연구 내용
- 연구의 핵심 목적: 마그네슘 합금의 용융 및 주조 공정을 요약하고, 자동차 산업을 중심으로 한 구조용 마그네슘 주조의 역사적 발전, 현재 및 잠재적 응용 분야를 검토하며, 관련 기술적 과제를 논의하는 것이다. 증가하는 세계적 에너지 수요, 환경 보호 및 정부 규제는 향후 수십 년 동안 경량 마그네슘 주조의 적용을 촉진할 것이다.
- 주요 방법론: 마그네슘 합금의 용융 및 주조 공정에 대한 문헌 조사와 분석을 통해 마그네슘 주조 기술의 역사적 발전, 현재 기술, 자동차, 항공우주, 전력 공구 산업에서의 구조적 적용, 기술적 과제 및 기회를 검토한다.
- 핵심 결과: 다양한 마그네슘 주조 공정 (고압 다이캐스팅, 저압 다이캐스팅, 압출 주조, 분실 폼 주조, 삭마 주조, 반고체 주조 등)에 대한 개요와 자동차 산업에서의 마그네슘 구조 응용 분야에 대한 심층적인 분석을 제공한다. 마그네슘 주조의 기술적 과제(다공성, 내식성, 피로강도)를 논의하고, 이러한 과제를 해결하기 위한 대안적인 주조 공정(진공 보조 다이캐스팅, 초고진공 다이캐스팅 등)을 제시한다. 통합 전산 재료 공학 (ICME) 도구의 개발을 통해 마그네슘 주조의 응용 분야가 가속화될 것으로 전망한다.
![Fig. 19. Magnesium powertrain components from the USCAR magnesium powertrain cast components project; (a) LPDC cylinder block, (b) Thixomolded front engine cover, (c) HPDC oil pan and (d) HPDC rear seal carrier [54].](https://castman.co.kr/wp-content/uploads/image-108-png.webp)
연구진 정보
- 소속 기관: 논문에 명시된 저자의 소속기관은 명확하게 언급되지 않았다.
- 저자명: Alan A. Luo
- 주요 연구 분야: 마그네슘 주조 기술
연구 배경 및 목적
- 해당 연구가 필요한 산업적 배경: 자동차, 항공우주, 전력 공구 산업 등에서 경량화 소재에 대한 수요 증가.
- 구체적인 기술적 문제점 과제: 마그네슘 합금 주조의 기술적 어려움 (높은 다공성, 내식성, 피로강도 등). SF6와 같은 환경오염 물질 사용에 대한 규제 강화.
- 연구 목표: 마그네슘 합금의 용융 및 주조 공정의 종합적 검토, 다양한 주조 방법 분석, 자동차 산업 중심의 구조용 마그네슘 주조의 역사적 발전 및 현황 분석, 기술적 과제 해결 방안 및 미래 전망 제시.
논문의 주요 목표와 연구 내용
- 논문의 주요 목표와 연구 내용: 마그네슘 합금 주조 기술 전반에 대한 종합적이고 체계적인 검토, 특히 자동차 산업에서의 구조적 응용에 중점.
- 문제점: 마그네슘 주조에서 발생하는 다공성, 내식성 저하, 피로강도 부족 등의 기술적 문제점과 SF6 사용에 따른 환경 규제 문제.
- 문제 해결을 위한 단계적 접근:
- 다양한 마그네슘 주조 방법 (고압 다이캐스팅, 저압 다이캐스팅, 진공 보조 다이캐스팅, 초고진공 다이캐스팅, 압출 주조, 분실 폼 주조, 삭마 주조, 반고체 주조) 소개 및 각 방법의 장단점 분석.
- 각 주조 방법의 특징과 적용 분야를 자동차 산업 중심으로 설명.
- 마그네슘 주조의 기술적 과제 (다공성, 내식성, 피로 강도)를 심층적으로 분석.
- 다공성을 감소시키는 진공 보조 다이캐스팅, 초고진공 다이캐스팅 등 대안적 주조 공정과 내식성 향상을 위한 표면처리 기술 제시.
- 통합 전산 재료 공학 (ICME) 도구의 활용을 통한 마그네슘 주조 기술 발전 전망.
- 주요 Figure:
- Fig. 1: 개방형 도가니 용융을 위한 고정식 연료 가열로의 단면도.
