본 논문 요약은 [Publisher]에서 발표된 논문 알루미늄 폼과 마그네슘 복합재료의 고압 다이캐스팅 생산을 기반으로 작성되었습니다.
1. 개요:
- 제목: 고압 다이캐스팅으로 생산된 알루미늄 폼과 마그네슘 복합재료 주조
- 저자: 이반 비카리오, 이그나시오 크레스포, 루이스 마리아 플라자, 파트리시아 카발레로, 이온 케파 이도이아가
- 발행 연도: 2016년
- 발행 저널/학회: Metals, MDPI 발행
- 키워드: 고압 다이캐스팅 (HPDC); 하이브리드 마그네슘 알루미늄 폼 주조 복합재료; 알루미늄 폼 코어; 마그네슘 주조 복합재료
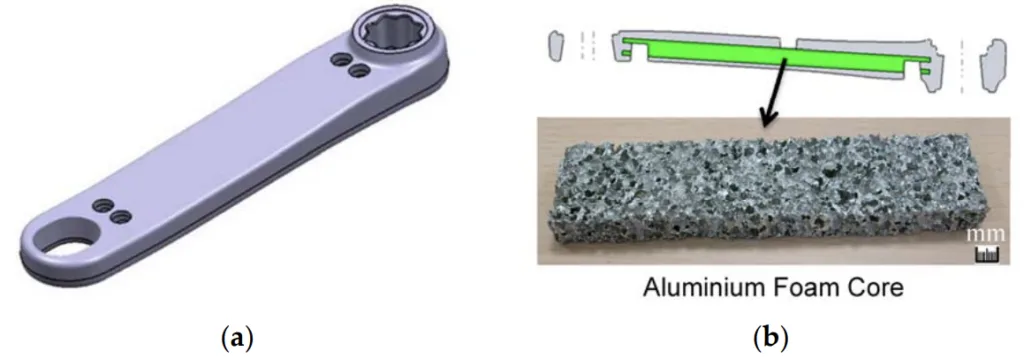
2. 연구 배경:
오늘날 자동차 및 운송 산업에서 연료 소비와 이산화탄소 배출량은 차량 설계의 주요 초점이며, 경량 재료를 사용하여 차량의 무게를 줄이는 것을 촉진하고 있습니다. 강철 및 철 주조 부품을 플라스틱, 탄소 섬유, 알루미늄 및 마그네슘 합금과 같은 더 가벼운 대체재로 대체하는 것이 중요한 추세입니다. 특히 자전거 산업에서는 고성능 자전거를 위해 탄소 섬유가 강철, 알루미늄, 티타늄을 대체하는 경향이 뚜렷합니다.
고압 다이캐스팅(HPDC)으로 생산된 마그네슘 부품은 이미 자동차 및 자전거 응용 분야에 사용되고 있습니다. 그러나 업계는 마그네슘 경량 구조가 제공하는 경량성과 기계적 특성의 균형을 활용할 수 있는 새로운 부품을 지속적으로 찾고 있습니다. HPDC는 대량 생산(연간 약 5,000~10,000개 이상)에 경제적으로 실현 가능한 고생산성 공정입니다.
기존 연구 및 HPDC 응용 분야에는 한계가 있습니다. HPDC의 주요 단점은 금속 주입 중 난류 흐름으로 인해 발생하는 내부 기공입니다. 이 기공은 열처리를 복잡하게 만들고 다른 주조 방법보다 달성 가능한 기계적 특성을 저하시킵니다. 또한 이종 재료로 복합 주물을 만드는 데 어려움이 있습니다. 알루미늄-마그네슘 복합재료가 연구되고 있지만, 알루미늄 폼 코어와 마그네슘 사이의 금속 결합을 달성하는 것은 알루미늄 폼 표면의 알루미나 층 때문에 어렵습니다. HPDC에서 중공 부품을 만들기 위해 염 코어를 사용하는 것과 같은 대안적인 방법도 코어 재료 제거의 복잡성을 야기하며 부품 설계를 제한할 수 있습니다. 따라서 이러한 한계를 극복하고 HPDC 부품의 성능을 더욱 향상시키기 위한 혁신적인 접근 방식을 모색할 필요성이 있습니다.
본 연구는 마그네슘 주물 내부에 알루미늄 폼 코어를 사용하여 HPDC에서 부품 무게를 줄이는 필요성을 해결합니다. 이 접근 방식은 무게 감소와 기계적 특성 사이의 절충점을 달성하는 것을 목표로 합니다.
