This article introduces the paper "Feasibility of Metal Additive Manufacturing for Internal Combustion Engines" by Jamee Gray, submitted to the University of Kansas in 2020.
1. Overview:
- Title: Feasibility of Metal Additive Manufacturing for Internal Combustion Engines
- Author: Jamee Gray
- Publication Year: 2020
- Publishing Journal/Academic Society: University of Kansas (Master of Science Thesis)
- Keywords: metal additive manufacturing, AM, internal combustion engines, IC engines, LPBF, lightweighting, reverse engineering, dynamometer testing, porosity, AlSi12, Ti-6Al-4V
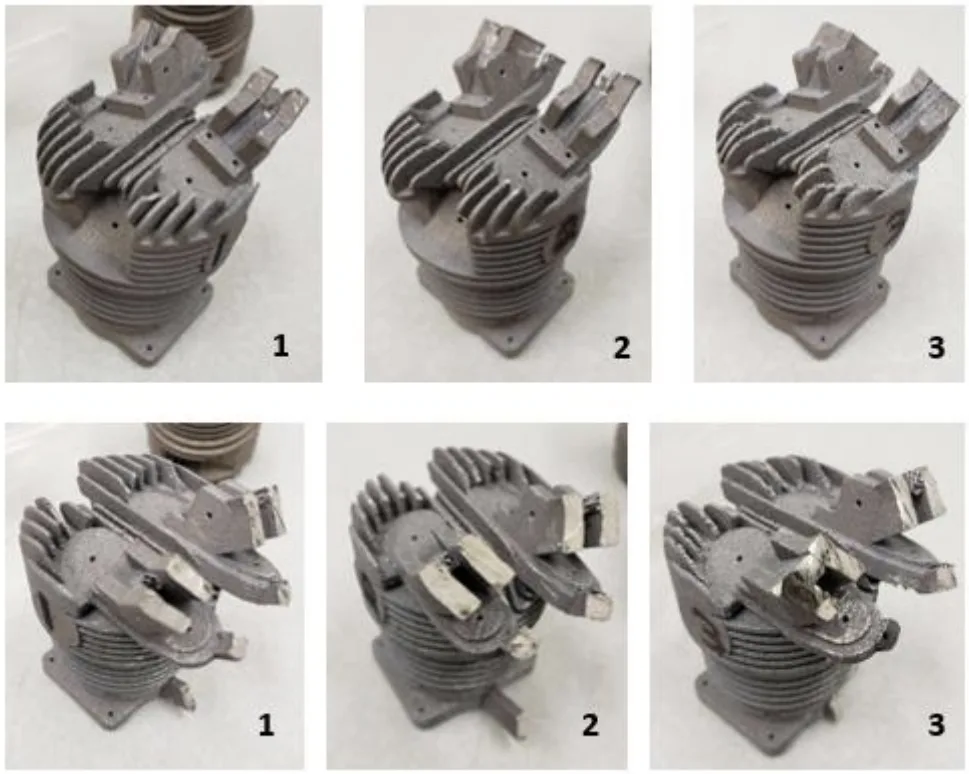
2. Research Background:
- Social/Academic Context of the Research Topic: The advancement of metal additive manufacturing (AM) presents opportunities for industries like automotive and defense to innovate and remain competitive. Implementing AM in internal combustion (IC) engines is a potential avenue for improving fuel economy through lightweighting and optimized designs. Reducing vehicle mass is crucial for improving fuel efficiency and reducing emissions, with powertrain components being a significant contributor to overall vehicle weight.
- Limitations of Existing Research: While AM is being explored for IC engine components, much of the current application is limited to prototyping and tooling, with actual part production focused on research, motorsport, and luxury vehicles. There is a need to demonstrate the feasibility of AM for producing functional IC engine components, especially for broader applications beyond niche markets. Existing weight reduction strategies using material substitution have limitations in cost and achievable weight savings using conventional manufacturing.
- Necessity of the Research: This research addresses the necessity of exploring AM as a viable manufacturing method for IC engine components. It investigates the feasibility of using Laser Powder Bed Fusion (LPBF) to produce functional parts, specifically focusing on the design, manufacturing, and testing of a crankcase and cylinder head for a Saito FG-11 engine. This research aims to contribute to the understanding and advancement of AM in practical engine applications.
