This article introduces the paper ["Prediction and Evaluation of Ejecting Stress Distribution at Die Surface of Die-Casting through Numerical Analyses"] published by ['電気製鋼'].
1. Overview:
- Title: Prediction and Evaluation of Ejecting Stress Distribution at Die Surface of Die-Casting through Numerical Analyses
- Author: Masamichi KAWANO, Satoshi UNO and Naoki YOKOI
- Publication Year: 2017
- Publishing Journal/Academic Society: 電気製鋼, Vol. 88, No. 1, pp. 33-38
- Keywords: Die casting, Ejecting stress, Soldering, Numerical analysis, MAGMASOFT, Fe-Al compound layer, AMICOAT®-D
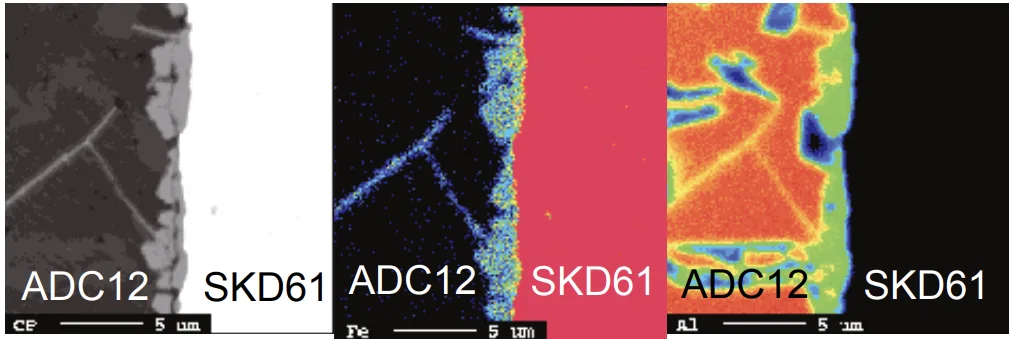
2. Abstracts or Introduction
In die casting, molten metal such as aluminum alloy is injected into a die cavity at high speed and solidified rapidly to efficiently produce complex shaped parts with high dimensional accuracy. However, the cavity surface of die casting dies can reach temperatures of 450~550°C due to contact with molten metal at 600~700°C. In these high-temperature regions, "soldering," where aluminum alloy adheres and remains on the die during part ejection, tends to occur. Soldering leads to the formation of a Fe/Al reaction layer at the interface between the casting and the die.
Soldering degrades the surface quality and dimensional accuracy of products. Removing adhered aluminum alloy from the die necessitates temporary suspension of casting, significantly reducing productivity. Severe soldering that is difficult to remove can even require die replacement, increasing die costs. Therefore, preventing soldering is a critical issue in die casting. In formulating casting plans, it is essential to identify areas prone to soldering and implement countermeasures.
Factors influencing soldering are diverse, including surface treatment type, internal cooling channel location and water flow rate, molten metal temperature, and injection conditions. Optimizing these factors through trial and error in casting is inefficient and may not yield the optimal solution. Consequently, melt flow analysis, which allows for systematic and easy variation of conditions, is frequently utilized for examining soldering countermeasures.
In melt flow analysis-based soldering countermeasure studies, a metric based on metallurgical phenomena (Fe/Al reaction layer formation due to diffusion) is needed to enhance process design accuracy. Therefore, this paper focuses on "ejecting stress" when removing the casting from the die and attempts to correlate it with reaction layer formation. This paper incorporates an experimentally derived ejecting stress prediction formula into melt flow analysis to validate its effectiveness as a soldering evaluation index.
3. Research Background:
Background of the Research Topic:
Soldering in die casting is a significant problem because it impairs product quality and dimensional precision, necessitates production halts for aluminum removal from dies, and potentially leads to costly die replacements. Thus, avoiding soldering is a crucial objective in die casting operations. Identifying soldering-prone areas and implementing effective countermeasures are essential for robust process design.
