This article introduces the paper ['ALLOY 718 AT PRATT & WHITNEY-HISTORICAL PERSPECTIVE AND FUTURE CHALLENGES'] published by ['TMS (The Minerals, Metals & Materials Society)'].
1. Overview:
- Title: ALLOY 718 AT PRATT & WHITNEY-HISTORICAL PERSPECTIVE AND FUTURE CHALLENGES
- Author: Daniel F. Paulonis and John J. Schirra
- Publication Year: 2001
- Publishing Journal/Academic Society: TMS (The Minerals, Metals & Materials Society)
- Keywords: Alloy 718, gas turbine engine, nickel alloys, superalloy, material development, process optimization, casting, wrought, mechanical properties, microstructure, applications, Pratt & Whitney
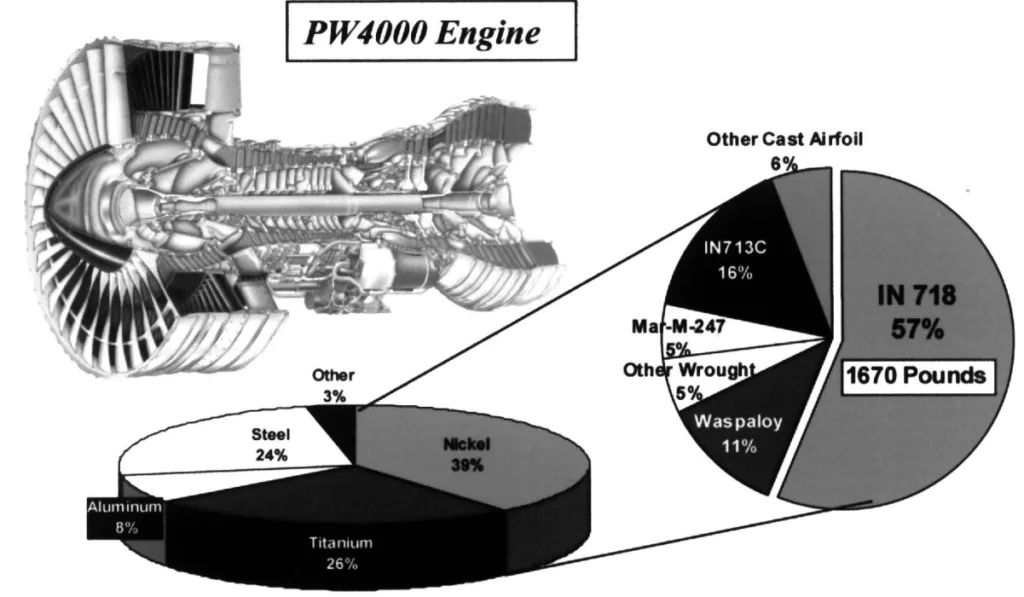
2. Abstracts or Introduction
The introduction of Alloy 718 at Pratt & Whitney (P&W) in the early 1960's marked a significant advancement in gas turbine engine technology. This innovation facilitated the production of engines with reduced cost, lighter weight, and simplified construction. This paper outlines the applications and evolution of Alloy 718 over four decades at P&W, including the rationale for its adoption. Initially utilized in 1963 for the diffuser case of the J58 engine in the SR-71 Blackbird, Alloy 718 has become the most extensively used nickel alloy at P&W. Its applications span various engine components such as disks, cases, shafts, blades, stators, seals, supports, tubes, and fasteners. The paper also details key studies undertaken by P&W to enhance the understanding, properties, uniformity, and quality of Alloy 718. Despite these advancements, challenges persist in fully exploiting the alloy system in the 21st century. Notable needs include improved process models for tailoring properties to specific applications and the development of a higher temperature derivative of Alloy 718. The desired alloy would maintain the advantages of Alloy 718 in terms of property, cost, and fabricability, while exhibiting enhanced resistance to overaging to enable a 50-100F (28-56C) increase in service temperature.
