본 논문 요약은 ['Materials Science and Engineering A']에 의해 출판된 ['Improved tensile properties of a new aluminum alloy for high pressure die casting'] 논문을 기반으로 작성되었습니다.
1. 개요:
- 제목: 고압 다이캐스팅용 신규 알루미늄 합금의 향상된 인장 특성 (Improved tensile properties of a new aluminum alloy for high pressure die casting)
- 저자: Peng Zhang, Zhenming Li, Baoliang Liu, Wenjiang Ding, Liming Peng
- 출판 연도: 2015년
- 출판 저널/학회: Materials Science and Engineering A
- 키워드: Al-5Mg-0.6Mn 알루미늄 합금; 고압 다이캐스팅; 인장 특성; 변형률 속도; 고온 (Al-5Mg-0.6Mn aluminum alloy; high pressure die casting; tensile properties; strain rate; high temperature)
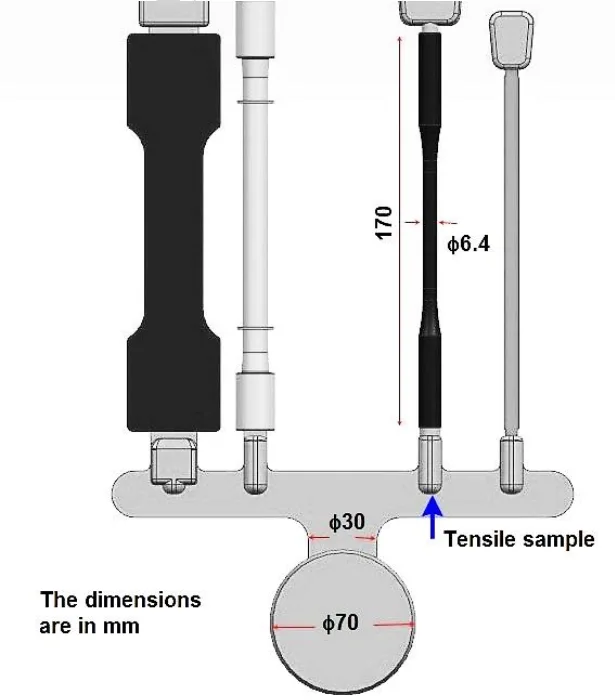
2. 초록 또는 서론
초록
본 논문은 최근 개발된 고연성 주조 알루미늄 합금 Al-5Mg-0.6Mn의 인장 특성 및 변형 거동에 미치는 변형률 속도 및 시험 온도의 영향을 조사합니다. 상온 및 최저 변형률 속도(~1.67 × 10⁻⁴ s⁻¹)에서 시험된 주조 상태 합금은 ~212 MPa의 가장 높은 항복 강도, ~357 MPa의 극한 인장 강도 및 연신율(~17.6%)을 나타냅니다. 변형률 속도가 증가함에 따라 주조 상태 합금의 극한 인장 강도와 연성이 감소합니다. 시험 온도가 증가함에 따라 주조 상태 합금은 인장 강도가 현저히 감소하고 연신율이 향상되는 경향을 보입니다. 합금의 인장 파괴는 주로 공정 입자의 균열 및 계면 분리에서 기인합니다. Portevin-Le Chatelier 효과는 상온에서 시험된 합금에서 발생합니다. 본 연구의 변형률 속도 범위는 합금의 가공 경화 거동에 큰 영향을 미치지 않습니다. 시험 온도 증가는 가공 경화 지수 및 계수를 명백히 감소시킵니다. 상온에서 시험된 합금의 경우, 모든 인장 파괴는 전반적인 불안정성 이전에 발생하여 국부적인 손상의 존재를 나타냅니다. 대조적으로, 고온에서 시험된 합금의 경우, 전반적인 불안정성은 대수 파괴 변형률 이하의 변형률에서 발생하여 여전히 포스트-네킹 손상이 있음을 시사합니다.
3. 연구 배경:
연구 주제 배경:
다이캐스팅 알루미늄 합금은 경량화 및 성능 향상을 위해 자동차, 항공우주 및 기타 운송 산업에서 점점 더 많이 사용되고 있습니다. 고압 다이캐스팅(HPDC)은 높은 생산 효율성, 복잡한 형상 및 박벽 부품 생산 능력, 우수한 치수 정확도, 표면 조도 및 기계적 특성으로 인해 대량 생산에 더 적합합니다 [5,6]. 그러나 높은 충전 속도와 빠른 냉각 속도로 인해 캐비티에서 가스가 빠져나갈 충분한 시간이 없습니다. 결과적으로 캐비티 내의 이러한 가스는 금속 액체에 불가피하게 혼입되어 기공 및 산화물 개재물과 같은 주조 결함을 유발합니다 [7-10]. 단조 또는 반복 하중 중 이러한 결함은 인장 또는 피로 균열 시작을 위한 응력 집중 부위 역할을 하여 주조물의 기계적 특성을 저하시킵니다 [11-13]. 고온 환경에서는 기공 내의 가스가 팽창하여 주조물 표면에 기포가 발생합니다. 이러한 결과는 제품의 외관 품질에 명백히 영향을 미치고 기계적 특성을 저하시킵니다. 따라서 기공을 포함하는 알루미늄 합금 다이캐스팅은 일반적으로 열처리를 할 수 없으며 고온에서도 작동하지 않습니다.
기존 연구 현황:
합리적인 부품 구조와 완벽한 설계 금형 외에도 고압 다이캐스팅에 적합한 합금 선택은 우수한 다이캐스팅 제품을 얻기 위한 가장 중요한 요소 중 하나입니다. 주조 알루미늄 부품의 사용 증가는 이러한 합금이 높은 인장 강도, 연신율 및 피로 특성을 가져야 함을 요구했습니다. 현재 상용 알루미늄 합금(예: Al-Si-Mg, Al-Si-Cu-Mg 및 Al-Si-Cu)은 구조적 응용 분야에 충분한 연성(δ< 5%)이 부족하여 현대 자동차 및 항공우주 산업의 요구 사항을 충족할 수 없습니다 [6]. 열처리는 주조 알루미늄 합금의 인장 특성에 영향을 미치는 가장 중요한 요소 중 하나로 인식되어 왔습니다. 이러한 합금은 높은 인장 강도와 연성을 얻기 위해 열처리를 받는 경향이 있습니다 [14-18]. 그러나 박벽을 가진 대형 다이캐스팅 부품의 경우, 이러한 부품의 크기 변화를 유발하는 경우가 많기 때문에 열처리 후 용체화 및 시효 경화 조건을 포함한 교정 작업이 필요합니다. 따라서 열처리 없이 새로운 다이캐스팅 알루미늄 합금을 개발하여 다이캐스팅 알루미늄 합금의 실제 적용 범위를 넓히는 것이 더 흥미로울 것입니다. 다이캐스팅 알루미늄 합금에 대한 기본 요구 사항은 다음과 같이 요약할 수 있습니다 [19-21]. (1) 우수한 유동성은 캐비티를 채우고 주조물의 양호한 표면을 얻는 데 매우 중요합니다. (2) 상온 및 고온에서 더 나은 기계적 특성은 더 크고 복잡한 박벽 주조물을 생산하는 요구를 충족할 수 있습니다. (3) 좁은 결정화 온도 범위는 수축을 줄이고 제품의 품질을 향상시킬 수 있습니다. (4) 합금과 금형 캐비티 사이의 낮은 상호 작용 경향은 다이 스티킹의 가능성을 줄일 수 있습니다.
