This article introduces the paper['Characterization of Mixed Metals Swaged Heat Sinks for Concentrated Heat Source'] published by ['Proceedings of InterPACK’03®'].
1. Overview:
- Title: Characterization of Mixed Metals Swaged Heat Sinks for Concentrated Heat Source
- Author: Ahmed M. Zaghlol, William Leonard and Richard Culham
- Publication Year: 2003
- Publishing Journal/Academic Society: Proceedings of InterPACK’03®: International Electronic Packaging Technical Conference and Exhibition
- Keywords: heat sink, mixed metal, swaged, thermal performance, forced convection, concentrated heat source
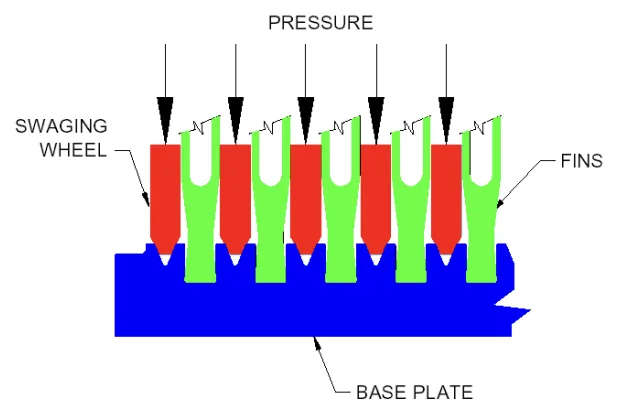
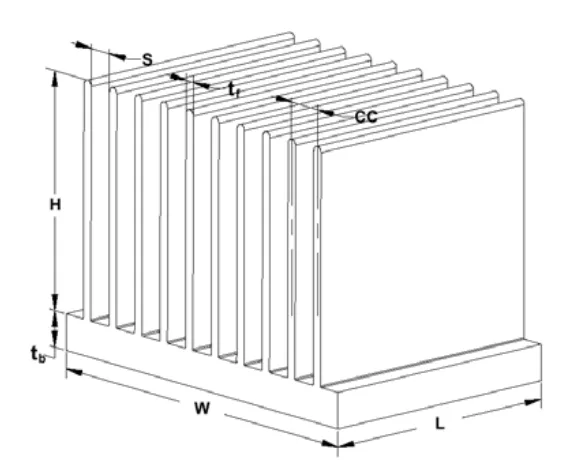
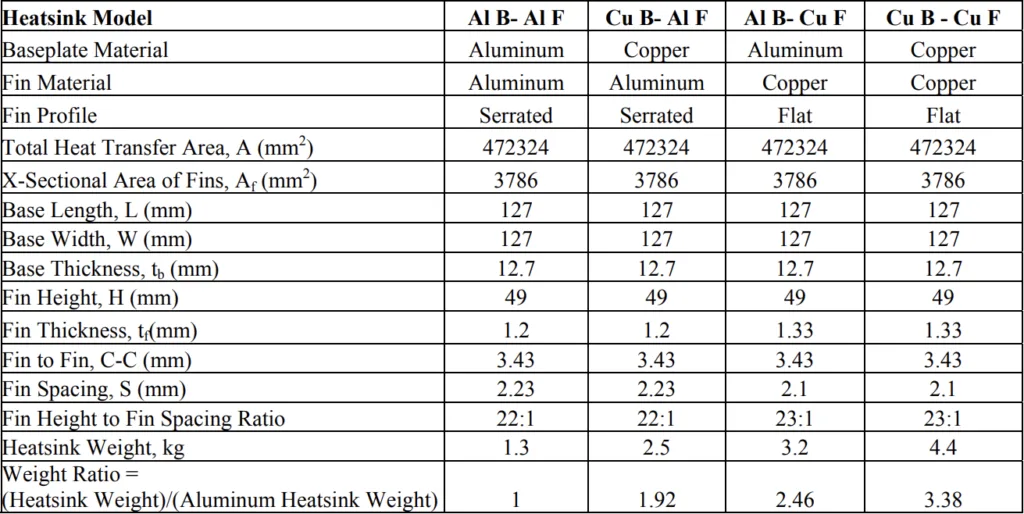
2. Abstracts or Introduction
This research paper presents an experimental investigation into the thermal performance of four distinct heatsink configurations under forced convection conditions. The study compares heatsinks constructed from Aluminum and Copper in various combinations: all Aluminum, all Copper, Copper baseplate with Aluminum fins, and Aluminum baseplate with Copper fins. The objective is to evaluate and contrast the thermal resistance characteristics of these mixed-metal swaged heatsinks when subjected to a concentrated heat source. Experiments were conducted within a vertical wind tunnel, systematically varying the Reynolds number to simulate different airflow velocities and assess the thermal behavior of each heatsink design.
