This introduction paper is based on the paper "New Optimal Heat Sink Design with Concave Fins for Cooling System in Light Emitting Diode Lamp" published by "Electrica".
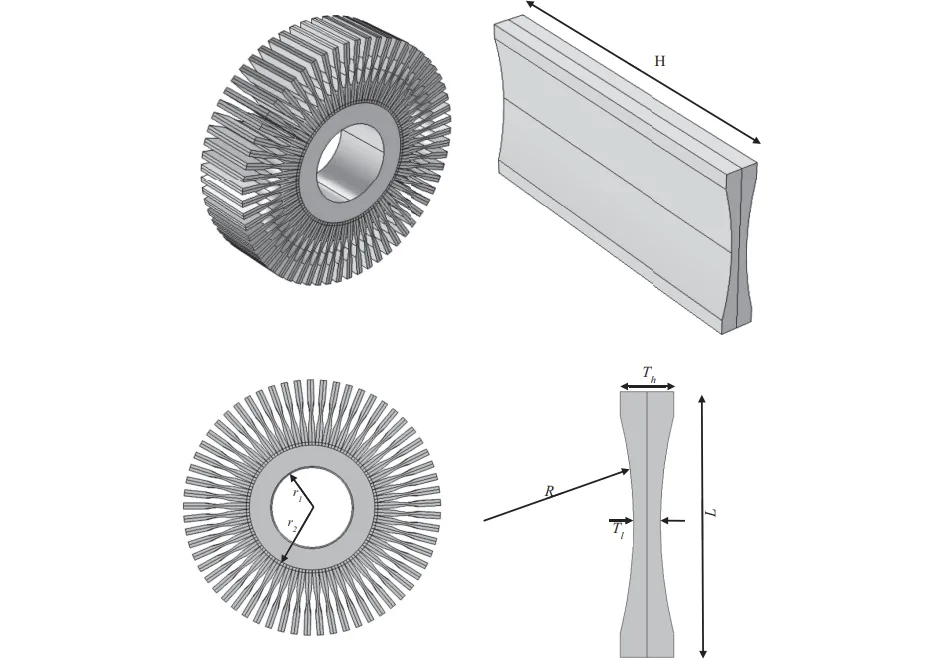
1. Overview:
- Title: New Optimal Heat Sink Design with Concave Fins for Cooling System in Light Emitting Diode Lamp
- Author: Mojtaba Babaelahi
- Year of publication: 2022
- Journal/academic society of publication: Electrica
- Keywords: Heat sink, LED, optimized geometry, numerical solution, analytical correlation
2. Abstract:
The heat sink is considered one of the most critical issues in designing and operating light-emitting diode (LED) lamps. The manufacturers in the technical catalogs indicate the maximum temperature tolerable by LED chips, which causes the light to drop and the color of the lamp output to change when this temperature range is not met. The selection and design of the cooling system usually affect the costs associated with the construction of the heat sink. This paper introduced a new heat sink system incorporating concave fins for the LED lamp cooling system. The numerical method was applied to solve the governing heat balance equations to examine this heat sink's capability. The optimum geometry was determined to achieve minimum electronic chip temperature and heat sink weight at different LED lamp capacities based on the coupled numerical solution of heat transfer and particle swarm optimization (PSO) optimization algorithm. A comprehensive database was created and used as input for genetic planning tools based on two objective optimal solutions for different LED lamp capabilities. Based on genetic programming results, an analytical relation was presented to determine the optimal geometric parameters for LED power. Therefore, it is possible to determine the optimum geometry for a given power without numerical resolution and optimization. The efficiency and volume of sinks are significantly improved in optimal heat sinks with concave fins compared to fixed cross-sections based on the results.
3. Introduction:
A light-emitting diode (LED) lamp, a solid-state lamp using a diode for illumination, produces heat that can adversely affect its performance without proper thermal management. Heat sink systems are commonly employed to maintain the LED electronic chip's temperature within a standard range. A significant challenge in LED heat sink design is the cost of materials and manufacturing. Consequently, numerous studies have focused on designing and optimizing cooling systems for LED lamps. This paper introduces a novel heat sink system with concave fins designed to improve cooling efficiency and reduce material usage for LED lamps.
4. Summary of the study:
Background of the research topic:
LED lamps generate heat, and improper thermal management can lead to performance degradation, such as light output drop and color changes, and reduced lifespan. Heat sinks are essential for managing this heat. The cost of materials (often aluminum) and manufacturing makes optimizing heat sink design crucial for economic viability while maintaining performance. The study focuses on a new heat sink design with concave fins to maximize external surface area for heat transfer in a minimum volume.
