This article introduces the paper 'DESIGN AND WEIGHT OPTIMIZATION OF OIL PAN BY FE ANALYSIS' published by 'INTERNATIONAL JOURNAL OF RESEARCH IN ADVANCED ENGINEERING TECHNOLOGIES'.
1. Overview:
- Title: DESIGN AND WEIGHT OPTIMIZATION OF OIL PAN BY FE ANALYSIS
- Author: SINGATHI SHARATH KUMAR, P. SUBRAMANYAM
- Publication Year: 2015
- Publishing Journal/Academic Society: INTERNATIONAL JOURNAL OF RESEARCH IN ADVANCED ENGINEERING TECHNOLOGIES
- Keywords: Oil pan, Manufacturing Methods, Cost Analysis, Design, Analysis
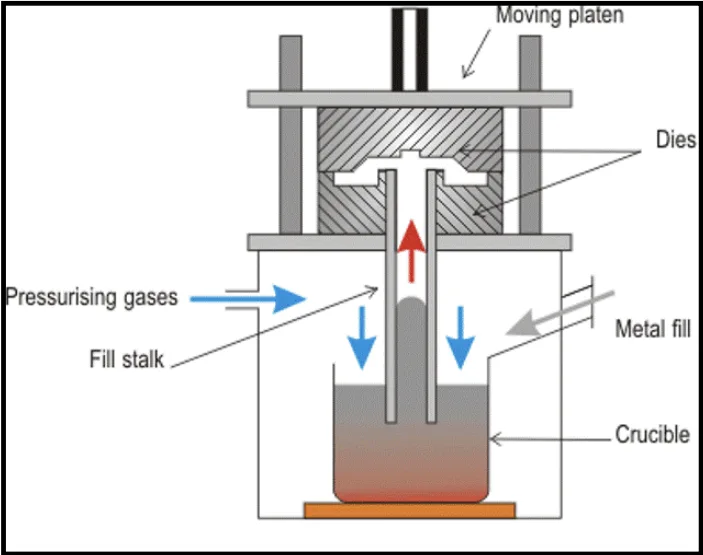
2. Abstracts or Introduction
Abstract- In an internal combustion engine of the reciprocating type the oil pan is the housing of the crankshaft. The enclosure forms the largest cavity in the engine and is located below the cylinder(s) which in a multi cylinder engine are usually integrated in to one or several cylinder blocks. Oil pan is located at the bottom of engine. It is used to store the engine oil. Oil will be pumped to the engine from the oil pan when required.
In this project modeling of oil pan used in submarine engine will be done. The aim of the project is to model Oil pan using CAD software, designing a Casting Tool by selecting a suitable casting manufacturing process and Generate CNC program by using CAM software for the same and reduction of weight will be done at unnecessary areas for casting tool.
Initially data will be collected to design mould tool and for the conditions of analysis. In next stage a model will be generated using pro-engineer for further study. Mould design calculations will be done to model the mould assembly. After mould preparation structural analysis will be conducted by comparing the suitable material selection for oil pan to optimize the die structure for weight reduction. Modeling, tool design and manufacturing (CNC) will be done using pro/engineer software.
INTRODUCTION TO OIL-PAN
An oil pan is a component that typically seals the bottom side of four-stroke, internal combustion engines in automotive and other similar applications. While it is known as an oil pan in the U.S., other parts of the world may call it an oil sump. Its main purpose is to form the bottommost part of the crankcase and to contain the engine oil before and after it has been circulated through the engine. When an oil pan is removed, some components revealed usually include the crankshaft, oil pickup, and the bottom end of the dipstick.
During normal engine operation, an oil pump will draw oil from the pan and circulate it through the engine, where it is used to lubricate all the various components. After the oil has passed through the engine, it is allowed to return to the oil pan. In a wet sump system like this, the amount of oil that an engine can hold is directly related to the size of the oil pan. An engine can hold no more oil than can fit in the pan without reaching the crankshaft, since a submerged crankshaft will tend to aerate the oil, making it difficult or impossible for the oil pump to circulate it through the engine.
The drain plug used to change the engine oil is typically located somewhere on the oil pan. An easy way to locate an oil drain plug is to find the pan and then look for its lowest point. The pan may be slanted, have a bulge on one end, or be at a slight angle due to the position of the engine. This low point is usually where the drain plug is located so that nearly all of the oil in the pan can be drained through it.
