This introduction paper is based on the paper "NOTCH EFFECT ON FATIGUE STRENGTH OF DIE CAST AM60 MAGNESIUM ALLOY" published by "Asian Pacific Conference for Materials and Mechanics 2009 at Yokohama, Japan, November 13-16".
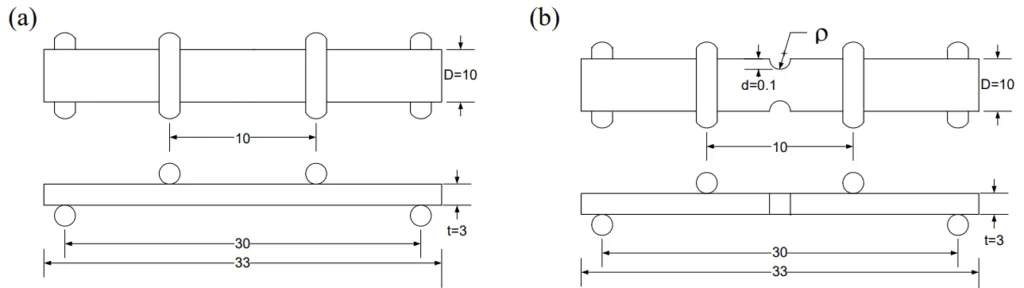
1. Overview:
- Title: NOTCH EFFECT ON FATIGUE STRENGTH OF DIE CAST AM60 MAGNESIUM ALLOY
- Author: Md. Shahnewaz Bhuiyan, Youshiharu Mutoh, Yukio Miyashita, Yuichi Ostuka, Toshikatsu Koike
- Year of publication: 2009
- Journal/academic society of publication: Asian Pacific Conference for Materials and Mechanics 2009 at Yokohama, Japan, November 13-16
- Keywords: AM60 magnesium alloy, die cast, fatigue strength, notch effect, stress concentration factor, fatigue notch sensitivity (Keywords are inferred as they are not explicitly listed in the paper)
2. Abstract:
This study investigates the notch effect on the fatigue strength of die-cast AM60 magnesium alloy. Four-point bending tests were performed using smooth specimens and notched specimens with varying stress concentration factors (Kt). The results indicated that fatigue life and fatigue limit decreased with increasing Kt up to a certain point (Kt=2.55), beyond which further increases in Kt did not significantly alter fatigue strength. The fatigue limit for notched specimens was found to correspond to the fatigue crack initiation limit, as no non-propagating cracks were observed. Cracks consistently initiated at the notch root, and internal casting porosity did not influence these results. The notch sensitivity of the AM60 alloy initially increased with Kt (from 1.57 to 2.09) and then decreased with further increases in Kt.
3. Introduction:
Magnesium alloys are gaining prominence in aerospace and automobile industries due to their low density, high specific strength, excellent castability, and machinability. Structural components in these applications often demand excellent fatigue properties. While many studies have focused on the fatigue properties of magnesium alloys under various environmental conditions, understanding fatigue notch sensitivity is crucial for engineering applications. Geometrical discontinuities like shoulders, keyways, and grooves act as notches, leading to stress concentrations where fatigue failure frequently initiates. Therefore, investigating the fatigue strength of notched parts is important, especially for emerging materials like magnesium alloys. This study performed four-point bending tests to understand the notch effect on the fatigue strength of die-cast AM60 magnesium alloy using specimens with different stress concentration factors (Kt).
4. Summary of the study:
Background of the research topic:
Magnesium alloys are increasingly utilized in sectors like aerospace and automotive due to their advantageous properties such as low density and high specific strength. A critical requirement for many structural components made from these alloys is excellent fatigue performance.
Status of previous research:
Previous research on magnesium alloys has largely concentrated on their fatigue properties under ambient and corrosive conditions. However, for practical engineering design, information on fatigue notch sensitivity is vital because the fatigue performance of components with notches can be significantly worse than that of smooth bodies, even if the latter exhibit good fatigue performance. Notches are common in engineering components and are primary sites for fatigue failure due to stress concentration.
