This introductory paper is the research content of the paper "Improvement and stabilization of the electrochemical properties of zinc alloys during casting" published by Int. J. Corros. Scale Inhib..
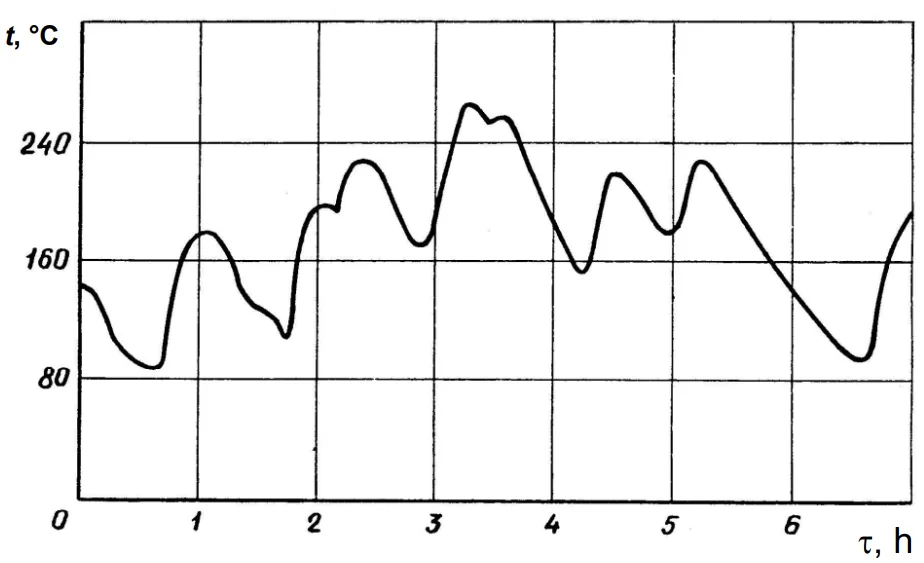
1. Overview:
- Title: Improvement and stabilization of the electrochemical properties of zinc alloys during casting
- Author: V.A. Kechin, E.Y. Lyublinski, A.V.Kireev and E.S. Prusov
- Publication Year: 2019
- Published Journal/Society: Int. J. Corros. Scale Inhib.
- Keywords: sacrificial anodes, structure, foundry, electrochemistry
2. Abstract
The main reasons for the appearance of electrochemical heterogeneity of cast sacrificial galvanic anodic alloys in the “metal-electrolyte" system are internal factors related to the nature of the metal, its composition, structure, etc. Obviously, when developing the technology for manufacturing of cast anodes, special attention should be paid to ensuring the structural homogeneity of the alloys. The main role in the formation of the structure and basic properties of cast anodes is played by thermal processes that affect the conditions for solidification of the melt in the mould. The results of studies of the structure and basic electrochemical properties of cast zinc sacrificial alloys (ZSA) depending on the cooling conditions are presented in this paper. The analysis of the temperature fields of the solidifying metal (when the metal is cooled) and the shape (when the mould is heated) at different cooling intensities has made it possible to optimize the duration of the casting cycle. This takes into account the cooling conditions determined by the initial temperature of the mould, which ensures a homogeneous structure and stable electrochemical properties of the material over the entire thickness of the tread. For example, it is established that for the casting of zinc alloys treads weighing 18 kg, the temperature of the mould before casting should be 120–160°C. In these conditions, the necessary quality of cast sacrificial anodic alloys is achieved: Current Capacity-Efficiency 93–96%; Corrosion Potential -Ec = 815–820 mV vs. SHE. The required duration of the casting cycle is 10–14 min. Similar data was obtained for sacrificial anodes of various shapes and sizes. Based on the results of studies of the thermal interaction of zinc anodes with a casting mould (sandy-argillaceous, cast iron and steel water-cooled) using numerical simulation methods, the expediency of casting anodes into water-cooled moulds is provided, providing the most favorable conditions for heat removal and obtaining a homogeneous structure of cast treads. Based on the results obtained, a technology has been developed for casting zinc anodes of various sizes, which provides high and stable electrochemical properties.