Status of previous research:
Previous research has explored various LED cooling strategies. Lio et al. [1] examined jet cooling configurations. Jang et al. [2] analyzed an air-circulating cooling arrangement for LED headlamps. Lu et al. [3] investigated loop heat pipes for high-power LED packages. Wang et al. [4] modeled LED packaging heat loss with thermoelectric cooling. Deng et al. [5] proposed liquid metal cooling for high-power LEDs. Anithambigai et al. [6] studied dual interface methods. Kim et al. [7] examined smart heat sinks with hybrid pin fins. Costa et al. [11] numerically analyzed spiral heat sinks. Park et al. [14, 19] proposed and improved spiral heat sinks, including designs with hollow cylinders and chimneys. Sökmen et al. [17] performed computational thermal analysis of cylindrical fins for LED automotive headlamps. These studies highlight ongoing efforts to improve thermal performance, reduce costs, and optimize LED cooling systems.
Purpose of the study:
The primary aim of this study was to develop a heat sink system with concave fins that achieves minimum electronic chip temperature and minimum heat sink weight. Furthermore, the study sought to provide analytical relations, derived from optimization results, to determine the optimal geometric parameters of the heat sink based on the LED lamp's power. This allows for finding the optimum geometry for a given power without requiring further numerical resolution and optimization.
Core study:
The core of this study involved:
- Introducing a new heat sink design featuring concave fins.
- Applying numerical methods (using COMSOL software) to solve governing heat balance equations and analyze the thermal performance of this new heat sink.
- Employing a multi-objective particle swarm optimization (MOPSO) algorithm (interfaced with MATLAB) to determine the optimum geometry for minimum electronic chip temperature and heat sink weight across various LED lamp capacities.
- Creating a comprehensive database of these optimized solutions.
- Using genetic programming (GP) tools with this database as input to derive analytical relations for predicting optimal geometric parameters based on LED power.
5. Research Methodology
Research Design:
The research employed a numerical and computational approach. Thermal analysis of the proposed heat sink with concave fins was conducted using COMSOL software for modeling and solving heat transfer equations. The geometrical dimensions of the heat sink were then optimized using a multi-objective particle swarm optimization (MOPSO) algorithm implemented in MATLAB, which interfaced with COMSOL. The optimization aimed to minimize both the electronic chip temperature and the heat sink volume. Finally, genetic programming was used to derive analytical equations from the optimized database, correlating optimal geometric parameters with LED lamp power.
Data Collection and Analysis Methods:
The study is based on solving the steady-state heat balance equation:
ρCpu.∇T –∇.(k∇T)=0 (1)
where velocity (u) is zero. Heat generated by the LED lamp (P) enters the heat sink from the inner surface:
-n.q = P (2)
Heat dissipation from external surfaces occurs via free convection, with the convective heat transfer coefficient (h) determined using an experimental correlation for the Nusselt number (Nu) [22]:
Nu = [(0.09112El0.6823)-3.5 + (0.5170El0.2813)-3.5]-3.5/3.5 (3)
where El is the Elenbaas number:
El = gβ(T-Tamb)Prwc4 / Lv2 (4)
The convective heat transfer coefficient is:
h = Nu k / L (5)
(Ambient temperature Tamb is 25°C).
Optimization was performed using MOPSO with two objective functions: minimizing electronic chip temperature and minimizing heat sink volume. Decision variables included geometrical parameters like radii, lengths, and thicknesses (Table I). The LINMAP technique was used for selecting the optimal solution from the Pareto frontier.
Genetic programming was then used to generate analytical relations for optimal geometry (Ropt, Te,opt, Tc,opt, Lopt, HL,opt, (r2/r1)ratio) as functions of LED power (PLED) from the database of optimized heat sinks.
Research Topics and Scope:
The research focused on a new heat sink design with concave fins for LED lamp cooling systems. The scope included:
- Numerical thermal analysis of the proposed heat sink.
- Multi-objective optimization of the heat sink's geometrical parameters (outer radius r2, fin length L, fin width HL, minimum fin thickness Tc, maximum fin thickness Te, inner radius r1) for various LED lamp power capacities (10W to 40W).
- Development of analytical correlations to predict these optimal geometric parameters directly from the LED lamp power, thereby eliminating the need for repeated numerical simulations and optimizations for new designs.
- Comparison of the performance (efficiency, volume) of the optimized concave fin heat sink with fixed cross-section heat sinks.
