This article introduces the paper ['LIGHTWEIGHT DESIGN OF VEHICLE SIDE DOOR'] published by ['POLITECNICO DI TORINO'].
1. Overview:
- Title: LIGHTWEIGHT DESIGN OF VEHICLE SIDE DOOR
- Author: JINDONG JI
- Publication Year: February 2015
- Publishing Journal/Academic Society: POLITECNICO DI TORINO, DOCTORATE SCHOOL, Ph.D in Mechanics (Ph.D THESIS)
- Keywords: Vehicle side door, Lightweight design, Composite material, Crashworthiness, Finite element analysis, NVH, Static analysis
![Figure 1.1-1 Passenger cars registrations by member state [1]](https://castman.co.kr/wp-content/uploads/image-741-png.webp)
2. Abstracts or Introduction
The thesis addresses the increasing environmental concerns regarding Green House Gas (GHG) emissions and stringent government regulations on vehicle safety, which necessitate the automotive industry to adopt new technologies for lighter and safer vehicles. Lightweight design is presented as an effective strategy to enhance fuel efficiency and reduce vehicle emissions. The research focuses on the vehicle lateral door substructure, a complex system traditionally made of steel, and explores the potential of composite materials as substitutes to achieve weight reduction without compromising safety and performance. The study develops and evaluates several composite side door structures for the Toyota Yaris 2010 model, considering static design requirements, NVH design criteria, and crashworthiness. Numerical simulations using ABAQUS and LS-DYNA are employed to assess the performance of composite designs against the original steel door structure, which serves as a reference solution. The thesis encompasses composite material characterization, finite element model simulations, static and modal analysis, and crashworthiness evaluation, providing a comprehensive investigation into the lightweight design of vehicle side doors using composite materials.
3. Research Background:
Background of the Research Topic:
Increasing environmental concerns about GHG emissions and government regulations on vehicle safety are driving vehicle manufacturers to seek new technologies. Lightweight design is becoming crucial for achieving higher fuel efficiency and reducing vehicle emissions. However, vehicle weight reduction techniques must not compromise customer comfort and vehicle safety.
Status of Existing Research:
Automotive research and design departments are actively exploring advanced materials like high strength steel, aluminum, magnesium, and composites to replace traditional materials. Composites offer advantages such as higher strength, lower weight, and better corrosion resistance. However, challenges remain in the widespread adoption of composites, including production cost, production volume, design methodologies, joining technology, and recycling issues. Vehicle safety remains a critical consideration when implementing lighter materials in automobiles.
Necessity of the Research:
The research is motivated by the need to address the challenges of lightweight vehicle design while maintaining safety standards. Vehicle lateral door substructure is selected as the focus due to its structural complexity and functional importance. Traditional steel door structures are heavy, and exploring composite alternatives for this component is essential for achieving overall vehicle weight reduction and improved performance.
4. Research Purpose and Research Questions:
Research Purpose:
The primary research purpose is to develop and evaluate composite side door structures for a vehicle, aiming for lightweight design while meeting static, NVH, and crashworthiness requirements. The thesis seeks to demonstrate the feasibility and benefits of using composite materials in vehicle side door design as a substitute for traditional steel.
Key Research:
The key research focuses on:
- Developing several composite side door structures for the Toyota Yaris 2010 model.
- Simulating and analyzing the performance of these composite structures using numerical tools ABAQUS and LS-DYNA.
- Comparing the performance of composite door solutions with the original Yaris steel door structure in terms of static behavior, NVH characteristics, and crashworthiness.
- Investigating innovative composite reinforcing panel designs for vehicle side doors.
Research Hypotheses:
The research hypothesizes that composite side door structures can achieve significant weight reduction compared to traditional steel doors while maintaining or improving structural performance in terms of stiffness, NVH, and crashworthiness. It is also hypothesized that innovative composite reinforcing panel designs can effectively replace traditional steel impact beams and reinforcements, enhancing the overall performance of composite side doors.
5. Research Methodology
Research Design:
The research employs a numerical simulation-based approach to design and evaluate composite side door structures. Finite Element (FE) models of both traditional steel and composite door designs are developed and analyzed under various loading conditions.
Data Collection Method:
Data is collected through numerical simulations using ABAQUS and LS-DYNA software. Material properties for steel and various composite materials (CFRP, GFRP, GMT, GMT-UD, GMT-TEX, SIMS) are used as input parameters for the FE models. Simulation outputs include stress distributions, displacements, intrusion measurements, and biomechanical responses of a dummy in crash simulations.