연구의 필요성:
(5) 우수한 기계적 특성 및 내식성은 구조적 응용 분야의 요구를 충족할 수 있습니다. Al-Mg 알루미늄 합금은 우수한 내식성 및 높은 기계적 특성을 나타내며 자동차의 서브프레임 및 도어프레임에 매우 매력적입니다 [22-25]. 일반적으로 기존 Al-Mg 알루미늄 합금의 유동성 및 산화 거동은 Al-Si 기반 알루미늄 합금만큼 좋지 않습니다. 다이캐스팅 공정 중 Al-Mg 기반 합금의 낮은 주조 성형 능력 및 내산화성으로 인해 Al-Si 합금에 비해 Al-Mg 기반 합금의 다이캐스팅을 얻는 것은 오랫동안 어려운 문제였습니다. 또한 고압 다이캐스팅용 신규 Al-Mg 기반 합금 개발에 초점을 맞춘 연구 및 보고서는 거의 없습니다. 새롭게 개발된 다이캐스팅 합금인 Al-5Mg-0.6Mn(별도로 명시되지 않은 모든 조성은 wt.% 기준)은 우수한 강도와 연성 및 내식성으로 인해 자동차 파워트레인 및 구조적 응용 분야에 매우 매력적입니다. 더욱 중요한 것은 열처리 없이도 이 합금의 인장 성능이 부품에 대한 요구 사항을 충족할 수 있다는 것입니다. 조성은 ~90 (HB, 브리넬 경도)의 경도, ~210 MPa의 항복 강도, ~340 MPa의 극한 인장 강도 및 ~15%의 연신율(상온)을 제공하도록 최적화되었습니다. Al-5Mg 합금의 성형성, 기계적 강도 및 연성을 개선하기 위해 본 연구에 적용된 합금의 화학적 조성은 다음과 같이 설계되었습니다. (1) 주조 알루미늄 합금에서 Fe 함량이 0.8% 이상이면 용융 금속이 다이강을 용해 및 납땜하는 경향이 거의 또는 전혀 없다고 보고되었습니다 [26]. 반면에 Fe는 주조물의 기계적 특성을 감소시키는 일부 취성 금속간 화합물을 형성하는 경향이 있습니다. 본 연구에서는 Fe 함량을 0.14%까지 낮추어 부정적인 영향을 피했습니다. Al-5Mg 합금에 첨가된 망간(Mn)(0.6%)의 주요 효과는 철(Fe)을 대체하고 다이 스티킹을 방지하는 것입니다. (2) 실리콘(Si) 함량(< 0.3%) 외에도 일부 기타 불순물 원소(예: Cu 및 Zn)는 낮은 수준(< 0.04% 및 0.08%)으로 엄격하게 제어됩니다. (3) RE(희토류)(≤ 0.1%)는 산화물 개재물을 줄이고 합금의 미세 조직을 정화하기 위해 합금에 첨가됩니다 [27-29]. 이 새로운 합금은 또한 다이캐스팅 공정 중 적절한 유동성 성능과 내산화성을 나타냅니다. 고응력 및 고온(HT) 하에서 주조 알루미늄 부품의 사용이 증가함에 따라 인장 속도 및 시험 온도 [30-37]와 일반적으로 관련된 인장 특성 및 변형 거동에 대한 상당한 관심이 높아졌습니다. 본 연구에서는 변형률 속도 및 시험 온도가 인장 특성, 변형 거동 및 합금의 파괴 메커니즘에 미치는 영향을 조사합니다.
4. 연구 목적 및 연구 질문:
연구 목적:
본 연구의 목적은 최근 개발된 고연성 주조 알루미늄 합금 Al-5Mg-0.6Mn의 인장 특성을 개선하는 것입니다. 특히 변형률 속도와 시험 온도가 인장 특성에 미치는 영향을 조사하는 데 중점을 둡니다.
핵심 연구 질문:
- 다양한 변형률 속도가 Al-5Mg-0.6Mn 합금의 인장 특성에 어떤 영향을 미치는가?
- 다양한 시험 온도가 Al-5Mg-0.6Mn 합금의 인장 특성에 어떤 영향을 미치는가?
- Al-5Mg-0.6Mn 합금의 변형 및 파괴 메커니즘은 무엇인가?
연구 가설:
- 변형률 속도가 증가하면 Al-5Mg-0.6Mn 합금의 인장 강도와 연성이 감소할 것이다.
- 시험 온도가 증가하면 Al-5Mg-0.6Mn 합금의 인장 강도는 감소하지만 연신율은 향상될 것이다.
- Al-5Mg-0.6Mn 합금의 파괴는 주로 공정 입자의 균열 및 계면 분리에서 기인할 것이다.
5. 연구 방법론
연구 설계:
본 연구는 실험적 연구 설계를 채택하여 Al-5Mg-0.6Mn 합금의 인장 특성에 미치는 변형률 속도와 시험 온도의 영향을 조사합니다. 인장 시험편은 ASTM B557-06 표준에 따라 준비되었습니다. 인장 시험은 다양한 변형률 속도와 시험 온도에서 수행되었습니다. 미세 조직 관찰 및 파면 분석을 통해 합금의 변형 및 파괴 메커니즘을 조사했습니다.
데이터 수집 방법:
- 재료 및 시편 준비: 공칭 조성 Al-5Mg-0.6Mn의 합금은 고순도 Al 및 Mg, Al-10Mn, Al-10Ti, Al-8Si 및 Al-10RE 모합금을 전기 저항로에서 준비하고 690~700°C의 주입 온도와 180~200°C의 금형 온도에서 금속 금형에 주조했습니다. 주입 전에 용융물을 690 ± 3°C의 전기로에서 30분 동안 유지하여 균질성과 현재 금속간 화합물의 용해를 보장했습니다. 충전 속도(mm/s) 및 충전 시간(s)을 포함한 다이캐스팅 매개변수는 그림 1에 나와 있습니다. 그림 2에 나와 있는 ASTM B557-06(게이지 직경 6.4mm 및 게이지 길이 64mm)에 따른 표준 인장 시편은 LK400S 4000KN HPDC 기계를 사용하여 얻었습니다. 실제 조성은 Optima 7300DV 유도 결합 플라즈마 광학 방출 분광법(ICP-OES)으로 측정했습니다(표 1에 표시).
- 인장 시험: 인장 시험은 부착된 고온 전기로가 ± 3°C 이내로 제어되는 Zwick/Roell-20kN 인장 시험기에서 수행되었습니다. 응력-변형률 곡선은 나이프 에지 신율계(50 µm)를 시편의 게이지 섹션에 부착하여 얻었습니다. 극한 인장 강도(UTS), 0.2% 항복 응력(YS) 및 연신율(A)은 시험 데이터에서 결정되었습니다. 본 연구에서는 모든 인장 시편을 시험 전에 최소 2개월 동안 상온에 보관하여 인장 특성을 안정화시켰습니다. 1.67 × 10⁻⁴ (B₁), 3.33 × 10⁻⁴ (B₂), 6.67 × 10⁻⁴ (B₃), 1.33 × 10⁻³ (B₄) 및 2.67 × 10⁻³ s⁻¹ (B₅)의 5가지 다른 변형률 속도를 사용하여 합금의 인장 특성, 변형 및 파괴 거동에 미치는 다양한 속도의 영향을 연구했습니다. 모든 시험은 상온(RT~20°C)에서 수행되었으며 각 변형률 속도에 대해 최소 4회의 시험을 수행했습니다. 또한 20°C(C₁), 120°C(C₂), 150°C(C₃), 185°C(C₄) 및 220°C(C₅)를 포함한 5가지 시험 온도를 적용하여 시험 온도가 합금의 인장 거동에 미치는 영향을 조사했습니다. 인장 시편은 먼저 원하는 온도로 가열하고 시험 온도에서 15분 동안 유지한 다음 6.67 × 10⁻⁴ s⁻¹의 변형률 속도로 시험했습니다. 또한 각 시험 온도에 대해 최소 4회의 인장 시험을 완료했습니다.
