This introductory paper is the research content of the paper ["Experimental Material Characterization and Formability studies on Aluminium Alloy (AA 8011)"] published by [E3S Web of Conferences].
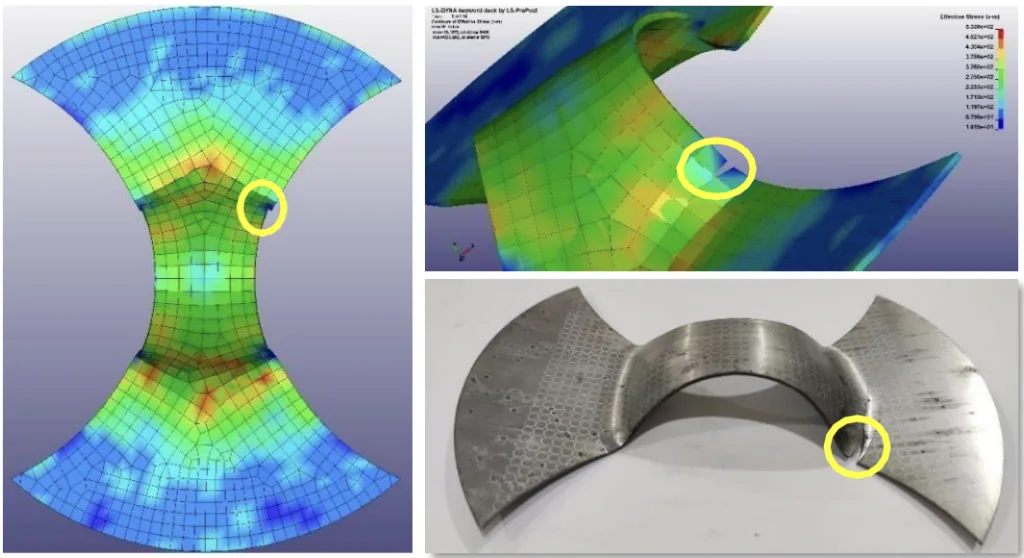
1. Overview:
- Title: Experimental Material Characterization and Formability studies on Aluminium Alloy (AA 8011)
- Author: Kuraku Ratna Babu, sattenapelli prashanth, Kethe Ganesh, Gone kiran kumar
- Publication Year: 2024
- Publishing Journal/Academic Society: E3S Web of Conferences 552, 01066 (2024)
- Keywords: Sheet metal shaping, plastic fragility, Forming Limit Diagram (FLD), Aluminum Alloy (AA8011), formability, Nakajima test, stretch forming, fractography, scanning electron microscope, LS-dyna software, extreme temperatures.
2. Abstracts / Introduction
Operations for sheet metal shaping are crucial for manufacturing diverse products. However, plastic fragility remains a significant challenge, leading to product defects. Addressing this issue necessitates considering factors such as the Forming Limit Diagram (FLD). This research investigates the formability of Aluminum Alloy (AA8011) at strain rates of 0.01 mm/s across ambient temperature, 100 °C, and 150 °C. The Nakajima test was employed to conduct stretch forming and derive results. The study revealed that the material's restricting stresses increased with temperature. Fractography, using a scanning electron microscope, and simulations with LS-dyna software were utilized for analysis. This study aims to contribute to the development of more efficient sheet metal-forming techniques by providing insightful data on the formability of AA 8011 sheets at extreme temperatures.
Aluminum alloys are utilized across various sectors due to their unique properties, including low weight, high thermal conductivity, and exceptional formability, particularly in aviation and automotive industries. Aluminum 8XXX alloys are prevalent in aircraft manufacturing. Duralumin (Al-Cu-Mg alloy) was the pioneering alloy in aircraft design. Precipitation hardening is a key method for enhancing 8XXX aluminum alloys. Copper is the primary alloying element in the 8xxx series, along with trace amounts of manganese and magnesium, resulting in excellent machinability, strength, and shapeability.
3. Research Background:
Background of the Research Topic:
Sheet metal shaping operations are fundamental in manufacturing. Plastic fragility in sheet metal forming is an ongoing industrial problem, often causing defects. To mitigate this, understanding factors like the Forming Limit Diagram (FLD) is essential. Aluminum alloys are advantageous due to their "small weight, outstanding thermal conductivity, and exceptional formability," making them suitable for "high-performing, portable parts for the aviation and automotive sectors." Their corrosion resistance, portability, and thermal insulation properties further enhance their utility. Aluminum 8XXX series alloys are extensively used in the aircraft industry. Duralumin, an early Al-Cu-Mg alloy, was initially adopted for aircraft design. Precipitation hardening is a primary method for strengthening 8XXX aluminum alloys. The combination of copper, manganese, and magnesium in these alloys provides "great machinability, substantial strength, and great shapeability."
