본 논문 요약은 ['MDPI']에서 발행한 ['Aluminium Foam and Magnesium Compound Casting Produced by High-Pressure Die Casting'] 논문을 기반으로 작성되었습니다.
1. 개요:
- 제목: 고압 다이캐스팅으로 생산된 알루미늄 폼 및 마그네슘 복합 주조 (Aluminium Foam and Magnesium Compound Casting Produced by High-Pressure Die Casting)
- 저자: Iban Vicario, Ignacio Crespo, Luis Maria Plaza, Patricia Caballero, Ion Kepa Idoiaga
- 발행 연도: 2016년
- 발행 저널/학술 단체: Metals
- 키워드: 고압 다이캐스팅 (HPDC); 하이브리드 마그네슘 알루미늄 폼 주조 복합재; 알루미늄 폼 코어; 마그네슘 주조 복합재
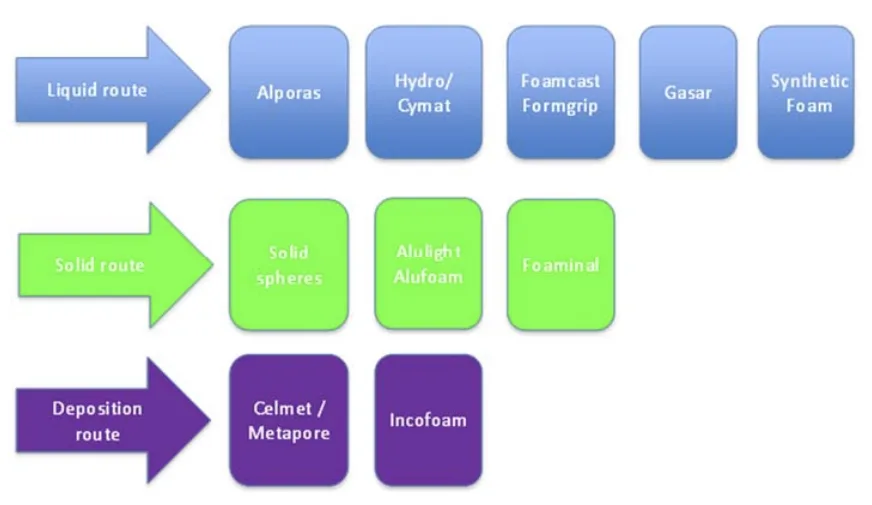
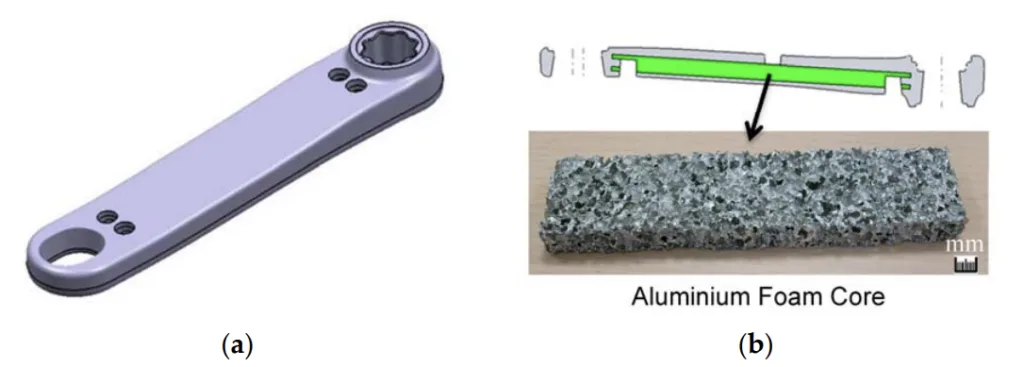
2. 초록 또는 서론
본 연구는 경량 복합 부품 생산을 위한 고압 다이캐스팅(HPDC) 기술을 조사합니다. 본 연구의 목표는 마그네슘 주조 부품에 코어로 사용되는 다양한 알루미늄 폼과 HPDC 사출 변수가 특성 및 무게에 미치는 영향을 평가하는 것입니다. 본 논문은 부품 특성과 무게 감소 사이의 균형을 달성하는 데 초점을 맞춰 HPDC 마그네슘 부품의 무게를 줄이기 위해 알루미늄 폼을 사용하는 타당성을 탐구합니다. 연구에서는 최종 주조 제품 품질에 대한 다양한 알루미늄 폼과 사출 변수의 영향을 평가하기 위해 알루미늄 폼 유형 및 밀도, 금속 온도, 플런저 속도 및 증압을 적절한 값의 범위 내에서 변화시켰습니다. 본 연구는 알루미늄 폼 코어를 사용하여 건전한 복합 주조물을 성공적으로 생산하여, 특히 자전거 부품 시연 부품과 같이 무게 감소가 필요한 응용 분야에서 마그네슘-알루미늄 폼 복합재 제조를 위한 HPDC의 잠재력을 입증했습니다.
