본 소개 내용은 [University of Teesside]에서 발행한 ["Development of water-based core technology for light alloys"] 의 연구 내용입니다.
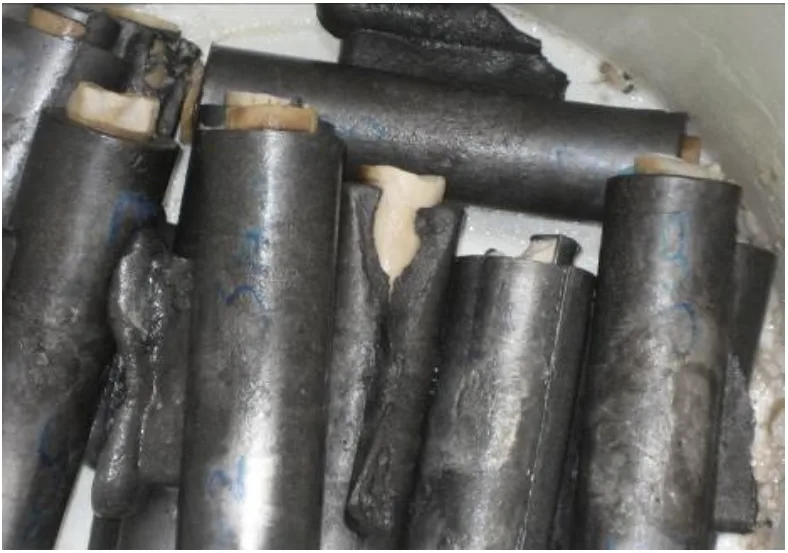
1. 개요:
- 제목: 경합금용 수용성 코어 기술 개발 (Development of water-based core technology for light alloys)
- 저자: Manu Ramegowda
- 발행 연도: 2008년 8월
- 발행 저널/학회: 미발행 박사 학위 논문. 티사이드 대학교 (Unpublished PhD Thesis. University of Teesside.)
- 키워드: 수용성 코어 기술 (water-based core technology), 경합금 (light alloys), 융용 실리카 (fused silica), 석고 (plaster), 산화마그네슘 (magnesium oxide), 침출 (leaching)
2. 초록 / 서론
본 논문은 제조 맥락에서 경합금용 새로운 수용성 코어 기술 개발에 대해 기술합니다.
강철 주조에 사용되는 코어는 융용 실리카로 만들어지며, 환류 하에 뜨거운 수산화나트륨(가압식 뜨거운 산)을 사용하여 제거됩니다. 그러나 알루미늄 및 기타 경합금은 수산화나트륨에 의해 부식됩니다. 현재 알루미늄 및 기타 경합금에 적합한 코어 시스템이 없습니다. 따라서 알루미늄 및 기타 경합금 주조를 위한 대체 재료/침출제 조합을 찾는 것이 바람직합니다.
최근 연구 검토에 따르면 세라믹 코어는 대부분 다양한 첨가제를 첨가한 융용 실리카로 만들어집니다. 이전 연구에서는 충전재로 융용 실리카(다양한 메쉬 크기)를 사용하고 코어 혼합물의 슬러리 작업 수명을 제어하기 위해 산화마그네슘을 사용하는 것을 제안했습니다. 규산칼슘은 묽은 산에서 코어 침출을 돕습니다. 석고(황산칼슘)는 특허 석고(Crystcal R, Fine Casting Plaster) 형태로 코어의 결합을 생성하고 강도를 부여하는 데 사용됩니다. 탄산리튬은 코어에서 석고의 강화 효과를 개선하는 촉진제 역할을 합니다. 바인더(Ludox® AM)와 물은 (첨가 재료로서) 조성물을 결합하는 역할을 합니다.
코어 조성을 경합금에 적합한 강도와 빠른 침출 특성을 기록하는 코어를 생산하기 위해 다양한 코어 시험을 통해 만들었습니다. 코어 시험은 개별적으로 혼합되어 나무 코어 상자에 부어졌습니다. 코어는 24시간 동안 예비 건조되었습니다. 코어는 2시간 동안 다양한 온도로 소성한 다음 2시간 동안 냉각했습니다. 코어는 굽힘 강도(MOR)를 기록하기 위해 컴퓨터화된 3점 굽힘 시험을 거쳤습니다. 평면 변형률 파괴 인성 및 와이블 파라미터를 계산했습니다. 와이블 파라미터는 Minitab 분석 소프트웨어를 사용하여 플로팅했습니다. 코어를 사용하여 중력 다이캐스팅 공정을 수행했습니다. 후속 주물은 코어를 침출하기 위해 묽은 질산, 구연산 및 아세트산에 담갔습니다.
다양한 코어 조성을 사용하여 코어 시험을 혼합, 붓고, 건조, 시험 및 침출했습니다. 코어가 200°-400°C 사이에서 소성되었을 때 코어 시험에서 높은 석고 함량은 높은 MOR을 기록하고, 600°-800°C 사이에서 소성되었을 때는 반대 결과를 나타냈습니다. 다양한 등급의 석고(CRP, FCP)는 강도에 영향을 미치지 않습니다. 1%의 산화마그네슘은 매우 짧은 작업 수명을 제공합니다. 코어 내 높은 함량의 바인더(Ludox® AM)는 강한 코어를 생성합니다.
작업 가능한 MOR 결과는 수동 취급 또는 왁싱 공정을 허용하는 조성에 따라 얻을 수 있습니다. 파괴 인성은 와이블 파라미터와 일치하는 전형적인 취성 재료의 특성입니다. 주조 공정은 새로운 재료가 충분히 내화성임을 시사합니다. 코어는 상업적 제조와 호환되는 속도로 묽은 질산, 아세트산 및 구연산을 사용하여 침출됩니다.
이 방법론은 알루미늄 및 경합금 가능성이 있는 융용 실리카와 석고 및 산화마그네슘을 사용하여 코어를 성공적으로 생산했습니다. 강도 및 금속을 공격하는 산으로 제거와 관련된 특정 산업 응용 분야에 따라 다양한 코어 시험을 사용할 수 있습니다. 최적의 침출 조건을 미세 조정하기 위한 추가 작업이 필요합니다.
3. 연구 배경:
연구 주제 배경:
코어는 금속 주조에서 필수적인 구성 요소이며, 주물 내부에 내부 특징을 만드는 데 사용됩니다. 전통적으로 강철 주조용 코어는 융용 실리카로 만들어지며 뜨거운 수산화나트륨을 사용하여 제거됩니다. 그러나 이 방법은 수산화나트륨이 이러한 합금을 부식시키기 때문에 알루미늄 및 경합금에는 적합하지 않습니다. 따라서 경합금용 대체 코어 기술 개발이 필요합니다.