3. Research Background:
Background of the Research Topic:
Alloy 718 is identified as the most widely used nickel alloy at P&W, constituting over 50% of the superalloy content in certain engines. Its introduction by INCO (H. Eiselstein's / INCO's gift) revolutionized gas turbine engine design by enabling engines with lower cost, reduced weight, and simplified construction. Furthermore, Alloy 718 provided increased design flexibility and its complex behavior has been a fertile area for materials engineering advancements. The unique combination of properties, processability in both wrought and cast forms, and weldability positioned Alloy 718 as a prime material for gas turbine applications.
Status of Existing Research:
Following INCO's announcement of IN718 in 1959, P&W recognized its attributes and began issuing specifications and selecting it for critical applications. Initial uses were in military engines (J58, TF30, and F100), expanding to commercial engines (JT9D, PW2000, and PW4000) from the late 1960s through the 1980s. P&W collaborated with the supply base to improve material quality and capability, focusing on process optimization for grain refinement and defect reduction. Later applications included critical components in the Space Shuttle Main Engine (SSME). Key milestones in Alloy 718 incorporation at P&W are illustrated in "Figure 1. Key specification and application milestones related to the incorporation of Alloy 718 at P&W."
Necessity of the Research:
The paper emphasizes the critical need for Alloy 718 to support P&W's initial application: a complex welded diffuser case structure for the JT11 (J58) engine for the SR-71 Blackbird aircraft. Waspaloy, initially used for the diffuser case, suffered from strain-age cracking in welds. Switching to Alloy 718 resolved this issue, demonstrating its superior weldability and initiating its broader application within P&W. Early Alloy 718 material exhibited limitations in uniformity and was prone to notch sensitivity. Research was needed to refine specifications and processing to fully realize the potential of Alloy 718 in demanding aerospace applications.
4. Research Purpose and Research Questions:
Research Purpose:
The primary purpose of the research, as presented in this paper, is to document the historical journey of Alloy 718 at Pratt & Whitney, from its initial adoption to its widespread use in gas turbine engines and beyond. It aims to trace the evolution of its applications, the improvements in material understanding and processing, and the ongoing challenges and future directions for this critical superalloy. The paper serves to provide a comprehensive overview of P&W's experience with Alloy 718, highlighting key milestones, technical advancements, and lessons learned over four decades.
Key Research:
The key research areas explored in this paper revolve around:
- Understanding Alloy 718's Metallurgy and Properties: Investigating the strengthening mechanisms, particularly the role of γ" phase, and addressing issues like notch sensitivity and overaging.
- Process Optimization: Improving manufacturing processes for both wrought and cast Alloy 718 components, including melting, billet conversion, forging, casting, and heat treatment, to enhance material quality, uniformity, and reduce defects.
- Expanding Applications: Extending the use of Alloy 718 to increasingly critical and complex engine components, from diffuser cases and turbine exhaust cases to disks, shafts, and SSME turbopump parts.
- Cost Reduction and Performance Enhancement: Driving cost savings through the substitution of wrought assemblies with single-piece castings and improving alloy properties to meet demanding performance requirements in advanced gas turbine engines.
- Addressing Future Challenges: Identifying and proposing solutions for the limitations of Alloy 718, particularly its temperature capability and time-dependent fracture behavior, to ensure its continued relevance in future engine designs.
Research Hypotheses:
While the paper is historical and descriptive, not hypothesis-driven research, some implicit hypotheses can be identified:
- Alloy 718's unique property balance, weldability, and fabricability make it a superior material for gas turbine engine components compared to existing alloys. This is supported by its rapid adoption and expanding applications at P&W.
- Process optimization and improved understanding of Alloy 718's metallurgy can significantly enhance its properties, uniformity, and reduce manufacturing costs. This is evidenced by the various process improvements and specification refinements detailed in the paper.
- Cast Alloy 718, especially with HIP, can achieve properties approaching those of wrought Alloy 718, offering significant cost advantages. This is demonstrated by the successful implementation of cast + HIP Alloy 718 in critical structural components.