Status of Existing Research:
Prior research has explored the properties of aluminum alloys. The precipitation stiffening relationship between magnesium and copper contributes to the sturdiness of aluminum alloys, which are also known for "outstanding anti-corrosion properties." They are suitable for applications requiring corrosion protection, including "aeronautical definitionsalongside additional parts." 2XXX series alloys are used for intricate shapes and tight tolerances due to high formability and can be heat-treated to improve mechanical properties, making them ideal for "hydraulic components and aircraft themes[3-4]." AA8011, an Al-4.5%Cu alloy, is used in aviation and automotive sectors for its strength-to-weight ratio and machinability, performing well in high-temperature environments like "motor and wing elements." Studies have examined alloying element effects on aluminum alloy behavior under fatigue and creep [5-6]. Naik, R.B., Ratna, [7] identified 513°C as the optimal solutionizing temperature for AA8011 under extreme heat. Valli Gogula, Kuldeep K, [8] conducted hot tensile tests on AA8011 from ambient to 300°C, finding sub-grain development during molding increases yield and tensile strength at lower temperatures. Dharavath, MT Naik, [9] studied AA2014-T6 steel alloy under tension and compression. Ji He, Z. Cedric Xia [12] investigated ASS 316 stretch forming and FLD from ambient to 400°C, noting strain variations and dynamic strain wrinkles influence on formability. S. Qin, H.M. Shang,[13] studied AA6061 cold forming limits, finding significantly higher limits in tension-tension areas at -196 °C. Sandeep Pandre,Ayush, [14] compared tests like Swift Cup and Fukui Cup Drawings Test for flexibility assessment. Xugang Wang, [15] developed a Nakazima test for thinner copper strips, comparable to Marciniak tests. R. Karthik Rao et.al, [16] observed increased radial tube expansion with temperature in AA8011. Lade Jayahari et.al, [17] used DYNAFORM with LS-DYNA for Ti-6Al-4V forming at 400 °C, validating Barlat 1989 criteria. Lumelskyj et.al, [18] used finite element analysis for FLCs of circular samples. Nejia Ayachi, [19] created FLD for AA8011 using Nakazima Test Simulation Application and validated it experimentally. L.Venugopal et.al, [20] analyzed reusable 2014-T6 metal strips, finding second-phase atoms and uniform grain size.
Necessity of the Research:
Understanding and improving sheet metal forming techniques is crucial to reduce plastic fragility and defects in manufactured goods. Specifically, gaining "insightful information on the formability of AA 8011 sheet at extreme temperatures" is necessary to "create more productive and successful sheet metal-forming techniques."
4. Research Purpose and Research Questions:
Research Purpose:
The primary research purpose is to investigate the formability characteristics of Aluminium Alloy (AA8011) at elevated temperatures. This involves studying the material's behavior under stretch forming conditions at ambient temperature, 100°C, and 150°C, with a strain rate of 0.01 mm/s. The ultimate goal is to "help create more productive and successful sheet metal-forming techniques by offering insightful information on the formability of AA 8011 sheet at extreme temperatures."
Key Research:
- Experimental characterization of AA8011 material.
- Formability analysis of AA8011 using the Nakajima test.
- Development of Forming Limit Diagrams (FLDs) for AA8011 at different temperatures.
- Simulation of the stretch forming process using LS-dyna software.
- Fractographic analysis using scanning electron microscopy to examine material failure modes.
- Analysis of Limiting Dome Height (LDH) at varying temperatures.
- Comparison of experimental and simulation results to validate the numerical model.
5. Research Methodology
Research Design:
This research employed a mixed methodology, combining experimental and numerical simulation approaches. Experimentally, Nakajima tests were conducted at varying temperatures. Numerically, Finite Element (FE) simulations were performed using LS-Dyna software to model the stretch forming process.
Data Collection Method:
- Nakajima Test (Hemispherical Dome test): Stretch forming experiments were performed using the Nakajima test on AA8011 sheets with a thickness of 1.0 mm. Tests were conducted at ambient temperature, 100°C, and 150°C, with a strain rate of 0.01 mm/s. Different specimen geometries (R62.5, R50, R75) were used.
