1. 개요:
- 제목: About the impact on gravity cast salt cores in high pressure die casting and rheocasting (고압 다이캐스팅 및 레오캐스팅에서 중력 주조 염 코어의 영향에 대하여)
- 저자: Andreas Schilling, Daniel Schmidt, Jakob Glück, Niklas Schwenke, Husam Sharabi, Martin Fehlbier
- 발행 연도: 2022년
- 발행 학술지/학회: Simulation Modelling Practice and Theory
- Keywords:
- Cast salt cores (주조 염 코어)
- Lost core (로스트 코어)
- Core damage (코어 손상)
- Rheocasting (레오캐스팅)
- Flow-3D
- Simulation (시뮬레이션)
- Core testing (코어 테스트)
- High pressure die casting (고압 다이캐스팅)
2. 연구 배경:
- 연구 주제의 사회적/학문적 맥락:
- 고압 다이캐스팅(HPDC)은 독일에서 알루미늄 주조물의 60%, 비철 주조물의 절반 이상을 차지합니다.
- 특히 e-모빌리티 분야에서 내부 형상이 복잡해지는 주조 부품의 요구 증가로 인해 기존 슬라이더를 사용하는 복잡한 금형 기술의 한계에 도달하고 있습니다.
- 로스트 솔트 코어 기술은 슬라이드 시스템의 대안으로 내부 형상을 구현하는 새로운 기술입니다.
- 염 코어는 수용성으로 제거가 용이하여 다른 코어 기술에 비해 유리합니다.
- 기존 연구의 한계점:
- 코어의 생존 가능성은 염 코어의 공정 안전한 사용에 결정적인 문제입니다.
- 다이캐스팅 공정에서 코어 로딩은 주로 용융 금속의 유입 속도에 기인합니다.
- 고압 다이캐스팅 공정의 높은 압력과 유속으로 인해 코어에 높은 기계적 요구 조건이 설정됩니다.
- 연구의 필요성:
- 용융 온도를 낮추고 코어 로딩을 줄일 수 있는 레오캐스팅과 같은 대체 주조 방법 탐색이 필요합니다.
- 레오캐스팅 기술을 염 코어에 적용하여 부품 품질과 코어 내구성을 동시에 향상시킬 수 있는지 조사해야 합니다.
3. 연구 목적 및 연구 질문:
- 연구 목적:
- 레오캐스팅 기술이 염 코어에 적용될 수 있는지 조사합니다.
- 레오캐스팅이 염 코어를 사용할 때 부품 품질을 동시에 향상시킬 수 있는지 평가합니다.
- 핵심 연구 질문:
- 레오캐스팅은 기존 고압 다이캐스팅에 비해 고압 다이캐스팅에서 중력 주조 염 코어의 내구성에 어떤 영향을 미칩니까?
- 연구 가설:
- 레오캐스팅에 사용된 염 코어는 하중 감소를 경험할 것입니다.
- 레오캐스팅의 염 코어는 기존 HPDC에 비해 코어 생존 가능성이 향상될 것입니다. (이는 레오캐스팅에서 예상되는 더 낮은 코어 로딩에 의해 암시됩니다.)
4. 연구 방법론
- 연구 설계:
- Flow-3D 유체-구조 연동(FSI) 시뮬레이션을 사용한 시뮬레이션 연구.
- 염 코어에 대한 3점 굽힘 시험을 통한 실험적 검증.
- 시뮬레이션 결과와 실험 데이터의 비교.
- 데이터 수집 방법:
- 시뮬레이션: 기존 HPDC 및 레오캐스팅 시뮬레이션 모두에서 금형 충전 중 코어 로딩, 응력 분포 및 에너지 전달에 대한 수치 데이터.
- 실험: 다양한 하중 조건(프리즘 선하중 및 면하중)에서 20°C 및 180°C에서 3점 굽힘 시험에서 염 코어의 파단 강도 및 변형에 대한 물리적 측정.
