This introductory paper is the research content of the paper "Increasing the conductivity of aluminium high-pressure die casting alloy AlSi9Cu3Fe (226D) by Sr modification of eutectic and intermetallic phases" published by Elsevier.
![Table 1
Composition of alloy 226D used for casting measured by OES and nominal composition of alloy 226D (AlSi9Cu3(Fe)(Zn)) from DIN EN 1706 [9] where the limits are maximum
values if no range is specified.](https://castman.co.kr/wp-content/uploads/image-1661-1024x74.webp)
Composition of alloy 226D used for casting measured by OES and nominal composition of alloy 226D (AlSi9Cu3(Fe)(Zn)) from DIN EN 1706 [9] where the limits are maximum values if no range is specified.
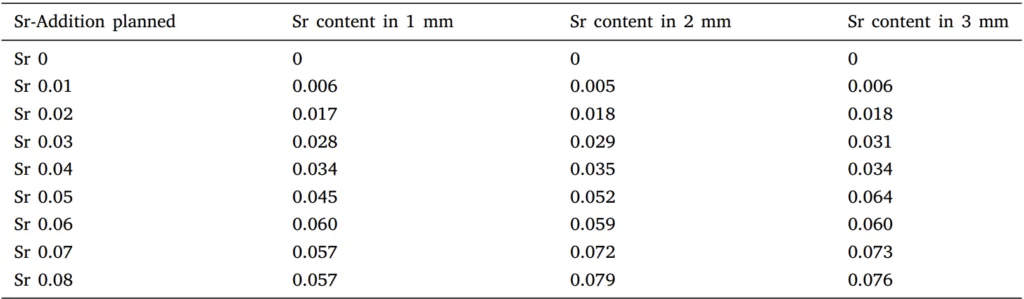
Planned and achieved Sr addition in alloy 226D for 1 mm, 2 mm and 3 mm samples in wt.-% measured by OES.
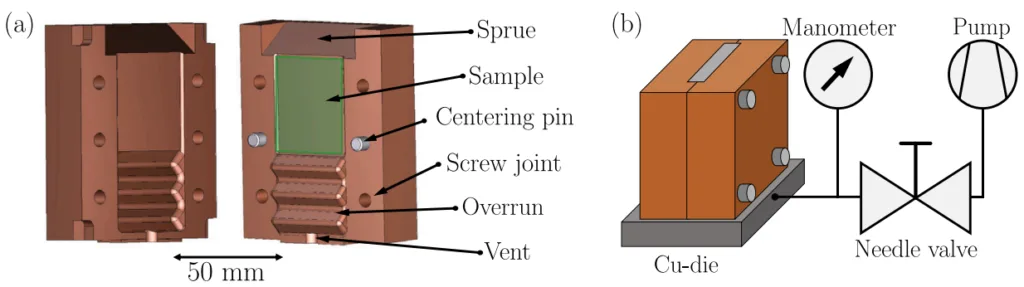
1. Overview:
- Title: Increasing the conductivity of aluminium high-pressure die casting alloy AlSi9Cu3Fe (226D) by Sr modification of eutectic and intermetallic phases
- Author: Felix Feyer, Michael Weigand, Peter Randelzhofer, Carolin Körner
- Publication Year: 2025
- Published Journal/Society: Materials Science and Engineering B
- Keywords: Al alloys, Si modification, Conductivity, Hardness, High throughput
2. Abstract
High-pressure die casting alloys are currently optimized to have an excellent castability and to fulfil the mechanical properties of the demanded parts. In general the conductivity of these alloys decreases from the efforts to improve the mechanical properties and the castability. Although new components in the mobility and communication sector demand alloys with improved conductivity. Focus of the work is the evaluation of influence of modification on the conductivity and mechanical properties of high-pressure die casting alloy AlSi9Cu3Fe. A new Cu-die design with vacuum assistance which mimics the microstructure of high-pressure die castings on lab scale for high throughput investigation was used. The combination of modification of the Si phase and intermetallic phases morphology and distribution collectively influences the properties of the alloy. The extent of modification is connected to the level of alloying elements and Sr content present. The conductivity is increased by more than 10%.
