This introductory paper is the research content of the paper "Improvement of the Die Casting Molds Cavities by Ceramic Surface Treatment" published by Interdisciplinarity in Engineering International Conference.

1. Overview:
- Title: Improvement of the Die Casting Molds Cavities by Ceramic Surface Treatment
- Author: Ferencz PETI, Lucian GRAMA, Ioan SOLOVĂSTRU
- Publication Year: 2012
- Published Journal/Society: Interdisciplinarity in Engineering International Conference
- Keywords: Mold, Aluminium, High Pressure Die Casting, Surface Treatment, Hard Surface
2. Abstract
The main components of the molds the cavities and inserts, which gave the final shape of the part, have a life time limited to a number of cycles due to the wear caused by the temperature of the injected aluminium in the mould, due to the thermal fatigue, due to the cracks which appears mainly in the ingate area and due to the undercuts or under washes caused by the aluminium injected with high pressure in the cavities.
3. Research Background:
Background of the research topic:
The lifespan of die casting molds is limited by wear, thermal fatigue, and cracks, especially in the ingate area. These issues are caused by the high temperature and pressure of injected aluminum.
Status of previous research:
Previous research has investigated various methods to improve mold life, including different materials and coating techniques.
Need for research:
There is a continuous need to improve the lifespan and resistance of die casting molds, particularly in areas susceptible to underwashes caused by aluminum flow.
4. Research purpose and research question:
Research purpose:
To increase the lifetime of molds and improve the resistance of ingate areas, aiming to reduce underwashes caused by aluminum flux.
Core research:
