This article introduces the paper 'Development of Copper MIM Powders for Thermal Management Applications' published by 'Not explicitly stated in the paper'.
1. Overview:
- Title: Development of Copper MIM Powders for Thermal Management Applications
- Author: R. Zauner, R. Nagel, E. Neubauer, K. Portschy, P.A Davies, M.A.Kearns
- Publication Year: Not explicitly stated in the paper
- Publishing Journal/Academic Society: Not explicitly stated in the paper
- Keywords: Metal Injection Moulding, Copper MIM powders, Thermal Management Applications, Heat sinks, Fine copper powders, Net-shape forming
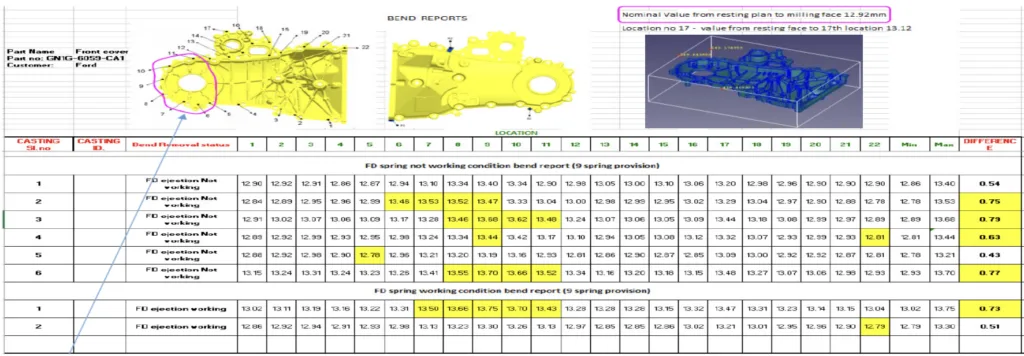
2. Abstracts or Introduction
Abstract
Metal Injection Moulding is continuing to see strong growth in the variety and volume of parts and
materials in use. We report here the development and application of fine copper powders for MIM
of heat sinks for thermal management applications. This is an important field for development in
view of the increasing need for cooling of compact electronic devices and the need to use cost
effective net-shape forming methods for expensive materials. Sandvik Osprey Ltd. has produced
fine, low oxygen powders (90% -22µm and 90% -31µm) which have been incorporated into MIM
feedstock at ARC Seibersdorf. The properties of the finished components are presented and the
potential for applications in thermal management is discussed.
INTRODUCTION
Copper is a particularly suitable material for thermal management applications due to its high
thermal conductivity and relatively high sintering activity. In combination with a net-shape process
like MIM, complex heat sink components with optimized thermal features can be manufactured
[1,2]. Composite structures integrating porous elements for heat pipes are also in development.
3. Research Background:
Background of the Research Topic:
The increasing demand for efficient cooling solutions in compact electronic devices necessitates the development of advanced thermal management materials and cost-effective net-shape forming techniques for processing expensive materials. Copper is identified as a particularly suitable material for thermal management applications due to its inherent high thermal conductivity and favorable sintering characteristics. Metal Injection Moulding (MIM) emerges as a promising net-shape process capable of producing complex heat sink components with optimized thermal features.
Status of Existing Research:
Prior research, notably by Johnson & Lye-King Tan [2], has explored the fabrication of copper MIM parts using various copper powder feedstocks produced through different methods. These studies have underscored the critical influence of porosity and impurities on the thermal conductivity of sintered components. Reported sintered densities ranged from 93% to 96%, with corresponding thermal conductivities spanning 280-385 W/mK. The upper end of these values approaches the performance of wrought copper, highlighting the potential of MIM for cost-effective manufacturing of high-performance copper components.
Necessity of the Research:
The limitations of conventional manufacturing processes, such as aluminium high pressure die-casting, and the inherent material properties necessitate the exploration of improved thermal management strategies. Specifically, the original aluminium heat sink design was only capable of managing the heat dissipation of a single 1.25W power LED. The increasing trend towards higher power density and the requirement to accommodate multiple power LEDs in confined spaces demand the development of enhanced thermal management solutions. This research addresses this need by investigating copper MIM as a viable alternative for producing high-performance heat sinks.