Analysis Method:
- Static Analysis: Linear and nonlinear static analyses are conducted to evaluate the structural stiffness and strength of composite door designs under vertical, horizontal, lateral stiffness, and sagging load cases. Modal analysis is performed to assess NVH characteristics.
- Dynamic Analysis: Explicit dynamic analysis is used for crashworthiness evaluation, simulating side impact scenarios according to FMVSS214 regulation. Biomechanical responses, including Head Injury Criteria (HIC), rib deflection, abdominal force, and pubic symphysis force, are analyzed to assess occupant safety.
- Comparative Analysis: The performance of composite door solutions is compared against the original Yaris steel door structure (reference solution) based on simulation results for static, NVH, and crashworthiness criteria.
Research Subjects and Scope:
The research subject is the vehicle side door structure, specifically for the Toyota Yaris 2010 model. The scope includes:
- Design and analysis of composite side door structures using CFRP, GFRP, GMT, GMT-UD, GMT-TEX, and SIMS materials.
- Numerical simulation of static, modal, and crashworthiness performance.
- Evaluation of intrusion displacement and biomechanical response in side impact scenarios.
- Comparison with a reference steel door structure.
6. Main Research Results:
Key Research Results:
- Static and Modal Analysis: Composite door structures, particularly those with composite frames, demonstrated comparable or slightly higher stiffness than the steel reference door in vertical and horizontal load cases. Modal analysis showed that composite door structures exhibited higher natural frequencies, indicating improved NVH performance.
- Crashworthiness Evaluation: Composite door solutions showed reduced intrusion displacements compared to the steel door in side impact simulations. Energy absorption capacity was significantly higher (around 20% increase) for composite doors. Biomechanical responses, including rib deflection, abdominal force, and pubic symphysis force, were within FMVSS214 regulation limits for composite door designs, indicating satisfactory occupant protection.
- Innovative Composite Panel: An innovative composite reinforcing panel design was developed and evaluated, showing potential for replacing traditional steel impact beams and reinforcements, further reducing weight while maintaining crashworthiness.
- Mass Reduction: Material substitution with composites resulted in significant weight reduction, with final mass reduction ratios ranging from 32% to 38% for different composite solutions compared to the steel door.