Investigating the application of a thin ceramic material (tungsten carbide or titanium carbide) on the active elements of molds using the "rocklinizer" method.
5. Research methodology
The research describes the materials, equipment, and process of applying hard surface treatments to die casting molds. The method is named "rocklinizing". The materials used are tungsten carbide and titanium carbide. The properties of these materials are detailed, including their chemical and physical characteristics. The equipment used is the Rocklinizer, with various models and electrode options presented. The application process involves electronically impregnating and depositing wear-resistant material onto the metal surfaces of the mold.
6. Key research results:
Key research results and presented data analysis:
- Tungsten carbide (WC) and titanium carbide (TiC) are identified as suitable materials for hard surface treatment due to their high hardness, wear resistance, and thermal stability.
- The Rocklinizer equipment and process can apply these materials to the active surfaces of molds.
- The Rocklinizer process deposits material both underneath and on top of metal surfaces, creating a strong bond without significant heat generation.
- The process can increase productivity and reduce costs by extending tool life and reducing downtime.
- Specific application areas on molds are identified, including the gate channel, cores, and areas prone to soldering.
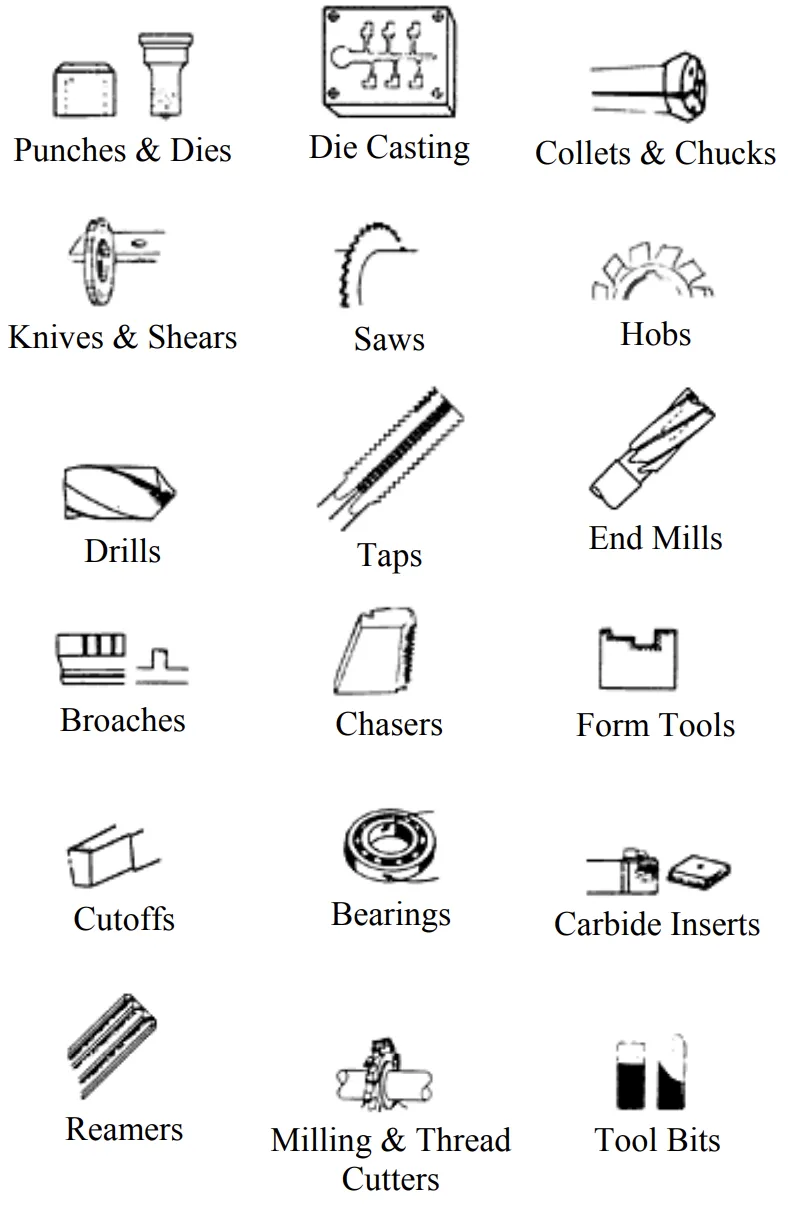
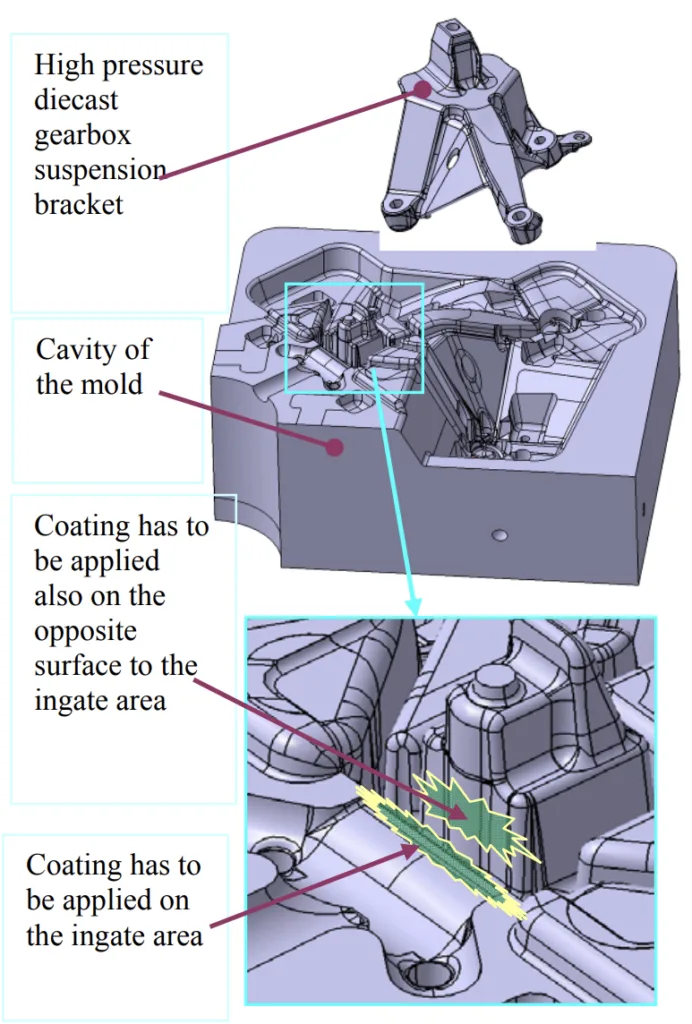
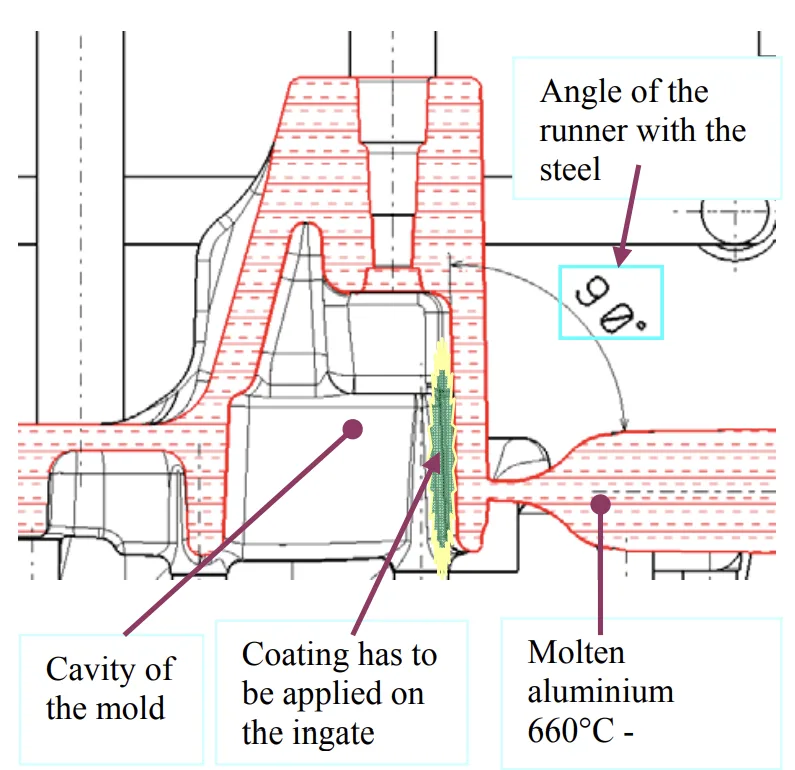
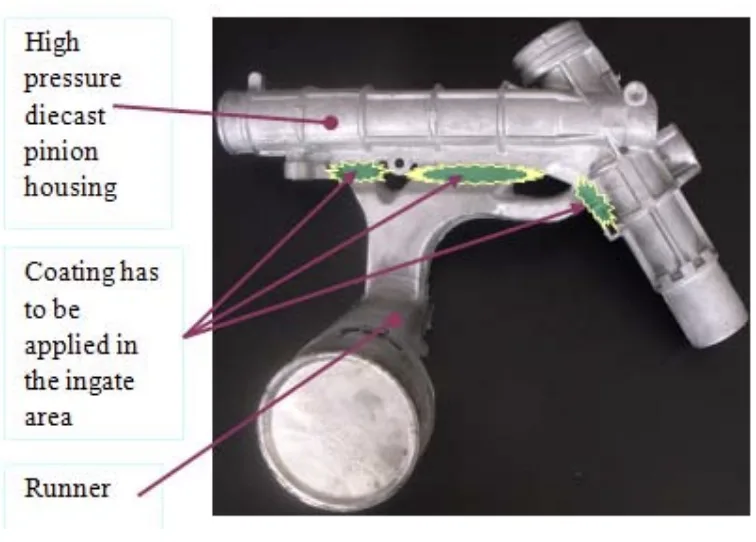
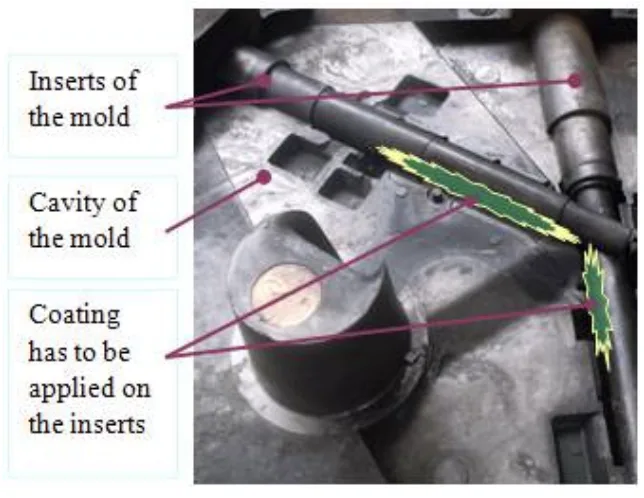
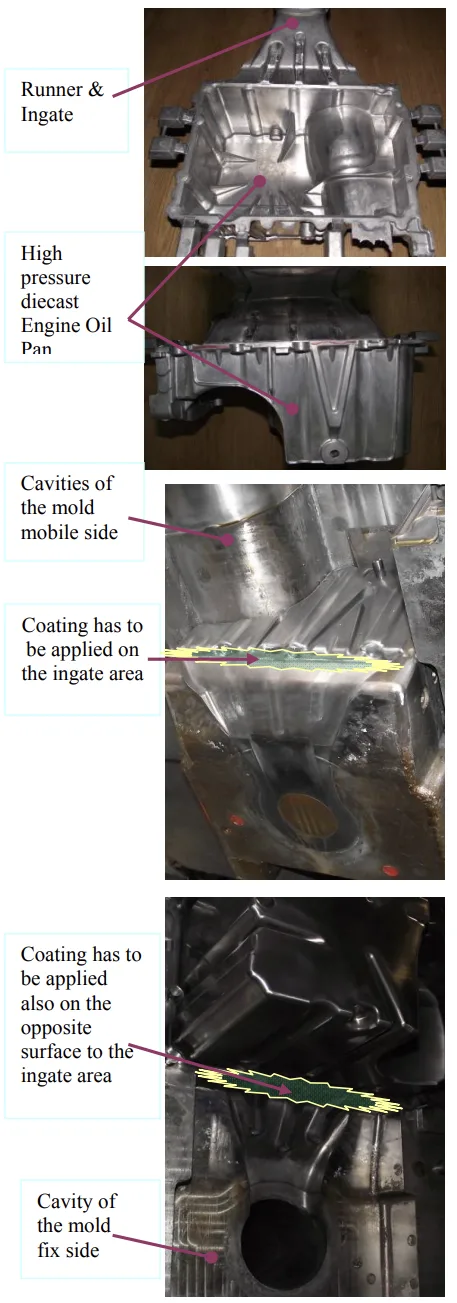
List of figure names:
- Fig. 1 - Tungsten carbide structure
- Fig. 2 - The molecular structure of the titan carbide TiC
