This introductory paper is the research content of the paper "Implementation Six Sigma and Data Mining to Improve Die Casting Production Process at PT. AB" published by Proceeding 7th International Seminar on Industrial Engineering and Management.
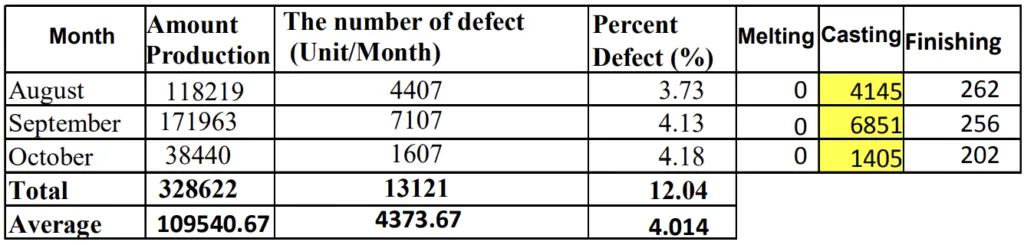
1. Overview:
- Title: Implementation Six Sigma and Data Mining to Improve Die Casting Production Process at PT. AB
- Author: Rina Fltriana, Johnson Saragih, Sitta Sarasaty
- Publication Year: 2013
- Published Journal/Society: Proceeding 7th International Seminar on Industrial Engineering and Management
- Keywords: Six Sigma, FMEA, Decision Tree.
2. Abstract
PT. AB is a motorcycle industry manufacturer where quality measurement is crucial. This research aims to improve quality control and reduce defect percentages in the die casting production process using the Six Sigma (DMAIC) method. The define phase identified the KYZ cylinder component as having the highest defect percentage (5.06% vs. a 3.36% limit). The measure phase calculated a DPMO value of 15,356 and a sigma level of 3.66. The analyze phase used cause and effect diagrams, Failure Mode and Effect Analysis (FMEA), and data mining (decision tree) to identify the dominant issue as flow line defects. The improvement stage involved operator training, Standard Operating Procedure (SOP) implementation, and QC PASS standardization using data mining. The control phase calculated post-implementation DPMO (13,221) and sigma level (3.71), showing an increase of 0.05 in sigma level.
3. Research Background:
Background of the research topic:
PT. AB, a motorcycle manufacturer in Indonesia, experiences high defect rates in its die casting production process, specifically with the KYZ cylinder component.
Status of previous research:
Six Sigma is a methodology for process improvement and variation reduction. (Pande,2002). Jang (2009) proposes data mining usage within Six Sigma. FMEA systematically identifies and evaluates potential failure. (Manggala, 2005). Data Mining is automatically discovering usefull infomation in large data. (Tan, 2006). Entropy and Gain Formula is introduce by (Kusrini, 2009).
Need for research:
High defect rates (16.8% actual vs. 3.36% standard) in the KYZ cylinder component production necessitate improvements to reduce rework, lower production costs, and enhance quality.
4. Research purpose and research question:
Research purpose:
To determine the sigma level of the company before and after implementing improvements and to propose improvements using data mining.
Core research:
To use Six Sigma and data mining techniques to improve quality and reduce defects in the die casting process of KYZ cylinder components at PT. AB.
5. Research methodology
The research employed the Six Sigma DMAIC methodology:
Research Design: The research followed the five phases of the DMAIC (Define, Measure, Analyze, Improve, Control) methodology.
Data Collection:
- Historical production data (August - October 2012, January - February 2013).
- Interviews with company personnel.
- Observation
Sample: 84,541 units of KYZ cylinder components from January to early February 2013.
Analysis Method:
- Define: Process identification, Voice of Customer, Project Charter, SIPOC diagram (Figure 4), and identification of Critical to Quality (CTQ) characteristics.
- Measure: Calculation of control maps p and u, DPMO, and sigma level.
- Analyze: Cause and effect diagrams (Figure 5), FMEA (Table 4), and data mining (decision tree with WEKA software, proposal in Figure 6).
- Improve Proposal by using 5W 1H Method, and Decisiton Tree In data mining.
- Improve: Operator training, SOP development, QC PASS standardization based on data mining results.
- Control: Recalculation of control maps p and u, DPMO, and sigma level after implementation.
Research Scope: The study focused on the die casting production process of KYZ cylinder components at PT. AB, specifically the casting process identified.
6. Key research results:
Key research results and presented data analysis:
- The highest percentage of defects in the KYZ cylinder component production occurred in the casting process (Table 1).
- The initial sigma level was 3.66, with a DPMO of 15,356.7 (Table 3).
- The most dominant defect type was "flow line" (Figure 5).
