본 논문 요약은 ['Naiyi Li']가 작성하고 ['Trans Tech Publications']에서 발행한 ['Magnesium Advances and Applications in North America Automotive Industry'] 논문을 기반으로 작성되었습니다.
1. 개요:
- 제목: 북미 자동차 산업의 마그네슘 발전 및 응용 (Magnesium Advances and Applications in North America Automotive Industry)
- 저자: Naiyi Li
- 발행 연도: 2005년
- 발행 학술지/학회: Materials Science Forum
- 키워드: 자동차 산업 응용 (Application automotive industry), 컴퓨터 모델링 (Computer modeling)
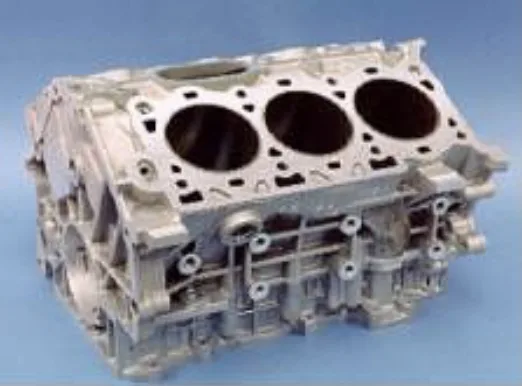
2. 초록 또는 서론
초록:
마그네슘은 차량 성능 요구 사항을 충족하기 위한 차량 중량 감소 능력으로 인해 강철, 알루미늄 및 폴리머 복합재를 대체할 매력적인 대안으로 점점 더 인식되고 있습니다. 기업 평균 연비 (CAFÉ) 기준을 충족하고 향후 차량 중량 감소를 극대화하기 위해 재료 크리프 저항이 요구되는 구조 및 파워트레인 부품 모두에서 마그네슘 응용 분야가 크게 증가할 것으로 예상됩니다. 본 논문의 전반부는 경량 금속 주조, 마그네슘 파워트레인 주조 부품 및 구조용 주조 마그네슘 개발을 포함한 최근 자동차 마그네슘 연구 개발 (R&D) 프로그램에 대한 개요를 제공합니다. 이러한 프로그램은 USCAR (United States Council for Automotive Research) 및 미국 에너지부의 지원을 받습니다. DaimlerChrysler Corporation, Ford Motor Company 및 General Motors로 구성된 우산 조직인 USCAR은 협력적이고 경쟁 전 연구를 통해 미국 자동차 산업의 기술 기반을 더욱 강화하기 위해 1992년에 설립되었습니다. 지난 10년 동안 마그네슘 주조 산업은 성장했지만 마그네슘 다이캐스팅의 재료 및 제조 공정 비용으로 인해 자동차 산업에 대규모로 구현하는 데 어려움이 있었습니다. 결과적으로 Ford Motor Company는 미국 국립 표준 기술 연구소 (National Institute of Standards and Technology)의 첨단 기술 프로그램과 협력하여 CORMAG (Cost Reduced Magnesium Die Castings Using Heated Runners) 프로그램을 시작했습니다. 본 논문의 후반부에서는 CORMAG 프로그램의 목표, 진행 상황 및 영향에 대해 간략하게 설명합니다. 또한 본 논문에서는 2004년형 Ford F-150 경트럭 전면 지지 어셈블리 및 2005년형 Ford GT 계기판 구조와 같은 특정 마그네슘 응용 분야를 소개합니다.
서론:
마그네슘은 많은 자동차 응용 분야에서 허용 가능한 비용으로 자동차 중량을 줄이는 입증된 능력을 가진 구조 재료로 사용되어 왔습니다 [1,2]. 마그네슘이 점점 더 매력적인 이유는 충돌 에너지 흡수 요구 사항을 동시에 충족하면서 부품 중량을 크게 줄일 수 있는 능력 때문이며, 강철, 알루미늄 및 폴리머 복합재를 대체할 수 있는 실행 가능한 재료로 자리매김하고 있습니다. 본 논문에서는 마그네슘의 세 가지 주요 속성을 강조합니다.
a. 낮은 밀도: 마그네슘 합금은 밀도가 1.8 kg/L로 경쟁 재료보다 훨씬 가볍습니다. 폴리머 복합재보다 20%, 알루미늄 합금보다 30%, 강철 및 아연 합금보다 75% 더 가볍습니다.