- Fig. 3 - Coated areas in the case of a HPDC mould for a gearbox suspension bracket
- Fig. 4 - Orientation of the molten aluminium to the steel of the mould
- Fig. 5 - Coated areas in the case of a HPDC mould for a pinion housing
- Fig. 6 - Coated areas in the case of a HPDC mould for a pinion housing
- Fig. 7 - Coated areas in the case of a HPDC mould for an engine oilpan
7. Conclusion:
Summary of key findings:
The Rocklinizer method, using tungsten carbide or titanium carbide, can effectively apply a hard and wear-resistant surface to die casting molds. This treatment can prolong mold life, reduce wear, and minimize issues like soldering, ultimately improving productivity and reducing costs. The application of this method is particularly beneficial in high-wear areas like the ingate.
8. References:
- [1] ERNST, B., (1991), Praxis der Druckgussfertigung, Ed. Schiele & Schön, Berlin, Germany
- [2] HERBERT, R., (2002), Mold Engineering, Ed. Carl Hanser Verlag, Munich, Germany
- [3] Faisal, F., Gyuyeol, B., (2011), Evaluation of Die-Soldering and Erosion Resistance of High Velocity Oxy-Fuel Sprayed MoB-Based Cermet Coatings, Journal of Thermal Spray Technology, Volume 20, Number 5, Pages 1022-1034
- [4] GRAMA, L., PETI, F., (2009), Analyze of the opportunities of the coating of the active elements of the high pressure die casting molds, Ed. UORADEA, Romania
- [5] MIHĂILĂ, I., (2003), Tehnologii Neconvenționale, Ediția II, Ed. Universității din Oradea, Romania
- [6] MONTES, J., (2008), Revision Tecnica del Producto, CIE C. Vilanova, Spain
- [7] NANU, A., (2003), Tratat de tehnologii neconvenționale, Vol.1, Tehnologii neconvenționale la început de mileniu, Ed. Angusta, Timişoara, Romania
- [8] STREET, A., (1977), The diecasting handbook, Portcullis Press LTD, UK