3. 연구 배경:
연구 주제 배경:
본 연구의 주요 동인은 연료 소비 및 이산화탄소 배출량을 줄이기 위한 차량 설계, 특히 운송 산업에서 무게 감소에 대한 수요 증가입니다. 강철 및 철과 같은 무거운 재료를 플라스틱, 탄소 섬유, 알루미늄 및 마그네슘 합금과 같은 더 가벼운 대체재로 대체하는 것이 주요 추세입니다. 자전거 산업의 경우, 이러한 추세는 고성능 자전거에 탄소 섬유를 사용하고 강철, 알루미늄 및 티타늄을 사용하지 않는 명확한 경향에서 분명히 나타납니다. HPDC를 통해 생산된 마그네슘 부품은 이미 자동차 및 자전거 분야에서 활용되고 있으며, 업계는 마그네슘 경량 구조가 제공하는 경량성과 기계적 특성의 균형이 유리한 새로운 부품을 계속 찾고 있습니다. HPDC는 연간 5,000~10,000개 이상의 대량 생산에 경제적으로 실현 가능한 고생산성 공정으로 강조됩니다 [2].
기존 연구 현황:
기존 연구에서는 HPDC가 주조 품질에 영향을 미치는 수많은 변수에 의해 영향을 받는 복잡한 공정임을 인정합니다 [6]. 주요 변수에는 사출 변수, 다이 온도, 합금 주조성, 부품 형상, 냉각 속도 및 장비 유형이 포함됩니다. 내부 기공은 HPDC 부품의 알려진 단점이며, 다른 주조 방법에 비해 열처리 및 기계적 특성을 제한합니다. 기공을 완화하고 HPDC 부품 성능을 개선하기 위한 전략이 모색되고 있으며, 여기에는 새로운 HPDC 변형이 포함됩니다. 알루미늄-마그네슘 복합재를 사용하는 것은 무게 감소 전략 중 하나이며 [13], BWM 알루미늄-마그네슘 블록 [14]이 그 예입니다. 그러나 마그네슘과 알루미늄 코어 사이의 금속 결합을 달성하는 것은 알루미늄의 알루미나 표면층 때문에 어렵습니다 [15]. 무게 감소를 위한 대안적인 방법으로는 염 코어를 사용하여 속이 빈 부품을 만드는 것 [16-18]과 개선된 특성을 가진 새로운 HPDC 합금을 개발하는 것 [19]이 있습니다. 알루미늄 폼의 사용은 중요한 발전으로 인식되고 있으며 [20], "그림 1. 알루미늄 폼 생산에 가장 많이 사용되는 공정 중 일부"에 제시되고 "표 1. 다양한 폼 생산 경로의 장단점"에 요약된 다양한 생산 방법이 있습니다.
연구의 필요성:
HPDC를 통해 알루미늄 폼 코어를 사용하여 복합 주조물을 얻는 데 있어 주요 과제는 높은 속도와 특정 압력으로 인해 코어 변형 또는 붕괴를 방지하는 동시에 주조 결함을 피하는 것입니다. 본 논문은 알루미늄 폼 코어 복합 주조를 위한 HPDC 변수를 이해하고 제어하는 데 격차가 있음을 확인합니다. 따라서 알루미늄 폼 코어를 사용하여 고품질 복합 부품을 얻기 위해 HPDC 변수를 분석하고 제어하는 연구가 필요하며, 이 특정 응용 분야에서 코어 무결성 및 주조 건전성 문제를 해결해야 합니다.
4. 연구 목적 및 연구 질문:
연구 목적:
주요 연구 목적은 기계적 특성과 무게 감소 사이의 절충점을 달성하는 복합 주조물을 생산하기 위해 다양한 알루미늄 폼과 HPDC 사출 변수의 영향을 평가하는 것입니다. 궁극적인 목표는 현재 단조 알루미늄, 티타늄, 마그네슘 또는 탄소 섬유와 같은 재료를 사용하여 제조되는 자전거 로드를 생산하기 위한 HPDC 공정을 개발하는 것입니다. HPDC 기능에 맞게 재설계된 자전거 로드는 "그림 2. (a) 3D 로드 설계; 및 (b) 알루미늄 폼 코어 배치 및 예시 상세도"에 나와 있습니다.
핵심 연구:
핵심 연구 질문은 다음의 최적 조합을 결정하는 데 중점을 둡니다.
- 알루미늄 폼 유형 (Alporas ALPO-PLA-03 [27,28], Formgrip 기반 가공 폼 [29,30], 및 0.4% TiB2 AlSi12 Alulight 폼 [31-34]) 및 밀도.
- 금속 온도, 플런저 속도 및 증압을 포함한 HPDC 사출 변수.
- 코어 배치 및 스퀴즈 핀 적합성.