기존 연구 현황:
이전 연구에 따르면 세라믹 코어는 주로 첨가제가 첨가된 융용 실리카로 만들어집니다. 다양한 메쉬 크기의 융용 실리카가 충전재로 사용되고, 산화마그네슘은 슬러리 작업 수명을 제어하는 데 사용됩니다.
규산칼슘은 묽은 산에서 코어 침출을 돕습니다. Crystcal R 및 Fine Casting Plaster와 같은 형태의 석고(황산칼슘)는 결합재로 사용되어 강도를 제공합니다. 탄산리튬은 석고 강화 효과를 높이는 촉진제로 사용됩니다. Ludox® AM 바인더와 물도 코어 조성물에 사용됩니다.
연구의 필요성:
현재 알루미늄 및 기타 경합금에 대한 최적의 코어 시스템이 없습니다. 수산화나트륨을 사용하는 기존 방법은 수산화나트륨의 부식성 때문에 이러한 합금에 적용할 수 없습니다. 알루미늄 및 경합금 주조를 용이하게 하기 위해 대체 재료 및 침출제 조합이 필요합니다.
본 연구는 가성 소다보다 덜 공격적인 침출제인 묽은 아세트산과 같은 침출제를 사용하여 경합금에 적합한 수용성 코어 기술을 개발함으로써 이러한 격차를 해소하는 것을 목표로 하며, 환경적 이점과 가성 소다와 관련된 폐기물 처리 문제를 해결합니다.
4. 연구 목적 및 연구 질문:
연구 목적:
본 프로젝트는 가성 소다보다 훨씬 덜 공격적인 침출제인 묽은 아세트산 등을 사용하여 알루미늄 및 합금 주물 내부에서 코어를 제거할 수 있도록 기존 조성을 수정하여 수용성 코어 기술을 개발하는 것을 목표로 합니다.
본 연구는 치수 안정성, 강도, 기계적 특성 및 환경 친화적인 시약으로 쉽게 제거할 수 있도록 최적의 코어 조성을 찾는 것을 목표로 합니다. 궁극적인 목표는 개발된 코어의 주조 코어로서의 적합성을 평가하는 것입니다.
핵심 연구:
- 경합금용 새로운 수용성 코어 기술 개발.
- 알루미늄 및 기타 경합금 주조를 위한 대체 재료/침출제 조합 찾기.
- 묽은 아세트산과 같이 덜 공격적인 침출제를 사용하여 알루미늄 및 합금 주물에서 제거할 수 있도록 코어 조성 수정.
- 치수 안정성, 강도 및 기타 기계적 특성에 대한 최적의 코어 조성 결정.
- 개발된 코어의 주조 코어로서의 적합성 평가.
5. 연구 방법론
연구 설계:
본 연구에서는 초기 코어 조성에서 시작하여 기계적 특성, 주조 성능 및 코어 제거를 위해 구성 요소를 체계적으로 변경하는 반복적인 실험적 접근 방식을 채택했습니다. 다양한 코어 조성을 제형화하고 시험했으며, 석고, 바인더 및 산화마그네슘 비율의 변화와 규산칼슘 및 다양한 석고 유형의 사용이 미치는 영향을 평가하기 위해 시험을 설계했습니다.
자료 수집 방법:
- 코어 준비: 코어 조성물을 혼합하고, 나무 코어 상자에 붓고, 예비 건조하고, 다양한 온도(200°C, 400°C, 600°C, 800°C)에서 소성했습니다.
- 기계적 시험: 굽힘 강도(MOR)를 측정하기 위해 컴퓨터화된 3점 굽힘 시험을 실시했습니다. 평면 변형률 파괴 인성 및 와이블 파라미터도 계산했습니다.
- 코어 제거 시험: 코어를 사용하여 중력 다이캐스팅을 만들고, 다양한 농도와 지속 시간의 묽은 질산, 구연산 및 아세트산 용액에서 후속적으로 침출했습니다. 코어 제거 용이성은 육안으로 그리고 프로빙을 통해 평가했습니다.
- 치수 측정: 수축률을 평가하기 위해 소성 전후 코어 치수(직경 및 길이)를 측정했습니다.
- 현미경 검사: 주사 전자 현미경(SEM)을 사용하여 선택된 코어 샘플의 표면 형태를 검사했습니다.
분석 방법:
- 굽힘 강도(MOR) 분석: 코어 강도를 평가하기 위해 3점 굽힘 시험 데이터에서 MOR 값을 계산했습니다.
- 와이블 분석: 코어 강도의 신뢰성 및 가변성을 분석하기 위해 Minitab 소프트웨어를 사용하여 와이블 파라미터를 계산하고 플로팅했습니다.
- 파괴 인성 분석: 재료의 취성 파괴에 대한 저항성을 평가하기 위해 평면 변형률 파괴 인성(KIC)을 계산했습니다.
- 통계 분석: Minitab 소프트웨어를 사용하여 분포 개요 플롯 및 와이블 분석을 포함한 통계 분석을 수행했습니다.
- 정성적 분석: 육안 검사 및 프로빙을 사용하여 코어 제거 효율성 및 코어 결함을 평가했습니다.
연구 대상 및 범위:
본 연구는 경합금, 특히 알루미늄용 수용성 코어 기술 개발에 중점을 두었습니다. 조사된 코어 재료에는 융용 실리카, 석고(다양한 유형), 산화마그네슘, 탄산리튬, 규산칼슘, 구연산삼나트륨 및 Ludox® AM 바인더가 포함되었습니다. 코어 조성물은 기계적 특성, 중력 다이캐스팅의 주조 성능 및 묽은 산을 사용한 제거에 대해 시험했습니다. 범위는 실험실 규모의 실험으로 제한되었으며, 본격적인 산업 시험으로 확장되지는 않았습니다.
6. 주요 연구 결과:
핵심 연구 결과:
- 코어 조성 및 MOR: 코어 시험에서 높은 석고 함량은 200°-400°C에서 소성했을 때 높은 MOR을 기록했지만, 600°-800°C에서 소성했을 때는 반대 결과가 나타났습니다. 다양한 등급의 석고(CRP, FCP)는 강도에 큰 영향을 미치지 않았습니다. 높은 바인더 함량(Ludox® AM)은 강한 코어를 생성했습니다.
- 슬러리 작업 수명: 1%의 산화마그네슘은 매우 짧은 슬러리 작업 수명을 초래했습니다.