3. 연구 목적 및 연구 질문:
연구 목적:
본 연구의 주요 목적은 다양한 유형의 알루미늄 폼과 고압 다이캐스팅(HPDC) 주입 변수가 마그네슘 복합 주물의 특성에 미치는 영향을 평가하는 것입니다. 목표는 알루미늄 폼을 마그네슘 주물 부품 내 코어로 사용하여 무게 감소와 허용 가능한 기계적 특성 사이의 균형을 이루는 건전한 복합 주물을 생산하는 것입니다.
주요 연구 질문:
- HPDC로 생산된 마그네슘-알루미늄 폼 복합 주물의 품질에 다양한 알루미늄 폼 유형(Alporas, Formgrip, Alulight)이 어떻게 영향을 미치는가?
- 마그네슘-알루미늄 폼 복합 부품의 최종 주조 품질에 금속 온도, 플런저 속도, 증압과 같은 HPDC 주입 변수가 미치는 영향은 무엇인가?
- HPDC로 생산된 마그네슘-알루미늄 폼 복합재료는 자전거 부품과 같은 구조적 응용 분야에 적합한 허용 가능한 기계적 특성을 유지하면서 상당한 무게 감소를 달성할 수 있는가?
연구 가설:
명시적으로 가설로 언급되지는 않았지만, 연구는 다음과 같은 전제하에 진행됩니다.
- 알루미늄 폼 코어의 유형을 신중하게 선택하고 HPDC 주입 변수를 최적화함으로써 건전한 마그네슘-알루미늄 폼 복합 주물을 생산하는 것이 가능하다.
- 마그네슘 주물에 알루미늄 폼 코어를 사용하면 솔리드 마그네슘 부품에 비해 상당한 무게 감소를 가져올 것이다.
- 복합 주물의 기계적 특성은 알루미늄 폼 코어의 유형과 HPDC 공정 변수에 의해 영향을 받을 것이다.
4. 연구 방법론
연구 설계:
본 연구에서는 HPDC를 사용한 마그네슘-알루미늄 폼 복합 주물의 생산을 조사하기 위해 실험적 연구 설계를 채택했습니다. 연구는 최종 주조 품질 및 특성에 미치는 영향을 평가하기 위해 알루미늄 폼 코어의 유형과 주요 HPDC 주입 변수를 체계적으로 변경하는 것을 포함했습니다.
데이터 수집 방법:
생산된 복합 주물의 품질은 다음을 사용하여 평가되었습니다.
- 육안 검사: 주물을 육안으로 검사하여 표면 결함 및 전체 형태를 확인했습니다.
- 방사선 검사 (RX): 160kV에서 General Electric X-cube 44XL을 사용하여 X선 분석을 수행하여 내부 건전성을 평가하고, 기공을 감지하고, 마그네슘 매트릭스 내 알루미늄 폼 코어의 무결성 및 위치를 확인했습니다.
- 인장 시험: 기계적 특성은 5mm/min의 크로스헤드 속도로 Instron 3369 전자 기계식 시험기를 사용하여 상온에서 UNE-EN ISO 6892-1 B:2010 표준에 따라 수행된 인장 시험을 통해 평가되었습니다. 인장 응력, 극한 인장 강도(UTS) 및 연신율을 측정했습니다.
분석 방법:
- 정성적 분석: 육안 및 RX 검사 데이터를 사용하여 주조 품질을 정성적으로 평가하고, 단락, 냉간 접합, 가스 기공 및 폼 코어 무결성과 같은 결함에 초점을 맞췄습니다.
- 정량적 분석: 인장 시험 데이터를 정량적으로 분석하여 솔리드 AM60B 마그네슘 합금 주물과 마그네슘-알루미늄 폼 복합 주물의 기계적 특성을 결정했습니다. 통계 분석을 사용하여 특성을 비교하고 알루미늄 폼 코어의 영향을 평가했습니다.
연구 대상 및 범위:
- 재료:
- 마그네슘 합금: AM60B가 주조 마그네슘 합금으로 사용되었습니다.
- 알루미늄 폼: 세 가지 유형의 폐쇄 기공 알루미늄 폼이 평가되었습니다.
