This article introduces the paper ["Case-Based Product Development of a High-Pressure Die Casting Injection Subset Using Design Science Research"] published by ["Faculty of Mechanical Engineering, Belgrade"].
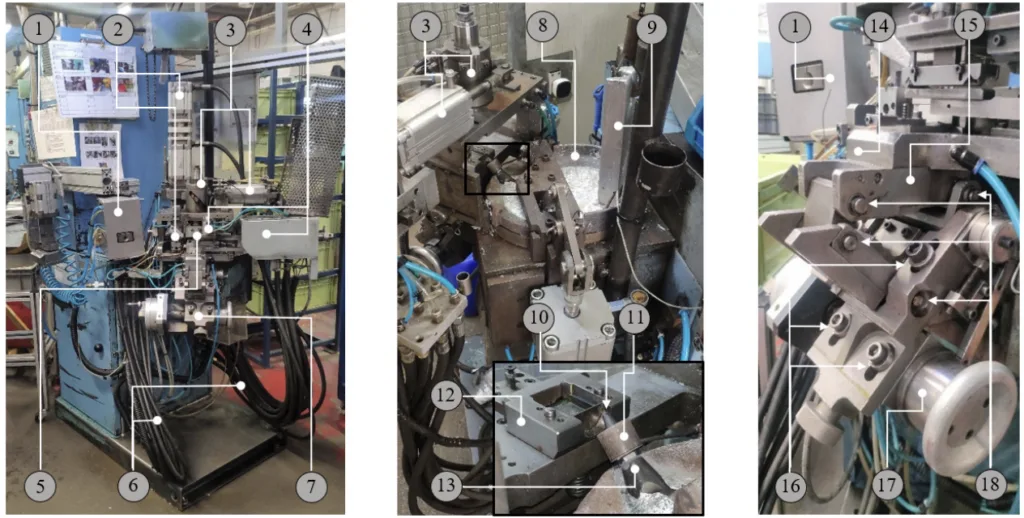
1. Overview:
- Title: Case-Based Product Development of a High-Pressure Die Casting Injection Subset Using Design Science Research
- Author: Matilde C. Tojal, F. J. G. Silva, R. D. S. G. Campilho, Arnaldo G. Pinto, Luís Pinto Ferreira
- Publication Year: 2022
- Publishing Journal/Academic Society: FME Transactions
- Keywords: Product Development; DSR; Maintenance; Sustainability; Die Casting;Productivity; FMEA; Wear analysis.
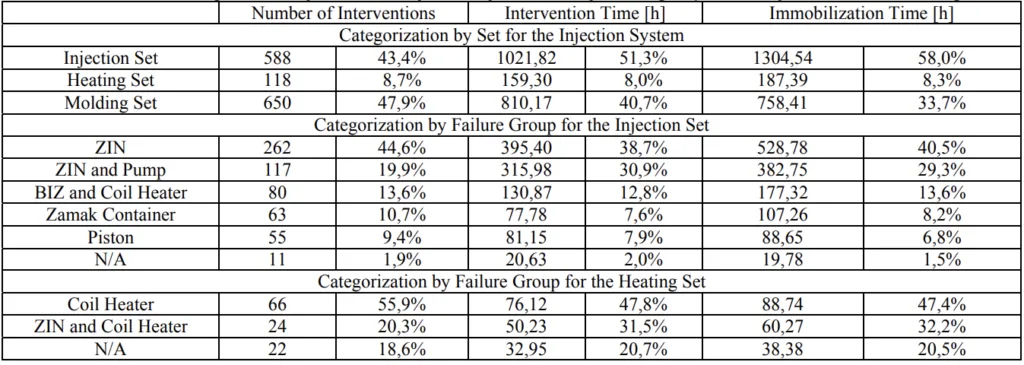
2. Abstracts or Introduction
The paper addresses the challenge of wear in components directly linked to hot parts in high-pressure die casting, a widely used process in metalworking. It proposes a sustainable maintenance approach by focusing resources on critical problem analysis and mitigation at human, machine/process, or supplier levels. Design Science Research (DSR) methodology is employed to develop a new injection subset concept. The implementation of this concept yielded beneficial outcomes, including reduced consumption, acquisition costs, waste, intervention time during maintenance, and increased equipment availability. The research emphasizes the importance of sustainable manufacturing in the automotive industry and the role of maintenance in achieving economic, environmental, and social sustainability. It highlights the application of DSR methodology to product development in die casting, focusing on improving the efficiency and lifespan of critical components like the injection nozzle.
3. Research Background:
Background of the Research Topic:
The automotive industry plays a significant role in the modern economy and is at the forefront of productive systems technology development. Spare part consumption is a major contributor to resource consumption in productive systems. Sustainable manufacturing is crucial for viable production considering economic, environmental, and social commitments. Maintenance significantly impacts production volume, cost, system availability, efficiency, and resource utilization. Die casting, particularly high-pressure die casting, is widely used but causes severe wear on components subjected to high temperatures, such as injection nozzles.
Status of Existing Research:
Existing research emphasizes the importance of data collection for critical spare part selection and root cause analysis [15]. Product development complexity necessitates data-driven decision-making [16]. Effective maintenance management systems are crucial for understanding conflicting factors in product lifecycle [17]. Innovation and product development are key success factors, requiring optimal performance/cost ratio, risk management, and system flaw intolerance [18-21]. Design Science Research (DSR) is a recognized methodology for developing new products from existing ones [26-27], with its technology background and focus on complex problem-solving [28]. Iterative DSR processes, like Vaishnavi and Kuechler's [30] and Peffers et al.'s [32], provide structured frameworks for design and development. Siedhoff [35] further developed DSR by integrating design thinking and pre-existing DSR stages.