- 침출: 묽은 질산, 구연산 및 아세트산은 상업적 제조와 호환되는 속도로 코어를 성공적으로 침출했습니다. 고농도 질산(1:1, 1:2, 1:5)이 코어 침출에 더 효과적이었지만, 묽은 아세트산 및 구연산도 특히 고농도(아세트산 1:100, 구연산 1:100)에서 유망한 침출 능력을 보였습니다.
- 치수 안정성: 미세 메쉬 크기 융용 실리카(-200)는 더 거친 융용 실리카에 비해 치수 안정성을 개선하고 수축률을 감소시켰습니다.
- 와이블 분석: 와이블 분석은 코어의 취성 특성을 확인했으며, 와이블 계수 값은 강도의 가변성을 시사했습니다.
- 파괴 인성: 파괴 인성(KIC) 값을 계산하여 재료의 파괴 전파 저항에 대한 정량적 측정을 제공했습니다.
제시된 데이터 분석:
- 온도에 따른 MOR 변화: MOR 값은 일반적으로 더 높은 소성 온도(600°-800°C)에서 감소했으며, 특히 석고 함량이 높은 코어 조성물에서 그러했는데, 이는 고온에서 석고 분해 및 결합 약화 때문일 수 있습니다.
- 산화마그네슘의 효과: 산화마그네슘은 슬러리 작업 수명을 크게 단축시켜 경화 과정을 가속화하는 역할을 강조했습니다.
- 침출 효율성: 묽은 질산은 일반적으로 구연산 및 아세트산에 비해 코어 침출에 더 효과적이었지만, 세 가지 산 모두 특히 고농도에서 침출 가능성을 보였습니다. 효율성은 코어 조성 및 소성 온도에 따라 달라졌습니다.
- 치수 변화: 미세 융용 실리카 및 특정 코어 조성물(예: Trial D)은 더 나은 치수 안정성 및 감소된 수축률을 나타냈습니다.
- 와이블 및 파괴 인성: 와이블 분석은 코어의 취성 특성을 확인했으며, 파괴 인성 값은 파괴 저항에 대한 정량적 척도를 제공했습니다.
그림 목록:
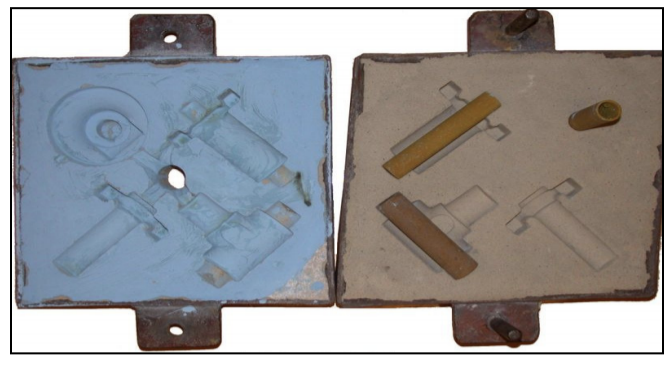
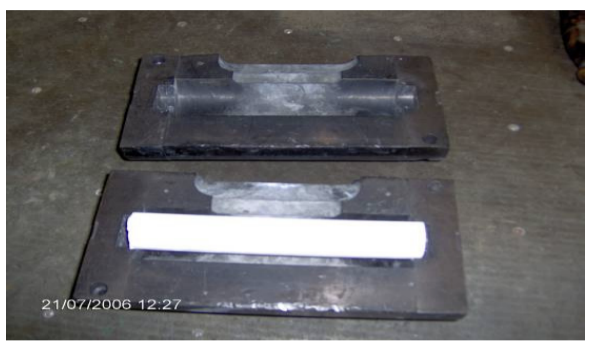
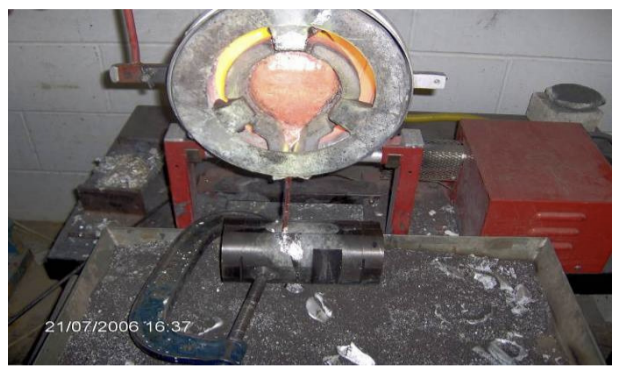
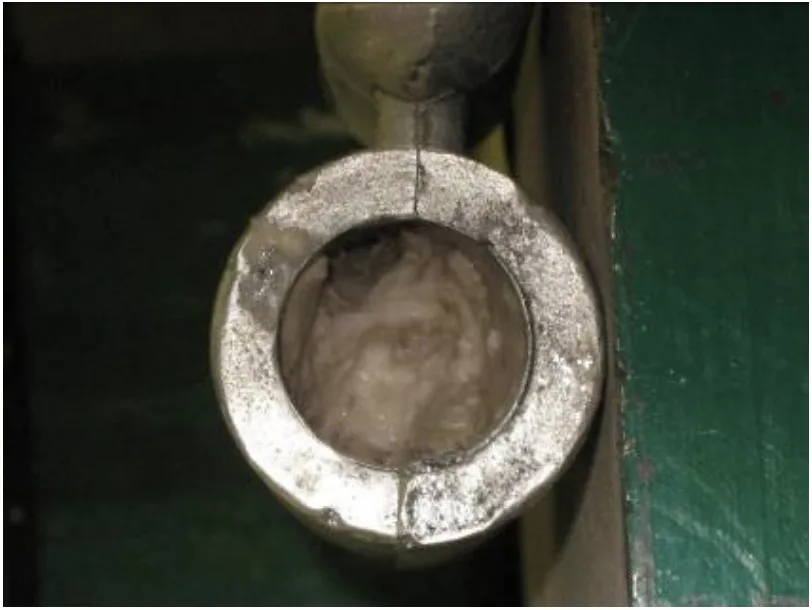

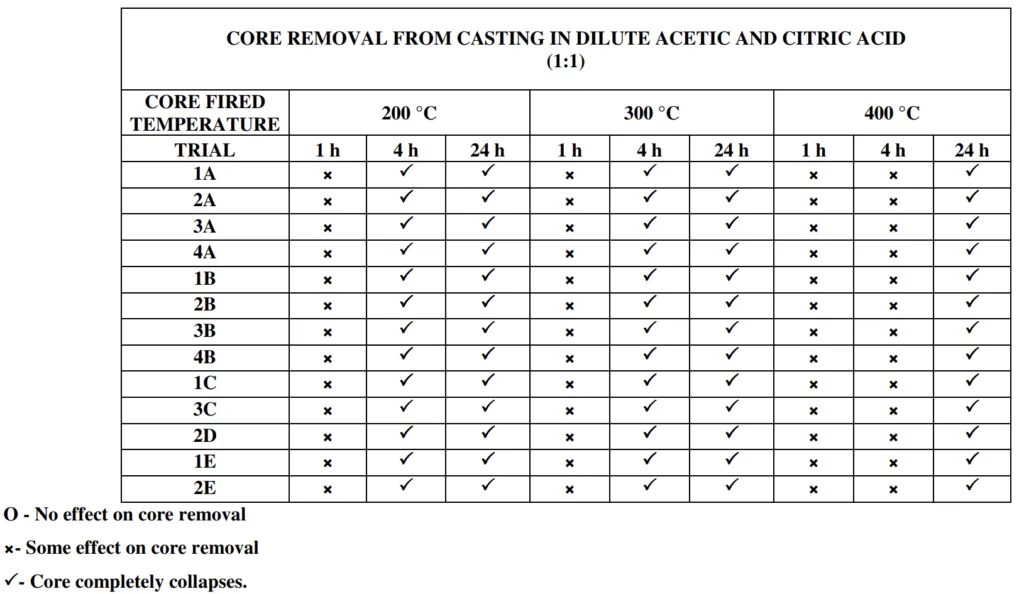
- 그림 1. 복잡한 모래 코어의 예 (9)
- 그림 2. 다양한 세라믹 코어 모양의 예 (10)
- 그림 3. 레이싱 카 배기 부품용 프리폼 코어 (10)
- 그림 4. 경화 후 드래그에 삽입되는 코어 (11)
- 그림 5. 컨베이어 코어 건조로 (13)
- 그림 6. 3점 하중 방식 (35)
- 그림 7. 모래 코어를 사용한 모래 주조 (59)
- 그림 8. (a) 코어 블로우 (b) 응고 전 코어에서 발생한 가스로 인한 결함 (54)
- 그림 9. 코어가 있는 코어 몰드 박스
- 그림 10. LLOYD 만능 시험기
- 그림 11. 3점 굽힘 하중을 가한 파단 시편
- 그림 12. 코어가 있는 주철 분할 몰드
- 그림 13. 조립된 몰드에 붓는 과정
- 그림 14. 주철 몰드의 일반적인 배열
- 그림 15. 표시된 주물 부품