b. 탁월한 주조성: 마그네슘은 탁월한 주조성을 나타내어 얇은 벽 두께 (1.0 ~ 1.5 mm)와 최소 드래프트 각도 (1 ~ 2도, 알루미늄의 일반적인 각도의 약 1/2)를 가진 부품 생산이 가능합니다. 마그네슘의 우수한 유체 흐름 능력은 복잡한 강철 구조물 어셈블리를 대체할 수 있는 대형 주조물을 만들 수 있게 합니다. 예로는 2004년형 Ford F-150 [2]의 라디에이터 지지대, 2005년형 Ford GT [3]의 계기판, 그리고 연성, 에너지 흡수 및 충격 저항이 중요한 스티어링 휠 등이 있습니다. 예를 들어, 강철 크로스-카 빔 계기판 (IP)은 35개 이상의 부품으로 구성될 수 있지만, 이에 상응하는 다이캐스트 마그네슘 IP는 5개 부품만 필요합니다.
c. 우수한 표면 특성: 다이캐스트 마그네슘의 표면 "스킨"은 벌크 재료보다 향상된 기계적 특성을 나타냅니다 [4]. 이러한 특성으로 인해 더 얇고, 리브가 있는, 더 가벼운 마그네슘 다이캐스팅이 가능하며, 재료 비용을 절감하면서 단위 면적당 높은 강도를 유지하여 더 무거운 알루미늄 및 플라스틱 부품과 경쟁할 수 있습니다.
이러한 장점에도 불구하고 마그네슘이 자동차 응용 분야에 널리 보급되는 데에는 상당한 장벽이 있습니다. 21세기 북미 자동차 산업에서 경량화의 필요성은 종종 생산 비용 통제의 필요성에 의해 우선 순위가 밀립니다. 마그네슘 다이캐스팅의 비용 경쟁력은 여전히 주요 장애물이며, 자동차 산업이 적극적으로 해결하기 위해 노력하는 복잡하고 역동적인 문제입니다.
본 논문은 두 부분으로 구성되어 있습니다. 첫 번째 부분은 Ford Motor Company가 참여한 두 가지 진행 중인 마그네슘 프로그램을 소개합니다. 두 번째 부분은 Ford Motor Company가 시작하고 구현할 마그네슘 연구 프로그램 중 하나에 초점을 맞추고 있으며, 가까운 미래에 업계 최초의 제조 기술을 개척하는 것을 목표로 합니다.
3. 연구 배경:
연구 주제 배경:
자동차 산업은 기업 평균 연비 (CAFÉ) 기준을 충족하고 연비를 향상시키기 위해 차량 중량을 줄여야 한다는 끊임없는 압력을 받고 있습니다. 마그네슘 합금은 강철, 알루미늄 및 폴리머 복합재에 비해 상당한 중량 감소 잠재력을 제공하므로 자동차 응용 분야에 매력적입니다. 그러나 마그네슘 다이캐스팅의 높은 비용은 광범위한 채택에 주요 장애물이었습니다.
기존 연구 현황:
1993년의 PNGV (Partnership for New Generation of Vehicles) [5]를 포함한 이전의 연구 개발 노력은 차량의 중량 감소의 중요성을 강조했습니다. 마그네슘 응용 분야를 촉진하기 위해 USCAR 및 USAMP의 조직적 리더십 하에 미국 에너지부의 지원을 받아 SCMD (Structural Cast Magnesium Development) 및 MPCC (Magnesium Powertrain Cast Components)와 같은 협력 프로그램 [6,7]이 설립되었습니다. 이러한 프로그램에는 주요 자동차 회사의 팀 구성원이 참여하며 섀시, 내부 및 차체 부품, 특히 엔진 크래들 및 마그네슘 집약적 엔진에서 마그네슘의 기술적 및 경제적 타당성을 평가하는 것을 목표로 합니다. 또한 BMW 및 VW와 같은 유럽 자동차 제조업체도 마그네슘 파워트레인 부품에 초점을 맞춘 연구 및 제조 프로그램을 시작했습니다 [9].