Purpose of the study:
The purpose of this study was "to understand the notch effect on the fatigue strength of die-cast AM60 magnesium alloy by using constant depth notched specimens with different stress concentration factors, Kt."
Core study:
The core of the study involved conducting four-point bending fatigue tests on die-cast AM60 magnesium alloy. Both smooth specimens and notched specimens were tested. The notched specimens featured a constant notch depth (0.1 mm) but varied in notch root radii (ρ = 1 mm, 0.3 mm, 0.25mm, 0.15 mm, 0.1 mm) to achieve different theoretical stress concentration factors (Kt = 1.57, 2.09, 2.19, 2.55, 2.90). The study focused on analyzing S-N curves, fracture surfaces, fatigue notch factor (Kf), and notch sensitivity (q).
5. Research Methodology
Research Design:
- Material: The material used was die-cast AM60 magnesium alloy. Its chemical composition was Al 5.5-6.5, Mn 0.13, Si 0.5, Cu 0.35, Zn 0.22, Ni 0.03 (in mass%). The mechanical properties are listed in Table 1.
- Table 1 Mechanical properties of the material used
Yield stress σ₀.₂ (MPa) | Tensile strength σᴮ (MPa) | Elongation % | Young's Modulus E (GPa) |
---|---|---|---|
103 | 224 | 9.0 | 43 |
- Specimen Preparation: Smooth (Figure 1(a)) and notched (Figure 1(b)) specimens were prepared. Notched specimens had semicircular side notches with a depth (d) of 0.1 mm and five different radii (ρ) of 1 mm, 0.3 mm, 0.25mm, 0.15 mm, and 0.1 mm. These corresponded to theoretical stress concentration factors (Kt) of 1.57, 2.09, 2.19, 2.55, and 2.90, respectively. Specimen surfaces were polished up to 1200 grid emery paper, annealed in vacuum at 270°C for 30 minutes to remove residual stress, and finally polished with 6 μm diamond paste.
- Fatigue Testing: Four-point bending tests were performed using a servo-hydraulic testing machine with a 2KN load capacity.
Data Collection and Analysis Methods:
- Test Conditions: Tests were conducted using a sinusoidal waveform at a frequency of 20 Hz and a stress ratio (R) of 0.1. All tests were performed at 20°C with 55%RH.
- Test Duration: Fatigue tests were continued until complete failure of the specimen or stopped if the specimen did not fail up to 107 cycles (runout).
- Stress Concentration Factor (Kt): Calculated using the expression [5]:
Kt = 1 + [1 / (1.55(D/d) - 1.3(t/ρ))]n
where n = [(D/d - 1) + 0.5(t/ρ)] / [(D/d - 1) + (t/ρ)]
and d, D, t, and ρ are shown in Figure 1. - Observation: Specimen surfaces and fracture surfaces were observed in detail using a scanning electron microscope (SEM).
Research Topics and Scope:
The research focused on evaluating the effect of stress concentration on the fatigue properties of die-cast AM60 magnesium alloy. This included:
- Determination of S-N curves for smooth and notched specimens.
- Observation of fracture surfaces to identify crack initiation sites and the influence of material defects.
- Investigation of the existence of non-propagating cracks.
- Analysis of the relationship between the fatigue notch factor (Kf), the theoretical stress concentration factor (Kt), and the notch sensitivity (q).
6. Key Results:
Key Results:
- S-N Curves: The smooth AM60 specimen exhibited a fatigue strength of approximately 81 MPa at 107 cycles. For notched specimens, as the notch radius decreased (and consequently Kt increased), the S-N curves tended to become flatter (Figure 2).
- Fracture Surface Analysis: Fatigue cracks in notched specimens initiated at the notch root surface due to cyclic slip deformation (Figure 3). Casting porosity, often found in the middle region of the specimen thickness, was not observed at or near the crack nucleation site and thus did not influence the fatigue test results.