- Alporas ALPO-PLA-03 (Alcan)
- Formgrip 기반 폼 (Tecnalia 가공)
- Alulight 0.4% TiB2 AlSi12 폼 (Alulight)
- 공정: 고압 다이캐스팅 (HPDC)
- 부품: 자전거 로드 부품이 복합 주조 접근 방식의 타당성과 이점을 평가하기 위한 시연 부품으로 선택되었습니다.
- 변수 변경:
- 알루미늄 폼 유형 및 밀도
- 금속 주조 온도 (680 °C 및 720 °C)
- 주입 압력 (플라스틱 주입 시뮬레이션의 경우 16-40 MPa, HPDC의 경우 20-80 MPa)
- 플런저 속도 (1단계 0.25 m/s, 2단계 20-80 m/s)
- 코어 배치 (금속 흐름에 수평 및 수직)
- 증압 핀 적용
5. 주요 연구 결과:
주요 연구 결과:
- 건전한 복합 주물 달성: 본 연구에서는 HPDC를 사용하여 건전한 마그네슘-알루미늄 폼 복합 주물을 성공적으로 생산했습니다.
- 폼 스킨 및 배치의 중요성: 알루미늄 폼 코어에 외부 연속 스킨이 존재하고 다이 캐비티 내부에 폼을 올바르게 배치하는 것이 양질의 부품을 얻는 데 중요한 것으로 밝혀졌습니다. 스킨은 마그네슘 주입 중 가스 방출 및 폼 붕괴를 방지합니다. 금속 흐름에 대한 폼 코어의 수직 배치가 수평 배치보다 우수했습니다.
- Alulight 폼 성능: 테스트된 폼 중에서 외부 스킨을 가진 Alulight 폼이 HPDC 공정을 지원하고 무결성을 유지하는 데 가장 우수한 성능을 보였습니다.
- 무게 감소: 마그네슘-알루미늄 폼 복합 자전거 부품은 솔리드 마그네슘 부품에 비해 약 35%의 무게 감소를 달성했습니다.
- 최적화된 변수: 마그네슘 합금의 최소 주입 온도 720 °C와 2단계 주입 속도 80 m/s 및 특정 압력 80 MPa의 표준 HPDC 변수가 건전한 복합 주물을 생산하는 데 적합한 것으로 확인되었습니다. 증압 핀은 폼 코어를 손상시키는 것으로 나타났습니다.
통계적/정성적 분석 결과:
- 주조 온도 효과 (그림 8): AM60B를 680 °C에서 주조하면 "단락/냉간 접합" 결함 및 가스 기공이 발생했습니다. 온도를 720 °C로 높이면 이러한 결함이 제거되었습니다.
- 플라스틱 주입 시뮬레이션 (표 4, 그림 10): HPDC 압력을 시뮬레이션한 플라스틱 주입 테스트에서 Alulight 폼 (밀도 0.54-1.55 Kg/dm³)은 붕괴 없이 40 MPa 압력을 견딜 수 있는 반면, Alporas (0.25-0.4 Kg/dm³) 및 Formgrip (0.4-0.55 Kg/dm³) 폼은 16 MPa 및 40 MPa 모두에서 실패했습니다.
- 증압 핀 영향 (그림 14): 알루미늄 폼 코어에 직접 증압 핀 압력 (최대 200 MPa)을 가하면 밀도에 관계없이 폼이 파괴되었습니다.
- 코어 배치 효과 (그림 15 및 16): 금속 흐름에 대한 폼 코어의 수평 배치는 폼의 전단 파괴를 초래했습니다. 수직 배치는 손상을 최소화하고 작은 수축 기공만 발생했습니다.
- 주입 속도 효과 (그림 18 및 19): 2단계 주입 속도를 20 m/s로 줄이면 "매우 불량한 충진"이 발생했습니다. 80 m/s 2단계 속도의 표준 HPDC 변수는 충진이 양호하고 작은 응고 기공만 있는 부품을 생산했습니다.
- 기계적 특성 (표 5):
- AM60B (솔리드): 항복 강도 (YS) = 141 ± 4.3 MPa, 극한 인장 강도 (UTS) = 219 ± 3.6 MPa, 연신율 = 3 ± 0.5%.
- 복합재료: YS = 79 + 1.75 MPa, UTS = 122 ± 2.16 MPa, 연신율 = 3 + 0.5%.
- 외삽된 복합재료 특성 (면적 감소 47%): YS = 149 ± 3.3 MPa, UTS = 230 ± 4.1 MPa, 연신율 = 3 ± 0.5%.