4. Research Purpose and Research Questions:
Research Purpose:
The primary objective of this research is to investigate the development and application of fine copper powders for Metal Injection Moulding (MIM) in the fabrication of heat sinks designed for thermal management applications. The study aims to evaluate the properties of MIM-processed copper components and assess their potential for use in thermal management, particularly in demanding applications such as LED cooling.
Key Research:
This study focuses on:
- Manufacturing a heat sink component utilizing MIM technology with fine copper powders.
- Evaluating the thermal performance of the manufactured heat sink against predefined design targets.
- Investigating the influence of different copper powder feedstocks, specifically powders with particle sizes of <31 µm and <22 µm, on the resulting thermal properties of MIM-processed components.
Research Hypotheses:
The research operates under the premise that Metal Injection Moulding of copper powder can achieve a thermal conductivity of approximately 380 W/mK, a value comparable to wrought copper and significantly higher than aluminium die-cast components. This study aims to validate this assumption through experimental investigation and thermophysical characterization of MIM copper parts.
5. Research Methodology
Research Design:
This research employs an experimental design encompassing material development, feedstock preparation, component fabrication via Metal Injection Moulding (MIM), and comprehensive thermophysical characterization. Two distinct copper powders with varying particle size distributions were utilized to fabricate test specimens and a representative heat sink component.
Data Collection Method:
The following data collection methods were employed:
- Particle Size Distribution: Measured using a Malvern Mastersizer to characterize the d10, d50, and d90 values of the copper powders.
- Oxygen Level: Measured for each powder batch to ensure minimal oxygen content.
- Pycnometric Density: Evaluated using a Quantachrome pycnometer for fresh powders, treated powders, and MIM feedstocks.
- Thermal Diffusivity: Measured using a laser flash method as a function of temperature.
- Specific Heat: Measured using Dynamic Scanning Calorimetry (DSC) as a function of temperature.
- Coefficient of Thermal Expansion (CTE): Measured using a dilatometer as a function of temperature.
Analysis Method:
The collected data was analyzed using the following methods:
- Comparison of Powder Properties: Particle size distribution and density of the two different copper powders were compared.
- Thermal Conductivity Calculation: Thermal conductivity was calculated from measured thermal diffusivity, specific heat, and density data using the relationship: λ(T) = a(T)· ρ(T)· cp (T).
- Graphical Analysis: Thermal diffusivity, specific heat, CTE, and thermal conductivity data were plotted as a function of temperature for both powder types and compared against literature values for pure copper.
- Performance Comparison: The thermal performance of the MIM copper heat sink was compared to the original aluminium die-cast heat sink design in terms of heat dissipation capability.
Research Subjects and Scope:
The research focused on:
- Materials: Two fine copper powders supplied by Sandvik Osprey Ltd., classified as 90% <31 µm and 90% <22 µm, produced from High Conductivity (HC) copper via gas atomization.
- Feedstock: Proprietary wax-polymer binder system and optimized powder loading of 60 vol% were used for MIM feedstock preparation at ARC Seibersdorf.
- Component: A heat sink for an automotive thermal management application designed for LED cooling was selected as the demonstrator component.
- Fabrication: Component fabrication was performed using an Arburg 320 C injection moulding machine and a combined debinding and sintering furnace under hydrogen atmosphere at a maximum temperature of 1030°C.
6. Main Research Results:
Key Research Results:
- Powder Characterization: Sandvik Osprey Ltd. produced fine copper powders with low oxygen content. Particle size distributions are shown in Table 1.
Table 1. Particle size distribution and powder density of starting materials.
Product | D10 μm | D50 μm | D90 μm |
---|---|---|---|
90% <31 μm | 6.0 | 14.5 | 30.5 |
90% <22 μm | 4.9 | 10.6 | 21.8 |
- Sintered Density: Achieved sintered densities were 96.5% for the 22 µm powder and 95.5% for the 31 µm powder.
