This article introduces the paper ['Design of die casting process of top cover of automobile generator through numerical simulations and its experimental validation'] presented at the ['International Journal of Cast Metals Research']
1. Overview:
- Title: Design of die casting process of top cover of automobile generator through numerical simulations and its experimental validation
- Author: J.-H. Chen, W.-S. Hwang, C.-H. Wu, and S.-S. Lu
- Publication Year: 2011
- Publishing Journal/Academic Society: International Journal of Cast Metals Research
- Keywords: Die casting, Numerical simulation, Experimental validation
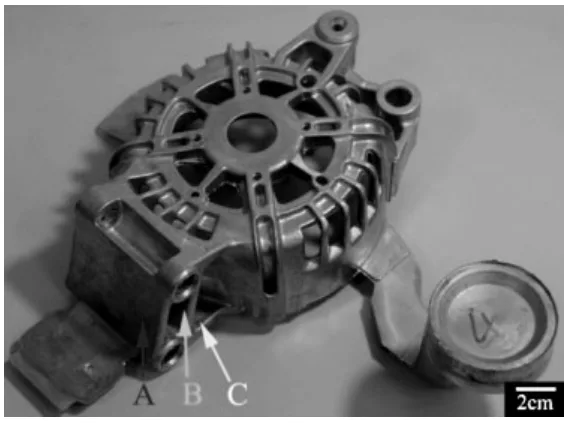
2. Research Background:
Background of the Research Topic:
Aluminium alloys are increasingly favored in various industries, including transportation and precision machining, owing to their advantageous properties such as light weight, excellent electrical and thermal conductivities, high heat and light reflectivity, fine surface finish, and superior corrosion resistance. In particular, their application in lightweight aircraft and automobiles is crucial for reducing CO2 emissions. Die casting stands out as a prominent foundry method for processing aluminium alloys. However, traditional die casting mould design and process parameter settings, reliant on experience and iterative modifications, are time-intensive and costly.
Status of Existing Research:
To mitigate product defect rates, Computer Aided Engineering (CAE) analysis and Computer Aided Design (CAD) techniques are increasingly employed to optimize process conditions and mould design in die casting. Numerical simulation has emerged as a powerful tool for optimizing mould design and enhancing casting quality. While numerous studies underscore the accuracy of numerical simulation, a notable gap exists in deeply investigating the underlying causes of casting defects, often focusing merely on demonstrating simulation accuracy.
Necessity of the Research:
This research is necessitated by the industry's ongoing need to reduce casting defects and improve the efficiency of die casting process design. There is a clear imperative to move beyond mere validation of numerical simulation and to utilize it proactively to diagnose and rectify the root causes of defects in die casting processes.
3. Research Purpose and Research Questions:
Research Purpose:
The primary purpose of this study is to leverage numerical simulation to predict the location and type of defects within an existing die casting mould design for an automobile generator top cover. Furthermore, the research aims to investigate the origins of these defects to facilitate the enhancement of the die casting mould design.
Key Research:
This research focuses on employing numerical simulation to analyze fluid flow and solidification heat transfer phenomena inherent in the die casting process. The simulation results are then validated through experimental die casting. Based on the detailed insights gained from the simulation, the study proposes and evaluates an improved die casting design.
Research Hypotheses:
The central hypotheses of this research are:
- Numerical simulation can accurately predict the occurrence and location of casting defects in the die casting process.
- An improved die casting design, informed by numerical simulation analysis, can effectively reduce or eliminate identified casting defects.
4. Research Methodology
Research Design:
This study adopts a mixed-method approach, combining numerical simulation and experimental validation. The research design involves a comparative analysis of an original single runner system die casting design and an improved double runner system design.
Data Collection Method:
Data collection is achieved through two primary methods:
- Numerical Simulation: Utilizing the software package ADSTEFAN, simulations were conducted to model fluid flow, temperature distribution, and residual gas within the die casting process.
- Experimental Die Casting: Cold chamber die casting was employed to manufacture the top cover of an automobile generator using both the original and improved mould designs. Castings were physically examined to identify and characterize surface defects.