Analysis of presented data:
The data presented in figures and tables throughout the thesis, particularly in Chapters 6 and 7, supports the key research results. Figures 6.1-4, 6.1-8, and 6.1-11 illustrate displacement distributions under static loading, showing reduced displacements for composite doors. Tables 6.1-1, 6.1-3, and 6.1-5 quantify stresses and displacements, confirming comparable or improved static performance. Figure 7.1-3 shows intrusion displacement history in crash simulations, indicating reduced intrusion for composite doors. Figures 7.2-5, 7.2-8, 7.2-9, and 7.2-10 present biomechanical responses, demonstrating that composite doors meet safety regulation limits. Table 7.3-1 summarizes mass reduction data, highlighting the lightweighting potential of composite solutions.
Figure Name List:
![Figure 1.1-2 Passenger cars registrations by vehicle brand [1]](https://castman.co.kr/wp-content/uploads/image-742-png.webp)
![Figure 1.2-1 Average fuel consumption in the EU by vehicle manufacture [1]](https://castman.co.kr/wp-content/uploads/image-743-png.webp)
![Figure 1.2-2 Passenger cars 𝑪𝑶𝟐 emissions by member state [1]](https://castman.co.kr/wp-content/uploads/image-744-png.webp)
![Figure 1.2-3 Passenger cars 𝑪𝑶𝟐 emissions by vehicle segment [1]](https://castman.co.kr/wp-content/uploads/image-745-1024x368.webp)
![Figure 2.1-1 Representative vehicle energy flows in an urban driving cycle [1]](https://castman.co.kr/wp-content/uploads/image-746-1024x414.webp)
![Figure 2.1-2 Energy flow within an automotive vehicle [2]](https://castman.co.kr/wp-content/uploads/image-747-png.webp)
![Figure 2.1-3 Future propulsion system pathways [1]](https://castman.co.kr/wp-content/uploads/image-748-png.webp)
![Figure 2.2-2 Different segment vehicle mass change [6]](https://castman.co.kr/wp-content/uploads/image-749-png.webp)
![Figure 2.2-4 Vehicle weight composition by mass ratio [8]](https://castman.co.kr/wp-content/uploads/image-750-png.webp)
![Figure 2.2-5 1975 and 2007 average vehicle mass breakdown by material [9]](https://castman.co.kr/wp-content/uploads/image-751-1024x427.webp)
![Figure 2.2-11 Vehicle material compositions by percent mass [15]](https://castman.co.kr/wp-content/uploads/image-752-png.webp)
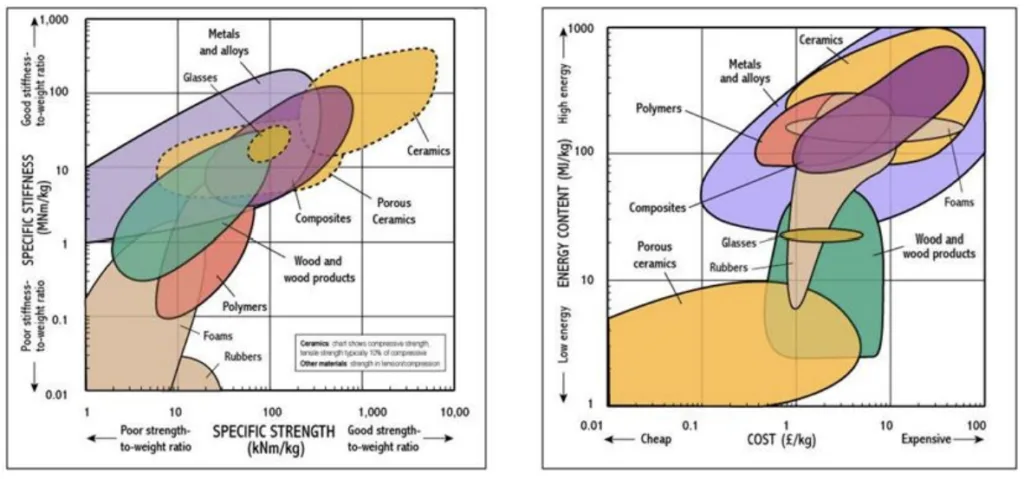
![Figure 2.2-15 Configure of BMW i3 [19]](https://castman.co.kr/wp-content/uploads/image-754-1024x281.webp)
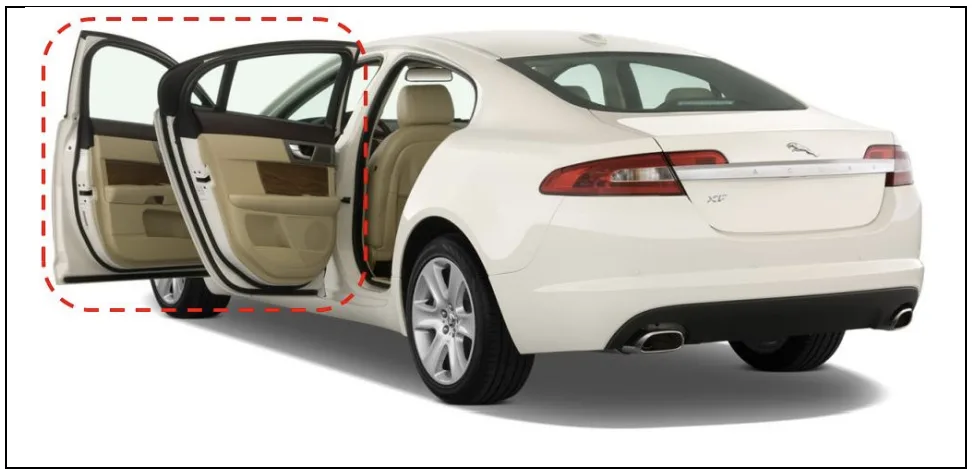
![Figure 3.1-4 Side door components of Toyota Yaris 2010 model [3]](https://castman.co.kr/wp-content/uploads/image-756-png.webp)
