본 소개 자료는 "[Materials Transactions / Japan Foundary Engineering Society]"에서 발행한 논문 "[Strength of Salt Core Composed of Alkali Carbonate and Alkali Chloride Mixtures Made by Casting Technique]"을 기반으로 합니다.
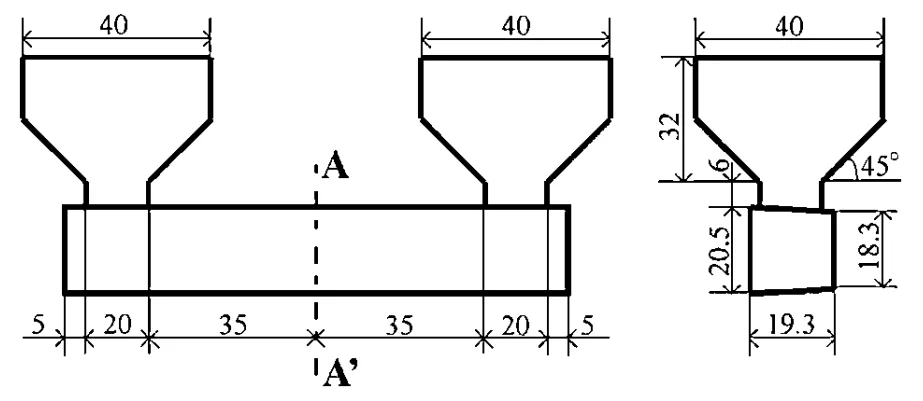
1. 개요:
- 논문 제목: Strength of Salt Core Composed of Alkali Carbonate and Alkali Chloride Mixtures Made by Casting Technique (주조 기술로 제작된 알칼리 탄산염 및 알칼리 염화물 혼합물 염중자의 강도)
- 저자: Jun Yaokawa, Daisuke Miura, Koichi Anzai, Youji Yamada and Hiroshi Yoshii
- 발행 연도: 2007
- 발행 학술지/학회: Materials Transactions / Japan Foundary Engineering Society
- 키워드: salt core, expendable core, carbonate, chloride, die casting, strength, microstructure (염중자, 소모성 코어, 탄산염, 염화물, 다이캐스팅, 강도, 미세조직)
2. 초록:
고압 다이캐스팅 공정용 소모성 염중자를 개발하기 위해 네 가지 이원계 시스템 NaCl-Na2CO3, KCI-K2CO3, KCI-NaCl 및 K2CO3-Na2CO3의 강도를 조사했습니다. 영구 주형 주조 기법을 사용하여 용융염으로 만든 시편의 강도를 결정하기 위해 4점 굽힘 시험을 수행했습니다. NaCl-Na2CO3 시스템의 강도는 Na2CO3 조성이 20 mol%와 30 mol% 사이, 그리고 50 mol%와 70 mol% 사이에서 20 MPa 이상이었습니다. 최고 강도는 NaCl-70 mol%Na2CO3 조성에서 약 30 MPa였으며, 이는 일반적으로 사용되는 모래 코어 강도의 5배에 달하는 수치입니다. KCI-K2CO3 시스템 또한 20 MPa의 강도를 보였습니다. 최고 강도를 얻은 조성에서 NaCl-Na2CO3 및 KCI-K2CO3 시스템의 응고 구조 내 공정 구조(eutectic structure)에 둘러싸인 초정 입자(primary particles)가 관찰되었습니다. 초정 입자의 존재는 균열 전파를 방지하거나 편향시킬 수 있기 때문에 구조 강화에 중요한 역할을 했습니다. 이들 이원계 시스템과는 대조적으로, KCI-NaCl 및 K2CO3-Na2CO3 시스템은 고용체 상의 상 분해 또는 기타 고상-고상 상 변태로 인해 매우 취약했습니다. 이 시스템들의 강도는 6 MPa 미만이었습니다.
3. 서론:
고압 다이캐스팅(HPDC)은 알루미늄 합금 및 기타 저융점 합금의 복잡한 형상 제품을 저비용으로 생산할 수 있는 잘 알려진 넷 셰이프(near-net-shape) 제조 기술입니다. 최근 이 공정을 통해 언더컷 형상의 부품을 제조하여 기계적 특성을 개선하고 생산성을 높이며 비용을 절감하려는 요구가 증가하고 있습니다.
