본 소개 내용은 한국생산기술연구원, 전북대학교에서 발행한 ["고압 다이캐스팅용 알루미늄 합금의 열전도성 및 주조성에 미치는 첨가원소의 영향"] 의 연구 내용입니다.
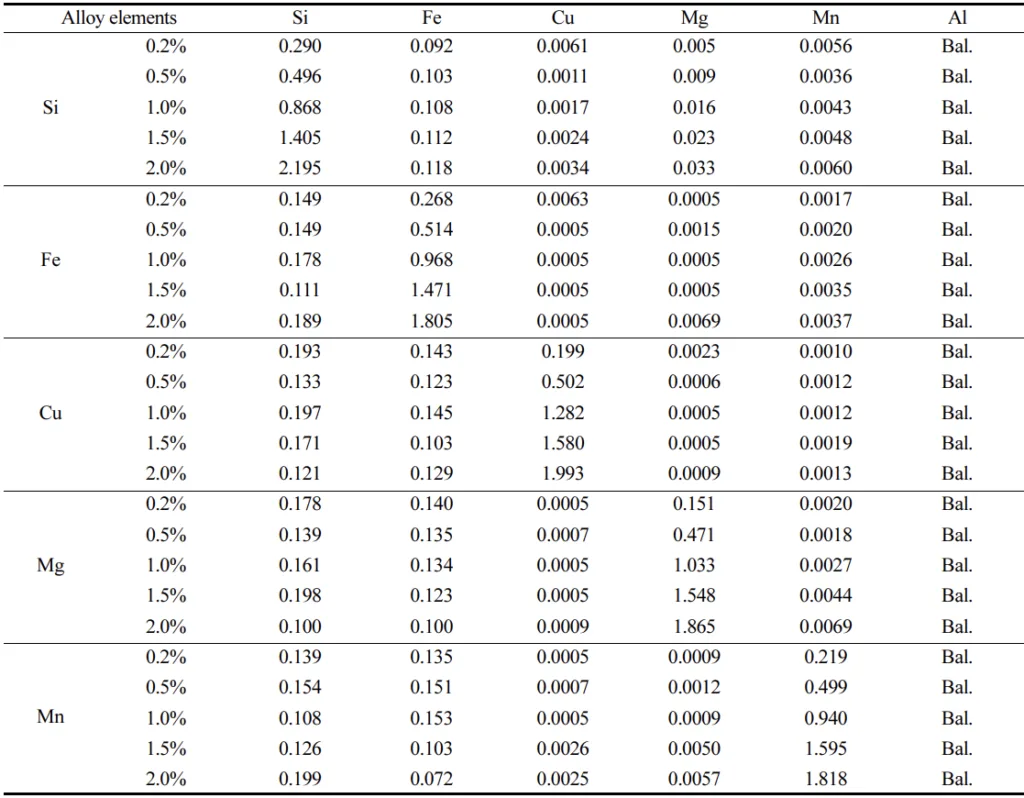
1. Overview:
- Title: 고압 다이캐스팅용 알루미늄 합금의 열전도성 및 주조성에 미치는 첨가원소의 영향 (Effect of Alloying Elements on the Thermal Conductivity and Casting Characteristics of Aluminum Alloys in High Pressure Die Casting)
- Author: 김철우, 김영찬, 김정한, 조재익, 오민석 (Cheol-Woo Kim, Young-Chan Kim, Jung-Han Kim, Jae-Ik Cho, Min-Suk Oh)
- Publication Year: 2018
- Publishing Journal/Academic Society: 대한금속·재료학회지 (Korean Journal of Metals and Materials)
- Keywords: thermal conductivity, heat sink, die-casting, radiation of heat
2. Abstracts / Introduction
Abstract: High pressure die casting is one of the precision casting methods. It is highly productivity and suitable for manufacturing components with complex shapes and accurate dimensions. Recently, there has been increasing demand for efficient heat dissipation components, to control the heat generated by devices, which directly affects the efficiency and life of the product. Die cast aluminum alloys with high thermal conductivity are especially needed for this application. In this study, the influence of elements added to the die cast aluminum alloy on its thermal conductivity was evaluated. The results showed that Mn remarkably deteriorated the thermal conductivity of the aluminum alloy. When Cu content was increased, the tensile strength of cast aluminum alloy increased, showing 1 wt% of Cu ensured the minimum mechanical properties of the cast aluminum. As Si content increased, the flow length of the alloy proportionally increased. The flow length of aluminum alloy containing 2 wt% Si was about 85% of that of the ALDC12 alloy. A heat dissipation component was successfully fabricated using an optimized composition of Al-1 wt%Cu-0.6 wt%Fe-2 wt%Si die casting alloy without surface cracks, which were turned out as intergranular cracking originated from the solidification contraction of the alloy with Si composition lower than 2 wt%.
- 서론
고압 다이캐스팅 공법은 정확하게 기계 가공된 금형에 용용금속을 주입하여 필요한 주조형상과 완전히 일치하는 주물을 얻는 정밀주조법이다. 다이캐스팅 공정을 적용하면 정밀하고 복잡한 형상의 부품을 빠른 시간에 대량으로 생산할 수 있어 생산성이 매우 높다 [1,2]. 최근 자동차 및 전기전자 산업 등 다양한 분야에서 부품의 고효율화 및 집적화 등에 기인한 발열 문제가 크게 대두되고 있다. 따라서 부품의 온도상승으로 인한 제품의 효율 저하 및 수명 단축을 방지하기 위해 방열특성이 우수한 부품 개발이 크게 요구된다.