3. Research Background:
Background of the research topic:
- Thermal processes play a leading role in the formation of most properties of castings during the solidification of the melt [1-11].
- Studying the conditions for solidification of the melt in a mould is the most important task of the thermal theory of casting.
Status of previous research:
- When casting sacrificial anodes (SA), there are significant temperature fluctuations of metallic moulds [12].
- Continuous monitoring of temperature on one of the series cast iron moulds during zinc SA casting showed that the initial mould temperature changes from 80 to 260°C during a shift (Figure 1).
- The current capacity (CC) of zinc-aluminum alloy drops from 96 to 80% when the mould temperature changes from 20 to 300°C.
- When considering the macrostructure of the ZSA, filled in metal moulds with different initial temperatures, three characteristic zones are distinguished: cortical, columnar and non-oriented crystals (Figure 2).
Need for research:
- Temperature fluctuations can explain the destabilization and reduction of the ZSA electrochemical properties.
- There is a need to control the temperature of the moulds before casting to avoid dispersion of protective properties, especially CC.
- Different cooling conditions lead to a change in the temperature drop across the section of the cast sacrificial anodes, thereby changing its crystal structure and properties.
4. Research purpose and research question:
Research purpose:
- To study the structure and basic electrochemical properties of cast sacrificial anodes from Zn-Al alloys depending on the thermal conditions of cooling.
Core research:
- Investigating the influence of cooling conditions on the structure and electrochemical properties of cast zinc sacrificial alloys.
- Optimizing the casting cycle duration based on the initial temperature of the mould.
- Developing a technology for casting zinc anodes with high and stable electrochemical properties.
5. Research methodology
- Research Design: Experimental study, using methods of thermometry and pouring out. Numerical simulation methods were also employed.
- Data Collection:
- Thermometry: Temperature fields of the tread and the shapes were constructed from the cooling curves of the melt solidification. Thermocouple arrangement (Figure 3) was used with a twelve-point potentiometer.
- Pouring out: Alloy was poured out at regular intervals to determine the nature of solidification.
- Electrochemical tests: Samples were tested in a 3% aqueous solution of NaCl with anodic polarization (Figure 4). Potentials were measured using a potentiator model IPC and a silver chloride reference electrode.
- Analysis Method: Analysis of temperature fields, macrostructure examination (Figure 2), and electrochemical testing. Regression equations were developed to describe the relationship between CC and casting temperature/solidification rate.
- Research Scope: Tread alloy of the Zn-Al system (Table 1). Casting temperature was kept constant at 480°C. Initial temperatures of the cast iron mould were 20, 160, and 310°C.
6. Key research results:
Key research results and presented data analysis:
- Different cooling conditions lead to changes in the crystal structure and properties of the cast sacrificial anodes.
- The best conditions for directional solidification are provided at a higher temperature drop (solidification in a mould with a temperature up to 160°C).
- The time of complete solidification of the ZSA tread in a metallic mould varies with the initial temperature (Table 2).
- The temperature of the mould before casting zinc alloy treads weighing 18 kg should be 120–160°C to achieve the necessary quality (Current Capacity-Efficiency 93–96%; Corrosion Potential –Ec = 815–820 mV vs. SHE).
- The required duration of the casting cycle is 10–14 min (Figure 7).
- The CC of alloys increases with the rate of solidification (Figure 10).
- Regression equations:
- CC = 127 – 0.072tc (Equation 1)
- CC = 84.21 + 0.035 Vs (Equation 2)
- Water-cooled moulds provide the most favorable conditions for heat removal and obtaining a uniform structure.