Necessity of the Research:
The injection nozzle area in die casting processes suffers from constant replacements, process stoppages, and productivity losses [25]. There is an urgent need to research new concepts for nozzles and connecting zones to enhance process efficiency in these critical areas. While DSR is established, its application to specific die casting component improvement, particularly focusing on sustainable maintenance and wear reduction of injection subsets, requires further investigation. This research addresses this gap by applying DSR to develop a case-based product development for a high-pressure die casting injection subset.
4. Research Purpose and Research Questions:
Research Purpose:
The primary purpose is to demonstrate how sustainable maintenance can be achieved in high-pressure die casting by applying Design Science Research (DSR) to develop a new injection subset concept. This aims to optimize resource allocation towards analyzing and mitigating critical problems originating at human, machine/process, or supplier levels, ultimately enhancing equipment lifespan and reducing waste.
Key Research:
The key research focuses on:
- Applying Design Science Research (DSR) methodology for product development in the context of high-pressure die casting.
- Developing a new injection subset design to improve the lifespan and performance of critical components, specifically the Zamak Injection Nozzle (ZIN).
- Analyzing wear mechanisms and failure modes of the existing injection subset to identify areas for improvement.
- Implementing and validating the new injection subset concept to assess its impact on sustainability, maintenance, productivity, and cost-effectiveness.
Research Hypotheses:
While not explicitly stated as hypotheses, the research operates under the implicit assumptions that:
- Design Science Research methodology is an effective approach for developing improved components in high-pressure die casting.
- A redesigned injection subset, developed through DSR, can significantly reduce wear and extend the lifespan of critical components like the ZIN.
- Implementing the new injection subset will lead to measurable improvements in sustainable maintenance, including reduced spare part consumption, lower maintenance costs, decreased downtime, and increased equipment availability.
5. Research Methodology
Research Design:
The research employs the Design Science Research (DSR) methodology, specifically the process developed by Siedhoff [35], which combines design thinking with pre-existing DSR stages in an iterative approach. It starts with exploratory research, followed by prescriptive research to generate solution recommendations. The DSR cycle begins with the initial design of the product under study and proceeds through iterative stages of problem identification, suggestion, development, evaluation, and conclusion. Case-based reasoning is utilized for modifying an existing product rather than starting a completely new design.
Data Collection Method:
Data collection methods include:
- Quantitative data: Spare part consumption data, acquisition costs, and overall expenses for different spare parts, collected from the company's task assistance software. This data was used for Pareto analysis to identify critical components.
- Qualitative data: Observation and monitorization of the manufacturing process to identify technical issues and complement software-based data.
- Technical analysis:
- SEM (Scanning Electron Microscopy) and EDS (Energy-Dispersive X-ray) analysis: Used for ZIN wear analysis.
- Metallographic and hardness testing: Performed for full wear characterization and material property assessment.
- Rockwell C hardness test: Conducted to measure hardness according to ISO 6508-1:2016 standard.
Analysis Method:
Analysis methods include:
- Pareto analysis: Used to prioritize spare parts for study based on acquisition costs, focusing on the most urgent components.
- FMEA (Failure Mode and Effects Analysis): Employed to identify failure modes, breakdown frequencies, and intervention times of the injection system components.
- Ishikawa diagram (Fishbone diagram): Developed to summarize findings and identify root causes of premature ZIN failure, guiding the development of solutions.
- Statistical analysis: Descriptive statistics to analyze intervention categorization and failure mode frequencies.
Research Subjects and Scope:
The research focuses on the injection system of a ZHPIM (Zamak High-Pressure Injection Machine) used for die casting Zamak 5 onto steel cable ends. The primary subject of investigation is the Zamak Injection Nozzle (ZIN) and related components within the injection subset. The scope encompasses the analysis of spare part consumption, failure modes, and the development of an improved injection subset design using DSR methodology to enhance its performance, lifespan, and contribute to sustainable maintenance practices.
6. Main Research Results:
Key Research Results:
- Pareto Analysis: Identified SP01, SP03, and SP06 as the most expensive spare parts, guiding the focus towards the injection set.
- Intervention Categorization: Indicated that the injection system (85% of interventions) and molding set (47.9% of interventions) were major sources of downtime. Within the injection set, ZIN interventions were significant (44.6%).
- Failure Mode Analysis of ZIN: Wear and fracture were the dominant failure modes of the ZIN. Damaged heating sets contributed to 5.7% of ZIN failures. 79.9% of fractured ZINs led to pump replacement, and 72.3% of wear failures required only ZIN replacement.
- DSR Iterations and Model Development: Four major DSR iteration processes led to the development of new ZIN models (Model 01 to Model 07). Modifications included changes to ZIN geometry (ICZ radius, chamfer removal), material hardness increase (56-58 HRC), and sealing methodology improvements.
- Wear Analysis: SEM analysis revealed distinct zones of wear on the ZIN's ICZ. Metallographic and hardness tests showed slight hardness reduction in impacted areas but no significant microstructural changes.
- Implementation and Validation of New Model (Model 07): Model 07, incorporating design changes and material specification compliance, demonstrated significantly improved performance. It exhibited wear due to plastic deformation (intended behavior) and achieved a working time exceeding 140 days, a substantial increase compared to previous models.
Analysis of presented data:
- Figure 1: Pareto analysis of spare part consumption by accumulated acquisition cost, highlighting the cost contribution of different spare parts.
- Table 1: Spare part consumption data, acquisition costs, and overall expenses for the top ten spare parts, used for Pareto analysis.
- Figure 2: ZHPIM equipment structure, illustrating the hierarchical breakdown of systems, sets, and components.
- Figure 3: Workstation, Injection System, and Coupling System components, showing the location and function of various parts.
- Table 2: Intervention categorization by system and failure group, quantifying intervention frequency and downtime for different components.
- Figure 4: Pareto analysis of ZIN failure modes, showing the frequency of wear, fracture, and other failure types.
