This article introduces the paper ["Evaluation of Soldering on Surface-Treated Specimens with both Actual Die Casting and Dipping Test into Molten Al Alloy"] published by [電気製鋼 (The Iron and Steel Institute of Japan)].
1. Overview:
- Title: Evaluation of Soldering on Surface-Treated Specimens with both Actual Die Casting and Dipping Test into Molten Al Alloy
- Author: Masamichi KAWANO
- Publication Year: 2021
- Publishing Journal/Academic Society: 電気製鋼, Vol.92, No.2, pp.87-92
- Keywords: Soldering behavior, surface coating, die casting, dipping tests, core-pins, round bar specimens, carbo-nitriding, PVD process, lubricants, water-based emulsion type, oiliness type, salt bath nitriding
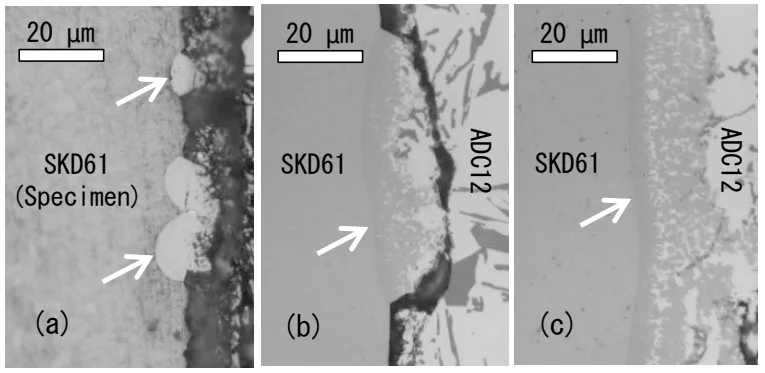
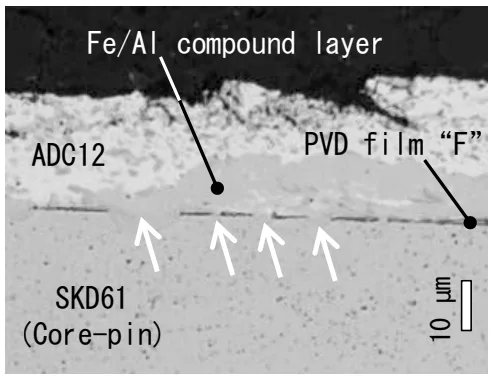
2. Abstracts or Introduction
This paper investigates the soldering behavior of surface coatings in both die casting and dipping tests. Core-pins and round bar specimens, surface-treated with carbo-nitriding or PVD processes, were evaluated. In die casting experiments, molten Al alloy at 735 °C was injected at a velocity of 54 m/s towards core-pins. Water-based emulsion and oiliness type lubricants were employed. The maximum temperature 1 mm below the core-pin surface reached 475 °C, with water-based emulsion lubricant yielding a lower temperature. Soldering on core-pins after 18 die casting shots was consistent regardless of surface coating or lubricant, and no Fe/Al compound layer was detected at the soldering interface. In dipping tests, round bar specimens were immersed in molten Al alloy at 750 °C for 30 seconds. Salt bath nitriding demonstrated superior anti-soldering performance compared to PVD. The study concludes that soldering behavior in die casting and dipping tests does not necessarily correlate.
The introduction of the paper highlights that soldering in die casting, defined as the adhesion of aluminum alloy (Al alloy) to the die, is a critical issue. Soldering on die cast products leads to surface roughness, dimensional inaccuracy, and in severe cases, makes product removal from the die impossible. Therefore, preventing soldering is essential for maintaining die casting quality and stable operation. Effective countermeasures include: (1) reducing die surface temperature and (2) preventing direct contact between the die material and the Al alloy. Method (1) involves optimizing internal cooling (内冷), including securing water flow rate through water quality management, high-pressure water jetting, and complex cooling channel designs using additive manufacturing. Method (2) includes applying release agent coatings (離型剤被膜) and surface treatments to form hard films of oxides or nitrides. Dipping tests in molten Al alloy (溶湯浸漬) are commonly used to evaluate soldering resistance by visually assessing the amount of adhered Al alloy. This cost-effective method is crucial for screening and developing surface treatments for die casting applications. This paper aims to compare the ranking of soldering resistance among different surface treatments in die casting and dipping tests, and to examine the influence of molten metal flow (湯流れ) and pressure on soldering, alongside the effect of die temperature variations due to different release agent types.