3. Research Background:
Background of the Research Topic:
The escalating demands for enhanced performance in electronic systems are increasingly constrained by issues related to high temperature and effective heat dissipation. Two critical domains where heatsinks are indispensable are microprocessors at the PC board level and within power electronics. The prevailing trend towards miniaturization of electronic packages coupled with increasing power densities leads to a significant rise in heat flux. To mitigate heatsink thermal resistance, design engineers are compelled to utilize materials exhibiting superior thermal conductivity compared to Aluminum, notably Copper. The strategic implementation of metals like Copper in heatsink designs, such as Copper fins on an Aluminum baseplate, Aluminum fins on a Copper baseplate, and all-Copper constructions, is instrumental in enhancing heat spreading capabilities.
Status of Existing Research:
For applications characterized by low power dissipation and modest heat flux, extruded heatsinks are predominantly employed due to their cost-effectiveness. However, the extrusion manufacturing process encounters limitations, particularly in fabricating high aspect ratio fins where the die is prone to breakage as fin thickness and spacing are reduced, as noted by Chu, Belady, and Patel. In scenarios involving high power dissipation and elevated heat flux, bonded heat sinks with high aspect ratios become pertinent. Die-casting emerges as a viable manufacturing alternative for high-volume production, offering a low average cost profile. Nevertheless, it is crucial to acknowledge that die-casting may result in products with increased porosity and reduced alloy purity, consequently diminishing thermal conductivity. In bonded fin heatsinks, the base is typically extruded with slots to facilitate the insertion of plates or extruded fins. The attachment of fins to the baseplate can be achieved through various methods including thermal epoxy, brazing, or "swaging." Thermal epoxy is frequently used for bonding high aspect ratio fins; however, its inherently low thermal conductivity necessitates minimal thickness to reduce thermal impedance. Brazing, a welding subgroup executed above the liquidus temperature of a filler material (450°C) and below the solidus of the base materials, relies on capillary action for filler material distribution within the joints.
Necessity of the Research:
This research focuses on characterizing the thermal performance of heatsinks fabricated using a "swaging" process, a metal displacement bonding technique. The swaging process, as depicted in Figure 1, is a cold forming process suitable for manufacturing high fin density heatsinks. This method ensures robust thermal contact between fins and the base, while also preventing corrosion by sealing grooves from air and moisture, thus enabling anodization. The study aims to experimentally quantify and compare the thermal resistance of different mixed metal configurations produced via swaging, providing valuable insights into optimizing material selection for enhanced heatsink performance.
4. Research Purpose and Research Questions:
Research Purpose:
The primary research purpose is to experimentally evaluate and compare the thermal performance of four distinct heatsink designs under forced convection. These designs are: Aluminum baseplate/Aluminum fin (Al Base-Al Fins), Copper baseplate/Aluminum fin (Cu Base-Al Fins), Aluminum baseplate/Copper fin (Al Base-Cu Fins), and Copper baseplate/Copper fin (Cu Base-Cu Fins). The investigation focuses on understanding how different combinations of baseplate and fin materials, specifically Aluminum and Copper, affect the overall thermal resistance of swaged heatsinks when subjected to a concentrated heat source.
Key Research:
The key research questions addressed in this study are:
- How does the material combination (Aluminum vs. Copper for baseplate and fins) influence the thermal resistance of swaged heatsinks under forced convection?
- What is the percentage reduction in thermal resistance achieved by utilizing mixed metal configurations compared to all-Aluminum heatsinks?
- How does the location of Copper (baseplate vs. fins) in mixed metal heatsinks affect the thermal performance when subjected to a concentrated heat source?
- What are the pressure drop characteristics associated with different heatsink designs as a function of Reynolds number?
Research Hypotheses:
While not explicitly stated as hypotheses, the research is implicitly guided by the expectation that:
- Heatsinks incorporating Copper, due to its higher thermal conductivity, will exhibit lower thermal resistance compared to all-Aluminum heatsinks.
- All-Copper heatsinks will demonstrate the lowest thermal resistance among the tested configurations.
- Mixed metal heatsinks will offer intermediate thermal performance, with the degree of improvement dependent on the strategic placement of Copper in either the baseplate or fins.
- Heatsinks with Copper fins, particularly flat Copper fins, may exhibit higher pressure drop compared to those with Aluminum serrated fins due to differences in fin geometry and thickness.