- Figure 5: Injection failure caused by coupling system problems, visually demonstrating technical issues.
- Figure 6: Location of protection plates, illustrating protective measures for heating set and ZIN.
- Figure 7: Extreme wear on coupling system tuning slots, showing wear-related issues.
- Figure 8: Clearances on dowel pins, highlighting fitting problems in the coupling system.
- Figure 9: Intervention process impact on coupling system wear, illustrating maintenance-induced wear.
- Figure 10: Technical problems with heating set seal, showing sealing issues.
- Figure 11: Failure mode by heating set corrosion, demonstrating corrosion-related failure.
- Figure 12: Bottom frame plate interaction with ZIN, illustrating geometric interaction.
- Figure 13: Contact points between BFP and ZIN ICZ, showing contact area details.
- Figure 14: Geometric issues contributing to fracture, highlighting design flaws.
- Figure 15: ICZ from BFP compliant with working state, showing a compliant ICZ.
- Figure 16: Non-compliance of ICZs due to abrasion and impact, showing non-compliant ICZs.
- Figure 17: Ishikawa diagram for ZIN premature failure, summarizing root causes of failure.
- Figure 18: SEM analysis of ZIN, showing SEM images of wear zones.
- Figure 19: Failure mode of ZIN ICZ by pitting, illustrating pitting wear.
