This introductory paper is the research content of the paper "Characterization of Mixed Metals Swaged Heat Sinks for Concentrated Heat Source" published by InterPACK’03®.
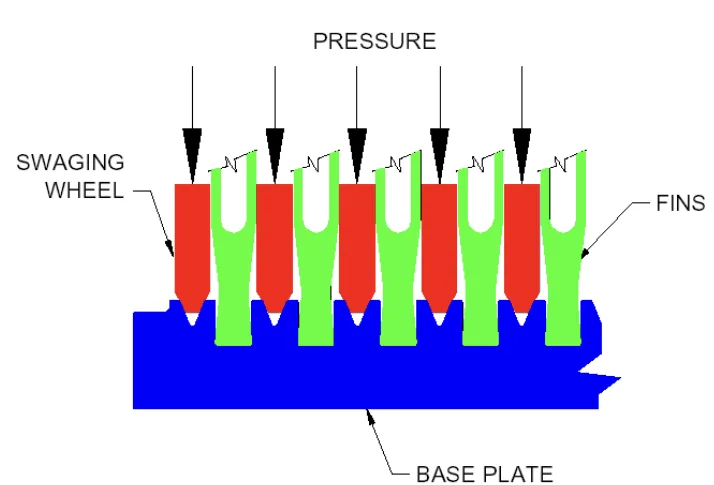
1. Overview:
- Title: Characterization of Mixed Metals Swaged Heat Sinks for Concentrated Heat Source
- Author: Ahmed M. Zaghlol, William Leonard and Richard Culham
- Publication Year: 2003
- Publishing Journal/Academic Society: Proceedings of InterPACK’03®: International Electronic Packaging Technical Conference and Exhibition
- Keywords: (The paper does not explicitly list keywords, but based on the content, relevant keywords would include: Heat Sink, Swaging, Thermal Resistance, Forced Convection, Copper, Aluminum, Mixed Metals, Concentrated Heat Source)
2. Abstracts / Introduction
Abstract
Experimental study investigating thermal performance of four heatsink combinations: all Aluminum, all Copper, Copper baseplate/Aluminum fin, and Aluminum baseplate/Copper fin. Tests in a vertical wind tunnel with Reynolds numbers (based on fin spacing) from 1000 to 4000. All-Copper heatsink showed the lowest thermal resistance (22% lower than all-Aluminum). Copper-Base/Aluminum-Fin showed 11.4% improvement, and Aluminum-Base/Copper-Fin showed 8.5% improvement compared to all-Aluminum.
Introduction
High temperature and heat dissipation limit electronic system capabilities. Heatsinks are crucial for microprocessors and power electronics. Increasing heat flux necessitates materials with higher thermal conductivity (e.g., Copper). This paper focuses on mixed-metal swaged heat sinks to improve heat spreading.
3. Research Background:
Background of the Research Topic:
- Electronic system limitations due to high temperature and heat dissipation.
- Need for heatsinks in microprocessors and power electronics.
- The trend toward higher power density.
Status of Existing Research:
- Extruded heatsinks are common, but have limitations in aspect ratio.
- Bonded fin heatsinks are used for high aspect ratios.
- Die-casting is an alternative for high-volume, low-cost production, but with porosity concerns.
- Bonding methods include thermal epoxy (low conductivity), brazing, and swaging.
Necessity of the Research:
- To explore mixed-metal heat sink designs using the swaging process.
- To reduce heatsink thermal resistance, improving thermal performance in high-power applications.
4. Research Purpose and Research Questions:
Research Purpose:
- To investigate the thermal performance of four heatsink combinations under forced convection.
- To compare the thermal resistance of these mixed-metal designs.
Key Research:
- How does the thermal resistance of all-Aluminum, all-Copper, Copper-base/Aluminum-fin, and Aluminum-base/Copper-fin heat sinks compare under forced convection?
- What is the impact of fin and base material on thermal performance?
- What is the effect when a high heat conductor is used as the base or the fins?
5. Research Methodology
Research Design:
- Experimental study using a forced convection heat transfer mode.
- Four heatsink designs tested in pairs.
Data Collection Method:
- Heat sinks placed in a vertical wind tunnel.
- Block heater (800W, 10% baseplate coverage) used as a heat source.
- Experiments at Reynolds numbers 1000-4000 (approach velocity 2-8 m/s).
- Temperature rise measured at eight locations.
- Dantec hot wire anemometer use.
- Dwyer differential pressure transducers use.
