This article introduces the paper "AM-HP2: A New Magnesium High Pressure Diecasting Alloy for Automotive Powertrain Applications" by Mark A. Gibson, Colleen J. Bettles, Morris T. Murray, and Gordon L. Dunlop, published in January 2006.
1. Overview:
- Title: AM-HP2: A New Magnesium High Pressure Diecasting Alloy for Automotive Powertrain Applications
- Authors: Mark A. Gibson, Colleen J. Bettles, Morris T. Murray, Gordon L. Dunlop
- Year: 2006
- Publication: Unspecified in provided image.
- Keywords: magnesium alloy, high pressure die casting, creep
2. Research Background:
The automotive industry seeks significant weight reduction. Magnesium alloys offer a potential solution, but their elevated temperature properties are often inadequate for engine applications. Two main processing routes exist for engine crankcases: low-pressure/gravity casting and high-pressure die casting. Low-pressure casting allows for complex designs and post-casting heat treatments but is more expensive. High-pressure die casting offers faster solidification and lower costs but requires alloy properties to be developed during the casting process. Existing high-pressure die-casting magnesium alloys, primarily based on the Mg-Al system, compromise elevated temperature creep resistance due to the presence of aluminum. Therefore, a new alloy was needed to overcome these limitations.
3. Research Objectives and Research Questions:
- Research Objective: To develop a new magnesium die-casting alloy (AM-HP2) with good diecastability and excellent creep resistance at 150-200°C, suitable for automotive powertrain applications.
- Key Research Question: Can a magnesium alloy be developed that combines good diecastability with superior creep resistance at temperatures relevant to automotive powertrain applications (150-200°C)?
- Research Hypothesis: A modified Mg-rare earth alloy can achieve both good diecastability and superior creep resistance compared to existing Mg-Al based alloys.
4. Research Methodology:
- Research Design: Comparative study of AM-HP2 with other commercially available high-temperature creep-resistant magnesium alloys (AZ91D, AE42, AJ62).
- Data Collection Methods: Oxidation trials, castability assessment, tensile testing (at RT, 100°C, 150°C, and 177°C), constant load tensile creep tests (600 hours), bolt load retention (BLR) tests (100 hours at 150°C and 177°C). Microstructural analysis was also performed.
- Analysis Methods: Statistical analysis of mechanical properties, microstructural examination using optical microscopy.
- Research Subjects and Scope: AM-HP2 alloy and comparative alloys (AZ91D, AE42, AJ62). The study focused on mechanical properties relevant to automotive powertrain applications, specifically creep resistance at elevated temperatures.
5. Main Research Results:
- Key Findings: AM-HP2 demonstrated significantly improved oxidation resistance compared to unmodified alloys. Its diecastability was similar to AZ91D. At temperatures of 100°C and above, AM-HP2 exhibited superior 0.2% proof stress compared to AE42 and AJ62. While AM-HP2 showed lower ductility than AE42 and AJ62, it possessed sufficient ductility for powertrain applications. Creep resistance of AM-HP2 was comparable to AM-SC1 (a successful sand-casting alloy) under stringent test conditions (177°C and 90 MPa). Bolt load retention (BLR) was superior to AJ52 at relevant temperatures. The microstructure of AM-HP2 consisted of a magnesium-rich matrix with a continuous intermetallic framework, contributing to its creep resistance.
- Statistical/Qualitative Analysis Results: Table I presents tensile test data for AM-HP2 at various temperatures. Figure 4 compares the 0.2% proof stress, UTS, and elongation of AM-HP2, AE42, and AJ62. Figure 5 compares the creep response of AM-HP2 and AM-SC1. Table II compares the creep behavior of AM-HP2 with other alloys. Figure 6 shows BLR results. Figure 7 illustrates the castability/creep performance space. Figures 1 and 3 show microstructural images.
- Data Interpretation: The superior creep resistance of AM-HP2 at elevated temperatures is attributed to its microstructure, specifically the continuous intermetallic framework. The good diecastability is attributed to modifications in alloy composition that reduce oxidation during solidification.
- Figure List:
- Figure 1: (a) Photograph of the as-solidified top surface of AM-HP2; (b) Optical photomicrograph showing limited oxidation.
- Figure 2: AM-HP2 part showing high-quality surface finish.
- Figure 3: Optical micrographs of AM-HP2 microstructure at low and high magnification.
- Figure 4: Comparison of tensile properties (0.2% proof stress, UTS, elongation) of AM-HP2, AE42, and AJ62 at various temperatures.
- Figure 5: Comparison of creep response of AM-HP2 and AM-SC1.
- Figure 6: Comparison of bolt load retention (BLR) behavior of AM-HP2 and AM-SC1.
- Figure 7: Schematic representation of castability/creep performance space for various magnesium alloys.