3. Research Background:
Background of the research topic:
Aluminium is increasingly important for structural and functional components due to climate protection, sustainable production, and low-emission products [1,2]. High thermal and electrical conductivity, favorable density-to-strength ratio, and good castability are crucial for Al casting alloys [3-5]. Advancing electrification in automotive engineering and increased requirements in other sectors drive innovations in Al casting to meet increasing weight and thermal requirements [6-8].
Status of previous research:
The widely used HPDC alloy AlSi9Cu3(Fe) (226D) has lower thermal conductivity (110-120 W/mK [9], 13-17 MS/m [9]) than pure Al (180-210 W/mK [9], 34 MS/m [9]) due to high silicon content and alloying elements [9]. Conductivity depends on composition, microstructure, and defects [4,7,9,10]. Stadler et al. [11] showed a linear correlation between electrical and thermal conductivity of Al-Si foundry. Chemical modifiers can change the microstructure of Al casting alloys [12]. Modifiers like Sr, Na, Ca, or Sb can modify eutectic silicon morphology [12-14]. Sr modification mechanisms have been extensively studied [12,15-18]. Timpel et al. [17,19] showed modification is based on two types of Sr-Al-Si co-segregations. Sr addition to Al-Si alloys can significantly improve electrical and thermal conductivity [6,8,10,20-22] by modifying the eutectic Si structure, attributed to reduced projected area of the silicon phase [8,10,20,22].
Need for research:
Sanna et al. [5] and Samuel et al. [23] observed that Sr addition also influenced intermetallic phases. However, these changes have not been investigated regarding their influence on conductivity, unlike in the work of Zhang et al. [8] and Wang et al. [10].
4. Research purpose and research question:
Research purpose:
To better understand the modification of commercial die casting alloy 226D by Sr addition to achieve improved conductivity and performance with typical wall thicknesses suited for HPDC.
Core research:
- Examine and quantify changes in microstructure through Sr addition for improved conductivity using MIPAR software.
- Characterize morphology changes of eutectic Si and other intermetallic phases.
- Reveal the influence of Sr on the structure and morphology of phases in HPDC alloy 226D leading to changes in conductivity.
5. Research methodology
- Research Design: Experimental study using a new Cu-die design with vacuum assistance to mimic HPDC microstructure on a lab scale.
- Material: Commercial HPDC alloy 226D (Table 1 shows the ingot and nominal composition).
- Sr Modification: Adding AlSr10 masteralloy from KBM AFFILIPS B.V. to the melt (Table 2 shows the Sr content of cast samples).
- Sample Preparation:
- Melting 1.5 kg of alloy in graphite crucibles at 720°C.
- Adding preheated AlSr10 alloy and stirring.
- Casting into smaller ingots, remelting, and casting into Cu-dies for sample production.
- Creating samples with wall thicknesses of 1 mm, 2 mm, and 3 mm using different dies with vacuum assistance (Fig. 1).
- Data Collection:
- Electrical Conductivity: Eddy-current measurement system SIGMASCOPE SMP 350 by HELMUT FISCHER GmbH (twelve positions over the whole sample area).
- Metallography: Cutting samples, grinding, polishing, and etching with 10% NaOH for 8 s.
- Microstructure Analysis:
- Light microscopy (LM) with Leica DM6000 M.
- Scanning electron microscopy (SEM) with FEI Quanta 450 equipped with EDAX Octane Elect.
- Electron-probe micro-analysis (EPMA) with JEOL-JXA8800.
- Hardness: Micro hardness tester M400G by Leco (HV0.5, DIN EN ISO 6507-1 [24]).
- Thermal Conductivity: Calculated from measured density (buoyancy weighing), thermal diffusivity (LFA 1000 by Linseis), and calculated heat capacity (based on OES composition) using formula (1).
- Image Analysis: Using MIPAR software to analyze SE- and BSE-images, separating Si phases and other phases with light/heavy elements (Fig. 3). Analyzing phase area, average neighbor distance (AND), and roundness.
6. Key research results:
Key research results and presented data analysis:
- Eutectic Si Structure Modification:
- SEM images (Fig. 4) show the structural change of the Si eutectic phase with Sr addition.
- EPMA mappings (Fig. 5, 7) show the distribution of elements in samples with and without Sr.
- Quantitative analysis using MIPAR (Fig. 9(a)-(c)) shows changes in Si phase area, AND, and roundness with Sr addition.