- 파면 분석 및 미세 조직 분석: 다양한 상의 식별은 D/MAX-IIIA X선 회절계(XRD)를 사용하여 수행되었습니다. 모든 시편의 파괴면은 JEOL JSM-6460 전계 방출 주사 전자 현미경(SEM)과 부착된 에너지 분산 분광기(EDS)(Japan Electron Optics Ltd., Tokyo, Japan)를 사용하여 추가로 검사했습니다. X선 에너지 분산 스펙트럼(EDS)은 상의 화학 원소 및 구성 성분을 결정하는 데 사용되었습니다. 합금의 미세 조직을 조사하기 위해 금속 조직 시편을 냉각수 냉각 저속 다이아몬드 휠을 사용하여 인장 시편의 그립 영역 또는 파괴 영역에서 채취했습니다. 냉간 마운팅된 시편은 조심스럽게 연마, 연마 및 0.5 ml HF 및 100 ml H₂O의 용액으로 에칭했습니다. 합금 시편의 미세 조직 관찰은 SEM으로도 수행되었습니다.
분석 방법:
- 인장 시험 데이터 분석
- 파면 분석 및 미세 조직 분석
- 변형 경화 거동 분석
- 인장 불안정성 분석
연구 대상 및 범위:
본 연구의 연구 대상은 Al-5Mg-0.6Mn 알루미늄 합금입니다. 연구 범위는 다양한 변형률 속도와 시험 온도에서 합금의 인장 특성을 조사하는 것으로 제한됩니다.
6. 주요 연구 결과:
핵심 연구 결과:
- Al-5Mg-0.6Mn 합금은 상온 및 최저 변형률 속도에서 시험했을 때 높은 인장 특성을 나타냅니다.
- 변형률 속도가 증가함에 따라 합금의 극한 인장 강도와 연성이 감소합니다.
- 시험 온도가 증가함에 따라 합금의 인장 강도는 감소하지만 연신율은 향상됩니다.
- 합금의 인장 파괴는 주로 공정 입자의 균열 및 계면 분리에서 기인합니다.
- Portevin-Le Chatelier 효과는 상온에서 시험된 합금에서 관찰됩니다.
- 변형률 속도는 합금의 가공 경화 거동에 큰 영향을 미치지 않습니다.
- 시험 온도 증가는 합금의 가공 경화 지수 및 계수를 감소시킵니다.
- 상온에서 시험된 합금의 경우, 모든 인장 파괴는 전반적인 불안정성 이전에 발생합니다.
- 고온에서 시험된 합금의 경우, 전반적인 불안정성은 대수 파괴 변형률 이하의 변형률에서 발생합니다.
제시된 데이터 분석:
- 변형률 속도 효과 (Fig. 7, Table 2): 항복 강도(YS)는 다양한 변형률 속도에서 큰 차이를 보이지 않았으며 평균 YS는 약 210 ± 3 MPa입니다. 극한 인장 강도(UTS)는 변형률 속도가 증가함에 따라 약간 감소하는 경향을 보입니다. ~1.67 × 10⁻⁴ s⁻¹(B₁)의 변형률 속도에서 시험된 시편은 ~357 MPa의 가장 높은 극한 인장 강도를 나타내며, 이는 ~2.67 × 10⁻³ s⁻¹(B₅)의 변형률 속도에서 시험된 시편에 비해 약 30 MPa 증가한 것입니다. 또한 변형률 속도가 증가함에 따라 합금의 연성(17.6%에서 10.2%로)이 현저히 감소합니다. 최저 변형률 속도(B₁)에서 시험된 시편은 ~2.67 × 10⁻³ s⁻¹의 변형률 속도에서 시험된 시편에 비해 연신율이 약 72% 향상되어 가장 높은 연성을 나타냅니다.
- 시험 온도 효과 (Fig. 8, Table 3): 그림 8과 표 3은 다양한 시험 온도(~6.67 × 10⁻⁴ s⁻¹의 변형률 속도)에서 시험된 주조 상태 Al-5Mg-0.6Mn 합금의 인장 특성을 보여줍니다. 상온(C₁)에서 시험된 시편의 데이터도 비교를 위해 포함되었습니다. 시험 온도가 증가함에 따라 합금의 YS와 UTS가 모두 감소하는 것으로 나타났습니다. 최고 온도(C₅~220°C)에서 시험된 시편은 가장 낮은 인장 강도를 나타내며, RT(YS ≈ 210 MPa, UTS ≈ 340 MPa)에서 시험된 시편에 비해 YS에서 47 MPa, UTS에서 149 MPa 감소했습니다. 대조적으로 합금의 연성은 시험 온도가 증가함에 따라 현저히 증가하며, 이는 그림 8에 나와 있습니다. 최고 온도 220°C에서 시험된 시편은 가장 높은 연신율(~23.9%)을 나타내며, 이는 RT에서 시험된 시편(A~12.1%)에 비해 ~100% 증가한 것입니다. RT와 HT에서 합금의 인장 특성 차이는 다양한 온도 환경에서 다양한 매트릭스 강도와 다양한 상 입자 강도에 크게 기인할 수 있습니다. 슬립 밴드는 RT에 비해 HT에서 쉽게 활성화되는 것으로 일반적으로 받아들여집니다. 비저면 슬립 시스템도 상승된 온도에서 활성화될 수 있습니다. 또한 상 입자는 전위 이동에 대한 장벽 역할을 하고 인장 시험 [49] 중 매트릭스 합금의 변형을 제한하는 경향이 있습니다. 그러나 Al₁₂Mg₁<0xE2><0x9F><0x87> 및 Al(Fe, Mn)Si 상 입자는 HT(> 130°C)에서 쉽게 연화되어 Al-5Mg-0.6Mn 합금 [50,51]의 인장 특성을 저하시킵니다. 따라서 RT에서 시험된 시편은 HT에서 시험된 시편에 비해 인장 강도가 현저히 향상되고 연성이 감소하는 것으로 나타났습니다.
- 파면 분석 (Fig. 9): 그림 9는 RT(20°C), 120°C, 150°C 및 220°C에서 시험된 주조 상태 Al-5Mg-0.6Mn 합금의 일반적인 파면 사진을 보여줍니다. 결과는 RT와 HT 모두에서 시험된 시편의 파괴면에 많은 딤플이 있음을 명확히 나타냅니다(그림 9a, c, e 및 g에 표시). 이는 이러한 시편의 높은 연성에 해당합니다. 작거나 큰 딤플은 상 입자 크기 순서이며(그림 9b, d, f 및 h), 이는 입자 균열 및 계면 분리가 RT와 HT 모두에서 시험된 주조 상태 합금의 최종 파괴 이전의 주요 손상 메커니즘임을 나타냅니다.