3. Research Background:
Background of the Research Topic:
Soldering in die casting is described as the phenomenon where aluminum alloy (Al alloy) adheres to the die. This adhesion results in defects on cast products, including rough surfaces and dimensional inaccuracies. In severe cases, extensive soldering can prevent the removal of castings from the die. Therefore, preventing soldering is paramount for maintaining the quality of die cast products and ensuring stable die casting operations.
Status of Existing Research:
Existing strategies to mitigate soldering are categorized into two main approaches: (1) lowering the die surface temperature and (2) preventing direct contact between the die material and the molten Al alloy. Approach (1) involves optimizing internal cooling (内冷), which includes techniques such as ensuring adequate coolant flow through water quality management, employing high-pressure water ejection, and utilizing complex cooling circuits fabricated by additive manufacturing. Approach (2) focuses on applying release agent coatings (離型剤被膜) and surface treatments that create hard films composed of oxides or nitrides on the die surface. Dipping tests in molten Al alloy (溶湯浸漬) are widely employed to assess the soldering resistance of surface treatments. The degree of soldering resistance is readily evaluated by visually inspecting the amount of Al alloy adhering to the test specimen. Dipping tests serve as an efficient and cost-effective screening method for selecting surface treatments for die casting applications.
Necessity of the Research:
While dipping tests are valuable for screening surface treatments, the correlation between the soldering behavior observed in dipping tests and actual die casting processes is not fully understood. This study aims to bridge this gap by comparing the ranking of soldering resistance for various surface treatments under both die casting and dipping test conditions. Furthermore, the research investigates the influence of molten metal flow (湯流れ) and pressure, inherent to the die casting process, on soldering behavior. It also examines how different types of release agents affect die temperature and consequently, soldering.
4. Research Purpose and Research Questions:
Research Purpose:
The primary purpose of this research is to compare the soldering resistance ranking of different surface treatments when evaluated using both die casting and dipping tests. Additionally, the study aims to elucidate the effects of molten metal flow (湯流れ) and pressure on soldering phenomena within the die casting process. The influence of release agent type on die temperature and its subsequent impact on soldering behavior are also investigated.
Key Research:
- To compare the soldering resistance ranking of surface treatments between die casting and dipping tests.
- To investigate the influence of molten metal flow and pressure on soldering in die casting.
- To examine the effect of release agent type and resulting die temperature variations on soldering.
5. Research Methodology
Research Design:
This research employed a comparative experimental design, utilizing both actual die casting and dipping tests to evaluate the soldering behavior of surface-treated specimens.
Data Collection Method:
- Die Casting Test: Die casting experiments were conducted using a 135-ton die casting machine manufactured by Shibaura Machine Co., Ltd. Casting conditions are detailed in Table 1. Molten ADC12 alloy at 735 °C was injected to directly impinge upon core-pins located 20 mm from the gate. These core-pins served as specimens for soldering evaluation. Temperature measurements were taken using thermocouples embedded 1 mm below the surface of integrated core-pins (一体ピン). Two types of commercially available die release agents were used: oiliness type "R" and water-based emulsion type "M".
- Dipping Test: For dipping tests, round bar specimens (Ø10 mm x 60 mm) made of SKD61 steel with the same surface treatments as the core-pins were used. Specimens were immersed in molten ADC12 alloy at 750 °C for 30 seconds without prior application of release agent. After 30 seconds, specimens were withdrawn and air-cooled to room temperature.
Analysis Method:
Soldering behavior was assessed primarily through visual inspection and photographic documentation of the specimens after both die casting and dipping tests. In the dipping test, soldering was determined by whether the adhered ADC12 alloy could be easily removed by rubbing or remained firmly attached. Microscopic observation of cross-sections of soldered parts was conducted to analyze the soldering interface and coating film conditions. Temperature data from the die casting experiments were analyzed to evaluate the effect of release agent type on core-pin temperature.
Research Subjects and Scope:
The research focused on evaluating four surface treatments applied to SKD61 die steel (46HRC): three types of PVD (Physical Vapor Deposition) coatings (identified as "A", "B", and "C") and one salt bath nitriding treatment ("D"). Non-treated SKD61 was also used as a baseline. The molten alloy used was ADC12. Die casting experiments utilized both oiliness type "R" and water-based emulsion type "M" release agents.