- Intermetallic Phase Morphology Modification:
- SEM and EDX measurements (Fig. 8) show changes in morphology of intermetallic phases.
- Quantitative analysis using MIPAR (Fig. 9(d)-(f)) shows changes in intermetallic phase area, AND, and roundness with Sr addition.
- Influence of Wall Thickness:
- Comparison of Si phase and intermetallic phase characteristics for different wall thicknesses (Fig. 10).
- Conductivity and Hardness:
- Measured electrical conductivity (Fig. 11(a)) shows an increase with Sr addition up to 0.02 wt.-%.
- Measured thermal conductivity (Fig. 11(b)) shows a similar trend.
- Measured Vickers hardness (Fig. 11(c)) shows a slight increase with Sr addition up to 0.02 wt.-%.
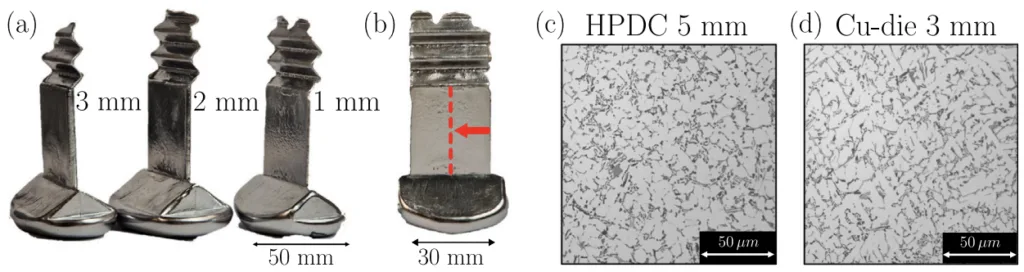
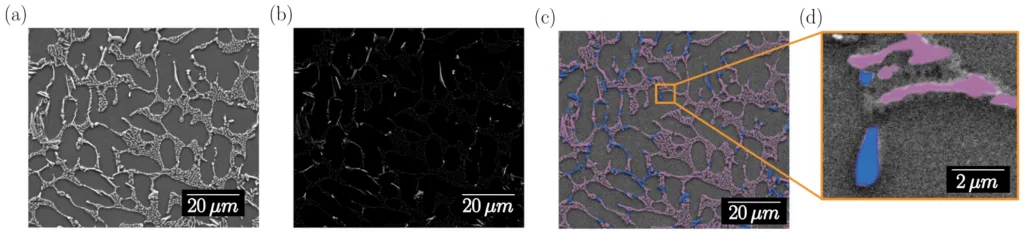
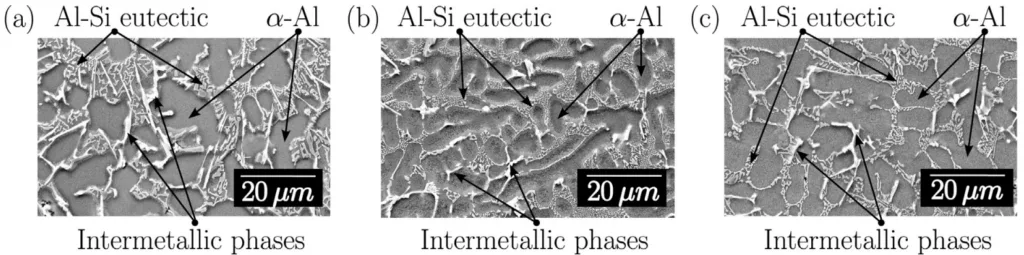
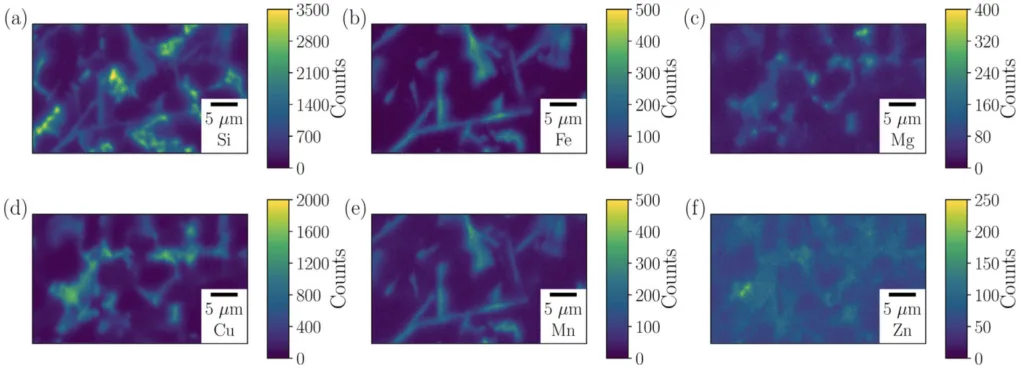
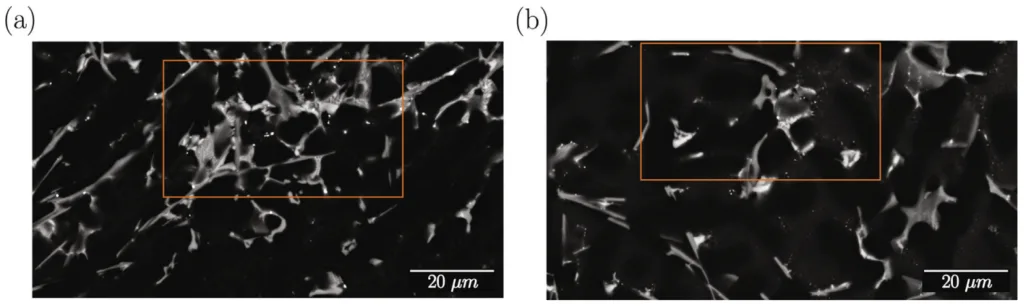
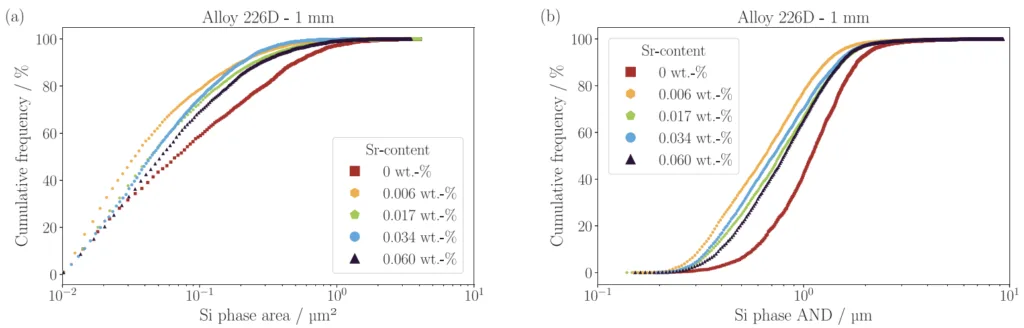


List of figure names:
- Fig. 1. (a) Cu-die used for casting plates and (b) set-up for the casting process with Cu-die, vacuum pump, manometer and needle valve for controlling the applied vacuum.