![Figure 3.2-2 Active safety and passive safety in automotive engineering [12]](https://castman.co.kr/wp-content/uploads/image-757-1024x667.webp)
![Figure 3.2-3 Different zones in vehicle crash impact [13]](https://castman.co.kr/wp-content/uploads/image-758-png.webp)
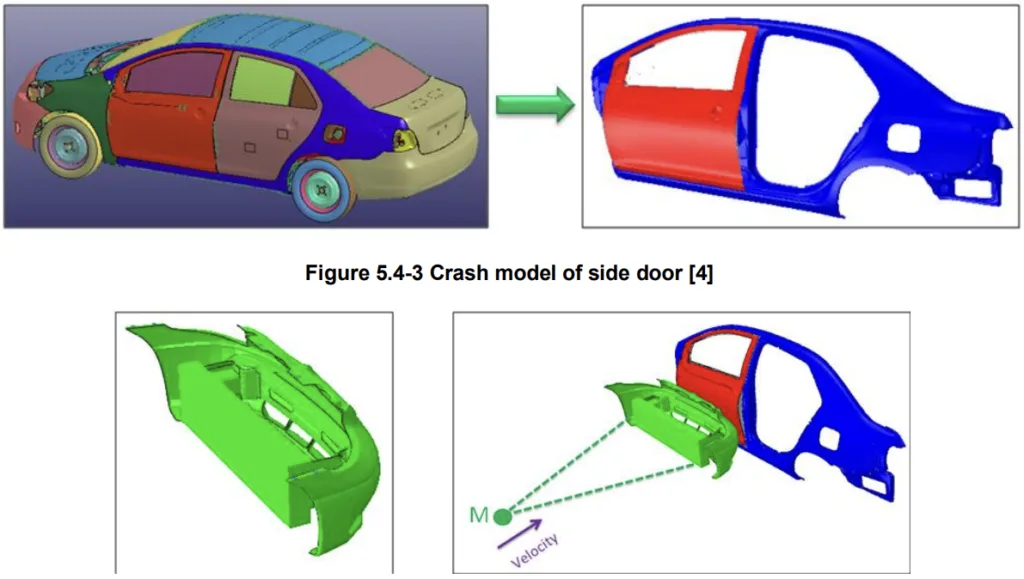
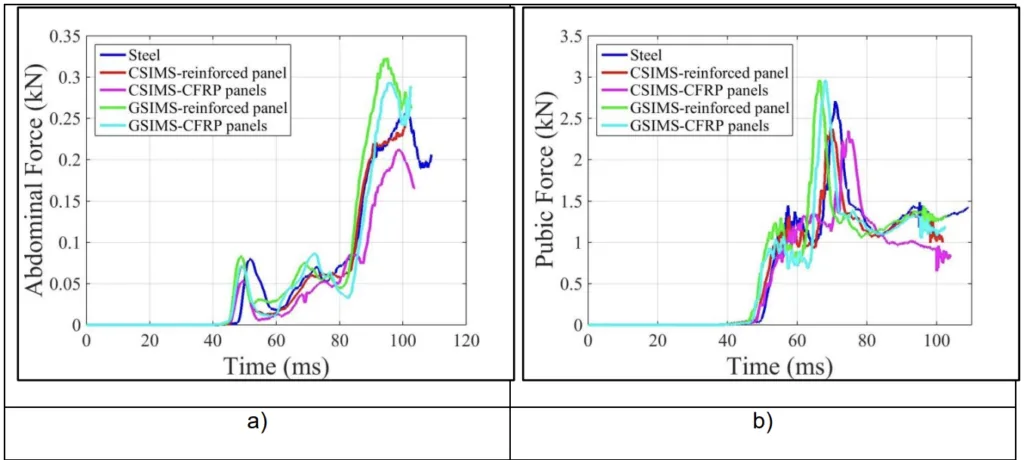
- Figure 1.1-1 Passenger cars registrations by member state [1]
- Figure 1.1-2 Passenger cars registrations by vehicle brand [1]
- Figure 1.2-1 Average fuel consumption in the EU by vehicle manufacture [1]
- Figure 1.2-2 Passenger cars CO2 emissions by member state [1]
- Figure 2.1-1 Representative vehicle energy flows in an urban driving cycle [1]
- Figure 2.1-2 Energy flow within an automotive vehicle [2]
- Figure 2.1-3 Future propulsion system pathways [1]
- Figure 2.1-4 Curb weight and fuel consumption of U.S. model year 2005 [1]
- Figure 2.2-1 Trend total vehicle weight [5]
- Figure 2.2-2 Different segment vehicle mass change [6]
- Figure 2.2-3 Vehicle weight change by member state in EU [7]
- Figure 2.2-4 Vehicle weight composition by mass ratio [8]
- Figure 2.2-5 1975 and 2007 average vehicle mass breakdown by material [9]
- Figure 2.2-6 Tensile strength requirements of different components of passenger cars and range of application of HSS [10]
- Figure 2.2-7 Average use of aluminum per car in Western Europe [11]
- Figure 2.2-8 Relative and absolute use of Aluminum in European cars [11]
- Figure 2.2-9 Aluminum intensive vehicles
- Figure 2.2-10 Composite applications in different areas
- Figure 2.2-11 Vehicle material compositions by percent mass [15]
- Figure 2.2-12 Ashby maps for comparison of mechanical performance of materials
- Figure 2.2-13 Ashby maps for comparison of strength and cost of materials
- Figure 2.2-14 Vehicles with reinforced carbon fibers
- Figure 2.2-15 Configure of BMW i3 [19]
- Figure 3.1-1 Conventional car side door
- Figure 3.1-2 Different types of vehicle side door [1]
- Figure 3.1-3 Three Different Door Architectures [2]
- Figure 3.1-4 Side door components of Toyota Yaris 2010 model [3]
- Figure 3.1-5 2010 Actual Toyota Yaris passenger sedan and FE model
- Figure 3.2-1 Evolution of accidents, fatalities and injured in EU [11]
- Figure 3.2-2 Active safety and passive safety in automotive engineering [12]
- Figure 3.2-3 Different zones in vehicle crash impact [13]
- Figure 3.2-4 Vehicle crash standards
- Figure 3.3-1 Regulation FMVSS 214. [14]
- Figure 3.3-2 Dimensions of Movable Deformable Barrier (mm) [14].
- Figure 3.3-3 Dummy family and different dummies used in side crash test
- Figure 3.3-4 Rating system in FMVSS standard
