This article introduces the paper "A Hybrid Design Support System for Die Casting Scheme" presented at The Hong Kong Polytechnic University.
1. Overview:
- Title: A Hybrid Design Support System for Die Casting Scheme
- Author: Lu Hong Yuan
- Publication Year: 2003
- Publishing Journal/Academic Society: The Hong Kong Polytechnic University
- Keywords: die casting, design support system, parting scheme, gating system, fuzzy synthetic evaluation, CAD, automation
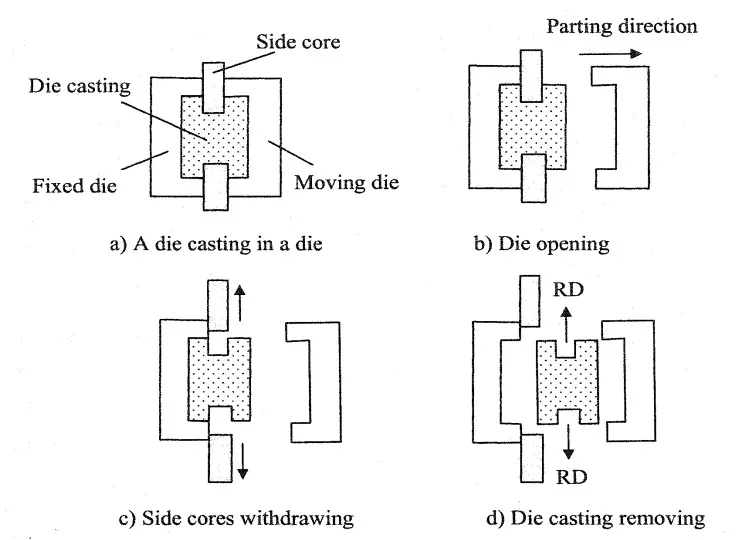
2. Research Background:
- Social/Academic Context of the Research Topic:
The research addresses the increasing demands in the die casting industry for enhanced casting quality, rapid production cycles, management of process complexity, and cost reduction. Continuous improvement in the die casting process is crucial to meet these demands. - Limitations of Existing Research:
The paper points out that achieving optimal solutions in die casting design cannot be solely reliant on empirical and analytical methods. Existing Computer-Aided Design (CAD) approaches are often insufficient. Specifically, current gating design systems presuppose substantial user knowledge, and parameter selection frequently depends on single factors, overlooking broader influences. Parting direction selection is often user-defined or limited to three principal axes, potentially missing optimal solutions. - Necessity of the Research:
This research is motivated by the necessity to automate the die design process, thereby compensating for the scarcity of experienced design experts. Automation is seen as a key strategy to shorten design lead times, reduce development costs, and enhance the overall quality of die casting production.
3. Research Purpose and Research Questions:
- Research Purpose:
The primary purpose of this research is to develop a "hybrid design support system (HDSS)" for die casting schemes. This system aims to automate the die design process and mitigate the challenges posed by a lack of design experts in the field. - Key Research Questions:
The research implicitly addresses several key questions related to automating die casting scheme design:- How can geometrical features of die castings be effectively recognized and extracted for automated design processes?
- What kind of mechanism can be developed for generating effective parting schemes?
- How can parting schemes be evaluated quantitatively to determine their performance?
- What is an effective approach for selecting process parameters in die casting?
- How can a knowledge-based system be developed for gating design in die casting?
- Research Hypotheses:
While not explicitly stated as hypotheses, the research operates under the premise that:- A hybrid design support system can significantly automate and improve the design process for die casting schemes.
- A hybrid approach, integrating knowledge-based systems with computer-aided design techniques, is an effective strategy for die casting design.
- The proposed methodology, when implemented, will be capable of producing sound and acceptable die castings.
4. Research Methodology
- Research Design:
The research employs a development and application approach to create a computerized Hybrid Design Support System (HDSS). This system integrates knowledge-based and feature-based approaches, utilizing fuzzy judgment techniques and computer-aided methods. The system development follows a Design-Evaluation-Verification-Modification (DEVM) iterative pattern. - Data Collection Method:
The proposed methodology was tested using "real castings from industry," indicating practical validation. Case studies are utilized to demonstrate the system's capabilities, including "Example I and Example II in Chapter 4" and a "Tap body casting in Chapter 7." - Analysis Method:
The analysis within the research incorporates several methods:- Geometrical feature analysis: To understand and process the geometry of die castings.