- 분석 방법:
- FSI 시뮬레이션: Flow-3D Cast Version 5.0.1을 사용하여 금형 충전 및 염 코어에 작용하는 힘을 모델링했습니다. Rankine 최대-정규 응력 이론을 사용하여 코어 손상을 예측했습니다. 에너지 분석을 수행하여 다양한 주조 조건에서 코어로의 에너지 전달을 비교했습니다.
- 3점 굽힘 시험: 수정된 3점 굽힘 시험을 사용하여 염 코어의 파괴 임계 재료 데이터를 결정했습니다. 코어 강도와 변형을 특성화하기 위해 다양한 온도와 하중 유형에서 테스트를 수행했습니다.
- 연구 대상 및 범위:
- 염 코어 형상: 전체 길이 60mm, 정사각형 단면(변 길이 10mm), 중간 부분 변 길이 6mm 및 길이 20mm의 단순 형상이 사용되었습니다.
- 주조 공정: 기존 고압 다이캐스팅과 레오캐스팅을 시뮬레이션하고 비교했습니다.
- 재료: A356 (AlSi7Mg0,3) 합금 및 코어용 50 wt-% 염화나트륨과 50 wt-% 탄산나트륨의 염 혼합물.
- 시뮬레이션 파라미터: 기존 HPDC의 경우 피스톤 속도 6m/s, 레오캐스팅의 경우 2m/s. 기존 HPDC의 경우 용융 온도 630°C, 레오캐스팅의 경우 600°C.
5. 주요 연구 결과:
- 핵심 연구 결과:
- 레오캐스팅은 기존 HPDC에 비해 염 코어에 대한 하중을 크게 줄입니다.
- 가장 높은 코어 하중은 용융 금속의 첫 번째 충격 시 발생합니다.
- 코어 하중은 초기 충격 후 추가 금형 충전 중에는 거의 일정하게 유지됩니다.
- 레오캐스팅의 염 코어는 굽힘 시험에서 관찰된 파괴 한계보다 훨씬 낮은 응력 수준을 보입니다.
- 통계적/정성적 분석 결과:
- 굽힘 시험:
- 코어 온도가 높을수록 삼각형 핀으로 파단 하중이 감소합니다.
- 압축은 더 높은 온도에서 약간 증가합니다.
- 전체 하중 시험은 더 높은 분산으로 더 높은 파단 하중과 파단 연신율을 보여줍니다.
- 가장자리 영역의 미세한 입자 구조(두께 0.8 - 1.0 mm)가 굽힘 강도에 결정적입니다.
- 프리즘 20°C, 프리즘 180°C 및 전체 면 20°C 하중 조건에 대한 파단 강도 및 압축 데이터가 그림 5에 나와 있습니다.
- 시뮬레이션:
- 메쉬 의존성 연구 결과 염 코어의 경우 0.5mm 메쉬 크기가 정확도와 계산 시간 사이의 합리적인 절충안임을 보여주었습니다.
- 기존 HPDC(피스톤 속도 6m/s)에서 최대 정규 응력은 용융 금속 충격 직후 최대 13 MPa에 도달합니다(그림 10).
- 레오캐스팅(피스톤 속도 2m/s)에서 최대 정규 응력은 훨씬 낮으며 약 2.3 MPa입니다(그림 12).
- 용융 금속 흐름 방향으로 계산된 변위는 0.17mm로 굽힘 시험 결과와 비슷합니다.
- 에너지 분석은 레오캐스팅에서 염 코어로의 에너지 전달이 더 낮다는 것을 나타냅니다.
- 굽힘 시험:
- 데이터 해석:
- 시뮬레이션 결과는 실험적 굽힘 시험 데이터와 일치하며 시뮬레이션 모델이 합리적으로 정확함을 시사합니다.
- 시뮬레이션에서 나타난 바와 같이 레오캐스팅에서 훨씬 낮은 코어 하중은 기존 HPDC에 비해 코어 생존 가능성이 향상되었음을 시사합니다.
- 초기 용융 금속 충격은 코어 로딩에 가장 중요한 단계입니다.
- Figure Name List:
- Fig. 1. Salt core geometry and casting die (염 코어 형상 및 주조 금형).