6. Key Results:
Key Results:
The study successfully developed and optimized a new heat sink design with concave fins for LED lamps.
- Effect of Geometrical Parameters:
- Increasing the outer radius (r2) of the heat sink, the length (L) of the fins, and the width (HL) of the fins leads to a decrease in the mean temperature and an increase in the heat sink volume (Fig. 3-5). This is due to the increased external thermal surface area and consequently higher heat transfer rate.
- Increasing the minimum fin thickness (Tc) decreases the mean temperature but increases the heat sink volume (Fig. 6).
- Increasing the maximum fin thickness (Te) increases the average temperature and decreases the heat sink volume, as it reduces the number of fins and the heat transfer rate (Fig. 7).
- Optimization Outcomes:
- Optimal geometric parameters were determined for LED lamp powers ranging from 10W to 40W, aiming for minimum chip temperature and minimum heat sink volume (Table I).
- The Pareto fronts for multi-objective optimization were generated for different LED powers (Fig. 8).
- Analytical Relations:
- Analytical equations (Eq. 6-13) were derived using genetic programming to calculate the optimal geometrical parameters (Ropt, Te,opt, Tc,opt, Lopt, HL,opt, and (r2/r1)ratio) directly from the LED lamp power (PLED).
- Performance Improvement:
- The new heat sink design with concave fins showed significant improvements in efficiency and volume reduction compared to heat sinks with fixed-section fins. For example, for a 40W LED, the efficiency improvement was 0.5202 (52.02%) and volume reduction was 0.7857 (meaning the new design is 78.57% of the volume of a comparable fixed-section sink, or a 21.43% reduction if interpreted as 1-0.7857, though the paper states "decrease in … volume", Table I implies the latter interpretation for "Improvement Volume" as values are <1). The paper states "The efficiency and volume of sinks are significantly improved". Table I shows "Improvement" for "Efficiency" and "Volume". For a 10W LED, efficiency improvement is 0.1392 and volume improvement is 0.9774. For a 40W LED, efficiency improvement is 0.5202 and volume improvement is 0.7857. The base efficiency is stated as 0.32.
Figure Name List:
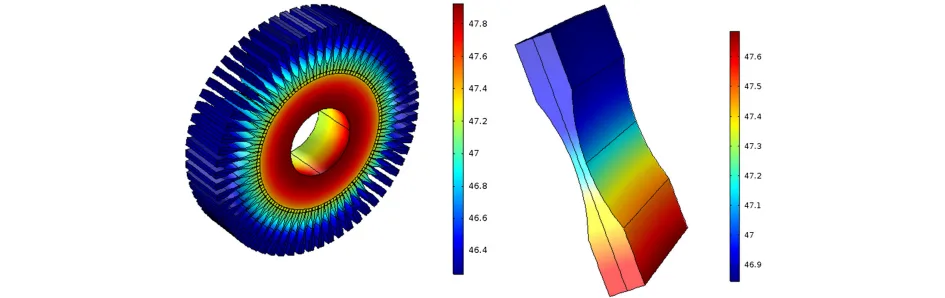
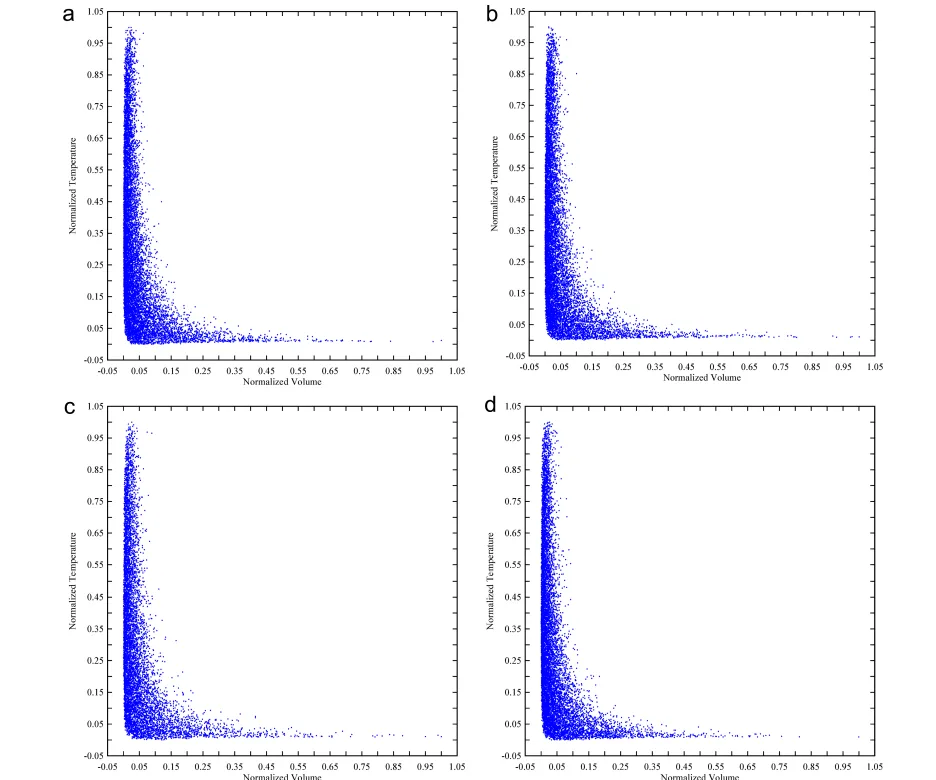
- Fig. 1. Schematic view of the proposed heat sink with concave fins.