5. Research Methodology
Research Design:
This study employed an experimental research design utilizing a controlled vertical wind tunnel to investigate the thermal performance of four different heatsink configurations under forced convection. The experimental setup involved testing pairs of identical heatsinks in a back-to-back configuration within the wind tunnel. This arrangement, as shown in Figure 3, aimed to minimize heat losses and ensure accurate measurement of heat dissipation.
Data Collection Method:
Temperature measurements were acquired using 5 mil T-type copper-constantan thermocouples with Teflon coating. Thermocouples were strategically placed at four interior locations (T1-T4 as shown in Figure 5) on each heater plate to measure the base plate temperature. Ambient temperatures were monitored using two thermocouples positioned outside the main flow corridor. Air velocity approaching the heatsink assemblies was measured using a Dantec hot wire anemometer placed upstream. Pressure drop across the heatsinks was measured using two Dwyer differential pressure transducers, with measurements taken upstream and downstream of the heatsink assembly.
Analysis Method:
The primary metric for evaluating thermal performance was thermal resistance (Rθ), calculated using Equation (1):
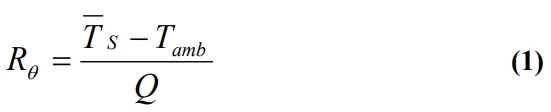
where Ts is the average baseplate temperature, Tamb is the ambient air temperature, and Q is the heat transfer rate. The average baseplate temperature Ts was calculated as the average of four thermocouple readings using Equation (2):
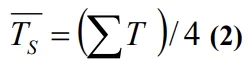
The reduction in thermal resistance for alternative metal heatsinks compared to the all-Aluminum heatsink was quantified using Equation (3):
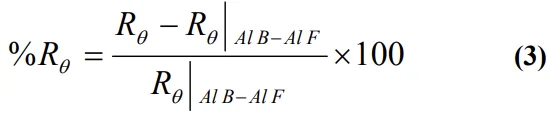
The Reynolds number (Res) for the fin channels' airflow was calculated using Equation (4):
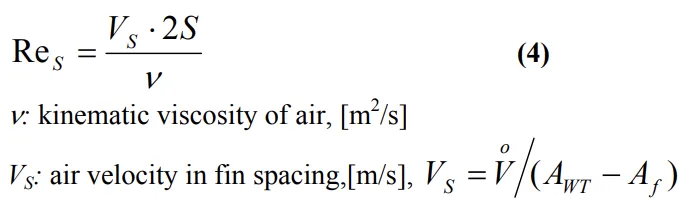
Research Subjects and Scope:
The research subjects were four distinct heatsink designs:
- Aluminum Baseplate/Aluminum Fin (Al B-Al F)
- Copper Baseplate/Aluminum Fin (Cu B-Al F)
- Aluminum Baseplate/Copper Fin (Al B-Cu F)
- Copper Baseplate/Copper Fin (Cu B-Cu F)
All heatsinks shared identical baseplate area, fin height, and fin-center-to-center distance, as detailed in Figure 2 and Table 1. Aluminum fins were serrated and extruded, while Copper fins were flat and sheared from rolled sheets. Experiments were conducted for Reynolds numbers ranging from 1000 to 4000, corresponding to approach velocities of 2 m/s to 8 m/s. The heat source covered 10% of the baseplate surface area.
6. Main Research Results:
Key Research Results:
The experimental results demonstrated significant differences in thermal performance among the tested heatsink configurations. The all Copper heatsink (Cu B-Cu F) exhibited the lowest thermal resistance, achieving a 22% average reduction compared to the all Aluminum heatsink (Al B-Al F). Mixed metal heatsinks showed intermediate performance improvements. Specifically, the Copper-Base/Aluminum-Fin (Cu B-Al F) heatsink improved thermal performance by 11.4% due to the enhanced heat spreading of the Copper baseplate. The Aluminum-Base/Copper-Fin (Al B-Cu F) heatsink showed an 8.5% improvement, attributed to the increased fin efficiency of Copper fins. Pressure drop measurements, shown in Figure 8, indicated that heatsinks with Copper fins (Al Base – Cu Fin & Cu Base-Cu Fin) experienced higher pressure drops compared to those with Aluminum fins.
Analysis of presented data:
Table 2 quantifies the percentage reduction in thermal resistance for each alternative metal heatsink relative to the all-Aluminum heatsink across the tested Reynolds number range. Figure 7 graphically presents the thermal resistance as a function of Reynolds number for all four heatsink types, illustrating the superior performance of the all-Copper design and the intermediate performance of mixed-metal designs. Figure 8 shows the pressure drop characteristics, highlighting the increased pressure drop associated with Copper fin heatsinks. The data indicates that while Copper significantly improves thermal performance, it also increases weight and, in the case of flat fins, pressure drop.