- Thermal Conductivity: Derived thermal conductivity values for both powder materials were approximately 380 W/mK, as shown in Figure 9.
Figure 9. Thermal diffusivity and derived thermal conductivity of sintered parts made from 22 µm and 31 µm copper powder compared to literature values of pure copper.
[Figure 9 is inserted here]
- Heat Dissipation Performance: The MIM copper heat sink design demonstrated a four-fold increase in heat dissipation capability (5.00W for 4 LEDs) compared to the original aluminium design (1.25W for 1 LED), as illustrated in Figure 7.
Figure 7. Old and new design for LED heat sink
[Figure 7 is inserted here]
Analysis of presented data:
The data presented in Figure 9 indicates that both copper powder materials exhibit similar thermal behavior in terms of thermal diffusivity and derived thermal conductivity across the temperature range tested. Despite a slight difference in porosity (1% higher for the 31 µm powder), the thermal conductivity values are comparable, suggesting that particle size within this range has a secondary influence compared to other factors like grain boundaries. Figure 8 shows the specific heat and CTE values for both powder sizes are also similar and consistent with literature values for pure copper, although CTE shows some deviation at higher temperatures for the 31µm powder, potentially due to porosity. The comparison in Figure 7 highlights the significant improvement in heat dissipation achieved by switching from aluminium to copper MIM and optimizing the heat sink design.
Figure Name List:
- Figure 1. LED heat sink for thermal management
- Figure 2. Injection moulding machine used for component fabrication at ARC Seibersdorf research GmbH
- Figure 3. Mould frame with mould inserts
- Figure 4. Injection moulded LED heat sinks
- Figure 5. Combined debinding and sintering furnace for maximum temperatures of 1100°C