- Fig. 2: 강철 덮개가 있는 현대식 전기로와 주조 기계로 용융 마그네슘을 공급하는 금속 이송관.
- Fig. 3: 고압 다이캐스팅의 고온 챔버 방식 개략도.
- Fig. 4: 고온 챔버 다이캐스팅 공정으로 제작된 대표적인 마그네슘 부품.
- Fig. 5: 저온 챔버 다이캐스팅 공정 개략도.
- Fig. 6: 냉각 챔버 다이캐스팅으로 제작된 GM 마그네슘 계기판 빔.
- Fig. 7: Gibbs Die Casting의 진공 보조 수직 다이캐스팅 공정.
- Fig. 8: 저압 주조 기계의 개략도.
- Fig. 9: GM에서 저압 다이캐스팅으로 제작한 마그네슘 제어 암 시제품.
- Fig. 10: 칙소몰딩 기계의 개략도.
- Fig. 11: 직접 압출 주조 공정 단계.
- Fig. 12: (a) 종래 다이캐스팅과 (b) 간접 압출 주조 공정에서의 금속 흐름 개략도.
- Fig. 13: 알루미늄 및 마그네슘 주조를 위한 삭마 주조 공정.
- Fig. 14: Pratt & Whitney F119 보조 케이싱.
- Fig. 15: Rolls Royce 트레이.
- Fig. 16: Meridian Lightweight Technologies의 Lincoln MKT 리프트게이트 인너.
- Fig. 17: Chevrolet Corvette용 LPDC 마그네슘 합금 휠.
- Fig. 18: 마그네슘 외장 및 알루미늄 내장을 보여주는 BMW 복합 엔진 블록의 절단면.
- Fig. 19: USCAR 마그네슘 파워트레인 주조 부품 프로젝트의 마그네슘 부품.
- Fig. 20: Chevrolet Corvette Z06 마그네슘 크래들의 알루미늄 절연체 위치.
- Fig. 21: USCAR 데모 구조물 제작에 사용된 (a) FSLW 및 (b) LSPR 결합 공정.
- Fig. 22: 마그네슘 응용을 위한 통합 전산 재료 공학(ICME) 프레임워크.
![Fig. 1. Cross section of a stationary fuel-fired furnace used for the open crucible melting of magnesium alloys [2].](https://castman.co.kr/wp-content/uploads/image-90-png.webp)
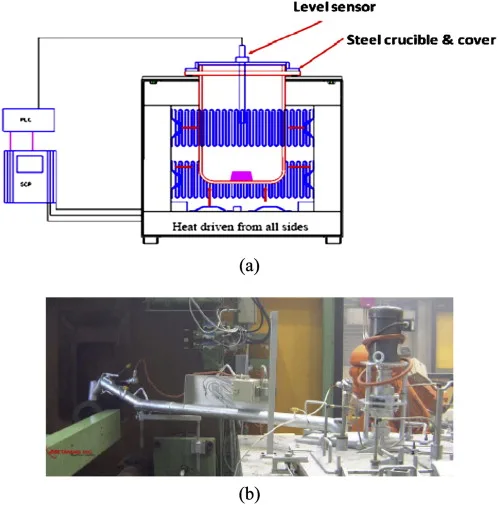
![Fig. 3. Schematics of hot chamber die casting [8].](https://castman.co.kr/wp-content/uploads/image-92-png.webp)
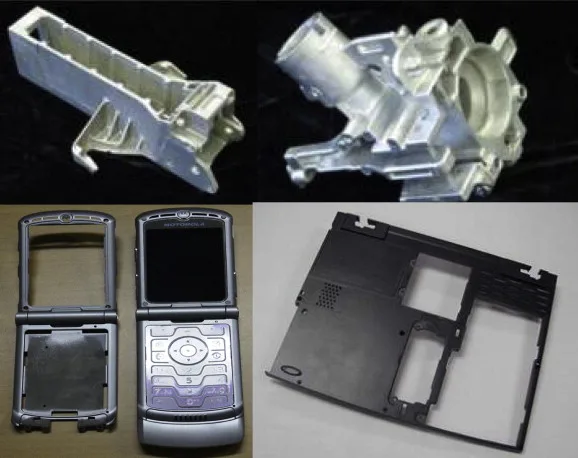
![Fig. 5. Schematics of cold chamber die casting [8].](https://castman.co.kr/wp-content/uploads/image-94-png.webp)

![Fig. 7. Gibbs vertical vacuum assisted die casting process (Courtesy of Gibbs Die Casting, Henderson, KY, USA [11]).](https://castman.co.kr/wp-content/uploads/image-96-png.webp)
![Fig. 8. A schematic diagram of a typical low pressure casting machine [17].](https://castman.co.kr/wp-content/uploads/image-97-png.webp)
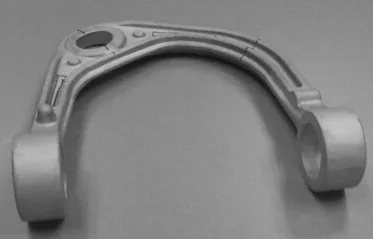
![Fig. 10. A schematic diagram of a Thixomolding machine [21].](https://castman.co.kr/wp-content/uploads/image-99-png.webp)