- Fig. 2. (a) Casting plates (226D) with plate thicknesses of 3 mm, 2 mm and 1 mm cast with vacuum assisted Cu-dies, (b) cutting directions (dotted line) for sample plate preparation with marked surface for microstructure analysis, (c) microstructure of HPDC 5 mm part made from alloy 226D and (d) microstructure of Cu-die casting part with 3 mm thickness made from alloy 226D.
- Fig. 3. (a) SEM SE-picture of the alloy 226D with 0.04 wt.-% Sr addition, (b) SEM BSE-picture on the same position as the SE-picture, (c) analysed and dyed SEM SE-picture with the informations from the SE- and BSE-picture of the present phases and (d) magnification of the detection of Si phase and intermetallic phases formed with heavy element by MIPAR.
- Fig. 4. Exemplary SEM pictures of the influence of Sr addition on the eutectic Si phase structure in 1 mm samples: (a) without Sr, (b) with a low amount of Sr (0.006 wt.-%) and (c) with a high amounts of Sr (0.060 wt.-%).
- Fig. 5. EPMA-mappings of 1 mm samples cast from alloy 226D without Sr addition for the main alloying elements: (a) Si, (b) Fe, (c) Mg, (d) Cu, (e) Mn and (f) Zn.
- Fig. 6. BSE-images of the areas the EPMA-mappings where conducted (a) 1 mm samples cast from alloy 226D without Sr addition and (b) 1 mm samples cast from alloy 226D with 0.034 wt.-% Sr.