데이터 해석:
결과는 HPDC를 통한 마그네슘-알루미늄 폼 복합 주물 생산이 가능하지만 알루미늄 폼 유형을 신중하게 선택하고 공정 변수를 최적화해야 함을 나타냅니다. 외부 스킨을 가진 Alulight 폼은 HPDC 압력을 견디고 가스 기공을 방지하는 능력으로 인해 이 응용 분야에 적합합니다. 코어 배치 및 주입 속도는 주조 품질에 영향을 미치는 중요한 변수입니다. 상당한 무게 감소가 달성되었지만 복합재료의 초기 기계적 특성은 솔리드 마그네슘보다 낮습니다. 그러나 외삽된 값은 최적화된 설계 및 재료 활용을 통해 복합재료가 상당한 무게 절감을 제공하면서 인장 강도 측면에서 솔리드 마그네슘의 기계적 성능과 일치하거나 약간 능가할 수 있음을 시사합니다.
그림 목록:
- 그림 1: 알루미늄 폼 생산에 가장 많이 사용되는 공정 중 일부.
- 그림 2: (a) 3D 로드 설계; 및 (b) 알루미늄 폼 코어의 배치 및 예시 상세도.
- 그림 3: Alulight로 알루미늄 폼을 생산하는 금속 다이.
- 그림 4: 알루미늄 폼 위에 마그네슘을 다이캐스팅하는 금속 다이.
- 그림 5: 알루미늄 폼이 있는 플라스틱 사출 금형.
- 그림 6: 마그네슘-알루미늄 폼 코어 복합재료를 얻기 위한 HPDC 공정.
- 그림 7: 알루미늄 폼 배치를 위한 고정 다이 캐비티의 고정 핀 상세도.
- 그림 8: (a) 단락 및 냉간 접합 결함; 및 (b) 가스 기공 결함.
- 그림 9: AM60B로 덮인 중앙 알루미늄 코어.
- 그림 10: 알루미늄 폼에 대한 플라스틱 주입을 위한 다양한 구성.
- 그림 11: (a) Alpora's 폼 (0.25 ~ 0.4 Kg/dm³); 및 (b) Formgrip's 폼 (0.4 ~ 0.65 Kg/dm³).
- 그림 12: 완전히 파괴된 알루미늄 폼이 있는 HPDC 부품.
- 그림 13: (a) 스킨 영역과 비스킨 영역이 있는 스킨 폼의 다이 내 배치; 및 (b) 비스킨 영역에서 폼으로부터의 가스 방출.
- 그림 14: 증압 핀 적용 후 1.55 Kg/dm³ 알루미늄 폼.
- 그림 15: 코어의 금속 흐름에 대한 수평 배치.
- 그림 16: 코어의 금속 흐름에 대한 수평 배치.
- 그림 17: 내부 알루미늄 폼 코어가 있는 마그네슘 HPDC로 만든 로드.
- 그림 18: 감소된 2단계 속도 (20 m/s) HPDC 주조 부품.
- 그림 19: 표준 변수에서 코어 폼으로 주입된 HPDC.