- Rule-based evaluation: To assess parting schemes against established design rules.
- Fuzzy synthetic evaluation: For parameter selection and scheme evaluation, handling uncertainties and multiple factors.
- Numerical simulation: To verify design validity and visualize the casting process.
- Research Subjects and Scope:
The research focuses on the design of die casting schemes, specifically addressing:- Parting scheme design
- Gating system configuration
- Process parameter selection
The scope is primarily on "cold chamber die casting" processes.
5. Main Research Results:
- Key Research Results:
The primary outcome is the development of a "hybrid design support system (HDSS)" for die casting schemes. The research details methodologies for:- Concave Feature Recognition: Utilizing a "ray detection method" to identify concave features in die castings.
- Release Direction Determination: Methods for calculating the release direction of identified concave features.
- Parting Scheme Generation: Employing a "direction-shifting approach" to generate candidate parting schemes.
- Parting Scheme Evaluation: Using "design rules" and "fuzzy synthetic evaluation" to assess and rank parting schemes.
- Gating System Design: Integrating "case-based" and "feature-based CAD approaches" for gating system configuration.
- Parameter Selection: Applying "fuzzy synthetic evaluation" for the selection of optimal process parameters.
- Statistical/Qualitative Analysis Results:
The HDSS was tested with industrial case studies, and the "recommended designs were found to be capable of producing sound and acceptable castings." The case studies serve as qualitative validation of the system's practical applicability and effectiveness. - Data Interpretation:
The research demonstrates that the developed HDSS offers a structured and automated approach to die casting scheme design. This system effectively addresses the limitations of traditional, experience-dependent design methods by incorporating computational tools and knowledge-based techniques. - Figure Name List:
The paper includes numerous figures to illustrate concepts and results. Representative figures include:- Fig. 2.1 DEVM model for die casting scheme design
- Fig. 2.2 Overview of the hybrid design support system
- Fig. 3.1 Removal of a die casting with side cores
- Fig. 4.2 The dependency graph of parting scheme design
- Fig. 5.4 Scheme A chosen as optimal parting scheme
- Fig. 6.2 Die casting parameter design with fuzzy synthetic evaluation
- Fig. 7.1 The framework of gating design
- Fig. 7.28 Casing body produced with the given die casting scheme
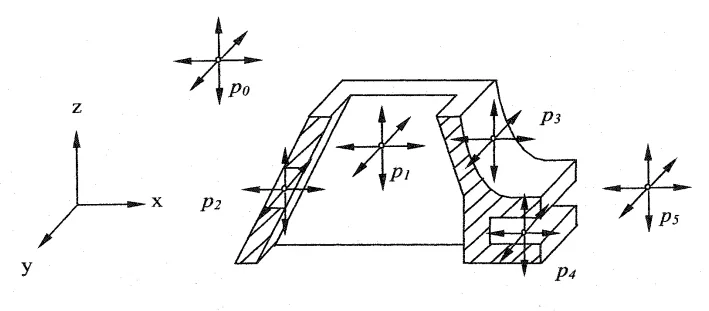
6. Conclusion and Discussion:
- Summary of Main Results:
The thesis successfully developed a "hybrid design support system (HDSS)" for die casting scheme design. This system integrates CAD techniques with fuzzy theory, numerical simulation, and knowledge-based approaches to address the critical aspects of die casting scheme design, including parting scheme design, gating system configuration, and parameter selection. - Academic Significance of the Research:
This research makes a significant academic contribution by advancing the automation of CAD systems in die casting die design. The "hybrid approach" is presented as a novel contribution, effectively linking diverse disciplines to create a comprehensive design tool. The work is positioned as "one of the first of its kind" in automating die casting die design. - Practical Implications:
The HDSS offers substantial practical benefits for the die casting industry. It has the potential to "reduce development time," "increase design reliability," and "avoid excessive trial and error work" in real-world die casting operations. The system provides a "useful tool for the die casting industry" by streamlining and improving the design process. - Limitations of the Research:
The research acknowledges that the developed HDSS is a "prototype." The scope of casting parts is "limited to conventional two-plate dies and rectilinear removal," indicating areas for future expansion. The effectiveness of the HDSS is also noted to be dependent on the "completeness of design knowledge" integrated into the system.