- Fig. 7. EPMA-mappings of 1 mm samples cast from alloy 226D with 0.034 wt.-% Sr addition for the main alloying elements: (a) Si, (b) Fe, (c) Mg, (d) Cu, (e) Mn and (f) Zn.
- Fig. 8. EDX-measurement of intermetallic phases present in BSE-images of cast samples with a wall thickness of 1 mm made from alloy 226D: (a) EDX-measurement of Cu rich precipitates marked in orange circles in BSE-image of alloy without Sr addition (b) and marked in green rectangles in picture (b) Fe and Mn rich precipitates and corresponding EDX-measurement in (c), (d) EDX-measurement of Cu rich precipitates marked in orange circles in BSE-image of alloy with 0.034 wt.-% Sr (e) and marked in green rectangles in picture (e) Fe and Mn rich precipitates and corresponding EDX-measurement in (f).
- Fig. 9. Cumulative frequency of Si and intermetallic phase structure in 3 mm casting: (a) Si phase area, (b) Si phase AND, (c) Si phase roundness, (d) intermetallic phase area formed with heavy elements, (e) intermetallic phase AND formed with heavy elements and (f) intermetallic phase roundness formed with heavy elements.
- Fig. 10. Si and intermetallic phase structure in 1 mm, 2 mm and 3 mm samples with one Sr content: (a) Si phase area, (b) Si phase AND, (c) Si phase roundness, (d) intermetallic phase area formed with heavy elements, (e) intermetallic phase AND formed with heavy elements and (f) intermetallic phase roundness formed with heavy elements.
- Fig. 11. Measured conductivity and hardness of cast samples with a thickness of 1 mm, 2 mm and 3 mm with different amounts of Sr addition: (a) electrical conductivity at 20 °C, (b) thermal conductivity at room temperature and (c) Vickers hardness.
- Fig. 12. Cumulative frequency of Si phase structure in 1 mm casting: (a) Si phase area and (b) Si phase AND.
- Fig. 13. Schematic two-dimensional overview of the change of interlinking paths of the a-Al phases (green arrows) with eutectic Si (blue) and intermetallic phases (orange): (a) without Sr modification, (b) with optimal modification of eutectic Si phase with intermediate amounts of Sr and (c) with overmodified Si with high amounts of Sr addition.
- Fig. 14. LM pictures of the influence of Sr addition on the a-Al structure in 3 mm samples: (a) without Sr, (b) with a low amount of Sr (0.006 wt.-%), (c) with a medium amount of Sr (0.018 wt.-%) and with a high amount of Sr (0.064 wt.-%).
7. Conclusion:
Summary of key findings:
- Modification of eutectic Si structure (area, AND, and roundness) for alloy 226D reaches the highest degree of modification around 0.005 wt.-% Sr. Higher additions do not further change the structure for medium/low cooling rates; high cooling rates cause overmodification with higher Sr additions.
- Increasing Sr amounts continuously modify the morphology of intermetallic phases (Cu, Mn, Fe), shifting to smaller, closer packed, and more circular phases.
- Sr addition (around 0.02 wt.-%) increases electrical conductivity of alloy 226D by over 10% for 1 mm, 2 mm, and 3 mm thicknesses. Thermal conductivity of 2 mm and 3 mm samples shows a similar trend. Higher Sr additions do not further increase electrical and thermal conductivity.
- Hardness increases to a maximum around 0.02 wt.-% Sr for all thicknesses, decreasing slightly with higher Sr additions.
- Electrical/thermal conductivity and hardness depend on the combined influence of eutectic Si, intermetallic phase, and a-Al phase size, morphology, and distribution.
The results indicate that Sr modification significantly improves conductivity by altering both eutectic Si and intermetallic phases. The optimal Sr content is around 0.02 wt.-%, beyond which conductivity does not further increase. The study highlights the combined influence of eutectic Si, intermetallic phases, and the α-Al phase on the overall properties. This has implications for optimizing alloy composition and processing for applications requiring high conductivity.
8. References:
- [1] E. Efthymiou, Ö.N. Cöcen, S.R. Ermolli, Sustainable aluminium systems, Sustainability 2 (9) (2010) 3100-3109, http://dx.doi.org/10.3390/su2093100.