![Fig. 11. Schematic illustrating direct squeeze casting process operations: (a) melt into die cavity; (b) close tooling, solidify melt under pressure; and (c) eject casting [8].](https://castman.co.kr/wp-content/uploads/image-100-png.webp)
![Fig. 12. Schematic illustrating metal flow in (a) conventional die casting; and (b) indirect squeeze casting process [8].](https://castman.co.kr/wp-content/uploads/image-101-png.webp)
![Fig. 13. Ablation casting process for aluminum and magnesium casting [26].](https://castman.co.kr/wp-content/uploads/image-102-png.webp)
![Fig. 14. Pratt & Whitney F119 auxiliary casing in ELEKTRON WE43 alloy [37].](https://castman.co.kr/wp-content/uploads/image-103-png.webp)
![Fig. 15. Rolls Royce tray in ELEKTRON ZRE1 alloy [37].](https://castman.co.kr/wp-content/uploads/image-104-png.webp)
![Fig. 16. HPDC magnesium casting Lincoln MKT liftgate inner (photo courtesy of Meridian Lightweight Technologies) [49].](https://castman.co.kr/wp-content/uploads/image-111-png.webp)
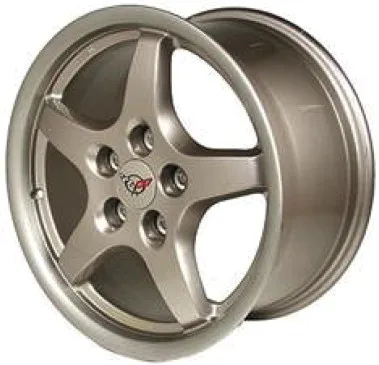
![Fig. 18. The BMW composite engine block showing a cutaway of the magnesium exterior revealing the aluminum interior [35].](https://castman.co.kr/wp-content/uploads/image-109-png.webp)
![Fig. 20. Aluminum isolator locations for Chevrolet Corvette Z06 magnesium cradle (bottom & top views) [50].](https://castman.co.kr/wp-content/uploads/image-107-png.webp)
![Fig. 21. USCAR demo structure build using (a) FSLW (friction stir linear welding); and (b) LSPR (laser-assisted self-pierce rivet) joining processes [67].](https://castman.co.kr/wp-content/uploads/image-106-png.webp)
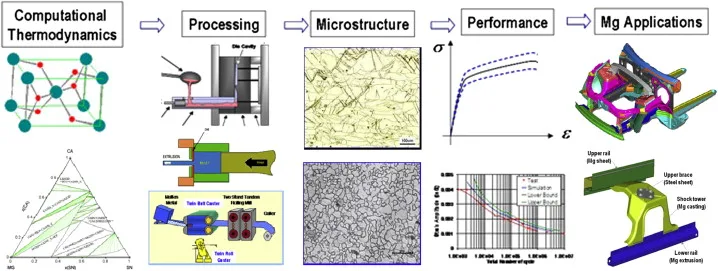
결과 및 성과:
- 정량적 결과: 다양한 마그네슘 주조 공정 (고압 다이캐스팅, 저압 다이캐스팅, 진공 보조 다이캐스팅, 초고진공 다이캐스팅, 압출 주조 등)에 대한 인장 강도, 항복 강도, 연신율 등의 기계적 특성 값 제시. (Table 1, Table 3, Table 4, Table 5 참조)
- 정성적 결과: 마그네슘 주조 기술의 발전 과정, 자동차 산업에서의 적용 사례, 기술적 과제, 대안적 주조 공정 제시, 미래 전망 제시.