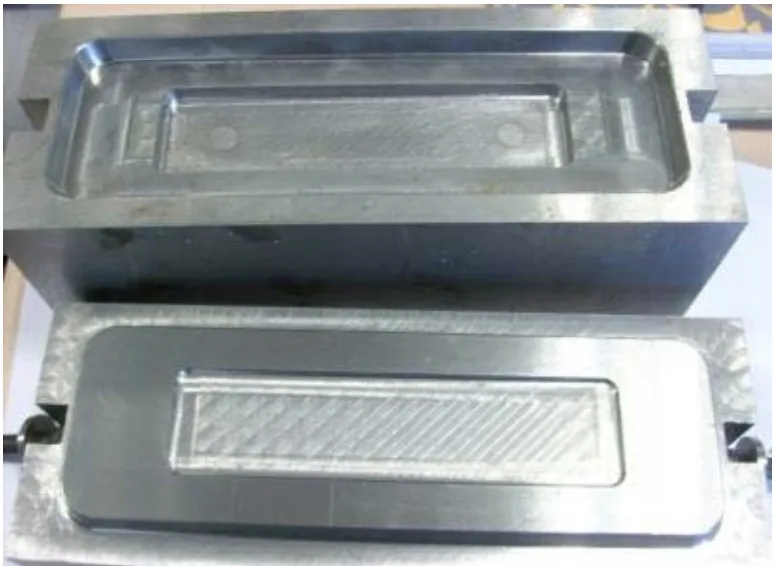
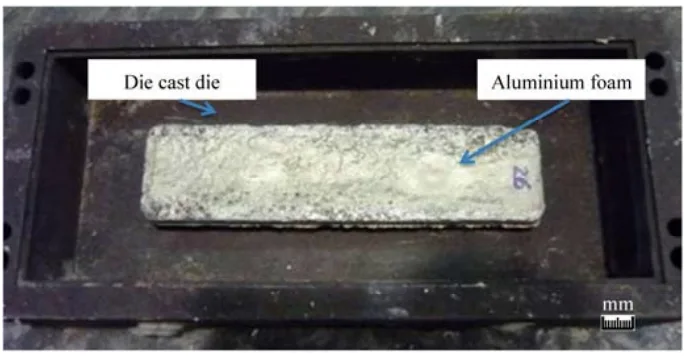
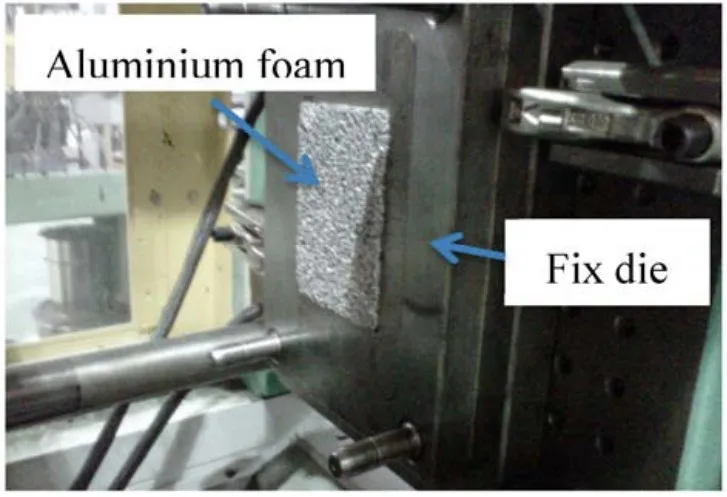
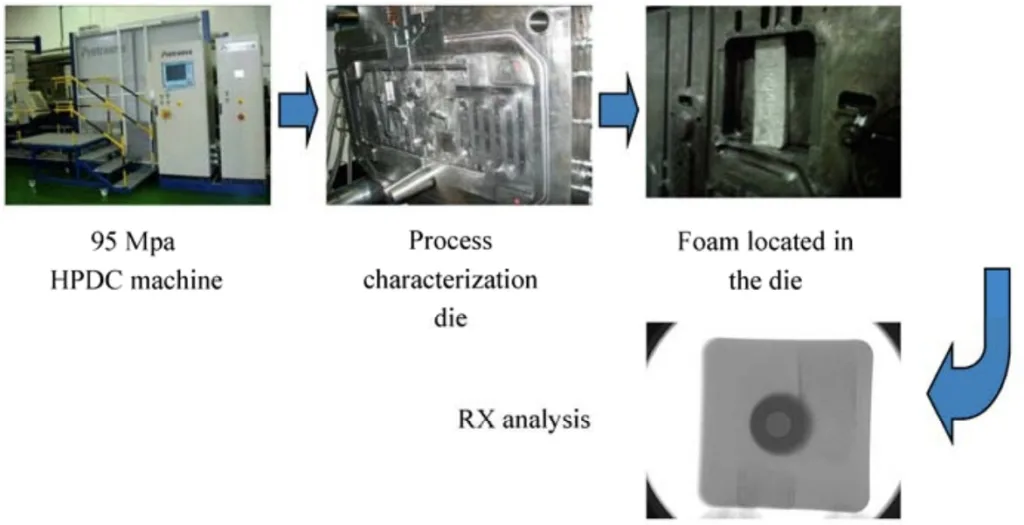
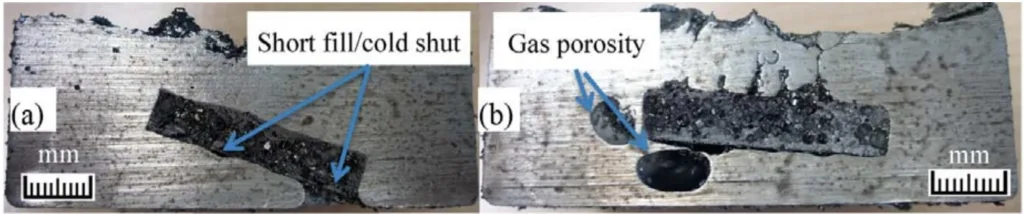
6. 결론 및 논의:
주요 결과 요약:
본 연구에서는 고압 다이캐스팅(HPDC)을 사용하여 마그네슘-알루미늄 폼 복합 주물을 생산하는 타당성을 성공적으로 입증했습니다. 본 연구에서는 외부 스킨을 특징으로 하는 Alulight 유형 알루미늄 폼을 이 공정에 적합한 코어 재료로 확인했습니다. 마그네슘 주입 온도 720 °C, 2단계 주입 속도 80 m/s, 폼 코어의 수직 배치와 같은 최적화된 HPDC 변수는 건전한 주물을 달성하는 데 중요합니다. 이 접근 방식을 사용하여 35%의 무게 감소를 가진 자전거 로드 부품을 성공적으로 생산했습니다.