7. Future Follow-up Research:
- Directions for Follow-up Research:
The paper suggests several directions for future research and system enhancement:- Extending the system to handle "rotational removal of casting."
- Integrating the HDSS with "commercial graphic and simulation software" to enhance its capabilities and interoperability.
- Incorporating "more intelligent techniques" to further automate the die design process.
- Developing a "similarity analysis model for efficient case retrieval" within the case-based reasoning component of the system.
- Exploring "virtual prototyping system for die design" based on the current work.
- Areas Requiring Further Exploration:
Further exploration is needed in areas such as:- Enhancing the "completeness and integrity of the design knowledge" embedded within the HDSS.
- Expanding the library of "design knowledge and geometrical primitives" to broaden the system's applicability.
- Investigating "virtual manufacturing technique" as a future direction for die casting design systems.
8. References:
- Akira Nishimura and Tatsuichi Fukusako, “A method of calculating cavity filling time and its evaluation in die casting”, Foundry, Vol. 57, No.8, p.503-509 (1985)
- Allsop D.F., D. Kennedy, Pressure Diecasting, Part 2, Pergamon Press, Oxford (1983)
- Andresen W.T., “Metlflow: Computer aids for die casting”, Die Casting Engineer, No.5, p.38-43 (1986)
- Andresen W. T., “Computer simulation and analysis of liquid metal flow and thermal conditions in die casting dies”, SDCE 14th International Die Casting Congress and Exposition, G-T87-019, May 11-14, Toronto Ontario Canada (1987)
- Andrew Kusiak and Juite Wang, “A knowledge-based system for building scheduling Models”, Artificial Intelligence in Optimal Design and Manufacturing, Prentice-Hall, Inc., pp173-197 (1994)
- Anthory, A. Amsden and fracis h. Harlow, “The SMAC method: A numerical technique for calculating incompressible fluid flow”, Los Alamos Scientific Laboratory Report LA-4370 (1970)
- Anzai Koichi, Toshio Uchida and Katsutoshi Kataoka, “prediction of defects in die castings by quisi three-dimensional flow analysis”, Foundry, Vol. 60, No.12, p.763-769 (1988)
- Balachandran M., Knowledge-Based Optimum Design, Computational Mechanics Publications, Hobbs the Printers Ltd (1993)
- M.R. Barone and D.A. Caulk, “dieCAS- Thermal analysis software for die casting: modeling approach”, Die Casting Technology, NADCA, October 18-21, Cleveland T93-013, p.19-25 (1993)
- Barton H.K., Product Design for Die Casting, Society of Die Casting Engineers, River Grove, ILL. (1981)
- Benedek Von Takach, “Some aspects of feed design for pressure die casting dies”, 10th SDCE Internatioanl Die Casting Exposition & Congress, March 19-22, St. Louis, Missouri, Paper No. G-T79-094 (1979)
- Ceng Yidan and Xiao Keze, “Expert system for analysis of casting porosity defects”, Special Casting and Nonferrous Alloys, No.1, p.25-27 (1993)
- Chen Jincheng, Die Casting Technology Basis, Beijing Radio Equipment Factory (1978)
- Chen Lin-Lin, Visibility algorithms for mould and die design, Ph.D. Dissertation, The University of Michigan (1992)
- Chen Lin-Lin, Shou-Yan Chou and Tony C Woo, “Parting directions for mould and die design”, Computer-Aided Design, Vol. 25, No.12, p.763-767 (1993)
- Chen C.W., C.R. Li and T.H. Han, “Numerical simulation of filling pattern for an industrial die casting and its comparison with the defects distribution of an
9. Copyright:
This material is Lu Hong Yuan's paper: Based on "A Hybrid Design Support System for Die Casting Scheme".
Paper Source: http://lib.polyu.edu.hk/
This material was summarized based on the above paper, and unauthorized use for commercial purposes is prohibited.
Copyright © 2025 CASTMAN. All rights reserved.