- [2] E. Cinkilic, M. Moodispaw, J. Zhang, J. Miao, A.A. Luo, A new recycled Al-Si-Mg alloy for sustainable structural die casting applications, Met. Mater. Trans. A 53 (8) (2022) 2861-2873, http://dx.doi.org/10.1007/s11661-022-06711-4.
- [3] G.K. Sigworth, The modification of Al-Si casting alloys: Important practical and theoretical aspects, Int. J. Met. 2 (2) (2008) 19-40, http://dx.doi.org/10.1007/ bf03355425.
- [4] R. Lumley, I. Polmear, H. Groot, J. Ferrier, Thermal characteristics of heat-treated aluminum high-pressure die-castings, Scr. Mater. 58 (11) (2008) 1006–1009, http://dx.doi.org/10.1016/j.scriptamat.2008.01.0
- [5] F. Sanna, A. Fabrizi, S. Ferraro, G. Timelli, P. Ferro, F. Bonollo, Multiscale characterisation of AISi9Cu3(Fe) die casting alloys after Cu, Mg, Zn and Sr addition, Met. Ital. 105 (2013) 13-24.
- [6] K. Wang, W. Li, W. Xu, S. Hou, S. Hu, Simultaneous improvement of thermal conductivity and strength for commercial A356 alloy using strontium modifica- tion process, Met. Mater. Int. 27 (11) (2020) 4742-4756, http://dx.doi.org/10. 1007/s12540-020-00669-x.
- [7] M. Qi, Y. Kang, Y. Xu, Z. Wulabieke, J. Li, A novel rheological high pressure die-casting process for preparing large thin-walled Al-Si-Fe-Mg-Sr alloy with high heat conductivity, high plasticity and medium strength, Mater. Sci. Eng.: A 776 (2020) 139040, http://dx.doi.org/10.1016/j.msea.2020.139040.
- [8] X. Zhang, Y. Zhou, G. Zhong, J. Zhang, Y. Chen, W. Jie, P. Schumacher, J. Li, Effects of Si and Sr elements on solidification microstructure and thermal conductivity of Al-Si-based alloys, J. Mater. Sci. 57 (11) (2022) 6428-6444, http://dx.doi.org/10.1007/s10853-022-07045-7.
- [9] Technischen Komitee CEN/T.C. 132 Aluminium und Aluminiumlegierungen, Aluminium und Aluminiumlegierungen - Gussstücke - Chemische Zusammenset- zung und mechanische Eigenschaften Deutsche Fassung EN 1706-2020+A1-2021, 2021, Deutsche Norm.
- [10] G. Wang, Z. Guan, J. Wang, M. Ren, R. Yan, J. Song, Effect of cooling rate and modification by strontium on the thermal conductivity of Al-8Si alloy, Metals 11 (9) (2021) 1334, http://dx.doi.org/10.3390/met11091334.
- [11] F. Stadler, H. Antrekowitsch, W. Fragner, H. Kaufmann, E. Pinatel, P. Uggowitzer, The effect of main alloying elements on the physical properties of Al-Si foundry alloys, Mater. Sci. Eng.: A 560 (2013) 481-491, http://dx.doi.org/10.1016/j. msea.2012.09.093.
- [12] S.-Z. Lu, A. Hellawell, The mechanism of silicon modification in aluminum-silicon alloys: Impurity induced twinning, Met. Trans. A 18 (10) (1987) 1721-1733, http://dx.doi.org/10.1007/bf02646204.
- [13] K. Nogita, A. Dahle, Eutectic growth mode in strontium, antimony and phos- phorus modified hypoeutectic Al-Si foundry alloys, Mater. Trans. 42 (3) (2001) 393-396, http://dx.doi.org/10.2320/matertrans.42.393.
- [14] K. Nogita, J. Drennan, A. Dahle, Evaluation of silicon twinning in hypo-eutectic Al-Si alloys, Mater. Trans. 44 (4) (2003) 625-628, http://dx.doi.org/10.2320/ matertrans.44.625.
- [15] M.G. Day, A. Hellawell, The microstructure and crystallography of alu- minium-silicon eutectic alloys, Proc. R. Soc. Lond. Ser. A. Math. Phys. Sci. 305 (1483) (1968) 473-491, http://dx.doi.org/10.1098/rspa.1968.0128.