이러한 조사는 경량 구조 응용 분야에 적합한 알루미늄 폼 코어를 사용하여 건전한 마그네슘-알루미늄 복합 주조물을 생성하는 변수를 식별하는 것을 목표로 합니다.
연구 가설:
공식적인 가설로 명시되지는 않았지만, 연구는 다음과 같은 전제하에 진행됩니다.
- 알루미늄 폼의 유형과 밀도를 신중하게 선택하고 HPDC 변수를 최적화함으로써 상당한 무게 감소를 가진 건전한 마그네슘-알루미늄 복합 주조물을 생산할 수 있습니다.
- 외부 스킨이 있는 알루미늄 폼은 높은 사출 압력에 대한 향상된 견고성으로 인해 HPDC에서 코어로 더 나은 성능을 나타낼 것입니다.
- 적절한 코어 배치 및 제어된 사출 속도는 폼 손상을 방지하고 주조 품질을 보장하는 데 중요합니다.
5. 연구 방법론
연구 설계:
본 연구는 알루미늄 폼 유형과 HPDC 공정 변수의 체계적인 변화를 포함하는 실험 설계를 채택합니다. AM60B 합금과 세 가지 다른 알루미늄 폼 코어를 사용하여 주조물을 생산했습니다. 압력 효과가 폼 무결성에 미치는 영향을 평가하기 위해 다이캐스팅, 플라스틱 사출 및 HPDC 공정을 사용한 예비 테스트를 수행했습니다. 그 후, 마그네슘-알루미늄 폼 복합 주조물을 생산하기 위해 950톤 HPDC 기계에서 HPDC 시험을 수행했습니다.
자료 수집 방법:
자료 수집 방법은 다음과 같습니다.
- 육안 검사: 외부 주조 품질을 평가하고 육안으로 보이는 결함을 식별합니다.
- 방사선 투과 검사 (RX): 논문에 언급된 General Electric X-cube 44XL (160 kV)을 사용하여 내부 주조 건전성을 평가하고, 기공을 감지하고, 알루미늄 폼 코어 무결성을 검증합니다.
- 인장 시험: 복합 로드의 기계적 특성을 결정하기 위해 크로스헤드 속도 5 mm/min의 Instron 3369 기계를 사용하여 실온에서 UNE-EN ISO 6892-1 B:2010 표준에 따라 수행되었습니다.
분석 방법:
분석에는 다음이 포함되었습니다.
- 정성적 평가: 육안 및 RX 검사 결과를 정성적으로 분석하여 주조 결함, 폼 변형 및 코어 배치를 평가했습니다.
- 정량적 분석: 인장 시험 데이터를 사용하여 인장 응력, 극한 인장 강도 및 연신율을 계산하여 AM60B 합금과 복합 주조물 간의 기계적 특성을 정량적으로 비교할 수 있었습니다.
연구 대상 및 범위:
본 연구는 다음 사항에 중점을 두었습니다.
- 재료: AM60B 마그네슘 합금 및 세 가지 유형의 폐쇄 셀 알루미늄 폼: Alporas ALPO-PLA-03, Formgrip 기반 폼, 및 Alulight 0.4% TiB2 AlSi12 폼.
- 공정: 고압 다이캐스팅 (HPDC).
- 부품: 자전거 로드 시연 부품.
- 변수: 알루미늄 폼 유형 및 밀도, 금속 주조 온도 (680 °C 및 720 °C), 사출 압력 (16-80 MPa, 스퀴즈 핀의 경우 최대 200 MPa) 및 사출 속도 (20-80 m/s).
6. 주요 연구 결과:
핵심 연구 결과:
본 연구의 주요 결과는 다음과 같습니다.
- 금속 주조 온도: "그림 8. (a) 단락 채움 및 냉간 접합 결함; 및 (b) 가스 기공 결함"에서 관찰된 바와 같이, 단락 채움/냉간 접합 결함을 피하기 위해서는 AM60B 합금의 최소 주입 온도 720 °C가 필요했습니다.
- 알루미늄 폼 무결성: "표 4. 플라스틱 사출 후 알루미늄 폼의 무결성"에서 볼 수 있듯이, Alulight 폼은 Alporas 및 Formgrip 폼에 비해 HPDC 압력에 대한 우수한 저항성을 입증했습니다. 0.54~1.55 Kg/dm³ 밀도의 Alulight 폼은 40 MPa 압력을 성공적으로 견딜 수 있었습니다.
- 외부 스킨 중요성: "그림 9. AM60B로 덮인 중앙 알루미늄 코어"에서 설명된 바와 같이, Alulight와 같이 외부 스킨이 있는 알루미늄 폼은 마그네슘 과다 사출 중에 가스 기공 및 코어 붕괴를 방지했습니다. "그림 13. (a) 다이에 스킨이 있는 폼과 스킨이 없는 영역 배치; 및 (b) 스킨이 없는 영역에서 폼으로부터 가스 방출"에서 볼 수 있듯이, 스킨이 없거나 손상된 스킨이 있는 폼은 가스 기공을 유발했습니다.
