This article introduces the paper 'Zinc alloy 8, a diecasting alloy with special relevance to underbonnet applications' published by 'Int. J. of Materials and Product Technology'.
1. Overview:
- Title: Zinc alloy 8, a diecasting alloy with special relevance to underbonnet applications
- Author: G.K. Willcox
- Publication Year: 1991
- Publishing Journal/Academic Society: Int. J. of Materials and Product Technology
- Keywords: Alloys, casting, diecasting, underbonnet applications, zinc alloys.
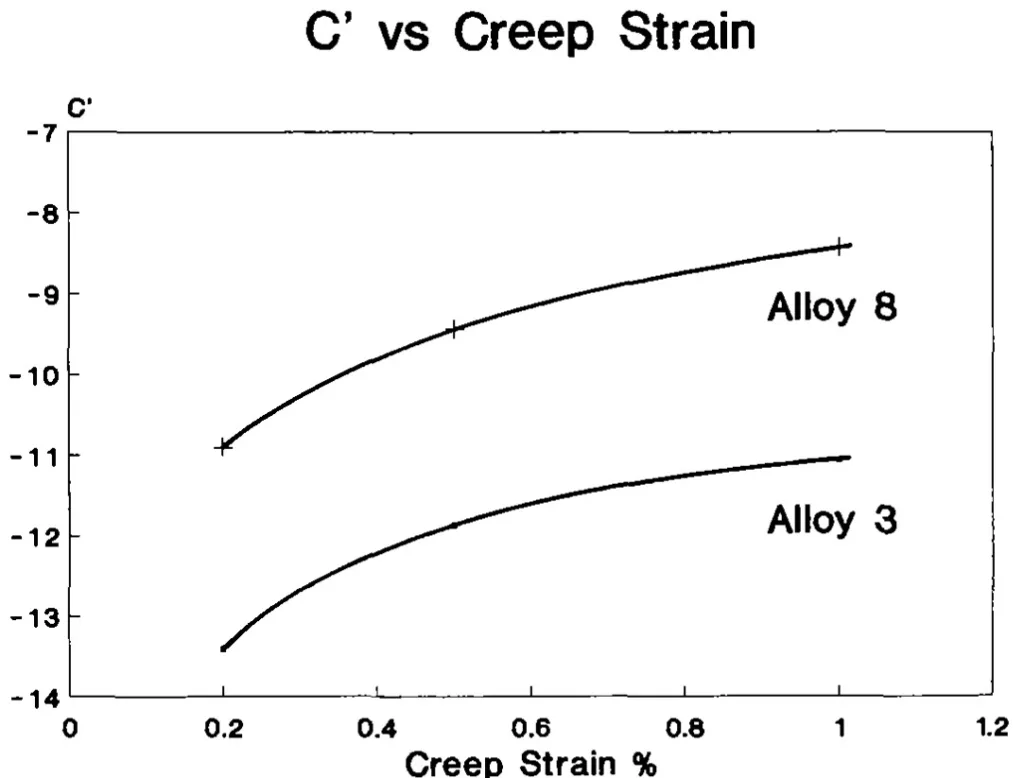
2. Abstracts
Conventional zinc alloys exhibit exceptional net shape castability and a spectrum of valuable mechanical and physical properties. However, their stressed application temperature is constrained to a maximum of approximately 100°C. Alloy 8, a novel alloy, has been introduced, enabling application temperatures to be elevated by up to 30°C. This paper revisits research findings that quantify the enhanced creep resistance and elucidates the utilization of these results for design optimization. Case studies from both automotive and non-automotive sectors are examined to showcase the practical implementation of creep resistance improvement and validate the practicality of hot chamber diecasting of Alloy 8.
3. Research Background:
Background of the Research Topic:
Zinc alloy diecastings have been utilized in the motor industry for over 50 years due to their advantageous cost-to-performance ratio for complex three-dimensional shapes. Conventional zinc alloys are widely employed in diverse applications, including automotive components such as locks, door handles, and underbonnet parts like carburettors and fuel pumps. Their widespread use is attributed to a combination of favorable mechanical and physical properties, including tensile strength, stiffness, toughness, and high thermal and electrical conductivity, coupled with a low melting point that facilitates net shape forming via hot chamber diecasting.
Status of Existing Research:
Existing research acknowledges the limitations of conventional zinc alloys concerning application temperature due to their susceptibility to creep distortion at elevated temperatures. Prior efforts by the zinc industry, through ILZRO, led to the development of creep-resistant alloys like ILZRO 14 and ILZRO 16. However, these alloys necessitate cold chamber diecasting, which is less productive than hot chamber diecasting, reducing their economic attractiveness. This context highlights the demand for a hot chamber diecastable alloy with enhanced creep resistance. Alloy 8 was developed to address this need, initially for gravity diecasting, but subsequently proven viable for hot chamber diecasting with superior creep resistance compared to conventional alloys.