- Fig. 2. Modified three-point bending test (수정된 3점 굽힘 시험).
- Fig. 3. Simulation model for the fluid structure interaction (FSI) calculation (유체-구조 연동(FSI) 계산을 위한 시뮬레이션 모델).
- Fig. 4. Detail of the core balance volume (코어 밸런스 볼륨 상세도).
- Fig. 5. Breaking strength and compression resulting from three-point bending tests (3점 굽힘 시험으로 인한 파단 강도 및 압축).
- Fig. 6. Sectional view of the salt core (6 x 6 mm) at 40x magnification (40배 확대된 염 코어(6 x 6 mm)의 단면도).
- Fig. 7. Mesh dependency of the stresses in the salt core after the impact of the melt (용융 금속 충격 후 염 코어의 응력에 대한 메쉬 의존성).
- Fig. 8. Balance volume of the salt core for energy consideration (purple) (에너지 고려를 위한 염 코어의 밸런스 볼륨(보라색)).
- Fig. 9. Simulated impact of the melt on the salt core (염 코어에 대한 용융 금속의 시뮬레이션된 충격).
- Fig. 10. Stress condition on salt core surface immediately after the first impact of the melt (용융 금속의 첫 번째 충격 직후 염 코어 표면의 응력 조건).
- Fig. 11. Deformation of the salt core after first impact of the melt (용융 금속의 첫 번째 충격 후 염 코어의 변형).
- Fig. 12. Stress condition on salt core surface immediately after the first impact of the semi solid melt (반용융 금속의 첫 번째 충격 직후 염 코어 표면의 응력 조건).
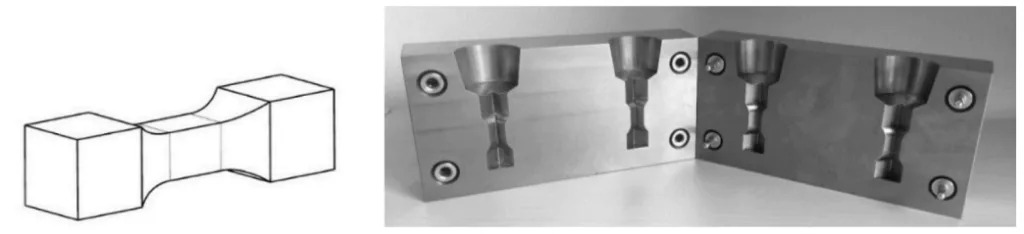
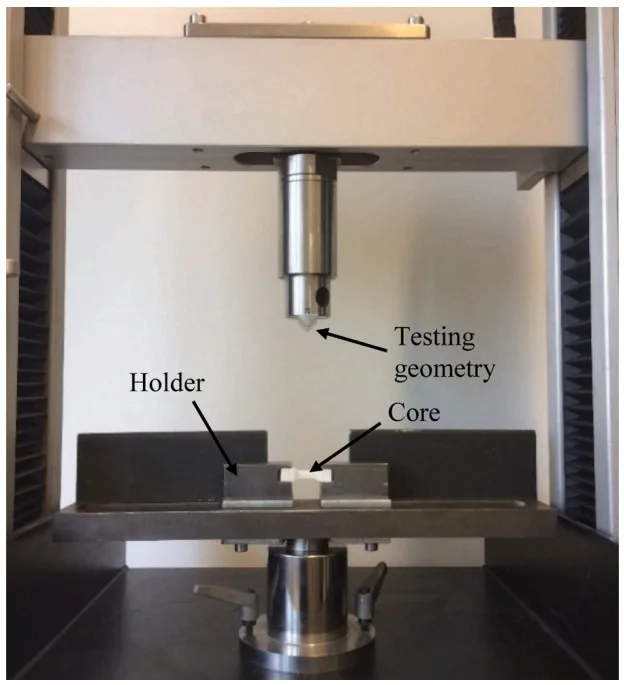
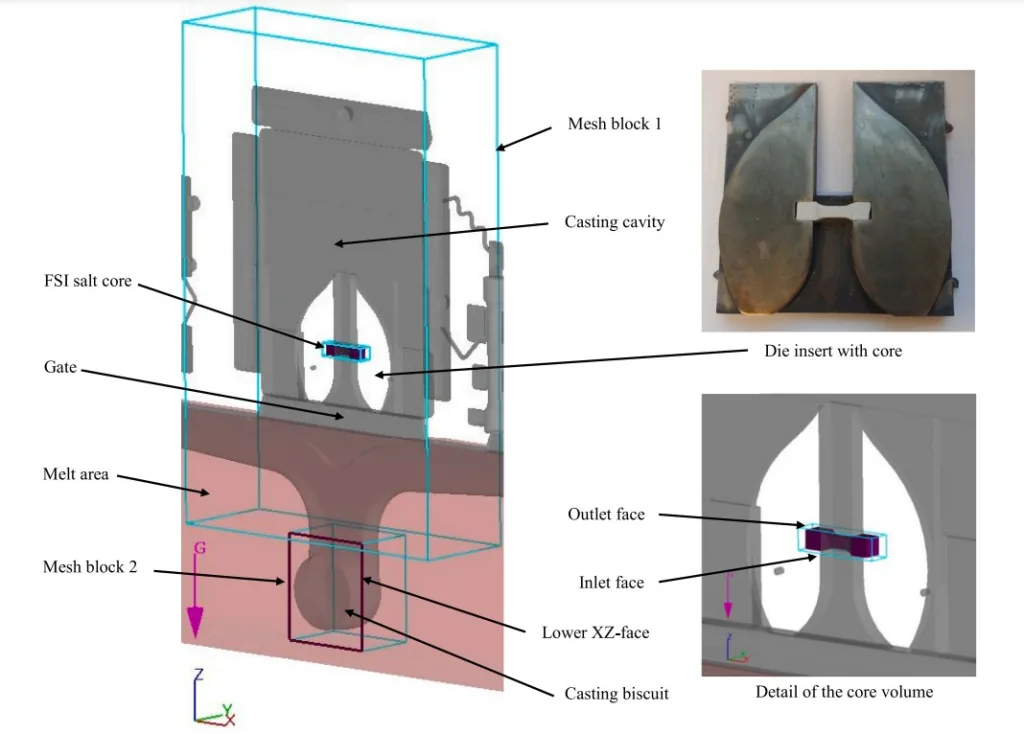
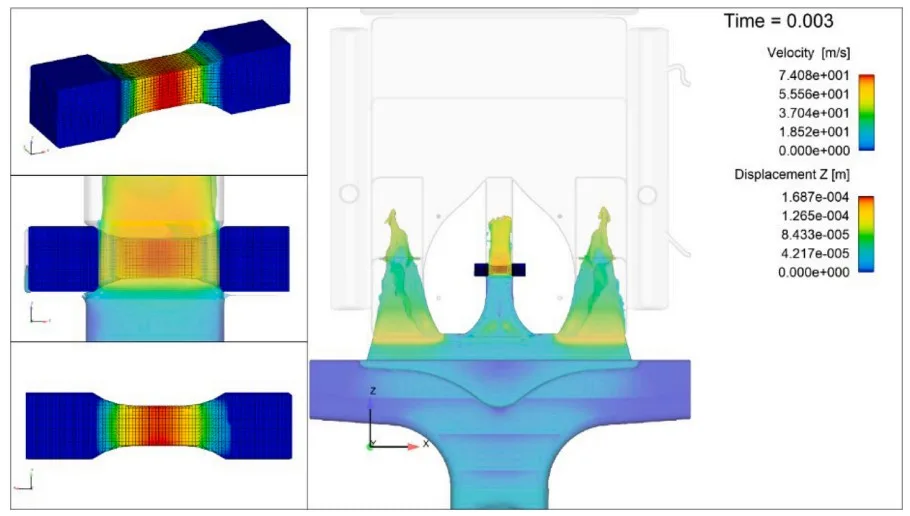
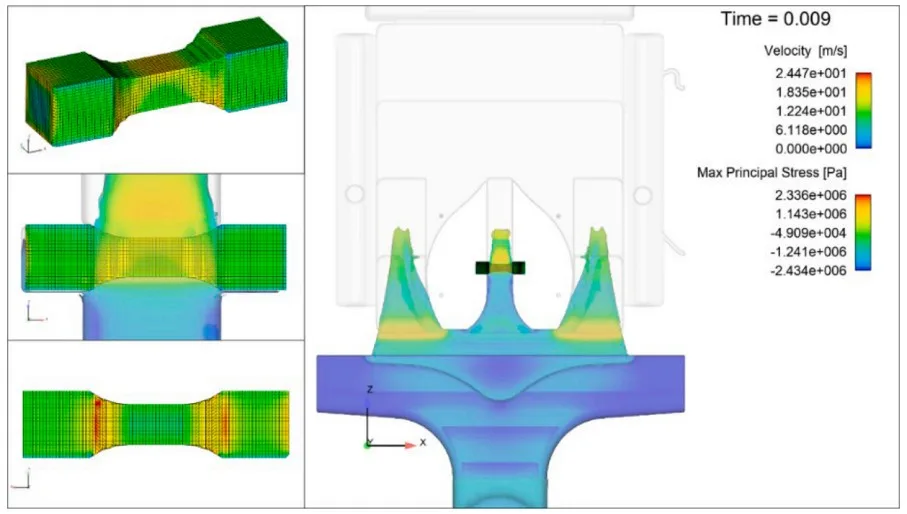
6. 결론 및 논의:
- 주요 결과 요약:
- 시뮬레이션 결과 레오캐스팅은 기존 HPDC에 비해 다이캐스팅 중 염 코어에 대한 하중을 크게 감소시키는 것으로 나타났습니다.
- 충격하는 용융 금속의 하중은 피스톤 속도 및 용융 금속 유량과 직접적인 관련이 있으며, 속도가 빠를수록 하중이 높아집니다.