- 코어 배치: "그림 15. 코어의 금속 흐름에 대한 수평 배치" 및 "그림 16. 금속 흐름에 대한 수직 코어 배치"에서 볼 수 있듯이, 금속 흐름에 대한 알루미늄 폼 코어의 수직 배치는 손상을 최소화하는 반면, 수평 배치는 전단 파단을 유발했습니다.
- 사출 속도: "그림 18. 감소된 2차 속도 (20 m/s) HPDC 주조 부품" 및 "그림 19. 표준 변수에서 코어 폼으로 사출된 HPDC"에서 볼 수 있듯이, 감소된 1차 사출 속도는 부품 품질에 부정적인 영향을 미치는 반면, 80 m/s의 2차 속도와 80 MPa 압력의 표준 HPDC 변수는 건전한 부품을 생성했습니다.
- 무게 감소: 0.56 Kg/dm³ 밀도의 Alulight 유형 알루미늄 폼을 사용하면 자전거 로드 시연 부품의 무게가 약 35% 감소했습니다.
- 기계적 특성: "표 5. 복합 로드의 획득된 특성"은 AM60B, 복합재 및 외삽된 복합재 특성의 인장 특성을 나타냅니다. 직접적인 화학적 결합은 달성되지 않았지만, 복합 로드는 무게 감소와 함께 합리적인 기계적 특성을 나타냈습니다.
제시된 데이터 분석:
데이터 분석 결과, Alulight 폼, 특히 외부 스킨으로 인해 테스트된 폼 중에서 HPDC 마그네슘 복합 주조에 가장 적합한 알루미늄 폼 코어임이 밝혀졌습니다. 외부 스킨은 사출 압력을 견디는 데 필요한 견고성을 제공하고 마그네슘 용융물로의 가스 방출을 방지합니다. 