Analysis Method:
The analysis method encompasses:
- Simulation Data Analysis: Analysis of filling time, temperature distribution, and residual gas flow patterns obtained from ADSTEFAN simulations to predict defect locations and types.
- Experimental Data Analysis: Visual inspection of experimental castings to identify and categorize surface defects, correlating these findings with the defect predictions from numerical simulation.
Research Subjects and Scope:
The research subject is the die casting process for manufacturing the top cover of an automobile generator, utilizing aluminium alloy ADC12. The scope of the study is confined to investigating and comparing the performance of a single runner system and a double runner system in this specific die casting application.
5. Main Research Results:
Key Research Results:
The key research results are summarized as follows:
- Defect Identification in Single Runner System: Die casting with the original single runner system resulted in surface defects, including "cold moire" and "filled undesirable" areas, as shown in Fig. 4.
- Numerical Simulation Validation: Numerical simulation using ADSTEFAN successfully predicted the locations and types of defects observed in the experimental castings. Analysis of filling time (Fig. 5), temperature distribution (Fig. 6-9), and residual gas flow (Fig. 10) from the simulation correlated with the experimentally observed defects.
- Improved Design with Double Runner System: An improved die casting design incorporating a double runner system (Fig. 12) was proposed based on simulation insights. This design demonstrated enhanced fluid flow and temperature distribution uniformity.
- Defect Elimination in Improved Design: Experimental validation of the double runner system design resulted in sound castings with no observable surface defects (Fig. 16, 17). The double runner system effectively mitigated the defects observed in the single runner system.
Data Interpretation:
The defects in the single runner system are attributed to asymmetrical cavity filling, non-uniform temperature distribution, and gas entrapment during the die casting process. Specifically, the simulation revealed that the single runner system led to:
- Asymmetrical filling pattern, with thicker sections filling last (Fig. 5).
- Non-uniform temperature distribution, potentially causing premature solidification and "cold moire" defects (Fig. 9).
- Trapped air pockets, leading to air pocket defects (Fig. 10).
- High gate velocity (~128 m/s), increasing die erosion risk (Fig. 11).