6. Main Research Results:
Key Research Results:
- Die Casting Tests: After 18 shots of die casting, soldering occurred on core-pins regardless of the surface treatment or release agent used. Visual inspection and cross-sectional analysis (Fig. 7, Fig. 8) revealed that the surface treatment films were not lost in the soldered areas, and no Fe/Al compound layer formation was observed. The ADC12 alloy appeared to be physically attached to the surface treatment film. The water-based emulsion lubricant "M" resulted in lower core-pin temperatures compared to the oiliness type lubricant "R" (Fig. 4, Fig. 5, Fig. 6).
- Dipping Tests: In dipping tests, salt bath nitriding ("D") demonstrated superior anti-soldering performance compared to the PVD coatings (Fig. 10). The ranking of soldering resistance among the surface treatments differed significantly between the dipping tests and the die casting tests.
- Temperature Measurement: Measurements of core-pin temperature during die casting showed that the water-based release agent "M" was more effective in reducing core-pin temperature than the oiliness type "R" (Fig. 5, Fig. 6).
Analysis of presented data:
- Figure 4: Shows the transient temperature at 1 mm below the surface of a non-coated core-pin during die casting. It illustrates the temperature difference between using oiliness type lubricant "R" and water-based emulsion lubricant "M", both with and without inner cooling.
- Figure 5 & 6: Present the minimum and maximum temperatures of non-coated core-pins in relation to the molten ADC12 temperature and lubricant type. These figures demonstrate the temperature-reducing effect of water-based lubricant "M" and inner cooling.
- Figure 7: Displays the appearance of coated core-pins after 18 die casting shots. It visually shows that soldering occurred across all surface treatments and lubricant conditions.