Certain engines, such as those in race or high performance cars, may make use of what is known as a dry sump system. Instead of storing all the oil in the crank case, these engines have a divorced reservoir that it is pumped to and from. Oil pans on engines like these will typically be much smaller than those in wet sump systems, since the oil is returned to the reservoir after being used for lubrication.
3. Research Background:
Background of the Research Topic:
In an internal combustion engine of the reciprocating type the oil pan is the housing of the crankshaft. The enclosure forms the largest cavity in the engine and is located below the cylinder(s). Oil pan is located at the bottom of engine and is used to store the engine oil.
Status of Existing Research:
Not explicitly mentioned in this section.
Necessity of the Research:
In this project modeling of oil pan used in submarine engine will be done. The aim of the project is to model Oil pan using CAD software, designing a Casting Tool by selecting a suitable casting manufacturing process and Generate CNC program by using CAM software for the same and reduction of weight will be done at unnecessary areas for casting tool. Initially data will be collected to design mould tool and for the conditions of analysis. In next stage a model will be generated using pro-engineer for further study. Mould design calculations will be done to model the mould assembly. After mould preparation structural analysis will be conducted by comparing the suitable material selection for oil pan to optimize the die structure for weight reduction. Modeling, tool design and manufacturing (CNC) will be done using pro/engineer software.
4. Research Purpose and Research Questions:
Research Purpose:
The aim of the project is to model Oil pan using CAD software, designing a Casting Tool by selecting a suitable casting manufacturing process and Generate CNC program by using CAM software for the same and reduction of weight will be done at unnecessary areas for casting tool. And to optimize the die structure for weight reduction by comparing suitable material selection for oil pan.
Key Research:
- Modeling of oil pan using CAD software (pro-engineer).
- Designing a Casting Tool.
- Selecting a suitable casting manufacturing process.
- Generate CNC program by using CAM software.
- Reduction of weight at unnecessary areas for casting tool.
- Structural analysis by comparing suitable material selection for oil pan to optimize the die structure for weight reduction.
Research Hypotheses:
Not explicitly mentioned in this section. The research is more exploratory and design-focused rather than hypothesis-driven.
5. Research Methodology
Research Design:
The research design involves modeling, design, analysis and optimization using software tools. Initially data will be collected to design mould tool and for the conditions of analysis. In next stage a model will be generated using pro-engineer for further study. Mould design calculations will be done to model the mould assembly. After mould preparation structural analysis will be conducted by comparing the suitable material selection for oil pan to optimize the die structure for weight reduction. Modeling, tool design and manufacturing (CNC) will be done using pro/engineer software.
Data Collection Method:
Initially data will be collected to design mould tool and for the conditions of analysis.
Analysis Method:
Structural analysis will be conducted by comparing the suitable material selection for oil pan to optimize the die structure for weight reduction using FE analysis.
Research Subjects and Scope:
Modeling of oil pan used in submarine engine. Material selection for oil pan. Casting tool design and manufacturing.
6. Main Research Results:
Key Research Results:
- Displacement value for M.S. F26: 0.24694 mm Max
- Strain Value for M.S. F26: 0.0069591 Max
- Von-misses stress value for M.S. F26: 133.38 N/mm²
- Displacement value for Aluminum A360: 0.66136 mm Max
- Strain value for Aluminum A360: 0.0018799 Max
- Von-misses stress value for Aluminum A360: 132.43 N/mm²
- Factor of safety for M.S. F26 is 2.186
- Factor of safety for Aluminum A360 is 2.12
- Difference in cost between existing and modified model: Rs. 2, 82,377/-
- Saving in machining time by using optimized mould: approximately 68 hours.
- Reduction in component cost by using Aluminium: nearly 40%.
Analysis of presented data:
The analysis results show that both Mild Steel F26 and Aluminum A360 are suitable materials based on the factor of safety being greater than 2 for both. However, Aluminum A360 shows a higher displacement but comparable Von-misses stress value to Mild Steel F26. The use of Aluminum A360 can lead to significant cost reduction and weight optimization. The optimized mould design also contributes to cost and time savings in manufacturing.
Figure Name List:
- Fig. 3.4 Principle of Cold Chamber Technologies
- Fig. 5-2 the main parts constituting a classical mould for gravity die-casting
- Selected design for assembly guidelines.
- Selected design for assembly guidelines.
