This introduction paper is based on the paper "Application of wear-resistant PACVD coatings in aluminium diecasting: economical and ecological aspects" published by "Surface and Coatings Technology".
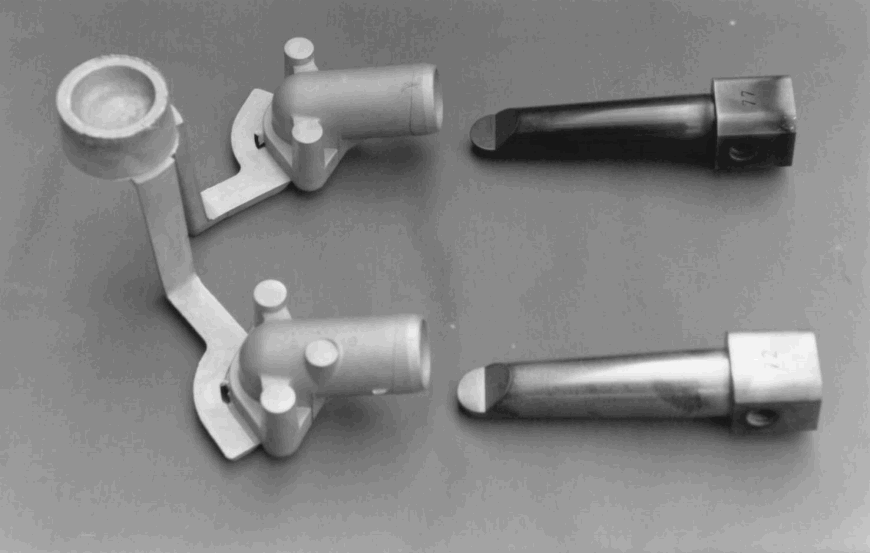
1. Overview:
- Title: Application of wear-resistant PACVD coatings in aluminium diecasting: economical and ecological aspects
- Author: C. Pfohl, A. Gebauer-Teichmann, K.-T. Rie
- Year of publication: 1999
- Journal/academic society of publication: Surface and Coatings Technology
- Keywords: PACVD; Thin films; Aluminium die coating; Coated cores; Minimal lubrication
2. Abstract:
One of the major manufacturing techniques for aluminium precision parts is the pressure diecasting process. However, nowadays the state of the art involves the application of large amounts of lubricants. Their side effects include a decrease in the surface quality of the cast as well as ecological risks. The deposition of wear-resistant coatings provides a means of minimising the use of lubricants while at the same time increasing the lifetime of the diecasting tools. In this study, nitrides, carbides and borides of titanium were synthesized with regard to their composition, structure, hardness, adhesion, wetting behaviour and corrosion resistance to aluminium melt. The coated cores were exposed to diecasting praxis tests under tightened-up conditions, reducing the amount of lubricants. The optimal PACVD coating led to an increase in lifetime by a factor of 300 compared to an uncoated tool. A reduction of 97% of the original amount of lubricants could be achieved.
3. Introduction:
Aluminium pressure diecasting is a common method for producing near-netshape precision parts, but current techniques require significant amounts of die lubricants. These lubricants negatively impact the surface quality of cast parts, lengthen cycle times, decrease job quality, and pose ecological risks due to waste and exhaust disposal. Applying wear-resistant coatings offers a potential solution to minimize lubricant use and extend the service life of diecasting tools. Plasma-assisted chemical vapour deposition (PACVD) is identified as a suitable method due to its ability to coat complex geometries conformally and its deposition temperatures being below the tempering temperatures of typical hot work steels used for diecasting tools. The coatings must endure complex loads like thermal shock, abrasive wear, adhesive wear, and corrosion by liquid aluminium. Titanium nitrides (TiN), carbides (TiC), and borides (TiB2) are established wear protection materials. TiN and TiC can form coherent interfaces for gradient/multilayer designs. TiN offers good thermal stability and low interaction tendency, while TiC provides high hardness and better adhesion. TiB2 is known for low solubility with aluminium, indicating excellent corrosion resistance to Al melt.
4. Summary of the study:
Background of the research topic:
Aluminium pressure diecasting is a key manufacturing process for precision parts, but it heavily relies on lubricants which cause reduced surface quality, longer cycle times, and significant ecological problems related to their use and disposal.
