본 소개 내용은 [International Journal of Mechanical Engineering and Robotics Research]에서 발행한 ["고성능 구리 합금 칠 벤트의 개발: 고압 다이캐스팅"] 의 연구 내용입니다.
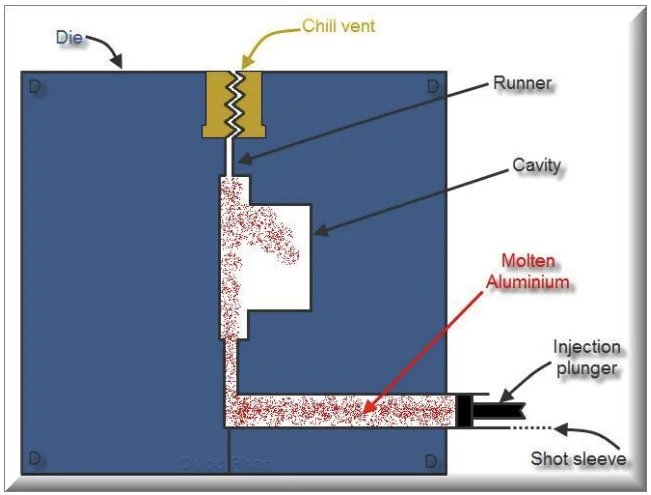
1. 개요:
- 제목: 고성능 구리 합금 칠 벤트의 개발: 고압 다이캐스팅 (Development of High Performance Copper Alloy Chill Vent for High Pressure Die Casting)
- 저자: Duoc T Phan, Syed H Masood, Syed H Riza, and Harsh Modi
- 발행 년도: 2020년 7월
- 발행 저널/학회: International Journal of Mechanical Engineering and Robotics Research, Vol. 9, No. 7
- 키워드: 고압 다이캐스팅 (High pressure die casting); 칠 벤트 (Chill vents); 열 해석 (Thermal analysis); 구리 합금 (Copper alloy); 열 전도율 (Thermal conductivity); 냉각 속도 (Cooling rates)
2. 초록 / 서론
고압 다이캐스팅(HPDC) 공정에서 칠 벤트는 잔류 공기와 가스를 금형 캐비티 밖으로 배출하는 데 필수적입니다. 본 논문은 기존 공구강에 비해 높은 강도와 높은 열전도율을 갖는 새로운 유형의 구리 합금 재료를 사용하여 고압 다이캐스팅용 고성능 칠 벤트의 설계 및 개발을 연구합니다. 유한 요소 해석은 칠 벤트에 대한 수치 열전달 모델을 개발하고 실험 결과를 통해 검증하는 데 적용됩니다. 검증된 모델은 구리 합금 칠 벤트와 기존 강철 칠 벤트의 성능을 비교하는 데 사용됩니다. 연구 결과, 칠 벤트 재료의 변경은 냉각 시간, 냉각 속도 및 내부 금형 온도 분포에 상당한 개선을 가져오는 것으로 나타났습니다. 특히, 구리 칠 벤트는 기존 강철 칠 벤트에 비해 응고 알루미늄 합금의 냉각 효율을 약 158% 증가시키는 것으로 나타났습니다. 본 연구는 고강도 구리 합금 칠 벤트의 사용이 급속한 열 전달과 가스의 빠른 방출을 가능하게 하여 HPDC 공정의 효율성과 효과를 향상시키고, 부품의 기공 및 플래시 결함을 줄이는 것으로 결론 내립니다.
3. 연구 배경:
연구 주제 배경:
고압 다이캐스팅(HPDC)은 경량 금속 부품 제조를 위해 자동차 산업에서 널리 사용되며, 특히 ADC12와 같은 경량 알루미늄 합금의 사용이 증가하는 추세입니다. 칠 벤트는 다이 캐비티에서 공기를 배출하기 위한 HPDC의 일반적인 기술이며, 일반적으로 지그재그 벤트 경로가 있는 강철 블록 쌍으로 구성됩니다. 그러나 기존 강철 칠 벤트는 강철의 낮은 열전도율로 인해 용융 금속 플러싱 및 결함 방지 어려움과 같은 제한 사항이 있습니다.