- 그림 16. 건조를 위해 남겨진 코어
- 그림 17. 코어 시험에서 평균 슬러리 작업 수명
- 그림 18. 코어 시험에서 평균 경화 시간
- 그림 19. 200°C에서 코어 시험에 대한 중량 감소와 함께 24시간 소성
- 그림 20. 400°C에서 코어 시험에 대한 중량 감소와 함께 24시간 소성
- 그림 21. 다양한 소성 온도에서 Trial A의 평균 MOR
- 그림 22. 다양한 소성 온도에서 Trial B의 평균 MOR
- 그림 23. 다양한 소성 온도에서 Trial C의 평균 MOR
- 그림 24. 다양한 소성 온도에서 Trial D의 평균 MOR
- 그림 25. 다양한 소성 온도에서 Trial E의 평균 MOR
- 그림 26. 4시간 동안 400°C에서 소성된 Trial 1E 코어에 대한 묽은 질산의 효과.
- 그림 27. 다양한 소성 온도에서 Trial A의 평균 MOR
- 그림 28. 단면 Al-LM25의 코어 블로우 결함 (코어 제거됨)
- 그림 29. 코어가 있는 수직 스탠딩 나무 코어 박스
- 그림 30. 바닥에 침전된 30/50 융용 실리카로 600°C에서 소성된 코어.
- 그림 31. 코어 시험의 평균 경화 시간
- 그림 32. 다양한 MgO 백분율에서 Trial 4A의 평균 슬러리 작업 수명
- 그림 33. 다양한 소성 온도에서 Trial A의 평균 MOR
- 그림 34. 다양한 소성 온도에서 Trial B의 평균 MOR
- 그림 35. 다양한 소성 온도에서 Trial C의 평균 MOR
- 그림 36. 다양한 소성 온도에서 Trial D의 평균 MOR
- 그림 37. 다양한 소성 온도에서 Trial E의 평균 MOR
- 그림 38. 1시간 후 200°C에서 소성된 Trial 1B에 대한 묽은 질산(1:1, 1:2 및 1:5)의 효과
- 그림 39. 4시간 후 200°C에서 소성된 Trial 1B에 대한 묽은 질산(1:1, 1:2 및 1:5)의 효과
- 그림 40. 다양한 소성 온도에서 Trial A의 평균 MOR
- 그림 41. 금속을 제대로 공급하지 않아 파단된 Al-LM25
- 그림 42. 코어 시험의 평균 경화 시간
- 그림 43. 다양한 소성 온도에서 Trial A의 평균 MOR
- 그림 44. 다양한 소성 온도에서 Trial B의 평균 MOR
- 그림 45. 다양한 소성 온도에서 Trial C의 평균 MOR
- 그림 46. 다양한 소성 온도에서 Trial D의 평균 MOR
- 그림 47. 다양한 소성 온도에서 Trial E의 평균 MOR
- 그림 48. 200°C에서 소성된 융용 실리카 메쉬 크기(-200/-120)를 가진 Trial 4A 코어 표면.
- 그림 49. 200°C에서 소성된 융용 실리카 메쉬 크기(-120/30-50)를 가진 Trial 4A 코어 표면.
- 그림 50. 묽은 수산화칼륨에 의해 부식된 Al-LM25.
- 그림 51. 200°C에서 묽은 구연산(1:1)으로 침출된 Trial 1B 코어.