연구의 학문적 중요성:
본 연구는 HPDC를 사용하여 경량 금속 매트릭스 복합재료를 만드는 실행 가능한 방법을 입증함으로써 학문 분야에 기여합니다. HPDC 조건에서 마그네슘 주조 환경 내에서 알루미늄 폼 코어가 어떻게 거동하는지에 대한 이해를 넓히고 폼 유형, 스킨 존재, 코어 배치 및 주입 변수의 중요성을 강조합니다.
실용적 의미:
본 연구 결과는 특히 운송 분야에서 경량화 솔루션을 추구하는 산업에 중요한 실용적 의미를 갖습니다. 개발된 HPDC 마그네슘-알루미늄 폼 복합 주조 공정은 자전거 부품과 같은 더 가벼운 부품을 제조할 수 있는 경로를 제공하여 솔리드 알루미늄, 티타늄 또는 강철과 같은 더 무거운 재료를 잠재적으로 대체할 수 있습니다. 이는 차량의 연비 향상과 자전거와 같은 응용 분야에서 성능 향상으로 이어질 수 있습니다. 자전거 로드에 알루미늄 폼을 사용하는 재료 및 생산 예상 비용은 부품당 약 0.3유로로 경제적 타당성을 시사합니다.
연구의 한계:
- 화학적 결합 부족: 본 연구에서는 폼의 알루미나 층으로 인해 알루미늄 폼 코어와 마그네슘 합금 사이에 화학적 결합이 없음을 인정합니다. 이러한 결합 부족은 복합재료의 전체 기계적 성능을 제한할 수 있습니다.
- 기계적 특성 감소: 무게 감소는 상당하지만 복합 주물의 초기 기계적 특성은 솔리드 AM60B 마그네슘 합금의 기계적 특성보다 낮습니다. 외삽된 값이 개선 가능성을 시사하지만 추가 최적화가 필요합니다.
- Alulight 폼에 대한 제한된 인장 시험 데이터: 본 연구에서는 특히 Alulight 유형 폼에 대한 인장 시험 값의 증가가 제한적이라고 언급하여 보다 심층적인 기계적 특성 평가의 필요성을 시사합니다.
7. 향후 후속 연구:
후속 연구 방향:
향후 연구는 알루미늄 폼과 마그네슘 사이의 화학적 결합의 한계를 해결하는 데 초점을 맞춰야 합니다. 알루미늄 폼 코어에 대한 표면 처리를 탐색하는 것이 주요 방향입니다.
추가 탐색이 필요한 영역:
특히 알루미늄 폼 코어에 Zn 기반 코팅과 같은 표면 처리를 적용하는 것을 조사하는 것이 좋습니다. 이는 알루미늄 폼과 주조 마그네슘 사이에 연속적인 계면을 생성하여 결합 강도와 기계적 맞물림을 향상시킬 수 있습니다. 추가 연구에서는 다양한 응용 분야에서 진동 감쇠, 소음 제어, 충돌 성능 또는 압축 특성을 개선하는 데 알루미늄 폼 코어의 잠재적 이점을 탐구할 수도 있습니다.