- Non-Propagating Cracks: SEM examination of runout specimens (those that did not fail after 107 cycles) revealed no non-propagating cracks at the notch root (Figure 4). This indicates that once a fatigue crack initiates from the notch, it continues to grow until failure. Therefore, the observed fatigue limits correspond to the threshold stresses for crack initiation.
- Fatigue Notch Factor (Kf) and Notch Sensitivity (q):
- The fatigue notch factor (Kf) values for the die-cast AM60 alloy were considerably lower than the theoretical stress concentration factor (Kt) values. The difference between Kt and Kf increased with increasing Kt, eventually tending to saturate at higher Kt values, suggesting that the material has low notch sensitivity (Figure 5).
- The notch sensitivity (q) of the die-cast AM60 alloy showed a specific trend with Kt: it increased as Kt increased from 1.57 to 2.09. However, further increases in Kt (beyond 2.09) led to a reduction in notch sensitivity (Figure 6(a)). This behavior is different from that observed in some steels (e.g., SUS304, AISI316 austenitic steel), where an inverse relationship is often seen (Figure 6(b)).
Figure Name List:
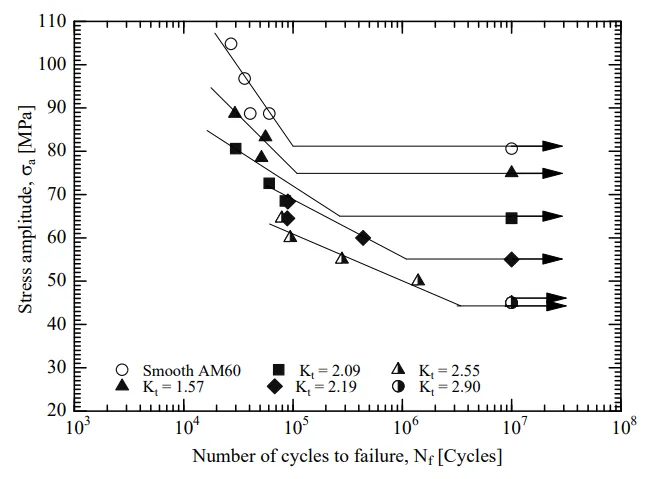
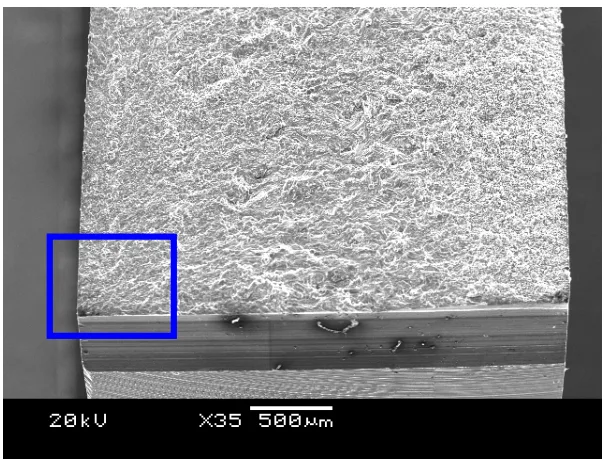
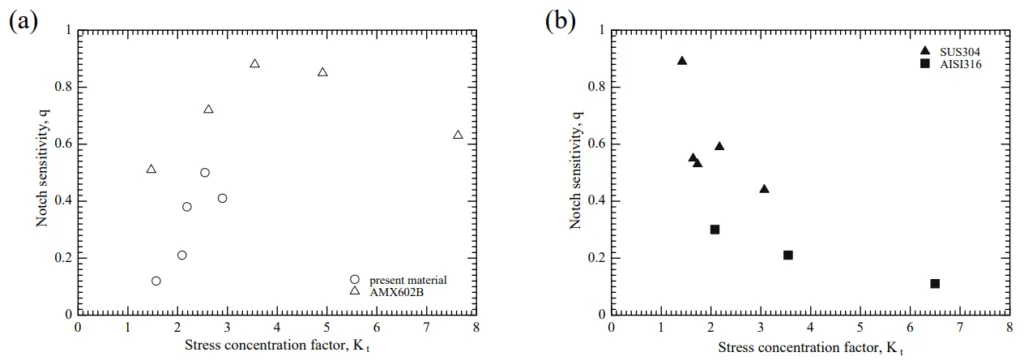
- Figure 1 Shape and dimensions of specimen (a) smooth specimen, (b) notched specimen (in mm)
- Figure 2 S-N curves for the smooth and notched specimens.