기존 연구 현황:
기존 연구에서는 HPDC 공정 효율성을 향상시키고 냉각 시간을 단축하기 위해 응고 및 열 공정의 수치 및 유한 요소 모델링을 광범위하게 탐구했습니다. 시뮬레이션 연구는 정확한 열 해석 및 결함 감소에 중요한 다양한 공정 매개변수를 분석했습니다. 그러나 논문에서 언급했듯이, "시뮬레이션 방법을 사용하여 여러 요인이 연구되었지만, HPDC 공정에서 칠 벤트의 설계 및 개발과 공기 배출 문제에 대한 관심은 거의 없었습니다."
연구의 필요성:
본 연구는 HPDC에서 칠 벤트의 설계 및 최적화와 관련된 기존 문헌의 격차를 확인합니다. 기존 강철 칠 벤트의 한계, 특히 낮은 열전도율은 대체 재료 탐색의 필요성을 야기합니다. 본 연구는 공기 배출 문제를 해결하고 HPDC 공정의 전반적인 효율성을 향상시키기 위해 개선된 칠 벤트 설계의 필요성을 강조하며, 특히 기공 및 플래시 결함을 목표로 합니다.
4. 연구 목적 및 연구 질문:
연구 목적:
주요 연구 목적은 "이러한 연구 격차를 해소하고 기존 공구강 대신 MoldMAX를 사용한 새로운 칠 벤트 구성의 성능을 조사하는 것"입니다. 여기에는 베릴륨 구리 합금인 MoldMAX를 사용하여 고성능 칠 벤트를 설계 및 개발하고 HPDC에서 기존 공구강(H13) 칠 벤트와 성능을 비교하는 것이 포함됩니다.
핵심 연구:
핵심 연구는 공구강(H13) 칠 벤트와 비교하여 베릴륨 구리 합금(MoldMAX) 칠 벤트의 성능을 평가하는 데 중점을 둡니다. 이 평가는 유한 요소 해석을 사용한 수치 시뮬레이션을 통해 수행되고 실험적 테스트로 검증됩니다. 성능 지표에는 냉각 시간, 냉각 속도 및 금형 내 온도 분포가 포함됩니다.
5. 연구 방법론
연구 설계:
본 연구는 칠 벤트의 열 전달을 모델링하기 위해 유한 요소 해석(FEA)을 사용하는 수치 시뮬레이션 접근 방식을 채택합니다. "유한 요소 해석은 칠 벤트에 대한 수치 열전달 모델을 개발하고 실험 결과를 통해 검증하는 데 적용됩니다." 모델은 다양한 칠 벤트 재료의 열 성능을 비교하도록 설계되었습니다.
자료 수집 방법:
실험적 검증은 "상용 800톤 다이캐스팅 기계에서 수행된 알루미늄 합금 주조의 실시간 실험 테스트"를 사용하여 수행되었습니다. 칠 벤트 표면의 온도 분포는 15.9초의 이젝션 시간에서 "고속 적외선 카메라, HPDC 기계의 FLIR PM850"을 사용하여 측정되었습니다.
분석 방법:
시뮬레이션된 온도 결과는 FEA 열 전달 모델을 검증하기 위해 실험 측정값과 비교되었습니다. 그 후, 검증된 모델은 냉각 시간, 냉각 속도 및 온도 분포를 분석하여 MoldMAX 구리 합금 칠 벤트와 공구강(H13) 칠 벤트의 성능을 비교하는 데 사용되었습니다.
연구 대상 및 범위:
본 연구는 HPDC에 사용되는 칠 벤트에 중점을 둡니다. 조사된 재료는 기존 공구강(H13)과 MoldMAX 베릴륨 구리 합금입니다. 실험적 검증 및 시뮬레이션에 사용된 주조 재료는 알루미늄 합금 ADC12입니다. 범위는 응고 알루미늄 합금에서 열을 제거하는 칠 벤트의 열 성능으로 제한됩니다.