- Gravity die casting
- Die casting processes, as summarized
- Principle of Cold Chamber Technologies
- Drafting for cavity part
- Drafting for Core part
- Drafting for Ejector plate
- Drafting for Retainer plate and pins
- Drafting for Water inlet knob, 25mm Bolts
- Drafting for Guide Pillar, Guide Sleeve
- Drafting for Back plate
- Drafting for Ejector pins
- Drafting for Housing
- Model of Core part
- Model of Retainer plate
- Model of Ejector plate
- Model of Back plate
- Complete Mould Assembly
- Exploded View
- Parting surface for Cavity
- Extracted Core part
- Extracted Cavity part
- CAVITY PREPARATION
- Model of Cavity
- Oil pan with feed system for the preparation of mould
- Parting surface for Core
- Geometry
- Meshing for model
- Displacement value for M.S. F26
- Strain Value 0.0069591 Max for M.S. F26
- Strain value 0.0018799 for Aluminum A360
- Von-misses stress value 133.38 N/mm² for M.S. F26
- Von-misses stress value 132.43 N/mm² for Aluminum A360
- Displacement value for Aluminum A360
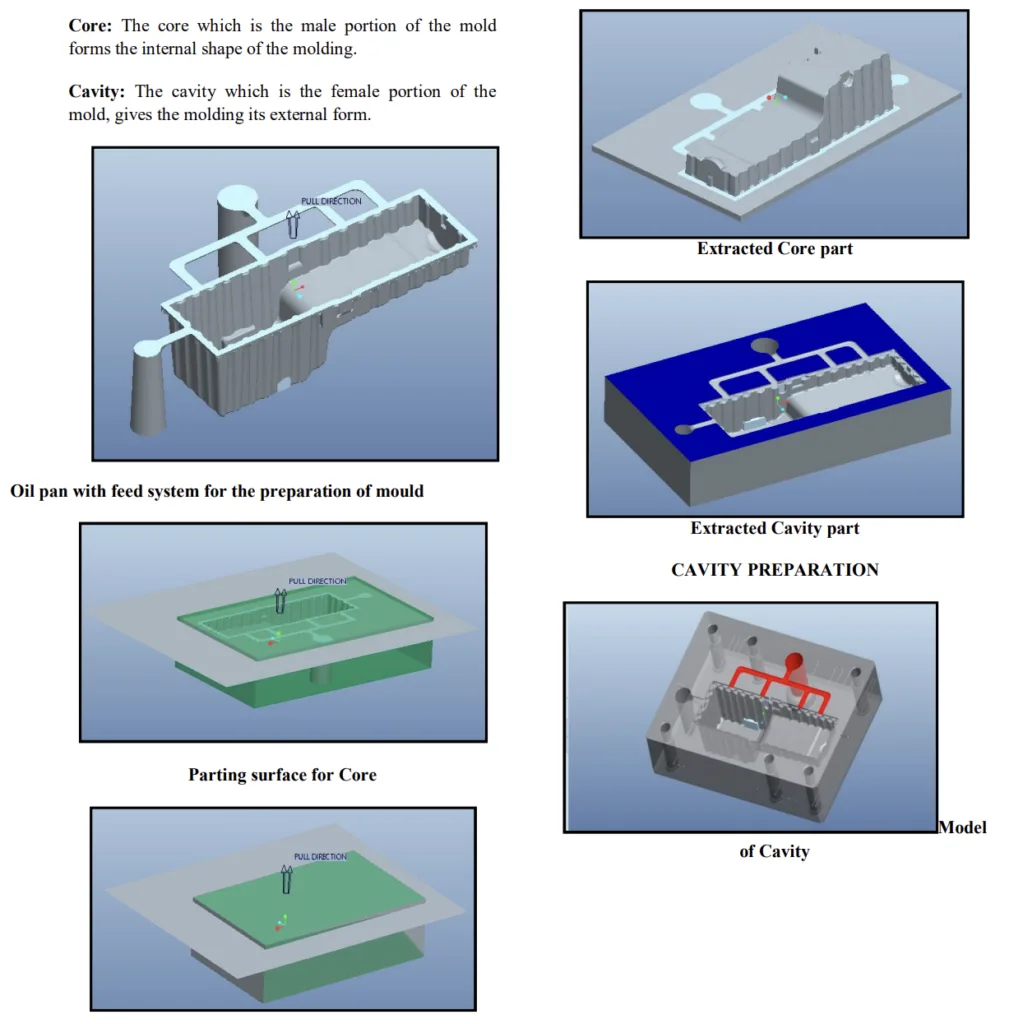
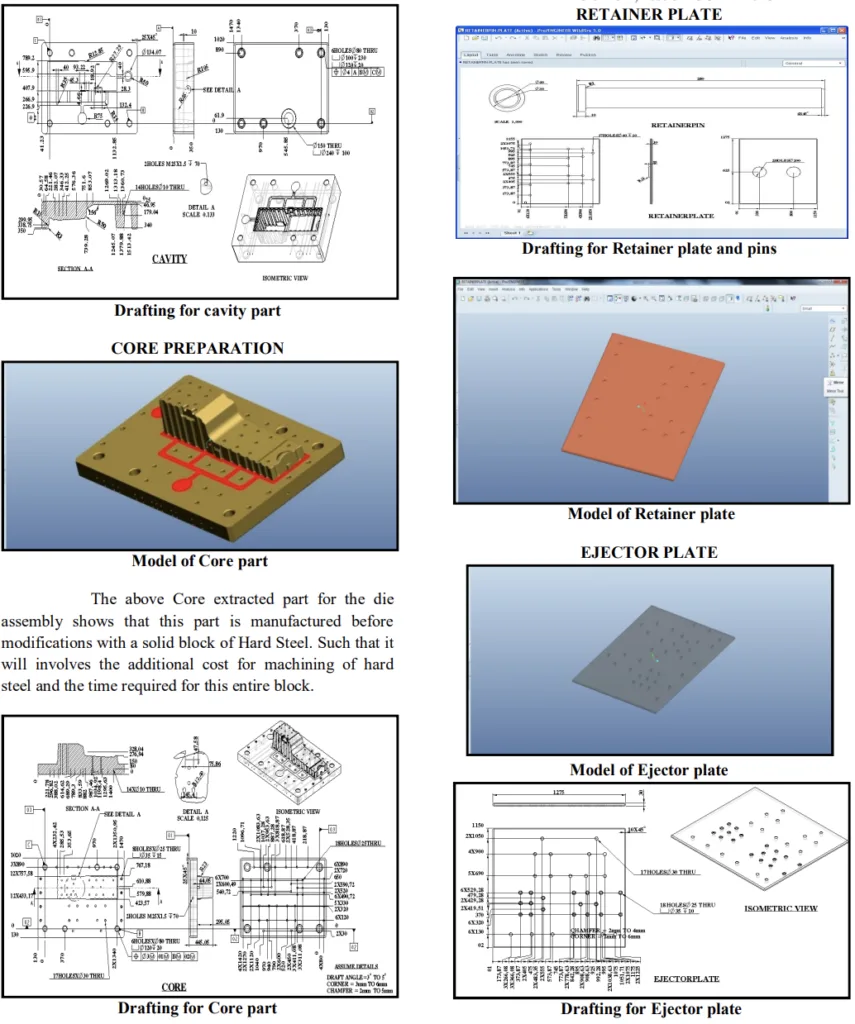
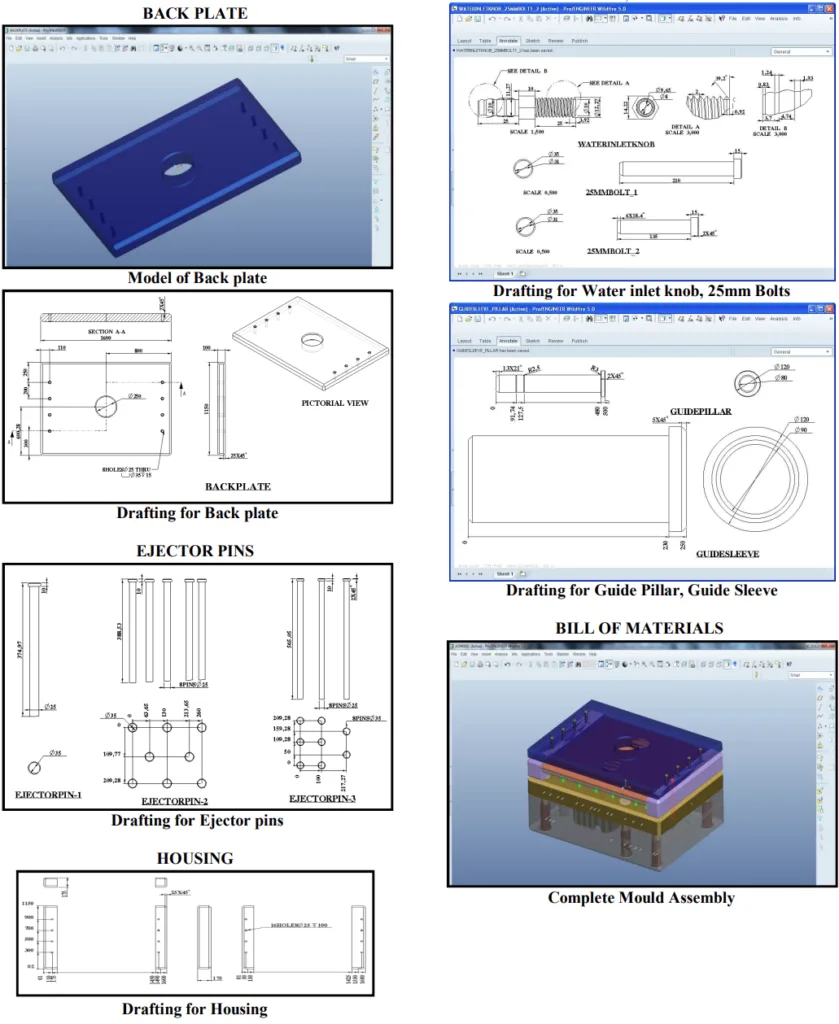
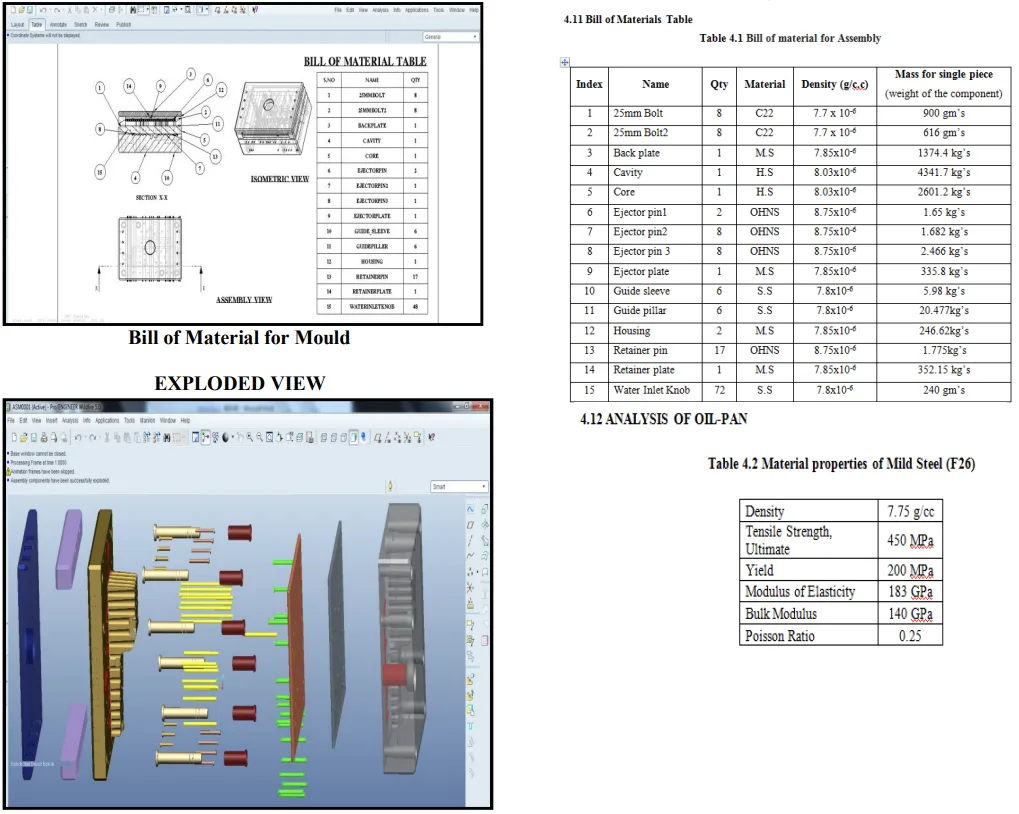
7. Conclusion:
Summary of Key Findings:
This project successfully optimized the design of an oil pan and its die casting mould using FE analysis and design modifications. The study compared Mild Steel F26 and Aluminum A360 as materials, finding Aluminum A360 to be a suitable alternative offering weight and cost advantages while maintaining structural integrity with a factor of safety of 2.12. The optimized mould design, incorporating a split core, reduces material usage, machining time by approximately 68 hours, and overall manufacturing costs by Rs. 2, 82,377/-, with a potential component cost reduction of nearly 40% by using Aluminium.