- Further development of Alloy 718 or its derivatives is necessary to meet the increasing demands of future gas turbine engines, particularly for higher temperature capability and improved durability. This is highlighted in the "Future Challenges" section of the paper.
5. Research Methodology
Research Design:
This paper employs a historical case study approach, documenting the experience of Pratt & Whitney with Alloy 718 over four decades. It is descriptive and analytical, tracing the chronological progression of Alloy 718's adoption, development, and application within the company. The design is structured around key milestones, technological advancements, and challenges encountered, providing a comprehensive overview of Alloy 718's evolution at P&W.
Data Collection Method:
The data presented in this paper are primarily drawn from Pratt & Whitney's internal records, specifications (e.g., PWA1010, PWA649, PWA1469, PWA1472), and accumulated knowledge from decades of research, development, and manufacturing experience with Alloy 718. The authors, being long-term employees of P&W, rely on their direct involvement and access to company archives and technical data. The paper also references external publications and conferences to contextualize P&W's work within the broader materials science and engineering community.
Analysis Method:
The analysis is qualitative and historical, focusing on describing trends, identifying key factors influencing Alloy 718's success, and explaining the underlying metallurgical and engineering principles. The paper analyzes the impact of process improvements (e.g., HIP, refined melting techniques), compositional modifications (e.g., PWA1472), and heat treatment optimizations on the properties and applications of Alloy 718. Data is presented in the form of historical accounts, descriptions of applications, and comparative assessments of different processing techniques and alloy versions. "Figure 10. Modified age results in improved tensile and rupture properties in Cast + HIP Alloy 718." visually represents the impact of heat treatment optimization. "Figure 13. Factors affecting the machinability of Alloy 718." and "Figure 14. Overview of material usage in the PW4000 engine." provide data on machinability and material usage respectively.
Research Subjects and Scope:
The primary research subject is Alloy 718 and its application within Pratt & Whitney gas turbine engines. The scope is limited to the historical experience of P&W, focusing on both wrought and cast forms of Alloy 718. The paper covers a wide range of applications, from early military engines to commercial engines and space applications (SSME). It examines the material from its initial introduction in the 1960s up to the time of publication in 2001, with a forward-looking perspective on future challenges and opportunities for Alloy 718.
6. Main Research Results:
Key Research Results:
- Early Success and Broad Application: Alloy 718 was successfully implemented at P&W starting in the early 1960s, initially for the J58 diffuser case, and rapidly expanded to numerous applications across military and commercial gas turbine engines due to its unique combination of properties, weldability, and fabricability.
- Process and Specification Development: P&W played a crucial role in developing specifications (PWA1010, PWA649, PWA1469, PWA1472) and optimizing processing techniques for both wrought and cast Alloy 718, leading to improved material quality, uniformity, and performance. Key developments included fine grain disk specification (PWA1085), Cast + HIP specification (PWA1469), and High Strength 718 specification (PWA1472).
- Understanding Strengthening Mechanisms: Research at P&W in the late 1960s identified γ" as the primary strengthening phase in Alloy 718 through dark field transmission microscopy, as shown in "Figure 4. Dark field transmission micrographs showing three variants of y" and a bright field image showing high coherency strains".
- Cast Alloy 718 Advancements: P&W successfully developed and implemented cast Alloy 718, particularly with HIP, for complex structural components, achieving cost savings and properties approaching those of wrought material. "Figure 3. First large Alloy 718 structural casting at P&W…. TF30 Turbine Exhaust Case. One casting replaced assembly of 38 parts." illustrates the replacement of wrought assemblies with castings.
- High Strength Alloy 718 (PWA1472): A higher strength version of cast Alloy 718 (PWA1472) was developed by modifying chemistry (increased Ti and Nb, reduced Cr), offering a 25% increase in yield strength and creep-rupture properties.