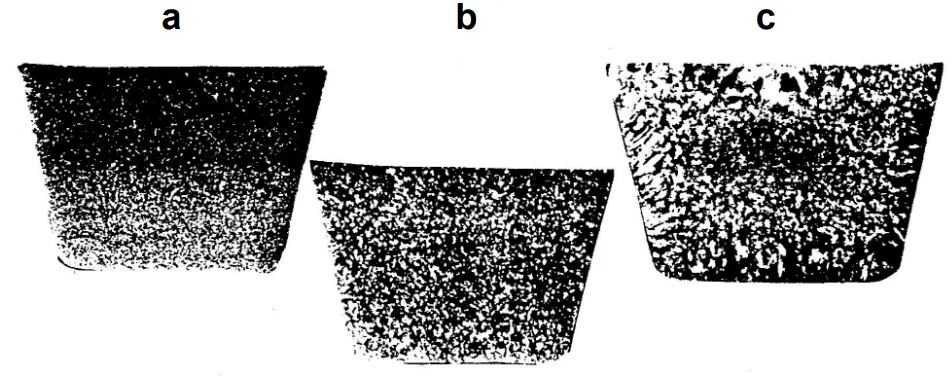

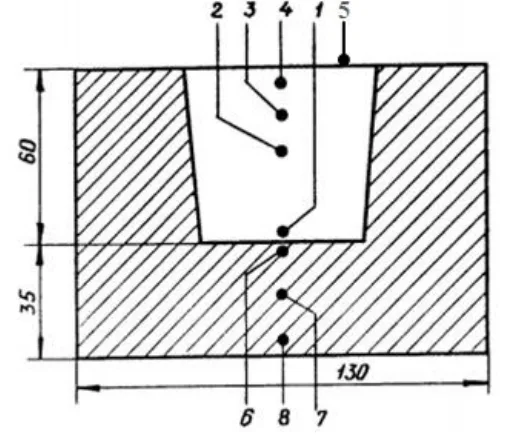

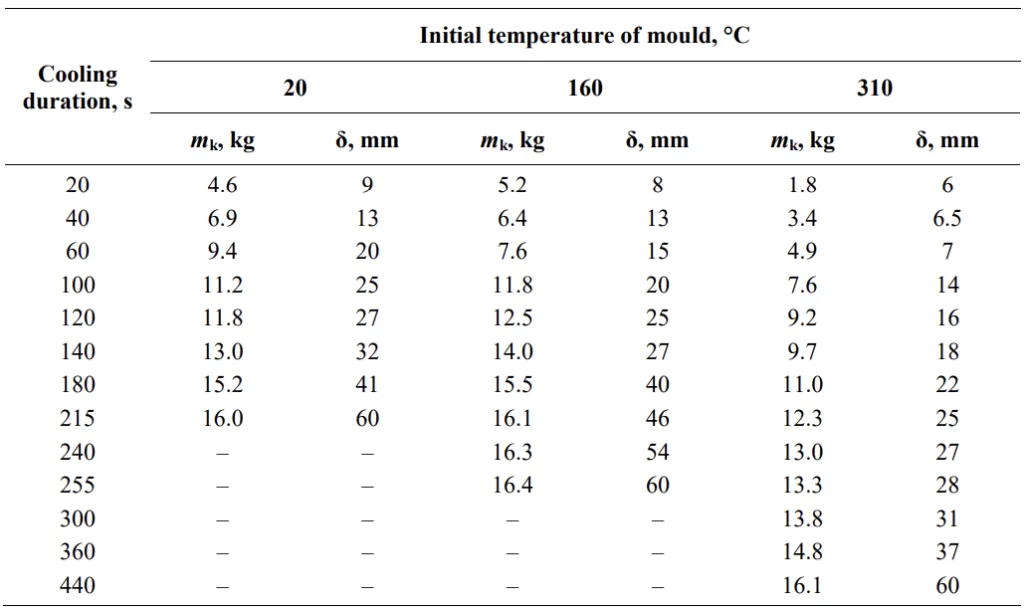
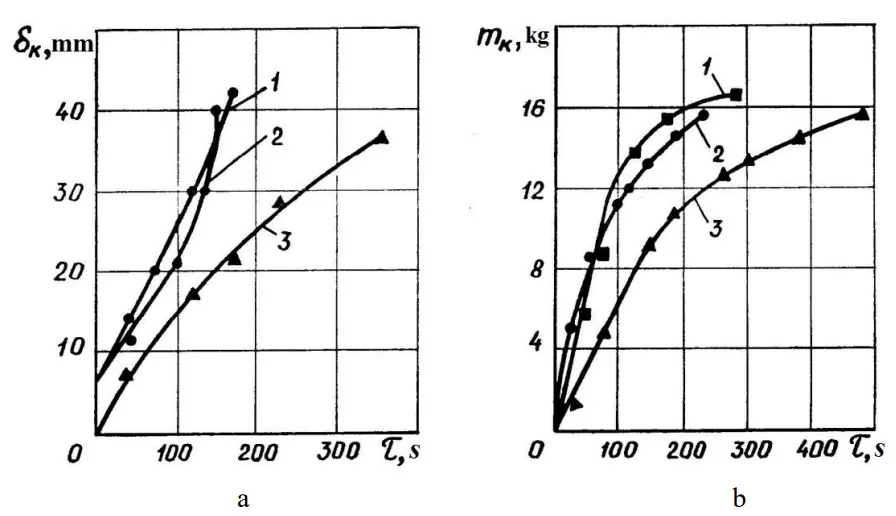
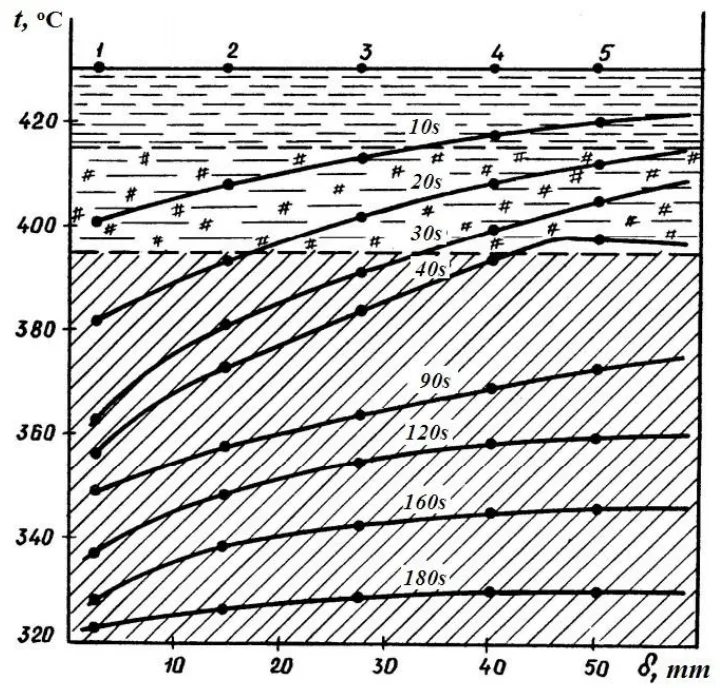
List of figure names:
- Figure 1. Change in mould temperature during the cast of ZSA.
- Figure 2. Macrostructure of zinc sacrificial anodes under various conditions of solidification and cooling in the mould at initial temperature of the mould 20°C (a), 160°C (b) and 310°C (c).
- Figure 3. The scheme of installation of thermocouples for measuring the temperature fields of a hardening alloy (1-5) and cast-iron moulds (6-8).
- Figure 4. A sample for electrochemical testing, fixed on a holder and coated with a mixture of bitumen and paraffin: 1 copper holder, 2 – PVC pipe, 3 – coating, 4 – test sample.
- Figure 5. Temperature variation in the solidifying alloys and cast-iron mould at their height at a mould temperature of 20°C (I), 160° C(II), 310°C (III): a, b – cooling and heating curves, respectively; c, d – the temperature fields in the solidifying alloy and the shape, respectively.
- Figure 6. Change in thickness (a) and mass (b) of metal under different cooling conditions. 1, 2, 3 – initial temperature of the mould, equal to 20, 160 and 310°C, respectively.
- Figure 7. Dependence of the cooling time of the casting in the mould t1, cooling the mould to the set temperature t2 and the total casting cycle tc from the initial temperature of the mould.
- Figure 8. Influence of the casting temperature on the change of zinc alloys CC by casting into nonmetallic (a) and metallic moulds (b).