Necessity of the Research:
The research is necessitated by the need to quantify and demonstrate the improved creep resistance of Alloy 8 compared to conventional zinc diecasting alloys. This quantification is crucial for designers to effectively utilize Alloy 8 in applications requiring elevated temperature performance, particularly in underbonnet automotive components and other industrial sectors. The paper aims to provide a comparative analysis of creep resistance and to illustrate the practical application of Alloy 8 through case studies, thereby validating its use in hot chamber diecasting for demanding applications.
4. Research Purpose and Research Questions:
Research Purpose:
The primary purpose of this research is to compare the creep resistance of Alloy 8 with other zinc diecasting alloys. Furthermore, the paper aims to elucidate the application of a creep equation, derived from prior research, to establish practical accelerated test procedures for Alloy 8. The study also intends to present case studies demonstrating the utilization of Alloy 8 in elevated temperature applications, both within and beyond the automotive sector.
Key Research:
The key research questions addressed in this paper are:
- How does the creep resistance of Alloy 8 compare to conventional hot chamber diecasting alloys (Alloy 3 and Alloy 5) and a cold chamber alloy (Alloy 27)?
- Can the creep equation, Int = C' - n (lnσ) + Q/RT, be effectively used to predict creep behavior and design accelerated testing procedures for Alloy 8?
- What are the practical applications where the enhanced creep resistance of Alloy 8 provides significant advantages, particularly in elevated temperature environments?
Research Hypotheses:
While not explicitly stated as hypotheses, the research operates under the premise that:
- Alloy 8 exhibits superior creep resistance compared to conventional hot chamber zinc diecasting alloys, making it suitable for elevated temperature applications.
- The derived creep equation can be effectively employed to characterize and predict the creep behavior of Alloy 8, enabling the design of accelerated testing methodologies.
- The improved creep resistance of Alloy 8 expands the application range of zinc diecastings, particularly in demanding environments such as underbonnet automotive applications.
5. Research Methodology
Research Design:
The research employs a comparative experimental design, focusing on the creep characteristics of different zinc alloys. It also incorporates case studies to demonstrate the practical application of Alloy 8.
Data Collection Method:
Creep data for Alloys 3, 8, and 27 were experimentally obtained at Aston University. The paper also references existing creep data for Alloys 3 and 5 from the New Jersey Zinc Company (NJZ) and Alloy 8 data from Murphy, Durman, and Hill. Application case studies were collected from industrial applications in the UK and elsewhere.
Analysis Method:
The creep behavior was analyzed using the creep equation: Int = C' - n (lnσ) + Q/RT. The parameters in this equation (C', n, Q) were determined experimentally. The analysis involved comparing the C' values and creep curves for different alloys. Accelerated testing methodologies were derived from the creep equation. Practical applications were evaluated through case study analysis, focusing on the performance of Alloy 8 in real-world conditions.
Research Subjects and Scope:
The research focuses on zinc diecasting alloys, specifically Alloy 8 and its comparison to Alloys 2, 3, 5, and 27. The scope includes the investigation of creep resistance, mechanical and physical properties, and casting production characteristics. The application scope is primarily underbonnet automotive components and other elevated temperature applications.
6. Main Research Results:
Key Research Results:
- Creep Resistance: Alloy 8 demonstrates significantly improved creep resistance compared to Alloy 3. Approximations derived from the creep equation and experimental data indicate that Alloy 8 offers either fourteen times the design service lifetime, double the design stress, or a 30°C increase in operating temperature capability compared to Alloy 3.
- Creep Equation Validation: The creep equation Int = C' - n (lnσ) + Q/RT was validated for describing the creep behavior of zinc alloys up to 1% strain, for stresses up to 40 MPa and temperatures up to 150°C.
- Accelerated Testing: The paper presents equations derived from the creep equation to calculate comparable service life from accelerated tests, necessary duration of accelerated tests, and maximum possible service temperature. These equations facilitate accelerated testing of Alloy 8 components.
- Mechanical Properties: Table 1 presents a comparison of tensile strength, elongation, hardness, impact strength, fatigue strength, specific gravity, thermal expansion, thermal conductivity, and electrical conductivity for Alloys 2, 3, 5, and 8, both in aged and unaged conditions. Alloy 8 exhibits comparable or superior mechanical properties to other hot chamber alloys, with notable improvements in fatigue strength.
- Practical Applications: Case studies demonstrate successful applications of Alloy 8 in modular electronic ignition bodies, daylight running light control units, electric power tool components, energy regulator casings for electric cookers, and transducer brackets for electronic scales. These applications leverage Alloy 8's enhanced creep resistance and thermal conductivity, particularly in elevated temperature environments.
Analysis of presented data:
- Figure 1 (C' vs Creep Strain): This figure graphically compares the C' values for Alloy 8 and Alloy 3 as a function of creep strain. It visually demonstrates the superior creep resistance of Alloy 8, as indicated by its lower C' values across the strain range.