- SSME Applications: Alloy 718 was successfully applied to critical components in the Space Shuttle Main Engine (SSME) turbopumps, leveraging its high strength, weldability, and cryogenic properties. "Figure 12. Alloy 718 components used in P&W's Space Shuttle Main Engine." shows examples of these components.
- Machinability Characterization: P&W and United Technologies Research Center conducted studies to understand factors influencing the machinability of Alloy 718, identifying hardness, grain size, and carbon content as key parameters. "Figure 13. Factors affecting the machinability of Alloy 718." summarizes these findings.
- Dominant Material Usage: Alloy 718 became the most widely used nickel alloy at P&W, accounting for over 40% of all nickel alloy purchases and 57% of the nickel alloy weight in the PW4000 engine, as depicted in "Figure 14. Overview of material usage in the PW4000 engine.".
Analysis of presented data:
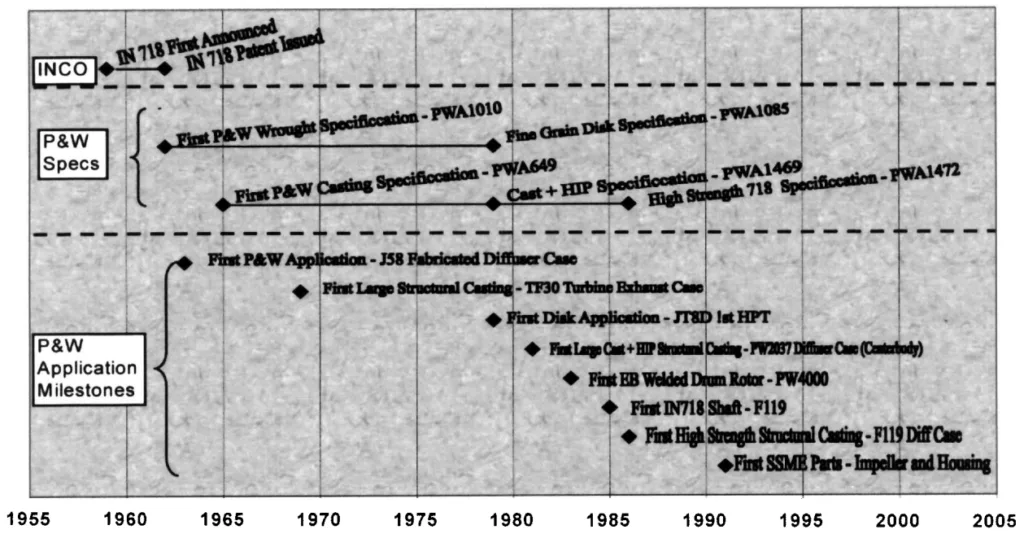
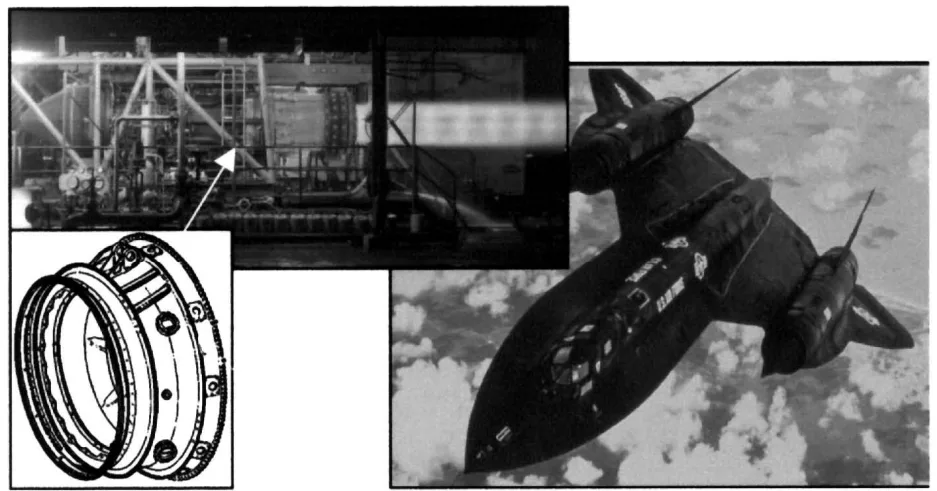
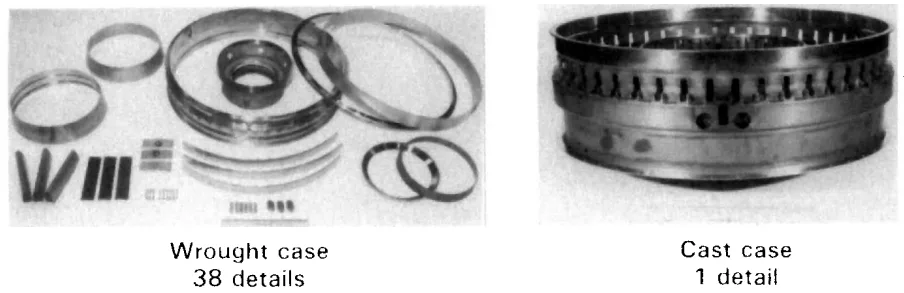
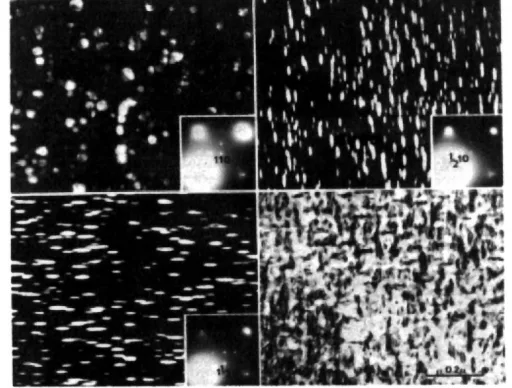
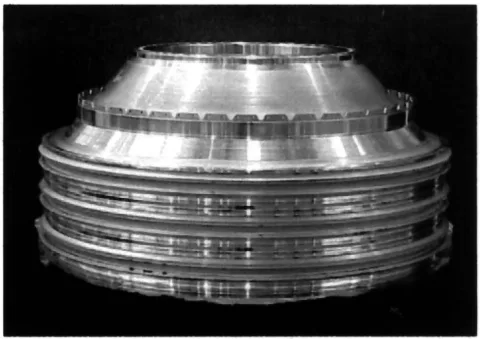
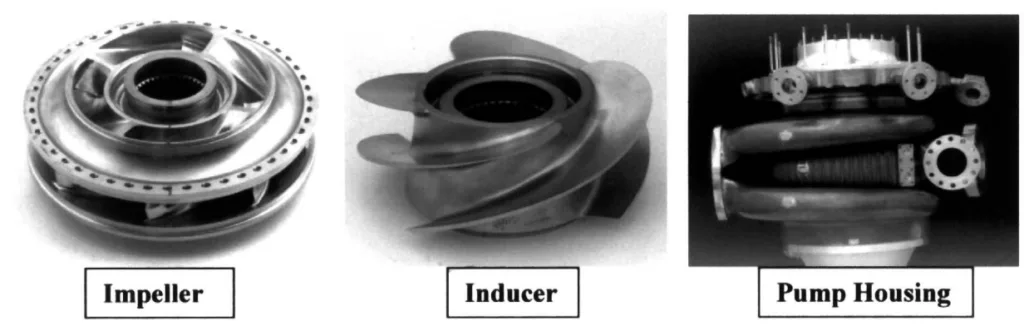
- Figure 1: Chronologically maps key specification and application milestones, demonstrating the progressive integration of Alloy 718 into P&W engines from the 1960s to 2000s.
- Figure 2: Illustrates the first critical application of Alloy 718 in the J58 diffuser case, highlighting its role in solving strain-age cracking issues experienced with Waspaloy.
- Figure 3: Visually compares a wrought case assembly with a single-piece cast Alloy 718 turbine exhaust case, emphasizing the cost and complexity reduction achieved through casting.