- [16] S.D. McDonald, A.K. Dahle, J.A. Taylor, D.H. StJohn, Eutectic grains in un- modified and strontium-modified hypoeutectic aluminum-silicon alloys, Met. Mater. Trans. A 35 (6) (2004) 1829-1837, http://dx.doi.org/10.1007/s11661- 004-0091-y.
- [17] M. Timpel, N. Wanderka, R. Schlesiger, T. Yamamoto, N. Lazarev, D. Isheim, G. Schmitz, S. Matsumura, J. Banhart, The role of strontium in modifying aluminium-silicon alloys, Acta Mater. 60 (9) (2012) 3920-3928, http://dx.doi. org/10.1016/j.actamat.2012.03.031.
- [18] J.H. Li, M. Albu, T. Ludwig, Y. Matsubara, F. Hofer, L. Arnberg, Y. Tsunekawa, P. Schumacher, Modification of eutectic Si in Al-Si based alloys, Mater. Sci. Forum 794-796 (2014) 130-136, http://dx.doi.org/10.4028/www.scientific.net/ msf.794-796.130.
- [19] M. Timpel, N. Wanderka, R. Schlesiger, T. Yamamoto, D. Isheim, G. Schmitz, S. Matsumura, J. Banhart, Sr-Al-Si co-segregated regions in eutectic Si phase of Sr-modified Al-10Si alloy, Ultramicroscopy 132 (2013) 216-221, http://dx.doi. org/10.1016/j.ultramic.2012.10.006.
- [20] M.H. Mulazimoglu, R.A.L. Drew, J.E. Gruzleski, The electrical conductivity of cast Al-Si alloys in the range 2 to 12.6 wt pct silicon, Met. Trans. A 20 (3) (1989) 383-389, http://dx.doi.org/10.1007/bf02653917.
- [21] J. Guo, Z.-P. Guan, R.-F. Yan, P.-K. Ma, M.-H. Wang, P. Zhao, J.-G. Wang, Effect of modification with different contents of Sb and Sr on the thermal conductivity of hypoeutectic Al-Si alloy, Metals 10 (12) (2020) 1637, http: //dx.doi.org/10.3390/met10121637.
- [22] J. qi G.A.N., Y. jian HUA.N.G., C. W.E.N., J. D.U., Effect of Sr modification on microstructure and thermal conductivity of hypoeutectic Al-Si alloys, Trans. Nonferr. Met. Soc. China 30 (11) (2020) 2879-2890, http://dx.doi.org/10.1016/ s1003-6326(20)65428-0.
- [23] A.M. Samuel, H.W. Doty, S. Valtierra, F.H. Samuel, Effect of Fe, Sr, P, Ti and undercooling on the precipitation of β-A15FeSi in A319.2 type alloys, Int. J. Met. 11 (4) (2016) 675-687, http://dx.doi.org/10.1007/s40962-016-0116-5.
- [24] Technischen Komitee ISO/TC164 "Mechanical testing of metals" and Tech- nischen Komitee CEN/TC459 "ECISS-Europäisches Komitee für Eisen- und Stahlnormung", Metallische Werkstoffe Härteprüfung nach Vickers Teil 1: Prüfverfahren (ISO 6507-1:2023); Deutsche Fassung EN ISO 6507-1:2023, 2024, Deutsche Norm.
- [25] X.-L. Zheng, S.-X. Li, J.-L. Ma, Q.-Y. Xu, H.-D. Zhao, Z.-Q. Han, Improvement of impact properties of Al-Si-Mg alloy via solution treatment and joint modification with Sr and La, Rare Met. 43 (7) (2024) 3301-3313, http://dx.doi.org/10.1007/ s12598-024-02622-y.
- [26] B. Closset, J.E. Gruzleski, Structure and properties of hypoeutectic Al-Si-Mg alloys modified with pure strontium, Met. Trans. A 13 (6) (1982) 945-951, http://dx.doi.org/10.1007/bf02643389.
- [27] W. Zhang, S. Ma, Z. Wei, P. Bai, The relationship between residual amount of Sr and morphology of eutectic Si phase in A356 alloy, Materials 12 (19) (2019) 3222, http://dx.doi.org/10.3390/ma12193222.