- 기존 HPDC(피스톤 속도 6m/s)에서 염 코어의 장력은 염 코어의 인장 강도(11 MPa)를 초과하는 약 13 MPa에 도달할 수 있어 코어 파손 가능성을 시사합니다.
- 레오캐스팅(피스톤 속도 2m/s)에서 최대 응력은 인장 강도보다 훨씬 낮은 약 2.3 MPa로 크게 감소합니다.
- 연구의 학술적 의의:
- 본 연구는 로스트 솔트 코어 기술을 사용하는 응용 분야에서 레오캐스팅이 기존 HPDC의 실행 가능한 대안으로서의 잠재력을 입증합니다.
- 이 연구는 HPDC 및 레오캐스팅 공정 모두에서 코어 로딩 메커니즘에 대한 귀중한 통찰력을 제공합니다.
- 실험적 검증과 결합된 FSI 시뮬레이션의 사용은 염 코어 다이캐스팅 공정을 분석하고 최적화하기 위한 강력한 방법론을 제공합니다.
- 실무적 시사점:
- 레오캐스팅은 코어 손상을 줄여 염 코어 다이캐스팅의 공정 안전성과 신뢰성을 향상시키는 유망한 접근 방식을 제공합니다.
- 레오캐스팅에서 더 낮은 코어 하중은 염 코어를 사용하여 더 복잡하고 섬세한 내부 형상의 생산을 가능하게 할 수 있습니다.
- 연구 결과는 레오캐스팅에서 주조 파라미터, 특히 피스톤 속도와 용융 온도를 조정하면 코어 생존 가능성을 크게 향상시킬 수 있음을 시사합니다.
- 연구의 한계점:
- 시뮬레이션 모델은 주조 공정을 단순화하고 등온 흐름 및 균질한 염 코어 재료 속성을 가정합니다.
- 3점 굽힘 시험의 변형 속도(5 mm/min)는 주조 공정의 변형 속도(약 0.001초 이내에 변형 발생)보다 훨씬 느리므로 파괴 한계의 직접적인 비교 가능성에 영향을 미칠 수 있습니다.