Analysis Method:
- Thermal resistance calculated from temperature measurements.
- Comparison of thermal resistance between different heatsink designs.
- Reynolds number based on fin spacing.
Research Subjects and Scope:
- Four heatsink designs: Al Base-Al Fins, Cu Base-Al Fins, Al Base-Cu Fins, and Cu Base-Cu Fins.
- Fin geometries and dimensions detailed in Table 1 and Figure 2.
- "Swaging" process used for bonding (Figure 1).
6. Main Research Results:
Key Research Results:
- All-Copper (Cu Base-Cu Fins) heatsink had the lowest thermal resistance.
- All-Aluminum (Al Base-Al Fins) heatsink had the highest thermal resistance.
- Copper-Base/Aluminum-Fin heatsink showed an 11.4% performance improvement over all-Aluminum.
- Aluminum-Base/Copper-Fin heatsink showed an 8.5% performance improvement over all-Aluminum.
Analysis of presented data:
- Table 2 shows the percentage reduction in thermal resistance compared to the all-Aluminum heatsink.
- Figure 7 shows thermal resistance vs. fin spacing Reynolds number.
- Figure 8 shows pressure drop vs. fin spacing Reynolds number.
- Higher pressure drop observed for Copper fin heat sinks due to smaller fin spacing.
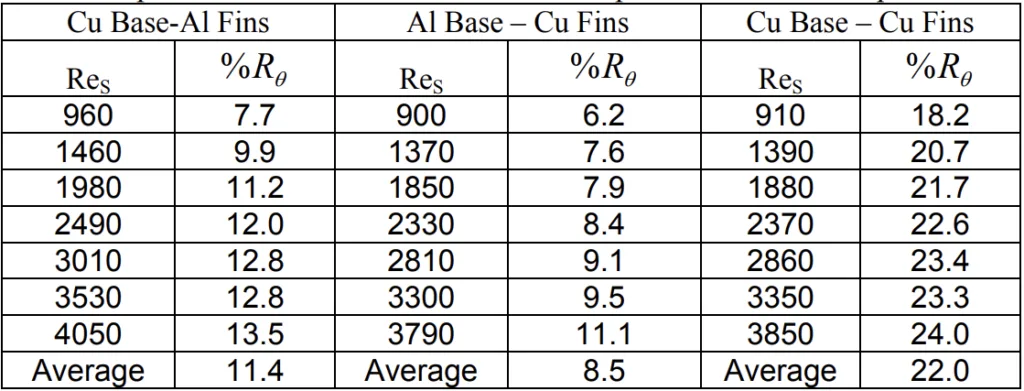
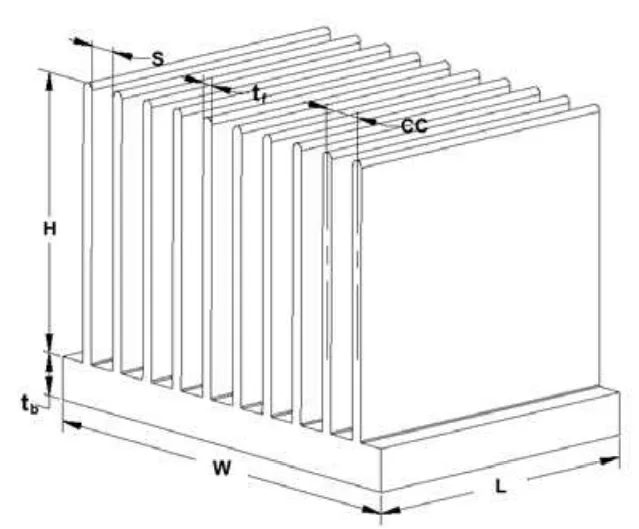
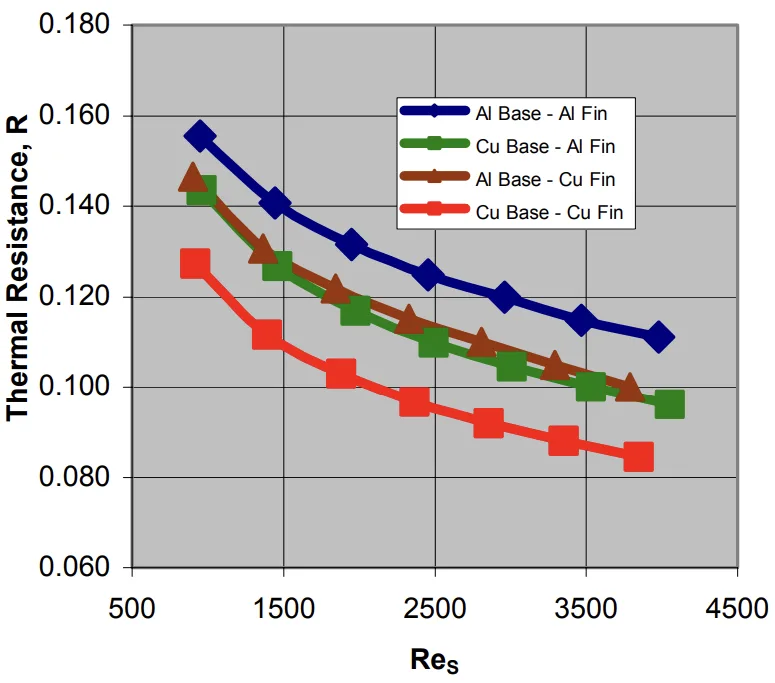
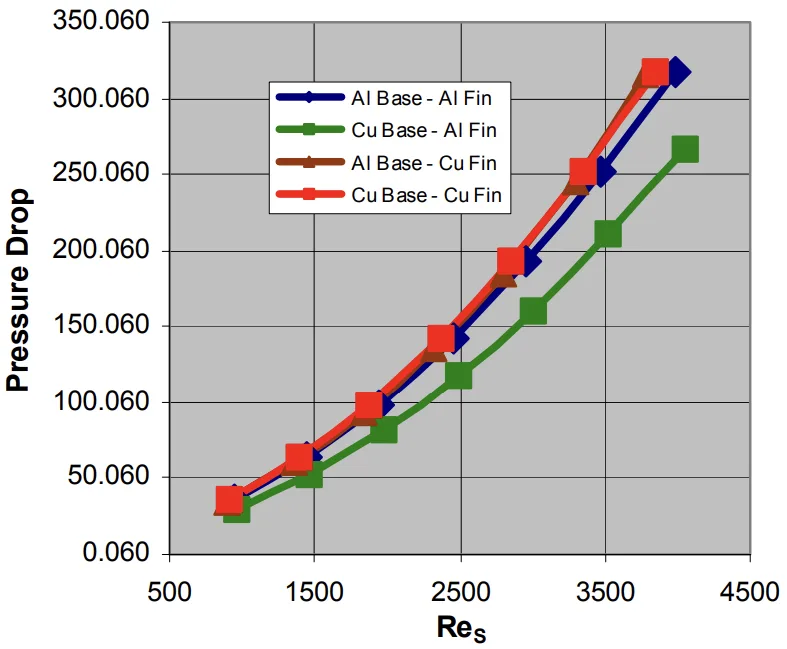
Figure Name List:
- Figure 1: Swaging process
- Figure 2: Heatsink geometry and dimensions
- Figure 3: Heat Sink Back-to-Back Configuration
- Figure 4: Heat Sink and Heater Plate
- Figure 5: Thermocouple Locations on 10% Coverage Heater Plate
- Figure 6: Testing Rig
- Figure 7: Thermal resistance vs. fin spacing Reynolds Number.