The improved double runner system addressed these issues by:
- Promoting more symmetrical cavity filling (Fig. 14).
- Achieving a more uniform temperature distribution (Fig. 15).
- Reducing gate velocity to ~62 m/s (Fig. 13), mitigating die erosion.
Figure Name List:
- Fig. 1 File (STL) of top cover of automobile generator imported into ADSTEFAN software
- Fig. 2 Mesh and position of inflow gate
- Fig. 3 Casting using single runner system
- Fig. 4 Defects on surface of die casting of single runner system
- Fig. 5 Filling time results of die casting of top cover of automobile generator with single runner system
- Fig. 6 Fluid flow results and temperature distribution at filling time of 0.0123 s
- Fig. 7 Fluid flow results and temperature distribution at filling time of 0.0346 s
- Fig. 8 Fluid flow results and temperature distribution at filling time of 0-0708 s
- Fig. 9 Fluid flow results and temperature distribution at filling time of 0.0746 s
- Fig. 10 Gas residual of filling process for die casting of top cover of automobile generator with single runner system
- Fig. 11 Velocity of fluid flow at gate of top cover of automobile generator with single runner system
- Fig. 12 Mesh of double runner system
- Fig. 13 Velocity of fluid flow at gate of top cover of automobile generator with double runner system
- Fig. 14 Filling time results of die casting of top cover of automobile generator with double runner system
- Fig. 15 Temperature distribution of top cover of automobile generator with double runner system at filling time of 0.069 s
- Fig. 16 Casting of double runner system
- Fig. 17 Improved surface defects of die casting of top cover of automobile generator with double runner system
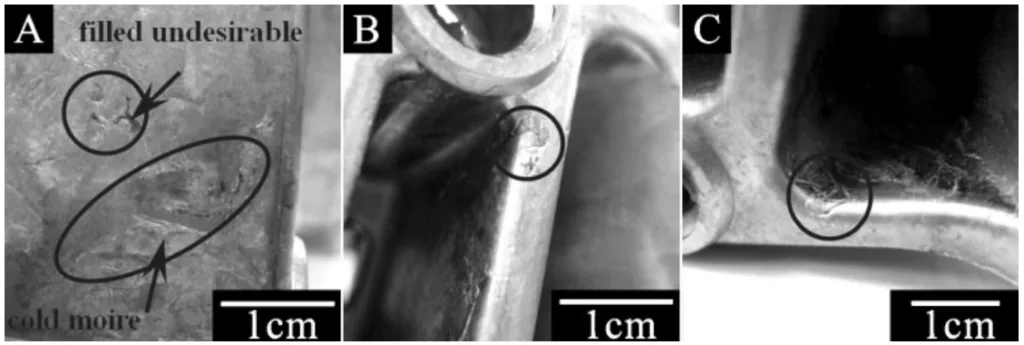
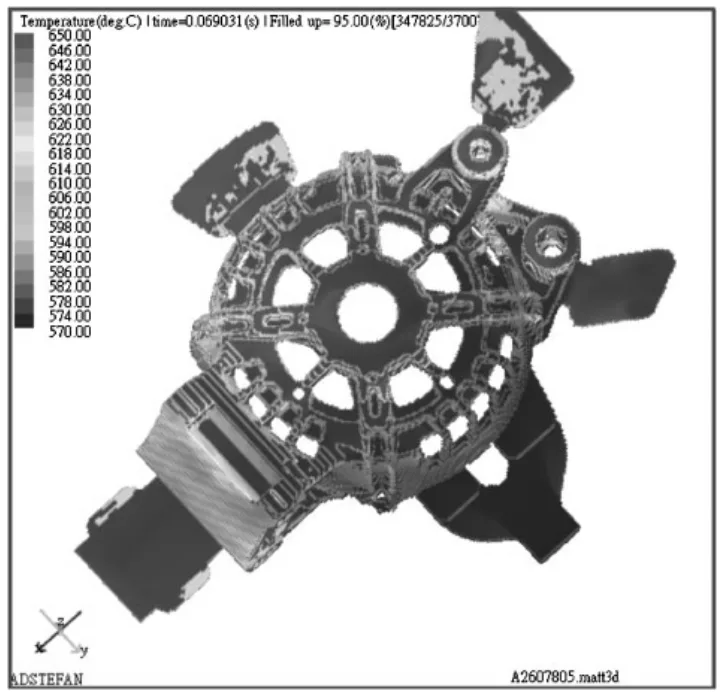
generator with double runner system at filling time of
0,069s
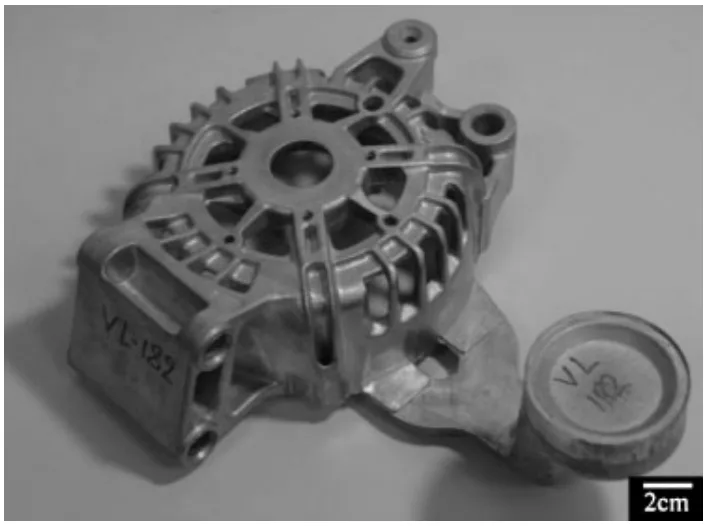
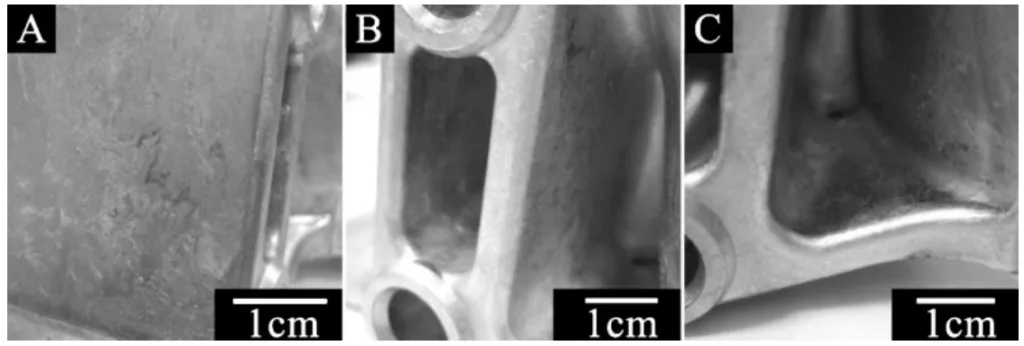
6. Conclusion:
Summary of Main Results:
This study successfully demonstrated the accuracy and reliability of numerical simulation in predicting casting defects in the die casting process. By employing ADSTEFAN software, the research team accurately identified and predicted defects in the single runner system design for an automobile generator top cover. Furthermore, leveraging the insights from numerical simulation, an improved double runner system design was developed and experimentally validated. This improved design effectively eliminated surface defects and enhanced the overall quality of the die casting.