- Figure 8: Shows a cross-sectional view of a soldered part after 18 die casting shots. It confirms the absence of an Fe/Al compound layer and indicates that the ADC12 is physically attached to the surface treatment film.
- Figure 9: Compares the coating film of nitriding "D" and PVD coating "B" before and after die casting with lubricant "R". It reveals a reduction in the thickness of the oxide film on the nitriding layer after 18 shots, suggesting erosion due to molten metal flow.
- Figure 10: Illustrates the appearance of coated round bar specimens after dipping in molten ADC12. It shows variations in the amount of soldering depending on the surface treatment, with nitriding "D" exhibiting the least soldering.
Figure Name List:
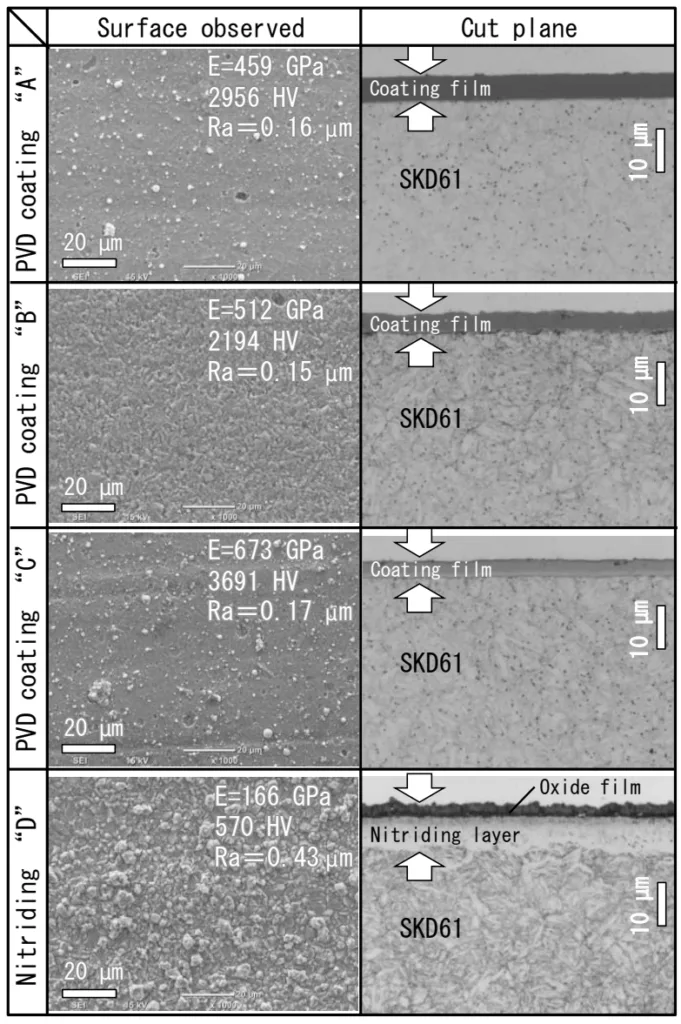
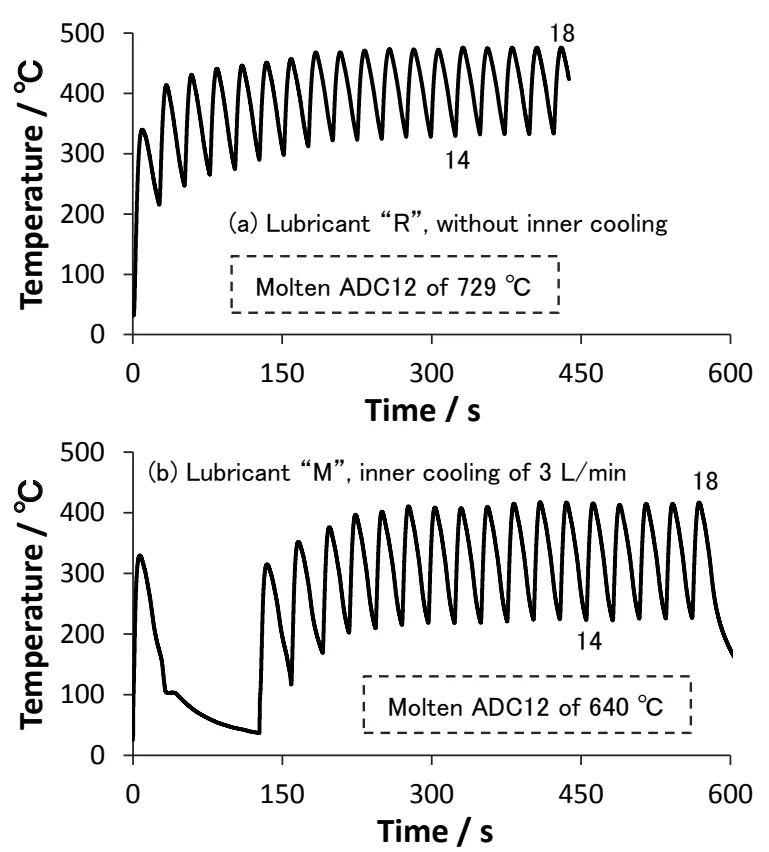
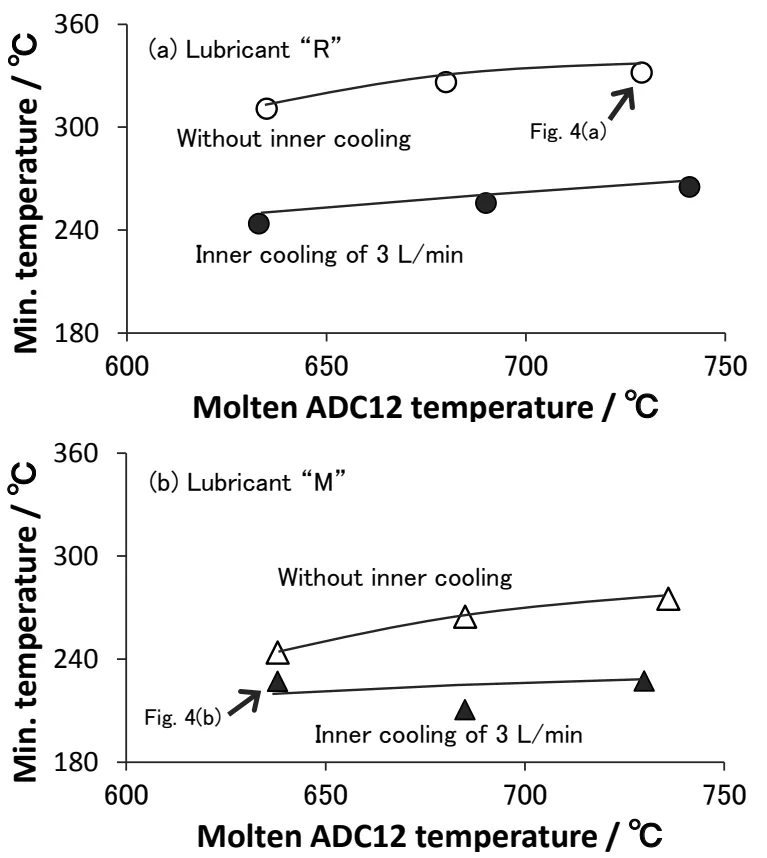
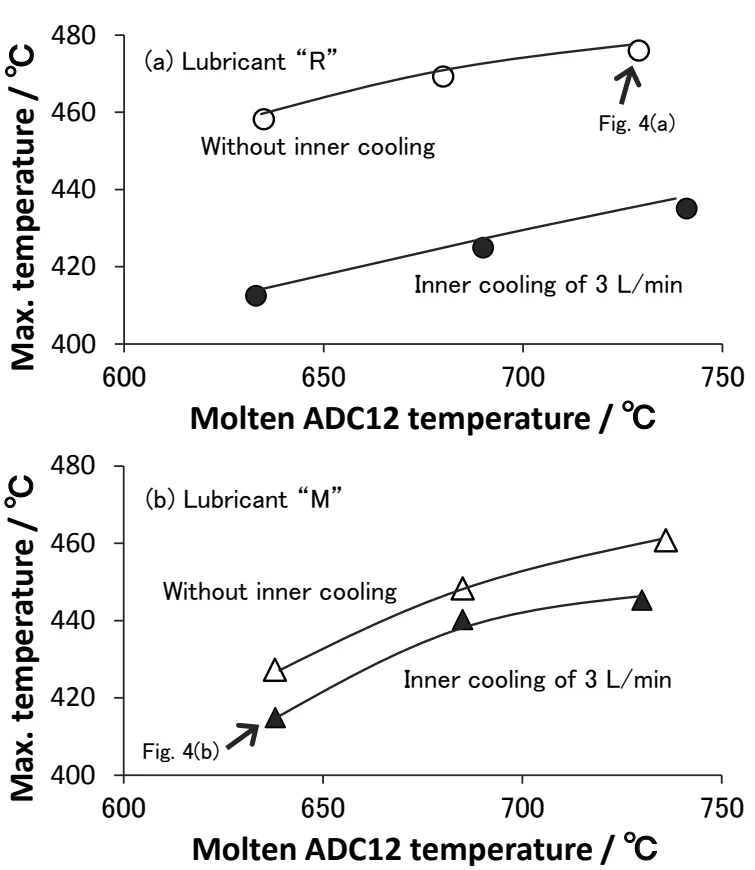
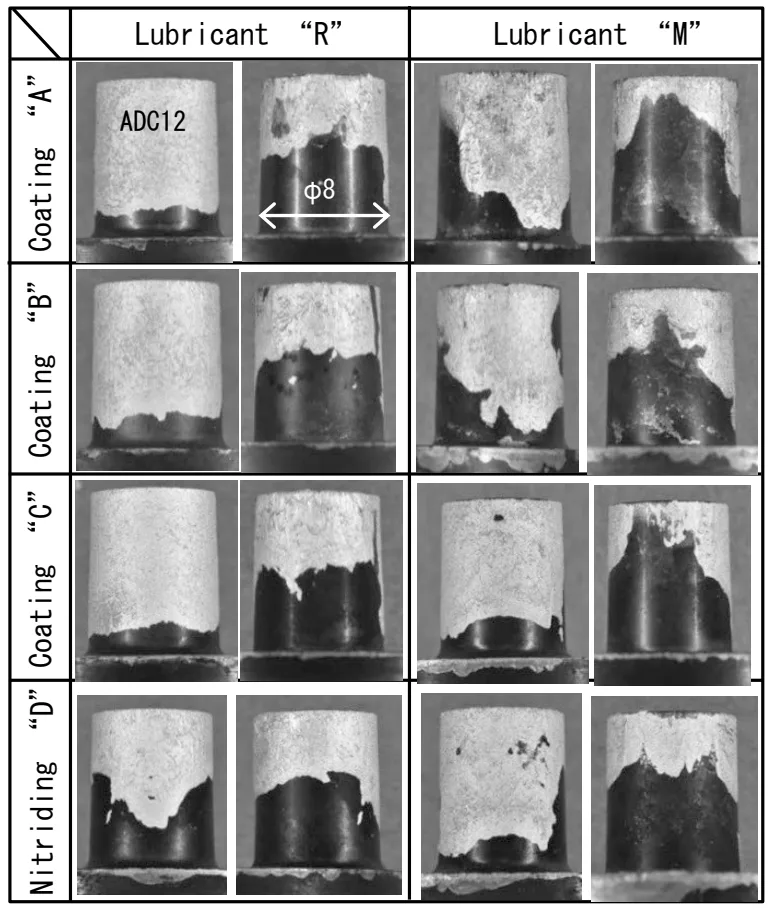
- Fig. 1. Initiation of soldering observed on dipping test into molten ADC12.