- Fractography: Failed specimens were examined using a scanning electron microscope (SEM) to analyze fracture surfaces and understand material failure mechanisms.
Analysis Method:
- Forming Limit Diagram (FLD) Analysis: FLDs were generated experimentally and numerically to assess the formability limits of AA8011 at different temperatures. Major and minor strains were analyzed to construct the FLDs.
- Finite Element (FE) Simulations: LS-Dyna software was used to simulate the Nakajima test. Material properties and process parameters were input into the model. Simulation results included stress distribution, strain distribution, and displacement.
- Limiting Dome Height (LDH) Measurement: LDH was measured to quantify the formability of AA8011 at different temperatures.
- Comparison of Experimental and Simulation Results: Simulation results were validated by comparing them with experimental data, particularly the FLDs and LDH values.
Research Subjects and Scope:
The research focused on Aluminium Alloy AA8011 sheets with a thickness of 1.0 mm. The study investigated the formability of this material under stretch forming conditions using the Nakajima test. The scope included:
- Material: Aluminium Alloy AA8011.
- Temperatures: Ambient temperature, 100°C, and 150°C.
- Strain rate: 0.01 mm/s.
- Specimen geometries: R62.5, R50, and R75 (radii of curvature for Nakajima test specimens).
- Analysis techniques: Nakajima test, FLD analysis, FE simulations (LS-Dyna), fractography (SEM), LDH measurement.
6. Main Research Results:
Key Research Results:
- Temperature Effect on Restricting Stresses: The material's restricting stresses increased as temperatures increased.
- Forming Limit Diagrams (FLDs): FLDs were generated for AA8011 at ambient temperature, 100°C, and 150°C, both experimentally and through LS-Dyna simulations (Figure 5 and Figure 10). The minimal error between experimental and simulated FLDs at 150°C was noted.
- Limiting Dome Height (LDH): LDH was observed to increase with temperature, indicating improved formability at higher temperatures (Figure 8). Drawing AA8011 at 150°C was found to be more feasible.
- Simulation Results: LS-Dyna simulations provided detailed insights into stress (Figure 11), plastic strain (Figure 12), and displacement (Figure 13) distributions during the stretch forming process. The R62.5 geometry showed the maximum effective stress.
- Microstructure Analysis: Microstructure evaluation indicated that all tested specimens exhibited brittle fractures.
- Failure Modes: Failure and binding were observed in dome-shaped cups during testing (Figure 6).
Analysis of presented data:
- FLD Analysis (Figure 5 & 10): The FLD plots (Figure 5 and Figure 10) illustrate the forming limits of AA8011 at different temperatures. Figure 5 shows experimental FLDs for 300°C, 150°C, and RT (Room Temperature), indicating how major strain varies with minor strain at the onset of necking. Figure 10 compares the experimental FLD with the FEA-generated FLD, showing a reasonable agreement. Table 4 quantifies the experimental and simulation results for major and minor strains for different specimen dimensions (R75, R62.5, R50), demonstrating consistency between experimental and simulation outcomes.
- LDH Variation (Figure 8): Figure 8 shows the variation of Limiting Dome Height (LDH) with the width of the sample at different temperatures (0.1/s strain rate, 300°C, 150°C, RT). The graph indicates that LDH generally increases with temperature, suggesting enhanced formability at higher temperatures.
- Stress, Strain, and Displacement Simulations (Figure 11, 12, 13): Figures 11, 12, and 13 present simulation results for effective stress, effective plastic strain, and resultant displacement, respectively, for different specimen geometries (R75, R50, R62.5). Figure 11 shows that the R62.5 geometry experiences the maximum effective stress. Figure 12 indicates the distribution of effective plastic strain, with the highest values near the center for R62.5 and R75, and near the dome's margins for R50. Figure 13 illustrates the resultant displacement, with the R63.5 sample showing a larger blow relocation.
- Load vs Displacement Graph (Figure 7): Figure 7 displays the Load vs Displacement graph for different specimen radii (R75, R50, R62.5) at various temperatures (RT, 150°C, 300°C). This graph shows the force required for deformation and failure at different conditions, indicating the material's response to stretch forming.
