetric heating profile - Fig 6) and billet geometry (Fig 9), to improve formability and reduce defects.
- Evaluating the internal soundness of formed rotors using non-destructive testing (RT) (Fig 7).
- Measuring the efficiency of the thixoformed Cu-rotors (Fig 8) and comparing it to standard Al D/C rotors (Fig 10).
5. Research Methodology
Research Design:
The study employed an experimental approach. It started with material selection (Cu-Ca alloys) and preparation using Vacuum Induction Melting (VIM) and the SIMA process. Thixoforming trials were conducted on a 3HP rotor geometry, varying process parameters like heating conditions and billet shape. Defect analysis involved visual inspection, sectioning, and microscopy. Non-destructive testing (RT) was used to assess internal quality. Finally, the efficiency of the produced Cu-rotors was measured and compared against baseline aluminum die-cast (Al D/C) rotors.
Data Collection and Analysis Methods:
- Material Preparation: VIM for initial Cu-Ca billet casting. Compression testing for applying prestrain in the SIMA process.
- Microstructure Control: Heat treatment following prestrain. Grain size measurement using optical microscopy (Fig 1.1).
- Thixoforming: 50kW induction heating for billets with thermocouple monitoring (Fig 6). 800ton hydraulic press for forming (Fig 3).
- Defect Analysis: Visual inspection, sectioning of rotors, optical microscopy to examine microstructure in filled and unfilled regions (Fig 5). Radiographic Testing (RT) for non-destructive evaluation of internal filling (Fig 7).
- Performance Measurement: Electrical conductivity measurement of alloys (Table 1, Fig 1.2). Motor efficiency testing of final rotor prototypes (Fig 10).
Research Topics and Scope:
The research focused on the thixoformability of Cu-Ca alloys, specifically Cu-0.5%Ca, for producing induction motor rotors. It investigated the application of the SIMA process to achieve a suitable semi-solid microstructure. The scope included optimizing thixoforming parameters (heating temperature, heating profile, billet geometry) for a specific 3HP rotor design (Fig 2). The study analyzed common filling defects (Fig 4) and their relationship to process parameters and microstructure (Fig 5). The ultimate scope was to demonstrate the feasibility of producing higher efficiency Cu-rotors via thixoforming compared to conventional Al D/C rotors.
6. Key Results:
Key Results:
- Cu-Ca alloys with Ca content below 1.0wt% exhibited electrical conductivity higher than 80% IACS, with lower Ca content yielding higher conductivity (Table 1). Cu-0.5%Ca (95.1% IACS) was selected for the study.
- The SIMA process, involving compressive prestrain (>15%) followed by heat treatment (1050°C for 4 minutes), successfully produced fine, globular microstructures suitable for thixoforming in Cu-0.5%Ca alloy (Fig 1.1). Electrical conductivity was optimal around 0.5%Ca composition after this treatment (Fig 1.2).
- Initial thixoforming trials resulted in filling defects, primarily back-filling (역방향 충전) and porosity (기공), attributed to premature solidification caused by temperature differences between the slurry and the core assembly, flow resistance, and potentially trapped air (Fig 4).
- Microstructural analysis revealed liquid/solid segregation during filling (more liquid phase observed towards the top of slots), but this was not considered the primary cause of the filling defects (Fig 5).
- Control of process parameters, including optimizing the billet heating temperature (empirically determined around 1075°C) and profile (using asymmetric heating to keep the top hotter, Fig 6), improved formability and reduced filling defects.
- Modifying the billet shape from a simple cylinder (Fig 9A) to one with a recess matching the rotor shaft (Fig 9B) improved material flow into the slots, resulting in better filling (observed via NDT, Fig 7, Fig 8) and higher efficiency.
- Comparative efficiency tests showed that the thixoformed Cu-Ca rotors achieved over 1% higher efficiency than the standard aluminum die-cast (Al D/C) rotors (Fig 10).
