This article introduces the paper ['Design of Conformal Cooling Channels Using Numerical Methods in a Metal Mold and Calculating Exergy Destruction in Channels'] published by ['Scientia Iranica'].
1. Overview:
- Title: Design of Conformal Cooling Channels Using Numerical Methods in a Metal Mold and Calculating Exergy Destruction in Channels
- Author: Ali BOLATTÜRK, Osman İPEK, Karani KURTULUŞ, Mehmet KAN
- Publication Year: August 2018
- Publishing Journal/Academic Society: Scientia Iranica
- Keywords: Metal Mold, Exergy Destruction, Cooling Channel Design.
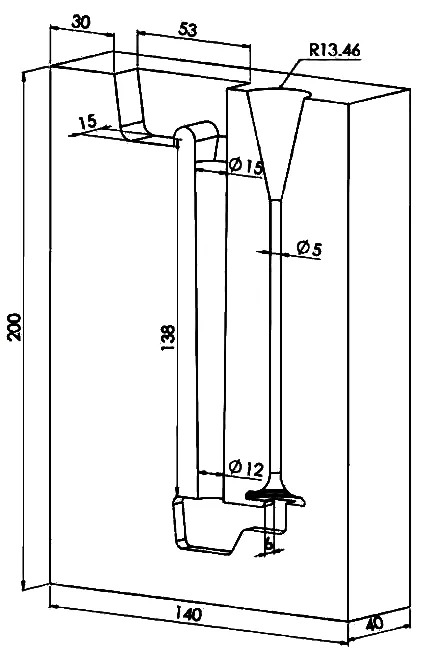
2. Abstracts or Introduction
Shorter cycle times and improved product quality are achievable through faster cooling in metal molds. Conventional manufacturing limits cooling channel design to linear directions and simple forms, restricting cooling performance. Additive manufacturing enables complex geometries, allowing for conformal cooling channels in metal molds. This study investigates the design of conformal cooling channels for optimal cooling in a monoblock permanent mold. Computational Fluid Dynamics (CFD) analyses were conducted under steady-state conditions to compare conformal and classical cooling channel molds. The study evaluated pressure drops, cooling channel outlet temperatures, and exergy destructions at varying flow velocity rates. Numerical investigations indicated that conformal cooling channels can achieve approximately 5% higher cooling performance compared to classical channels. However, conformal cooling exhibits higher pressure drop and approximately 12% greater exergy destruction than classical cooling channels.
3. Research Background:
Background of the Research Topic:
The cooling process is critical in metal molds for the solidification of liquid metal, influencing casting quality. Non-uniform cooling leads to defects like hot spots and distortion. Conventional methods limit cooling channels to linear designs, restricting cooling efficiency. Conformal cooling channels, enabled by additive manufacturing, offer a solution to enhance cooling performance.
Status of Existing Research:
Existing research indicates the benefits of conformal cooling channels. Studies on hot extrusion dies with conformal cooling showed production speed increases up to 300% compared to standard cooling channels [2]. Injection molds with conformal cooling channels have demonstrated improved product quality through shorter cycle times and homogeneous temperature distribution [3-9]. Numerical studies have also shown that conformal cooling channels can increase cooling performance and reduce solidification time [10-12].
Necessity of the Research:
The high production cost of metal molds manufactured with additive manufacturing necessitates optimizing conformal cooling channel designs to achieve desired performance. While numerical studies suggest improved cooling performance with conformal channels, there is a need for detailed analysis and comparison with classical cooling channels, particularly regarding exergy destruction, to optimize design and efficiency.
4. Research Purpose and Research Questions:
Research Purpose:
The primary purpose of this research is to design and numerically analyze conformal cooling channels in a metal mold to achieve optimum cooling performance, comparing them to classical cooling channel designs. The study aims to evaluate the performance differences in terms of heat transfer, pressure drop, and exergy destruction.
Key Research:
- Design of conformal cooling channels for a permanent mold.
- Numerical comparison of conformal cooling channels (curved channel (CC) and spherical fin channel (SFC)) with a standard channel (SC) in a metal mold using CFD.
- Calculation and comparison of pressure drops, cooling channel outlet temperatures, and exergy destructions for different cooling channel designs at varying flow velocity rates.
Research Hypotheses:
- Conformal cooling channels will exhibit higher cooling performance compared to classical cooling channels.
