This introductory paper is the research content of the paper "Temperature field and failure analysis of die-casting die" published by International Scientific Journal.
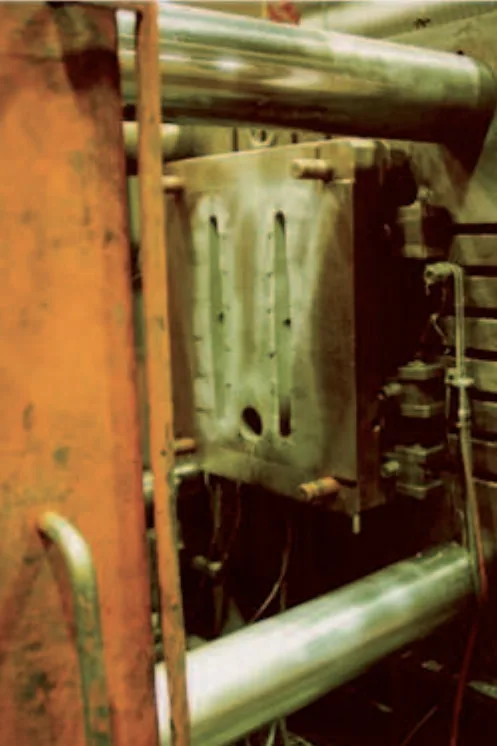
1. Overview:
- Title: Temperature field and failure analysis of die-casting die
- Author: B. Kosec, G. Kosec, M. Soković
- Publication Year: 2007
- Published Journal/Society: Archives of Materials Science and Engineering, Volume 28, Issue 3, Pages 182-187.
- Keywords: Casting; Aluminium alloys; Die-casting die; Temperature field; Failure analysis
2. Abstract
Dies for aluminium alloys die-casting fail because of a great number of a different and simultaneously operating factors. Some of them may be controlled to some extent by the die-casting experts. In the process of the die-casting the primary source of loading is cyclic variation of the temperature; the influence of other loads is relatively insignificant. For economical production of aluminium and aluminium alloys die-castings it is important that the dies have a long working life.
3. Research Background:
Background of the research topic:
Die-casting is a cost-effective method for producing complex and precise aluminum products in large quantities [1]. Aluminum alloy die-castings are used in various industries, including automotive, household appliances, and electrical applications [2]. Approximately half of all aluminum alloy castings worldwide are made using die-casting [3].
Status of previous research:
Aluminum die-casting dies fail due to various stresses, including those created during manufacturing and those occurring during operation [4]. Common failures include heat checking, big cracks, cracking in corners/sharp radii, and cracking due to wear or erosion [1]. Heat checking, caused by thermal stress fatigue, is a primary cause of die failure [8-11].
Need for research:
Die replacement is expensive and time-consuming [5-7]. Therefore, understanding the factors that contribute to die failure is crucial for extending die life and improving the economics of aluminum alloy die-casting.
4. Research purpose and research question:
Research purpose:
To investigate the failures on the working surface of a testing die for die-casting of aluminum alloys.
Core research:
- Observe failures using non-destructive testing methods.
- Analyze the temperature field and its homogeneity during the die preheating process.
- Identify the relationship between temperature distribution, preheating procedures, and crack formation.
5. Research methodology
The experimental part of this work involved observing failures on the working surface of the fixed half of a testing die for die-casting of aluminum alloys. The following non-destructive testing methods were used:
- Thermographic analysis: To measure the temperature distribution and homogeneity on the die surface during preheating.
- Penetrants: To reveal and identify surface cracks.
- Metallographic examination of polymeric replicas: To examine the microstructure and crack characteristics using optical microscopy (OM) and scanning electron microscopy (SEM).
The testing die-casting die is shown in Figure 1. The die was made from BOEHLER W300 ISODISC hot work tool steel [13]. The chemical composition of the steel is given in the Table 2.
6. Key research results:
Key research results and presented data analysis:
- The primary source of loading in the die-casting process is the cyclic variation of temperature.
- Thermographic measurements (Figure 4 & 5) revealed that the required temperatures and homogeneity of the temperature field were not achieved during the preheating process.
- Cracks and pits were observed on the working surface of the die (Figure 6 & 7), attributed to heat checking initiated at identification marks and in corners/sharp edges.