- Figure 9. Microstructure of the alloys of CP1 (I, II, III), CP2 (IV, V, VI) when casting into nonmetallic and metallic (VII, VIII, IX) moulds at the following casting temperatures: I, IV, VII – 450°C; II, V, VII – 500°C; III, VI, IX – 550°C (×100).
- Figure 10. Change in CC and microstructure of ZSA1 (a) and ZSA2 (b) alloys, depending on the rate of solidification.
- Figure 11. Construction of a mould for the production of zinc treads (sacrificial anodes).
- Figure 12. Changing the temperature of the cast tread when casting into a water-cooled mould.
7. Conclusion:
Summary of key findings:
- Different cooling conditions significantly affect the electrochemical properties of cast zinc sacrificial anodes.
- Directional solidification is best achieved with a mould temperature not exceeding 160°C.
- Maintaining a constant mould temperature before pouring is crucial for consistent casting quality.
- Water-cooled moulds with a directed heat sink offer improved control over solidification and product quality.
- The use of shaking open cast iron moulds reduced the complexity of the casting process.
8. References:
- [1] D.M. Stefanescu, Science and Engineering of Casting Solidification, 3rd ed., 2015, Springer International Publishing AG, Switzerland, p. 559.
- [2] J. Dantzig and M. Rappaz, Solidification, 2009, Taylor & Francis Group, CRS Press, p. 621.
- [3] J. Campbell, Casting, 2nd ed., 2003, Butterworth-Heinemann, Elsevier, p. 335.
- [4] F.S. Yang and F. Ni, Effect of Cooling Rate on the Solidification of Zn-5wt%Al Alloy, Adv. Mater. Res., 2012, 366, 502-505.
- [5] M. Krupiński, B. Krupińska, K. Labisz, Z. Rdzawski and W. Borek, Influence of cooling rate on crystallization kinetics on microstructure of cast zinc alloys, J. Therm. Anal. Calorim., 2014, 118, no. 2, 1361–1367.
- [6] R.-N. Ma, Y.-Z. Fan, A. Du and P.-P. Zhang, Effect of cooling rate on morphology and corrosion resistance of Zn-Al-Mg alloy, Cailiao Rechuli Xuebao/Transactions of Materials and Heat Treatment, 2015, 36, no. 4, 49–55.
- [7] V.A. Kechin and E.Y. Lyublinski, New Sacrificial Anodic Alloys, NACE International, 2018, Phoenix, USA, Paper C2018–11388.
- [8] C. Jennings, A comparison of the structure and Consumption Rate for Centrifugally Cast Anodes Compared with Die-Cast Anodes, NACE International, 2018, Phoenix, USA, Paper C2018–10954.
- [9] E. Lyublinski and V. Kechin, Formation of basic properties of galvanic anodes during the industrial production, EUROCORR 2017, Prague, Czhech Republic, Paper 72701.
- [10] A. Aghajani, M. Atapour and R. Alibek, Passivation of Zinc Anodes in Marine Conditions, Mater. Perform., 2016, 55, no. 9, 34.
- [11] V. Kechin and E. Lyublinski, New Sacrificial Anodic Alloys, EUROCORR 2016, Montpellier, France, Paper 0-6242.
- [12] V.A. Kechin, Theory and Technology of Cast Sacrificial Materials, Vladimir State University, 2004, p. 181 (in Russian).
- [13] V.A. Kechin and E.Y. Lyublinski, Zinc Alloys, Moscow, Metallurgiya, 1986, p. 247 (in Russian).
- [14] V.A. Kechin and A.B.Kireev, Riser for the production of cast treads sacrificial anodes, RF Patent No. 2492020, 2013 (in Russian).
9. Copyright:
- This material is a paper by "V.A. Kechin, E.Y. Lyublinski, A.V.Kireev and E.S. Prusov": Based on "Improvement and stabilization of the electrochemical properties of zinc alloys during casting".
- Source of paper: doi: 10.17675/2305-6894-2019-8-1-7
This material was created to introduce the above paper, and unauthorized use for commercial purposes is prohibited. Copyright © 2025 CASTMAN. All rights reserved.