- Figure 3 SEM fractograph of fracture surface at crack nucleation region of the notched specimen tested at 100 MPa (Kt = 1.57).
- Figure 4 Magnified view near notched region of run out specimen showing the absence of non-propagating crack.
- Figure 5 Relationship between fatigue notch factor and stess concentration factor.
- Figure 6 Relationship between notch sensitivity and stress concentration factor, (a) magnesium alloy and (b) steel.
7. Conclusion:
From the four-point bending fatigue tests conducted to evaluate the effect of stress concentration on die-cast AM60 magnesium alloy, the following conclusions were summarized:
- The fatigue life and the fatigue limit decreased with increasing stress concentration factor from 1.57 to 2.55. Further increase in stress concentration factor did not affect the fatigue strength.
- The fatigue limit in die-cast AM60 for all the notched specimens corresponded to the fatigue crack initiation limit, because non-propagating cracks did not exist in the specimen at the fatigue limit.
- Fracture surface observation of all the notched specimens revealed that the crack was initiated from the notche root. Casting porosity was not observed near the crack nucleation site. Therefore, in the present test, casting defects, which were often found in the middle region of specimen thickness, did not influence the forgoing test results.
- With increasing stess concentration factor from 1.57 to 2.55, the notch sensitivity of the material also increased. Further increase in stress concentration factor induced the reduced notch sensitivity.
8. References:
- [1] Alan, A., Luo, JOM, 42-49, 2002.
- [2] Mordike, B.L., Ebert. T., Material Science and Engineering A, vol. 302, 37-45, 2001.
- [3] Ruden. T., Light Metal Age, 36-41, 2005.
- [4] Kulekci. M.K., Int J Adv Manuf Technol, DOI 10.1007/s00170-007-1279-2, 2007.
- [5] Heywood. R.B., Designing by Photoelasticity, Chapman & Hill, London, 163, 1952.
- [6] Awatani.J., Katagiri. K., Shiraishi. T., Matsuyama. T., J.Soc.Mater.Sci.Jpn. vol.25, 151, 1976.
- [7] Hatanaka. K., S. Shimizu. S., Bull, JSME, 25, 1982.
- [8] Linder. J., Larsson. M., Internal report Swedish Institute for Metal Research, IM-3491, 1997.
- [9] Itatani. M., Asano. K., Iida. K., ASME PVP, vol. 374, 145, 1998.
- [10] Akita. M., Tokaji. K, Surface & Coatings Technology, vol. 200, 6073-6078, 2006.
- [11] Hattori. N., Nishida. S., Yano. Y. J., Ding, Key Engineering Materials, vol. 353-358, 243-247, 2007.
- [12] Peterson. P.E., Stress Concentration Factors, Wiley, 1974.
- [13] Noguchi. H., Kitahara. Y., Sakamoto. M., Ueno. H., In Proceedings of JSME Annual Conference, 987-988, 2006.
9. Copyright:
- This material is a paper by "Md. Shahnewaz Bhuiyan, Youshiharu Mutoh, Yukio Miyashita, Yuichi Ostuka, Toshikatsu Koike". Based on "NOTCH EFFECT ON FATIGUE STRENGTH OF DIE CAST AM60 MAGNESIUM ALLOY".
- Source of the paper: Asian Pacific Conference for Materials and Mechanics 2009 at Yokohama, Japan, November 13-16. DOI not provided in the paper.
This material is summarized based on the above paper, and unauthorized use for commercial purposes is prohibited.
Copyright © 2025 CASTMAN. All rights reserved.