- 그림 52. 코어 시험의 평균 경화 시간
- 그림 53. 다양한 소성 온도에서 Trial A의 평균 길이 수축률
- 그림 54. 다양한 소성 온도에서 Trial B의 평균 길이 수축률
- 그림 55. 다양한 소성 온도에서 Trial D의 평균 길이 수축률
- 그림 56. 다양한 소성 온도에서 Trial E의 평균 길이 수축률
- 그림 57. 다양한 소성 온도에서 Trial A의 평균 직경 수축률
- 그림 58. 다양한 소성 온도에서 Trial B의 평균 직경 수축률
- 그림 59. 다양한 소성 온도에서 Trial D의 평균 직경 수축률
- 그림 60. 다양한 소성 온도에서 Trial E의 평균 직경 수축률
- 그림 61. 다양한 소성 온도에서 Trial A의 평균 MOR
- 그림 62. 다양한 소성 온도에서 Trial B의 평균 MOR
- 그림 63. 다양한 소성 온도에서 Trial D의 평균 MOR
- 그림 64. 다양한 소성 온도에서 Trial E의 평균 MOR
- 그림 65. 코어 시험의 평균 경화 시간
- 그림 66. 다양한 소성 온도에서 Trial A의 평균 길이 수축률
- 그림 67. 다양한 소성 온도에서 Trial 2D의 평균 길이 수축률
- 그림 68. 다양한 소성 온도에서 Trial E의 평균 길이 수축률
- 그림 69. 다양한 소성 온도에서 Trial A의 평균 직경 수축률
- 그림 70. 다양한 소성 온도에서 Trial 2D의 평균 직경 수축률
- 그림 71. 다양한 소성 온도에서 Trial E의 평균 직경 수축률
- 그림 72. 다양한 소성 온도에서 Trial A의 평균 MOR
- 그림 73. 다양한 소성 온도에서 Trial 2D의 평균 MOR
- 그림 74. 다양한 소성 온도에서 Trial E의 평균 MOR
- 그림 75. 600 °C에서 Trial A의 분포 개요 플롯
- 그림 76. 600 °C에서 Trial E 및 2D의 분포 개요 플롯
- 그림 77. 800 °C에서 Trial A의 분포 개요 플롯
- 그림 78. 800 °C에서 Trial E 및 2D의 분포 개요 플롯
- 그림 79. (a) 800 °C에서 노치 코어 Trial 3A의 균열, (b) 600 °C에서 노치 코어 Trial 3A의 균열.
- 그림 80. 코어 시험의 평균 경화 시간
- 그림 81. 다양한 소성 온도에서 코어 조성물 [6]의 평균 MOR
- 그림 82. 다양한 소성 온도에서 코어 조성물 [7]의 평균 MOR
- 그림 83. 코어 조성물 [8] 및 [9]의 평균 경화 시간
- 그림 84. 다양한 소성 온도에서 코어 조성물 [8]의 평균 MOR
- 그림 85. 다양한 소성 온도에서 코어 조성물 [9]의 평균 MOR
7. 결론:
주요 연구 결과 요약:
본 연구는 융용 실리카, 석고 및 산화마그네슘을 사용하여 경합금용 수용성 코어 기술을 성공적으로 개발했습니다. 본 연구에서는 수산화나트륨보다 덜 공격적인 대안인 묽은 질산, 구연산 및 아세트산을 코어 제거에 사용하는 것이 가능하다는 것을 입증했습니다. 주요 결과에는 MOR, 슬러리 작업 수명 및 침출 특성에 대한 코어 조성의 영향이 포함됩니다. 미세 융용 실리카 입자는 코어 강도와 표면 마감을 개선했습니다. 최적의 코어 조성은 특정 응용 분야 요구 사항에 따라 강도, 침출 효율성 및 치수 안정성의 균형을 맞추어 결정됩니다.
연구의 학문적 의의:
본 연구는 경합금용 수용성 코어 기술에 대한 과학적 이해에 기여합니다. MOR, 파괴 인성 및 침출 거동을 포함하여 코어 특성에 대한 다양한 코어 조성 및 소성 온도의 영향에 대한 귀중한 데이터를 제공합니다. 또한 본 연구는 세라믹 코어의 신뢰성을 특성화하는 데 있어 와이블 분석의 적용을 발전시킵니다.
실용적 의미:
개발된 수용성 코어 기술은 기존 코어 시스템의 한계를 해결하여 알루미늄 및 경합금 주조에 대한 실용적인 솔루션을 제공합니다. 묽은 구연산 및 아세트산을 침출제로 사용하면 가성 소다에 대한 환경 친화적인 대안을 제시합니다. 본 연구 결과는 주조 공장에서 특정 주조 요구 사항 및 산업 응용 분야에 따라 적절한 코어 조성 및 침출 방법을 선택하는 데 지침을 제공합니다.
연구의 한계 및 향후 연구 분야:
본 연구는 실험실 규모로 수행되었으며, 산업 환경에서 기술을 검증하기 위한 추가 연구가 필요합니다. 본 연구에서는 향후 연구를 위한 여러 분야를 제시합니다.
- 기공률 및 밀도 분석: 코어의 기공률 및 밀도와 침출 속도에 미치는 영향 조사.
- 상 변화 분석: 최적의 소성 사이클을 위해 고온에서 코어 재료의 상 변화 분석.
- 상업적 생산 및 시험: 다양한 저융점 합금으로 상업적 주조 환경에서 코어 조성물 [4] 및 [5]의 생산 규모 확대 및 시험.
- 미세 융용 실리카 분말: 코어 마감, 강도 및 묽은 산으로부터의 침출 개선을 위해 더 미세한 분말 등급의 융용 실리카 사용 탐색.
- 크리프 특성: 고온에서 응력 변형 및 장기 성능에 대한 이해를 얻기 위해 크리프 거동 조사.
- 바인더 등급 변화: 다양한 바인더 등급(Ludox HS 및 SK)이 코어 특성에 미치는 영향 조사.
- 혼합 슬러리 주입 공정 최적화: 더 높은 입자 패킹 및 MOR을 달성하기 위해 혼합 슬러리 주입 공정 탐색.
8. 참고 문헌:
- [1. CAD Casting: Direct Fabrication of Ceramic Shells and Cores by Three Dimensional Printing, Sachs E B, Curodeau A D, Manufacturing Review (USA). Volume 5, p117-126, June 1992.]
- [2. Ceramic slurry composition for ceramic core of a dental prosthesis, Kim J D, Lee M H, Korean Science Technology, US patent 5975905, November 1999.]
- [3. Moulded ceramic cores for the production of precision cast impellers by the unicast process, Greenwood R E, Precision casting supplements, Foundry trade journal, p178-182, March 1984.]
- [4. Elements of material science and engineering, Van Vlack L H, Third edition, Addison- Wesley Publishing Company, 1975.]
- [5. Ceramic cores in the sand foundry, Greenwood R E, Cast metal times, p11-12, April 2002.]
- [6. Casting solutions Ltd, Robson B, Ceramic core and mould expert, Sheffield, February 2004.]
- [7. Principles of foundry technology, Jain P L, Second edtion, Tata McGraw Hill, 1996.]
- [8. Ferrous foundry-man’s handbook, Brown J, Elsevier, p18-20, July 2000.]