- Figure 4.1-1 Composite classification based on matrix materials [1]
- Figure 4.1-2 Composite classifications based on structure property [2]
- Figure 4.1-3 Summary of matrix materials [2]
- Figure 4.1-4 Weave types: plain weave, twill weave and satin weave [11]
- Figure 4.2-1 Vehicle deformation after crash
- Figure 4.2-2 a) structure of GMT, b) structure of GMT-UD, c) structure of GMT-TEX
- Figure 4.2-3 a) stacking of CSIMS, b) Stacking of GSIMS
- Figure 4.2-4 Properties of materials of Yaris door outer panel, inner panel and impact beam. [16]
- Figure 5.3-1 Simplified FE Model of Yaris door [4]
- Figure 5.3-2 Extraction process to get traditional door model [4]
- Figure 5.3-3 Composite beams
- Figure 5.3-4 Composite beams distribution in plane and curved models
- Figure 5.3-5 Joints shapes and position in composite door models
- Figure 5.3-6 Three FE Models of lateral frontal door
- Figure 5.4-1 Yaris side door model [4]
- Figure 5.4-2 Parts considered: outer panel, inner panel and impact beam
- Figure 5.4-3 Crash model of side door [4]
- Figure 5.4-4 Simulation of side impact: deformable bumper and side door structure
- Figure 5.5-1 Simulation model, a) Regulation FMVSS 214, b) Yaris model, c) Movable Deformable Barrier (MDB), d) dummy of EURO-SID 2
- Figure 5.6-1 a) Schematic aluminum door construction including a Simplified Total Aluminum Reinforcement (STAR) panel; b) Vertical door section showing the inner, outer, and STAR panel; c) STAR panel corrugation geometries. [9]
- Figure 5.6-2 a) STAR panel of Yaris; b) Original door model of Yaris; c) Innovative door model of Yaris
- Figure 5.6-3 a) Parts could be replaced; b) Innovative part made with composite; c) Four connecting areas
- Figure 5.7-1 Composite material model in ABAQUS
- Figure 5.7-2 Composite material model in LS-DYNA
- Figure 6.1-1 Three FE Modes of vehicle side door
- Figure 6.1-2 - Force applied in vertical load case and hinge positions in composite models.
- Figure 6.1-3 Von Mises stress distribution in three models for load case 1.
- Figure 6.1-4 Vertical displacements distribution for load case 1.
- Figure 6.1-5 Vertical displacement and reaction force for load case 1.
- Figure 6.1-6 – Horizontal load case.
- Figure 6.1-7 - Von Mises stress in three models under horizontal load.
- Figure 6.1-8 - Horizontal displacements in three models for horizontal load.
- Figure 6.1-9- Horizontal displacement and reaction force for load case 2.
- Figure 6.1-10- Quasi static intrusion simulation model
- Figure 6.1-11- Displacements in extrusion direction in three models for load case 3.