그러나 HPDC 공정의 매우 가혹한 주조 조건은 소모성 코어(expendable cores) 사용을 제한하여 이러한 부품 제조를 매우 어렵게 만듭니다. 코어는 제품의 언더컷 형상을 형성하는 데 필수적입니다. HPDC 공정에서는 용탕의 높은 유동 속도(게이트에서 30 m/s 이상)와 높은 정수압(60 MPa 이상)이 일반적으로 사용됩니다. 이러한 주조 조건은 금형과 코어에 매우 높은 기계적 부하를 유발합니다.
따라서 소모성 코어는 이러한 높은 하중을 견딜 수 있는 충분한 강도를 가져야 합니다. 그러나 코어 강도의 증가는 일반적으로 붕괴성(collapsibility)을 감소시켜 코어 제거 시간을 더 필요로 합니다. 일반적으로 코어 강도가 증가할수록 붕괴성은 감소하여 코어 제거 시간이 길어지고, 결과적으로 총 처리 비용이 증가합니다.
이러한 문제를 해결하기 위해 모래 코어(sand cores), 금속 코어(metallic cores), 유기 재료 코어(organic material cores), 염중자(salt cores) 등 다양한 유형의 HPDC용 소모성 코어가 개발되었습니다. 그러나 강도와 제거성(removability)을 모두 만족시키는 소모성 코어는 아직 HPDC 공정에서 사용되지 못했습니다.
주조 기술로 제작된 수용성 염중자는 높은 제거성 때문에 새로운 소모성 코어의 매력적인 후보입니다. 또한 주조 기술을 사용하면 복잡한 형상의 염중자를 제작할 수 있습니다. 최근 알루미늄 보레이트 휘스커로 강화된 알칼리 할로겐화물 염중자가 영구 주형 주조법으로 제작되어 HPDC 공정에 사용하기에 충분히 높은 강도를 갖는다고 보고되었습니다.
그러나 이러한 연구들은 세라믹 강화재 첨가가 용융염의 유동성을 감소시킨다는 것을 보여주었습니다. 또한 세라믹 강화재 사용은 재료 비용을 증가시키고 추가적인 재활용 공정을 필요로 합니다. 많은 특허에서는 강화재 없이 염 혼합물로 구성된 염중자가 우수한 주조성(castability)과 높은 제거성을 갖는다고 보고되었습니다.
따라서 염 혼합물의 사용은 HPDC 공정용 염중자 제작에 더 바람직합니다. 그러나 이러한 염 혼합물의 강도에 대한 연구는 거의 보고되지 않았으며, 염 혼합물 조성이 강도에 미치는 영향을 체계적으로 조사한 연구는 부족합니다.
본 연구의 목적은 알루미늄 합금의 HPDC 공정에 사용하기에 적합한 액상선 온도를 가진 사원계 시스템(염화나트륨, 탄산나트륨, 염화칼륨, 탄산칼륨)의 일부인 네 가지 이원계 시스템, 즉 염화나트륨-탄산나트륨(NaCl-Na2CO3), 염화칼륨-탄산칼륨(KCl-K2CO3), 염화칼륨-염화나트륨(KCl-NaCl), 탄산칼륨-탄산나트륨(K2CO3-Na2CO3)의 강도를 조사하는 것입니다.
영구 주형 주조법으로 용융 염 혼합물로부터 제작된 시편에 대해 4점 굽힘 시험을 수행했습니다. 조성과 응고 구조가 강도에 미치는 영향을 파단면 분석(fractgraphy) 및 상평형도 지식을 기반으로 논의했습니다. 결과는 NaCl-Na2CO3 및 KCl-K2CO3 시스템의 혼합물에서 매우 높은 강도를 실현할 수 있음을 보여주었습니다.
4. 연구 요약:
연구 주제 배경:
특히 알루미늄 합금의 HPDC 공정을 통해 복잡한 언더컷 부품을 생산하기 위해, 강도가 높고 쉽게 제거할 수 있는 소모성 코어에 대한 요구가 증가하고 있습니다. 수용성 염중자는 유망한 후보 기술입니다.