- Figure 20: Failure mode of ZIN ICZ by spalling, illustrating spalling wear.
- Figure 21: Feed marks impact on failure, showing machining marks.
Figure Name List:
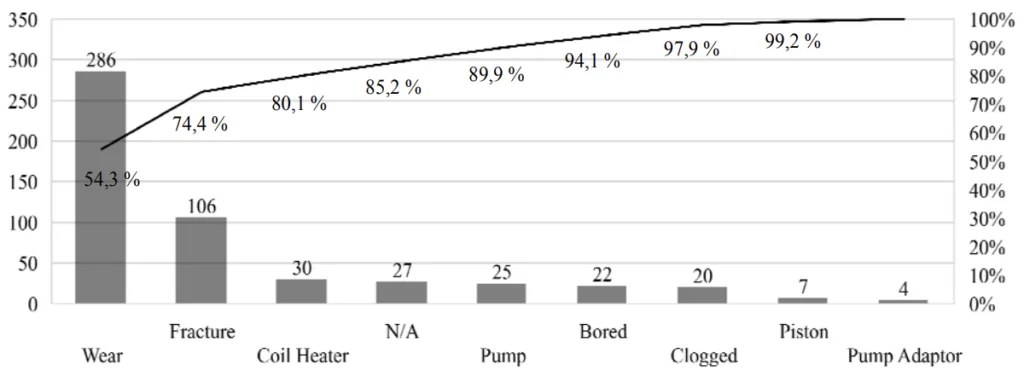
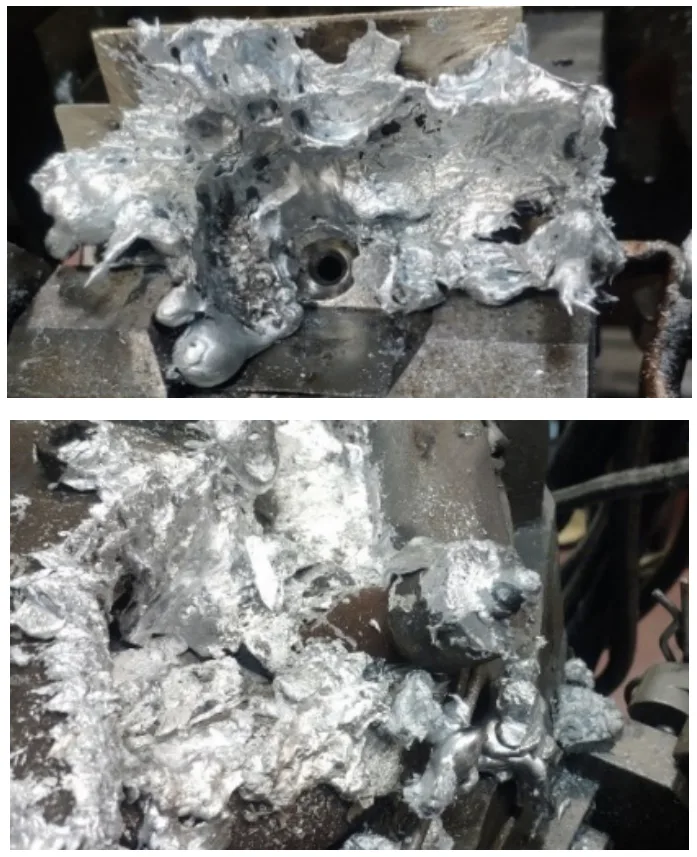
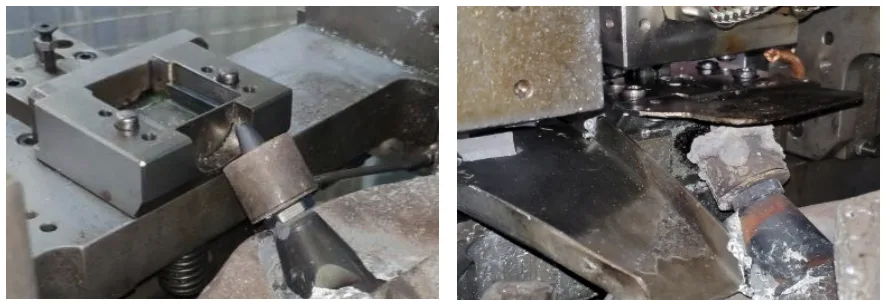
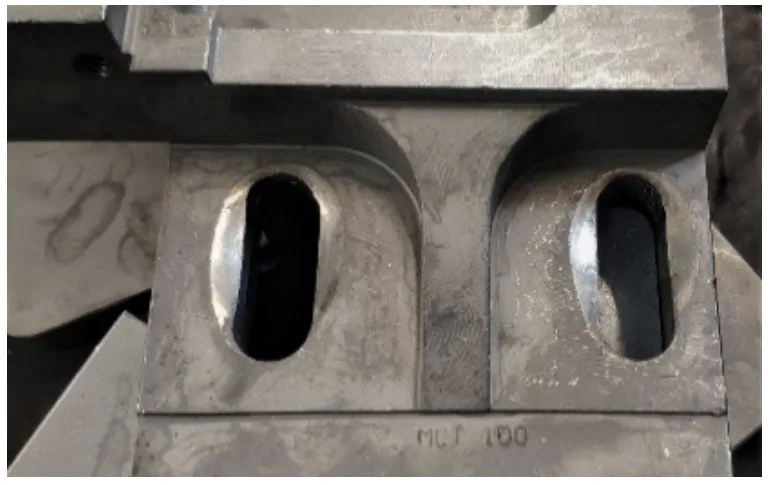
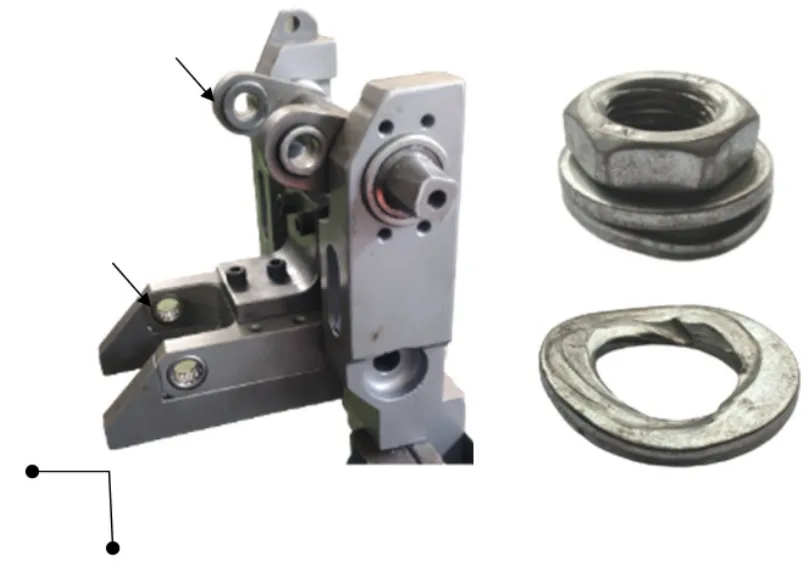
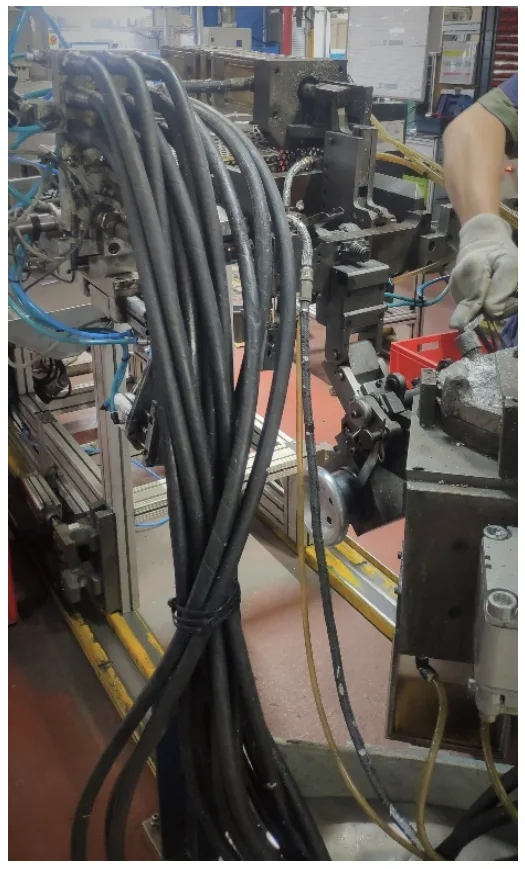
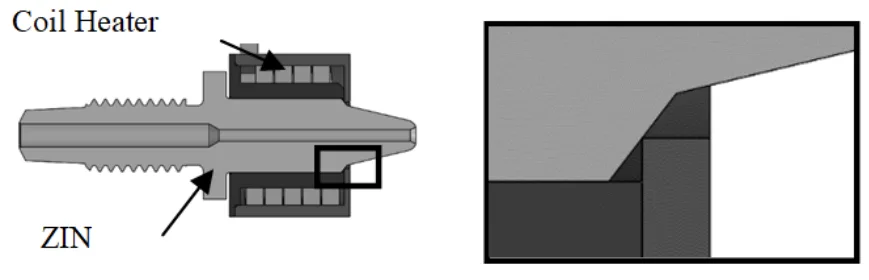
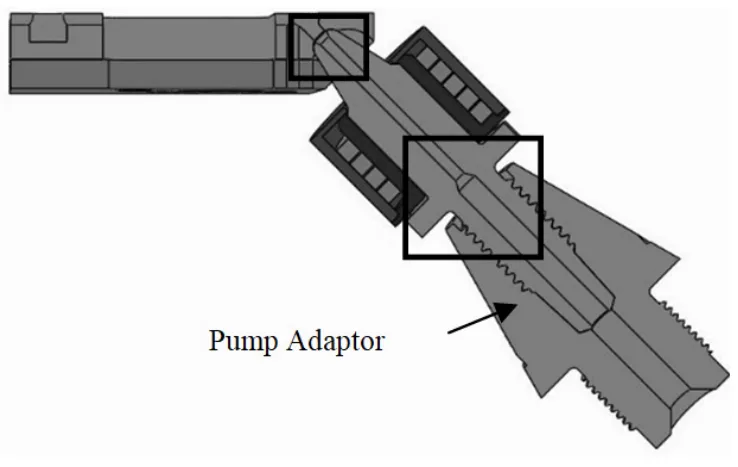
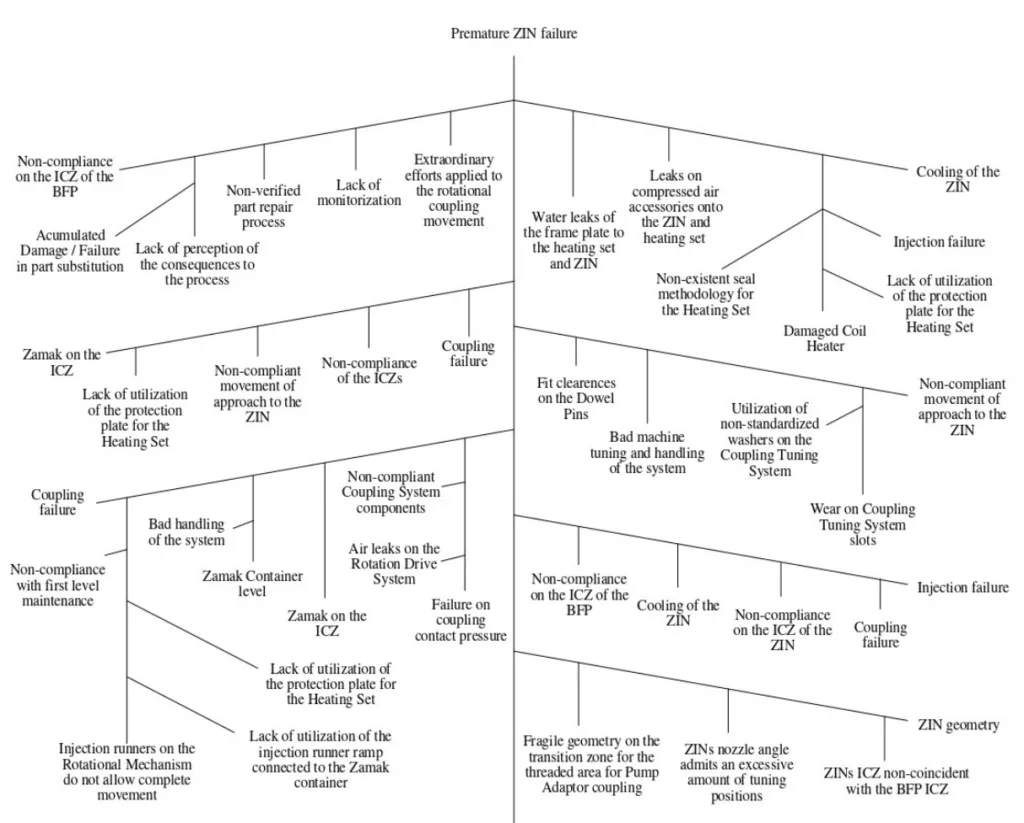
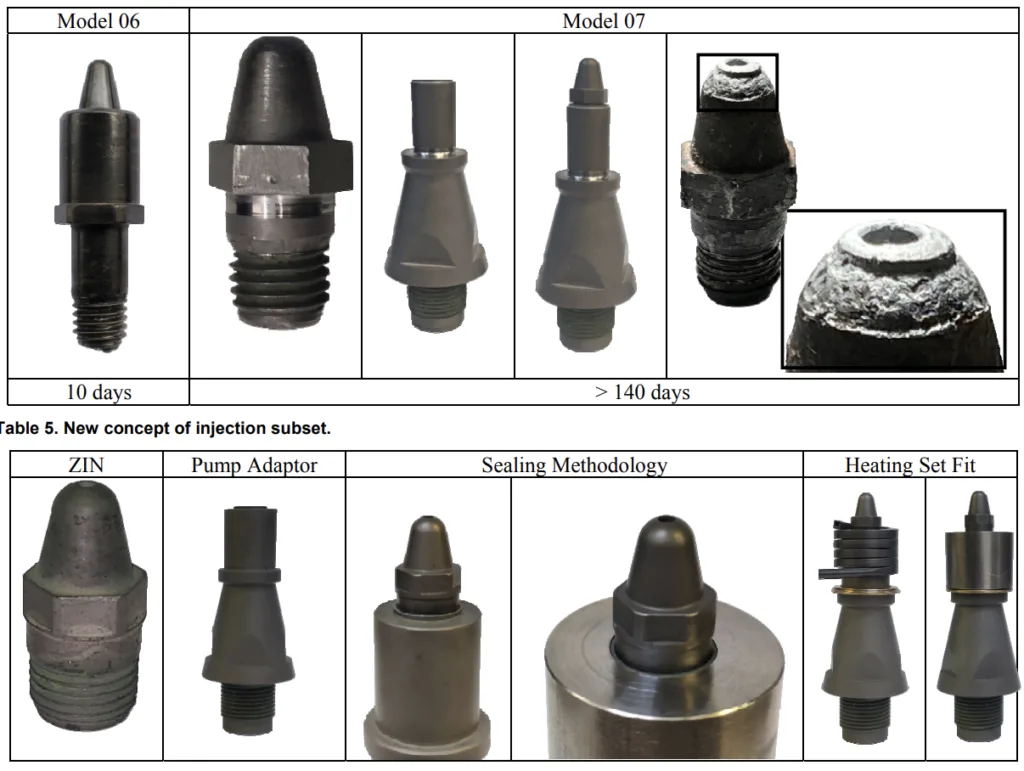
- Figure 1. Pareto's analysis on spare part consumption by accumulated acquisition cost (Overall expenses).