- Fig. 2. Soldering observed on die-cast after 2000 shots.
- Fig. 3. Four surface treatments for SKD61 of 46HRC.
- Fig. 4. Temperature transient at 1 mm below surface of non-coated core-pin.
- Fig. 5. The minimum temperature of non-coated core-pin related to Fig. 4.
- Fig. 6. The maximum temperature of non-coated core-pin related to Fig. 4.
- Fig. 7. Appearance of coated core-pins after 18 shots.
- Fig. 8. Observation of cut plane at soldered part after 18 shots.
- Fig. 9. Comparison of coating film between before and after casting with lubricant "R".
- Fig. 10. Appearance of coated round bar specimens after dipping into molten ADC12.
7. Conclusion:
Summary of Key Findings:
The study revealed that the ranking of soldering resistance for surface treatments differs between die casting and dipping tests. In die casting, significant soldering occurred regardless of the surface treatment or release agent type after 18 shots. Water-based emulsion lubricant effectively lowered core-pin temperatures. Conversely, in dipping tests, salt bath nitriding exhibited superior anti-soldering performance compared to PVD coatings. The discrepancy in soldering behavior between the two test methods is attributed to the differences in molten metal flow velocity and pressure.
Academic Significance of the Study:
This research clarifies the distinction in soldering evaluation between die casting and dipping tests, emphasizing the critical role of process conditions, particularly molten metal flow and pressure, in soldering phenomena. It highlights that dipping tests alone may not fully represent the complex soldering mechanisms occurring in actual die casting environments.
Practical Implications:
The findings suggest that dipping test results should be interpreted cautiously when predicting the soldering performance of surface treatments in actual die casting applications. Factors specific to die casting, such as molten metal flow and pressure, must be considered in surface treatment selection. The study also confirms the effectiveness of water-based lubricants in reducing die component temperatures, which can be beneficial in mitigating soldering.
Limitations of the Study and Areas for Future Research:
This study focused on a limited set of surface treatments and specific die casting conditions. Further research is recommended to investigate a broader range of surface treatments and die casting parameters, including varying injection velocities and pressures. Quantifying the individual contributions of flow velocity and pressure to soldering, and exploring the soldering behavior over extended die casting cycles, are also suggested areas for future research.
8. References:
- 1) 向川博, 樋口博, 小野英敏, 金子博志: 2004日本ダイカスト会議論文集,(2004), 25.
- 2) 古川雄一, 佐藤理通, 古倉冬彦, 植林秀悟: 2004日本ダイカスト会議論文集, (2004), 63.
- 3) 井戸信介: 型技術, 28(2013), 3, 30.
- 4) 野村康弘, 深見尚男, 小林竜之, 早藤哲典: 2016日本ダイカスト会議論文集,(2016), 35.
- 5) 木村有貴, 佐藤良輔, 鈴木将宏, 植田真広, 井川秀昭, 工藤英弘: 豊田自動織機技報, 70(2019), 83.
- 6) 前原一仁, 早藤哲典, 小林竜之: 2018日本ダイカスト会議論文集,(2018),75.
- 7) 河田一喜, 木立徹: 2016日本ダイカスト会議論文集, (2016), 7.
- 8) 石塚はる菜, 高村宏, 渡邊陽一: 2018日本ダイカスト会議論文集,(2018),11.
- 9) 横井直樹, 河野正道, 保母誠: 型技術者会議 2011 講演論文集,(2011), 202.
- 10) 河野正道, 宇野聡, 横井直樹: 2016日本ダイカスト会議論文集,(2016), 53.
- 11) 佐々木英人: 素形材, 51(2010), 10, 29.
- 12) (株)青木科学研究所「ダイカスト用原液塗布型油性離型 WFR series」(http://www.lubrolene.co.jp/industrials/wfr.html)
9. Copyright:
- This material is "Masamichi KAWANO"'s paper: Based on "Evaluation of Soldering on Surface-Treated Specimens with both Actual Die Casting and Dipping Test into Molten Al Alloy".
- Paper Source: 電気製鋼, Vol.92, No.2, pp.87-92, 2021.
This material was created to introduce the above paper, and unauthorized use for commercial purposes is prohibited.
Copyright © 2025 CASTMAN. All rights reserved.