- 실제 주조 시험에서 시뮬레이션 결과에 대한 실험적 검증이 여전히 필요합니다.
7. 향후 후속 연구:
- 후속 연구 방향:
- 주조 실험실에서 실제 다이캐스팅 및 레오캐스팅 시험을 통한 시뮬레이션 결과의 실험적 검증.
- 코어 로딩 및 부품 품질에 대한 다양한 레오캐스팅 파라미터의 영향 조사.
- 레오캐스팅에서 코어 강도와 생존 가능성을 더욱 향상시키기 위한 다양한 염 코어 재료 및 조성 탐색.
- 레오캐스팅 및 염 코어 기술이 주조 부품의 미세 구조 및 전체 품질에 미치는 영향 평가.
- 추가 탐구가 필요한 영역:
- 레오캐스팅에서 고상 형성 및 코어 로딩에 미치는 영향에 대한 상세 분석.
- 레오캐스팅 응용 분야를 위한 염 코어 설계 및 주조 공정 파라미터 최적화.
- 레오캐스팅 및 염 코어 기술을 사용하여 생산된 부품의 장기적인 내구성과 성능 조사.
8. 참고문헌:
- [1] B. Nogowizin, Theorie Und Praxis des Druckgusses, Fachverlag Schiele&Schön, Berlin, 2011.
- [2] Jelínek, P.; Adámková, E.: Lost Cores for High-Pressure Die Casting, Archives of Foundry Engineering, 14(2) 101-104, 2014, doi:10.2478/afe-2014-0045.
- [3] B. Fuchs, Salzkerntechnologie Für Hohlgussbauteile im Druckguss, Cuvillier Verlag, PhD, Erlangen, Nürnberg, 2014.
- [4] D. Pierri, C. Beck, Lost Core-Technologie - offen für alle, Chancen und Grundlagen des Verfahrens, In: Giesserei, Jg 103 (2016), 10/2016, DVS Media GmbH, Düsseldorf.
- [5] J. Yaokawa, D. Miura, K. Anzai, Strength of Salt Core Composed of Alkali Carbonate and Alkali Chloride Mixtures Made by Casting Technique, Mater. Trans. 48 (5) (2007) 1034-1041.
- [6] Schilling, A. et al.: Approach on simulation of solidification and shrinkage of gravity cast salt cores, Simulation Modelling Practice and Theory, 107, 102231, 2021, ISSN 1569-190X, doi:10.1016/j.simpat.2020.102231.
- [7] Kohlstädt, S.; Vynnycky, M.; Goeke, S.: On the CFD Modelling of Slamming of the Metal Melt in High-Pressure Die Casting Involving Lost Cores, Metals 2021, 11 (1), 78, doi:10.3390/met11010078.
- [8] Uggowitzer, P.J.; Gullo, G.; Wahlen, A.: Metallkundliche Aspekte bei der semi-solid Formgebung von Leichtmetallen, In: Vom Werkstoff zum Bauteil, ed. H. Kaufmann und P.J. Uggowitzer, LKR-Verlag Ranshofen, 95-107, 2000.
- [9] P. Das, Rheological Characterization of Semi-Solid A356 Aluminium Alloy, In: Solid State Phenomena, Vols. 192-193, Trans Tech Publications, Switzerland, 2013, pp. 329-334.
- [10] Fickel, P.: Hohl- und Verbundguss von Druckgussbauteilen – Numerische Auslegungsmethoden und experimentelle Verifikation, PhD, Stuttgart, 2017.
- [11] R.K. Freier, Aqueous Solutions, Data Inorg. Org. Compd. 2 (1978). Supplements, Gruyter, Berlin.
9. Copyright:
- 본 자료는 Andreas Schilling의 논문: About the impact on gravity cast salt cores in high pressure die casting and rheocasting을 기반으로 작성되었습니다.
- 논문 출처: https://doi.org/10.1016/j.simpat.2022.102585
본 자료는 위 논문을 바탕으로 요약 작성되었으며, 상업적 목적으로 무단 사용이 금지됩니다.
Copyright © 2025 CASTMAN. All rights reserved.