- Figure 2. ZHPIM equipment structure by main systems, sets and working groups.
- Figure 3. Workstation, Injection System and Coupling System and corresponding main components and location: (1) Cable trimming device; (2) Flower device and drive cylinder; (3) Mold closure system and drive cylinder; (4) Transfer and drive cylinder; (5) Mold and frame; (6) Air, water and oil hoses; (7) Coupling system; (8) Zamak container; (9) Zamak ingot; (10) Zamak injection nozzle; (11) Heating set; (12) Frame base; (13) Pump adaptor; (14) Support base; (15) Rotation mechanism; (16) Coupling tuning system; (17) Rotation drive system; (18) Dowel pins.
- Figure 4. Pareto's analysis for ZIN failure mode count for the period under study.
- Figure 5. Injection failure caused by technical problems on the coupling system elements.
- Figure 6. Location of the protection plates of the heating set and the internal parts of the moulding set
- Figure 7. Extreme wear on the coupling system tunning slots.
- Figure 8. Clearances on the dowel pins that connect to the coupling system and group of washers found on the ΖΗΡΙΜ.
- Figure 9. Intervention process impact on premature coup-ling and tunning system wear.
- Figure 10. Technical problems with the seal of the contact between the heating set and the ZIN.
- Figure 11. Failure mode by excessive corrosion of the heating set incapacitating the coil heater.
- Figure 12. Bottom frame plate interaction with the ZIN.
- Figure 13. Contact points between BFP and the ZIN inject-tion contact zones.
- Figure 14. Geometric issues function as a major contributor to failure mode by fracture.
- Figure 15. ICZ from BFP compliant with the required working state.
- Figure 16. Non-compliance of ICZs for the BFP due to abrasion and impact.
- Figure 17. Ishikawa diagram for ZINs premature failure
- Figure 18. SEM analysis to the ZIN.
- Figure 19. Failure mode of the ZIN injection contact zone by pitting.
- Figure 20. Failure mode of the ZIN injection contact zone by spalling.
- Figure 21. Feed marks impact on nucleation and propagation of premature failure.
7. Conclusion:
Summary of Key Findings:
The research successfully applied Design Science Research (DSR) to develop a new injection subset concept for high-pressure die casting, significantly improving the lifespan and performance of the Zamak Injection Nozzle (ZIN). The new Model 07 demonstrated a substantial increase in working time (over 140 days) and exhibited wear due to plastic deformation, indicating improved wear resistance. The implementation of the new concept resulted in reduced spare part consumption, acquisition costs, waste, intervention time, and increased equipment availability.
Academic Significance of the Study:
This study demonstrates the effective application of Design Science Research methodology in the context of die casting product development. It provides a detailed case study of using DSR to address a real-world industrial problem, offering a structured approach for improving component design and maintenance practices in manufacturing. The research contributes to the body of knowledge on sustainable manufacturing and the role of maintenance optimization in achieving sustainability goals.
Practical Implications:
The findings have significant practical implications for the die casting industry, particularly for operations using high-pressure die casting. The developed injection subset concept offers a tangible solution for reducing downtime, maintenance costs, and spare part consumption, while enhancing equipment reliability and productivity. The systematic approach to problem analysis and solution development can be adopted by other manufacturers to improve the design and maintenance of critical components in their processes.
Limitations of the Study and Areas for Future Research:
The study is limited to a specific case study within one manufacturing environment. Further research could explore the generalizability of the findings to other die casting applications and different types of injection systems. A deeper investigation into the material behavior of the ZIN under die casting conditions, particularly regarding the slight hardness reduction observed, could further optimize material selection and heat treatment processes. Future research could also focus on automating data collection and analysis for predictive maintenance in die casting processes, building upon the DSR framework established in this study.
8. References:
- [1] R. J. S. Costa, F. J. G. Silva, R. D. S. G. Campilho, "A novel concept of agile assembly machine for sets applied in the automotive industry," Int. J. Adv. Manuf. Technol., Vol. 91, pp. 4043-4054, 2017. doi: 10.1007/s00170-017-0109-4
- [2] W. Araújo, F. J. G. Silva, R. Campilho, "Manufacturing cushions and suspension mats for vehicle seats: A novel cell concept," Int. J. Adv. Manuf. Tech., Vol. 90, pp. 1539-1545. 2017, doi: 10.1007/s00170-016-9475-6
- [3] A. Gritsenko, V. Shepelev, E. Zadorozhnaya, K. Shubenkova, "Test Diagnostics of Engine Systems in Passenger Cars," FME Trans., Vol. 48, pp. 46-52, 2020, doi: 10.5937/fmet2001046G.
- [4] F. J. G. Silva, R. M. Gouveia, Cleaner Production - Towards a Better Future. Cham, Switzerland: Springer International Publishing, 2020.
- [5] J. Malek and T. N. Desai, "A systematic literature review to map literature focus of sustainable manufacturing,” J. Clean. Prod., Vol. 256, p. 120345, 2020, doi: 10.1016/j.jclepro.2020.120345.
- [6] M. Siladić, B. Rašuo, "On-Condition Maintenance for Nonmodular Jet Engines: An Experience," J Eng Gas Turbine Power, Vol. 131(3), p. 032502, May 2009, doi: 10.1115/1.3019104.
- [7] B. Rašuo, G. Djuknić, "Optimization of the aircraft general overhaul process," Aircr. Eng. Aerosp. Technol., Vol. 85(5), pp. 343-354. 2013, doi: 10.1108/AEAT-02-2012-0017.
- [8] C. Franciosi, A. Voisin, S. Miranda, S. Riemma, and B. Iung, “Measuring maintenance impacts on sustainability of manufacturing industries: from a systematic literature review to a framework proposal," J. Clean. Prod., Vol. 260, p. 121065, 2020, doi: 10.1016/j.jclepro.2020.121065.