Status of previous research:
State-of-the-art diecasting production involves considerable lubricant usage. While nitrides, carbides, and borides of titanium are known wear protection materials [1, 2, 3], their specific application via PACVD to simultaneously reduce lubricants and extend tool life in Al diecasting under practical conditions required investigation.
Purpose of the study:
The study aimed to investigate the potential of wear-resistant PACVD coatings (specifically titanium nitrides, carbides, and borides) to minimize lubricant use and increase the lifetime of diecasting tools in aluminium diecasting, addressing both economical and ecological aspects.
Core study:
The core of the study involved synthesizing TiN, TiC, and Ti(B,N) coatings using PACVD on hot work steel substrates. These coatings were characterized for their composition, structure, hardness, adhesion, wetting behaviour towards aluminium alloy, and corrosion resistance in molten aluminium. Subsequently, the performance of the best coatings was evaluated in practical diecasting field tests under conditions of significantly reduced lubrication, focusing on tool lifetime extension.
5. Research Methodology
Research Design:
The research employed an experimental design involving the deposition of various titanium-based coatings (TiN, TiC, Ti(B,N), and multilayers) onto diecasting cores using PACVD. This was followed by laboratory characterization of the coatings and practical field testing in an industrial diecasting environment under tightened conditions (reduced lubrication).
Data Collection and Analysis Methods:
- Coating Deposition: PACVD pilot plant with a 400mm diameter, 1000mm height reaction chamber. Coatings deposited on hardened hot work steel X40CrMoV5 1 (1.2344) at substrate temperatures around 500°C. Precursor: TiCl4. Process gases: Ar, H2, N2, CH4, BCl3. Deposition parameters (pressure: 80–250Pa, voltage: 400–700V, pulse: 200–600µs, pause: 100–600µs) were varied.
- Coating Characterization: Metallography, XRD, SEM, EDS, WDS for composition and structure. Knoop hardness, scratch test (adhesion), pin-on-disk test (friction, 100Cr6 pin, FN:5N). Wetting tests with Al alloy up to 800°C at 2×10⁻⁵ mbar. Corrosion resistance evaluated via dip tests in Al melt at 700°C.
- Diecasting Field Tests: Coated cores used for producing induction pipes. Al melt (700°C) injected at 1260bar. Cycle time: 40s. Core temperature cycled between 560°C and 300°C (internal cooling). Lubricant amount continuously reduced. Failure criterion: tearing of the cast during ejection.
Research Topics and Scope:
The research focused on the synthesis, characterization, and performance evaluation of PACVD TiN, TiC, and Ti(B,N) coatings for aluminium diecasting applications. The scope included investigating the influence of deposition parameters, characterizing coating properties (mechanical, structural, chemical, tribological, corrosion, wetting), and assessing their impact on tool lifetime and lubricant reduction in practical diecasting trials.
6. Key Results:
Key Results:
- TiN coatings showed N/Ti ratios of 0.95-1.06, <5% chlorine, {200} preferred orientation, thickness 1-5µm, Ra 20-100nm, max hardness 3300HK0.005, friction coefficient µ=0.27-0.31.
- TiC and Ti-C-N multilayer systems (e.g., TiN/TiC, TiN/Ti(C,N)/TiC) reached up to 4µm thickness, smooth surfaces (Ra=20-70nm). Hardness depended on C/Ti ratio; TiN sublayers improved adhesion.
- Ti(B,N) coatings with 10-60at.% boron were 1.5-2µm thick, very smooth (Ra=35nm). Boron-rich types were amorphous (hardness ~325HK0.005); lower boron content led to crystalline structure (TiN, TiB peaks detected by XRD) with hardness up to 4400HK0.005. Boron was incorporated into a widened TiN lattice (4.26Å vs 4.24Å for TiN).
- Wetting tests showed very high wetting angles (174-177°) for selected TiN, TiN/TiC, and Ti(B,N) coatings with the Al alloy, indicating poor wettability and low adhesion tendency between the melt and the coating.
- Corrosion tests (6h dip in 700°C Al melt) showed coatings prevented reaction between Al melt and steel substrate, exhibiting good corrosion resistance.