- PLC 효과 (Fig. 10, 11): 그림 10a는 주조 상태 Al-5Mg-0.6Mn 합금의 유동 거동에 미치는 변형률 속도의 영향을 보여줍니다. 더 나은 보기를 위해 곡선 B₁(~1.67 × 10⁻⁴ s⁻¹의 변형률 속도) 및 B₂(~3.33 × 10⁻⁴ s⁻¹)는 각각 원시 곡선보다 20 MPa 및 10 MPa 위로 이동되었습니다. 대조적으로 곡선 B₄(~1.33 × 10⁻³) 및 B₅(~2.67 × 10⁻³)는 각각 원시 곡선보다 10 MPa 및 20 MPa 아래로 이동되었습니다. RT에서 시험된 이러한 시편에 대한 진응력-대수 변형률 곡선과 다양한 변형률 속도가 Portevin-Le Chatelier 효과 [57-65]를 나타내는 것이 분명히 관찰되었습니다(그림 10a에 표시). 이는 특정 온도 및 변형률 속도 범위에서 동적 변형 시효(DSA)의 결과로 간주됩니다 [66-75]. 일반적인 PLC 효과는 주로 용질 원자의 피닝과 확산 과정에 의해 제어됩니다. PLC 효과는 주조 상태 Al-5Mg-0.6Mn 합금에서 용액 내 마그네슘 원자와 글라이드 전위 사이의 상호 작용에 기인하는 것으로 생각됩니다. 하중 톱니 또는 밴드 전파 특성에 따르면 본 연구에서 PLC 효과는 유형 A 거동 [76]로 확인되었습니다. 일반적으로 알루미늄 합금에서 PLC 효과의 체계적인 통계 분석에는 응력 강하 진폭과 재하 시간 [64]이 주로 포함됩니다. 본 연구에서는 응력 강하 진폭, 응력 증가 진폭, 응력 감소 시간, 재하 시간(그림 10b에 표시)을 분석하여 PLC 효과의 변형률 속도 의존성을 밝혔습니다. 그림 10b에서 σ₁, σ₂, σ₃ 및 σ₂ +σ₃는 응력 강하 진폭, 급격한 증가 단계에서의 응력 증가 진폭, 안정적인 증가 단계에서의 응력 증가 진폭 및 총 응력 증가 진폭입니다. t₁, t₂, t₃ 및 t₂ + t₃는 응력 감소 시간, 급격한 재하 시간, 안정적인 재하 시간, 총 재하 시간입니다(그림 10b). 그림 11은 주조 상태 Al-5Mg-0.6Mn 합금에 대한 대수 변형률의 함수로서 σ₁, σ₂, σ₃, σ₂ +σ₃ 및 t₁, t₂, t₃, t₂ + t₃를 보여줍니다. 결과는 대수 변형률이 증가함에 따라 σ₁(응력 강하 진폭), σ₂(급격한 증가 단계에서의 응력 증가 진폭), σ₂ +σ₃(총 응력 증가 진폭) 및 t₃(안정적인 재하 시간), t₂ + t₃(총 재하 시간)가 증가함을 나타냅니다. 반면에 σ₃(안정적인 증가 단계에서의 응력 증가 진폭), t₁(응력 강하 시간) 및 t₂(급격한 재하 시간)은 대수 변형률이 증가함에 따라 거의 변하지 않는 것으로 나타났습니다. 그림 11a 및 11d에 표시된 바와 같이 총 응력 증가 진폭(σ₂+σ₃)은 응력 강하 진폭보다 명백히 더 큽니다. 유사한 결과가 시간에도 얻어졌으며, 총 응력 증가 시간(t₂ + t₃)도 응력 강하 시간(t₁)보다 더 깁니다(그림 11e 및 11g에 표시). 또한 그림 11e-g의 결과는 t₁, t₂, t₃ 및 t₂ + t₃가 변형률 속도가 증가함에 따라 감소함을 명확히 나타냅니다. ~1.67 × 10⁻⁴ s⁻¹의 최저 변형률 속도에서 시험된 시편을 제외한 모든 연구된 합금 시편의 경우, 응력 증가 진폭과 응력 강하 진폭(그림 11a-d)의 유의미한 차이는 거의 없습니다.
- 변형 경화 (Fig. 12, 13, 14, 15): 그림 10c는 다양한 변형률 속도 및 상온(~20°C)에서 시험된 주조 상태 Al-5Mg-0.6Mn 합금의 진응력-대수 소성 변형률 곡선을 보여줍니다. 낮은 변형률 0.0015에서 변형 경화율 dσ/dε에 미치는 변형률 속도의 영향은 그림 12a에 나와 있습니다. 결과는 변형률 속도가 증가해도 낮은 변형률에서 변형 경화율 dσ/dε(~4 GPa)에 큰 영향을 미치지 않음을 나타냅니다. Hollomon 방정식(σ = kεⁿ)은 소성 변형 단계에서 알루미늄 합금의 응력-변형률 곡선을 나타내는 것으로 가정되었습니다. 변형 경화 지수(n)와 변형 경화 계수(k)는 그림 12b에 표시된 바와 같이 약 0.01에서 불안정성까지의 변형률 범위에 걸쳐 log(진응력)-log(대수 소성 변형률) 데이터에 대한 선형 피팅에서 결정되었습니다. 그림 12c-d는 변형률 속도가 소성 변형률 0.01에서 불안정성까지의 n 값과 k 값에 미치는 영향을 보여줍니다. 변형률 속도가 다른 시편 간에 변형 경화 지수 또는 변형 경화 계수(n~ 0.16, k~ 480 MPa)의 명백한 차이는 거의 없는 것으로 나타났습니다. 따라서 본 연구의 변형률 속도 범위는 주조 상태 Al-5Mg-0.6Mn 합금의 가공 경화 거동에 큰 영향을 미치지 않는 것으로 생각됩니다.
- 인장 불안정성 (Fig. 16, 17): 그림 13a는 주조 상태 Al-5Mg-0.6Mn 합금의 유동 거동에 미치는 시험 온도의 영향을 보여줍니다. RT에서 시험된 시편의 곡선도 비교를 위해 포함되었습니다. 결과는 유동 응력이 감소하고 총 변형률이 시험 온도가 증가함에 따라 증가함을 보여줍니다. 또한 고온에서 시험된 합금의 진응력 곡선은 모두 유동 응력이 변형률 증가에 따라 최대값에 도달한 후 연화되는 것으로 명확히 나타났습니다. 최대 진응력에 해당하는 대수 변형률은 시험 온도가 증가함에 따라 감소하며, 이는 그림 13b에 나와 있습니다. 최대 유동 응력(εm)에서의 대수 변형률과 파괴 변형률(εf)의 비율은 그림 13c에 요약되어 있습니다. 결과는 다양한 온도에서 시험된 시편에 대한 εm /εf 비율이 시험 온도가 증가함에 따라 감소함을 나타냅니다. 그림 13a의 곡선에 따르면 선형 경화와 포물선 경화로 구성된 두 가지 영역이 있는 것으로 볼 수 있습니다. 두 영역 사이의 전이는 연질 매트릭스와 경질 공정 입자 [76-81]의 상대적 강도에 의해 제어될 가능성이 높습니다. 두 영역 사이의 전이 부위에서의 대수 변형률(εt)도 그림 13b에 나와 있습니다. 다양한 온도에서 시험된 시편의 경우 시험 온도 증가는 전이 부위에 해당하는 변형률을 향상시키는 것으로 볼 수 있습니다. 주조 상태 Al-5Mg-0.6Mn 합금의 경우 εt /εf 비율은 다양한 시험 온도에 대한 전이 부위에서의 대수 변형률 추세와 유사한 추세를 보이며, 이는 그림 13c에 나와 있습니다. 최고 온도 220°C에서 시험된 시편은 가장 높은 εt /εf 비율(~0.124)을 나타내며, 이는 RT에서 시험된 시편에 비해 400% 증가한 것입니다. 또한 주조 상태 Al-5Mg-0.6Mn 합금의 경우 PLC 거동은 고온 환경(그림 13a)에서 사라지는 것으로 나타났습니다. PLC 효과는 효과적인 용액 분위기가 이동 가능한 전위를 고정하기 어렵기 때문에 실제로 제거되었습니다. 진응력-대수 소성 변형률 곡선은 다양한 시험 온도와 동일한 변형률 속도(~1.67 × 10⁻⁴ s⁻¹)에서 시험된 주조 상태 합금에 대해 그림 13d에 나와 있습니다. 낮은 변형률 0.0015에서 변형 경화율 dσ/dε에 미치는 시험 온도의 영향은 그림 14a에 나와 있습니다. 다양한 시험 온도에서 시험된 주조 상태 시편은 RT에서 시험된 시편과 동일한 ~4 GPa의 유사한 변형 경화율을 나타냅니다. n 및 k 값도 log(진응력)-log(대수 소성 변형률) 데이터에 대한 선형 피팅에서 결정되었으며, 이는 그림 14b에 표시된 바와 같이 약 0.01에서 불안정성까지의 변형률 범위에 걸쳐 있습니다. 그림 14c는 시험 온도가 n 값에 미치는 영향을 보여줍니다. 결과는 주조 상태 Al-5Mg-0.6Mn 합금에서 시험 온도를 높이면 변형 경화 지수 n이 현저히 감소함을 명확히 보여줍니다. 예를 들어 주조 상태 합금의 변형 경화 지수(n)는 시험 온도가 20°C에서 220°C로 증가함에 따라 0.157에서 0.043으로 감소합니다. 변형 경화 계수(k)도 시험 온도가 증가함에 따라 감소하며, 이는 그림 14d에 나와 있습니다. RT에서 시험된 시편은 ~465 MPa의 가장 높은 k 값을 나타내며, 이는 220°C에서 시험된 시편에 비해 ~243 MPa 향상된 것입니다. 또한 변형 경화 지수 또는 변형 경화 계수와 시험 온도 사이에 좋은 상관 관계가 있는 것으로 볼 수 있습니다. 현재 데이터에 대한 최적 적합선은 시험 온도(T(K))를 통한 n 및 k 값의 관계를 나타냅니다.