720°C의 금속 온도와 표준 사출 속도 및 압력을 포함한 최적의 HPDC 변수는 건전한 복합 주조물을 생산하는 데 중요합니다. 스퀴즈 핀은 과도한 압력으로 인해 알루미늄 폼 코어 근처 영역에 적합하지 않습니다. 달성된 35% 무게 감소는 경량 부품 제조에 대한 이 접근 방식의 잠재력을 입증합니다. 기계적 특성 분석은 솔리드 AM60B에 비해 복합재에서 항복 강도(YS) 및 극한 인장 강도(UTS)가 감소함을 나타내지만, 외삽된 값은 최적화된 설계 및 결합을 통해 복합 접근 방식이 무게와 성능의 실행 가능한 균형을 제공할 수 있음을 시사합니다.
그림 목록:
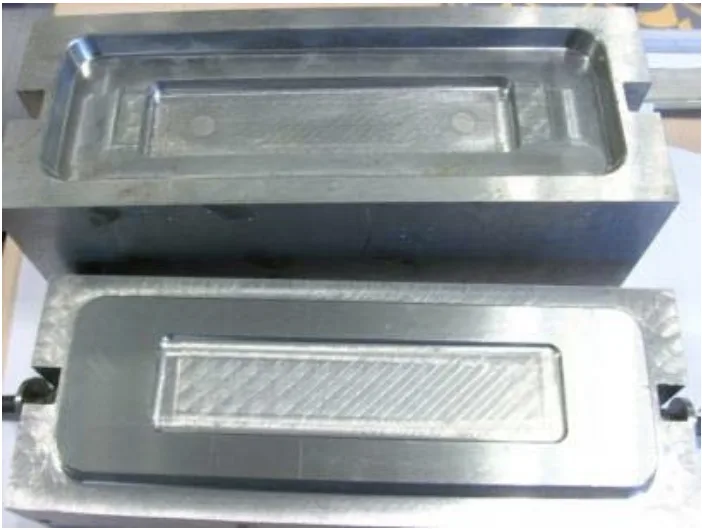
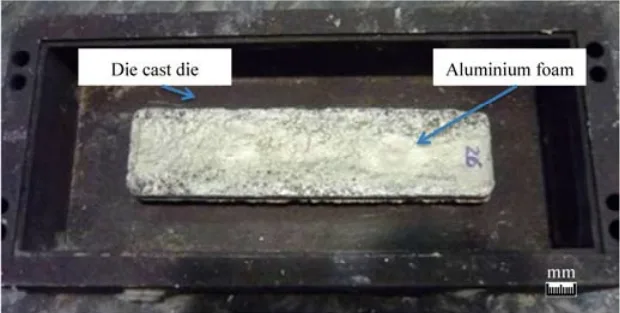
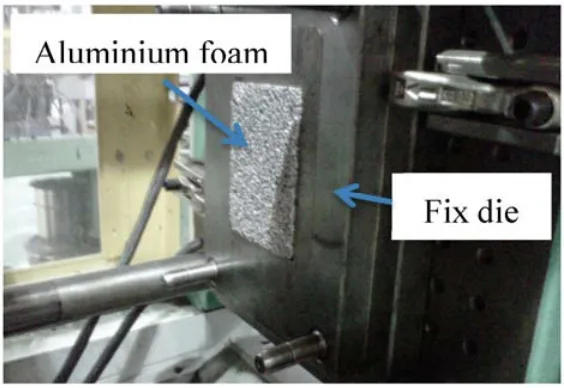
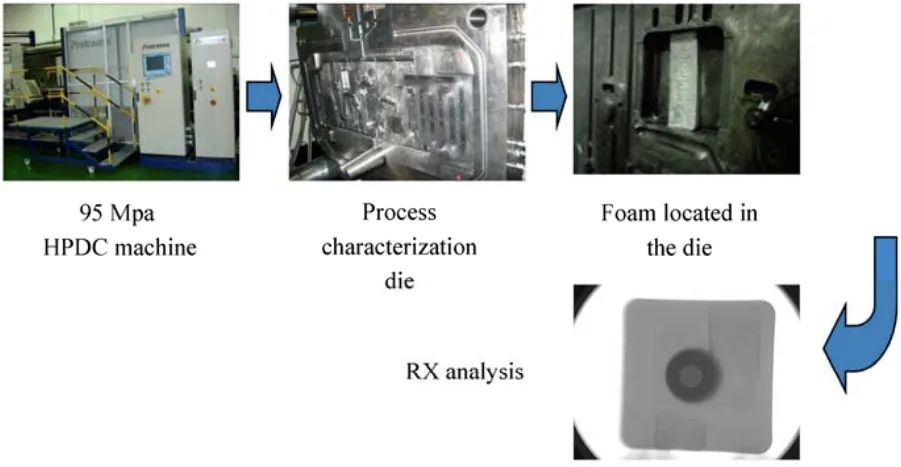
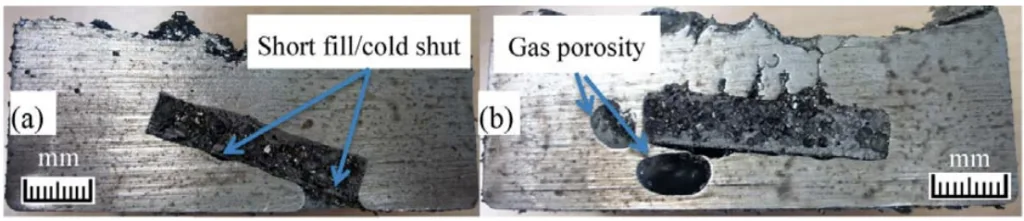
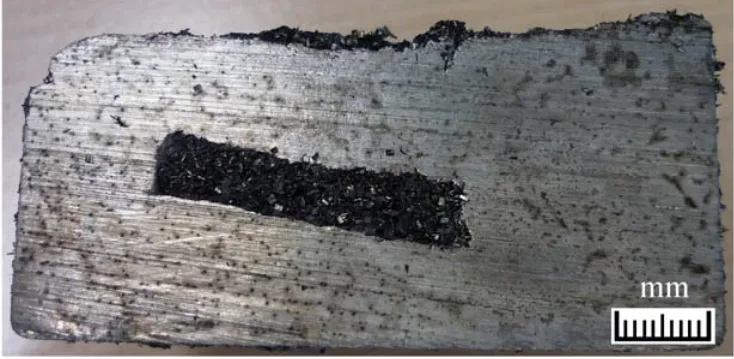
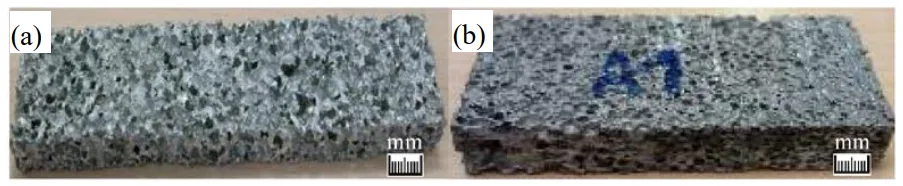
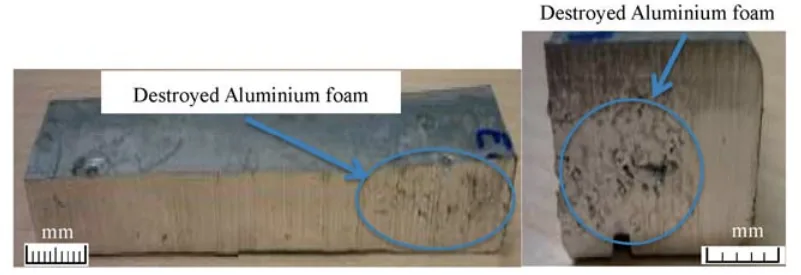
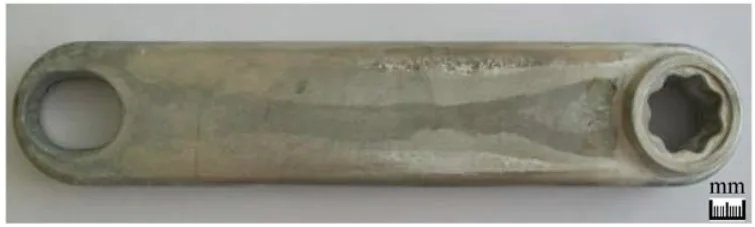
- 그림 1. 알루미늄 폼 생산에 가장 많이 사용되는 공정 중 일부.