- [9] Ugues, D., (2006), Hard coatings to prevent the washout phenomena in high pressure die casting tools, Ed. BHM Berg- und Hüttenmännische Monatshefte, Volume 151, Number 3, Pages 109-112
- [10] Woon, Y.K., (2004), Development of a die design system for die casting, The International Journal of Advanced Manufacturing Technology, Volume 23, Numbers 5-6, Pages 399-411
- [11] The Society of Manufacturing Engineers website, (2012), [Online]. Available: http://www.sme.org
- [12] The Rocklin Manufacturing co. Website, (2012), [Online]. Available: http://www.rocklinmanufacturingco.com
- [13] The Wikipedia website, (2012), [Online]. Available: http://en.wikipedia.org/wiki/Die_casting
- [14] The CIE Automotive website, (2011), [Online]. Available: http://ciepedia.cie.lan/ciepedia/index.php
- [15] The North American Die Casting Association website, (2012), [Online]. Available: http://www.diecasting.org
- [16] Casting of Light Metals, (2007), Engineering Materials and Processes, Casting: An Analytical Approach, Pages 1-12
- [17] Norma Ingenieria NCV21007B, (2006), Velocidad en el ataque, CIE C. Vilanova, Spain
- [18] Part Design, (2007), Engineering Materials and Processes, Casting: An Analytical Approach, Pages 43-96
- [19] Procedimiento IDT 05/1, (2007), Cuaderno de cargas de moldes, rev05, CIE Inyectametal, Spain
- [20] Process Design, (2007), Engineering Materials and Processes, Casting: An Analytical Approach, Pages 97-155
9. Copyright:
- This material is a paper by "Ferencz PETI, Lucian GRAMA, Ioan SOLOVĂSTRU": Based on "Improvement of the Die Casting Molds Cavities by Ceramic Surface Treatment".
- Source of paper: Not mentioned in this paper.
This material was created to introduce the above paper, and unauthorized use for commercial purposes is prohibited. Copyright © 2025 CASTMAN. All rights reserved.