그림 목록:
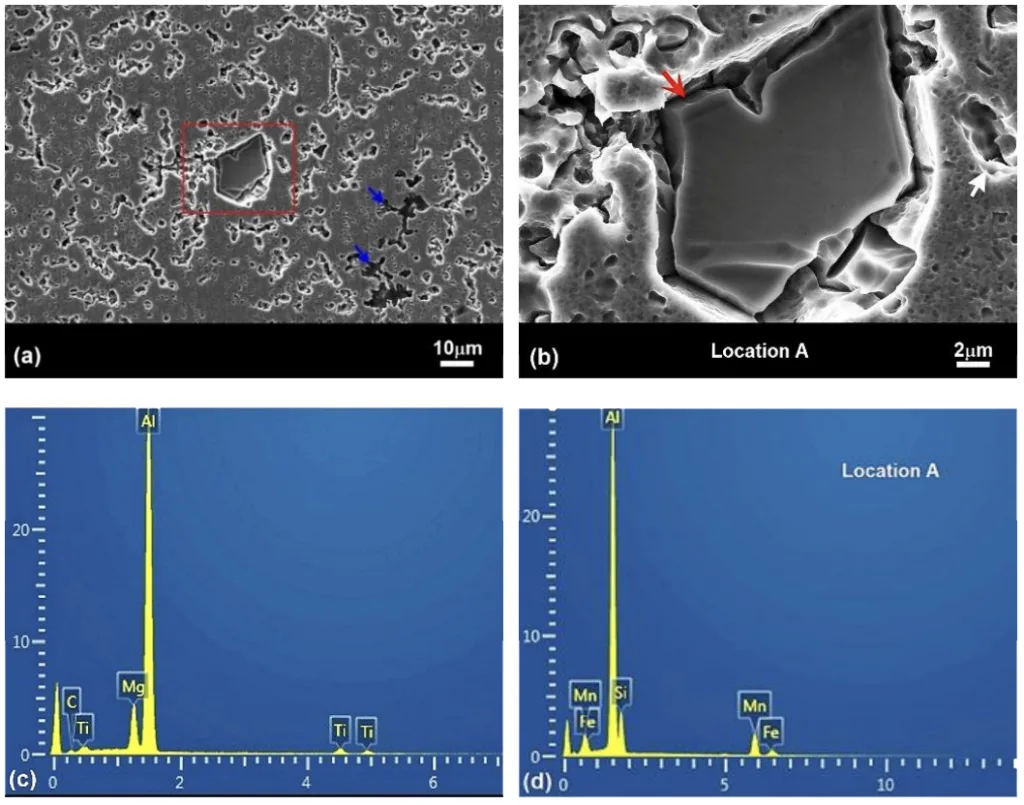
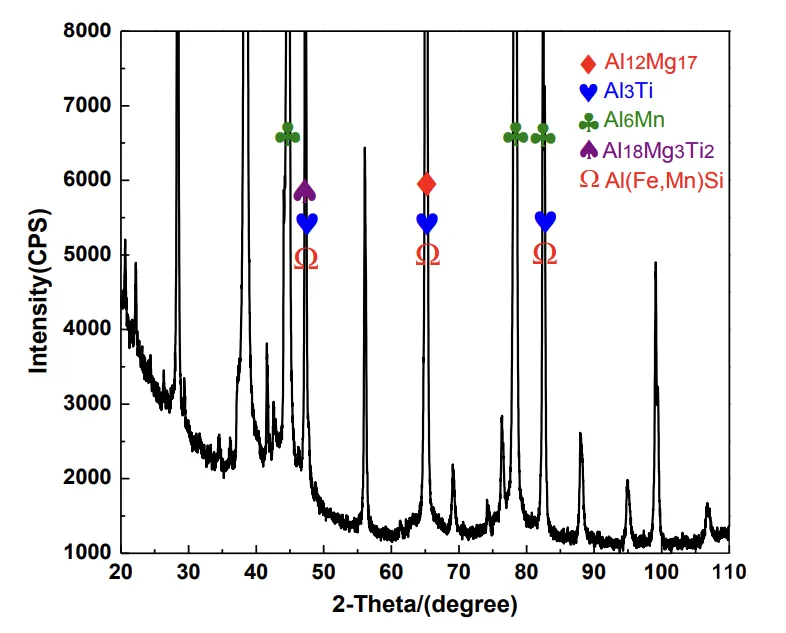
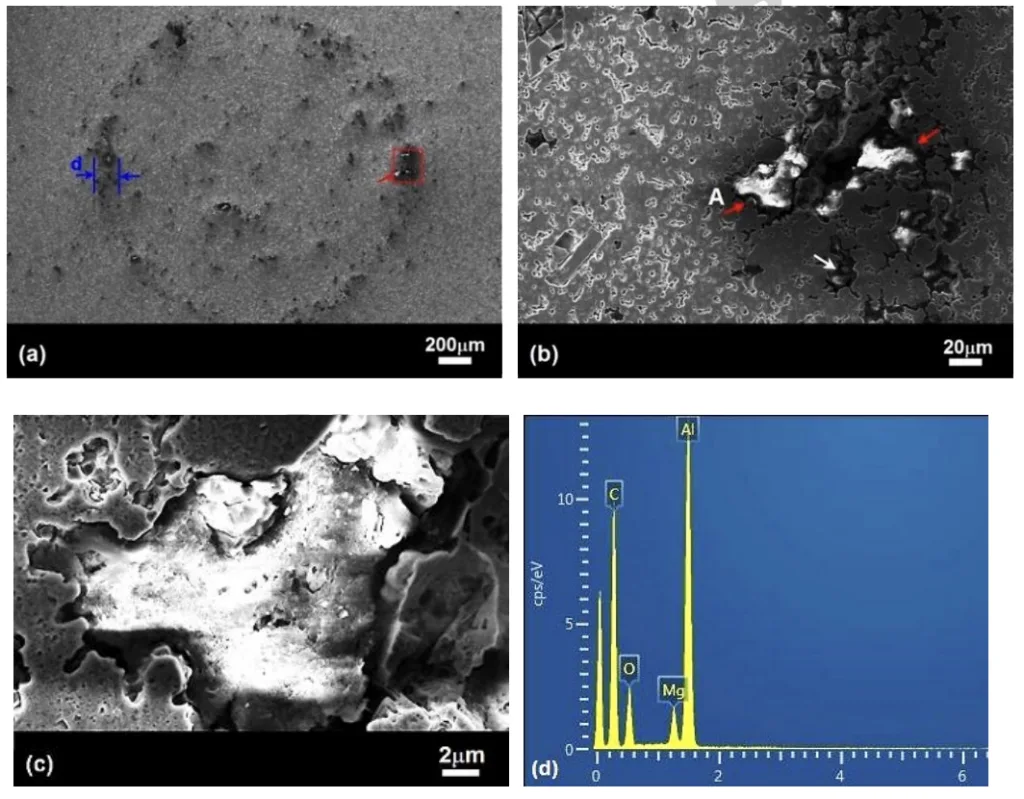
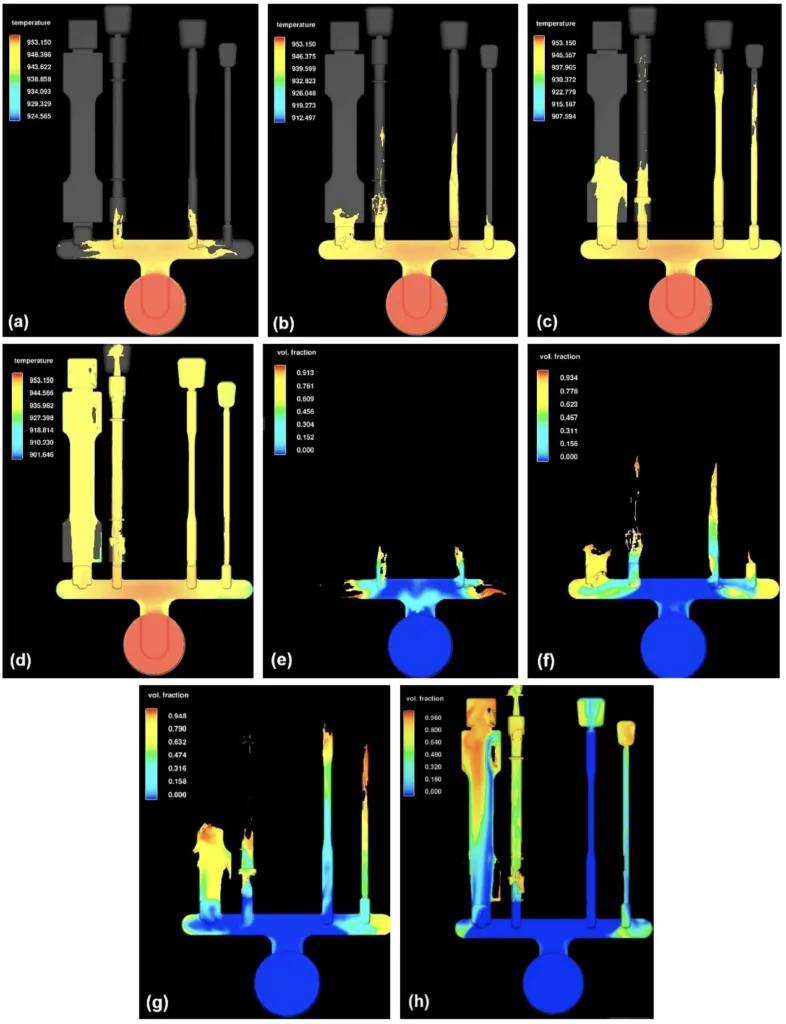
- Fig. 1. 다이캐스팅 매개변수 (충전 속도 (mm/s) 및 충전 시간 (s) 포함)
- Fig. 2. ASTM B557-06에 정의된 표준 인장 시험편 다이캐스팅 다이어그램
- Fig. 3. (a) 주조 Al-5Mg-0.6Mn 합금 시편의 그립 단면에서 얻은 이차 SEM 이미지. (b) 위치 A. (c) Al-Mg 상을 보여주는 에너지 분산 분광기 (EDS). (d) 위치 A에서 상의 에너지 분산 분광기 (EDS).
- Fig. 4. Al-5Mg-0.6Mn 합금의 XRD 곡선.
- Fig. 5. (a) 결함 밴드를 보여주는 주조 Al-5Mg-0.6Mn 합금의 미세 조직 관찰. (b) 이미지 (b)의 위치. (c) 이미지 b에서 개재물의 고배율 이미지. (d) 이미지 b (위치 A)에서 개재물의 에너지 분산 분광기 스펙트럼.
- Fig. 6. Flow-3D 분석 소프트웨어를 기반으로 한 (a, b, c, d) 열장 및 (e, f, g, h) 혼입된 공기 부피 분율에 대한 수치 유동 시뮬레이션 이미지 (결함 밴드 형성 과정 표시).
- Fig. 7. 주조 Al-5Mg-0.6Mn 합금의 인장 특성에 미치는 변형률 속도의 영향.
- Fig. 8. 주조 Al-5Mg-0.6Mn 합금의 인장 특성에 미치는 시험 온도의 영향.
- Fig. 9. 주조 Al-5Mg-0.6Mn 합금의 파괴에 미치는 시험 온도의 영향을 보여주는 SEM 파면 사진: (a, b) 20°C; (c, d) 120°C; (e, f) 150°C; 및 (g, h) 220°C.
- Fig. 10. (a) 주조 Al-5Mg-0.6Mn 합금의 진응력-대수 변형률 곡선에 미치는 변형률 속도의 영향. (b) 그림 9a에서 위치 A의 확대 곡선. (c) 주조 합금의 유동 거동에 미치는 변형률 속도의 영향을 보여주는 진응력-대수 소성 변형률 곡선.
- Fig. 11. (a) σ₁, (b) 62, (c) 63, (d) 62 +63 및 (e) t1, (f) t2, (h) t3, (g) t2 + t3 (그림 9b에서) (주조 Al-5Mg-0.6Mn 합금에 대한 대수 변형률의 함수).