3. Research Purpose and Research Questions:
- Research Purpose: To demonstrate the feasibility of using metal Additive Manufacturing (AM), specifically Laser Powder Bed Fusion (LPBF), to produce working Internal Combustion (IC) engine components. The thesis aims to prove AM as a feasible option for IC engine components, focusing on the design, manufacturing, and testing process.
- Key Research Questions:
- Can functional IC engine components (crankcase and cylinder head) be produced using LPBF?
- What are the critical tolerances and design considerations for AM production of IC engine components?
- How does an AM-produced IC engine perform compared to a stock engine in terms of operational characteristics?
- What are the material characteristics (porosity, dimensional accuracy, surface finish) of AM-produced engine components, and how do they compare to conventionally manufactured parts?
- Research Hypotheses:
- LPBF can be used to manufacture functional crankcase and cylinder head components for a small IC engine.
- AM-produced engine components will exhibit comparable, though potentially slightly degraded, performance compared to stock components.
- Post-processing techniques like machining and honing are crucial to achieve functional AM engine components with required tolerances and surface finishes.
4. Research Methodology
- Research Design: Experimental research involving reverse engineering, AM manufacturing, post-processing, and performance testing of IC engine components. Comparative analysis of AM-produced engine with stock engine components.
- Data Collection Method:
- Reverse Engineering: Measurement and modeling of stock Saito FG-11 engine crankcase and cylinder head. CT scanning for dimensional verification.
- AM Manufacturing: LPBF process using Ti-6Al-4V for crankcase and AlSi12 for cylinder head.
- Post-Processing: Stress relieving, heat treatments, machining, and cylinder honing. CT scanning to assess porosity and dimensional accuracy post-AM and post-machining. Surface roughness measurements using profilometer.
- Engine Performance Testing: Dynamometer and propeller testing to measure engine speed, torque, temperatures (cylinder head, crankcase, exhaust, intake), pressures (intake, exhaust), airflow, and fuel consumption.
- Analysis Method:
- Dimensional Analysis: Nominal/actual dimensional comparison using Volume Graphics Software to compare AM parts to CAD models and cast parts.
- Porosity Analysis: CT data analysis using Volume Graphics and CTAn software to quantify porosity in AM and cast parts.
- Performance Comparison: Comparative analysis of engine performance parameters (volumetric efficiency, air-fuel ratio, equivalence ratio, torque, speed, temperatures) between stock and AM-modified engines under propeller and dynamometer loads. Statistical analysis to calculate averages and standard deviations.
- Research Subjects and Scope: Saito FG-11 four-stroke 10.9 cc engine. Focus on crankcase and cylinder head components. Material scope: Ti-6Al-4V and AlSi12 for AM parts, die-cast aluminum for stock parts.
5. Main Research Results:
- Key Research Results:
- Functional crankcase and cylinder head for Saito FG-11 engine were successfully produced using LPBF.
- AM engine was operable and ran for over 3.5 hours during testing without failure.
- AM engine exhibited degraded performance compared to the stock engine, but was still functional.
- Degraded performance was hypothesized to be due to assembly variations or increased friction from insufficient honing, not the AM process itself.
- Porosity in AM parts was quantified and found to be comparable or better than die-cast parts after machining, except in specific support regions.
- Dimensional accuracy of AM parts was within acceptable ranges for functional engine components after post-machining.
- Statistical/Qualitative Analysis Results:
- Porosity: AM parts showed comparable or lower porosity levels than die-cast parts after machining. Average percent porosity area for AM crankcase was 0.0027%, compared to 0.0280% for die-cast crankcase.
- Dimensional Accuracy: Nominal/actual dimensional analysis showed most critical features within ±0.005" tolerance after machining.
- Engine Performance: AM engine (ACAH and ACS configurations) generally showed lower volumetric efficiency and torque compared to the stock engine (SE) in both propeller and dynamometer testing. ACS configuration showed higher engine speed and exhaust temperature compared to SE and ACAH in propeller testing.
- Data Interpretation:
- While AM engine performance was slightly degraded, the successful operation and durability demonstrated the feasibility of AM for IC engine components.