- 그림 2. (a) 3D 로드 설계; 및 (b) 알루미늄 폼 코어 배치 및 예시 상세도.
- 그림 3. Alulight로 알루미늄 폼을 생산하는 금속 다이.
- 그림 4. 알루미늄 폼 위에 마그네슘을 다이캐스팅하는 금속 다이.
- 그림 5. 알루미늄 폼이 있는 플라스틱 사출 금형.
- 그림 6. 마그네슘-알루미늄 폼 코어 복합재를 얻기 위한 HPDC 공정.
- 그림 7. 알루미늄 폼 배치를 위한 고정 다이 캐비티의 고정 핀 상세도.
- 그림 8. (a) 단락 채움 및 냉간 접합 결함; 및 (b) 가스 기공 결함.
- 그림 9. AM60B로 덮인 중앙 알루미늄 코어.
- 그림 10. 알루미늄 폼에 대한 플라스틱 사출을 위한 다양한 구성.
- 그림 11. (a) Alpora의 폼 (0.25~0.4 Kg/dm³); 및 (b) Formgrip의 폼 (0.4~0.65 Kg/dm³).
- 그림 12. 완전히 파괴된 알루미늄 폼이 있는 HPDC 부품.
- 그림 13. (a) 다이에 스킨이 있는 폼과 스킨이 없는 영역 배치; 및 (b) 스킨이 없는 영역에서 폼으로부터 가스 방출.
- 그림 14. 스퀴즈 핀 적용 후 1.55 Kg/dm³ 알루미늄 폼.
- 그림 15. 코어의 금속 흐름에 대한 수평 배치.
- 그림 16. 금속 흐름에 대한 수직 코어 배치.
- 그림 17. 알루미늄 폼 내부 코어를 사용하여 마그네슘 HPDC로 만든 로드.
- 그림 18. 감소된 2차 속도 (20 m/s) HPDC 주조 부품.
- 그림 19. 표준 변수에서 코어 폼으로 사출된 HPDC.
7. 결론:
주요 결과 요약:
본 연구는 무게 감소 응용 분야를 위한 HPDC 마그네슘-알루미늄 폼 복합 주조물의 타당성을 성공적으로 입증했습니다. 폐쇄 셀 구조와 외부 스킨이 특징인 Alulight 유형 알루미늄 폼은 HPDC 마그네슘 과다 사출에 가장 효과적인 코어 재료임이 입증되었습니다. 720°C의 마그네슘 용융 온도를 유지하고 표준 사출 속도 및 압력을 사용하는 것을 포함하여 HPDC 변수를 최적화하는 것은 건전한 주조물을 얻는 데 중요합니다. 이 복합 접근 방식을 사용하여 자전거 로드 시연 부품에서 35%의 무게 감소가 달성되었습니다.
연구의 학문적 의의:
본 연구는 마그네슘 매트릭스 내에서 알루미늄 폼 코어를 사용하는 HPDC의 복합 주조에 대한 학문적 이해에 기여합니다. 알루미늄 폼 특성 (유형, 밀도, 스킨 존재) 및 HPDC 공정 변수가 결과 복합 주조 품질에 미치는 영향에 대한 귀중한 통찰력을 제공합니다. 본 연구는 HPDC 중 코어 무결성을 위해 알루미늄 폼의 외부 스킨의 중요성을 강조하고 코어 배치 및 사출 속도 제어에 대한 지침을 제공합니다.
실용적 의미:
본 연구 결과는 특히 경량화 솔루션을 모색하는 분야의 제조업에 중요한 실용적 의미를 갖습니다. 마그네슘-알루미늄 폼 복합재를 위한 입증된 HPDC 공정은 자동차, 항공 우주 및 스포츠 장비 응용 분야에서 더 무거운 재료를 대체할 수 있는 경량 부품의 대량 생산을 위한 실행 가능한 경로를 제공합니다. 자전거 로드 시연 부품은 자전거 산업에서 즉각적인 적용 가능성을 보여줍니다.