기존 연구 현황:
이전 연구에서는 강화 염중자를 탐구했으며, 이는 높은 강도를 달성했지만 비용, 용탕 유동성 및 재활용 문제를 겪었습니다. 특허들은 비강화 염 혼합물의 가능성을 시사했지만, 특히 조성의 영향에 대한 강도 특성에 대한 체계적인 데이터가 부족했습니다.
연구 목적:
본 연구는 영구 주형 주조법으로 제작된 네 가지 이원계 염 시스템(NaCl-Na2CO3, KCl-K2CO3, KCl-NaCl, K2CO3-Na2CO3)의 강도를 체계적으로 조사하는 것을 목표로 했습니다. 목표는 염 혼합물 조성, 응고 구조 및 기계적 강도 간의 관계를 이해하고 HPDC 염중자에 적합한 조성을 식별하는 것이었습니다.
핵심 연구:
연구의 핵심은 영구 주형 주조를 사용하여 다양한 조성의 네 가지 이원계 염 시스템으로부터 시편을 준비하는 것이었습니다. 이 주조된 시편의 기계적 강도는 4점 굽힘 시험을 사용하여 결정되었습니다. 응고 미세 구조와 파단면은 SEM, EDX 및 XRD를 사용하여 분석하여 구조와 강도를 연관시켰습니다. 상평형도는 응고 거동과 결과적인 미세 구조를 해석하는 데 사용되었습니다. 비커스 경도(Vickers hardness)도 측정되었습니다.
5. 연구 방법론
연구 설계:
본 연구는 실험적 설계를 사용했습니다. 네 가지 이원계 염 시스템의 다양한 조성을 준비하고, 영구 주형을 사용하여 표준화된 시험 시편으로 주조하고, 굽힘 강도와 경도를 측정하고, 미세 구조와 파괴 거동을 분석하여 강도를 결정하는 기본 메커니즘을 이해하는 과정을 포함했습니다.
데이터 수집 및 분석 방법:
- 재료: 순수 염(NaCl, KCl, Na2CO3, K2CO3, 99.5 mass% 순도)을 혼합하여 다양한 조성의 이원계 시스템을 만들었습니다(Table 1).
- 시편 제작: 염 혼합물을 용융시키고 액상선 온도보다 10K 과열시킨 후, 라이저(riser)가 있는 예열된(373 K) JIS-SCM440 강철 영구 주형(Fig. 1)에 주입했습니다. 시편은 60초 후 추출하여 냉각했습니다.
- 기계적 시험: 주조된 시편(치수 명시, 굽힘 속도 1.6 x 10⁻² mm·s⁻¹)에 대해 4점 굽힘 시험을 수행하여 최대 굽힘 하중(P)을 결정하고 식 (1)을 사용하여 굽힘 강도(σ)를 계산했습니다. 연마된 단면에 대해 비커스 경도를 측정했습니다.
- 미세 구조 분석: 응고된 구조는 연마 및 에칭된 샘플에서 주사 전자 현미경(SEM)을 사용하여 관찰했습니다. 에너지 분산형 X선 분광 분석(EDX)은 국소 조성을 결정했습니다. X선 회절(XRD)은 결정상을 식별했습니다. 파단면은 SEM-EDX를 사용하여 분석했습니다.
- 상평형도: Thermo-Calc™ 소프트웨어를 사용하여 계산했습니다.
연구 주제 및 범위:
본 연구는 영구 주형 주조로 준비된 네 가지 이원계 알칼리 염화물-알칼리 탄산염 시스템(NaCl-Na2CO3, KCl-K2CO3, KCl-NaCl, K2CO3-Na2CO3)의 굽힘 강도와 미세 구조에 초점을 맞췄습니다. 범위에는 조성의 강도 및 경도에 대한 영향 조사, 응고 구조 식별, 주조 결함(표면 불균일, 내부 수축, Fig. 2) 분석, 미세 구조 및 파괴 분석을 기반으로 한 강화 메커니즘 규명이 포함되었습니다. 강도 분석은 일반적인 주조 결함을 포함하는 주조된 시편에 대해 수행되었습니다.
6. 주요 결과:
주요 결과:
- 이원계 시스템 KCl-NaCl 및 K2CO3-Na2CO3는 매우 낮은 강도(6 MPa 미만)를 보였고 취성이 있었으며 상당한 균열을 나타냈습니다(Fig. 3). 이는 냉각 중 연속 고용체 구조에서 발생하는 고상-고상 상 변태(분해 또는 공석 반응) 때문인 것으로 추정됩니다(Fig. 4).