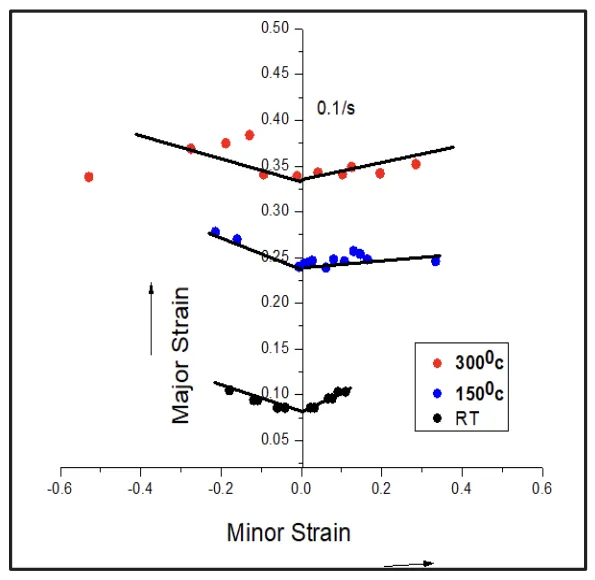
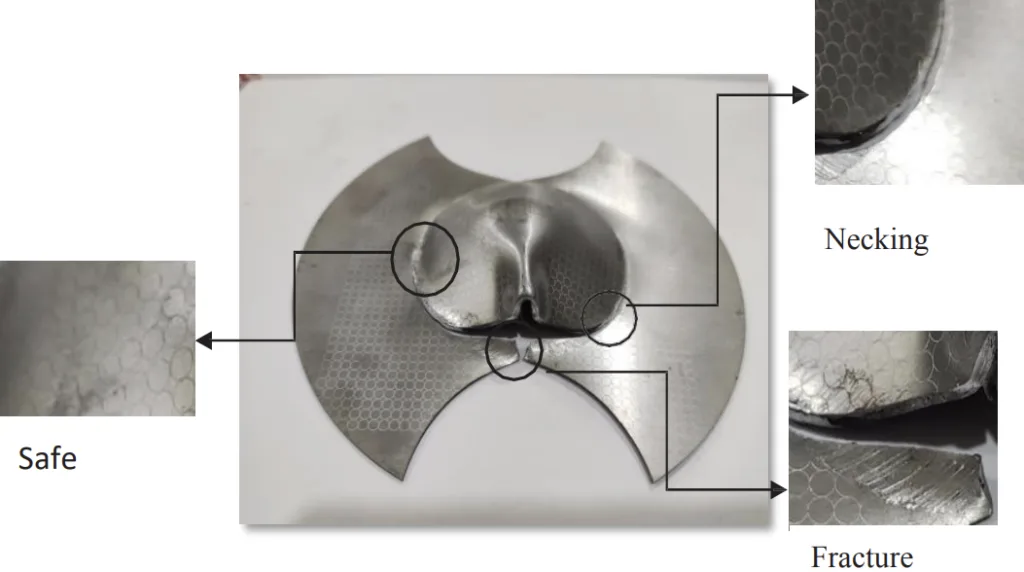
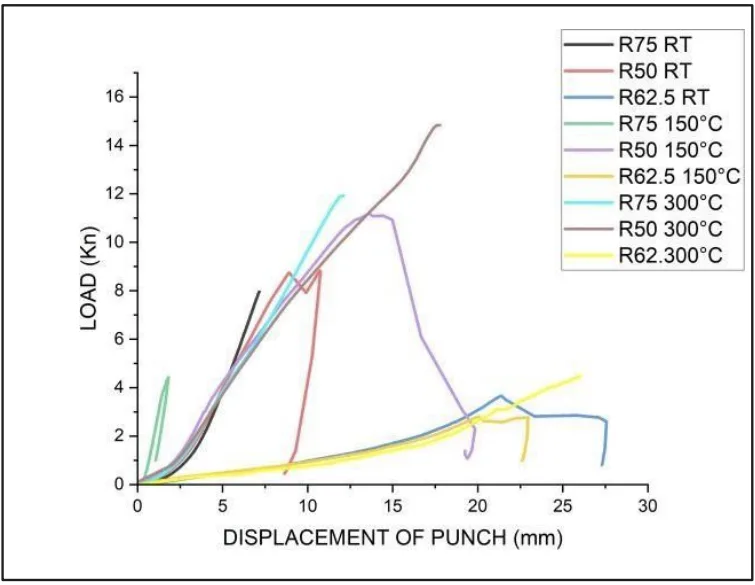
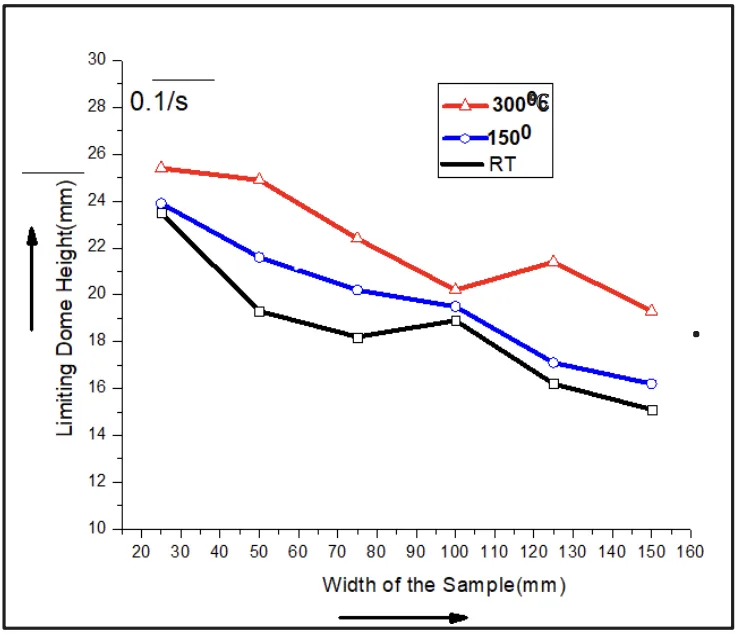
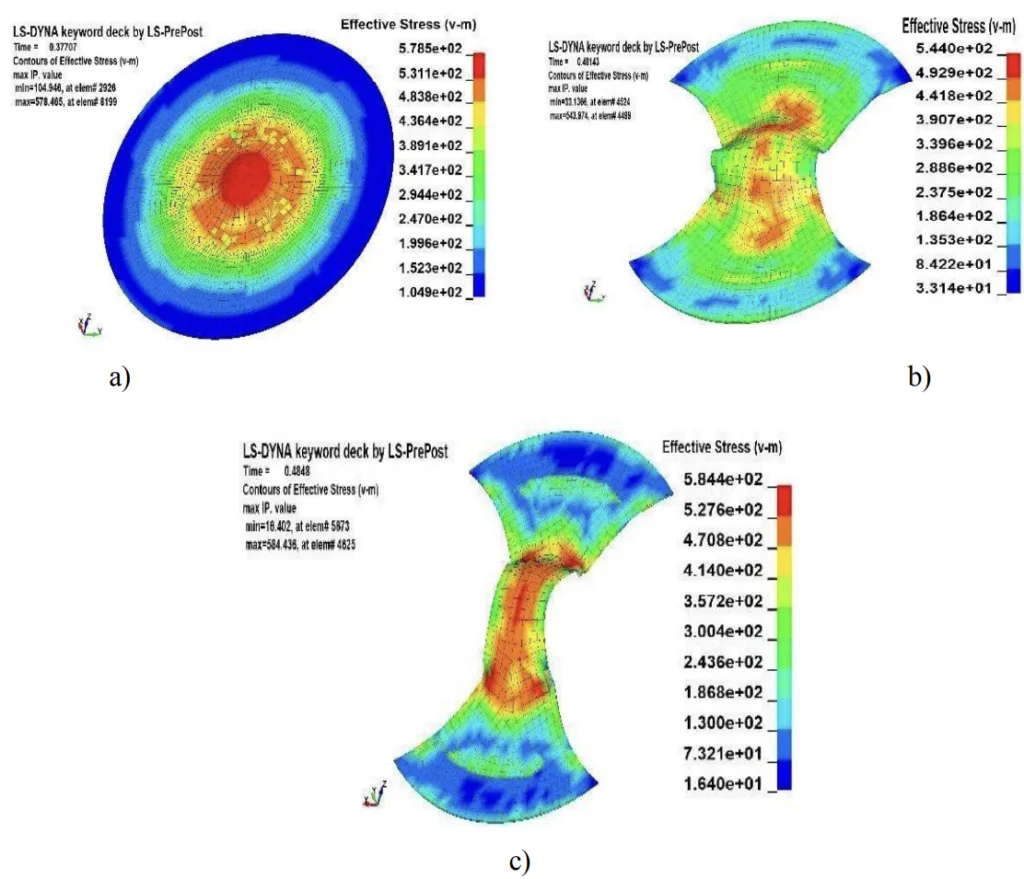
Figure Name List:
- Fig. 1. FLD
- Fig. 2. a) Experimental setup; b) Schematic Diagram
- Fig. 3. specimens for Nakazima test a) R62.5; b) R50; c) R75
- Fig.4. a) 3D model for stretch forming; b) Finite element model
- Fig. 5. FLD for different temperatures 300,150 and RT
- Fig.6. Necking, Failure, and Safe Regions of The Dome-Shaped Specimen
- Fig. 7. Load vs Displacement graph
- Fig. 8. variation of LDH
- Fig. 9. comparison between the experimental sample and simulation result
- Fig. 10. FLD generated by experiment and FEA
- Fig. 11. Simulations result of a) R75; b) R50; c) R62.5
- Fig. 12. Simulations result of a) R75; b) R50; c) R62.5
- Fig. 13. Simulations result of resultant displacement a) R75; b) R50; c) R62.5
7. Conclusion:
Summary of Key Findings:
This study investigated the formability of AA8011 aluminum alloy at different temperatures using experimental Nakajima tests and FE simulations. Key findings include:
- Increased temperature leads to higher restricting stresses in AA8011.