- [28] E. Samuel, A.M. Samuel, H.W. Doty, S. Valtierra, F.H. Samuel, Intermetallic phases in Al-Si based cast alloys: new perspective, Int. J. Cast Met. Res. 27 (2) (2013) 107-114, http://dx.doi.org/10.1179/1743133613y.0000000083.
- [29] L. Liu, A.M. Samuel, F.H. Samuel, H.W. Doty, S. Valtierra, Role of iron in relation to silicon modification in Sr-treated 319 and 356 alloys, Int. J. Cast Met. Res. 16 (4) (2003) 397-408, http://dx.doi.org/10.1080/13640461.2003.11819616.
- [30] S. Nafisi, R. Ghomashchi, Effects of modification during conventional and semi- solid metal processing of A356 Al-Si alloy, Mater. Sci. Eng.: A 415 (1-2) (2006) 273-285, http://dx.doi.org/10.1016/j.msea.2005.09.108.
- [31] G. Timelli, A. Fabrizi, The effects of microstructure heterogeneities and casting defects on the mechanical properties of high-pressure die-cast AlSi9Cu3(Fe) alloys, Met. Mater. Trans. A 45 (12) (2014) 5486-5498, http://dx.doi.org/10. 1007/s11661-014-2515-7.
- [32] Z. Li, A.M. Samuel, F.H. Samuel, C. Ravindran, S. Valtierra, Effect of alloying elements on the segregation and dissolution of CuAl2 phase in Al-Si-Cu 319 alloys, J. Mater. Sci. 38 (6) (2003) 1203-1218, http://dx.doi.org/10.1023/a: 1022857703995.
- [33] M. Wang, W. Xu, Q. Han, Study of refinement and morphology change of AlFeSi phase in A380 alloy due to addition of Ca, Sr/ Ca, Mn and Mn, Sr, Mater. Trans. 57 (9) (2016) 1509-1513, http://dx.doi.org/10.2320/matertrans.m2015329.
- [34] Q. Li, J. Wang, C. Xue, Y. Miao, Q. Hou, X. Yang, Y. Meng, Z. Yang, G. Tian, H. Su, X. Li, Effects of Sr on Fe-rich intermetallics in recycled Al-Si-Cu alloys, J. Mater. Sci. 59 (25) (2024) 11572-11595, http://dx.doi.org/10.1007/s10853- 024-09854-4.
- [35] A. Fortini, L. Lattanzi, M. Merlin, G.L. Garagnani, Comprehensive evaluation of modification level assessment in Sr-modified aluminium alloys, Int. J. Met. 12 (4) (2017) 697-711, http://dx.doi.org/10.1007/s40962-017-0202-3.
- [36] H. Liao, Y. Sun, G. Sun, Correlation between mechanical properties and amount of dendritic a-Al phase in as-cast near-eutectic Al-11.6 strontium, Mater. Sci. Eng.: A 335 (1-2) (2002) 62-66, http://dx.doi.org/10.1016/s0921-5093(01) 01949-9.
- [37] L. Liu, A.M. Samuel, F.H. Samuel, H.W. Doty, S. Valtierra, Characteristics of a- dendritic and eutectic structures in Sr-treated Al-Si casting alloys, J. Mater. Sci. 39 (1) (2004) 215-224, http://dx.doi.org/10.1023/b:jmsc.0000007747.43275. 34.
- [38] M.D. Hanna, S.-Z. Lu, A. Hellawell, Modification in the aluminum silicon system, Met. Trans. A 15 (3) (1984) 459-469, http://dx.doi.org/10.1007/bf02644969.
- [39] A.P. Hekimoğlu, M. Çalış, G. Ayata, Effect of strontium and magnesium additions on the microstructure and mechanical properties of Al-12Si alloys, Met. Mater. Int. 25 (6) (2019) 1488-1499, http://dx.doi.org/10.1007/s12540-019-00429-6.
9. Copyright:
- This material is a paper by "Felix Feyer, Michael Weigand, Peter Randelzhofer, Carolin Körner": Based on "Increasing the conductivity of aluminium high-pressure die casting alloy AlSi9Cu3Fe (226D) by Sr modification of eutectic and intermetallic phases".
- Source of paper: https://doi.org/10.1016/j.mseb.2025.118109
This material was created to introduce the above paper, and unauthorized use for commercial purposes is prohibited. Copyright © 2025 CASTMAN. All rights reserved.