- In diecasting field tests, the amount of lubricant agent was reduced by 97%, with water replacing the volume for cooling (Fig. 2).
- Compared to an uncoated core lifetime of approx. 100 casts:
- TiN coatings increased lifetime by a factor of 45 to 130 (up to 13,001 casts) (Fig. 3).
- TiN/Ti(C,N)/TiN multilayer failed after 5992 casts.
- Carbon-rich TiC coatings achieved a lifetime increase factor of 160 (up to 15,976 casts), with lifetime correlating to carbon content (Fig. 4).
- Ti(B,N) coatings showed the most promise, surviving over 300 times the lifetime of the uncoated dummy core without failure during the reported tests (Fig. 3).
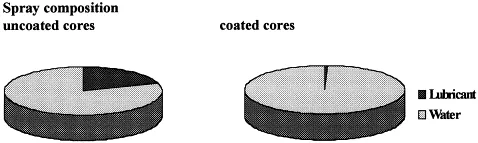
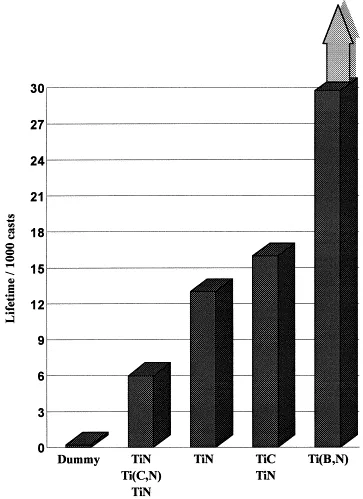
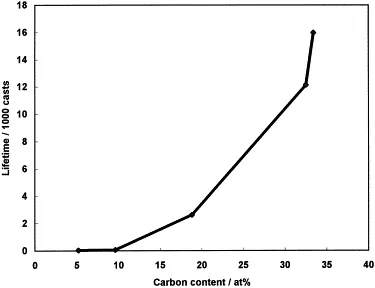
Figure Name List:
- Fig. 1. TiN- and Ti(B,N)-coated core with the corresponding cast.
- Fig. 2. Composition of the spray before and after study.
- Fig. 3. Maximal service life of the coating systems in diecasting field tests.
- Fig. 4. Service life of TiC coatings versus carbon content.
7. Conclusion:
Functional coatings deposited by PACVD offer a significant opportunity to minimize lubricant use in Al diecasting, providing both economical and ecological benefits. This study demonstrated a 97% reduction in lubricant consumption. Concurrently, the analysed titanium nitrides, carbides, and borides significantly increased the lifetime of diecasting tools compared to uncoated tools under the same demanding, low-lubrication conditions. TiN coatings increased lifetime by a factor of up to 130, while multilayer TiN/TiC achieved a factor of 160. Ti(B,N) coatings proved particularly promising, surviving over 300 times the service life of the uncoated dummy core in the tests conducted.
8. References:
- [1] H.O. Pierson Mater. Manufact. Process., 8 (4/5) (1993), pp. 519-534
- [2] H. Holleck J. Vac. Sci. Technol. A, 4 (6) (1986), pp. 2661-2669
- [3] M. Kornmann, R. Funk Aluminium, 53 (1977), pp. 249-252
- [4] C. Pfohl, A. Gebauer-Teichmann, K.-T. Rie Matwiss. Werkstoffech., 29 (1998), pp. 51-56
- [5] K.-T. Rie, A. Gebauer, C. Pfohl, 18. Ulmer Gespräch, DGO, VDI-TZ, Ulm 1996, pp. 66–74.
- [6] N. Kikuchi, Y. Oosawa, A. Nishiyama, in: Proceedings of the Ninth International Conference on Chemical Vapour Deposition, Electrochemical Society, Pennington, 1984, pp. 728-744.
9. Copyright:
- This material is a paper by "C. Pfohl, A. Gebauer-Teichmann, K.-T. Rie". Based on "Application of wear-resistant PACVD coatings in aluminium diecasting: economical and ecological aspects".
- Source of the paper: https://doi.org/10.1016/S0257-8972(98)00796-8
This material is summarized based on the above paper, and unauthorized use for commercial purposes is prohibited.
Copyright © 2025 CASTMAN. All rights reserved.