- Pressure drop and exergy destruction may be higher in conformal cooling channels compared to classical cooling channels.
- Optimized conformal cooling channel designs can improve cooling efficiency despite potential increases in pressure drop and exergy destruction.
5. Research Methodology
Research Design:
This study employs a numerical simulation-based research design. Three cooling channel configurations were designed: standard channel (SC), curved channel (CC), and spherical fin channel (SFC). CFD analyses were performed under steady-state conditions to compare the thermal and hydrodynamic performance of these designs.
Data Collection Method:
Data was collected through CFD simulations using ANSYS-FLUENT 16.1 software [24]. The simulations calculated pressure drops, cooling channel outlet temperatures, and heat transfer rates for each channel design at varying cooling oil velocities. Material properties and boundary conditions were defined based on literature and experimental data.
Analysis Method:
The collected numerical data was analyzed to compare the performance of the different cooling channel designs. Exergy destruction was calculated using Engineering Equation Solver (EES) software [25]. The analysis focused on evaluating the heat transfer rate, pressure drop, outlet temperature, and exergy destruction as a function of flow velocity for each channel type. Validation of the numerical model was performed by comparing results with existing experimental data from Imran et al. [23].
Research Subjects and Scope:
The research subject is a permanent mold for gravity die casting, specifically modeled for an exhaust valve of a gasoline internal combustion engine (Fig. 1). The scope of the study is limited to the numerical analysis of three different cooling channel designs (SC, CC, SFC) within this mold geometry, using "Petro-therm" brand heat transfer oil as a refrigerant and GGG 50 ductile cast iron (for SC) and stainless steel 316 L (for CC and SFC) as mold materials.
6. Main Research Results:
Key Research Results:
- Cooling Performance: SFC exhibited approximately 5% higher heat transfer rate than SC at a reference velocity of 1 m/s. SFC transfers more heat than CC and SC (Figure 7a).
- Pressure Drop: Pressure drop in SFC (up to approximately 50 kPa) was significantly higher than in SC (1-4 kPa) as velocity increased.
- Exergy Destruction: Exergy destruction in SFC was approximately 12% greater than in SC. For SC and CC, exergy destruction initially increased and then decreased with increasing velocity, while SFC showed fluctuating exergy destruction around 0.37 kW (Figure 7b).