Status of Existing Research:
Conventional approaches to mitigate soldering often rely on inefficient trial-and-error adjustments of casting parameters. While melt flow analysis is increasingly used to explore soldering countermeasures, these methods often lack a quantitatively robust metric grounded in the metallurgical mechanisms of soldering. Optimizing through casting trials is inefficient and may not lead to optimal solutions. Melt flow analysis is actively used to systematically and easily change conditions for examining soldering countermeasures.
Necessity of the Research:
To improve the accuracy of process design using melt flow analysis for soldering countermeasures, a metric that aligns with metallurgical phenomena, specifically Fe/Al reaction layer formation, is required. There is a need for a reliable indicator that reflects the degree of soldering based on the underlying metallurgical reactions at the die-casting interface.
4. Research Purpose and Research Questions:
Research Purpose:
The purpose of this research is to develop a method for predicting and evaluating ejecting stress distribution at the die surface in die casting, based on the formation of the Fe/Al reaction layer, which is the root cause of soldering. By incorporating an experimentally derived formula for ejecting stress into melt flow analysis software, the study aims to validate the ejecting stress as an effective index for evaluating soldering potential.
Key Research:
The key research question is to establish the ejecting stress as a quantitative metric for assessing soldering risk in die casting. This involves:
- Deriving a formula to predict ejecting stress based on the Fe/Al reaction layer formation.
- Integrating this formula into melt flow analysis.
- Validating the ejecting stress as a reliable indicator for soldering through numerical analysis and experimental verification.
5. Research Methodology
Research Design:
This research employed a numerical analysis approach using MAGMASOFT software to simulate melt flow and temperature distribution during die casting. The derived ejecting stress formula, based on Fe/Al compound layer formation, was integrated into the software to predict ejecting stress distribution on the die surface.
Data Collection Method:
Experiments were conducted using a 135-ton Toshiba Machine DC-135JT die-casting machine to quantify ejecting resistance. A core-pin like specimen made of SKD61 was used, and ADC12 aluminum alloy was cast. Thermocouples were inserted near the surface of the core pin to measure temperature. Ejecting load was measured using a load cell at the back of the ejector pin.
Analysis Method:
The ejecting resistance F (MPa) was calculated by dividing the ejecting load PN (measured by the load cell) by the surface area of the ejector pin. The soldering parameter S, related to Fe/Al reaction layer formation, was calculated using the integral of exp(-Q/R/Ts) over time. The correlation between the soldering parameter S and the ejecting stress F was analyzed. FEM (Finite Element Method) analysis was used to estimate the surface temperature Ts by correlating thermocouple measurements with thermal analysis results.
Research Subjects and Scope:
The study focused on the interface between SKD61 die steel and ADC12 aluminum alloy, which are commonly used in die casting. The scope of the research was to predict and evaluate the ejecting stress at the die surface under various die casting conditions, including molten metal temperature, die cooling, and surface treatment.
6. Main Research Results:
Key Research Results:
- Ejecting Stress Formula Derivation: An equation for ejecting stress at the die surface was derived by considering the Fe-Al compound layer formation at the boundary between SKD61 and ADC12. The activation energy Q for Fe-Al reaction was estimated to be 313 kJ/mol.
- Influence of Casting Conditions: Numerical results indicated that lower molten ADC12 temperature and die cooling using inner water lines effectively reduce ejecting stress.
- Effect of Surface Treatment: A significant reduction in ejecting stress was observed with "AMICOAT®-D" surface treatment, even under high molten ADC12 temperature conditions without internal water cooling.
- Correlation between S and F: A clear positive correlation between the soldering parameter S (related to Fe/Al reaction layer thickness) and ejecting stress F was established, represented by the formula F = C1⋅SC2.