- Figure 8: Pressure drop vs. fin spacing Reynolds Number
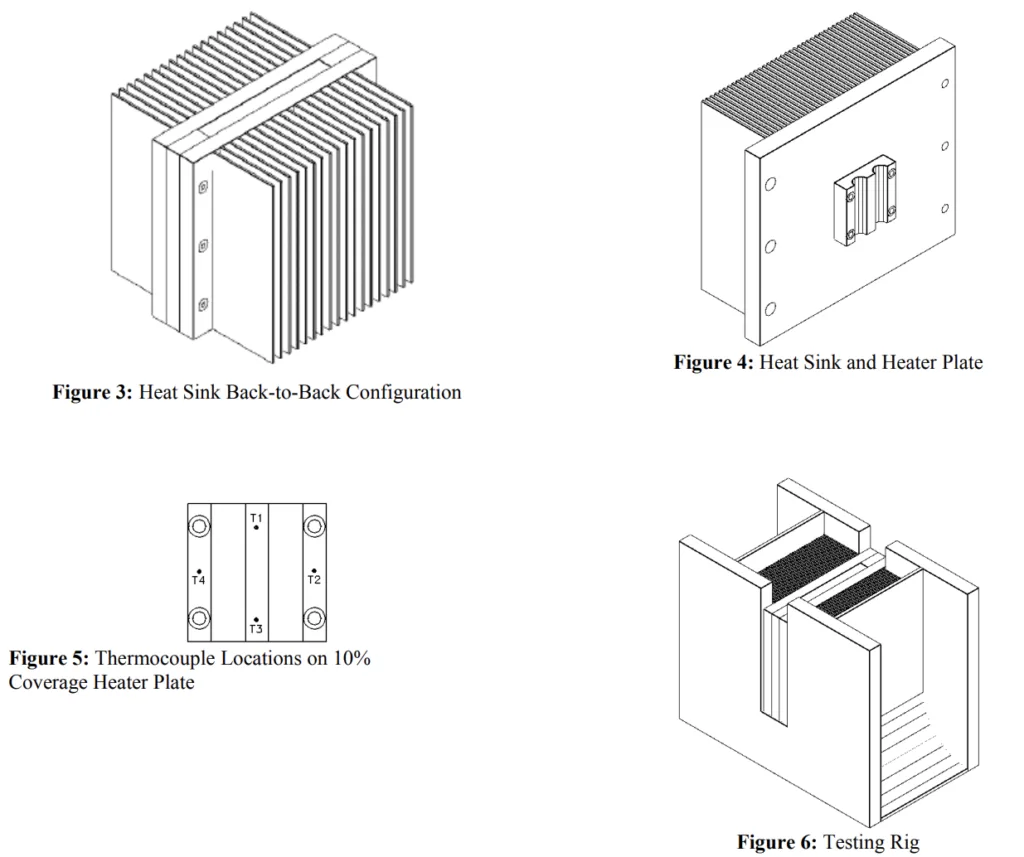
7. Conclusion:
Summary of Key Findings:
- All-Copper heat sink had the lowest thermal resistance (22% reduction).
- Mixed-metal designs showed improved performance compared to all-Aluminum.
- Using copper as the base material is more effective for heat spreading than using it as the fin material in 10% coverage.
Academic Significance of the Study:
- Provides experimental data on the performance of mixed-metal swaged heat sinks.
- Quantifies the benefits of using copper in different configurations.
Practical Implications:
- Guidance for heatsink design in high-power electronics.
- Demonstrates the advantages of swaged mixed-metal heat sinks.
Limitations of the Study and Areas for Future Research:
- The paper does not explicitly state limitations, Future research could explore:
- Different heat source sizes and distributions.
- Other metal combinations.
- Optimization of fin geometry.
- Cost analysis.
8. References:
- H.W. Chu, C.L. Belady and C.D. Patel, “A Survey of High-performance, High Aspect Ratio, Air Cooled Heat Sinks", 1999 International Systems Packaging Symposium, Jan. 11-13, 1999, San Diego, California, USA.
- H. Jonsson and B. Palm, “Influence of Airflow Bypass on the Thermal performance and Pressure Drop of Plate Fin and Pin Fin Heat Sinks for Electronics Cooling", Proceedings of Eurotherm Sem. No. 58, Nantes, France, Sept. 24-26, 1997, pp. 44-50.
- W. Leonard, P. Teertstra, J.R. Culham and A. Zaghlol, "Characterization of Heat Sink Flow Bypass in Plate Fin Heat Sinks", Proceedings of IMECE 2002: International Mechanical Congress and Exposition Nov. 17-22, 2002 New Orleans, Louisiana.
- Robert W. Messler Jr., Joining of Advanced Materials, Stoneham, MA, 1993.
- R-Theta Catalogues.
- Zaghlol, K. Hermann, J. Butler, P. Teertstra, and J.R. Culham, "Forced Convection Heat Transfer for Swaged Mixed Metal Heat sinks," Proceedings of Itherm2002, IEEE Symposium, May 29-June1, 2002, San Diego, California, USA.
- Zaghlol, W. Leonard, and J.R. Culham, “Characterization of Swaged Mixed Metal Heat sinks," to be presented in APEC 2003, Miami Beach, Florida, February 2003.
9. Copyright:
- This material is Ahmed M. Zaghlol, William Leonard and Richard Culham's paper: Based on "Characterization of Mixed Metals Swaged Heat Sinks for Concentrated Heat Source".
- Paper Source: [Paper Number: InterPack2003-35315]
This material was created to introduce the above paper, and unauthorized use for commercial purposes is prohibited.
Copyright © 2025 CASTMAN. All rights reserved.