- Figure 4: Presents dark field transmission micrographs confirming γ" as the primary strengthening phase in Alloy 718, contributing to the understanding of its exceptional strength.
- Figure 5: Shows a PW4000 3-stage EB Welded Drum Rotor made of Alloy 718, demonstrating its application in large, critical rotating components.
- Figure 6: Depicts a one-piece cast stator/case component for the TF30 engine, showcasing the increasing complexity and size of cast Alloy 718 parts.
- Figure 7: Graphically illustrates the effect of HIP temperature on LCF life, justifying the selection of 2175F (1191C) for HIP processing of Alloy 718 castings.
- Figure 8: Shows a PW4000 one-piece cast + HIP Diffuser Case, representing a large and complex structural casting made possible by HIP technology.
- Figure 9: Micrograph showing Laves phase segregation in large castings, highlighting a challenge addressed through process control and pre-HIP homogenization.
- Figure 10: Bar chart comparing the properties of standard age and optimized age Cast + HIP Alloy 718, demonstrating the improvement in tensile and rupture properties through heat treatment optimization.
- Figure 11: Photograph of the Space Shuttle Main Engine, contextualizing the application of Alloy 718 in SSME turbopumps.
- Figure 12: Photographs of Alloy 718 components used in SSME, including Impeller, Inducer, and Pump Housing, showcasing diverse applications in extreme environments.
- Figure 13: Graph plotting Machinability Rating (%) against Hardness (Rc) for different forms of Alloy 718 and Inconel 718, illustrating the factors affecting machinability.
- Figure 14: Pie chart showing the material usage breakdown in the PW4000 engine, emphasizing the dominant proportion of Alloy 718.
Figure Name List:
- Figure 1. Key specification and application milestones related to the incorporation of Alloy 718 at P&W.
- Figure 2. First critical application of Alloy 718 at Pratt & Whitney… welded diffuser case in the J58 engine for the SR-71 Blackbird.
- Figure 3. First large Alloy 718 structural casting at P&W…. TF30 Turbine Exhaust Case. One casting replaced assembly of 38 parts.
- Figure 4. Dark field transmission micrographs showing three variants of y" and a bright field image showing high coherency strains
- Figure 5. PW4000 3-stage EB Welded Drum Rotor
- Figure 6. First one-piece cast stator/case component for TF30
- Figure 7. Effect of HIP temperature on LCF life
- Figure 8. PW4000 one-piece cast + HIP Diffuser Case
- Figure 9. Laves phase due to segregation in large castings.
- Figure 10. Modified age results in improved tensile and rupture properties in Cast + HIP Alloy 718.
- Figure 11. Space Shuttle Main Engine
- Figure 12. Alloy 718 components used in P&W's Space Shuttle Main Engine.
- Figure 13. Factors affecting the machinability of Alloy 718.
- Figure 14. Overview of material usage in the PW4000 engine.
7. Conclusion:
Summary of Key Findings:
Alloy 718 has been instrumental in the advancement of gas turbine engine technology at Pratt & Whitney over the past four decades. Its introduction enabled the manufacturing of more cost-effective, lighter, and simpler engines. Through continuous research and development, P&W has expanded the applications of Alloy 718, improved its properties and processing, and addressed manufacturing challenges. Key achievements include the development of cast + HIP Alloy 718 for complex structural components, optimization of heat treatments, and creation of higher strength variants. Alloy 718 has become the dominant nickel alloy at P&W, demonstrating its versatility and reliability in diverse and demanding applications, including the Space Shuttle Main Engine.
Academic Significance of the Study:
This historical review provides valuable insights into the evolution of a critical superalloy and its impact on aerospace engineering. It highlights the importance of understanding material metallurgy, optimizing manufacturing processes, and continuous innovation in materials science. The paper contributes to the academic knowledge base by documenting a successful case study of alloy development and application over an extended period, offering lessons in materials engineering, process optimization, and industry-academia collaboration. The detailed account of the identification of γ" as the primary strengthening phase and the subsequent process developments are of particular academic interest.