- Fig. 12. (a) 주조 Al-5Mg-0.6Mn 합금의 변형률 속도 함수로서 0.0015의 소성 변형률에서 측정된 변형 경화율. (b) 다양한 변형률 속도에서 시험된 합금에 대한 n 및 K 값 결정. (c) 변형 경화 지수 n 및 (d) 변형 경화 계수 k (대수 소성 변형률 범위에서 측정 (약 0.01에서 불안정성까지)).
- Fig. 13. (a) 주조 Al-5Mg-0.6Mn 합금의 진응력-대수 변형률 곡선에 미치는 시험 온도의 영향. (b) 두 영역 사이의 전이 부위 및 최대 진응력에 해당하는 대수 변형률. (c) 전이 부위에서의 변형률 (εt) 대 파괴 변형률 (εf) 비율 및 최대 유동 응력 (Em) 대 파괴 변형률 (εf) 비율. (d) 주조 합금의 유동 거동에 미치는 시험 온도의 영향을 보여주는 진응력-대수 소성 변형률 곡선.
- Fig. 14. (a) 주조 Al-5Mg-0.6Mn 합금의 시험 온도 함수로서 0.0015의 소성 변형률에서 측정된 변형 경화율. (b) 다양한 시험 온도에서 시험된 합금에 대한 n 및 K 값 결정. (c) 변형 경화 지수 n 및 (d) 변형 경화 계수 k (대수 소성 변형률 범위에서 측정 (약 0.01에서 불안정성까지)).
- Fig. 15. (a) 변형 경화 지수 n 및 (b) 강도 계수 k (다양한 대수 소성 변형률 범위에서) (다양한 시험 온도의 함수로서 주조 Al-5Mg-0.6Mn 합금).
- Fig. 16. 다양한 변형률 속도 및 시험 온도에서 시험된 주조 Al-5Mg-0.6Mn 합금에 대한 인장 불안정성 플롯: (a) B₁-1.67 × 10⁻⁴, B₂-3.33 × 10⁻⁴, B₃-6.67 × 10⁻⁴, B₄-1.33 × 10⁻³ 및 B₅-2.67 × 10⁻³; (b) C₁-20°C, C₂-125°C, C₃-150°C, C₃-185°C 및 C₄-220°C.
- Fig. 17. 다양한 변형률 속도 (a) 및 시험 온도 (b)에서 시험된 주조 Al-5Mg-0.6Mn 합금의 파괴 변형률 εf에 대한 인장 불안정 변형률 ε¡ 비율.
- Fig. 18. 다양한 온도 (C₁-20°C 및 C₄-220°C)에서 시험된 주조 Al-5Mg-0.6Mn 합금의 거시적 인장 파괴 특징.