- The AM process, combined with post-processing, can produce parts with acceptable dimensional accuracy and porosity for engine functionality.
- Material choice and design optimization are crucial for mitigating potential performance differences and fully leveraging AM benefits.
- Figure Name List:
- Figure 3.13: Original crankcase design build results
- Figure 3.14: Modified crankcase build results
- Figure 3.15: Cylinder head build plate result
- Figure 3.16: AM cylinder head results
- Figure 3.18: Nominal actual dimensional analysis of AM parts vs. CAD files for original and modified crankcase designs
- Figure 3.19: Nominal actual dimensional analysis of AM parts vs. CAD files for cylinder head
- Figure 3.21: Visual representation of porosity in AM crankcase 1 (original, left) and crankcase 2 (modified, right) designs
- Figure 3.23: Visual representation of porosity in cylinder head
- Figure 3.24: Visual representation of porosity in AM cylinder head 2
- Figure 3.25: Crack defect in AM crankcase original design number 1
- Figure 3.26: Crack defect in AM cylinder head number 2
- Figure 5.7: Intake air flow rate results during prop testing
- Figure 5.8: Fuel consumption results during prop testing
- Figure 5.9: Engine speed results during prop testing
- Figure 5.10: Exhaust temperature results during prop testing
- Figure 5.11: Cylinder head temperature results during prop testing
- Figure 5.12: Crankcase temperature results during prop testing
- Figure 5.13: Air intake flow rates results during dyno testing
- Figure 5.14: Fuel consumption results during dyno testing
- Figure 5.15: Exhaust temperatures results during dyno testing
- Figure 5.16: Cylinder head temperatures results during dyno testing
- Figure 5.17: Crankcase temperatures results during dyno testing
- Figure 5.18: Engine torques produced results during dyno testing
6. Conclusion and Discussion:
- Summary of Main Results: The research successfully demonstrated the feasibility of using LPBF to manufacture functional IC engine components (crankcase and cylinder head). While the AM engine showed slightly degraded performance compared to the stock engine, it operated without failure for over 3.5 hours. Post-processing, including machining and honing, was crucial for achieving functional parts.
- Academic Significance of the Research: This thesis contributes to the growing body of knowledge on AM applications in IC engines. It provides a detailed case study of the entire AM process, from design and manufacturing to testing and validation, for critical engine components. The research highlights the potential and challenges of using LPBF for functional parts in demanding applications.
- Practical Implications: The findings suggest that AM can be a viable manufacturing method for IC engine components, particularly in scenarios where rapid prototyping, design optimization, or on-demand part replacement is needed, such as in military UAV applications. The scalability of LPBF also indicates potential for larger engine components.
- Limitations of the Research: The study focused on a small, single-cylinder engine. Performance degradation was observed, and further investigation is needed to fully understand and mitigate the causes. The research also acknowledges potential variations due to manual assembly and tappet adjustments, which could influence performance comparisons.
7. Future Follow-up Research:
- Directions for Follow-up Research:
- Implement design optimizations, including topology optimization, to further lightweight and enhance AM engine component performance.
- Conduct simulations to verify engine performance against theoretical calculations and guide design modifications.
- Investigate the use of cylinder liners in AM cylinder heads to potentially improve wear resistance and performance.
- Develop stricter procedures for part swaps and engine setup to minimize variations in comparative testing.
- Explore different AM materials and post-processing techniques to optimize engine component properties and performance.
- Areas Requiring Further Exploration:
- In-cylinder pressure measurement to better understand combustion characteristics in AM engines.
- Durability testing over extended operation periods to assess long-term reliability of AM engine components.
- Optimization of cooling strategies for AM engines, considering the thermal properties of AM materials.
- Investigation of different engine sizes and configurations to broaden the applicability of AM in IC engines.
8. References:
- References are available in the original thesis document.
9. Copyright:
- This material is Jamee Gray's paper: Based on Feasibility of Metal Additive Manufacturing for Internal Combustion Engines.
- Paper Source: [DOI URL - Not available in the provided document, insert DOI URL if available]
This material was summarized based on the above paper, and unauthorized use for commercial purposes is prohibited.
Copyright © 2025 CASTMAN. All rights reserved.