- [9] S. Ferreira, L. Martins, F. J. G. Silva, R. B. Casais, R. D. S. G. Campilho, and J. C. Sá, “A novel approach to improve maintenance operations," Procedia Manuf., Vol. 51, pp. 1531-1537, 2020, doi: 10.1016/j.promfg.2020.10.213.
- [10] L. Silvestri, A. Forcina, V. Introna, A. Santolamazza, and V. Cesarotti, “Maintenance transformation through Industry 4.0 technologies: A systematic literature review," Comput. Ind., Vol. 123, p. 103335, 2020, doi: 10.1016/j.compind.2020.103335.
- [11]L. Morgado, F. J. G. Silva, and L. M. Fonseca, "Mapping occupational health and safety management systems in Portugal: Outlook for ISO 45001:2018 adoption," Procedia Manuf., Vol. 38, pp. 755-764, 2019, doi: 10.1016/j.promfg.2020.01.103.
- [12] M. Jasiulewicz-Kaczmarek and P. Żywica, “The concept of maintenance sustainability performance assessment by integrating balanced scorecard with non-additive fuzzy integral," Eksploat. Niezawodn., Vol. 20(4), pp. 650–661, 2018, doi: 10.17531/ein.2018.4.16.
- [13] S. Ferreira, F. J. G. Silva, R. B. Casais, M. T. Pereira, and L. P. Ferreira, "KPI development and obsolescence management in industrial maintenance," Procedia Manuf., Vol. 38, pp. 1427–1435, 2019, doi: 10.1016/j.promfg.2020.01.145.
- [14] C. Franciosi, A. Lambiase, C. Franciosi, A. Lambiase, S. Alfredo, "Sustainable Maintenance: i a Maintenance: a Periodic Maintenance: Sustainable Maintenance: a Periodic Preventive Spare Parts Sustainable Spare Parts Management,” IFAC-PapersOnLine, Vol. 50(1), pp. 13692–13697, 2017, doi: 10.1016/j.ifacol.2017.08.2536.
- [15]T. Santos, F. J. G. Silva, S. F. Ramos, R. D. S. G. Campilho, and L. P. Ferreira, “Asset priority setting for maintenance management in the food industry," Procedia Manuf., Vol. 38, pp. 1623-1633, 2019, doi: 10.1016/j.promfg.2020.01.122.
- [16]T.G. Chondros, "The Development of Mechanics and Engineering Design and Machine Theory since the Rennaissance," FME Trans., Vol. 49, pp. 291-307, 2021, doi: 10.5937/fme2102291C.
- [17] F. Schönberg and M. Messer, "Decision data model in virtual product development,” Comput. Ind. Eng., Vol. 122, pp. 106-124, 2018, doi: 10.1016/j.cie.2018.05.047.
- [18]S. Altuntas, E. B. Özsoy, and Şi. Mor, “Innovative new product development: A case study," Procedia Comput. Sci., Vol. 158, pp. 214–221, 2019, doi: 10.1016/j.procs.2019.09.044.
- [19]M. Riesener, C. Doelle, M. Mendl-Heinisch, and N. Klumpen, "Identification of evaluation criteria for algorithms used within the context of product development," Procedia CIRP, Vol. 91, pp. 508-515, 2020, doi: 10.1016/j.procir.2020.02.207.
- [20] G. Bastchen, F. Silva, and M. Borsato, "Risk management analysis in the product development process," Procedia Manuf., Vol. 17, pp. 507-514, 2018, doi: 10.1016/j.promfg.2018.10.090.
- [21]J. G. Persson, “Current Trends in Product Development," Procedia CIRP, Vol. 50, pp. 378-383, 2016, doi: 10.1016/j.procir.2016.05.088.
- [22]R. G. Cooper, “The drivers of success in new-product development,” Ind. Mark. Manag., Vol. 76, pp. 36-47, 2019, doi: 10.1016/j.indmarman.2018.07.005.
- [23] V. Nunes, F. J. G. Silva, M. F. Andrade, R. Alexandre, A. P. M. Baptista, "Increasing the lifespan of high-pressure die cast molds subjected to severe wear," Surf Coat Tech, Vol. 332, pp. 319-331, 2017. doi: 10.1016/j.surfcoat.2017.05.098.
- [24]B.M.D.N. Moreira, R.M. Gouveia, F.J.G. Silva, R. D. S. G. Campilho, "A Novel Concept Of Production And Assembly Processes Integration," Procedia Manuf., Vol. 11, pp. 1385-1395. 2017, doi: 10.1016/j.promfg.2017.07.268.
- [25] V.F.C. Sousa, F.J.G. Silva, L.P. Ferreira, R.D.S.G. Campilho, T. Pereira, E. Braga, "Improving the Design of Nozzles Used in Zamak High-Pressure Die-Casting Process," FME Trans., Vol. 49, pp. 1005-1013, 2021. doi: 10.5937/fme2104005S.
- [26] O.I. Abdullah, W.T. Abbood, H.K. Hussein, "Development of Automated Liquid Filling System Based on the Interactive Design Approach," FME Trans., Vol. 48, pp. 938-945, 2020. doi: 10.5937/fme2004938A.
- [27] S. Tamada, M. Chandra, P. Patra, S. Mandol, D. Bhattacharjee, P.K. Dan, " Modeling for Design Simplification and Power-Flow Efficiency Improvement in an Automotive Planetary Gearbox: A Case Example," FME Trans., Vol. 48, pp. 707-715, 2020. doi: 10.5937/fme2003707T.
- [28] J. Grenha Teixeira, L. Patrício, K. H. Huang, R. P. Fisk, L. Nóbrega, and L. Constantine, “The MINDS Method: Integrating Management and Interaction Design Perspectives for Service Design," J. Serv. Res., Vol. 20(3), pp. 240-258, 2017, doi: 10.1177/1094670516680033.