- [9. www.eos-gmbh.de/030356_appl_cm06.htm, 18 September 2006.]
- [10. http://www.core-tech-inc.com/form_ground.html, 18 September 2006.]
- [11. Properties of ceramic cores, Mills D, The British investment casters technical association, Fifteenth annual conference, 1980.]
- [12. Principle of metal casting, Heine R W, Loper C R, Philip C, Second edition, Tata McGraw-Hill, New Delhi,p121-175, 1976.]
- [13. http://www.enercombustion.com/EnServices.htm,19 September 2006.]
- [14. Methods of firing core, Altoonian M A, Runions R D, US patent 6403020-B1, p1-7, June 2002.]
- [15. Ceramic core; Nucleus for precision internal section, Greenwood R E, Unicast development corporation, Modern technology, p29-31, 1985.]
- [16. Alumina-based ceramics for core materials, Greskovich C D, US patent 4156614, GE company, p1-4, October 1977.]
- [17. Low temperature co-fired ceramic with improved registration, Shepherd P N, US patent 6560860-B2, CTS Corporation, p 1-6, January 2001.]
- [18. Injection molding of ceramic components provides flexibility in metal casting and forming, Uram S, Industrial heating, p42-43, 1987.]
- [19. Multipiece core assembly for cast airfoil, Sikkenga W E, Grumm A W, Howmet research corporation, US patent 6347660, February 2002.]
- [20. The effect of cristobalite seed on the crystallization of fused silica based ceramic core- A kinetic study, Wang L Y, ceramic international, p187-193, 1995.]
- [21. Printed materials on manufacturing fused silica, Minco Company, Midway, TN, USA, 2004.]
- [22. Dimensional changes and creep of silica core ceramics used in investment casting of supper alloys, Wereszczak A A, Breder K, Journal of material science, p 4235-4245, April 2002.]
- [23. Alumina core having a high degree of porosity and crushability characteristics, Klung F J, US patent 4164424, GE company, p1-12, August 1979.]
- [24. Basic inorganic chemistry, Cotton A, Gaus P L, Third Edition, Wiley J &sons Inc, p307-208, 1995.]
- [25. Printed material for calcium silicate and Lithium carbonate, Material safety data sheet, Sigma Aldrich Company, Pool,Doorset, UK, 2002.]
- [26. A textbook of quantitative inorganic analysis, Vogel A I, Second edition, Longmans, s1939.]
- [27. BPB gypsum special plasters, Data sheets on plasters, BS EN 9002:1994.]
- [28. Printed material data sheet for tri-sodium citrate, University of Teesside Chemistry online database, 2005.]
- [29. CRC handbook of chemistry and physics, Forty fourth edition, p2292.]
- [30. Ludox AM®, Colloidal silica data sheet, Grace division , Grace W R & Co, Worms, Germany, 2006.]
- [31. Water Soluble cores and methods for manufacturing cast rotor, Aiga T, Toshiaki M, US patent 4438804, March1984.]
- [32. Basic inorganic chemistry, Cotton A, Gaus P L, Third edition, Wiley J &sons Inc, p231-232, 1995.]
- [33. Inorganic Chemistry , An Intermediate Text, Wood C W, Holliday A K, Third Edition, Butterworth’s, 1967,p165-166.]
- [34. Standard test method for flexural strength of advanced ceramics at ambient temperature, ASTM Standard C1161.]
- [35. Materials handbook, Brady G S, Clauser H R, Vaccari J A, fifteenth edition, McGraw-Hill, 2002.]
- [36. http://www.qualitydigest.com/jan99/html/body_weibull.html,19 September 2007.]
- [37. Interpret the shape, scale, and threshold on a Weibull probability plot, ID766, Minitab help handbook.]
- [38. Weibull Analysis, Weibull W, Journal of applied mechanics, p293-297, 1951.]
- [39. Engineering materials 2, Ashby M F, Jones D R H, Third edition, Elsevier Publications, p196-197, 2006.]
- [40. Strength, fracture toughness and microstructure of a selection of all ceramic materials, Ringer S P, Swain M V, Dental materials, p441-448, June2004.]
- [41. Fracture toughness comparison of three test methods with four dental porcelains, Wang H, Pallav P, Dental materials, p905-910, July2007.]
- [42. Engineering Materials 2 , Ashby M F, Jones D R H, Third edition, Elsevier Publications, p198-199, 2006.]
- [43. Aluminum alloys- structures and properties, Mondolfo L f, Butterworths London and Boston, p971, 1976.]
- [44. Aluminum LM25 data sheet, MRT casting limited, Foundries and machinist for non-ferrous cast parts, www.mrt-castings.co.uk., 20th September 2007.]
- [45. 일반적으로 사용되는 마그네슘 합금은 알루미늄, 아연, 망간, 구리, 실리콘, 철 및 니켈을 포함하는 화학 조성을 가지고 있습니다.]
- [46. 구리 및 그 합금은 용융 금속으로 만든 가장 초기의 금속 물체 중 하나였습니다. 구리는 천연 금속으로 발견되었기 때문에 인공물로 가공되었습니다. 구리 생산의 주요 부분은 구리 함량을 위해 주로 채굴되는 광석에서 나옵니다. 주요 합금 원소에는 니켈, 아연 및 다양한 금속의 조합이 포함됩니다. 금, 주석 및 아연을 포함한 구리 및 그 합금의 융점은 목재 및 숯불로 도달할 수 있는 온도 범위 내에 있을 만큼 충분히 낮습니다.]
- [47. 구리 주조 합금은 우수한 내식성, 전기 전도성, 우수한 베어링 표면 품질 및 기타 특수 특성이 요구되는 서비스에 대해 지정됩니다. 불순물에 대한 허용 오차는 일반적으로 열간 또는 냉간 가공성에 대한 부작용 때문에 단조 구리보다 주물에서 더 큽니다.]
- [48. 표 17. 다양한 알루미늄 주조 공정 비교 (48)]
- [49. 압력 다이캐스팅은 모든 주조 공정 중 가장 빠르며, 동일한 부품을 대량으로 필요로 하는 스탬핑, 다이 단조, 플라스틱 사출 성형과 경쟁합니다. 용융 금속은 고압 하에서 몰드 캐비티로 강제로 주입됩니다. 핫 챔버(금속이 챔버로 흐름)와 콜드 챔버는 압력 다이캐스팅에 사용되는 두 가지 유형의 기계 원리입니다. 금속은 고속 제트로 다이에 들어가며, 제트의 치수와 속도는 게이트와 러너의 치수에 따라 달라집니다. 이 제트는 다이 캐비티의 반대쪽 면을 때리고 모든 방향으로 퍼져 다이 캐비티를 빠르게 채우고 캐비티가 채워짐에 따라 난류 흐름으로 분해됩니다. 응고는 압력 하에서 발생합니다. 다이 자체는 일반적으로 강철 단조품에서 가공되며, 복잡한 캐비티에는 스파크 부식 방법이 사용됩니다.]