- Figure 6.1-12- Displacement and reaction force in quasi static intrusion simulation.
- Figure 6.2-1 Side door structure model of Yaris
- Figure 6.2-2 Equal stiffness criteria
- Figure 6.2-3 Lateral stiffness and sagging load case.
- Figure 6.2-4 Load-displacement diagrams for different loading cases
- Figure 6.2-5 Load-displacement diagram for three models under sagging case
- Figure 6.3-1 Modal shapes for first order and second order.
- Figure 6.3-2 Frequency change theory
- Figure 7.1-1 Yaris side door structure model.
- Figure 7.1-2 Crash model for crashworthiness evaluation.
- Figure 7.1-3 Intrusion displacement history of three models
- Figure 7.1-4 Reaction force history of three models
- Figure 7.1-5 Energy absorbed by side door structures
- Figure 7.1-6 Kinetic energy and internal energy of model CFRP_Panel&Beam.
- Figure 7.2-1 Side crash model: a) Toyota Yaris 2010, b) Movable Deformable Barrier, c) Side impact regulation FMVSS214, d) ES-2 Dummy.
- Figure 7.2-2 Parts considered in Yaris door: a) Outer panel, b) Inner panels, c) Reinforcing impact beam.
- Figure 7.2-3 Movements of dummy during side crash impact
- Figure 7.2-4 9 critical points for investigation of intrusion displacement on inner panel.
- Figure 7.2-5 Intrusion displacements of 9 critical points on inner panels of side door
- Figure 7.2-6 Reaction force and head acceleration
- Figure 7.2-7 a) Dummy head impact with roof rail, b) Foam around roof rail, c) Side air bags.
- Figure 7.2-8 Rib deflections, a) Upper rib, b) Middle rib, c) Lower rib.
- Figure 7.2-9 Abdominal Force.
- Figure 7.2-10 Pubic Symphysis Force.
- Figure 7.3-1 Outer panel, reinforced panel and inner panels.
- Figure 7.3-2 Intrusion displacements of occupant compartment
- Figure 7.3-3 Rib deflections
- Figure 7.3-4 Abdominal resultant force
- Figure 7.3-5 Pubic symphysis force
- Figure 7.3-6 Intrusion displacements
- Figure 7.3-7 Rib deflection a) Upper rib, b) Middle rib, c) Lower rib
- Figure 7.3-8 a) Abdominal force, b) Pubic symphysis force
- Figure 7.3-9 Intrusion displacement
- Figure 7.3-10 Rib deflection a) Upper rib, b) Middle rib, c) Lower rib
- Figure 7.3-11 a) Abdominal force, b) Pubic symphysis force
- Figure 7.3-12 Intrusion displacement
- Figure 7.3-13 Rib deflection a) Upper rib, b) Middle rib, c) Lower rib
- Figure 7.3-14 a) Abdominal force, b) Pubic symphysis force
7. Conclusion:
Summary of Key Findings:
The research concludes that composite materials offer a viable alternative to steel for vehicle side door construction, achieving significant lightweighting and maintaining or improving structural and safety performance. Composite door solutions demonstrated comparable static stiffness, enhanced NVH characteristics, and superior crashworthiness in terms of intrusion reduction and energy absorption. Biomechanical responses in crash simulations were within FMVSS214 regulation limits, indicating adequate occupant protection. Innovative composite reinforcing panel designs further enhance weight reduction potential.
Academic Significance of the Study:
This study contributes to the academic field by providing a comprehensive investigation into the application of composite materials for vehicle side door design. It offers detailed numerical simulation methodologies for evaluating static, NVH, and crashworthiness performance of composite structures. The research also expands the understanding of composite material behavior in automotive structural applications and provides valuable data for future research in lightweight vehicle design and safety.
Practical Implications:
The findings have significant practical implications for the automotive industry. The demonstrated feasibility of lightweight composite side doors offers a pathway to reduce vehicle weight, improve fuel efficiency, and lower emissions, aligning with global environmental regulations and consumer demands. The research provides design guidelines and validated numerical models that can be utilized by automotive engineers for developing and implementing composite side door structures in vehicle production.
Limitations of the Study and Areas for Future Research:
The study acknowledges limitations, including the exclusion of lateral airbags and detailed modeling of foam and seatbelt systems in crash simulations, which may affect head acceleration results. Future research areas include:
- Experimental validation of the numerical simulation results through physical testing of prototype composite side doors.