- Table 1 (Alloy Properties): This table provides a quantitative comparison of the mechanical and physical properties of Alloys 2, 3, 5, and 8. The data highlights Alloy 8's competitive property profile, particularly its high tensile and fatigue strength, and lower thermal expansion compared to other alloys. The aging data further illustrates the performance characteristics of each alloy after exposure to elevated temperatures.
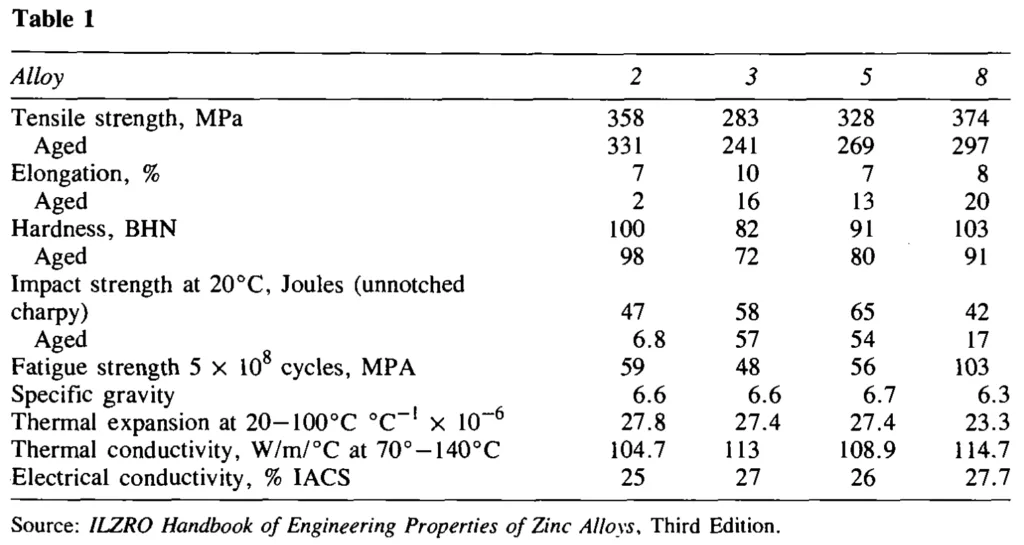
Figure Name List:
- Figure 1: C' vs Creep Strain
7. Conclusion:
Summary of Key Findings:
The study conclusively demonstrates that Alloy 8 possesses superior creep resistance compared to conventional Alloy 3, making it particularly suitable for applications operating at elevated temperatures, such as underbonnet automotive components. The research validates the use of a creep equation for characterizing and predicting the creep behavior of Alloy 8 and for designing accelerated testing procedures. Practical case studies further confirm the successful application of Alloy 8 in diverse industrial sectors, leveraging its enhanced creep resistance and other beneficial properties.
Academic Significance of the Study:
This study contributes to the scientific understanding of creep behavior in zinc diecasting alloys, specifically highlighting the improved performance of Alloy 8. The validation and application of the creep equation provide a valuable tool for material selection and component design in elevated temperature environments. The research also expands the knowledge base regarding the property profiles of various zinc alloys, offering a comprehensive comparative dataset.
Practical Implications:
The findings have significant practical implications for engineers and designers in various industries, particularly automotive and electronics. Alloy 8 offers a viable material solution for hot chamber diecasting components requiring enhanced creep resistance and performance at elevated temperatures. The provided accelerated testing methodologies enable efficient product development and validation. The case studies serve as practical examples, guiding the application of Alloy 8 in new and existing product designs.
Limitations of the Study and Areas for Future Research:
The study primarily focuses on creep resistance up to 1% strain and stresses up to 40 MPa. Further research could explore creep behavior at higher strain levels and stress conditions. Direct comparative creep tests between Alloy 8 and Alloys 2 and 5 at sensible stress levels are recommended to further refine the comparative performance assessment. Long-term performance data and more extensive application case studies would further solidify the understanding and broaden the application scope of Alloy 8. Further investigation into the aggressiveness of Alloy 8 towards diecasting machine components and optimization strategies could also be beneficial.
8. References:
- Klein, F. (1987) 'Creep ruptive tests on zinc pressure die casting alloys', Transactions of the 14th International SDCE Pressure Die Casting Congress, Paper G-T87-028. NADCA River Grove, Illinois, USA.
- Klein, F. (1989) 'Effect of section size and aging treatments on mechanical properties of three zinc alloys', Transactions of 15th NADCA International Die Casting Congress, Paper G-T89-083. NADCA River Grove, Illinois, USA.
- Murphy, S., Durman, M. and Hill, J. (1988) 'Kinetics of creep in pressure diecast commercial zinc-aluminium alloys', Zeitschrift Fur Metallkunde, vol. 79, pp. 243-247.
9. Copyright:
- This material is "G.K. Willcox"'s paper: Based on "Zinc alloy 8, a diecasting alloy with special relevance to underbonnet applications".
- Paper Source: [DOI URL - Not available in the provided text]
This material was summarized based on the above paper, and unauthorized use for commercial purposes is prohibited.
Copyright © 2025 CASTMAN. All rights reserved.