- NaCl-Na2CO3 시스템은 높은 강도를 나타냈으며, Na2CO3 조성이 20-30 mol% 및 50-70 mol% 범위에서 20 MPa를 초과했습니다. 최고 강도는 NaCl-70 mol%Na2CO3에서 30 MPa 이상이었으며, 이는 일반적인 모래 코어보다 약 5배 높은 수치입니다(Fig. 5b).
- KCl-K2CO3 시스템 또한 상당한 강도를 보였으며, K2CO3 20 mol% 및 50-80 mol% 사이에서 10 MPa를 초과했습니다. 최고 강도는 K2CO3 조성 50 mol% 및 60 mol%에서 25 MPa를 초과했습니다(Fig. 5d).
- NaCl-Na2CO3 및 KCl-K2CO3 시스템의 높은 강도는 공정 매트릭스 내에 분산된 초정상 입자(염화물 또는 탄산염)로 구성된 미세 구조를 초래하는 조성과 상관관계가 있었습니다(Fig. 7, Fig. 11e). 강도는 순수 성분 근처와 공정 조성 자체에서 가장 낮았습니다(Fig. 11a, 11c).
- 고강도 조성에서의 강화는 초정 입자가 벽개면(cleavage planes)을 따라 "균열 편향(crack deflection)"(Fig. 9a, Fig. 10b) 및 입자 주위에서 "균열 만곡(crack bowing)"(Fig. 9b, Fig. 10a)을 통해 균열 전파를 방해함으로써 발생한 것으로 설명됩니다(Fig. 11f에 개략적으로 표시됨).
- 비커스 경도 측정(Fig. 6) 결과, NaCl-Na2CO3 시스템이 전체 조성 범위에서 KCl-K2CO3 시스템보다 일반적으로 더 단단했으며, 이는 더 높은 전체 강도와 일치합니다. 초정 입자와 공정 구조 모두의 경도가 전체 강도에 역할을 합니다.
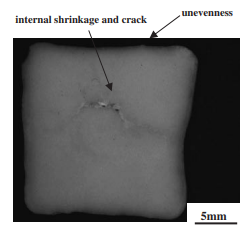
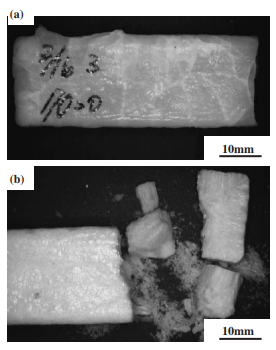
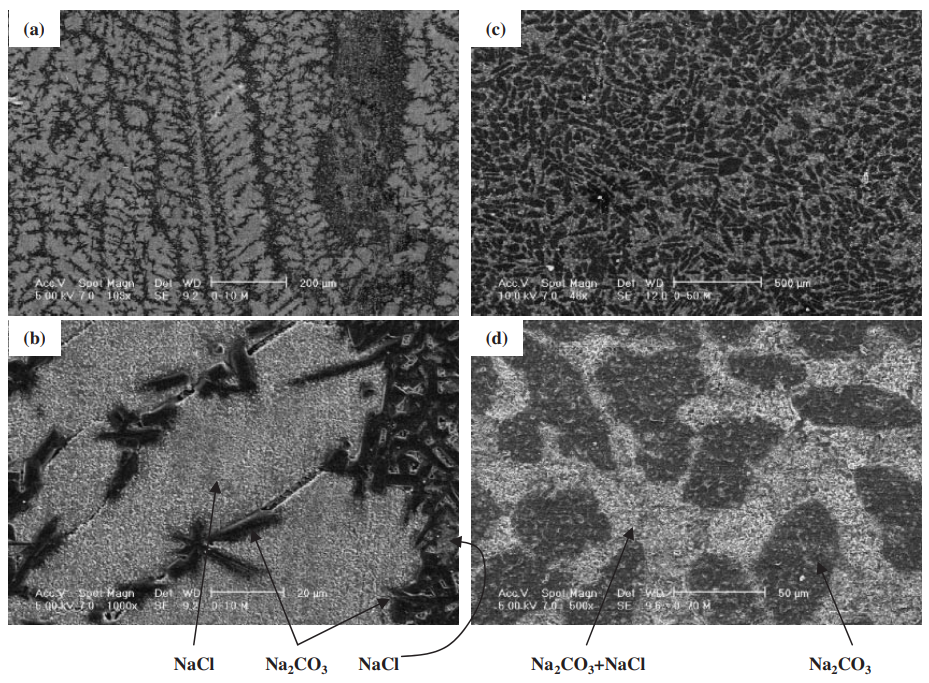
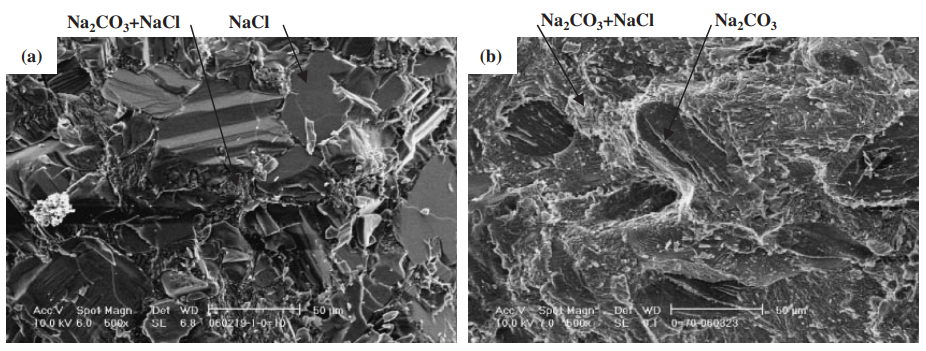
그림 목록:
- Fig. 1 Casting design of bending test specimens.
- Fig. 2 Cross section of KCl-80 mol%K2CO3 specimen.
- Fig. 3 Photographs of specimens at ambient temperature. (a) KC1-30 mol%NaCl. (b) K2CO3-50 mol% Na2CO3.
- Fig. 4 Strength and phase diagrams¹⁵⁾ of KCl-NaCl and K2CO3-Na2CO3 binary systems.