- Fig. 2. Temperature distribution in proposed fin and heat sink.
- Fig. 3. Effect of heat sink’s outer radius on the mean temperature and volume.
- Fig. 4. Effect of fin’s length on the mean temperature and volume.
- Fig. 5. Effect of fin’s width on the mean temperature and volume.
- Fig. 6. Effect of fin’s minimum thickness on the mean temperature and volume.
- Fig. 7. Effect of fin’s maximum thickness on the mean temperature and volume.
- Fig. 8. The Pareto front at different LED power: (A) 15 W, (B) 25 W, (C) 35 W, and (D) 40 W.
7. Conclusion:
The paper presents an analytical formulation to determine the optimum geometry of a heat sink with concave fins for LED lamp applications. The optimum geometry for various LED lamp capacities was determined using a coupled numerical solution (COMSOL and MATLAB) and the MOPSO optimization method, targeting minimization of electronic chip surface temperature and thermal sink volume. Based on this database of optimal points and genetic programming, analytical relations were derived to calculate the optimum geometry for an arbitrary LED lamp power. These equations allow for determining the heat sink's optimal geometry without needing further numerical solution or optimization. The results demonstrated that the new concave fins significantly increased efficiency and improved the heat sink volume compared to fixed cross-section heat sinks. It was also found that increasing the outer radius, fin length, and fin width reduces the chip temperature while increasing volume. Minimum and maximum fin thicknesses have opposing effects on the objective functions: one typically decreases temperature and increases volume, while the other does the opposite.
8. References:
- [1] Sh. Liu, J. Yang, Zh. Gan, and X. Luo, "Structural optimization of a microjet based cooling system for high power LEDs," Int. J. Therm. Sci., vol. 47, no. 8, pp. 1086-1095, 2008. [CrossRef]
- [2] S. Jang, and M. W. Shin, "Thermal analysis of LED arrays for automotive headlamp with a novel cooling system," IEEE Trans. Dev. Mater. Reliab., vol. 8, no. 3, pp. 561-564, 2008. [CrossRef]
- [3] X. Lu, T. Hua, M. Liu, and Y. Cheng, "Thermal analysis of loop heat pipe used for high-power LED," Thermochim. Acta, vol. 493, no. 1-2, pp. 25-29, 2009. [CrossRef]
- [4] N. Wang, C. Wang, J. Lei, and D. Zhu, Numerical Study on Thermal Management of LED Packaging by Using Thermoelectric Cooling. Beijing: International Conference on Electronic Packaging Technology & High Density Packaging, 2009, pp. 433-437.
- [5] Y. Deng, and J. Liu, "A liquid metal cooling system for the thermal management of high power LEDs," Int. Commun. Heat Mass Transf., vol. 37, no. 7, pp. 788-791, 2010. [CrossRef]
- [6] P. Anithambigai, K. Dinash, D. Mutharasu, S. Shanmugan, and C. K. Lim, "Thermal analysis of power LED employing dual interface method and water flow as a cooling system," Thermochim. Acta, vol. 523, no. 1-2, pp. 237-244, 2011. [CrossRef]
- [7] H. Kim, K. Kim, and Y. Lee, Thermal Performance of Smart Heat Sinks for Cooling High Power LED Modules. San Diego: 13th InterSociety Conference on Thermal and Thermomechanical Phenomena in Electronic Systems, 2012, pp. 962-967.