- Optimization of composite material selection and lay-up configurations for enhanced performance and cost-effectiveness.
- Investigation of joining technologies for composite-aluminum hybrid door structures.
- Further refinement of FE models to incorporate detailed airbag and restraint systems for more accurate crashworthiness predictions.
- Exploration of manufacturing processes and scalability for high-volume production of composite side doors.
8. References:
- [1]. The International Council on Clean Transportation, ―European Vehicle Market Statics, Pocketbook 2013‖.
- [2]. The Organization for Economic Co-operation and Development (OECD), ―Strategies to Reduce Greenhouse Gas Emissions from Road Transport: Analytical Methods‖, 2002.
- [3]. European Environment Agency, ―Monitoring CO2 emissions from new passenger cars in the EU: summary of data for 2012‖.
- [4]. David C., Sean B., Emily W. and Martin W., ―Trends in NOx and NO2 emissions and ambient measurements in the UK‖, 2011.
- [5]. TNO Science and Industry, ―Review and analysis of the reduction potential and cost of technological and other measures to reduce CO2-emisssions from passenger cars‖, 2006.
- [6]. www.autosteel.org.
- [7]. Nicholas L., ―Review of technical literature and trends related to automobile mass-reduction technology‖, report for California Air Resources Board, May 2010.
- [8]. The International Council on Clean Transportation, ―European Vehicle Market Statics, Pocketbook 2013‖.
- [9]. Stodolsky F., A. Vyas, et al. (1995), ―Life-Cycle Energy Savings Potential from Aluminum-Intensive Vehicles‖, Conference Paper, 1995 Total Life Cycle Conference&Exposition. October 16-19, 1995, Vienna, Austria.
- [10]. Abraham, A. Ducker Worldwide. (2011, May). ―Future Growth of AHSS [PowerPoint presentation at Great Designs in Steel Seminar]‖.
- [11]. J. Galan, L. Samek, P. Verleysen, K. Verbeken and Y.Houbaert, ―Advanced high strength steels for automotive industry‖, Revista de Metalurgia, 48 (2), ISSN: 0034-8570.
- [12]. J.Hirsch, ―Automotive Trends in Aluminum- The European Perspective‖, Materials Forum Volume 28, 2004.
- [13]. Ducker Worldwide, ―The Past, Present and Future of Aluminum in North American Light Vehicles‖, October 16, 2012.
- [14]. McWilliams A., ―Advanced Materials, Lightweight Materials in Transportation‖, report, Report Code: AVM056A, 2007.
- [15]. Ghassemieh E., ―Materials in Automotive Application, State of the Art and Prospects, New Trends and Developments in Automotive Industry‖, InTech, Marcello Chiaberge, ISBN: 978-953-307-999-8, 2011.
- [16]. http://wardsauto.com/subscriptions/facts-figures.
- [17]. Taub A., Krajewski P., Luo A. and Owens J., ―The Evolution of Technology for Materials Processing over the Last 50 Years: The Automotive Example ‖, JOM, February.
- [18]. Marc R., Deena P. and Tom W., ―Vehicle Design and the Physics of Traffic Safety‖, Physics Today, January 2006.
- [19]. http://www.bmw.com/
- [20]. http://www.euroncap.com/tests/fiat_500_2007/298.aspx.
- [21]. European Aluminum Association, ―The Aluminum Automotive MANUAL-Hang on parts‖, 2013.
- [22]. Daniel E.Whitney, MIT Engineering System Division and Cambridge MA, ―Design and Manufacturing of Car Doors: Report on Visits Made to US, European and Japanese Car Manufacturers in 2007‖, March 2008.
- [23]. National Crash Analysis Center, http://www.ncac.gwu.edu/
- [24]. World Health Organization, ―Global Status Report on Road Safety‖, 2013.
- [25]. Volvo Trucks, ―European Accident Research and Safety Report 2013‖.
- [26]. National Highway Traffic Safety Administration, ―An Analysis of Recent Improvements to Vehicle Safety‖, DOT HS 811 572, June 2012.
- [27]. EVALUE Project, ―Testing and evaluation methods for active vehicle safety‖, http://www.evalue-project.eu/.
- [28]. Final report of ELVA Project, ―Societal scenarios and available technologies for electric vehicle architectures in 2020‖, Grant Agreement Number 265898.
- [29]. Nat’l Highway Traffic Safety Admin., DOT §571.214, Dec. 13, 1979.