- Figure 6. Sintered component: dimensions 56 mm x 48 mm x 32 mm (height)
- Figure 7. Old and new design for LED heat sink
- Figure 8. Specific heat and CTE as a function of temperature for sintered parts made of 22 µm and 31 µm copper powder compared to literature values of pure copper.
- Figure 9. Thermal diffusivity and derived thermal conductivity of sintered parts made from 22 µm and 31 µm copper powder compared to literature values of pure copper.
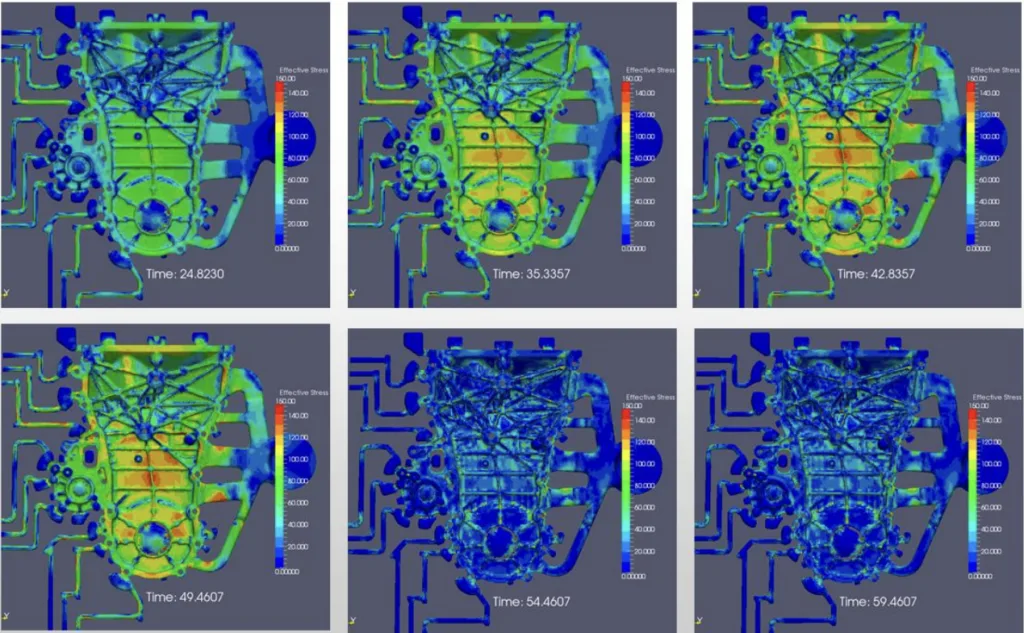
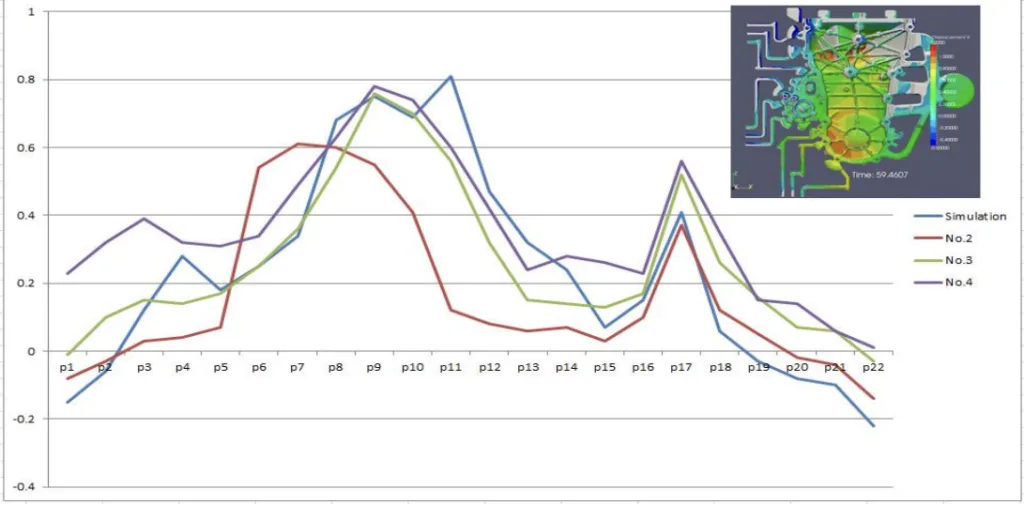
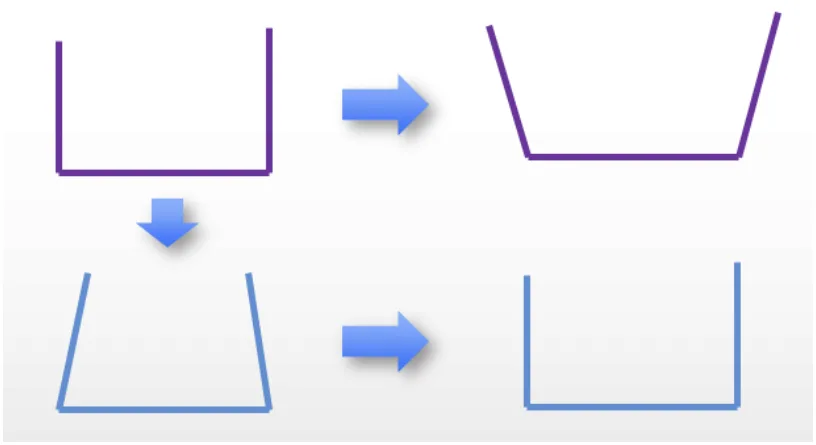
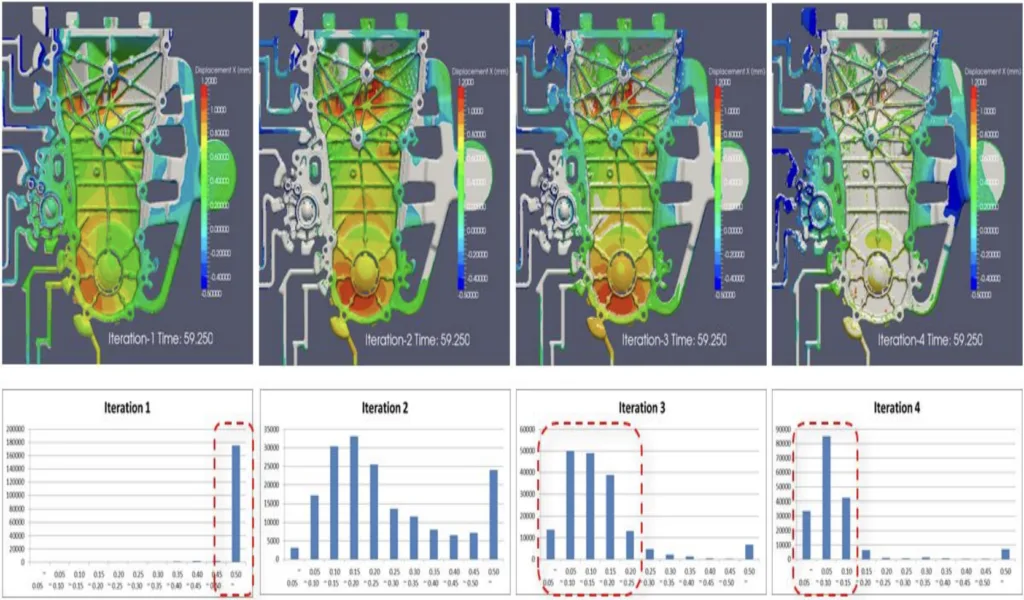
7. Conclusion:
Summary of Key Findings:
This study successfully demonstrated the suitability of fine copper powders for Metal Injection Moulding (MIM) of high-performance thermal management components. The fabricated copper MIM heat sink achieved a four-fold increase in heat dissipation compared to a conventional aluminium die-cast solution. Both copper powder sizes (90% <22 µm and 90% <31 µm) resulted in comparable thermal properties, with sintered thermal conductivity reaching approximately 380 W/mK.
Academic Significance of the Study:
This research contributes to the academic understanding of material selection and processing for advanced thermal management applications. It provides empirical evidence for the feasibility of utilizing copper MIM to produce components with high thermal conductivity, addressing the growing demands of compact electronic devices. The study also highlights the complex interplay between powder characteristics, processing parameters, and resulting material properties in MIM.
Practical Implications:
The findings of this study have significant practical implications for the electronics industry, particularly in the design and manufacturing of cooling solutions for high-power density LEDs and other heat-generating components. Copper MIM offers a viable manufacturing route for producing complex-shaped, high-performance heat sinks, enabling enhanced thermal management and potentially improving the reliability and performance of electronic devices.