Academic Significance of the Study:
This study demonstrates the application of FE analysis and optimized design methodologies in die casting for weight and cost reduction. It provides a case study for material selection and mould design optimization in automotive component manufacturing, specifically for oil pans.
Practical Implications:
The findings offer practical guidelines for die casting manufacturers to reduce material costs, machining time, and component weight in oil pan production. The optimized mould design and material selection (Aluminum A360) can be directly implemented to improve manufacturing efficiency and product performance.
Limitations of the Study and Areas for Future Research:
The study is focused on a specific oil pan design for a submarine engine. Further research could explore the generalizability of these optimization techniques to other types of oil pans and die casting components. The analysis could be extended to include thermal analysis and fatigue analysis for a more comprehensive evaluation. Further investigation into different Aluminium alloys and casting parameters could also be beneficial.
8. References:
- [1] Kennedy J, Eberhart RC (1995) "Particle swarm optimization". In: Proceedings of the 1995 IEEE International Conference on Neural Networks (ICNN'95), Perth, Australia, November/December 1995, vol 4, pp 1942-1948
- [2] Jerald J, Asokan P, Prabaharan G, Saravanan R (2005) "Scheduling optimisation of flexible manufacturing systems using particle swarm optimisation algorithm". International Journal Advance Manufacturing Technology 25:964-971
- [3] K. Vidyarthi and M.K. Tiwari “Machine loading problem of FMS: a fuzzy-based heuristic approach", International Journal of Production Research, 2001, 39(5), 953-979
- [4] M. K. Tiwari, B. Hazarika “Heuristic solution approach to the machine loading problem of an FMS and its Petri net model", International Journal of Production Research, 1997, 35(8), 2269-2284
- [5] Swarnkar R, Tiwari MK (2004) Modeling machine loading problem of FMSs and its solution methodology using a hybrid tabu search and simulated annealing-based heuristic approach. Robot Computer-Integrated Manufacturing 20(3):199–209
- [6] Nagarjuna N, Mahesh O, Rajagopal K (2006) A heuristic based on multi-stage programming approach for machine-loading problem in a flexible manufacturing system. Robot Computer-Integrated Manufacturing 22:342-352
- [7] S. G. Ponnambalam and Low Seng Kiat (2008) "Solving Machine Loading Problem in Flexible Manufacturing Systems Using Particle Swarm Optimization" World Academy of Science, Engineering and Technology 39
- [8] Sandhyarani Biswas, S. S. Mahapatra "Machine loading in Flexible manufacturing System: A swarm optimization approach" Eighth Int. Conference on Opers. & Quant. Management, 2007, NITR, 621-628
- [9] Kathryn E. Stecke, (1986), “A hierarchical approach to solving machine grouping and loading problems of FMS'S", European journal of operational research, 24, 369-378
- [10] M. K. Tiwari& N.K. Vidyarthi (2000): Solving machine loading problems in a flexible manufacturing system using a genetic algorithm based heuristic approach, International Journal of Production Research, 38:14, 3357-3384
- [11] Paul S. Andrews, An Investigation into Mutation Operators for Particle Swarm Optimization
- [12] Akhilesh kumar, prakash, MK Tiwari (2006), "Solving machine loading problem of a FMS with constraint based Genetic Algorithm”, European Journal of Operational Research (2006) 1043-1069 175
- [13] Sandhyarani Biswas, S. S. Mahapatra, “Modified particle swarm optimization for solving machine-loading problems in flexible manufacturing systems”. International Journal of Advanced Manufacturing Technology (2008) 39:931-942
9. Copyright:
- This material is "SINGATHI SHARATH KUMAR, P. SUBRAMANYAM"'s paper: Based on "DESIGN AND WEIGHT OPTIMIZATION OF OIL PAN BY FE ANALYSIS".
- Paper Source: https://www.ijraet.com/wp-content/uploads/2024/01/IJRAET_2178.pdf
This material was summarized based on the above paper, and unauthorized use for commercial purposes is prohibited.
Copyright © 2025 CASTMAN. All rights reserved.