6. 주요 연구 결과:
핵심 연구 결과:
주요 연구 결과는 "구리 칠 벤트가 기존 강철 칠 벤트에 비해 응고 알루미늄 합금의 냉각 효율을 약 158% 증가시킨다"는 것입니다. 특히, 구리 합금 칠 벤트가 이젝션 온도까지 냉각되는 데 걸리는 시간은 강철 칠 벤트(15.9초)에 비해 현저히 짧았습니다(6.70초). 냉각 속도 또한 구리 합금 칠 벤트(77°C/s)가 강철 칠 벤트(32.5°C/s)보다 훨씬 높았습니다.
제시된 데이터 분석:
- 온도 분포: 그림 4와 그림 6은 각각 강철 및 구리 합금 칠 벤트에 대한 이동 블록 표면의 온도 분포를 보여줍니다. 그림 4는 15.9초에서 강철 칠 벤트의 최대 온도가 98.67°C임을 보여줍니다. 그림 6은 구리 합금 칠 벤트가 단 6.7021초 만에 유사한 최대 온도(98.675°C)에 도달하여 더 빠른 냉각을 보여줍니다.
- 냉각 곡선: 그림 7은 강철(H13) 및 MoldMAX 칠 벤트에 대한 냉각 시간 곡선의 비교를 제시합니다. 곡선은 주조 공정 전반에 걸쳐 H13 강철 칠 벤트에 비해 MoldMAX 칠 벤트의 현저히 빠른 냉각 속도를 시각적으로 보여줍니다. 그래프는 "다른 시간에서 동일한 온도"를 보여주며 구리 합금의 시간적 이점을 강조합니다.
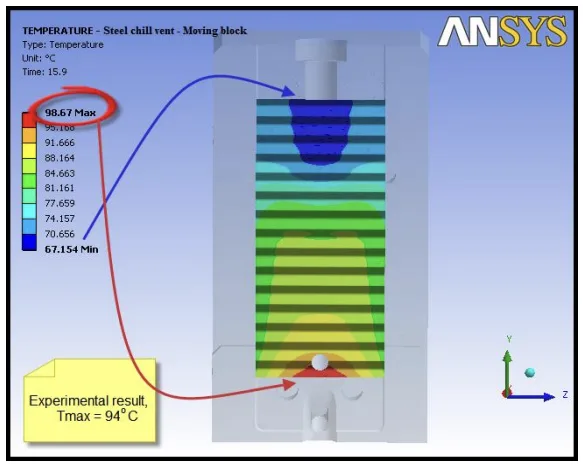
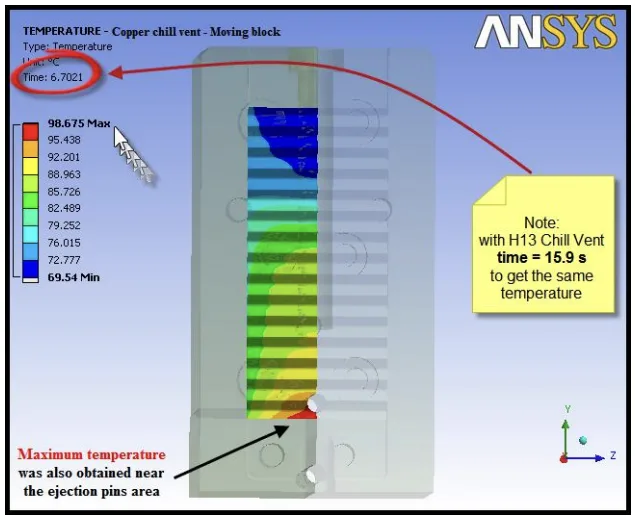
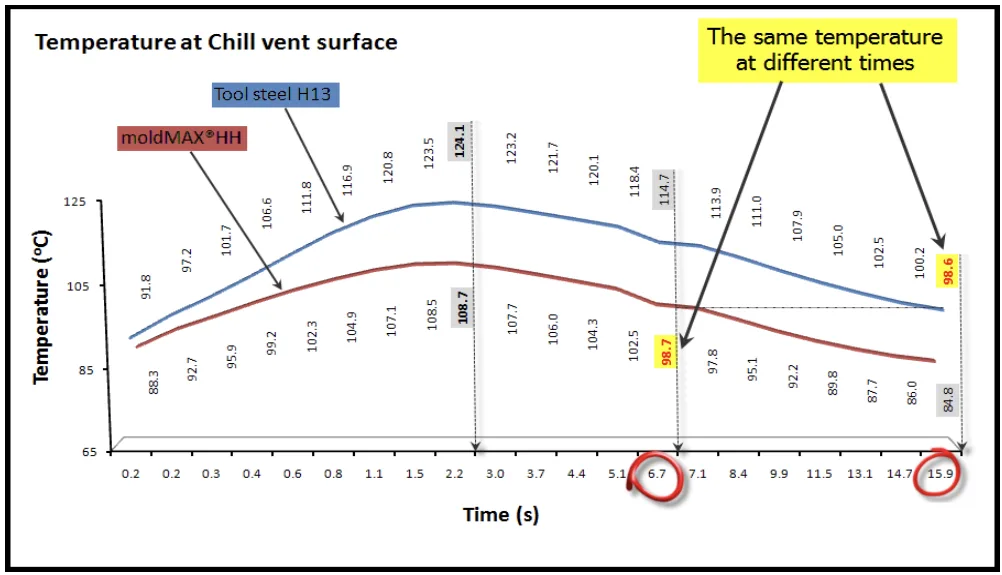
그림 목록:
- 그림 1. 일반적인 HPDC 공정의 개략도.
- 그림 2. HPDC에 사용된 칠 벤트의 CAD 모델
- 그림 3. 열 해석에 사용된 열 발생률 및 열 유속 값.
- 그림 4. 이동 블록 표면의 온도 분포 - 강철 칠 벤트.