- [30]. Juan M. A. G, PhD thesis, ―A study to improve the crash compatibility between cars in side impact‖, Marzo 2008.
- [31]. Samaha RR, Elliott DS, ―NHTSA side impact research: motivation for upgraded test procedures‖, 18th International Technical Conference on the Enhanced Safety of Vehicles, Nagoya, Japan, 2003.
- [32]. Kathleen D. K., Carol A. C. F., Kristen N., Lawrence W. S. and Jonathan D. R., ―Abdominal injury in motor-vehicle crashes‖, UMTRI-2008-40, Nov. 2008.
- [33]. Peter S., Uli F., Sebastian S., Markus P., Arno E., DYNAmore GmbH, MAGNA STEYR, ―Comparison of ES-2re with ES-2 and USSID Dummy‖ , DYNAmore GmbH, 2014.
- [34]. Aimar A., Molina G. and Volpenge M., ―The magnesium door project‖, proc. of Int. Conf. Florence ATA 2003, Florence (1), paper 03A1039.
- [35]. Seong S. C, Dai G. L and Kwang S. J., ―Composite side-door impact beams for passenger cars.‖ Composite Structures Vol. 38, No. 1-4, 1997, pp. 229-239.
- [36]. Patberg L., Philipps M. and Dittmann R., ―Fiber-reinforced composites in the car side structure‖, Proc Instn Mech Engrs, 1999, Vol.213 part D, pp. 417-423.
- [37]. Belingardi G., ―Recent advances in joining technology for car body applications‖, proc. Int. Conf. MVM 2006 (Motor Vehicle and Motors), Kragujevac (Serbia), 4-6 October 2006.
- [38]. Banea M. D. and Da Silva L. F., ―Adhesively bonded joints in composite materials: an overview‖, Proc Instn Mech Engrs, 2009, Vol.223 part L, pp.1-18.
- [39]. http://www.slideshare.net/BKLR/polymer-matrix-composites.
- [40]. Giovanni B. , presentation of course ―Progettazione di strutture meccaniche in materiale composito‖, Politecnico di Torino, 2014.
- [41]. Frederick T. W., James C. W. and Hong Li, PPG Industries, Inc, ―Glass Fibers‖, ASM Handbook, Vol. 21: Composites (#06781G), 2001.
- [42]. Paul J. W., Zoltek Corporation, ―Carbon Fibers‖, ASM Handbook, Vol.21: Composites, 2001.
- [43]. http://www.angelfire.com/ma/ameyavaidya/b_fiber.htm#boron
- [44]. Reashad B. K. and Nasrin F., ―Kevlar-The Super Tough Fiber‖, International Journal of Textile Science 2012, pp78-83.
- [45]. David Roylance, ―Introduction to composite materials‖, March 24, 2000.
- [46]. Curt A., ―NM EPOXY HANDBOOK‖, third edition,2004.
- [47]. http://www.netcomposites.com/guide/polyester-resins/8
- [48]. Ermias G. Korico., ―Implementation of Composites and Plastics Materials for Vehicle Lightweight‖, PhD thesis,2012.
- [49]. MIL-HDBK-17-5, ―Composite Materials Handbook‖, 17 June, 2002.
- [50]. http://composite.about.com/library/data/blc-cfs003ltm25-rtd.htm
- [51]. Giovanni B. and Brunetto M., ―Recent research results in composite materials and adhesive applications for vehicle lightweight‖, Int. Cong. Motor Vechiles&Motors 2014,October 9th-10th.
- [52]. Patent US2002/0064640A1, ―Thin composite laminate and use thereof in making sports articles, especially boots‖.
- [53]. P. Nieri, I. Montanari, A. Terenzi, L. Torre and J. M. Kenny, ―A novel composite configuration for low-cost panels with improved toughness‖, 29th International Conference and Forum- SECO 08, March 31st–April 2nd.
- [54]. http://www.ncac.gwu.edu/
- [55]. Giovanni B., Alem T. Beyene and Ermias G. Korico., ―Geometrical optimization of bumper beam profile made of pultruded composite by numerical simulation‖, Composite Structures, 2013.
9. Copyright:
- This material is "JINDONG JI"'s paper: Based on "LIGHTWEIGHT DESIGN OF VEHICLE SIDE DOOR".
- Paper Source: [DOI URL]
This material was summarized based on the above paper, and unauthorized use for commercial purposes is prohibited.
Copyright © 2025 CASTMAN. All rights reserved.