연구의 필요성:
마그네슘의 고유한 장점에도 불구하고 대체 재료에 비해 높은 제조 비용으로 인해 자동차 산업에서 더 광범위하게 응용하는 데 제한이 있습니다. 이러한 장벽을 극복하려면 마그네슘 다이캐스팅 공정의 비용 절감에 초점을 맞춘 연구가 매우 필요합니다. 특히, 더 크고 얇은 벽 구조 부품의 다이캐스팅과 관련된 문제를 해결하는 것은 마그네슘의 경쟁력을 높이고 자동차 제조에 더 널리 구현하는 데 필수적입니다.
4. 연구 목적 및 연구 질문:
연구 목적:
본 논문에 설명된 연구의 주요 목적은 자동차 응용 분야를 위한 비용 효율적인 마그네슘 다이캐스팅 기술을 조사하고 개발하는 것입니다. 이러한 포괄적인 목표는 USCAR 프로그램 (SCMD 및 MPCC)과 Ford가 시작한 CORMAG 프로그램을 검토하여 해결합니다. 본 연구는 구조 및 파워트레인 부품 모두에서 마그네슘의 타당성을 입증하고 제조와 관련된 비용 장벽을 극복하는 것을 목표로 합니다.
주요 연구:
본 논문에서 탐구하는 주요 연구 분야는 다음과 같습니다.
- USCAR 프로그램 (SCMD 및 MPCC): 엔진 크래들 및 마그네슘 집약적 엔진에 초점을 맞춰 경량 섀시, 내부 및 차체 부품에 마그네슘 합금을 사용하는 것의 기술적 타당성 및 비용-편익 비율을 결정합니다. MPCC 프로그램은 특히 비용 효율적인 성능 이점과 제조 가능성을 입증할 수 있는 마그네슘 집약적 파워트레인을 개발하는 것을 목표로 합니다.
- CORMAG 프로그램: 제조 비용을 절감하고 주조 수율을 개선하며 부품 품질을 향상시키기 위해 고압 마그네슘 다이캐스팅에 혁신적인 핫 러너 기술을 개발하고 구현합니다. 이 프로그램은 특히 크고 얇은 벽 주조물에 대한 기존 콜드 러너 시스템의 한계를 극복하는 데 중점을 둡니다.
연구 가설:
명시적으로 가설로 명시되지는 않았지만, 연구는 다음과 같은 암묵적인 가정 하에 진행됩니다.
- 마그네슘 다이캐스팅 비용은 핫 러너 시스템 (CORMAG)과 같은 혁신적인 공정 기술을 통해 크게 절감할 수 있습니다.
- 최적화된 설계-제조 규칙 및 고급 CAE 모델링은 마그네슘 다이캐스팅에서 주조 수율을 개선하고 스크랩을 줄일 수 있습니다.
- 특히 파워트레인 및 구조 응용 분야에서 마그네슘 부품은 자동차에 구현하는 것을 정당화하는 비용 효율적인 성능 이점을 제공할 수 있습니다.
5. 연구 방법론
연구 설계:
본 연구는 협력적 R&D 이니셔티브에 초점을 맞춘 프로그램 기반 접근 방식을 채택합니다. 응용 분야 중심 프로그램 (USCAR의 SCMD 및 MPCC)과 기술 중심 프로그램 (Ford의 CORMAG)을 모두 포함합니다. USCAR 프로그램은 특정 자동차 부품 범주에서 마그네슘의 타당성을 평가하도록 설계되었으며, CORMAG 프로그램은 특정 제조 기술을 개발하고 검증하도록 설계되었습니다.
자료 수집 방법:
본 논문은 주로 프로그램 목표, 접근 방식 및 예상 결과에 대한 개요를 제시합니다. 특정 마그네슘 응용 분야 (Ford F-150 전면 지지대, Ford GT 계기판) 및 프로그램 활동 (CORMAG 주조 시험)의 사례를 참조합니다. 참조된 프로그램 내의 자료 수집 방법에는 재료 테스트, 부품 성능 평가, 비용 분석 및 공정 최적화 연구가 포함될 가능성이 높습니다. CORMAG 프로그램은 특히 핫 러너 기술을 검증하기 위해 주조 시험 및 컴퓨터 모델링을 활용합니다.
분석 방법:
설명된 분석 방법은 주로 다음 사항에 중점을 둡니다.