Figure Name List:
- Figure 1: Swaging process
- Figure 2: Heatsink geometry and dimensions
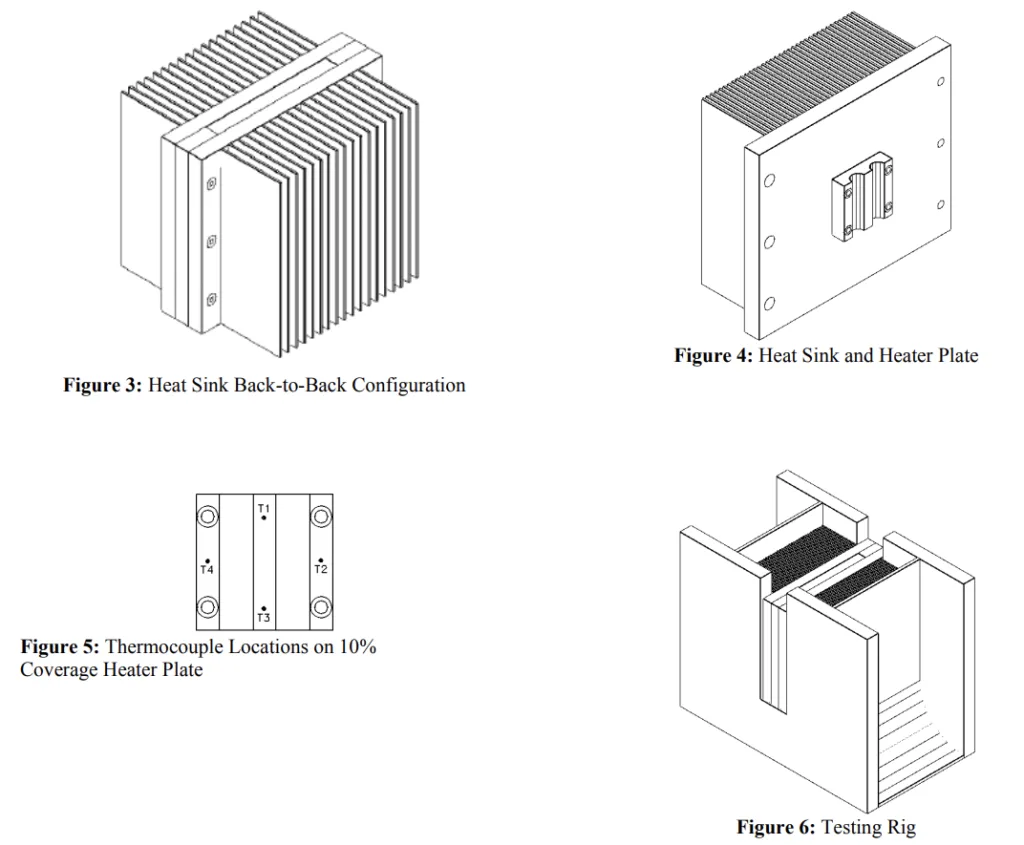
Figure 4: Heat Sink and Heater Plate
Figure 5: Thermocouple Locations on 10% Coverage Heater Plate
Figure 6: Testing Rig
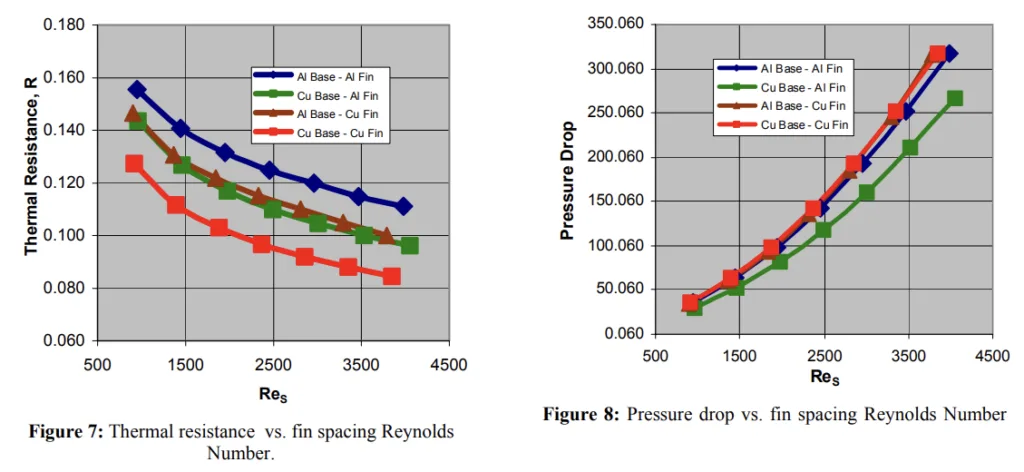
Figure 8: Pressure drop vs. fin spacing Reynolds Number
7. Conclusion:
Summary of Key Findings:
This experimental study conclusively demonstrates the thermal performance advantages of mixed metal swaged heatsinks. The all-Copper heatsink provides the best thermal performance, achieving a 22% reduction in thermal resistance compared to all-Aluminum. Mixed metal designs offer a trade-off between performance and weight. Utilizing a Copper baseplate (Cu B-Al F) is more effective in reducing thermal resistance (11.4% improvement) than using Copper fins on an Aluminum baseplate (Al B-Cu F, 8.5% improvement) for concentrated heat sources covering a small portion (10%) of the baseplate. However, Copper heatsinks are significantly heavier.
