This introduction paper is based on the paper "Improvement in Conventional Water Jacket Method in Mould Cooling Using Heat Pipe" published by "International Journal of Engineering Science and Technology (IJEST)".
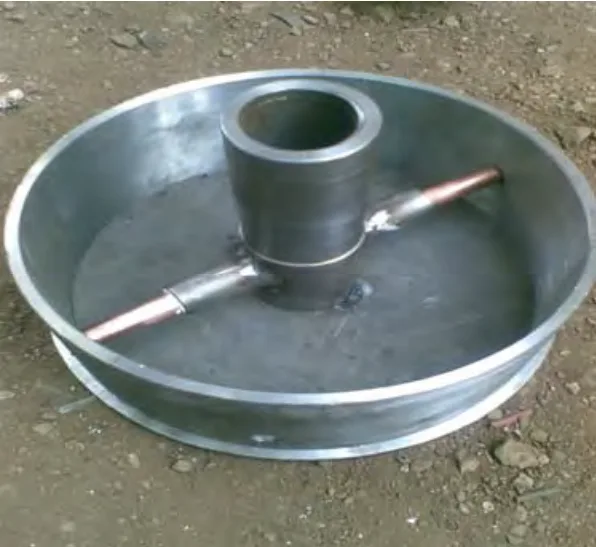
1. Overview:
- Title: Improvement in Conventional Water Jacket Method in Mould Cooling Using Heat Pipe
- Author: Sulas G. Borkar, R.S. Shelke
- Year of publication: 2012
- Journal/academic society of publication: International Journal of Engineering Science and Technology (IJEST)
- Keywords: Conventional water jacket, mould cooling, heat pipe.
2. Abstract:
Die casting moulds and injection moulding are cooled by conventional water jacket method. Cooling of mould is very essential for the purpose of quality of parts and cycle time. The conventional water jackets methods used are having many disadvantages, due to which the effect of mould cooling is not optimum. Hence a technique which can overcome all the disadvantages and become optimum emerged. The main aim of this proposed work is to improve conventional water jackets methods in mould cooling by the application of heat pipe. Heat pipe plays an very important role in such situations, and shows effective results, there by improving the conventional water jacket method in mould cooling. It transfers heat many times faster than pure copper.
3. Introduction:
Plastics are versatile synthetic organic materials mouldable into various shapes using heat and pressure, offering advantages in weight, cost, and resistance. Moulding, particularly injection moulding and die casting, is a primary fabrication method. In these processes, softened or molten material is forced into a mould where it solidifies. Cooling the mould is crucial for both the quality of the final part and the overall productivity (cycle time) of the process.
4. Summary of the study:
Background of the research topic:
Die casting involves forcing molten metal under pressure into split metal dies, while injection moulding involves injecting thermoplastic or thermosetting resins into a mould. Both processes require effective cooling systems to solidify the material within the mould. The conventional method relies on water jackets.
Status of previous research:
The conventional water jacket method, often used with baffles and blades, is the standard technique for cooling moulds in die casting and injection moulding. However, this method suffers from several limitations:
- Low heat transfer due to laminar flow.
- Formation of hot spots in inaccessible areas.
- Increased cycle time due to slow cooling.
- Part rejection due to defects like sink marks, pulling, and spotting caused by insufficient cooling.
- High maintenance and operating costs due to scale formation, calcium deposits, and port clogging.
Purpose of the study:
The study aims to propose an improved mould cooling technique by applying heat pipes within the conventional water jacket method framework. The goal is to overcome the disadvantages of the traditional water jacket system and optimize the mould cooling process.
Core study:
The core proposal is the integration of heat pipes into mould cooling systems. A heat pipe is described as a vacuum-tight copper tube containing a wick and a working fluid. It functions by evaporating the working fluid at the hot end (evaporator), transporting the vapour to the cold end (condenser), where it condenses, releasing latent heat. The condensed liquid returns to the evaporator via capillary action through the wick. This cycle allows heat pipes to transfer heat significantly faster than solid copper. The study notes that heat pipe performance depends on factors like orientation, with horizontal orientation generally providing the best thermal performance for mould cooling. Heat pipes are available for different temperature ranges suitable for injection moulds (+5°C to +200°C) and die casting dies (+5°C to +350°C). Various working fluids can be used depending on the operating temperature range (Table 3.1). Typical applications include cooling small cores, thin sections, retrofitting old moulds with blocked channels, and enhancing cooling in reverse moulds. The benefits highlighted include faster cooling, reduced cycle times, improved part quality (eliminating hot spots, sink marks), simplified mould design, lower manufacturing costs, reduced maintenance (eliminating scaling and clogging issues), and the ability to upgrade existing moulds.
5. Research Methodology
Research Design:
The paper presents a proposal for improving mould cooling based on the known principles and advantages of heat pipe technology compared to the limitations of the conventional water jacket method. It outlines the concept, operation, and application of heat pipes in this context.
Data Collection and Analysis Methods:
The study analyzes the limitations of the conventional water jacket cooling method based on established knowledge. It describes the operational characteristics of heat pipes and compares their heat transfer capabilities to conventional methods qualitatively. The influence of orientation is discussed, referencing figures illustrating different setups. Information on suitable working fluids and their operating ranges is presented (Table 3.1). The analysis focuses on the potential benefits derived from applying heat pipe properties to solve known problems in mould cooling.