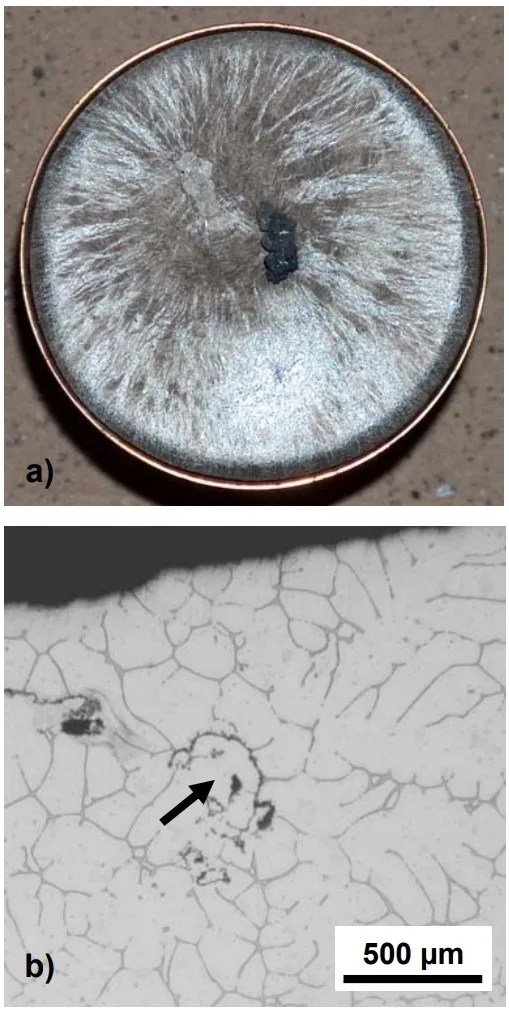
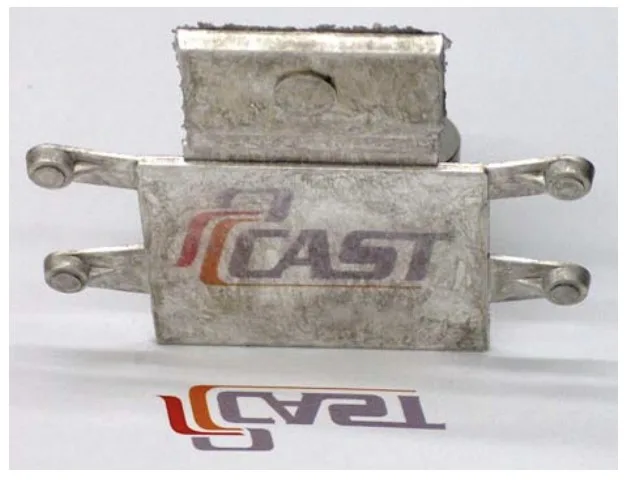
6. Conclusion and Discussion:
AM-HP2 exhibits a favorable combination of diecastability and high-temperature creep resistance, surpassing existing alloys like AE42 and AJ62 at relevant temperatures for automotive powertrain applications. Its performance is comparable to the successful sand-casting alloy AM-SC1, but without the need for post-casting heat treatment. The superior creep resistance is linked to its microstructure.
7. Limitations of the Study:
The study's scope was limited to specific alloys and test conditions. Further research could explore a wider range of alloys and processing parameters.
8. Future Research:
Further research could investigate the long-term creep behavior of AM-HP2 under various load and temperature conditions. The influence of different processing parameters on the microstructure and mechanical properties could also be explored. Investigating the alloy's performance in real-world automotive components would be valuable.
9. References:
The provided image lists references 1-6, but the full bibliographic details are not included in the image. Reference details are partially visible and refer to publications on magnesium alloys, die casting, and creep behavior.
- M.A. Gibson, C.J. Bettles, M.T. Murray, G.L. Dunlop, S.P. Cashion, “AM-HP2: A New Magnesium Alloy with Improved Diecastability and Creep Strength for Powertrain Applications”, (Paper presented at the 13th Magnesium Automotive and End User Seminar, Aalen, 22nd-23rd September 2005).
- K. Pettersen and S. Fairchild “Stress relaxation in Bolted Joints of Die Cast Magnesium Components” SAE Technical Paper 970326, 1997.
- P. Labelle, “Compliation of AJ62A Typical Alloy Properties”, Noranda Inc., December 2004.
- P. Bakke and H. Westengen, “The Role of Rare Earth Elements in Structure and Property Control of Magnesium Die Casting Alloys”, Magnesium Technology 2005, ed. N.R. Neelameggham, H.I. Kaplan, and B.R. Powell (Warrendale, PA: The Minerals, Metals & Materials Society, 2005), 291-296.
- P. Labelle, “Compliation of AJ52A Typical Alloy Properties”, Noranda Inc., December 2004.
- E. Aghion, B. Bronfin, H. Friedrich and Z. Rubinovich, “The Environmental Impact of New Magnesium Alloys on the Transportation Industry”, Magnesium Technology 2004, ed. A.A. Luo (Warrendale, PA: The Minerals, Metals & Materials Society, 2004), 167-172.
This summary is based on the above-mentioned paper and is not permitted for commercial use without authorization.
Copyright © 2025 CASTMAN. All rights reserved.