7. 결론:
주요 연구 결과 요약:
본 연구에서는 고압 다이캐스팅으로 제조된 신규 주조 Al-5Mg-0.6Mn 알루미늄 합금의 인장 특성을 변형률 속도와 시험 온도의 영향을 중심으로 종합적으로 평가했습니다. 주요 결과는 합금이 특히 낮은 변형률 속도와 상온에서 유망한 인장 성능을 나타내며 최적 조건에서 ~212 MPa의 항복 강도, ~357 MPa의 극한 인장 강도 및 ~17.6%의 연신율을 달성했음을 나타냅니다. 변형률 속도가 증가하면 인장 강도와 연성이 감소하는 반면, 온도가 상승하면 인장 강도는 감소하지만 연신율은 향상됩니다. 인장 파괴 메커니즘은 주로 공정 입자의 균열 및 계면 분리에 기인합니다. Portevin-Le Chatelier 효과는 상온에서 관찰되며, 가공 경화 거동은 시험 온도에 영향을 받지만 연구된 범위 내에서 변형률 속도에는 큰 영향을 받지 않습니다. 인장 불안정성 분석은 상온에서 국부적인 손상을, 고온에서 포스트-네킹 손상을 시사합니다.
연구의 학문적 의의:
본 연구는 HPDC로 제조된 Al-Mg-Mn 합금의 기계적 거동에 대한 학문적 이해에 기여합니다. 이 연구는 변형률 속도와 온도가 이 합금 시스템의 인장 특성, 변형 메커니즘 및 파괴 특성에 미치는 영향에 대한 자세한 통찰력을 제공합니다. Portevin-Le Chatelier 효과의 식별과 가공 경화 및 인장 불안정성 거동 분석은 알루미늄 합금 변형 물리학의 기본 지식을 더합니다. 또한 이 연구는 공정 입자 및 결함 밴드와 같은 미세 조직 특징이 합금의 기계적 반응을 결정하는 데 중요한 역할을 한다는 점을 강조합니다.
실용적 의미:
본 연구 결과는 고압 다이캐스팅에서 Al-5Mg-0.6Mn 합금의 응용에 대한 중요한 실용적 의미를 갖습니다. 특히 상온 및 저변형률 속도에서 합금의 높은 인장 강도와 연성은 경량화가 중요한 자동차, 항공우주 및 기타 운송 산업의 구조 부품에 대한 잠재력을 시사합니다. 이러한 성능이 열처리 없이 주조 상태에서 달성된다는 사실은 비용 및 가공 시간 측면에서 상당한 제조상의 이점을 제공합니다. 그러나 고온 또는 동적 하중 조건에서 작동하는 부품, 특히 고온 및 변형률 속도에서 인장 강도 감소를 응용 설계 시 고려해야 합니다.
연구의 한계 및 향후 연구 분야:
본 연구는 준정적 인장 시험과 특정 범위의 변형률 속도 및 온도로 제한됩니다. 추가 연구는 다음 사항을 탐구하는 것이 좋습니다.
- Al-5Mg-0.6Mn 합금의 피로 및 크리프 특성 (많은 구조적 응용 분야에 중요).
- 합금의 충격 특성 및 파괴 인성 (갑작스러운 충격 하중에 대한 저항성 평가).
- 다양한 환경에서의 부식 거동 (장기적인 내구성 보장).
- 결함 밴드 형성을 최소화하고 기계적 특성을 더욱 향상시키기 위한 다이캐스팅 매개변수 최적화.
- 합금 특성에 대한 열처리 효과 (본 연구는 주조 상태 성능을 강조하지만).
- 복잡한 하중 조건에서 성능을 예측하기 위한 합금의 변형 및 파괴 거동 모델링 및 시뮬레이션.
8. 참고 문헌:
- [1] A.I. Taub, P.E. Krajewski, A.A. Luo, J.N. Owens, JOM 59(2) (2007) 48-57.
- [2] S.X. Ji, D. Watson, Z.Y. Fan, M. White, Mater. Sci. Eng. A 556(2012) 824-833.
- [3] Z.Q. Hu, L. Wan, S.L. Lü, P. Zhu, S.S. Wu, Mater. Design. 55(2014) 353-360.
- [4] S. Farahany, A. Ourdjini, T.A.A. Bakar, M.H. Idris, Thermochim. Acta 575(2014) 179-187.
- [5] V.S. Zolotorevsky, N.A. Belov, M.V. Glazoff, Casting Aluminum Alloys, Elsevier, Oxford, 2007.
- [6] S.X. Ji, F. Yan, Z.Y. Fan, Mater. Sci. Eng. A 626(2015) 165-174.
- [7] S.X. Ji, Z.Y. Fan, Metall. Mater. Trans. A 33(11)(2002) 3511-3520.
- [8] V.D. Tsoukalas, Mater. Design. 29(10) (2008) 2027-2033.
- [9] S.G. Lee, A.M. Gokhale, Scripta Mater. 55(4)(2006) 387-390.
- [10] H.D. Zhao, F. Wang, Y.Y. Li, W. Xia, J. Mater. Process Tech. 209(9)(2009) 4537-4542.
- [11] M. Avalle, G. Belingardia, M.P. Cavatora, R. Doglione, Int. J. Fatigue 24(1)(2002) 1-9.
- [12] H. Mayer, M. Papakyriacou, B. Zettl, S.E. Stanzl-Tschegg, Int. J. Fatigue 25(2003) 245-256.
- [13] Z. Ma, A.M. Samuel, F.H. Samuel, H.W. Doty, S. Valtierra, Mater. Sci. Eng. A 490(1-2)(2009) 36-51.
- [14] R. Sharma, Anesh, D.K. Dwivedi, Mater. Sci. Eng. A 408(1-2)(2005) 274-280.
- [15] B. Lin, W.W. Zhang, Z.H. Lou, D.T. Zhang, Y.Y. Li, Mater. Design. 59(2014) 10-18.
- [16] I.A. Luna, H.M. Molinar, M.J.C. Román, J.C.E. Bocardo, M.H. Trejo, Mater. Sci. Eng. A 561(20)(2013) 1-6.
- [17] Y. Han, A.M. Samuel, H.W. Doty, S. Valtierra, F.H. Samuel, Mater. Design. 58(2014) 426-438.
- [18] Z.X. Wang, H. Li, F.F. Miao, B.J. Fang, R.G. Song, Z.Q. Zheng, Mater. Sci. Eng. A 607(2014) 313-317.
- [19] S.F. Radtke, D.C. Herrschaft, Inter. J. Mater. Eng. Appl. 1(4)(1979) 209-226.
- [20] A.A. Luo, J. Magnes. Alloys 1(1)(2013) 2-22.
- [21] F. Casarotto, A.J. Franke, R. Franke, in: J. Rowe (ed.), Advanced Materials in Automotive Engineering, Woodhead Publishing limited, Cambridge, 2012, pp.109-149.
- [22] L. Kramer, M. Phillippi, W.T. Tack, C. Wong, J. Mater. Eng. Perform. 21(2012) 1025-1029.
- [23] R.H. Jones, D.R. Baer, M.J. Danielson, J.S. Vetrano, Metall. Mater. Trans. A 32(2001) 1699-1711.
- [24] J.L. Searles, P.I. Gouma, R.G. Buchheit, Metall. Mater. Trans. A 32(2001) 2859-2867.
- [25] C.Y. Meng, D. Zhang, C. Hua, L.Z. Zhuang, J.S. Zhang, J. Alloys Comp. 617(2014) 925-932.
- [26] G. Timelli, B. Franco, Mater. Sci. Eng. A 528(2010) 273-282.
- [27] X.W. Hu, F.G. Jiang, F.R. Ai, H. Yan, J. Alloys Comp. 538(2012) 21-27.