- 프로그램 개요: USCAR 및 CORMAG 프로그램의 목표, 참가자 및 기술적 접근 방식을 설명합니다.
- 기술 설명: CORMAG 핫 러너 시스템의 원리 및 혁신을 설명합니다.
- 사례 연구: 마그네슘 응용 분야 및 주조 시험의 사례를 제시하여 마그네슘 및 CORMAG 기술의 잠재력을 설명합니다.
- 컴퓨터 모델링: CAE 소프트웨어 (EKK)를 활용하여 마그네슘 다이캐스팅, 특히 핫 러너 시스템 설계 및 최적화와 관련하여 금속 흐름, 열 전달 및 응고를 시뮬레이션합니다.
연구 대상 및 범위:
연구 대상은 주로 마그네슘 다이캐스팅 기술과 북미 자동차 산업에서의 응용에 초점을 맞춥니다. 범위는 다음을 포함합니다.
- 마그네슘 합금: CORMAG 주조 시험에 사용된 AM60B 합금을 구체적으로 언급합니다.
- 자동차 부품: 구조 부품 (전면 지지대, 엔진 크래들, 섀시 구조) 및 파워트레인 부품 (엔진 블록, 베드플레이트, 오일 팬, 전면 커버, 계기판)에 중점을 둡니다.
- 다이캐스팅 공정: 기존 핫 챔버 다이캐스팅과 CORMAG 핫 러너 다이캐스팅을 비교하고, 고압 다이캐스팅 (HPDC) 및 저압 영구 금형 (LPPM) 방법을 언급합니다.
- 컴퓨터 모델링 소프트웨어: 공정 시뮬레이션을 위해 EKK 소프트웨어를 활용합니다.
6. 주요 연구 결과:
주요 연구 결과:
본 논문은 다음과 같은 주요 연구 결과 및 프로그램 결과를 제시합니다.
- USCAR 프로그램 (SCMD 및 MPCC): 이러한 프로그램은 진행 중이며 자동차 구조 및 파워트레인에서 마그네슘의 기술적 및 경제적 타당성을 입증하는 것을 목표로 합니다. 개발 및 평가를 위해 특정 부품 (엔진 크래들, 마그네슘 집약적 엔진)을 식별했습니다. MPCC 프로그램은 Ford 2.0L V6 DURATEC 엔진을 마그네슘 부품으로 재설계하기 위한 기반으로 선택했습니다 (그림 1). SCMD 프로그램은 전면 구조 크래들 개발에 중점을 둡니다 (그림 2).
- CORMAG 프로그램: 이 프로그램은 300톤 IdraPrince 핫 챔버 기계를 CORMAG 핫 러너 기술로 성공적으로 개조했습니다. "뮬 툴" (얇은 벽 컴퓨터 케이스)을 사용한 초기 주조 시험이 성공적이었습니다. 그림 6은 기존 핫 챔버 및 CORMAG 핫 러너 공정으로 주조된 컴퓨터 케이스의 비교를 보여주며, CORMAG 공정에서 스프루 재료가 감소했음을 보여줍니다. EKK 소프트웨어를 사용한 컴퓨터 모델링은 핫 러너 시스템 설계 및 공정 매개변수를 최적화하는 데 사용되고 있습니다 (그림 7). 이 프로그램은 핫 러너 시스템을 위한 고속 작동 밸브 기술과 러너/인게이트 시스템 설계를 위한 소프트웨어 기반 모델링 도구를 개발하고 있습니다.
제시된 데이터 분석:
제시된 데이터는 주로 프로그램 설명, 목표 및 부품 및 주조 공정의 시각적 표현으로 구성됩니다. 그림 1과 2는 USCAR 프로그램의 목표 부품을 보여줍니다. 그림 3, 4 및 5는 CORMAG 프로그램에 사용된 핫 챔버 다이캐스팅 공정 및 툴링을 묘사합니다. 그림 6은 기존 공정과 CORMAG 공정으로 생산된 주조물을 시각적으로 비교하여 스프루 재료의 감소를 강조합니다. 그림 7은 EKK 소프트웨어의 시뮬레이션 결과를 보여주며, 주조 공정에서 온도 및 냉각 속도를 분석하는 데 적용됨을 보여줍니다. 분석 결과 CORMAG 프로그램은 마그네슘 다이캐스팅을 위한 핫 러너 기술 개발 및 검증에 진전을 보이고 있으며, 비용 절감 및 재료 활용도 향상 가능성이 있음을 시사합니다.