- 기술적 성과: 마그네슘 주조의 다공성 감소, 내식성 향상, 피로 강도 개선을 위한 기술적 해결 방안 제시. 통합 전산 재료 공학 (ICME) 도구의 개발을 통한 마그네슘 주조 기술 발전 전망 제시.
저작권 및 참고 자료
본 자료는 Alan A. Luo의 논문 "Magnesium casting technology for structural applications"을 기반으로 작성되었습니다.
논문 출처: https://doi.org/10.1016/j.jma.2013.02.002
본 자료는 위 논문을 바탕으로 요약 작성되었으며, 상업적 목적으로 무단 사용이 금지됩니다.
References
- [1]A.A. Luo, K. SadayappanTechnology for Magnesium CastingsAmerican Foundry Society, Schaumburg, IL (2011)pp. 29–47Google Scholar
- [2]M.M. Avedesian, H. BakerMagnesium and Magnesium AlloysASM International, Materials Park, OH (1999)Google Scholar
- [3]J.W. Freuling, J.D. HanawaltTransactions of the American Foundrymen's Society, 77 (1969), pp. 159-164
- [4]J.W. Freuling, Protective Atmospheres for Molten Magnesium, Ph.D. Dissertation, University of Michigan, Ann Arbor, MI, USA, 1970.Google Scholar
- [5]J.F. King, Environmental Challenges Facing the Magnesium Industry – SF6 Replacement, in: Proceedings of the 60th Annual World Magnesium Conference, The International Magnesium Association, Wauconda, IL, USA, 10–16.Google Scholar
- [6]R.E. Brown, Future of Magnesium Developments in 21st Century, in: Presentation at Materials Science & Technology Conference, Pittsburgh, PA, USA, October 5–9, 2008.Google Scholar
- [7]T. Ruden, Magnesium vs. Plastics: A Comparative Study, (Paper G-T89-113), in: Presented at the 15th International Die Casting Congress & Exposition, St. Louis, MO, 1989.Google Scholar
- [8]E.J. VinarcikHigh Integrity Die Casting ProcessesJohn Wiley & Sons, Inc., New York, NY (2003)Google Scholar
- [9]M. Nehan, R. MaloneyMagnesium AM60B Instrument Panel Structure for Crashworthiness FMVSS 204 and 208 Compliance(1996)SAE Paper No. 960419, Warrendale, PAGoogle Scholar
- [10]Die Casting Industry Capability Directory, North American Die Casting Association, Rosemont, IL, USA (2000)
- [11]http://www.gibbsdc.com/.Google Scholar
- [12]A.A. Luo, P.H. Fu, Y.D. Yu, H.Y. Jiang, L.M. Peng, C.Q. Zhai, A.K. SachdevVacuum-assisted High Pressure Die Casting of AZ91 Magnesium AlloyNorth American Die Casting Association Transactions, T08-083(2008)Google Scholar
- [13]Z. Brown, B. Szymanowski, M. Musser, D. Saha, S. Seaver, Manufacturing of Thin Wall Structural Automotive Components Through High Vacuum Die Casting Technology, 2007 Metal Casting Congress.Google Scholar
- [14]H. Koch, A.J. FrankeDuctile Pressure Die Castings for Automotive ApplicationS.K. Das (Ed.), Automotive Alloys, TMS (The Minerals, Metals and Materials Society), Warrendale, PA (1997), pp. 185-198View in ScopusGoogle Scholar
- [15]Z. Brown, A.A. Luo, K. Sadayappan, L.J. Ouimet, J. Zindel, R. Beals, M. MusserDevelopment of Super Vacuum Die Casting Process for Magnesium AlloysNorth American Die Casting Association Transactions, T09-043(2009)Google Scholar
- [16]M. Sahoo, D. Weiss, M. Marlatt, Factors Affecting Successful Permanent Mold Casting of Magnesium, in: Presented at International Conference on Permanent Mold Casting of Al and Mg, February 11–12, 2008, Dallas, Texas, USA.Google Scholar
- [17]P. Fu, A.A. Luo, H. Jiang, L. Peng, Y. Yu, C. Zhai, A.K. SachdevJournal of Materials Processing Technology, 205 (2008), pp. 224-234View PDFView articleView in Scopus
- [18]H. Westengen, O. HoltaFoundry Trade Journal (1989), pp. 738-742