Figure Name List:
- Fig. 1.1 Grain size of Cu-Ca alloy specimens compressed to various deformation levels at room temperature followed by heat treatment at 1050 °C for 4 minutes
- Fig. 1.2 Electrical conductivity of Cu-Ca alloy specimens compressed to various deformation levels at room temperature followed by heat treatment at 1050℃ for 4 minutes
- Fig. 2 Rotor core assembly (A) and squirrel cage (B)
- Fig. 3 Die for Cu-rotor thixoforming and thixoformed Cu-Rotor
- Fig. 4 Filling defects of thixoformed Cu-rotor (A) upper end ring (B) lower end ring
- Fig. 5 Microstructures of as-thixoformed Cu-rotor slot at the various positions
- Fig. 6 Heating curves measured at (#1) 5 mm (#2) 20 mm, apart from surface
- Fig. 7 Results of non-destructive testing
- Fig. 8 Thixoformed Cu-rotor for efficiency test
- Fig. 9 Billet shape (A) cylinder type (B) modified type
- Fig. 10 Thixoformed Cu-rotor efficiency
7. Conclusion:
Based on the thixoforming of Cu-Ca alloys for high-efficiency motor rotors and subsequent efficiency measurements, the following conclusions were drawn:
(1) The SIMA process enabled the use of lower Ca content Cu-Ca alloys (which have better electrical conductivity) by producing globular particles with a grain size similar to that of higher Ca content alloys.
(2) Incomplete slot filling was identified as the primary cause of reduced efficiency. Controlling heating conditions and forming process parameters improved formability and reduced filling defects.
(3) Using a modified billet shape resulted in higher efficiency, indicating that design improvements (like billet or core assembly geometry) can enhance both formability and performance.
(4) In simultaneous comparative efficiency tests with Al D/C rotors, the thixoformed Cu-rotor demonstrated an efficiency increase of more than 1%.
8. References:
- [1] D. H. Kang, H. D. Ha, K. C. Chang, D. H. Goo, et al, 1998, Planning of long-term technology for the development of high efficiency motors, Report for the Ministry of Commerce, Republic of Korea, p. 250.
- [2] R. G. R. Sellors, J. G. Heyes, 1979, Engineering, Vol. 219, No.11, pp. 1434~1437.
- [3] E. Y. Lee, B. M. Kang, S. Y Lee, 2003, J. of the Korean Society for Heat Treatment, Vol. 16, No. 5, pp. 267~274.
- [4] S. Kleiner, O. Beffort, M. Fuchs, P. J. Uggowitzer, 2003, Advanced Semi-solid Processing of Alloys and Composites, Proceedings of the 7th S2P, pp. 257~262.
- [5] Lee Sang-Yong, Lee Jung-Hwan, Lee Young-Sun, 2001, Journal of Materials Processing Technology, 4845, 1-6.
- [6] Keun Yong Sohn, Dong Woo Seo, and Sang Yong Lee, 2003, AMPT, pp. 1497~1500.
- [7] 윤성원, 서판기, 강충길, 2003, 고액공존재료의 변형거동에서 재료의 크기가 액상편석에 미치는 영향, 한국소성가공학회지, 제12권 제2호, pp. 94~101.
- [8] J. C. Lee, H. K. Seok, H. I Lee, 2003, Effect of the Gate Geometry and the Injection Speed on the Flow Behaviors of a Semi-Solid A356 Al Alloy, Metals and Materials Int., Vol.9, No. 4, pp. 351~357.
9. Copyright:
- This material is a paper by "W. S. Jung, S. Y. Lee, P. W. Shin". Based on "Process Control and Thixoforming of Cu Rotor for High Efficiency Motors".
- Source of the paper: [DOI URL not provided in the source document]
This material is summarized based on the above paper, and unauthorized use for commercial purposes is prohibited.
Copyright © 2025 CASTMAN. All rights reserved.