Practical Implications:
The practical implications of this study are significant for the die casting and aerospace industries. The paper demonstrates the feasibility and benefits of using Alloy 718 in both wrought and cast forms for a wide range of critical engine components. It underscores the importance of process control, especially HIP and heat treatment, in achieving desired material properties and component performance. The experience of P&W provides a roadmap for other manufacturers looking to adopt and optimize Alloy 718 or similar superalloys in demanding applications. The machinability study offers practical guidelines for machining Alloy 718 components efficiently.
Limitations of the Study and Areas for Future Research:
This paper is primarily a historical overview and does not delve into the detailed experimental data or quantitative analysis of material properties. It is limited to the perspective of Pratt & Whitney and may not fully represent the broader industry experience with Alloy 718. The paper identifies future challenges for Alloy 718, particularly the need for higher temperature capability and improved time-dependent fracture behavior. Areas for future research include:
- Developing higher temperature derivatives of Alloy 718 that retain its desirable properties while offering improved overaging resistance and service temperature capability.
- Further investigation into process models to tailor Alloy 718 properties for specific applications.
- Continued research into improving the creep and oxidation resistance of Alloy 718 at elevated temperatures.
- Exploring new processing technologies like powder injection molding and vacuum die casting for cost-effective manufacturing of complex Alloy 718 components.
- Addressing the limitations of Alloy 718 in terms of environmentally assisted crack growth and dwell sensitivity at higher temperatures.
8. References:
- 1. H. L. Eiselstein, “Metallurgy of Columbium-Hardened Nickel-Chromium-Iron Alloy,” Advances in the Technology of Stainless Steel and Related Alloys, ASTM STP No. 369, 62-77, 1965.
- 2. D. F. Paulonis, J. M. Oblak, and D. S. Duvall, "Precipitation in Nickel-Base Alloy 718," Trans. ASM, 62 (1969), 611-622.
- 3. J. M. Oblak, D. F. Paulonis and D. S. Duvall, “Coherency Strengthening in Ni Base Alloys Hardened by DO22 Y" Precipitates," Met Transactions, 3 (1974), 143-153.
- 4. R. W. Hatala, "Alloy 718 Castings in Gas Turbine Engines: An Overview," (Paper presented at the 1st International Conference on the Metallurgy and Applications of Superalloy 718, Pittsburgh, PA, June 1989)
- 5. R. P. Jewett and J. A. Halchak, "The Use of Alloy 718 in the Space Shuttle Main Engine," Superalloys 718, 625, and Various Derivatives, ed. by E. A. Loria, TMS, 1991, 749-760.
- 6. G. K. Bouse, R. A. Dunham and J. Lane, “Mechanical Properties of Fine-Grain Microcast-X® Alloy 718 Investment Castings for SSME, Gas Turbine Engine, and Airframe Components,", Superalloys 718, 625, 706 and Various Derivatives, ed. by E. A. Loria, TMS, 1997, 459-468.
- 7. J. J. Schirra and D. V. Viens, "Metallurgical Factors Influencing the Machinability of Inconel 718," Superalloys 718, 625, 706 and Various Derivatives, ed. by E. A. Loria, TMS, 1994, 827-838.
- 8. E. A. Loria, "Rene 220: In Retrospect and Prospect," Superalloys 718, 625, 706 and Various Derivatives, ed. by E. A. Loria, TMS, 1994, 739-750.
9. Copyright:
- This material is "Daniel F. Paulonis and John J. Schirra"'s paper: Based on "ALLOY 718 AT PRATT & WHITNEY-HISTORICAL PERSPECTIVE AND FUTURE CHALLENGES".
- Paper Source: [https://doi.org/Not available in the paper]
This material was summarized based on the above paper, and unauthorized use for commercial purposes is prohibited.
Copyright © 2025 CASTMAN. All rights reserved.