- Fig. 5 Strength and phase diagrams¹⁵⁾ of NaCl-Na2CO3 and KCl-K2CO3 binary systems.
- Fig. 6 Vickers hardness of the system NaCl-Na2CO3 and the system KCI-K2CO3. Solid and dotted lines connect average hardness value of each composition, respectively.
- Fig. 7 The scanning electron microscope (SEM) images of solidified structure. (a) and (b): NaCl-10 mol%Na2CO3. (c) and (d): NaCl-70 mol%Na2CO3.
- Fig. 8 The X-ray diffraction pattern of NaCl-70 mol% Na2CO3.
- Fig. 9 The scanning electron microscope (SEM) images of broken surface. (a): NaCl-10mol%Na2CO3. (b): NaCl-70 mol%Na2CO3.
- Fig. 10 Schematic drawings of two strengthening mechanisms²⁰⁾ in the systems NaCl-Na2CO3 and KCI-K2CO3. (a) crack bowing. (b) crack deflection.
- Fig. 11 Schematic drawings of the solidification structure and the crack propagation. (a) and (b): at the eutectic composition. (c) and (d): pure salt. (e) and (f): the composition between the eutectic and the unary.
7. 결론:
본 연구는 영구 주형 주조 기법으로 주조된 네 가지 이원계 염 시스템(NaCl-Na2CO3, KCl-K2CO3, KCl-NaCl, K2CO3-Na2CO3)의 강도를 조사하고, SEM-EDX 및 XRD로 미세 구조를 분석했습니다. 주요 결과는 다음과 같습니다.
- NaCl-Na2CO3 시스템은 Na2CO3 20-30 mol% 및 50-70 mol% 사이에서 20 MPa 이상의 강도를 달성했으며, NaCl-70 mol%Na2CO3에서 최대 강도는 30 MPa를 초과했습니다.
- KCl-K2CO3 시스템은 K2CO3 20 mol% 및 50-60 mol% 사이에서 10 MPa 이상의 강도를 보였으며, K2CO3 50-60 mol%에서 최대 강도는 25 MPa를 초과했습니다.