8. 참고 문헌:
- [1] Schultz, R. Aluminium Association Auto and Light Truck Group 2009 Update on North American Light Vehicle Aluminium Content Compared to the other Countries and Regions of the World. Phase II; Ducker Worlwide LLC: Troy, MI, USA, 2008; pp. 8–19.
- [2] Bonollo, F.; Urban, J.; Bonatto, B.; Botter, M. Gravity and low pressure die casting of aluminium alloys: A technical and economical benchmark. Metall. Ital. 2005, 97, 23-32.
- [3] Luo, A.A. Magnesium casting technology for structural applications. J. Magnes. Alloys 2013, 1, 2-22.
- [4] Gertsberg, G.; Nagar, N.; Lautzker, M.; Bronfin, B. Effect of HPDC parameters on the performance of creep resistant alloys MRI153M and MRI230D. SAE Tech. Pap. 2005, 1, 1–7.
- [5] Otarawanna, S.; Laukli, H.I.; Gourlay, C.M.; Dahle, A.K. Feeding mechanisms in high-pressure die castings. Metall. Mater. Trans. A 2010, 41, 1836-1846.
- [6] Bonollo, F.; Gramegna, N.; Timelli, G. High-pressure die-casting: Contradictions and challenges. JOM 2015, 67, 901-908.
- [7] Yim, C.D.; Shin, K.S. Semi-solid processing of magnesium alloys. Mater. Trans. 2003, 44, 558–561.
- [8] Sabau, A.S.; Dinwiddie, R.B. Characterization of spray lubricants for the high pressure die casting processes. J. Mater. Process. Technol. 2008, 195, 267–274.
- [9] Kimura, R.; Yoshida, M.; Sasaki, G.; Pan, J.; Fukunaga, H. Characterization of heat insulating and lubricating ability of powder lubricants for clean and high quality die casting. J. Mater. Process. Technol. 2002, 130–131, 289-293.
- [10] Puschmann, F.; Specht, E. Transient measurement of heat transfer in metal quenching with atomized sprays. Exp. Therm. Fluid Sci. 2004, 28, 607-615.
- [11] Rogers, K.J.; Savage, G. In-cavity pressure sensors-errors, robustness and some process insights. Die Cast Eng. 2000, 44, 76-80.
- [12] Kong, L.X.; She, F.H.; Gao, W.M.; Nahavandi, S.; Hodgson, P.D. Integrated optimization system for high pressure die casting processes. J. Mater. Process. Technol. 2008, 201, 629-634.
- [13] Keber, K.; Bormann, D.; Möhwald, K.; Hollander, U.; Bach, W. Compound casting of aluminium and magnesium alloys by High Pressure Die Casting. In Proceedings of the Magnesium 8th International Conference on Magnesium Alloys and Their Applications, Weimar, Germany, 26-29 October 2009; pp. 390-397.
- [14] Kunst, M.; Fischersworring-bunk, A.; Liebscher, C.; Glatzel, U.; Esperance, G.L.; Plamondon, P.; Baril, E.; Labelle, P. Microstructural characterization of Die Cast Mg-Al-Sr (AJ) Alloy. In Proceedings of the Magnesium: Proceedings of the 7th International Conference on Magnesium Alloys and Their Applications, Dresden, Germany, 6–9 November 2006; pp. 498-505.
- [15] Vicario, I. Study of high pressure die cast AZ91D magnesium alloy with surface treated aluminium 6063 cores for Al-Mg multi-material. In Proceedings of the 2nd Annual World Congress of Advanced Materials, Suzhou, China, 5-7 June 2013; pp. 7–21.
- [16] Yaokawa, J.; Miura, D.; Anzai1, K.; Yamada, Y.; Yoshii, H. Strength of salt core composed of alkali carbonate and alkali chloride mixtures made by casting technique. Mater. Trans. 2007, 5, 1034–1041.
- [17] Moschini, R. Production of Hollow Components in HPDC through the Use of Ceramic Lost Cores; XXXI Congreso Tecnico di Fonderia: Vincenza, Italy, 2012; pp. 1–33.
- [18] Yamada, Y.; Yaokawa, J.; Yoshii, H.; Anzai, K.; Noda, Y.; Fujiwara, A.; Suzuki, T.; Fukui, H. Developments and application of expendable salt core materials for high pressure die casting to apply closed-deck type cylinder block. SAE Int. 2007, 32-0084, 1–5.