- 그림 5. 적외선 카메라로 측정한 칠 벤트 표면의 실험적 온도 분포
- 그림 6. 이동 블록 표면의 온도 분포 - MoldMAX 구리 합금 칠 벤트
- 그림 7. 강철 및 구리 칠 벤트를 사용하여 주조 공정 중 냉각 시간 곡선 비교.
7. 결론:
주요 결과 요약:
본 연구는 HPDC에서 칠 벤트에 고강도, 고열전도율 구리 합금(MoldMAX)을 활용하면 냉각 성능이 크게 향상된다는 결론을 내립니다. 주요 결과는 다음과 같습니다.
- 향상된 냉각 효율: 구리 합금 칠 벤트는 강철 칠 벤트에 비해 냉각 효율을 약 158% 증가시킵니다.
- 단축된 냉각 시간: 이젝션 온도에 도달하는 냉각 시간이 구리 합금 칠 벤트에서 현저히 단축됩니다.
- 향상된 열 전달: 구리 합금의 더 높은 열전도율은 급속한 열 전달을 용이하게 합니다.
- 더 빠른 가스 방출: 향상된 열 전달은 다이 캐비티에서 더 빠른 가스 방출에 기여합니다.
- 결함 감소: 향상된 냉각 및 가스 방출은 HPDC 부품의 기공 및 플래시 결함을 줄이는 데 기여합니다.
연구의 학문적 의의:
본 연구는 HPDC 연구에서 종종 간과되는 측면인 칠 벤트의 설계 및 성능에 초점을 맞춰 연구 격차를 해소합니다. 칠 벤트에 고열전도율 재료를 사용하는 것의 이점에 대한 귀중한 통찰력을 제공하고 수치 시뮬레이션 및 실험적 검증을 통해 이러한 이점을 검증합니다. 본 연구는 HPDC의 열 전달 메커니즘에 대한 더 깊은 이해에 기여하고 칠 벤트 설계를 최적화하기 위한 경로를 제공합니다.
연구의 실제적 의미:
본 연구의 실제적 의미는 다이캐스팅 산업에 매우 중요합니다. MoldMAX와 같은 구리 합금 칠 벤트를 구현하면 다음과 같은 결과를 얻을 수 있습니다.