- [19]S.T. Robison, D. Weiss, G. Gegel, G. Woycik, M. Marlatt, B. CoxMagnesium Casting Process Development: Designing an Engine Cradle for Magnesium Semi-permanent Mold CastingAFS Paper 05-217American Foundry Society, Schaumburg, IL (2005)Google Scholar
- [20]A.A. Luo, P.H. Fu, Y.D. Yu, L.M. Peng, H.Y. Jiang, C.Q. Zhai, A.K. SachdevLow Pressure Die Casting of AZ91 and AM50 Magnesium AlloysAFS Paper 08-147American Foundry Society, Schaumburg, IL (2007)Google Scholar
- [21]S.E. LeBeau, M.W. Walukas, R.F. Decker, P. LaBelle, A.R. Moore, J.W. JonesEvaluation of Thixomolded Magnesium Alloy Components for Structural Automotive ApplicationsSAE Technical Paper 2004-01-0137SAE International, Warrendale, PA (2008)Google Scholar
- [22]S. Corbit, R. DasGuptaSqueeze Cast Automotive Applications and Squeeze Cast Aluminum Alloy PropertiesSAE Technical Paper 1999-01-0343SAE, Warrendale, PA (1999)Google Scholar
- [23]R. DasGupta, P. Burton, Z. BrownMicrostructure and Mechanical Properties of Squeeze Cast AZ91D Magnesium AlloySAE Technical Paper 2005-01-0330SAE, Warrendale, PA (2005)Google Scholar
- [24]B. Szymanowski, Magnesium Squeeze Casting Update, in: Presentation at the 111th Metalcasting Congress, Houston, TX, May 15–18, 2007.Google Scholar
- [25]Y. Fasoyinu, M. Sahoo, Lost Foam Casting of Magnesium Alloys for Automotive Applications, in: Proceedings of 64th Annual World Magnesium Conference, International Magnesium Association, Wauconda, IL, USA, 117–134.Google Scholar
- [26]J. Grassi1, J. Campbell, M. Hartlieb, F. MajorMaterials Science Forum, 618–619 (2009), pp. 591-594View in Scopus
- [27]B. Cox, J. Zindel, M. Maj, L. Ouimet, A. Luo, D. Osborne, M. Osborne, R. Beals, E. McCarty, S. Robison, D. Weiss, D. Penrod, High Integrity Magnesium Automotive Components (HIMAC), in: Presentation at the 111th American Foundry Society Metalcasting Congress, Houston, TX, USA, May 15–18, 2007.Google Scholar
- [28]A.I. Taub, P.E. Krajewski, A.A. Luo, J.N. OwensJournal of Metals, 59 (2) (February 2007), pp. 48-57CrossrefView in Scopus
- [29]A.A. LuoChapter 8. Applications: Aerospace, Automotive and Other Structural Applications of Magnesiumbook chapterFundamentals of Magnesium Alloy Metallurgy, Woodhead Publishing Ltd, Cambridge, UK (2012)pp. 393–426Google Scholar
- [30]K.U. KainerMagnesium – Alloys and TechnologiesWiley-VCH, Weinheim, Germany (2003)Google Scholar
- [31]A.A. LuoJournal of Metals, 54 (2) (2002), pp. 42-48View in Scopus
- [32]H.-H. Becker, Status, Potential & Challenges for Automotive Magnesium Applications from the Point of View of an OEM, in: Presentation at 65th Annual World Magnesium Conference, May 18–20, 2008, Warsaw, Poland.Google Scholar
- [33]Y. Michiura, Current Magnesium Research & Application in Automotive Industry in Japan, in: Presentation at International Automotive Body Congress, November 7–8, 2007, Troy, MI, USA.Google Scholar
- [34]J.S. Balzer, P.K. Dellock, M.H. Maj, G.S. Cole, D. Reed, T. Davis, T. Lawson, G. SimondsStructural Magnesium Front End SupportSAE Technical Paper 2003-01-0185SAE International, Warrendale, PA (2003)Google Scholar
- [35]M. Hoeschl, W. Wagener, J. WolfBMW's Magnesium–aluminium Composite Crankcase, State-of-the-art Light Metal Casting and ManufacturingSAE Technical Paper 2006-01-0069SAE International, Warrendale, PA (2006)Google Scholar