그림 목록:
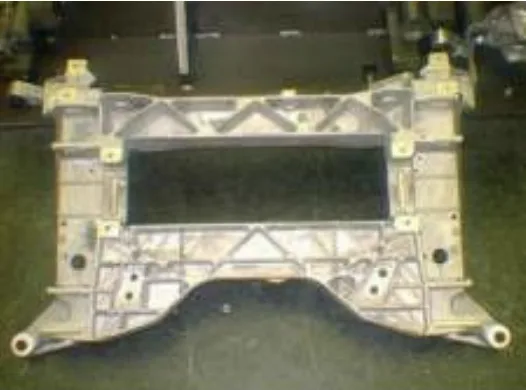
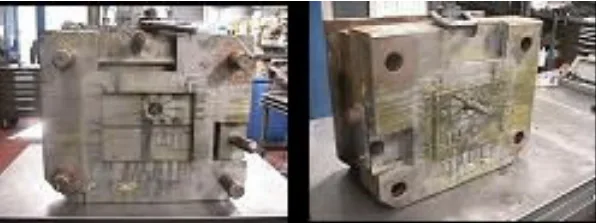
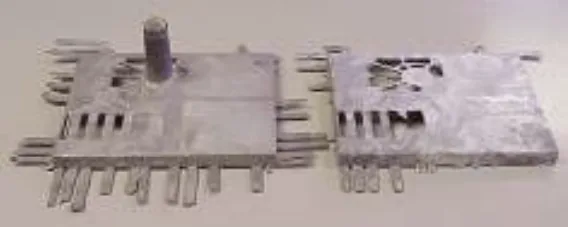
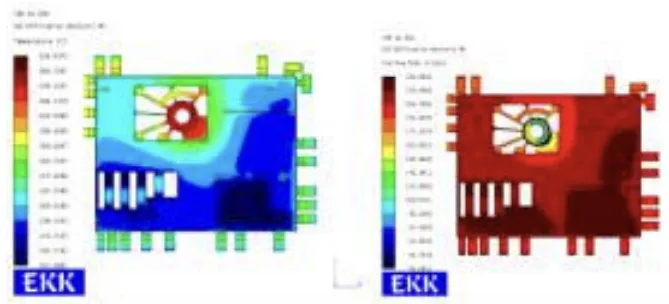
- 그림 1. DURATEC V6 엔진 블록 및 베드플레이트 (MPCC)
- 그림 2. 마그네슘 전면 엔진 크래들 주조물 (SCMD)
- 그림 3. 핫 챔버 공정 개략도
- 그림 4. 기존 핫 챔버 주조용 커버 및 이젝터 다이 세트
- 그림 5. CORMAG 공정용 커버 및 이젝터 다이 세트
- 그림 6. 핫 챔버 공정 (왼쪽) 및 CORMAG 핫 러너 공정 (오른쪽)으로 제작된 AM60B 컴퓨터 케이스.
- 그림 7. 이젝션 시 컴퓨터 케이스의 시뮬레이션된 온도 (왼쪽) 및 냉각 속도 (오른쪽)
7. 결론:
주요 결과 요약:
본 논문은 마그네슘 주조 산업이 성장했지만 마그네슘 다이캐스팅의 높은 비용이 자동차 산업에 대규모로 구현하는 데 여전히 장벽으로 남아 있다고 결론 내립니다. USCAR 프로그램 (SCMD 및 MPCC)과 CORMAG 프로그램은 이러한 문제를 해결하기 위한 핵심 이니셔티브입니다. USCAR 프로그램은 구조 및 파워트레인 부품에서 마그네슘의 타당성을 입증하는 데 중점을 두고 있으며, CORMAG 프로그램은 다이캐스팅 비용을 절감하고 효율성을 개선하기 위해 혁신적인 핫 러너 기술을 개발하고 있습니다. CORMAG 프로그램은 주조 시험 및 컴퓨터 모델링에서 유망한 초기 결과를 보여주며, 핫 러너 기술이 마그네슘 다이캐스팅을 발전시킬 잠재력이 있음을 시사합니다.