- [19] Vicario, I.; Egizabal, P.; Galarraga, H.; Plaza, L.M.; Crespo, I. Study of an Al-Si-Cu HPDC alloy with high Zn content for the production of components requiring high ductility and tensile properties. Int. J. Mater. Res. 2013, 4, 392-397.
- [20] Benedick, C. Production and application of aluminium foam, past product potential revisited in the new millennium. Light Met. Age 2002, 60, 24-29.
- [21] Bausmesiter, J.; Weise, J. Structural Materials and Processes in Transportation, Metal Foams; John Wiley & Sons: Hoboken, NJ, USA, 2013; pp. 415-440.
- [22] Banhar, J. Metal foams: Production and stability. Adv. Eng. Mater. 2006, 9, 781–794.
- [23] Coleto, J.; Goñi, J.; Maudes, J.; Leizaola, I. Applications and manufacture of open and closed cell metal foams by foundry routes. In Proceedings of International Congress Eurofond, La Rochelle, France, 2–4 June 2004; pp. 1-10.
- [24] Körner, C.; Hirschmann, M.; Wiehler, H. Integral Foam Moulding of Light Metals. Mater. Trans. 2006, 47, 2188-2194.
- [25] Baumeister, J.; Weise, J. Application of aluminium-polymer hybrid foam sandwiches in battery housings for electric vehicles. Procedia Mater. Sci. 2014, 4, 301-330.
- [26] Vesenjak, M.; Borovinšek, M.; Fiedler, T.; Higa, Y.; Ren, Z. Structural characterisation of advanced pore morphology (APM) foam elements. Mater. Lett. 2013, 110, 201-203.
- [27] Miyoshi, T.; Itoh, M.; Akiyama, S.; Kitahara, A. Aluminium foam, “ALPORAS": The production process, properties and application. In Materials Research Society Symposium Proceedings, Boston, MA, USA, 1-3 December 1998; 1998; pp. 133-137.
- [28] Miyoshi, T.; Itoh, M.; Akiyama, S.; Kitahara, A. Alporas aluminum foam: Production process, properties, and applications. Adv. Eng. Mater. 2000, 2, 179–183.
- [29] Gegerly, V.; Clyne, T.W. The formgrip process: Foaming of reinforced metals by gas release in precursors. Adv. Eng. Mater. 2002, 2, 175–178.
- [30] Gergely, V.; Curran, D.C.; Clyne, T.W. Advances in the melt route production of closed cell aluminium foams using gas-generating agents. In Proceedings of Global Symposium of Materials Processing and Manufacturing Processing & Properties of Lightweight Cellular Metals and Structures, Seattle, WA, USA, 17-21 February 2002; pp. 3-8.
- [31] Baumeister, J. Production technology for aluminium foam/steel sandwiches. In Proceedings of the International Conference on Metal Foams and Porous Metal Structures, Bremen, Germany, 14-16 June 1999; pp. 113-118.
- [32] Seeliger, H.W. Cellular Metals: Manufacture, properties, applications. In Proceedings of the MetFoam, Berlin, Germany, 23-25 June 2003; pp. 5-12.
- [33] Kováãik, J.; Simančík, F.; Jerz, J.; Tobolka, P. Reinforced aluminium foams. In Proceedings of the International Conference on Advanced Metallic Materials, Smolenice, Slovakia, 5–7 November 2003; pp. 154–159.
- [34] Braune, R.; Otto, A. Tailored blanks based on foamable aluminium sandwich material. In Proceedings of the International Conference on Metal Foams and Porous Metal Structures, Bremen, Germany, 14-16 June 1999; pp. 119-124.
- [35] Gutiérrez-Vázquez, J.A.; Oñoro, J. Fabricación y comportamiento de espumas de aluminio con diferente densidad a partir de un precursor AlSi12. Rev. Metal. 2010, 46, 274–284.
9. 저작권:
본 자료는 이반 비카리오, 이그나시오 크레스포, 루이스 마리아 플라자, 파트리시아 카발레로, 이온 케파 이도이아가의 논문 고압 다이캐스팅으로 생산된 알루미늄 폼과 마그네슘 복합재료 주조를 기반으로 합니다.
논문 출처: doi:10.3390/met6010024
본 자료는 위 논문을 바탕으로 요약되었으며, 상업적 목적으로 무단 사용하는 것을 금지합니다.
Copyright © 2025 CASTMAN. All rights reserved.