- Forming Limit Diagrams (FLDs) for AA8011 were successfully developed for ambient, 100°C, and 150°C temperatures, with good agreement between experimental and simulated FLDs, especially at 150°C.
- Limiting Dome Height (LDH) increases with temperature, indicating improved formability at elevated temperatures. Drawing AA8011 at 150°C is more feasible.
- LS-Dyna simulations effectively predicted stress, strain, and displacement distributions during stretch forming, with the R62.5 geometry experiencing maximum stress.
- Microstructure analysis revealed brittle fracture in all tested specimens.
- Dome-shaped cup tests showed failure and binding phenomena.
Academic Significance of the Study:
This research contributes to the fundamental understanding of the formability behavior of AA8011 aluminum alloy at elevated temperatures. The developed FLDs and validated simulation model provide valuable data for predicting and analyzing the forming limits of this material under warm forming conditions.
Practical Implications:
The findings offer practical insights for optimizing sheet metal forming processes for AA8011. The demonstrated improvement in formability at 150°C suggests that warm forming techniques can be effectively employed to enhance the manufacturability of complex shapes from AA8011 sheets, potentially leading to more efficient and successful sheet metal forming operations in industries like automotive and aerospace.
Limitations of the Study and Areas for Future Research:
The paper does not explicitly state limitations or areas for future research.
8. References:
- [1] Nitin Kotkunde, Amit Kumar Gupta, Prudvi Reddy Paresi, Swadesh Kumar Singh, Materials Today: Proceedings Volume 4, Issue 4, 2017.
- [2] Jayahari Lade ,Dharavath Baloji ,M.Sai sharath ,G.Rajul ,Anil Kalluri , A.Anitha Lakshmi , Minakshi Memoria “Finite Element Analysis on Experimental Stretch
- [3] Forming Process of AA2014 Alloy at 423 to 623K Temperatures”, E3S Web of Conferences, 011 (2023) ICMPC 2023
- [4] Jürgen HIRSCH, Transactions of Non ferrous Metals Society of China, Volume 24, Issue 7, (July 2014).
- [5] TolgaDursun, Costas Soutis, Materials & Design (1980-2015) Volume 56, (April 2014),
- [6] R. Baloji Naik, D. Ratna, S.K. Singh.” Synthesis and characterization of novel hyperbranched alkyd and isocyanate trimer based high solid polyurethane coatings” Progress in Organic Coatings Volume 77, Issue 2, February 2014, Pages 369-379
- [7] .S. P. Ringer, T. Sakurap And I. J. Polmear, Acta Materialia, Volume 45, Issue 9, September 1997
- [8] Naik, R.B., Ratna, D., Singh, S.K., Synthesis and characterization of novel hyperbranched alkyd and isocyanate trimer based high solid polyurethane coatings, Progress in Organic Coatings, 2014, 77(2), pp. 369–379
- [9] Tanya Buddi, Susmitha Valli Gogula, Kuldeep K. Saxena, Manufacturing and Evaluation of Mechanical Properties for Rice Husk Particle Board Using IoT, Indian Journal of Engineering & Materials Sciences: Volume 29, Issue 6, December 2022
- [10] B Dharavath, MT Naik, A Badrish, T Buddi, Experimental and Finite Element Studies of Stretch Forming Process for ASS 316L at Elevated Temperature, Indian Journal 2022 - ischolar.sscldl.in Volume 29, Issue 6, December 2022
- [11] B. Taleb Araghi, G.L. Manco, M. Bambach, G. Hirt” Investigation into a new hybrid forming process: Incremental sheet forming combined with stretch forming” CIRP Annals Volume 58, Issue 1, 2009, Pages 225-228K.