Research Topics and Scope:
The research focuses on the application of heat pipes as an enhancement to conventional water jacket cooling systems in die casting and injection moulds. The scope includes:
- Identifying limitations of conventional water jacket cooling.
- Describing the working principle of heat pipes.
- Discussing the effect of heat pipe orientation.
- Identifying suitable heat pipe types and working fluids for moulding applications.
- Outlining typical applications and benefits of using heat pipes in mould cooling.
6. Key Results:
Key Results:
The study concludes that applying heat pipes in conjunction with conventional water jacket methods can effectively eliminate the disadvantages associated with traditional mould cooling. Key results highlighted are:
- Heat pipes overcome limitations like low heat transfer rates, hot spots, long cycle times, part defects, and maintenance issues (scaling, clogging).
- Heat pipes enable faster mould cooling, leading to reduced cycle times and increased production rates.
- Improved thermal management leads to better part quality by ensuring more uniform cooling and eliminating defects like sink marks.
- Mould design can be simplified, and manufacturing costs potentially lowered.
- Maintenance and operating costs are reduced due to the elimination of scaling and corrosion issues within the heat pipe.
- Heat pipes offer a way to upgrade the performance of existing moulds.
- Horizontal orientation is identified as providing the best thermal performance for heat pipes in mould cooling applications.
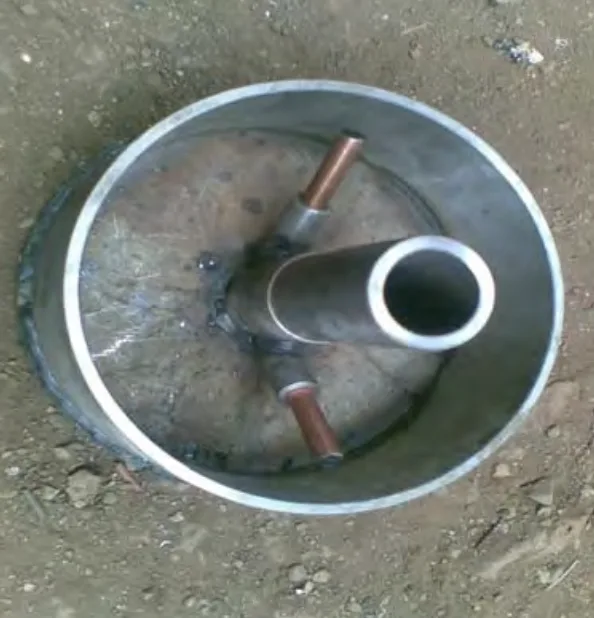
Figure Name List:
- Fig 3.1: Heat Pipe.
- Fig 3.2: Heat pipe in horizontal orientation
- Fig 3.3: Heat pipe in inclined Orientation
- Fig 3.4: Heat pipe in vertical orientation
7. Conclusion:
The application of heat pipes to conventional water jacket methods in mould cooling effectively addresses the various disadvantages of the traditional approach. This integration leads to the elimination of cooling-related problems, improvement in the quality of moulded parts, and achievement of a higher production rate. The study concludes that heat pipes represent an efficient and beneficial tool for mould cooling in die casting and injection moulding industries.
8. References:
- [1] C. G. Li, Yuguang Wu, "Evolutionary optimization of plastic injection mould cooling system layout design" 2010 International Conference on Intelligent system Design and Engineering Application.
- [2] C. L. Li, C. G. Li, A. C. K. MoK "Automatic layout design of plastic injection mould cooling system" Computer- Aided Design 37(2005) 645-662.
- [3] Lubos Behalek, Jozef Dobransky, "Process of cooling injection mould and quality of injection parts" ACTA Technica Corviniensis Bulletin of Engineering.
- [4] H. Xie and M. Aghazadeh, J. Toth"The Use of Heat Pipes in the Cooling of Portables with High Power Packages"-A Case Study with the Pentium Processor Based Notebooks and Sub-notebooks.
- [5] Ioan Sauciuc, Masataka Mochizuki, Kouichi Mashiko, Yuji Saito, Thang Nguyen, The Design and Testing of the Super Fiber Heat Pipes for Electronics Cooling Applications" Sixteenth IEEE SEMI-THREMtm Symposium.
- [6] CK Loh, Enisa Harris and DJ Chou, Comparative Study of Heat Pipes Performances in Different Orientations" 21st IEEE SEMI-THERM Symposium.
- [7] R. S. Khurmi, J. K. Gupta, A Textbook of workshop Technology (Manufacturing Process).
- [8] S.K. Hajra Choudhury, A. K. Hajra Choudhury, Nirjhar Roy, Elements of Workshop Technology Vol: i Manufacturing Processes
- [9] A Faghri, Heat pipe Science and Technology, Taylor and Francis, Washington DC, 1995.
- [10] PD Dunn and D A Reay, Heat Pipes, 4th Edition, Oxford publication, 1994.
- [11] Brennan, P. J. And Kroliczek, E. J., Heat Pipe Design Handbook, B and K Engineering, 1979.
9. Copyright:
- This material is a paper by "Sulas G. Borkar, R.S. Shelke". Based on "Improvement in Conventional Water Jacket Method in Mould Cooling Using Heat Pipe".
- Source of the paper: [DOI URL not provided in the paper]
This material is summarized based on the above paper, and unauthorized use for commercial purposes is prohibited.
Copyright © 2025 CASTMAN. All rights reserved.