Analysis of presented data:
- Figure 3: Shows the difference between (a) ejecting load P and (b) ejecting stress F. Ejecting stress F, compensated for the core-pin surface area, provides a size-independent measure of soldering severity. Figure 3(b) indicates a temperature-sensitive region for soldering, with ejecting stress doubling from 5 MPa to 10 MPa with a 14°C temperature increase around 432°C.
- Figure 5: Illustrates the transition change of (a) surface temperature Ts and (b) soldering parameter S=∫(exp(-Q/R/Ts))dt. The soldering parameter S, representing the integrated thermal history relevant to Fe/Al reaction, is shown to correlate with ejecting stress.
- Figure 6: Depicts the relationship between soldering parameter S and ejecting stress F. Surface treatments like Salt-bath nitrocarburizing (PS) and PVD (AMICOAT®-D) significantly reduce ejecting stress compared to Non-coat.
- Figure 9: Shows the distribution of cast ejecting stress F under different conditions. Figure 9(a) (700°C molten metal, no cooling) exhibits the highest ejecting stress. Lowering molten metal temperature to 650°C (Figure 9(b)), applying water cooling (Figure 9(c)), and using AMICOAT®-D surface treatment (Figure 9(d)) all effectively reduce ejecting stress.
Figure Name List:
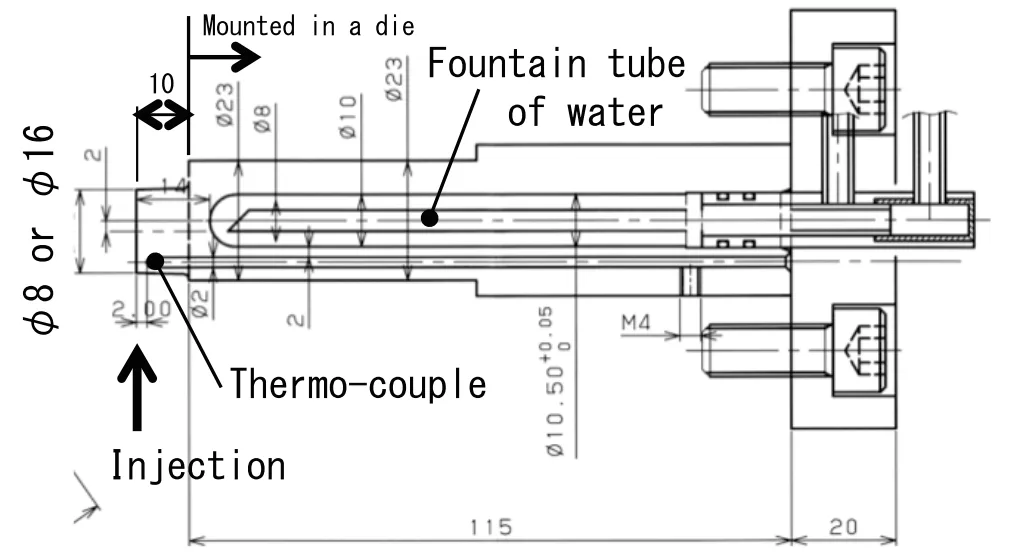
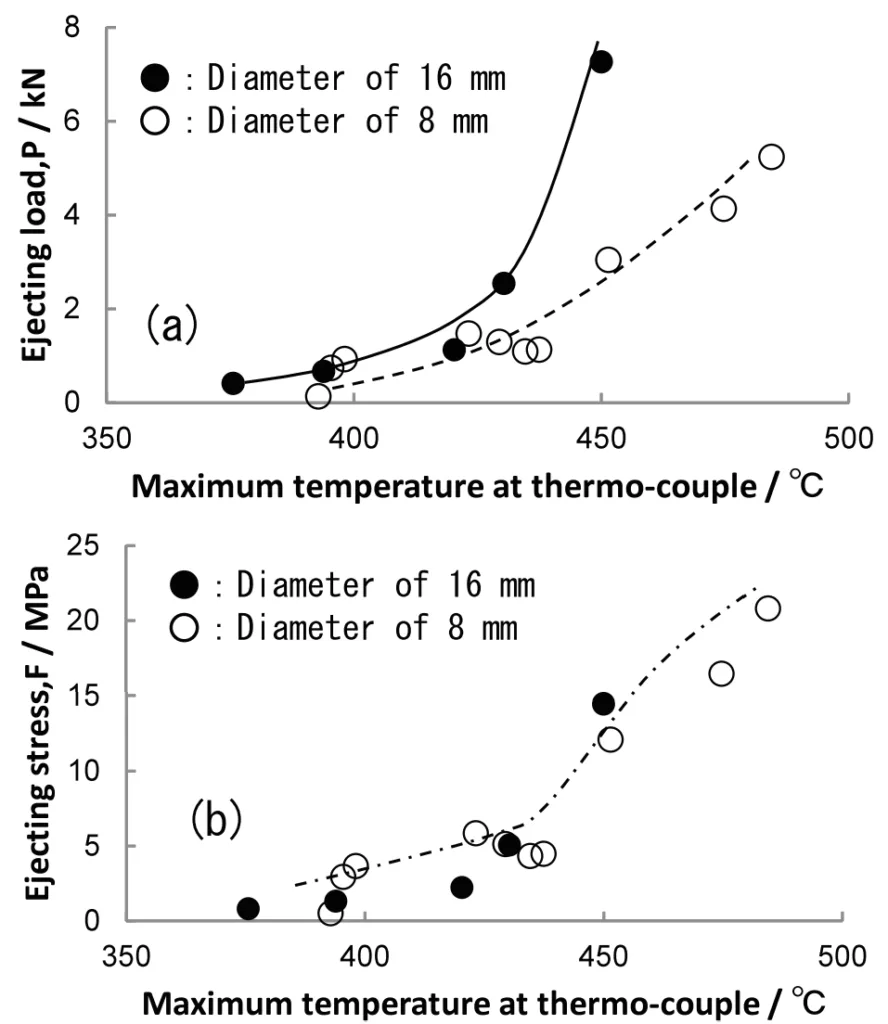

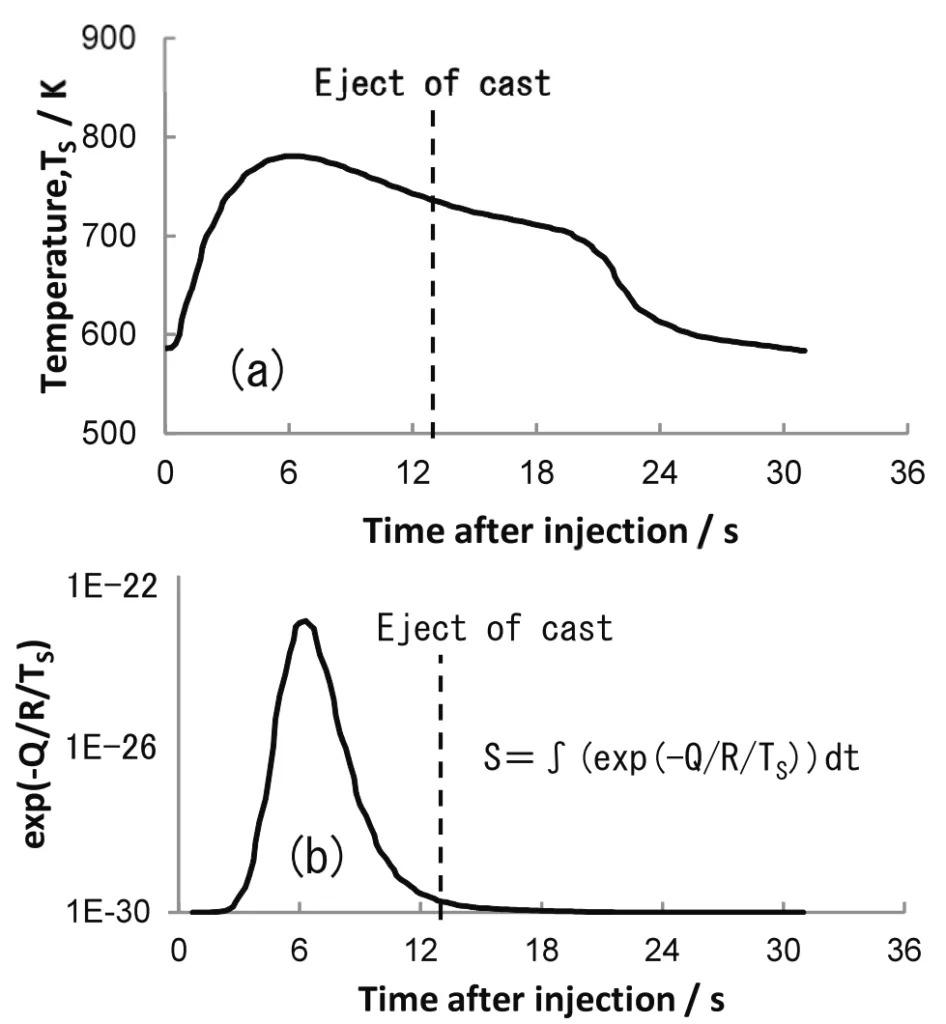
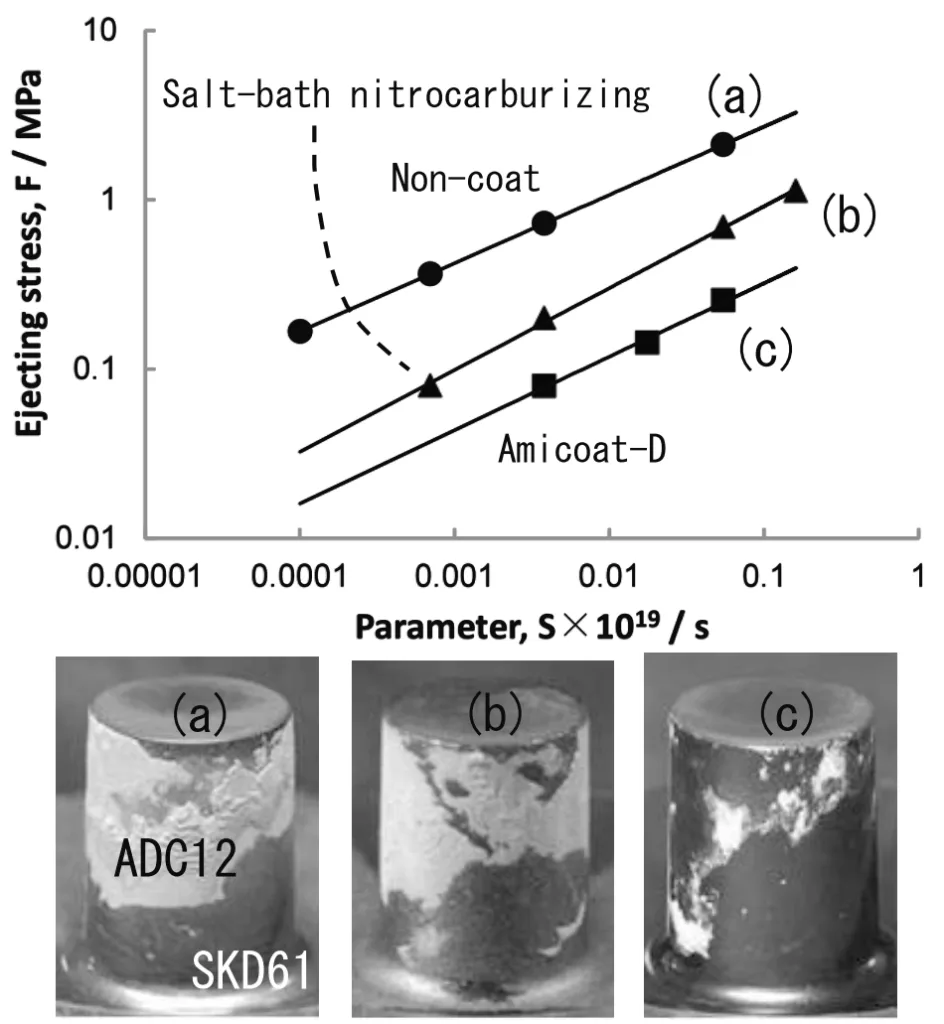
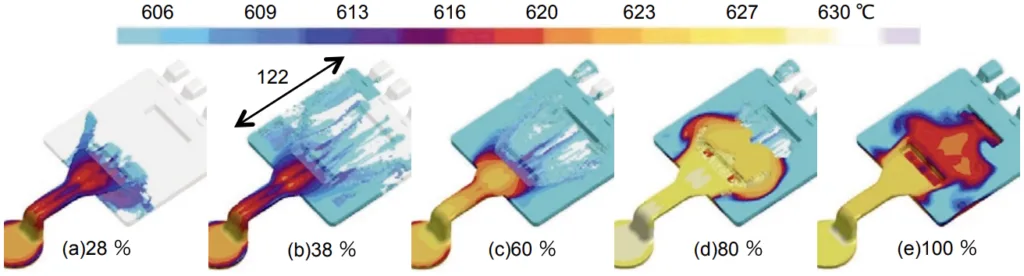
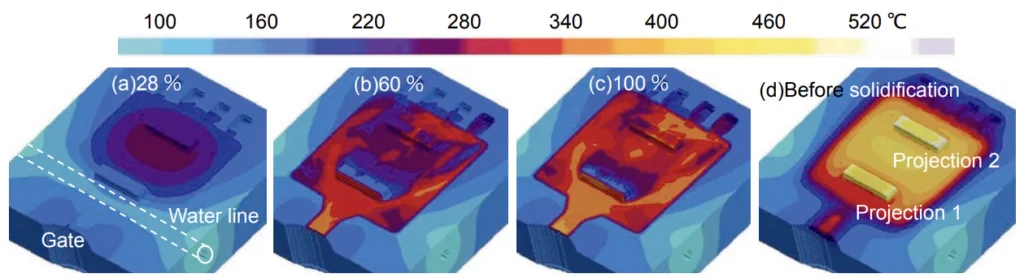
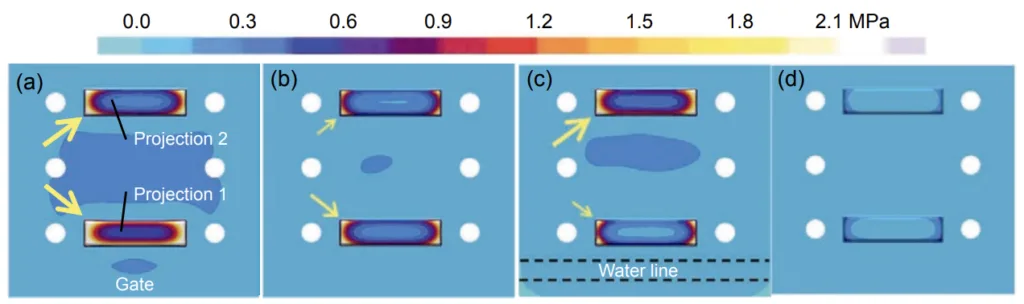
- Fig. 1. Distribution of Fe and Al at soldering part. Fe/Al compound layer is observed.
- Fig. 2. Core-pin like specimen of soldering experiment on die-casting. Dimension is given in millimeters. Specimen is mounted in a die located close to the injection gate. A thermo-couple is inserted at 1 mm below the surface of the specimen.
- Fig. 3. Difference between (a) ejecting load P and (b) ejecting stress F. F is given by considering the surface area of core-pin then size effect is compensated.