- The practical preheating time of the die was insufficient.
- The flow rate of the heating oil was needed to be increased.
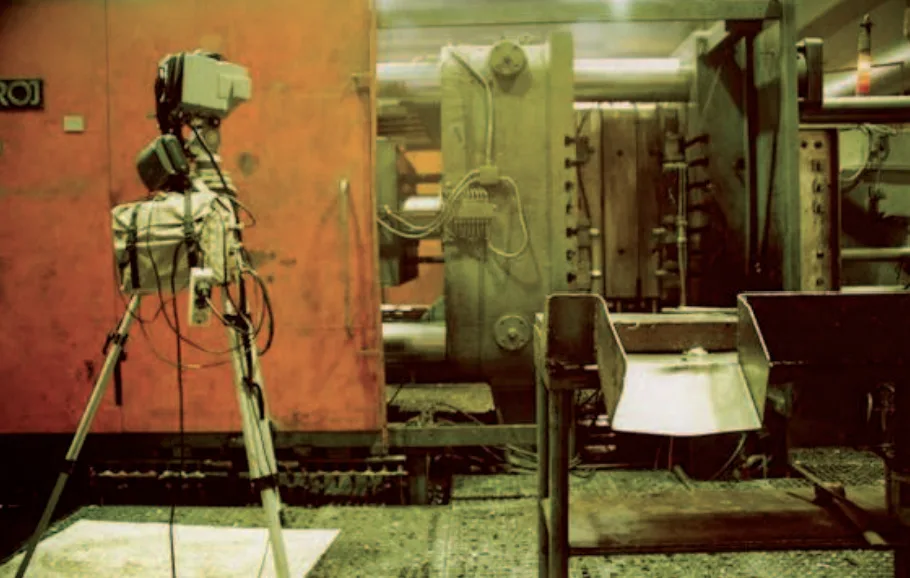
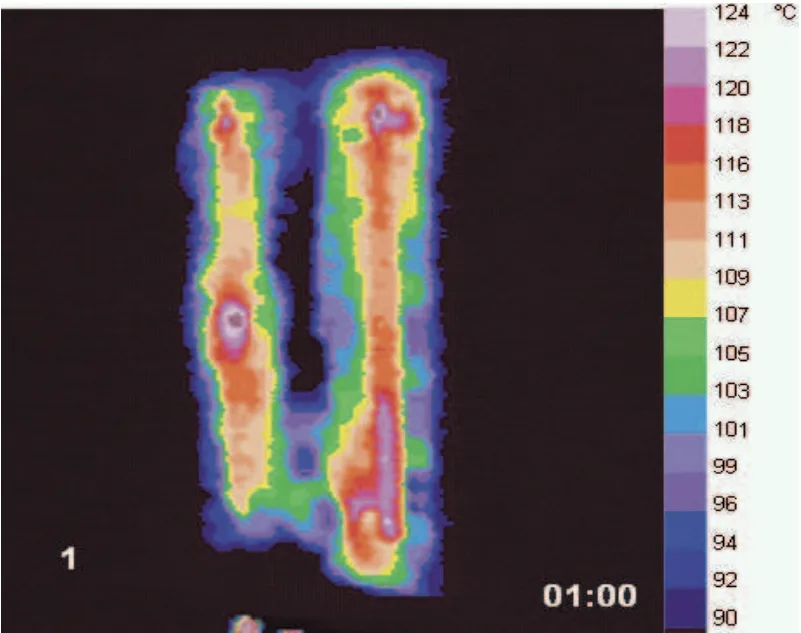
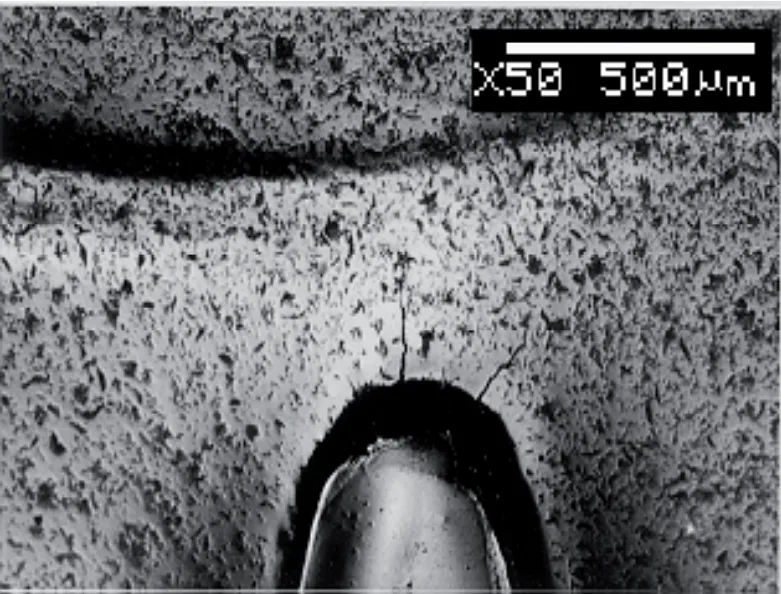
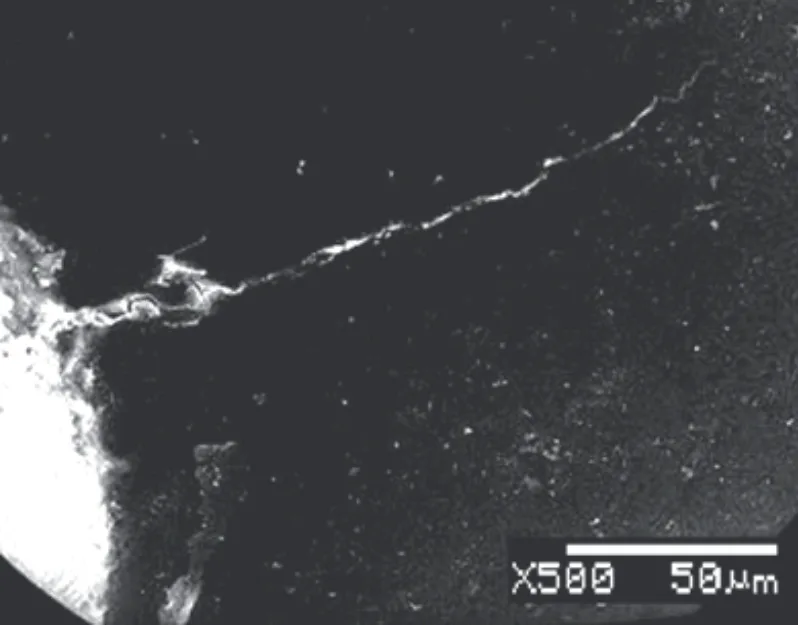
List of figure names:
- Fig. 1. Fixed half of the testing die-casting die
- Fig. 2. Hot dies produce more
- Fig. 3. Position of the thermographic camera and the die-casting machine
- Fig. 4. Working surface of the fixed part of testing die-casting die (see Figure 1, Table 3). Preheating process. Thermographs.
- Fig. 5. Working surface of the fixed part of testing die-casting die. At the beginning of preheating process
- Fig. 6. Working surface of the testing die-casting die. Surface pits and cracks at identification mark. OM
- Fig. 7. Working surface of the testing die-casting die. Surface crack and pits. SEM
7. Conclusion:
Summary of key findings:
Cracking in die-casting dies for aluminum alloys is caused by multiple factors, some controllable by experts. The inhomogeneous and low initial temperature of the die, in addition to die design, material selection, and thermal stress fatigue, contribute to crack formation. The observed die failures were categorized as heat checking and cracking in stress concentration areas.
The presented thermographs demonstrate that achieving the required temperatures and temperature field homogeneity is impossible without modifying the heating method and die design. The primary loading source is cyclic temperature variation; other loads' influence is insignificant. Therefore, the initial solution should involve adjusting the position of heating and/or cooling channels, moving them closer to the die's working surface.
8. References:
- [1] S. Kalpakjian, Tool and die failures - source book, ASM International, Metals Park, Ohio, 1982.
- [2] B. Kosec, M. Sokovic, Failures on the working surface of aluminium die-casting die, Masinstvo 6 1 (2002) 23-28.