연구의 학문적 의의:
본 논문은 자동차 산업을 위한 마그네슘 다이캐스팅의 진행 중인 연구 개발 노력에 대한 귀중한 개요를 제공합니다. 혁신을 주도하고 기술적 및 경제적 장벽을 극복하는 데 있어 USCAR과 같은 협력 프로그램과 CORMAG과 같은 산업 주도 이니셔티브의 중요성을 강조합니다. 본 논문은 대량 생산 자동차 제조에서 마그네슘 응용과 관련된 과제와 기회에 대한 학문적 이해에 기여합니다.
실용적 의미:
설명된 연구는 자동차 및 다이캐스팅 산업에 중요한 실용적 의미를 갖습니다. CORMAG 핫 러너 시스템과 같은 비용 효율적인 마그네슘 다이캐스팅 기술의 성공적인 개발 및 구현은 차량에서 경량 마그네슘 부품의 더 넓은 채택을 가능하게 할 수 있습니다. 이는 연비 향상, 배기가스 감소 및 차량 성능 향상으로 이어져 CAFÉ 기준 및 지속 가능성 목표를 충족하는 데 기여할 수 있습니다.
연구의 한계 및 향후 연구 분야:
본 논문은 개요이며 연구 프로그램에 대한 자세한 실험 데이터 또는 심층 분석을 제시하지 않습니다. CORMAG 프로그램은 아직 개발 중이며 핫 러너 기술을 완전히 검증하고 복잡한 자동차 부품 생산에서 성능을 평가하려면 추가 연구가 필요합니다. 향후 연구는 다음 사항에 중점을 두어야 합니다.
- CORMAG 기술로 생산된 마그네슘 부품의 상세한 성능 평가.
- 기존 다이캐스팅 방법과 비교한 CORMAG 기술의 비용-편익 분석.
- 다양한 마그네슘 합금 및 부품 형상에 대한 핫 러너 시스템 설계 및 공정 매개변수 최적화.
- 내식성 및 접합 기술과 같은 마그네슘 채택에 대한 기타 장벽 해결.
8. 참고 문헌:
- [1] D. Albright, "Global Automotive Applications Review," the 13th Automotive Magnesium Seminar, International Magnesium Association, 2002.
- [2] J. Balzer et al., 'Structural Magnesium Front End Support Assembly', SAE paper 2003-01-0186.
- [3] T. Hubbert, X. Chen, N. Li, and S. Pineo, "2005 Ford GT Magnesium I/P Structure," SAE paper 2004-01-1261.
- [4] W. Sequeira and G. Dunlop, "Microstructure, Mechanical Properties and Fractography of High Pressure Diecast Magnesium Alloy AZ91D," p213-221, NADCA Congress 2003.
- [5] R. J. Osborne et al., "Design and Product Optimization for Cast Light Metals USAMP-LMD Project", AFS publication, ISBN 0-87433-246-X, 2001.
- [6] R .J. Osborne et al., "USCAR Project on Magnesium Structural Castings," Proc. 57th Annual World Magnesium Conference, International Magnesium Association, p1-5, 2000.
- [7] B. R. Powell, "The USAMP Magnesium Powertrain Cast Components Project," p141-150, NADCA Congress 2003.
- [8] R. S. Beals et al., "The USAMP Magnesium Powertrain Cast Components Project: Part III," Magnesium Technology, p11-17, TMS 2004.
- [9] J. Bohme et al, "AUDI Hybrid Magnesium Technology – A new approach to the lightweight engine block," Proc. 61st Annual World Magnesium Conference, International Magnesium Association, 2004.
- [10]R. J. Osborne et al., "Large, Complex Magnesium Chassis Structure Development", SAE 2004.
- [11]N. Li et al., "The Cost Reduced Magnesium Die Castings Using Heated Runners (CORMAG) Program and Computer Simulations," p395-403, NADCA Congress 2003.
9. 저작권:
- 본 자료는 "Naiyi Li"의 논문: "Magnesium Advances and Applications in North America Automotive Industry"를 기반으로 합니다.
- 논문 출처: doi:10.4028/www.scientific.net/MSF.488-489.931
본 자료는 위 논문을 요약한 것이며, 상업적 목적으로 무단 사용하는 것을 금지합니다.
Copyright © 2025 CASTMAN. All rights reserved.