- [50. 알루미늄, 마그네슘, 구리 기반 및 기타 고융점 합금은 콜드 챔버 원리(금속을 챔버에 붓는 방식)를 사용합니다. 압력 다이캐스팅을 사용하면 제품 생산에 필요한 시간(조립)과 비용(툴링)이 절감됩니다.]
- [51. 모래 주조는 모래로 만든 몰드를 사용하여 거친 금속 주물을 생산하는 수단입니다. 모래는 주조할 물체의 복제품 주위에 형성되며, 모래가 압축되면 제거됩니다. 중간 크기의 "녹색" 모래 몰드는 상부(코프)와 하부(드래그)의 두 부분으로 구성된 플라스크에 둘러싸여 있습니다. 원하는 주물의 모양은 몰딩 모래가 형성되는 패턴에 의해 시뮬레이션됩니다. 패턴은 나무 또는 금속으로 만들어지며, 함께 끼울 수 있는 두 부분으로 되어 있습니다. 녹색 모래는 드래그에 놓인 패턴의 절반 주위에 다져집니다. 동일한 공정이 코프에서 스퍼(러너) 및 게이트(라이저)와 함께 수행됩니다.]
- [52. 알루미늄 합금을 모래 주조할 때 가스 함량과 결정립 미세화는 고려해야 할 두 가지 특별한 사항입니다. 가스 함량은 블로우홀 및 기공 형성 방지를 위해 합리적으로 낮은 수준으로 제어해야 합니다. 탈기 정제(헥사클로로에탄)는 가스 함량을 제어하는 데 사용됩니다. 천천히 냉각된 주물에서는 큰 결정이 형성되어 기계적 특성이 저하되는 경향이 있을 수 있습니다. 티타늄과 붕소를 첨가하면 알루미늄 합금 모래 주조에서 결정립 미세화를 방지할 수 있습니다.]
- [53. 주물에서 결함의 형태와 위치는 크기보다 더 중요한 경우가 많습니다. 주물의 낮은 응력 영역에 있는 큰 기공은 높은 인장 응력을 받는 날카로운 모서리에 있는 작은 "바이필름"보다 덜 해로울 수 있습니다. 다이가 마모되었거나 단단히 고정되지 않은 경우 핀 또는 플래시가 발생할 수 있습니다. 또한 런아웃이 발생할 수도 있습니다. 주물 부품]
- [54. 그림 8. (a) 코어 블로우 (b) 응고 전 코어에서 발생한 가스로 인한 결함 (54)]
- [55. 1974년 영국 주철 연구 협회(BCIRA)는 "쇄석술"을 사용하여 무거운 코어 주물의 내부 통로에서 CO2 코어 모래를 느슨하게 하는 것을 보고했습니다. 금속 코어 박스는 코어를 대량 생산하거나 더 내구성이 있는 격리가 필요한 경우에 선호됩니다.]
- [56. 초음파 진동을 사용하여 코어를 제거하려는 다른 시도가 있었습니다. 초기 시험에서는 터빈 블레이드에서 코어를 제거하기 위해 초음파 진동만을 사용했습니다. 이것은 주물이 담겨 있는 뜨거운 가성 알칼리를 통해 생성 및 전파되는 초음파를 사용하여 기계적 및 화학적 코어 제거 기술을 결합하는 것으로 발전했습니다.]
- [57. 대형 커패시터 뱅크에서 생성된 전기 에너지는 집중될 수도 있습니다. 물 속의 충격파에서 부품으로 전달되는 압력파의 강도는 세라믹 코어 자체의 음향 임피던스에 따라 달라지므로 세라믹 코어에 사용되는 재료의 강도를 아는 것이 필요합니다.]
- [58. 물줄기가 큰 압력으로 코어에 집중되고 코어가 점진적으로 씻겨 나갑니다. 이 절차는 목적에 맞게 제작된 시설 또는 블라스팅 룸에서 진행됩니다. "Cerabite"는 전형적인 상업적 공정의 예입니다.]
- [59. 그림 7. 모래 코어를 사용한 모래 주조 (59)]
- [60. 미세 융용 실리카 입자를 사용하면 혼합이 개선되고 매끄럽게 흐르는 쉬운 슬러리가 생성되었으며, 허용 가능한 경화 및 나무 코어 상자에서 제거가 가능했습니다. 이러한 코어는 부어 넣은 코어이기 때문에 전체 평균 강도는 혼합 슬러리를 압력 하에서 코어 상자에 주입하여 만든 프리폼 코어보다 낮습니다.]
- [61. 물은 일반적으로 바인더로 생각되지 않습니다. 최적의 비율의 물이 코어 혼합물에 존재하지 않으면 바인더와 첨가제가 제대로 작동하지 않습니다. 물을 충분히 사용하지 않으면 "시리얼"에서 녹색 강도가 발달하지 않고 긁힘 경도가 낮으며 소성 후 인장 강도가 낮아집니다. 이 요소는 물 분자를 강한 양성자 수용체로 만듭니다.]
- [62. 다양한 재료를 치과용 석고와 물에 첨가하면 강도와 조성의 균형이 깨지기 때문에 다양한 온도에서 소성했을 때 코어의 MOR 변화가 예상됩니다.]
- [63. 높은 비율의 바인더를 세라믹 원료에 첨가하면 슬러리 흐름이 매우 부드럽고 느려집니다.]
- [64. 산화마그네슘을 사용하면 혼합된 슬러리가 매우 빠르게 경화됩니다. 콜로이드 실리카를 사용하면 4~10분 이내에 뜨거운 물에서 쉽게 경화될 수 있는 세라믹 슬러리가 형성됩니다.]
- [65. 세라믹 코어의 도입은 경쟁력 있는 비용과 단축된 시간으로 매끄러운 정밀 내부 캐비티를 갖춘 모래 주조 공장에 도움이 되었습니다. 다른 곳의 연구자들은 1530 - 1600 °C에서 소성하고 최대 온도에서 10~30분 동안 유지한 6개의 서로 다른 실리카 코어를 조사했습니다.]
- [66. 경합금용 세라믹 코어 시스템. 단일 소성 사이클을 갖는 세라믹 코어는 대부분 1300 °C 이상에서 소성됩니다. 더 높은 온도는 세라믹 재료의 더 작은 치수 변화와 경화를 확인합니다.]