- [29] Richard Baskerville & Vijay Vaishnavi, 2020. "A Novel Approach to Collectively Determine Cybersecurity Performance Benchmark Data," Progress in IS, in: Jan vom Brocke & Alan Hevner & Alexander Maedche (ed.), Design Science Research. Cases, pages 17-41, Springer.
- [30] V. K. Vaishnavi and W. K. Jr., “Introduction to Design Science Research in Information and Communication Technology," Des. Sci. Res. Methods Patterns Innov. Inf. Commun. Technol., 2nd edition, pp. 7-30, Boca Raton, FL, USA, CRC Press, 2015. ISBN: 9780429172205.
- [31]F. Devitt and P. Robbins, “Design, Thinking and Science," Commun. Comput. Inf. Sci., Vol. 388, pp-38-48, 2013, doi: 10.1007/978-3-319-04090-5.
- [32] K. Peffers, T. Tuunanen, M. A. RotUhenberger, and S. Chatterjee, "A design science research methodology for information systems research,” J. Manag. Inf. Syst., Vol. 24(3), pp. 45–77, 2007, doi: 10.2753/MIS0742-1222240302.
- [33]J. Q. Azasoo and K. O. Boateng, "A Retrofit Design Science Methodology for Smart Metering Design in Developing Countries," Proc. - 15th Int. Conf. Comput. Sci. Its Appl. ICCSA 2015, pp. 1–7, 2015, doi: 10.1109/ICCSA.2015.23.
- [34] Jan vom Brocke & Alan Hevner & Alexander Maedche, "Introduction to Design Science Research," Progress in IS, in: Jan vom Brocke & Alan Hevner & Alexander Maedche (ed.), Design Science Research. Cases, pages 1-13, 2020, Springer. doi: 10.1007/978-3-030-46781-4_1.
- [35] S. Siedhoff, "Design science research,” Seizing Bus. Model Patterns Disruptive Innov., pp. 29-43, Spinger, 2019. ISBN: 978-3658263355.
- [36] S. Gregor and A. R. Hevner, “Positioning and presenting design science research for maximum impact," MIS Q., Vol. 37(2), pp. 337–355, 2013, doi: 10.2753/MIS0742-1222240302.
- [37] K. Lepenioti, A. Bousdekis, D. Apostolou, and G. Mentzas, “Prescriptive analytics: Literature review and research challenges,” Int. J. Inf. Manage., Vol. 50, pp. 57–70, 2020, doi: 10.1016/j.ijinfomgt. 2019.04.003.
- [38] M. Relich and P. Pawlewski, “A case-based reasoning approach to cost estimation of new product development,” Neurocomputing, Vol. 272, pp. 40-45, 2018, doi: 10.1016/j.neucom.2017.05.092.
- [39] H. Saranga, et al. "Resource configurations, product development capability, and competitive advantage: An empirical analysis of their evolution," J. Bus. Res., Vol. 85, pp. 32-50, 2018, doi: 10.1016/j.jbusres.2017.11.045.
- [40] G. Pinto, F. J. G. Silva, A. Baptista, R. D. S. G. Campilho, and F. Viana, “Investigations on the Oxidation of Zn-coated Steel Cables," FME Trans., Vol. 49(3) pp. 587-597, 2021, doi: 10.5937/fme2103587P.
- [41]N. Martins, F. J. G. Silva, R. D. S. G. Campilho, and L. P. Ferreira, "A novel concept of Bowden cables flexible and full-automated manufacturing process improving quality and productivity,” Procedia Manuf., Vol. 51, pp. 438-445, 2020, doi: 10.1016/j.promfg.2020.10.062.
- [42] R. Ribeiro, F. J. G. Silva, A. G. Pinto, R. D. S. G. Campilho, and H. A. Pinto, “Designing a novel system for the introduction of lubricant in control cables for the automotive industry," Procedia Manuf., Vol. 38, pp. 715-725, 2019, doi: 10.1016/j.promfg.2020.01.096.
- [43]H. A. Pinto, F. J. G. Silva, R. P. Martinho, R. D. S. G. Campilho, and A. G. Pinto, “Improvement and validation of Zamak die casting moulds," Procedia Manuf., Vol. 38, pp. 1547–1557, 2019, doi: 10.1016/j.promfg.2020.01.131.
- [44] H. Pinto, F. J. G. Silva, “Optimisation of Die Cast-ing Process in Zamak Alloys," Procedia Manuf., Vol. 11, pp. 517–525, 2017, doi: 10.1016/j.prom fg.2017.07.145.
- [45]B. Arh, B. Podgornik, and J. Burja, "Electroslag remelting: A process overview,” Mater. Tehnol., Vol. 50(6), pp. 971-979, 2016, doi: 10.17222/mit.2016.108.
- [46] A. Pribulová, P. Futaš, M. Bartošová, “Cleanness and mechanical properties of steel after remelting under different slags by ESR," Key Eng. Mater., Vol. 635, pp. 112-117, 2015, doi: 10.4028 /www.scientific.net/KEM.635.112.
- [47]Y. Pan, C. Chen, S. Wang, “Properties Evaluation of a H13 ESR Hot Work Tool Steel Produced Using a Continuous Casting Electrode," China Steel Technical Report, Vol. 29, pp. 49-55, 2016.
9. Copyright:
- This material is "Matilde C. Tojal, F. J. G. Silva, R. D. S. G. Campilho, Arnaldo G. Pinto, Luís Pinto Ferreira"'s paper: Based on "Case-Based Product Development of a High-Pressure Die Casting Injection Subset Using Design Science Research".
- Paper Source: https://doi.org/10.5937/fme2201032T
This material was created to introduce the above paper, and unauthorized use for commercial purposes is prohibited.
Copyright © 2025 CASTMAN. All rights reserved.