Academic Significance of the Research:
This research contributes to the academic body of knowledge by:
- Validating the application of numerical simulation as a robust tool for predicting and diagnosing defects in die casting processes.
- Highlighting the critical role of runner system design in influencing fluid flow, temperature distribution, and defect formation in die casting.
- Providing a detailed case study demonstrating the effectiveness of numerical simulation-driven design optimization in die casting.
Practical Implications:
The practical implications of this research are significant for the die casting industry:
- It provides a clear methodology for utilizing numerical simulation to optimize die casting designs, reduce defect rates, and improve casting quality.
- The study demonstrates the tangible benefits of transitioning from single runner systems to double runner systems for complex die casting components, particularly in achieving uniform filling and temperature distribution.
- The findings offer valuable guidance for die casting engineers in designing runner systems to minimize defects such as cold moire, filled undesirable areas, and air pockets.
Limitations of the Research
The limitations of this research include:
- The study is focused on a specific component, the top cover of an automobile generator, and a single aluminium alloy, ADC12. The generalizability of the findings to other component geometries and alloy systems requires further investigation.
- The research primarily investigated runner system design. Other process parameters and mould design aspects that could influence casting quality were not extensively explored.
7. Future Follow-up Research:
- Directions for Follow-up Research:
Future research should extend this methodology to a broader range of die casting components and aluminium alloys to validate the wider applicability of numerical simulation-based optimization. Further investigation into the influence of other die casting process parameters, such as injection speed, pressure, and cooling strategies, on casting quality is also warranted. - Areas Requiring Further Exploration:
Areas requiring further exploration include the parametric optimization of double runner system designs to determine optimal runner dimensions and configurations for various casting geometries. Additionally, the long-term effects of reduced gate velocity in double runner systems on die life and maintenance costs should be evaluated.
8. References:
- 1. P. O. Lafsson, R. Sandstro and As. Karlsson: J. Mater. Sci., 1997, 32, (16), 4383-4390.
- 2. A. Kaye: 'Die casting metallurgy', 23-41; 1982, London, Butterworth Scientific.
- 3. M. C. Flemings: 'Solidification processing', 181-183; 1974, New York, McGraw-Hill.
- 4. N. A. El-Mahallawy, M. A. Taha, E. Pokora and F. Klein: J. Mater. Process. Technol., 1998, 73, (1-3), 125-138.
- 5. Y.-B. Jiao and Y.-H. Wei: Mech. Eng. Autom., 2008, 5, 97-100.
- 6. M. T. Rowley (ed.): 'International atlas of casting defects', 46-47; 1979, Des Plaines, IL, American Foundrymen Society.
9. Copyright:
- This material is "J.-H. Chen et al."'s paper: Based on "Design of die casting process of top cover of automobile generator through numerical simulations and its experimental validation".
- Paper Source: DOI 10.1179/136404611X13001912813906
This material was summarized based on the above paper, and unauthorized use for commercial purposes is prohibited.
Copyright © 2025 CASTMAN. All rights reserved.