- [3] R.N. Lumby, R.G. O'Donnel, D.R. Gunasegaram, M. Girard, New Heat Treatment for Al high pressure die- castings, Heat Treating Progress 6 (2006) 31-37.
- [4] S.S. Manson, Thermal stress and low-cycle fatigue, McGraw - Hill, New York, 1996.
- [5] L.A. Dobrzański, Technical and economical issues of materials selection, Silesian University of Technology, Gliwice, 1997.
- [6] L.A. Dobrzański, Synergic effects of the scientific cooperation in the field of materials and manufacturing engineering, Journal of Achievements in Materials and Manufacturing Engineering 15 (2006) 9-20.
- [7] L.A. Dobrzański, Significance of materials science for the future development of societies, Journal of Materials Processing Technology 173 (2006) 133-148.
- [8] B. Smoljan, An analysis of combined cyclic heat treatment performance, Journal of Materials Processing Technology 155 (2004) 1704 -1707.
- [9] J.V. Tuma, J. Kranjc, The tempeature distribution in the superheater tube, forschung in ingenieurwessen Engineering Research 66 (2001) 153-156.
- [10] L. Gusel, I. Anzel, M. Brezocnik, Effect of lubrication on the stress distribution in an extruded material, International Journal of Advanced Manufacturing Technologies 25 (2005) 288-291.
- [11] L. Kosec, F. Kosel, Heat checking of hot work tools, Mechanical Engineering Journal 29 (1983) 151-158.
- [12] Handbook of case histories in failure analysis, Volume 1, ASM International, Materials Park, Ohio, 1992.
- [13] Böhler Edelstahlhandbuch auf PC V2.0, Kapfenberg, 1996.
- [14] M. Gojic, L. Lazic, B. Kosec, M. Bizjak, Application of mathematical modelling to hardenability testing of low alloyed Mn-Mo steel, Strojarstvo 47 (2005) 101-108.
- [15] L. Kosec, Tool steels from powders, IRT3000 1 (2006) 78-84 (in Slovene).
- [16] J.V. Tuma, Properties and fracture of structural steels with yield stress 373-737 MPa in ambient to nil ductility temperature, Journal of Materials Processing Technology, 121 (2002) 323-331.
- [17] L.A. Dobrzanski, M. Krupinski, J.H. Sokolowski, Computer aided classification of flows occured during casting of aluminium, Journal of Materials Processing Technology 167 (2005) 456-462.
- [18] L.A. Dobrzanski, M. Krupinski, P. Zarychta, R. Maniara, Analysis of influence of chemical composition of Al-Si-Cu casting alloy on formation of casting deffects, Journal of Achievements in Materials and Manufacturing Engineering 20 (2007) 475-478.
- [19] S. Kumar, R. Singh, A Knowledge - based system of progressive die components, Journal of Achievements in Materials and Manufacturing Engineering 21 (2007) 53-56.
- [20] B. Kosec, G. Kosec, Temperature field analysis on active working surface of the die-casting die, Metall 57 (2003) 134-136.
- [21] L. Masalski, K. Eckersdorf, J. McGhee, Temperature measurement, John Wiley & Sons, Chichester, 1991.
- [22] H. Haferkamp, F.W. Bach, M. Niemeyer, R. Veits, Thermogram Characteristics for process monitoring of permanent mould casting, Aluminium 75 (1999) 945-953.
- [23] B. Kosec, G. Kosec, M. Sokovic, Case of temperature field and failure analysis of die-casting die, Journal of Achievements in Materials and Manufacturing Engineering 20 (2007) 471-474.
- [24] B. Kosec, J. Kopac, L. Kosec, Analysis of casting die failures, Engineering Failure Analysis 8 (2001) 355 – 359.
- [25] B. Kosec, M. Sokovic, G. Kosec, Failure analysis of dies for aluminium alloys die-casting, Journal of Achievements in Materials and Manufacturing Engineering 13 (2005) 339-342.
9. Copyright:
- This material is a paper by "B. Kosec, G. Kosec, M. Soković": Based on "Temperature field and failure analysis of die-casting die".
- Source of paper: [DOI not provided in the original document]
This material was created to introduce the above paper, and unauthorized use for commercial purposes is prohibited. Copyright © 2025 CASTMAN. All rights reserved.