연구의 한계 및 향후 연구 분야:
확인된 주요 한계는 폼의 알루미나 층으로 인해 알루미늄 폼 코어와 마그네슘 매트릭스 사이에 화학적 결합이 부족하다는 것입니다. 이러한 결합 부족은 복합재의 기계적 특성 향상의 잠재력을 제한할 수 있습니다. 향후 연구는 다음 사항에 초점을 맞춰야 합니다.
- 마그네슘과의 금속 결합을 촉진하고 계면 강도를 개선하기 위해 Zn 기반 코팅과 같은 알루미늄 폼의 표면 처리 조사.
- 기계적 성능을 유지하거나 향상시키면서 무게 감소를 극대화하기 위한 HPDC 변수 및 부품 설계의 추가 최적화.
- 더 넓은 범위의 부품 형상 및 산업 응용 분야에 대한 이 복합 주조 접근 방식의 적용 탐구.
8. 참고 문헌:
- [1] Schultz, R. Aluminium Association Auto and Light Truck Group 2009 Update on North American Light Vehicle Aluminium Content Compared to the other Countries and Regions of the World. Phase II; Ducker Worlwide LLC: Troy, MI, USA, 2008; pp. 8–19.
- [2] Bonollo, F.; Urban, J.; Bonatto, B.; Botter, M. Gravity and low pressure die casting of aluminium alloys: A technical and economical benchmark. Metall. Ital. 2005, 97, 23-32.
- [3] Luo, A.A. Magnesium casting technology for structural applications. J. Magnes. Alloys 2013, 1, 2-22. [CrossRef]
- [4] Gertsberg, G.; Nagar, N.; Lautzker, M.; Bronfin, B. Effect of HPDC parameters on the performance of creep resistant alloys MRI153M and MRI230D. SAE Tech. Pap. 2005, 1, 1–7.
- [5] Otarawanna, S.; Laukli, H.I.; Gourlay, C.M.; Dahle, A.K. Feeding mechanisms in high-pressure die castings. Metall. Mater. Trans. A 2010, 41, 1836-1846. [CrossRef]
- [6] Bonollo, F.; Gramegna, N.; Timelli, G. High-pressure die-casting: Contradictions and challenges. JOM 2015, 67, 901-908. [CrossRef]
- [7] Yim, C.D.; Shin, K.S. Semi-solid processing of magnesium alloys. Mater. Trans. 2003, 44, 558–561. [CrossRef]
- [8] Sabau, A.S.; Dinwiddie, R.B. Characterization of spray lubricants for the high pressure die casting processes. J. Mater. Process. Technol. 2008, 195, 267–274. [CrossRef]
- [9] Kimura, R.; Yoshida, M.; Sasaki, G.; Pan, J.; Fukunaga, H. Characterization of heat insulating and lubricating ability of powder lubricants for clean and high quality die casting. J. Mater. Process. Technol. 2002, 130–131, 289-293. [CrossRef]
- [10] Puschmann, F.; Specht, E. Transient measurement of heat transfer in metal quenching with atomized sprays. Exp. Therm. Fluid Sci. 2004, 28, 607-615. [CrossRef]
- [11] Rogers, K.J.; Savage, G. In-cavity pressure sensors-errors, robustness and some process insights. Die Cast Eng. 2000, 44, 76-80.
- [12] Kong, L.X.; She, F.H.; Gao, W.M.; Nahavandi, S.; Hodgson, P.D. Integrated optimization system for high pressure die casting processes. J. Mater. Process. Technol. 2008, 201, 629-634. [CrossRef]
- [13] Keber, K.; Bormann, D.; Möhwald, K.; Hollander, U.; Bach, W. Compound casting of aluminium and magnesium alloys by High Pressure Die Casting. In Proceedings of the Magnesium 8th International Conference on Magnesium Alloys and Their Applications, Weimar, Germany, 26-29 October 2009; pp. 390-397.
- [14] Kunst, M.; Fischersworring-bunk, A.; Liebscher, C.; Glatzel, U.; Esperance, G.L.; Plamondon, P.; Baril, E.; Labelle, P. Microstructural characterization of Die Cast Mg-Al-Sr (AJ) Alloy. In Proceedings of the Magnesium: Proceedings of the 7th International Conference on Magnesium Alloys and Their Applications, Dresden, Germany, 6–9 November 2006; pp. 498-505.
- [15] Vicario, I. Study of high pressure die cast AZ91D magnesium alloy with surface treated aluminium 6063 cores for Al-Mg multi-material. In Proceedings of the 2nd Annual World Congress of Advanced Materials, Suzhou, China, 5-7 June 2013; pp. 7–21.
- [16] Yaokawa, J.; Miura, D.; Anzai1, K.; Yamada, Y.; Yoshii, H. Strength of salt core composed of alkali carbonate and alkali chloride mixtures made by casting technique. Mater. Trans. 2007, 5, 1034–1041. [CrossRef]
- [17] Moschini, R. Production of Hollow Components in HPDC through the Use of Ceramic Lost Cores; XXXI Congreso Tecnico di Fonderia: Vincenza, Italy, 2012; pp. 1–33.