- NaCl-Na2CO3 및 KCl-K2CO3 시스템의 강도 증가는 공정 구조 내의 초정 입자가 균열 전파를 효과적으로 방지하거나 편향시키는 응고 구조 때문입니다.
- NaCl-Na2CO3 시스템은 KCl-K2CO3 시스템보다 높은 강도를 나타냈으며, 이는 초정 입자와 공정 구조의 더 높은 경도 값 때문입니다.
- KCl-NaCl 및 K2CO3-Na2CO3 시스템은 응고 구조(연속 고용체)와 냉각 중 해로운 고상-고상 상 변태로 인해 낮은 강도(6 MPa 미만)를 보였습니다.
8. 참고 문헌:
- [1) T. Manabe, M. Nitta and M. Yaguchi: SOKEIZAI 44 (2003) 26–30.
- 2) Yamazaki, A. Takai, O. Murakami, M. Kawabata, O. Ito and M. Kawabata: SAE Technical Paper 2004-01-1447.
- 3) Y. Mizukusa: U.S. Patent No. 5,690,159 (Jun. 20, 1997).
- 4) K. Fujita and K. Atake: Japanese Patent Publication No. H9-108779 (Apr. 28, 1997).
- 5) T. Sakoda: U.S. Patent No. 3,963,818 (Jun. 15, 1976).
- 6) W. A. Gibbons: U.S. Patent 1,523,519 (Feb. 12, 1924).
- 7) F. D. Obolentsev, V. A. Voznesenskii, L. A. Ivanova and I. D. Chmykh: Chem. Petroleum Eng. 13 (1977) 519–521.
- 8) Y. Utsu: Japanese Patent Publication No. 52-10803 (Mar. 26, 1977).
- 9) R. W. Foreman: U. S. Patent No. 4,840,219 (Jun. 20, 1989).
- 10) A. D. Ackerman, H. A. Aula: U.S. Patent 4,446,906 (May 8, 1984).
- 11) Y. Urabe and K. Takeda: Japanese Patent Publication, No. 48-39696 (Nov. 26, 1973).
- 12) J. Yaokawa, K. Anzai, Y. Yamada, H. Yoshii and H. Fukui: J. JFS, 76 (2004) 823–829.
- 13) J. Yaokawa, K. Anzai, Y. Yamada and H. Yoshii: NADCA Transactions T05-083 (2005).
- 14) General editors, L. P. Cook and H. F. McMurdie: Phase diagrams for ceramists vol. 1, Fig. 1857 (The American Ceramic Society, Columbus, Ohio, 1964).
- 15) B. Sundman, B. Jansson, J.-O. Andersson: Calphad 9 (1985) 153–190.
- 16) S. Dong, E. Niyama and K. Anzai: Cast Metals 6 (1993) 115–120.
- 17) S. Pehkonen: J. Phys. D: Appl. Phys. 6 (1973) 544–551.
- 18) L. P. Cook and H. F. Mcmurdie: Phase Diagrams for Ceramists vol. 7, Fig. 6976 (The American Ceramic Society, Columbus, Ohio, 1976) pp. 16–17.
- 19) A. Reisman: J. Am. Chem. Soc. 81 (1959) 807–811.
- 20) Y. Kagawa and H. Hatta: Ceramic Matrix Composites—Tailoring Ceramic Composites, (Agune Shohusha, 1990) 120–157.
- 21) C. Gandhi and M. F. Ashby: Acta Metall. 27 (1979) 1565.
- 22) E. Scheil: Z. Metallk. 34 (1942) 70.
- 23) J. Sangster and A. D. Pelton: J. Phys. Chem. Ref. Data 16 (1987) 509.]
9. 저작권:
- 본 자료는 "Jun Yaokawa, Daisuke Miura, Koichi Anzai, Youji Yamada and Hiroshi Yoshii"의 논문입니다. "[Strength of Salt Core Composed of Alkali Carbonate and Alkali Chloride Mixtures Made by Casting Technique]" 논문을 기반으로 합니다.
- 논문 출처: https://doi.org/10.2320/matertrans.48.1034
본 자료는 상기 논문을 바탕으로 요약되었으며, 상업적 목적의 무단 사용을 금지합니다.
Copyright © 2025 CASTMAN. All rights reserved.