- [28] Q.L. Li, T.D. Xia, Y.F. Lan, W.J. Zhao, L. Fan, P.F. Li, J. Alloys Comp. 562(2013) 25-32.
- [29] W.H. Yuan, Z.Y. Liang, C.Y. Zhang, L.J. Wei, Mater. Design. 34(2012) 788-792.
- [30] Y.L. Duan, G.F. Xu, D. Xiao, L.Q. Zhou, Y. Deng, Z.M. Yin, Mater. Sci. Eng. A 624(2015) 124-131.
- [31] M.M. Sharma, J.D. Tomedi, T.J. Weigley, Mater. Sci. Eng. A 619(2014) 35-46.
- [32] A.C. Magee, L. Ladani, Mater. Sci. Eng. A 582(2013) 276-283.
- [33] H. Toda, Z.A.B. Shamsudin, K. Shimizu, K. Uesugi, A. Takeuchi, Y. Suzuki, M. Nakazawa, Y. Aoki, M. Kobayashi, Acta Mater. 61(2013) 2403-2413.
- [34] S. Banerjee, P.S. Robi, A. Srinivasan, L.P. Kumar, Mater. Sci. Eng. A 527(2010) 2498-2503.
- [35] G. Han, W.Z. Zhang, G.H. Zhang, Z.J. Feng, Y.J. Wang, Mater. Sci. Eng. A 633(2015) 161-168.
- [36] Y.Y. Li, W.H. Wang, Y.F. Hsu, S. Trong, Mater. Sci. Eng. A 497(2008) 10-17.
- [37] Q.G. Wang, Metall. Mater. Trans. A 35A(2004) 2707-2718.
- [38] S. Murali, K.S. Raman, K.S.S. Murthy, Mater. Sci. Eng. A 190A(1995) 165-172.
- [39] G. Davignon, A. Serneels, B. Verlinden, L. Delaey, Metall. Mater. Trans. A 27A(1996) 3357-3361.
- [40] X. Fang, G. Shao, Y.Q. Liu, Z. Fan, Mater. Sci. Eng. A 445-446(2007) 65-72.
- [41] H.I. Laukli, C.M. Gourlay, A..K. Dahle, O. Lohne, Mater. Sci. Eng. A 413-414(2005) 92-97.
- [42] A.K. Dahle, S. Sannes, D.H.S. John, H. Westengen, J. Light Met. 1(2001) 99-103.
- [43] C.M. Gourlay, H.I. Laukli, A.K. Dahle, Metall. Mater. Trans. A 38(2007) 1833-1844.
- [44] S. Otarawanna, C.M. Gourlay, H.I. Laukli, A.K. Dahle, Metall. Mater. Trans. A 40(2009) 1645-1659.
- [45] E. Fiorese, F. Bonollo, G. Timelli, L. Arnberg, E. Gariboldi, Int. J. Metalcast 9(1) (2015) 55-66.
- [46] W.G. Walkington, Die casting defects – causes and solutions, North American Die Casting Association, 1997.
- [47] E. Gariboldi, F. Bonollo, M. Rosso, La Metallurgia Italiana 99(2007) 39-46.
- [48] Aluminium and aluminium alloys-Classification of defects and imperfections in high Pressure, Low Pressure and Gravity Die Cast Products, CEN/TR 16749, 2014.
- [49] Q.G. Wang, C.H. Cáceres, J.R. Griffiths, Metall. Mater. Trans. A 34A(2003) 2901-2912.
- [50] B. Kondori, R. Mahmudi, Metall. Mater. Trans. A 40A(2009) 2007-2015.
- [51] F. Kabirian, R. Mahmudi, Metall. Mater. Trans. A 40A(2009) 116-127.
- [52] C.D. Lee, Mater. Sci. Eng. A 464(1-2) (2007) 249-254.
- [53] C.D. Lee, K.S. Shin, Mater. Sci. Eng. A 599(2014) 223-232.
- [54] H.R. Ammar, A.M. Samuel, F.H. Samuel, Inter. J. Fatigue 30(6)(2008) 1024-1035.
- [55] Y.X. Gao, J.Z. Yi, P.D. Lee, T.C. Lindler, Fatigue Fract. Eng. Mater. Struct. 27(7) (2004) 559-570.
- [56] Q.G. Wang, D. Apelian, D.A. Lados, J. Light Met. 1(2001) 73-84.
- [57] M.A. Le Chatelier, Revue de Metallurgie 6 (1909) 914.
- [58] A. Portevin, F. Le Chatelier, Comptes Rendus Acad. Sci. Paris 176(1923) 507-509.
- [59] Q.G. Wang, M. Praud, A. Needleman, K.S. Kim, J.R. Griffiths, C.J. Davidson, C.H. Cáceres, A.A. Benzerga, Acta Mater. 58(2010) 3006-3013.
- [60] M. Niinomi, T. Kobayashi, K. Ikeda, J. Mater. Sci. 5(9)(1986) 847-848.
- [61] H.S. Rosenbaum, D. Turnbull, Acta Metall. Mater. 6(1958) 653-659.
- [62] J. Coër, P.Y. Manach, H. Laurent, M.C. Oliveira, L.F. Menezes, Mech. Res. Commun. 48(2013) 1-7.
- [63] S. Zhang, P.G. Mccormick, Y. Estrin, Acta Mater. 49(2001) 1087-1094.
- [64] H.F. Jiang, Q.C. Zhang, X.D. Chen, Z.J. Chen, Z.Y. Jiang, X.P. Wu, J.H. Fan, Acta Mater. 55(2007) 2219-2228.
- [65] T.A. Lebedkina, M.A. Lebyodkin, Acta Mater. 56(2008) 5567-5574.
- [66] A.H. Cottrell, Dislocations and plastic flow in crystals, Oxford University Press, London, 1953, pp. 134.
- [67] Y. Estrin, L.P. Kubin, J. Mech. Behav. Mater. 2(1989) 255.
- [68] C. Fressengeas, A.J. Beaudoin, M. Lebyodkin, L.P. Kubin, Y. Estrin, Mater. Sci. Eng. A 400-401(2005) 226-300.
- [69] L.P. Kubin, Y. Estrin, J. Phys. III France 1(1991) 929-943.
- [70] A. Nortmann, C.H. Schwink, Acta Mater. 45(1997) 2043-2051.
- [71] A. Nortmann, C.H. Schwink, Acta Mater. 45(5)(1997) 2051-2058.
- [72] R.A. Mulford, U.F. Kocks, Acta Metall. Mater. 27(7)(1979) 1125-1134.
- [73] P.G. McCormick, Acta metall. Mater. 20(1972) 351-354.
- [74] L.P. Kubin, Y. Estrin, Acta Metall. Mater. 33(1985) 397-407.
- [75] A. van den Beukel, Physica status. solidi. (a) 30(1975) 197-206.
- [76] P. Rodriguez, S. Venkadesans, Solid State Phenom. 42-43(1995) 257-266.
- [77] C.H. Cáceres, J.R. Griffiths, P. Reiner, Acta Mater. 44(1996) 15-23.
- [78] L.M. Brown, W.M. Stobbs, Phil. Mag. 23(1971) 1185-1199.
- [79] L.M. Brown, W.M. Stobbs, Phil. Mag. 23(1971) 1201-1233.
- [80] S.F. Corbin, D.S. Wilkinson, Acta Metall. Mater. 42(4)(1994) 1311-1318.
- [81] Q.G. Wang, Metall. Mater. Trans. A 35A(2004) 2707-2718.
9. 저작권:
- 본 자료는 "[Peng Zhang]"의 논문: "[Improved tensile properties of a new aluminum alloy for high pressure die casting]"을 기반으로 합니다.
- 논문 출처: https://dx.doi.org/10.1016/j.msea.2015.10.127
본 자료는 상기 논문을 기반으로 요약되었으며, 상업적 목적으로 무단 사용하는 것을 금지합니다.
Copyright © 2025 CASTMAN. All rights reserved.