Academic Significance of the Study:
This research provides valuable experimental data and comparative analysis of different mixed metal heatsink configurations fabricated using the swaging process. It quantifies the thermal performance benefits of incorporating Copper in heatsink designs, contributing to a deeper understanding of material selection impacts on thermal management in electronic systems. The study highlights the effectiveness of Copper baseplates in enhancing heat spreading and Copper fins in improving fin efficiency under forced convection.
Practical Implications:
The findings offer practical guidance for heatsink designers in selecting appropriate materials and configurations based on performance requirements, weight considerations, and cost constraints. For applications demanding the highest thermal performance, all-Copper heatsinks are optimal, albeit with increased weight. Mixed metal designs, particularly Copper-base/Aluminum-fin heatsinks, provide a compelling balance of improved thermal performance with a less drastic increase in weight. The study also validates the swaging process as a viable manufacturing technique for producing high-performance mixed metal heatsinks.
Limitations of the Study and Areas for Future Research:
This study is limited to forced convection conditions and specific heatsink geometries tested within a controlled wind tunnel environment. The heat source size was fixed at 10% baseplate coverage. Future research could explore a broader range of heatsink geometries, fin designs (e.g., different fin profiles and spacing), and heat source sizes to generalize the findings. Investigating the thermal performance under natural convection and varying airflow conditions would also be beneficial. Further studies could also explore the long-term reliability and cost-effectiveness of swaged mixed metal heatsinks in real-world electronic applications.
8. References:
- H.W. Chu, C.L. Belady and C.D. Patel, “A Survey of High-performance, High Aspect Ratio, Air Cooled Heat Sinks", 1999 International Systems Packaging Symposium, Jan. 11-13, 1999, San Diego, California, USA.
- H. Jonsson and B. Palm, “Influence of Airflow Bypass on the Thermal performance and Pressure Drop of Plate Fin and Pin Fin Heat Sinks for Electronics Cooling", Proceedings of Eurotherm Sem. No. 58, Nantes, France, Sept. 24-26, 1997, pp. 44-50.
- W. Leonard, P. Teertstra, J.R. Culham and A. Zaghlol, "Characterization of Heat Sink Flow Bypass in Plate Fin Heat Sinks", Proceedings of IMECE 2002: International Mechanical Congress and Exposition Nov. 17-22, 2002 New Orleans, Louisiana.
- Robert W. Messler Jr., Joining of Advanced Materials, Stoneham, MA, 1993.
- R-Theta Catalogues.
- Zaghlol, K. Hermann, J. Butler, P. Teertstra, and J.R. Culham, "Forced Convection Heat Transfer for Swaged Mixed Metal Heat sinks," Proceedings of Itherm2002 IEEE Symposium, May 29-June1, 2002, San Diego, California, USA.
- Zaghlol, W. Leonard, and J.R. Culham, “Characterization of Swaged Mixed Metal Heat sinks," to be presented in APEC 2003, Miami Beach, Florida, February 2003.
9. Copyright:
- This material is "Ahmed M. Zaghlol, William Leonard and Richard Culham"'s paper: Based on "Characterization of Mixed Metals Swaged Heat Sinks for Concentrated Heat Source".
- Paper Source: [DOI URL] (DOI URL is not available in the paper, if available, it should be inserted here)
This material was summarized based on the above paper, and unauthorized use for commercial purposes is prohibited.
Copyright © 2025 CASTMAN. All rights reserved.