- [18] Yamada, Y.; Yaokawa, J.; Yoshii, H.; Anzai, K.; Noda, Y.; Fujiwara, A.; Suzuki, T.; Fukui, H. Developments and application of expendable salt core materials for high pressure die casting to apply closed-deck type cylinder block. SAE Int. 2007, 32-0084, 1–5.
- [19] Vicario, I.; Egizabal, P.; Galarraga, H.; Plaza, L.M.; Crespo, I. Study of an Al-Si-Cu HPDC alloy with high Zn content for the production of components requiring high ductility and tensile properties. Int. J. Mater. Res. 2013, 4, 392-397. [CrossRef]
- [20] Benedick, C. Production and application of aluminium foam, past product potential revisited in the new millennium. Light Met. Age 2002, 60, 24-29.
- [21] Bausmesiter, J.; Weise, J. Structural Materials and Processes in Transportation, Metal Foams; John Wiley & Sons: Hoboken, NJ, USA, 2013; pp. 415-440.
- [22] Banhar, J. Metal foams: Production and stability. Adv. Eng. Mater. 2006, 9, 781–794. [CrossRef]
- [23] Coleto, J.; Goñi, J.; Maudes, J.; Leizaola, I. Applications and manufacture of open and closed cell metal foams by foundry routes. In Proceedings of International Congress Eurofond, La Rochelle, France, 2–4 June 2004; pp. 1-10.
- [24] Körner, C.; Hirschmann, M.; Wiehler, H. Integral Foam Moulding of Light Metals. Mater. Trans. 2006, 47, 2188-2194. [CrossRef]
- [25] Baumeister, J.; Weise, J. Application of aluminium-polymer hybrid foam sandwiches in battery housings for electric vehicles. Procedia Mater. Sci. 2014, 4, 301-330. [CrossRef]
- [26] Vesenjak, M.; Borovinšek, M.; Fiedler, T.; Higa, Y.; Ren, Z. Structural characterisation of advanced pore morphology (APM) foam elements. Mater. Lett. 2013, 110, 201-203. [CrossRef]
- [27] Miyoshi, T.; Itoh, M.; Akiyama, S.; Kitahara, A. Aluminium foam, “ALPORAS": The production process, properties and application. In Materials Research Society Symposium Proceedings, Boston, MA, USA, 1-3 December 1998; 1998; pp. 133-137.
- [28] Miyoshi, T.; Itoh, M.; Akiyama, S.; Kitahara, A. Alporas aluminum foam: Production process, properties, and applications. Adv. Eng. Mater. 2000, 2, 179–183. [CrossRef]
- [29] Gegerly, V.; Clyne, T.W. The formgrip process: Foaming of reinforced metals by gas release in precursors. Adv. Eng. Mater. 2002, 2, 175–178.
- [30] Gergely, V.; Curran, D.C.; Clyne, T.W. Advances in the melt route production of closed cell aluminium foams using gas-generating agents. In Proceedings of Global Symposium of Materials Processing and Manufacturing Processing & Properties of Lightweight Cellular Metals and Structures, Seattle, WA, USA, 17-21 February 2002; pp. 3-8.
- [31] Baumeister, J. Production technology for aluminium foam/steel sandwiches. In Proceedings of the International Conference on Metal Foams and Porous Metal Structures, Bremen, Germany, 14-16 June 1999; pp. 113-118.
- [32] Seeliger, H.W. Cellular Metals: Manufacture, properties, applications. In Proceedings of the MetFoam, Berlin, Germany, 23-25 June 2003; pp. 5-12.
- [33] Kováãik, J.; Simančík, F.; Jerz, J.; Tobolka, P. Reinforced aluminium foams. In Proceedings of the International Conference on Advanced Metallic Materials, Smolenice, Slovakia, 5–7 November 2003; pp. 154–159.
- [34] Braune, R.; Otto, A. Tailored blanks based on foamable aluminium sandwich material. In Proceedings of the International Conference on Metal Foams and Porous Metal Structures, Bremen, Germany, 14-16 June 1999; pp. 119-124.
- [35] Gutiérrez-Vázquez, J.A.; Oñoro, J. Fabricación y comportamiento de espumas de aluminio con diferente densidad a partir de un precursor AlSi12. Rev. Metal. 2010, 46, 274–284. [CrossRef]
9. 저작권:
- 본 자료는 "Iban Vicario 외"의 논문: "Aluminium Foam and Magnesium Compound Casting Produced by High-Pressure Die Casting"을 기반으로 합니다.
- 논문 출처: https://doi.org/10.3390/met6010024
본 자료는 상기 논문을 요약한 것으로, 상업적 목적으로 무단 사용하는 것을 금지합니다.
Copyright © 2025 CASTMAN. All rights reserved.