- [67. 반무한 폭의 플레이트가 단일 중심 또는 가장자리 균열을 포함하는 경우 길이 Y (a/W)는 1.1입니다. 세라믹 재료의 KIC 값은 금속보다 작으며, 일반적으로 10 MN √m보다 작습니다. 일반적으로 세라믹은 열팽창 계수가 낮습니다. 세라믹 재료에서 발견되는 강한 원자간 결합력은 0.5-15 × 10-6 (per °C) 범위의 열팽창 계수 값을 제공합니다.]
- [68. 산화마그네슘 및 인산칼슘 코어는 실리카 기반 코어의 사용을 피하기 위해 슈퍼합금을 주조하는 데 사용되었으며, 이는 비부식성 침출 매체를 사용하여 침출하기 어렵습니다.]
- [69. 75% 산화마그네슘과 25% 염화마그네슘 혼합물을 사용하여 슬러리를 형성했습니다.]
- [70. 경금속 및 슈퍼합금의 경우 묽은 질산과 수산화칼륨과 같은 염기가 사용됩니다. 코어 시험의 평균 경화 시간은 Trial C의 경우를 제외하고 모든 상업적 응용 분야에 이상적이었습니다.]
- [71. 침출 속도는 밀도가 20-25%인 경우 약 10 mm/h입니다.]
- [72. 규산칼슘, 염화나트륨, 염화칼륨 및 메타규산나트륨을 첨가하여 코어를 생산합니다.]
- [73. "그린캐스트" 공정은 수용성 코어를 사용하여 열가소성 수지 및 열경화성 수지에서 중공 부품을 생산하는 새로운 로스트 코어 기술입니다.]
- [74. 산은 염기에 수소 이온을 나타낼 수 있는 물질(양성자 수용체)입니다.]
- [75. 0.05% MgO를 첨가한 실리카 재료로 생산된 세라믹 코어는 합성 비정질 실리카(바인더)로 2% 수축률을 나타냈습니다. 코어 수축률의 양은 코어 재료 슬러리에서 합성 비정질 실리카의 백분율에 따라 직접적으로 달라집니다.]
- [76. 실리카(17%), 지르콘(30%) 및 바인더(콜로이드 실리카 겔)로 생산된 세라믹 코어는 치수에서 0.5%의 수축률을 나타냅니다.]
- [77. 표 3. 융용 실리카의 특성 (77)]
- [78. 고급 세라믹의 평면 변형률 파괴 인성은 3 MN m-3/2만큼 낮을 수 있고 12 MN m-3/2만큼 높을 수 있습니다.]
- [79. 3점 굽힘에서 반원형 노치가 있는 원형 단면에 대한 'Y'를 계산하기 위해 폐쇄형 솔루션이 개발되었습니다.]
- [80. 균열 또는 노치가 절단면(날카로운)을 갖는 경우 응력 집중 정도가 낮아지고 가짜 값을 제공할 수 있습니다.]
- [81. 인산수소나트륨을 바인더로 사용했습니다.]
- [82. 탄산리튬은 중요한 산업 화학 물질입니다. 실리카 및 기타 재료와 함께 저융점 플럭스를 형성합니다.]
- [83. 여러 첨가제 또는 촉진제를 첨가하면 코어의 경화 시간과 강도가 증가한다고 주장되어 왔습니다.]
- [84. 표준 온도 및 압력에서 해리된 산은 완전히 해리된 강산과는 대조적으로 수용액에서 비해리된 형태로 평형 상태로 존재하기 때문에 약산으로 간주됩니다.]
- [85. 표 9. 아세트산의 특성 (85)]
- [86. 수산화나트륨은 물에 매우 잘 녹으며 열을 방출합니다.]
- [87. 농축된 수산화칼륨 수용액을 수산화칼륨 "라이"라고 합니다.]
- [88. 하나의 오토클레이브 기술은 주물을 수산화칼륨 수용액(예: 45% KOH)에 상승된 압력 및 상승된 온도(예: 1.72 MN/m2 및 177 °C)에서 적절한 시간 동안 담가 코어를 주물에서 용해 또는 침출시키는 것을 포함합니다.]
- [89. 모범적인 개방형 주전자 기술은 주물을 유사한 수성 가성 용액에 담그는 것을 포함합니다.]
- [90. 슈퍼 합금 에어포일 주물의 내부 통로에서 세라믹 코어 재료를 제거하는 방법은 주물의 외부 루트 표면의 통로 개구부에서 물을 포함하는 가압 유체를 분출하는 것을 포함합니다. 이것은 가압 유체를 분출하는 것은 컴퓨터 수치 제어(CNC) 기계에 의해 제어됩니다.]
- [91. 세라믹의 취성 특성으로 인해 평균 "6 mm"에서 비교적 큰 수동 노치 또는 균열이 반원형이라고 가정합니다.]
- [92. 무기 바인더에 의해 나타나는 전형적인 결함에는 코어와 몰드와 같은 몰딩 모양에 대해 제안된 규산염이 낮은 붕괴성을 갖는다는 결과와 금속 주물에서 몰딩 모양을 제대로 제거하지 못한다는 결과가 포함됩니다.]
- [93. 융용 실리카는 침출하는 데 시간이 더 오래 걸리고 산화마그네슘은 혼합 슬러리를 너무 빨리 경화시키기 때문에 두 재료 모두에 대한 대안을 검토합니다.]
- [94. 본 프로젝트는 확립된 수용성 코어 기술을 사용하여 코어 모양을 생산하는 것을 모색하되, 코어를 가성 소다보다 훨씬 덜 공격적인 침출제인 묽은 아세트산 등을 사용하여 알루미늄 및 합금 주물 내부에서 제거할 수 있도록 조성을 수정하는 것을 모색할 것입니다.]
- [95. 아마인유 기반 유기 바인더는 널리 사용됩니다. 수지 및 희석제를 포함하여 우수한 습윤성 및 작업성 특성을 제공합니다.]
- [96. 실험 설계 기술은 평가되었지만, 예: Taguchi는 궁극적으로 사용되지 않았습니다.]
9. 저작권:
- 본 자료는 "[Manu Ramegowda]"의 논문: "[Development of water-based core technology for light alloys]"을 기반으로 함.
- 논문 출처: http://tees.openrepository.com/tees/handle/10149/112685
본 자료는 위 논문을 소개하기 위해 제작되었으며, 상업적 목적으로 무단 사용하는 것을 금지합니다.
Copyright © 2025 CASTMAN. All rights reserved.