This introduction paper is based on the paper "Minimise the Nonfilling defect in the high pressure casting process component for an automotive application with metal flow simulation analysis" published by "International Journal of Mechanical Engineering".
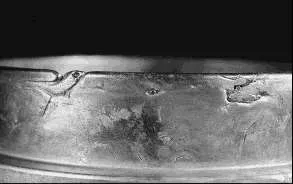
1. Overview:
- Title: Minimise the Nonfilling defect in the high pressure casting process component for an automotive application with metal flow simulation analysis
- Author: R.Govindarao, Dr.K.Eshwara Prasad (Rted)
- Year of publication: 2022
- Journal/academic society of publication: International Journal of Mechanical Engineering
- Keywords: Nonfilling, Machine parameters, Simulation flow analysis.
2. Abstract:
The High pressure die casting process is the one of the vital leading casting process in the world to resolve the all engineering applications .The High pressure diecasting products are used in so many applications like, aerospace, automotive, domestic, agriculture and other engineering applications. In the High pressure diecasting process the scrap rate is nearly about 7% to 10%. The scrap rate includes the rejections due to surface defect and internal defects. The surface defects can be visible and can be maximum resolved while process running time. In all surface defects the non-filling is one of the most repeated defects in all configurations of the castings. Some surface defects like coldshot, chipp off, crack, casting broken etc. can be eliminate at the process itself. But the surface defect like nonfilling defect can't able to resolve immediately. It needs some analysis like optimization of machine parameters and tool design concepts.
3. Introduction:
The High pressure diecasting process involves injecting high-temperature molten metal into a closed steel mould. The casting solidifies for a time dependent on its thickness (Min- 6sec Max-15sec). After solidification, the mould opens, the casting is ejected, and an extractor collects it. The mould requires cooling to a desired temperature (240°C) before the next cycle, typically using a specialized chemical coolant mixed with RO water sprayed for a few seconds (Min-4sec to Max-10 sec). Sticking can occur if cooling is insufficient. The cycle repeats, and the casting undergoes further operations like burr removal.
4. Summary of the study:
Background of the research topic:
High pressure diecasting faces significant costs due to rejections, with rates up to 9%. Nonfilling defects account for a major portion of these rejections (around 5% absolute, or 47% of total defects based on the presented Pareto analysis for a 500-piece batch). While some surface defects can be addressed by modifying process parameters like temperatures, pressures, and velocities during production, nonfilling often requires more in-depth analysis.
Status of previous research:
The paper indicates that traditional methods involve diecasters fine-tuning process parameters through trial and error until a defect-free casting is achieved. This manual approach is described as time-consuming. Simulation methods, like MAGMASOFT, exist and are widely used for various casting processes, including pressure diecasting, offering capabilities to analyze turbulent filling and metal temperatures.
Purpose of the study:
The study aims to minimise the nonfilling defect in a high-pressure die-cast automotive component by employing metal flow simulation analysis. The goal is to use simulation to check metal flow paths, analyze temperatures at different locations, identify defect locations, and optimize runner design and machine parameters, thereby reducing scrap and improving the process.
Core study:
The core of the study involved using MAGMASOFT flow simulation software to analyze the high-pressure die casting process for an automotive component. Four different runner design models were created, primarily varying the metal input locations and runner cross-sections. The simulation analyzed the turbulent filling of molten metal into the mould across the three phases of the shot cycle (S1: slow approach, S2: high-velocity filling, S3: intensification pressure). Key parameters like metal temperatures, pressures, velocities, fill time, and fill ratio were evaluated at various locations and stages (18 stages analyzed per model) to compare the performance of the four runner designs. The objective was to identify the design that best mitigates the risk of nonfilling defects. The findings from the simulation were then used to manufacture a mould based on the optimal design (Model-4), followed by experimental trials to validate the results.
5. Research Methodology
Research Design:
The research employed a simulation-based comparative study followed by experimental validation. Four distinct runner designs for a high-pressure die casting mould were simulated using MAGMASOFT. The simulation results (fill time, fill ratio, temperature distribution) were compared to identify the optimal design for minimizing nonfilling defects. A mould was then manufactured based on the selected design (Model-4), and production trials were conducted to validate the simulation predictions by measuring the actual rejection rate.
Data Collection and Analysis Methods:
Data collection involved:
- Creating complete 3D models of the mould segments (core, cavity, runner, gates, overflows, channels, cooling/heating lines) based on component drawings.
- Performing machine capacity calculations (e.g., 800T, 900T) based on casting configuration and area.
- Synchronizing 3D model dimensions for mathematical calculations, including plunger tip and chamber dimensions.
- Inputting process parameters into the simulation software (MAGMASOFT), running simulations iteratively (low, medium, high parameter ranges).
- Executing the simulation, which involved meshing the geometry for accuracy and analyzing the three phases of the shot cycle.
- Collecting simulation output data for each of the four models across 18 stages, including metal temperatures, pressures, velocities, plunger travel, molten metal flow direction, total fill time, and fill ratio (volume of metal filled per unit time).
- Analyzing the simulation results, focusing on comparing fill times and temperature distributions (especially at end-of-fill locations like overflows and chill vents) between the four models.
- Conducting experimental trials (500 units batch) with the mould built according to the selected simulation model (Model-4).
- Collecting and analyzing rejection data (specifically nonfilling defects) from the experimental trials using Pareto analysis.
Research Topics and Scope:
The research focused on the high-pressure die casting (HPDC) process for an automotive component. The primary scope was the reduction of the nonfilling defect through the application of metal flow simulation analysis (specifically MAGMASOFT). The study encompassed:
- Simulation of the molten metal filling process.