- FMEA analysis identified key failure modes and their causes within the flow line defect. (Table 4)
- Data mining using a decision tree (Figure 6) provided rules for QC PASS standardization.
- Post-implementation, the DPMO decreased to 13,221, and the sigma level increased to 3.71.
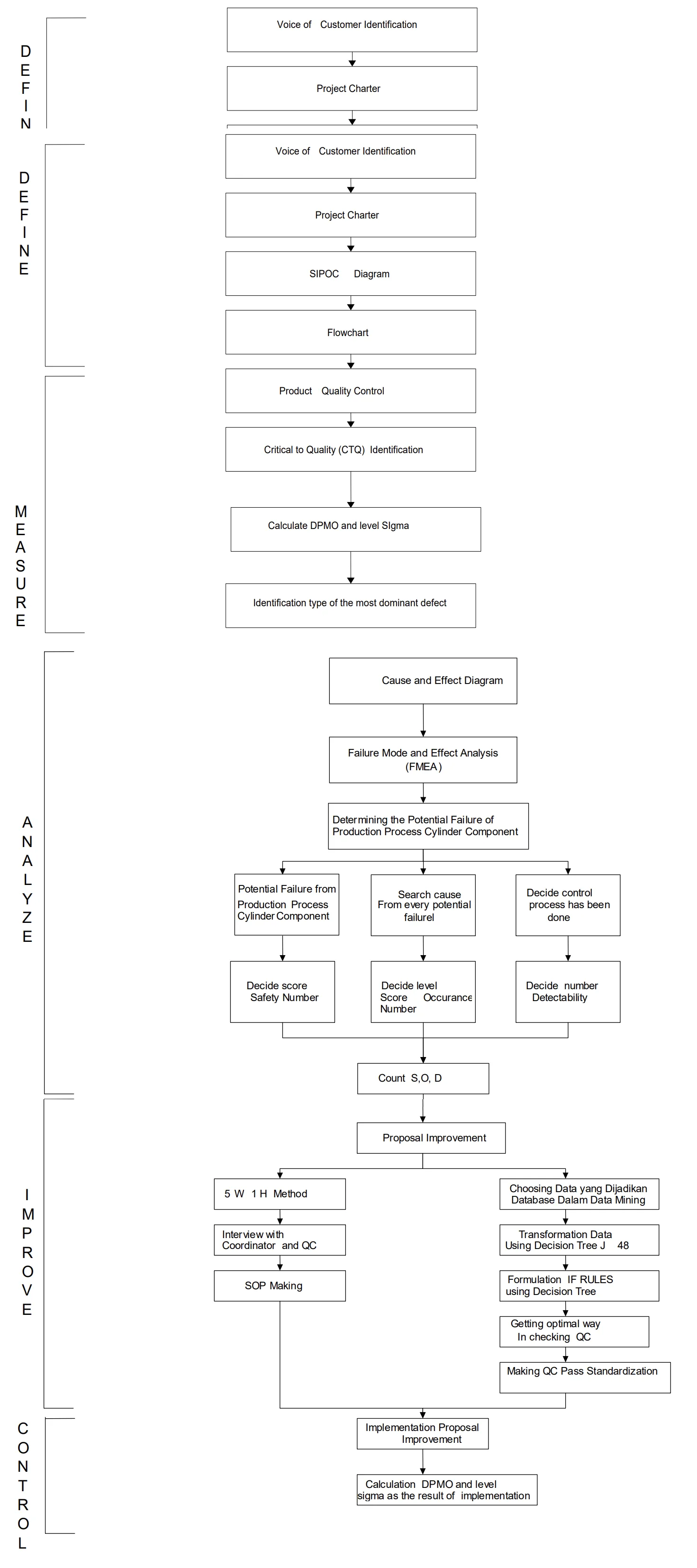
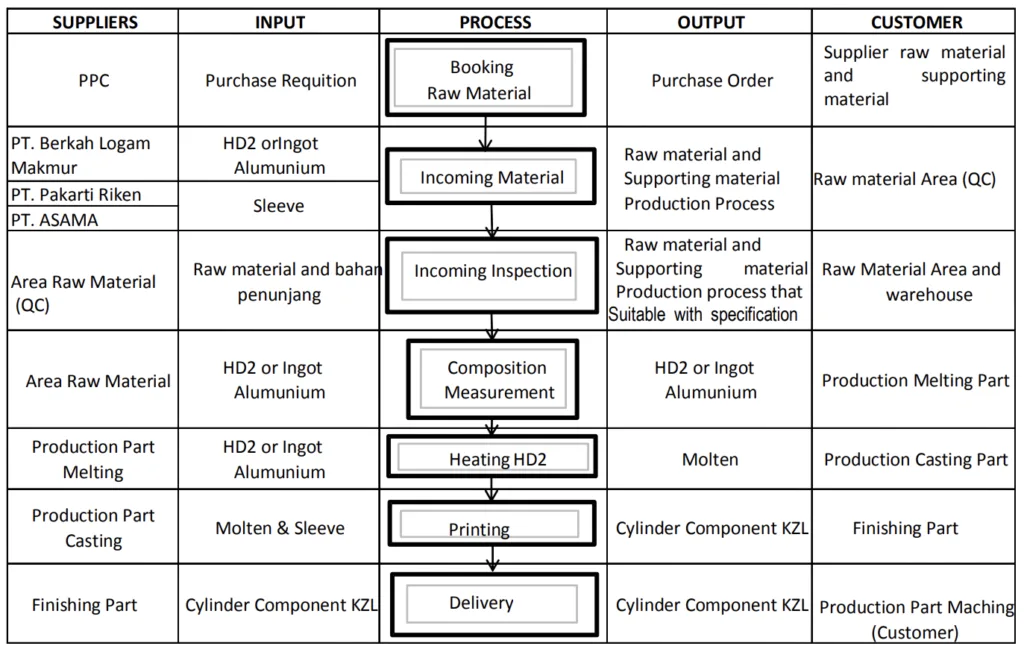
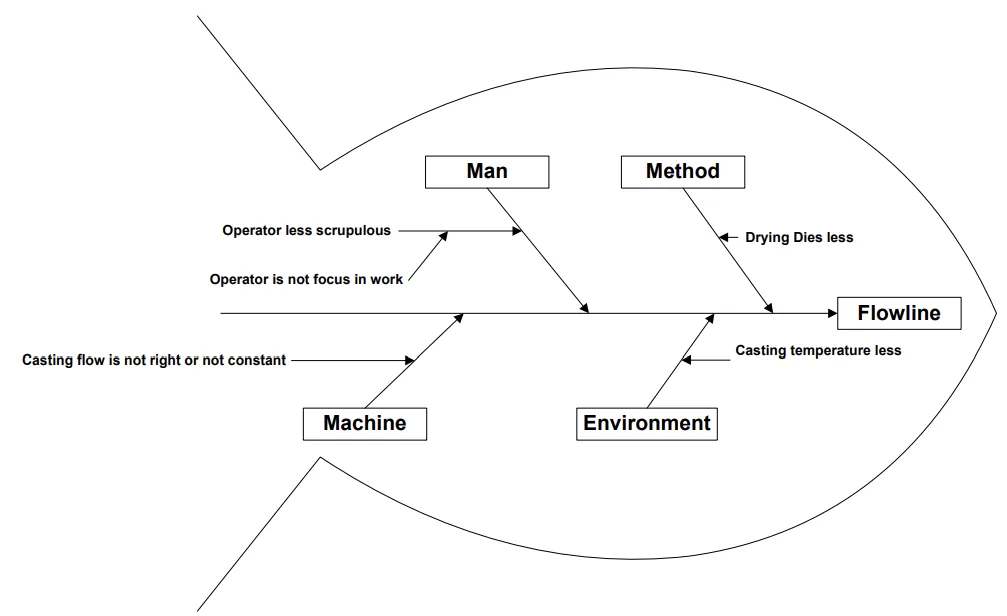
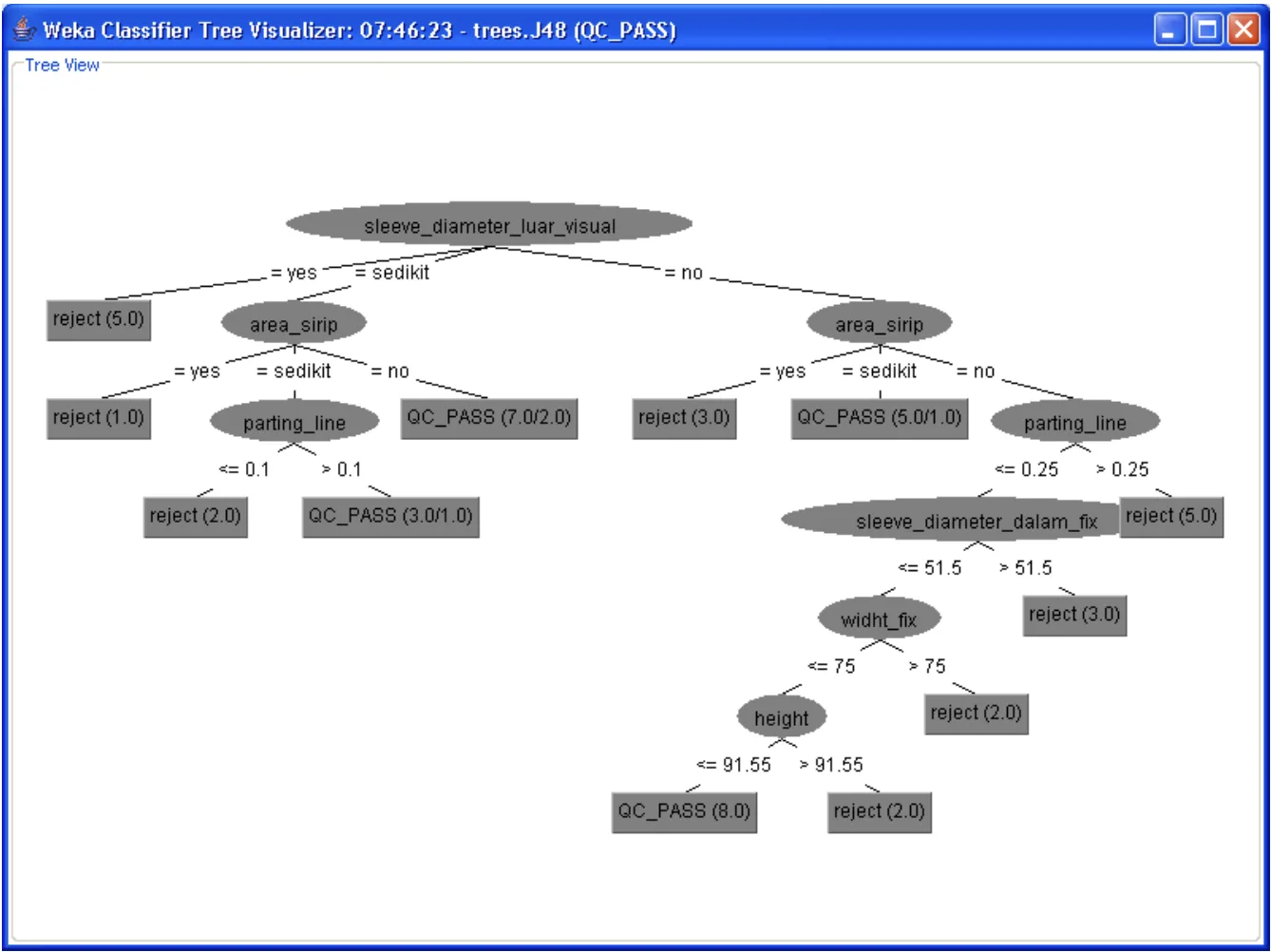
List of figure names:
- Figure 3. Project Charter Declaration Produk Cylinder Component KYZ
- Figure 4. Diagram SIPOC (Supplier – Input – Process – Output - Customer) Produk Cylinder
Component KYZ - Figure 5. Cause-effect Diagram Flowline Defect
- Figure 6. Proposal Decision Tree In WEKA Software
7. Conclusion:
Summary of key findings:
The research successfully applied Six Sigma and data mining to identify and address the root causes of defects in the die casting process. The implementation of proposed improvements, including operator training, SOPs, and data mining-based QC PASS standardization, led to a reduction in DPMO and an increase in the sigma level.
Possible areas for future expansion research:
The document does not specify any future research.
8. References:
- (a) Gaspersz, Vincent. 2002. Pedoman Implementasi Program Six Sigma. Jakarta: PT. Gramedia Pustaka Utama.
- (b) Manggala, D. 2005. Menerapkan Konsep Lean dan Six Sigma di Sektor Publik. IPOMS Newsletter, Vol 1/1/4-5 Agustus 2005.
- (c) Jang Gill-Sang, Jeon Jong-Hag. 2009. A Six Sigma Methodology Using Data Mining: A Case Study on Six Sigma Project for Heat Efficiency Improvement of Hot Stove System in Korean Steel Manufacturing Company. Springer-Verlag Berlin Heidelberg.
- (d) Pande, Peter S., dkk. 2002. The Six Sigma Way. Yogyakarta: Andi.
- (e) Kusrini, Emha TL. 2009. Algoritma Data Mining. Yogyakarta:Andi.
- (f) Tan, Steinbach Kumar. 2006. Introduction to Data Mining. Pearson Education,Inc. Addison Wesley
9. Copyright:
- This material is a paper by "Rina Fitriana": Based on "Implementation Six Sigma and Data Mining to Improve Die Casting Production Process at PT. AB".
- Source of paper: ISSN: 1978-774X, Proceeding 7th International Seminar on Industrial Engineering and Management
This material was created to introduce the above paper, and unauthorized use for commercial purposes is prohibited. Copyright © 2025 CASTMAN. All rights reserved.