- [36]C.J. Duke, S. LoganLightweight Magnesium Spare Tire CarrierProceedings of the 64th Annual World Magnesium Conference, International Magnesium Association, Wauconda, IL 60084, USA (2007), pp. 75-80View in ScopusGoogle Scholar
- [37]G.D. Wardlow, A Changing World with Different Rules – New Opportunities for Magnesium Alloys?, in: Presentation at the 64th Annual World Magnesium Conference, Vancouver, BC, Canada, May 13th–15th, 2007.Google Scholar
- [38]O. Pashkova, I. Ostrovsky, Y. Henn, Present State and Future of Magnesium Application in Aerospace Industry, in: Presentation at New Challenges in Aeronautics, Moscow, 2007.Google Scholar
- [39]J. HillisThe Effects of Heavy Metal Contamination on Magnesium Corrosion PerformanceSAE Technical Paper No. 830523SAE International, Warrendale, PA, USA (1983)Google Scholar
- [40]R.E. Brown, E. LeeMagnesium Usage Grew Rapidly in 1930–1950W.J. Poole, K.U. Kainer (Eds.), Proceedings of 9th International Conference on Magnesium Alloys and Their Applications (July 8–12, 2012), pp. 453-460Vancouver, BC, CanadaCrossrefView in Scopus
- [41]B.R. Powell, P.E. Krajewski, A.A. LuoChapter 4: Magnesium Alloysbook chapterMaterials Design and Manufacturing for Lightweight Vehicles, Woodhead Publishing Ltd, Cambridge, UK (2010)pp. 114–168Google Scholar
- [42]E.F. EmleyPrinciples of Magnesium TechnologyPergamon Press (1966)Google Scholar
- [43]S. Schumann, H. FriedrichThe Use of Magnesium in Cars – Today and in the FutureB. Mordike, K. Kainer (Eds.), Magnesium Alloys and Their Applications, Werkstoff-Informationsgesellschaft, Frankfurt, Germany (1998), pp. 3-13Google Scholar
- [44]H. Friedrich, S. SchumannJournal of Materials Processing Technology, 117 (2001), pp. 276-281View PDFView articleView in Scopus
- [45]F. Hollrigl-RostaLight Metal Age (1980), pp. 22-29View in Scopus
- [46]A. Hector, W. HeissMagnesium Die-castings as Structural Members in the Integral Seat of the New Mercedes-Benz RoadsterSAE Technical Paper No. 900798SAE, Warrendale, PA (1990)Google Scholar
- [47]D. AlexanderAutomotive Engineering International (May 2004), pp. 22-24View in Scopus
- [48]L. Riopelle, Magnesium Applications, in: International Magnesium Association (IMA) Annual Magnesium in Automotive Seminar, Livonia, MI, April 20, 2004.Google Scholar
- [49]S. GibbsMetal Casting Design and Purchasing (July/August 2010), pp. 29-33View in Scopus
- [50]J. Aragones, K. Goundan, S. Kolp, R. Osborne, L. Ouimet, W. PinchDevelopment of the 2006 Corvette Z06 Structural Cast Magnesium CrossmemberSAE International Technical Paper No. 2005-01-0340SAE International, Warrendale, Pennsylvania (2005)Google Scholar
- [51]J. Greiner, C. Doerr, H. Nauerz, M. GraeveThe New ‘7G-TRONIC’ of Mercedes-Benz: Innovative Transmission Technology for Better Driving Performance, Comfort, and Fuel EconomySAE Technical Paper No. 2004-01-0649SAE International, Warrendale, PA, USA (2004)Google Scholar
- [52]S. Koike, K. Washizu, S. Tanaka, T. Baba, K. KikawaSAE Technical Paper No. 2000-01-1117SAE International, Warrendale, PA, USA (2000)Google Scholar