- Outlet Temperature: Outlet temperatures decreased for all channels as velocity increased. The temperature difference between inlet and outlet was small (4K) for all channels.
Analysis of presented data:
The numerical results indicate that conformal cooling channels, particularly SFC, enhance heat transfer compared to standard channels. However, this improvement comes with trade-offs in pressure drop and exergy destruction. The SFC design, while providing the highest heat transfer rate, also exhibits the highest pressure drop and exergy destruction. The fluctuating exergy destruction in SFC suggests complex flow dynamics within the spherical fin structure. The small temperature difference between inlet and outlet across all channels indicates efficient heat removal, but also highlights the need for optimizing channel design to minimize exergy losses.
Figure Name List:
- Figure 1. The solid model of metal mold symmetry part
- Figure 2. The assumptions in the mold cooling channels heat transfer mechanism
- Figure 3. Computational domains of the analyzed cooling channels
- Figure 4. Boundary conditions used for the analyzed mold configuration
- Figure 5. Comparison of Imran et al. [23] and current study results for base temperature
- Figure 6. Comparison of Imran et al. [23] and current study results for pressure drop
- Figure 7 a. Comparison of heat transfer rate and pressure drops of SC, CC and SFC depending on flow rates, b. Comparison of channel outlet temperatures and exergy losses of SC, CC and SFC depending on flow rates
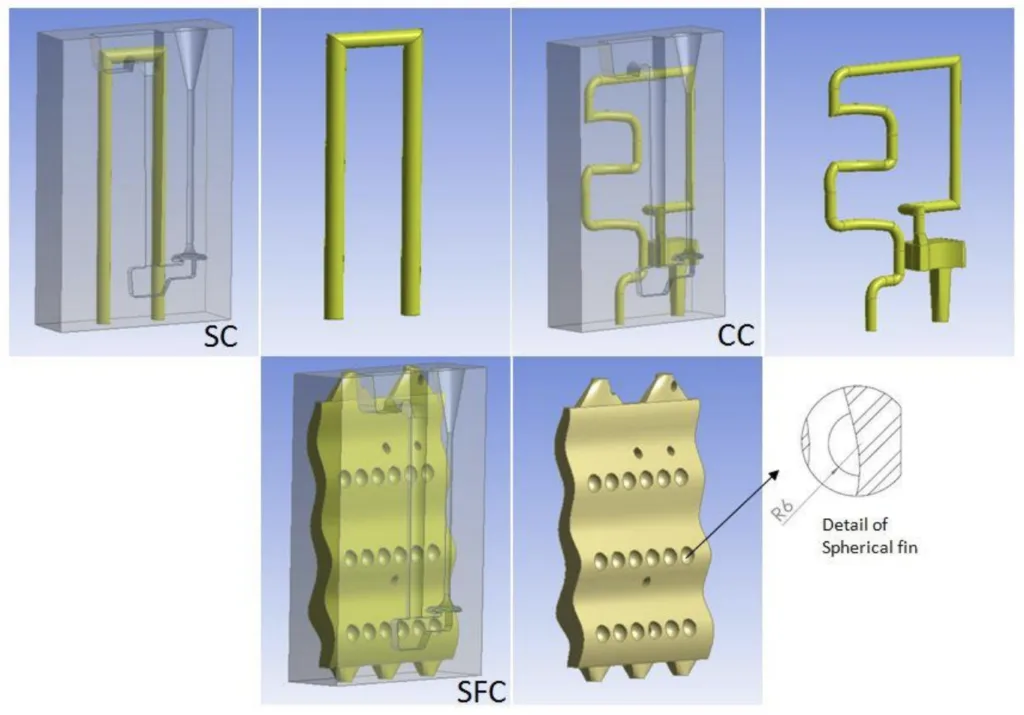
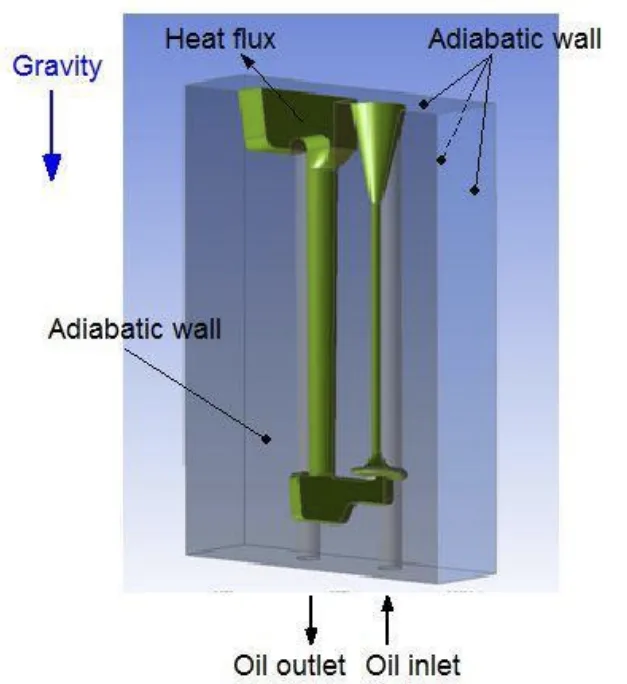
![Figure 5. Comparison of Imran et al. [23] and current study results for base temperature](https://castman.co.kr/wp-content/uploads/image-950-1024x707.webp)
![Figure 6. Comparison of Imran et al. [23] and current study results for pressure drop](https://castman.co.kr/wp-content/uploads/image-951-1024x699.webp)
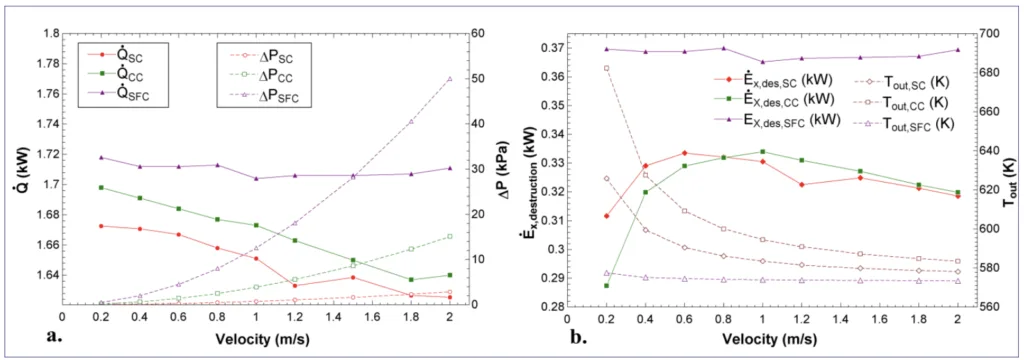
7. Conclusion:
Summary of Key Findings:
This study numerically compared standard (SC), curved (CC), and spherical fin (SFC) conformal cooling channels for metal molds. SFC demonstrated a 5% higher heat transfer rate than SC at 1 m/s reference velocity, but also exhibited significantly higher pressure drop and 12% greater exergy destruction. Heat transfer rate increases with decreasing cycle time. For 1m/s velocity, SC and SFC required pump power of 0.157 W and 11.7 W, respectively. SFC achieved 40 W more heat transfer rate, but pressure drop was highest in SFC. Temperature difference between outlet and inlet was higher in SC and CC compared to SFC as flow rate decreased. Exergy destruction in SFC fluctuated and was consistently higher than SC.