- [12] Woei-Shyan Lee, Chi-Feng Lin” Plastic deformation and fracture behaviour of Ti-6Al-4V alloy loaded with high strain rate under various temperatures” Plastic deformation and fracture behaviour of Ti-6Al-4V alloy loaded with high strain rate under various temperatures
- [13] Ji He, Z. Cedric Xia, Xinhai Zhu, Danielle Zeng, Shuhui Li, Sheet metal forming limits under stretch-bending with anisotropic hardening, International Journal of Mechanical Sciences Volume 75, October 2013, Pages 244-256
- [14] S. Qin, H.M. Shang, C.J. Tay, J. Mo “Stretching during axisymmetrical forming of sheet metal"Journal of Materials Processing Technology Volume 63, Issues 1–3, January1997,Pages117-122
- [15] Sandeep Pandre, Ayush Morchhale,Nitin Kotkunde &Swadesh Kumar Singh" Influence of processing temperature on formability of thin-rolled DP590 steel sheet"Pages 901-909 | Received 03 Feb 2020, Accepted 09 Mar 2020, Published online: 21 Apr 2020
- [16] Xugang Wang, Xiaobo Fan, Xianshuo Chen, Shijian Yuan, Journal of Materials Processing Technology Volume 306, August 2022
- [17] R. Karthik Rao, Phaneendra Babu Bobba , T. Suresh Kumar , Satyanarayana Kosaraju, Feasibility analysis of different conducting and insulation materials used in laminated busbars. Materials Today: Proceedings, 2019, 26, pp. 3085–3089
- [18] Lade Jayahari, P.V. Sasidhar, P. Prudvi Reddy, B. BaluNaik, A.K. Gupta, Swadesh Kumar Singh, Formability studies of ASS 304 and evaluation of friction for Al in deep drawing setup at elevated temperatures using LS-DYNA, Journal of King Saud University - Engineering Sciences, Volume 26, Issue 1, 2014, Pages 21–31.
- [19] J. Pavan Kumar, R. Uday Kumar, B. Ramakrishna, B. Ramu and K. Baba Saheb 2nd International Conference on Advancements in Aeromechanical Materials for Manufacturing, volume 455, July 2018.
- [20] Nejia Ayachi, Noamen Guermazi, Cong Hanh Pham. Metals 2020, 10(9), 116, August 2020.
- [21] L. Venugopal, M. J. Davidson & Material and manufacturing process, volume 28, issue 3, 2013
- [22] Suresh Kumar Tummala, Phaneendra Babu Bobba & Kosaraju Satyanarayana (2022) SEM & EDAX analysis of super capacitor, Advances in Materials and Processing Technologies, 8:sup4, 2398–2409.
- [23] Lumelskyja, J. Rojeka, L. Lazarescub, D. Banabic, Procedia Manufacturing, Volume 27, 2019
- [24] B. J. Varghese, P. B. Bobba and M. Kavitha, “Effects of coil misalignment in a four coil implantable wireless power transfer system,” 2016 IEEE 7th Power India International Conference (PIICON), Bikaner, India, 2016, pp. 1–6
- [25] Mahalle G, Morchhale A, Kotkunde N, Gupta AK, Singh SK, & Lin Y C, J Manuf Processes, (2020) 482.
- [26] L. Venugopal, M. J. Davidson & N. SelvarajMaterial and manufacturing process, volume 28, issue 3,2013.
9. Copyright:
- This material is "Kuraku Ratna Babu, sattenapelli prashanth, Kethe Ganesh, Gone kiran kumar"'s paper: Based on "Experimental Material Characterization and Formability studies on Aluminium Alloy (AA 8011)".
- Paper Source: https://doi.org/10.1051/e3sconf/202455201066
This material was created to introduce the above paper, and unauthorized use for commercial purposes is prohibited.
Copyright © 2025 CASTMAN. All rights reserved.