- Fig. 4. Estimated temperature distribution through FE-analysis. Marked influence of (a) time and (b) depth from a surface on temperature can be seen.
- Fig. 5. Transition change of (a) surface temperature Ts and (b) soldering parameter S=f(exp(-Q/R/Ts))dt.
- Fig. 6. Relationship between soldering parameter S and ejecting stress F.
- Fig. 7. Flow behavior and temperature of molten ADC12 in a cavity. Filling rate given by volume fraction represent from (a) 28 percent up to (e) 100 percent.
- Fig. 8. Transition of die temperature. Filling rate of molten ADC12 represent (a) 28 percent up to (c) 100 percent. At 6 seconds after filling corresponds to (d) just before finish of solidification.
- Fig. 9. Distribution of cast ejecting stress F. (a), (b), (c) and (d) represent molten ADC12 of 700 °C, molten ADC12 of 650 °C, water cooling line in a die with molten ADC12 of 700 °C and surface treatment “AMICOAT®-D" with molten ADC12 of 700°C under the condition of no internal water cooling respectively.
7. Conclusion:
Summary of Key Findings:
This research successfully formulated and validated ejecting stress as a quantitative index for soldering evaluation in die casting. Key findings include:
- Derivation of an ejecting stress formula based on Fe/Al reaction layer formation, with an estimated activation energy Q of 313 kJ/mol.
- Confirmation that lower molten metal temperature, die cooling, and AMICOAT®-D surface treatment effectively reduce ejecting stress.
- Establishment of a correlation between soldering parameter S and ejecting stress F, enabling prediction of soldering potential through melt flow analysis.
Academic Significance of the Study:
This study introduces a novel, objective, and temperature-sensitive metric, ejecting stress F, for evaluating soldering risk in die casting. Unlike conventional subjective methods relying on critical temperatures, ejecting stress provides a quantitative measure directly linked to the metallurgical phenomenon of Fe/Al reaction layer formation.
Practical Implications:
The ejecting stress F can be utilized as a practical indicator for process design and optimization in die casting. By predicting ejecting stress distribution through melt flow analysis, engineers can quantitatively assess the effectiveness of various soldering countermeasures, such as adjusting casting conditions, optimizing cooling systems, and selecting appropriate surface treatments. The guideline for process design is to ensure that the ejecting stress F does not exceed the strength or tensile strength of the casting.
Limitations of the Study and Areas for Future Research:
While the study provides a valuable framework for soldering evaluation, further research could explore the influence of other factors such as die surface roughness, ejection speed, and different alloy systems on ejecting stress and soldering behavior. Further validation across a broader range of die casting processes and geometries would also strengthen the general applicability of the ejecting stress metric.
8. References:
- 1) 青山俊三,下条浩:鋳造工学会 131回全国講演大会講演概要集(1997), 94.
- 2) 柴田浩二,諸住正太郎,幸田成康:日本金属学会誌, 30(1966), 382.
- 3) 伊吹基宏,尾崎公造:電気製鋼,76(2005), 241.
- 4) 西直美:鋳造工学,70(1998), 648.
- 5) 三中西信治,小川裕二,鈴木孝尚:鋳造工学会 130回全国講演大会講演概要集(1997), 54.
- 6) 特開2011-79053.
- 7) 西田公至:生産研究,28(1976), 464.
- 8) http://www.zerocut-watanabe.co.jp/pg321.html
9. Copyright:
- This material is "Masamichi KAWANO, Satoshi UNO and Naoki YOKOI"'s paper: Based on "Prediction and Evaluation of Ejecting Stress Distribution at Die Surface of Die-Casting through Numerical Analyses".
- Paper Source: [DOI URL will be added if available, otherwise use paper source information]
This material was created to introduce the above paper, and unauthorized use for commercial purposes is prohibited.
Copyright © 2025 CASTMAN. All rights reserved.