- Comparison of four different runner designs.
- Analysis of the three shot phases (S1 - slow shot, S2 - fast shot/filling, S3 - intensification).
- Evaluation of key process indicators: fill time, fill ratio, metal temperature distribution, pressure, and velocity.
- Identification of the optimal runner design based on simulation results.
- Experimental validation of the chosen design by measuring defect rates in a production batch.
6. Key Results:
Key Results:
- Initial Pareto analysis (Graph 1.0) showed nonfilling defects accounted for 47% of casting rejections in the studied case, making it the most significant defect.
- Flow simulation analysis compared four runner designs (Model 1-4). Models 1 and 2 were deemed unsuitable due to high fill times and low fill ratios.
- Model 3 exhibited the lowest fill time among the four models (Graph 2.0). However, it showed lower metal temperatures (592°C - 615°C) at the overflow and chill vent areas compared to Model 4.
- Model 4 had a fill time nearly equal to Model 3 but maintained higher metal temperatures at the chill vent and overflow areas. Higher temperatures in these regions are beneficial as they facilitate the escape of hidden gases and reduce the likelihood of defects like blow holes and shrinkage porosity. Model 4 also showed a higher fill ratio compared to other models (Graph 3.0).
- Based on the simulation results, Model 4 was selected as the best suited for manufacturing the mould.
- Experimental trials conducted using the mould designed according to Model 4 demonstrated a significant reduction in the nonfilling defect rate, decreasing from an initial 6.0% to 1.60% (Graph 5.0). The rejection data for the validation batch is shown in Graph 4.0.
- The study concluded that simulation is a valuable tool for optimizing runner design and process parameters, effectively reducing nonfilling defects and reliance on time-consuming manual trial-and-error methods.
Figure Name List:
- Graph 1.0 Diecasting defects Pareto analysis
- Fig: 1.0 Nonfilling defect
- Fig: 2.0 The runner design models in four types for the simulation model
- Fig:3.0 Metal flow during Firsr phase
- Fig 4.0 Metal flow during second phase
- Fig 5.0 Metal flow during third phase
- Graph 2.0 The filling time in each model for each cycle in Second phase condition
- Graph 3.0 Fill ratios of the all simulation models
- Graph:4.0 Non filling rejection data
- Graph 5.0 Initial nonfilling and final nonfilling
7. Conclusion:
The simulation model is applicable across diecasting industries and offers potential for significant cost savings, as the reduction in wastage due to rejections can offset the cost of the simulation package. Simulation in high-pressure diecasting design is highly effective, potentially more so than in steel casting simulation, enabling the production of high-quality castings. While simulation software may not yield 100% perfect results, it provides crucial information to mould makers, helping avoid major mistakes. It is recommended that mould flow simulation be considered a necessary activity for any new project to achieve time, cost, and quality improvements. Utilizing simulation models in new projects can lead to savings in time and money, eliminate waste from rejections and machine breakdowns, and ultimately improve customer satisfaction.
8. References:
- [1] Proceedings of the NADCA, “Diecasting defects and design of experiments”, WG. Cleveland, USA Year -1993, Chapter-2 Page: 13-14
- [2] Edward J,Vinarcik, “High Integrity Die-casting processes", Year- 2003.Page: 134-136.
- [3] Genick, Bar-Meir,Minneapolis, “Fundamentals of Die Casting Design", Version: 0.1.2 April 1, 2009, Chapter-1, Page 8-9.
- [4] Hyuk-jae kwon, Hong-kyu Kown, “Computer aided engineering (CAE) simulation for the design optimisation of gate system on high pressure diecasting process (HPDC)”, Elsevier 2018 Page: 149-152
- [5] A J Norwood, P M Dickens*, "Surface temperature of tools during the high-pressure die casting of aluminium", Wolfsan School of Mechanical and Manufacturing Engineering, Loughborough University,UK DOI: 10.1243/09544054JEM745. Year-Aug-2007, Page-1659
- [6] Emil Ragan, Marta Kollarova, "Calculation of Transient Haracterostics in Mould cavity, International journal of Engineering", Tome IX (Year 2011). Fascicule 3. ISSN 1584 – 2673 Page: 1-2.
- [7] Hanxue,chaos shen, chengwang,Hui xui, Direct “Observation of filling Process and Porosity Prediction in High Pressure" Diecasting, Journal name: Materials MPDI 2nd April-2009. Page: 2-9
- [8] M. T. Alonso Rasgado, K. Davey, L. D. Clark and S. Hinduja “Simplified Thermal Stress Analysis "- Department of Mechanical, Aerospace and Manufacturing Engineering UMIST, Manchester, 12TH INTERNATIONAL SCINETIFIC CONFERENCE. Year-2003, Page: 1-2.
- [9] G-Bar Meir, Minnesota The mathematical “Theory of PQ² Diagram", Supercomputing Institute. University of MINNESOTA USA, USMI 99/40 MARCH-1999. Page- 5-6
- [10] John wronowicz, Mike Cox, RexFish,” PQ²- EC-700", July 1998. Page 1-29
9. Copyright:
- This material is a paper by "R.Govindarao and Dr.K.Eshwara Prasad (Rted)". Based on "Minimise the Nonfilling defect in the high pressure casting process component for an automotive application with metal flow simulation analysis".
- Source of the paper: [DOI URL not provided in the paper]
This material is summarized based on the above paper, and unauthorized use for commercial purposes is prohibited.
Copyright © 2025 CASTMAN. All rights reserved.