Academic Significance of the Study:
This research provides a detailed numerical analysis of conformal cooling channel designs, contributing to the understanding of their thermal and hydrodynamic performance compared to classical designs. The study highlights the trade-offs between enhanced heat transfer and increased pressure drop and exergy destruction in conformal cooling, offering valuable insights for optimizing cooling channel design in metal molds.
Practical Implications:
The findings suggest that while conformal cooling channels, particularly SFC, can improve cooling performance and potentially reduce cycle times, designers must consider the increased pressure drop and exergy destruction. The choice of cooling channel design should be based on a balance between desired heat transfer rate, allowable pressure drop, and energy efficiency. For applications where maximizing heat transfer is paramount, SFC may be suitable despite higher energy consumption. For applications prioritizing energy efficiency, SC or CC designs might be more appropriate.
Limitations of the Study and Areas for Future Research:
This study is limited to numerical simulations and does not include experimental validation for the specific mold geometry and channel designs investigated. Future research should focus on experimental validation of these numerical findings. Further optimization studies are needed to minimize exergy destruction in conformal cooling channel designs while maintaining high heat transfer rates. Investigating the impact of different conformal cooling channel geometries and flow parameters on mold performance and casting quality would also be beneficial.
8. References:
[1] Hsu, F.H. Wang, K. Huang, C.T. Chang, R.Y. “Investigation on conformal cooling system design in injection molding”, Advances in Production Engineering & Management., 8(2), pp.107-115 (2013).
[2] Hölker, R. Haase, M. Khalifa, N.B. Takkaya, A. E. “Hot extrusion dies with conformal cooling channels produced by additive manufacturing”, Aluminum Two Thousand World Congress and International Conference on Extrusion and Benchmark ICEB, pp. 4838-4846 (2015).
[3] Sachs, E. Wylonis, E. Allen, S. Cima, M. Guo, H. “Production of Injection Moulding Tooling With Conformal Cooling Channels Using the Three Dimensional Printing Process”, Polymer Engineering and Science., 40(5), (2000).
[4] Eimsa-ard, K. and Wannisorn, K. “Conformal bubbler cooling for molds by metal deposition process”, Computer-Aided Design., 69, pp. 126-133 (2015).
[5] Wang, Y. Yu, K. M. Wang, C. C. L. “Spiral and conformal cooling in plastic injection molding", Computer-Aided Design., 63, pp. 1-11 (2015).
[6] Vojnová, E. "The benefits of a conforming cooling systems the molds in injection moulding process", Procedia Engineering., 149, pp. 535-543 (2016).
[7] Venkatesh, G. Y. Ravi, K. Raghavendra, G. "Comparison of Straight Line to Conformal Cooling Channel in Injection Molding", Materials Today: Proceedings., 4(2), pp. 1167-1173 (2017).
[8] Jahan, A.S. and Mounayri, H. "Optimal Conformal Cooling Channels in 3D Printed Dies for Plastic Injection Molding", Procedia Manufacturing., 5, pp. 888-900 (2016).
[9] Park, H. Dang, X.P. "Development of a smart plastic injection mold with conformal cooling channels", Procedia Manufacturing., 10, pp. 48-59 (2017).