- 생산성 향상: 냉각 시간 단축은 HPDC에서 더 빠른 사이클 시간과 생산 속도 증가로 이어집니다.
- 부품 품질 향상: 기공 및 플래시 결함 감소는 기계적 특성 및 표면 조도가 향상된 고품질 주조 부품을 만듭니다.
- 공정 효율성 향상: HPDC 공정의 전반적인 효율성 및 효과가 향상됩니다.
연구의 한계 및 향후 연구 분야:
논문에서는 "향후 연구에서는 주입 온도, 과열, 에어 갭 형성, 주입 속도 및 압력 증강과 같은 다른 매개변수의 영향을 고려해야 합니다."라고 제안합니다. 이러한 매개변수는 칠 벤트 성능에 대한 이해를 더욱 개선하고 HPDC 공정을 최적화할 수 있습니다.
8. 참고 문헌:
- [1] A Kaye, A Street. Die Casting Metallurgy. Butterworth and Co Ltd., 1982
- [2] F. Bonollo, N. Gramegna, and G. Timelli, "High-pressure die- casting: contradictions and challenges," The Minerals, Metals & Materials Society, JOM, vol. 67, no. 5, pp. 901-908, 2015.
- [3] L. H. Wang. "Mathematical modelling of air evacuation in die casting process via CASTvac and other venting devices," Int Journal of Cast Metals Research, vol. 20 pp. 191-197, 2007.
- [4] MoldMAX HH Material Property Data, Materion Performance Alloys, Materion Corporation 2017.
- [5] I. Rosindale and K. Davey, "Steady state thermal model for the hot chamber injection system in the pressure die casting process," Journal of Materials Processing Technology, vol. 82, no. 1, pp. 27-45, 1998.
- [6] M. T. A. Rasgado, "Bi-metallic dies for rapid die casting," Journal of Materials Processing Technology vol. 175, pp. 109- 116, 2006.
- [7] S. R. Ahmed, K. D. Devi, and S. V. S. Himathejeswini, "Design & analysis of heat sink high-pressure die casting component," International Journal of Current Engineering and Technology, 2016
- [8] H. J. Kwon, H. K. Kwon, "Computer Aided Engineering (CAE) simulation for the design optimization of gate system on high pressure die casting (HPDC) process," Robotics and Computer-Integrated Manufacturing vol. 55 pp. 147-153, 2018.
- [9] W. B. Yu, Y. Y. Cao, X. B. Li et al, "Determination of interfacial heat transfer behavior at the metal/shot sleeve of high pressure die casting process of AZ91D alloy," Journal of Materials Science & Technology vol. 33 pp. 52-58, 2017
- [10] S. I. Jeong, C. K. Jin, H. Y. Seo et al, "Mould design for clutch housing parts using a casting simulation of high pressure die casting," International Journal Of Precision Engineering And Manufacturing, vol. 17, no. 11, pp. 1523-1531, 2016
- [11] R. W. R. W. Jeppson, Analysis of Flow in Pipe Networks, Butterworth Publications, 1976
- [12] MatWeb Material Property Data, Aluminum ADC12 Die Casting Alloy, Automation Creations, Inc 2009.
- [13] K. N. Prabhu, "Casting/mold thermal contact heat transfer during solidification of Al-Cu-Si alloy (LM 21) plates in thick and thin molds," Journal of Materials Engineering and Performance, ASM International vol. 14, no. 5, pp. 604-609, 2005.
9. 저작권:
- 본 자료는 "Duoc T Phan, Syed H Masood, Syed H Riza, and Harsh Modi"의 논문: "고성능 구리 합금 칠 벤트의 개발: 고압 다이캐스팅"을 기반으로 합니다.
- 논문 출처: doi: 10.18178/ijmerr.9.7.943-948
본 자료는 위 논문을 소개하기 위해 제작되었으며, 상업적 목적으로 무단 사용하는 것을 금지합니다.
Copyright © 2025 CASTMAN. All rights reserved.