- [8] J. Li, F. Lin, D. Wang, and W. Tian, "A loop-heat-pipe heat sink with parallel condensers for high-power integrated LED chips," Appl. Therm. Eng., vol. 56, no. 1-2, pp. 18-26, 2013. [CrossRef]
- [9] B. Alvarado, B. Feng, and G. P. Peterson, "Comparison and optimization of single-phase liquid cooling devices for the heat dissipation of high-power LED arrays," Appl. Therm. Eng., vol. 59, no. 1-2, pp. 648-659, 2013.
- [10] I. Y. Chen, M. Guo, K. Yang, and C. Wang, "Enhanced cooling for LED lighting using ionic wind," Int. J. Heat Mass Transf., vol. 57, no. 1, pp. 285-291, 2013. [CrossRef]
- [11] V. A. F. Costa, and A. M. G. Lopes, "Improved radial heat sink for led lamp cooling," Appl. Therm. Eng., vol. 70, no. 1, pp. 131-138, 2014. [CrossRef]
- [12] Sh. Hsieh, Y. Hsu, and M. Wang, "A microspray-based cooling system for high powered LEDs," Energy Convers. Manag., vol. 78, pp. 338-346, 2014. [CrossRef]
- [13] S. F. Sufian, Z. M. Fairuz, M. Zubair, M. Z. Abdullah, and J. J. Mohamed, "Thermal analysis of dual piezoelectric fans for cooling multi-LED packages," Microelectron. Reliab., vol. 54, no. 8, pp. 1534-1543, 2014. [CrossRef]
- [14] S. Park, D. Jang, and K. Lee, "Thermal performance improvement of a radial heat sink with a hollow cylinder for LED downlight applications," Int. J. Heat Mass Transf., vol. 89, pp. 1184-1189, 2015. [CrossRef]
- [15] B. Ahn, J. Park, S. Yoo, J. Kim, S. Leigh, and Ch. Jang, "Savings in cooling energy with a thermal management system for LED lighting in office buildings," Energies, vol. 8, no. 7, pp. 6658-6671, 2015. [CrossRef]
- [16] X. Zhao, Y. Cai, J. Wang, X. Li, and C. Zhang, "Thermal model design and analysis of the high-power LED automotive headlight cooling device," Appl. Therm. Eng., vol. 75, pp. 248-258, 2015. [CrossRef]
- [17] K. F. Sökmen, E. Yürüklü, and N. karadeniz, "Computational thermal analysis of cylindrical fin design parameters and a new methodology for defining fin structure in LED automobile headlamp cooling applications," Appl. Therm. Eng., vol. 94, pp. 534-542, 2016. [CrossRef]
- [18] D. H. Shin, S. H. Baek, and H. S. Ko, "Development of heat sink with ionic wind for LED cooling," Int. J. Heat Mass Transf., vol. 93, pp. 516-528, 2016. [CrossRef]
- [19] S. Park, D. Jang, S. Yook, and K. Lee, "Optimization of a chimney design for cooling efficiency of a radial heat sink in a LED downlight," Energy Convers. Manag., vol. 114, pp. 180-187, 2016. [CrossRef]
- [20] S. Moon, Y. Park, and H. Yang, "A single unit cooling fins aluminum flat heat pipe for 100 W socket type COB LED lamp," Appl. Therm. Eng., vol. 126, pp. 1164-1169, 2017. [CrossRef]
- [21] Y. Young, and P. Hyun, "Natural cooling characteristics of a heat sink for LED headlight used in passenger cars," Korean Soc. Manufac. Pro. Eng., vol. 16, pp. 142-148, 2017.
- [22] T. H. Kim, D. Kim, and K. H. Do, "Correlation for the fin Nusselt number of natural convective heat sinks with vertically oriented plate-fins," Heat Mass Transf., vol. 49, no. 3, pp. 413-425, 2013. [CrossRef]
- [23] H. Sayyaadi, and M. Babaelahi, "Exergetic optimization of a refrigeration cycle for re-liquefaction of LNG boil-off gas," Int. J. Thermodyn., vol. 13, pp. 127-133, 2010.
- [24] M. Babaelahi, E. Mofidipour, and E. Rafat, "Design, dynamic analysis and control-based exergetic optimization for solar-driven Kalina power plant," Energy, vol. 187, p. 115977, 2019.
9. Copyright:
- This material is a paper by "Mojtaba Babaelahi". Based on "New Optimal Heat Sink Design with Concave Fins for Cooling System in Light Emitting Diode Lamp".
- Source of the paper: https://doi.org/10.54614/electrica.2022.21108
This material is summarized based on the above paper, and unauthorized use for commercial purposes is prohibited.
Copyright © 2025 CASTMAN. All rights reserved.