[10] Wang, G. Zhao, G. Li, H. Guan, Y. “Multi-objective optimization design of the heating/cooling channels of the steam-heating rapid thermal response mold using particle swarm optimization”, Int. J. of Thermal Science., 50, pp. 790-802 (2011).
[11] Franke, M. M. Hilbinger, R. M. Lohmüller, A. Singer, R. F. “The effect of liquid metal cooling on thermal gradients in directional solidification of super alloys: Thermal analysis”, Journal of Material Processing Technology., 213, pp. 2081-2088 (2013).
[12] Furumoto, T. Ueda, T. Amino, T. Ksunoki, D. Hosokowa, A. Tanaka, T. “Finishing performance of cooling channel with face protuberance inside the molding die", Journal of Material Processing Technology., 212, pp. 2154-2160 (2012). DOI: 10.1016/j.jmatprotec.2012.05.016
[13] Khairul, M. A. Alim, M. A. Mahbubul, I. M. Saidur, R. Hepbasli, A. Hossain, A. “Heat transfer performance and exergy analyses of a corrugated plate heat exchanger using metal oxide nanofluids", International Communications in Heat and Mass Transfer., 50, pp. 8–14 (2014).
[14] Dizaji, H. S. Jafarmadar, S. Asaadi, S. “Experimental exergy analysis for shell and tube heat exchanger made of corrugated shell and corrugated tube”, Experimental Thermal and Fluid Science., 81, pp. 475-481 (2017).
[15] Ipek, O. Kan, M. Gurel, B. “Examination of Different Heat Exchangers and the Thermal Activities of Different Designs”, Acta Physica Polonica A., 132(3), pp. 580-583 (2017).
[16] Kan, M. Ipek, O. Gurel, B. "Plate Heat Exchangers as a Compact Design and Optimization of Different Channel Angles”, Acta Physica Polonica A., 128(2B), B-49 (2015).
[17] Karaail, R. Öztürk, I. T. “Thermoeconomic Analyses of Steam Injected Gas Turbine Cogeneration Cycles", Acta Physica Polonica A., I, 128(2B), B-279 (2015).
[18] Zehtabiyan, R. N. Damirci, D. S. Fazel, Z.M.H. Saffar, A. M. "Generalized heat transfer and entropy generation of stratified air-water flow in entrance of a mini-channel", Scientia Iranica B., 24(5), pp. 2406-2417 (2017).
[19] Nouri, B. A. and Seyyed, H. M. H. "Numerical analysis of thermally developing turbulent flow in partially filled porous pipes", Scientia Iranica В., 22(3), pp. 835-843 (2015).
[20]Altinsoy, İ. Çelebi Efe, G.F. Yener, T. Önder, K. G. Bindal, C. “Effect of Double Stage Nitriding on 34CrAlNi7-10 Nitriding Steel”, Acta Physica Polonica A., 132, pp. 663-666 (2017).
[21] Arunkumar, S. Rao, K. S. Kumar, T. P. "Spatial variation of heat flux at the metal-mold interface due to mold filling effects in gravity die-casting", Int. J. of Heat and Mass Transfer., 51(11), pp. 2676-2685 (2008).
[22] Hallam, C. P. and Griffiths, W. D. “A model of the interfacial heat-transfer coefficient for the aluminum gravity die-casting process”, Metallurgical and materials transactions B., 35(4), pp. 721-733 (2004).
[23] Imran, A. A. Nabeel, S. M. Hayder, M. J. "Numerical and experimental investigation of heat transfer in liquid cooling serpentine mini-channel heat sink with different new configuration models" Thermal Science and Engineering Progress., 6, pp. 128-139 (2018).
[24] Fluent, Version 16.1 User's Guide, Fluent Inc., Lebanon (NH) (2016).
[25] Klein, S. A. “Engineering Equation Solver (EES)”, Academic Commercial V8.208.F-Chart Software, www.fChart.com (2008).
9. Copyright:
- This material is "Ali BOLATTÜRK, Osman İPEK, Karani KURTULUŞ, Mehmet KAN"'s paper: Based on "Design of Conformal Cooling Channels Using Numerical Methods in a Metal Mold and Calculating Exergy Destruction in Channels".
- Paper Source: https://doi.org/10.24200/sci.2018.50090.1502
This material was summarized based on the above paper, and unauthorized use for commercial purposes is prohibited.
Copyright © 2025 CASTMAN. All rights reserved.