Limitations of the Study and Areas for Future Research:
While this study demonstrates promising results, further optimization is necessary to achieve fully dense sintered compacts and potentially reach the intrinsic thermal conductivity of pure copper. The research suggests that grain boundary effects may play a role in limiting thermal conductivity, even with high sintered densities. Future research should focus on:
- Microstructural analysis to characterize grain size and grain boundaries and their impact on thermal transport.
- Investigating advanced sintering techniques and post-processing heat treatments to further enhance density and thermal conductivity.
- Exploring the influence of powder morphology and oxygen content in more detail.
- Conducting cost-benefit analyses to fully evaluate the economic viability of copper MIM heat sinks compared to other manufacturing methods as LED power densities continue to increase.
8. References:
- [1] R. M. German and A. Bose, ‘Injection Molding of Metals and Ceramics', 1997, Princeton, NJ, MPIF.
- [2] J.L. Johnson and Lye- King Tan, Electronics Cooling, 2004.
- [3] K. Portschy, MSc Thesis, FH Technikum Wien, 2006
- [4] H. Klan, VDI Wärmeatlas, 8th edition, Part F, VDI – Gesellschaft Verfahrenstechnik und Chemieingenieurwesen (VDI-GVC), 1996
9. Copyright:
- This material is "R. Zauner, R. Nagel, E. Neubauer, K. Portschy, P.A Davies, M.A.Kearns"'s paper: Based on "Development of Copper MIM Powders for Thermal Management Applications".
- Paper Source: First page of the provided paper.
This material was summarized based on the above paper, and unauthorized use for commercial purposes is prohibited.
Copyright © 2025 CASTMAN. All rights reserved.