- [53]B. Powell, et al., Progress Toward a Magnesium-intensive Engine: The USAMP Magnesium Powertrain Cast Components Project, SAE 2004 Transactions, Journal of Materials & Manufacturing Paper No. 2004-1-0654, SAE International, Warrendale, PA, USA, 250–259.Google Scholar
- [54]B.R. PowellMagnesium Powertrain Cast ComponentsPublished in FY2008 Annual Progress Report for Automotive Lightweighting MaterialsU.S. Department of Energy, Washington, D.C (April 2009)
- [55]International Magnesium AssociationMagnesium's Tough Strength Endures Abuse to Protect Portable Electronic DevicesInternational Magnesium Association, Wauconda, IL, USA (2008)Google Scholar
- [56]International Magnesium AssociationLighter Magnesium Improves Power Tool PerformanceInternational Magnesium Association, Wauconda, IL, USA (2008)Google Scholar
- [57]C.L. Mendis, C.J. Bettles, M.A. Gibson, C.R. HutchinsonMaterials Science and Engineering A, 435/436 (2006), pp. 163-171View PDFView articleView in Scopus
- [58]A.A. Luo, P. Fu, L. Peng, X. Kang, Z. Li, T. ZhuMetallurgical and Materials Transactions A, 43A (2012), pp. 360-368CrossrefView in Scopus
- [59]P. Fu, L. Peng, H. Jiang, J. Chang, C. ZhaiMaterials Science and Engineering A, 486 (2008), pp. 183-192Crossref
- [60]A.A. Luo, R.K. Mishra, B.R. Powell, A.K. SachdevMaterials Science Forum, 706–709 (2012), pp. 69-82View in Scopus
- [61]A.A. Luo, W. Shi, K. Sadayappan, E.A. NybergMagnesium Front End Research and Development: Phase I Progress Report of a Canada–China–USA CollaborationProceedings of IMA 67th Annual World Magnesium Conference, International Magnesium Association (IMA), Wauconda, IL, USA (2010)Google Scholar
- [62]M. Easton, A. Beer, M. Barnett, C. Davies, G. Dunlop, Y. Durandet, S. Blacket, T. Hilditch, P. BeggsJOM, 60 (11) (2008), pp. 57-62CrossrefView in Scopus
- [63]F. Zhu, C.C. Chou, K.H. Yang, X. Chen, D. Wagner, S. Bilkhu, A.A. LuoInternational Journal of Crashworthiness, 17 (5) (2012), pp. 540-552CrossrefView in Scopus
- [64]S. Logan, A. Kizyma, C. Patterson, S. RamaLightweight Magnesium-intensive Body StructureSAE International Technical Paper No. 2006-01-0523SAE International, Warrendale, PA, USA (2006)Google Scholar
- [65]W. Wen, A.A. Luo, T. Zhai, Y. Jin, Y.-T. Cheng, I. HoffmannScripta Materialia, 66 (2012), 10.1016/j.scriptamat.2012.08.010View at publisher
- [66]H.A. Patel, N. Rashidi, D.L. Chen, S.D. Bhole, A.A. LuoMaterials Science and Engineering A, 546 (2012), pp. 72-81View PDFView articleView in Scopus
- [67]A.A. Luo, J.F. Quinn, Y.-M. Wang, T.M. Lee, R. Verma, D.A. Wagner, J.H. Forsmark, X. Su, J. Zindel, M. Li, S.D. Logan, S. Bilkhu, R.C. McCuneLight Metal Age (April 2012), pp. 54-58View in Scopus
- [68]National Research CouncilIntegrated Computational Materials Engineering: A Transformational Discipline for Improved Competitiveness and National SecurityThe National Academies Press, Washington, DC, USA (2008)Google Scholar
- [69]M. Li, A.A. Luo, Integrated Computational Materials Engineering for Magnesium, Published in FY2011 Annual Progress Report for Automotive Lightweighting Materials, U.S. Department of Energy, Washington, D.C., USA, http://www1.eere.energy.gov/vehiclesandfuels/pdfs/lm_11/4_usamp_cooperative_research.pdf.Google Scholar
- [70]T.M. PollockScience, 328 (2010), pp. 986-987View at publisherCrossrefView in Scopus