3. Research Background:
Background of the Research Topic:
최근 자동차 및 전기전자 산업에서 부품의 고효율화 및 집적화로 인해 발열 문제가 대두되고 있으며, 부품의 온도 상승으로 인한 제품의 효율 저하 및 수명 단축을 방지하기 위해 방열 특성이 우수한 부품 개발이 요구되고 있다. 일반적으로 방열 특성이 요구되는 부품의 경우 열전도도가 높은 AI 전신재 합금이나 99 wt% 이상의 AI을 이용한 주조공법이 적용되고 있다.
Status of Existing Research:
다이캐스팅용 Al 합금은 합금의 주조성이나 제품의 물리적·화학적 특성 향상을 위해 첨가되는 소량의 금속원소로부터 열전도도가 낮아지는 경향이 있다. 예컨대 용탕의 유동성 및 주조성 향상을 위한 Si 첨가 [4], 강도 및 가공성 향상을 위한 Cu 및 Mn 첨가 [5-7], 금형의 소착 저항성 향상을 위한 Fe 첨가 [8] 등 Al에 첨가되는 상기 미량 금속원소의 양이 증가할수록 제품의 열물성은 열화된다.
Necessity of the Research:
다이캐스팅 공정 적용 가능하며 방열특성이 우수한 Al 합금 개발을 위해서는 미량 첨가원소의 조성 최적화가 필수적이다. 기존의 ALDC12 합금은 열전도도가 99 W/m·k로 순수 알루미늄(234 W/m·k) 대비 매우 낮아 기존의 합금 조성 및 제조방법으로는 방열부품 제작이 불가하다 [3]. 따라서 높은 열전도도 뿐만 아니라 다이캐스팅 주조가 가능한 고압 다이캐스팅용 Al 합금 개발이 매우 절실하다.
4. Research Purpose and Research Questions:
Research Purpose:
본 연구의 목적은 고압 다이캐스팅용 Al 합금의 열전도도에 미치는 첨가원소의 영향을 평가하고, 방열 특성이 우수한 Al 합금 개발을 위한 최적 합금 조성을 도출하는 것이다.
Key Research:
본 연구에서는 첨가되는 합금원소의 성분을 변화시킨 후 열전도성 및 유동성에 미치는 영향을 고찰하였으며, 도출된 최적 합금 조성으로 실제 자동차 음향기기에 적용되는 방열부품을 제작하여 그 성능을 비교 평가하였다.
5. Research Methodology
Research Design:
본 연구는 첨가 원소(Si, Fe, Cu, Mg, Mn)의 함량을 변화시키면서 Al 합금의 열전도성, 유동성, 기계적 특성 및 미세 조직을 분석하는 실험적 연구로 설계되었다.
Data Collection Method:
- 성분 분석: Spark emission spectrometer (QUANTRON)를 사용하여 합금의 화학 조성 분석.
- 열전도도 측정: Laser flash 기술을 활용한 열물성 분석장치(LFA 477, Netzsch)를 이용하여 열전도도 측정.
- 미세 조직 관찰: 광학 현미경 및 FE-SEM(JSM-7000F, JEOL)과 EDS를 이용하여 미세 조직, 석출상 및 미세 구조 분석.
- 기계적 특성 평가: ASTM E8M 규격에 따른 인장시험기(AG-IS, SHIMADZU)를 사용하여 인장 강도 및 연신율 측정.
- 유동성 측정: 서펜타인(Serpentine) 형태의 금형을 이용한 다이캐스팅 후 주편의 길이 측정.
Analysis Method:
측정된 열확산계수, 비열 및 밀도를 이용하여 열전도도를 계산하고, 첨가 원소의 종류와 함량 변화에 따른 열전도도, 유동성, 기계적 특성 및 미세 조직 변화를 분석하였다. image analysis를 통해 Al-Cu 석출상의 면적 분율을 측정하였다.
Research Subjects and Scope:
본 연구의 연구 대상은 다양한 첨가 원소(Si, Fe, Cu, Mg, Mn)를 각각 0.2~2 wt% 첨가한 Al 합금이다.
6. Main Research Results:
Key Research Results:
- Mn: Al 합금의 열전도도를 현저히 저하시키는 것으로 나타났다.
- Cu: Cu 함량이 증가함에 따라 Al-Cu 금속간 화합물의 석출량이 증가하고, 인장 강도가 비례하여 증가하였다. 1 wt% Cu 첨가 시 최소 기계적 특성이 확보되었다.
- Si: Si 함량이 증가함에 따라 Al 합금의 유동성이 비례하여 증가하였다. 2 wt% Si 첨가된 Al 합금의 유동 길이는 ALDC12 합금의 약 85% 수준이었다.
- 최적 합금 조성: Al-1 wt%Cu-0.6 wt%Fe-2 wt%Si 조성의 다이캐스팅 합금을 사용하여 표면 균열이 없는 방열 부품 제작에 성공하였다.
Analysis of presented data:
- 열전도도: 그림 1(d)는 첨가 원소의 함량이 증가할수록 열전도도가 감소하는 것을 보여준다. 특히 Mn 첨가가 열전도도 저하에 가장 큰 영향을 미쳤다. Si 함량 변화에 따른 열전도도 변화는 그림 8(b)에 나타나 있으며, Si 함량이 증가할수록 열전도도가 감소하는 경향을 보인다.
- 기계적 특성: 그림 2는 Cu 함량 증가에 따라 인장 강도가 증가하고 연신율이 감소하는 것을 보여준다.
- 유동성: 그림 7은 Si 함량 증가에 따라 유동 길이가 증가하는 것을 나타낸다. 2 wt% Si 첨가 시 ALDC12 대비 약 85% 수준의 유동성을 나타냈다.
- 미세 조직: 그림 3, 4, 5는 Cu 함량 증가에 따라 Al-Cu 석출상이 증가하는 것을 보여준다.
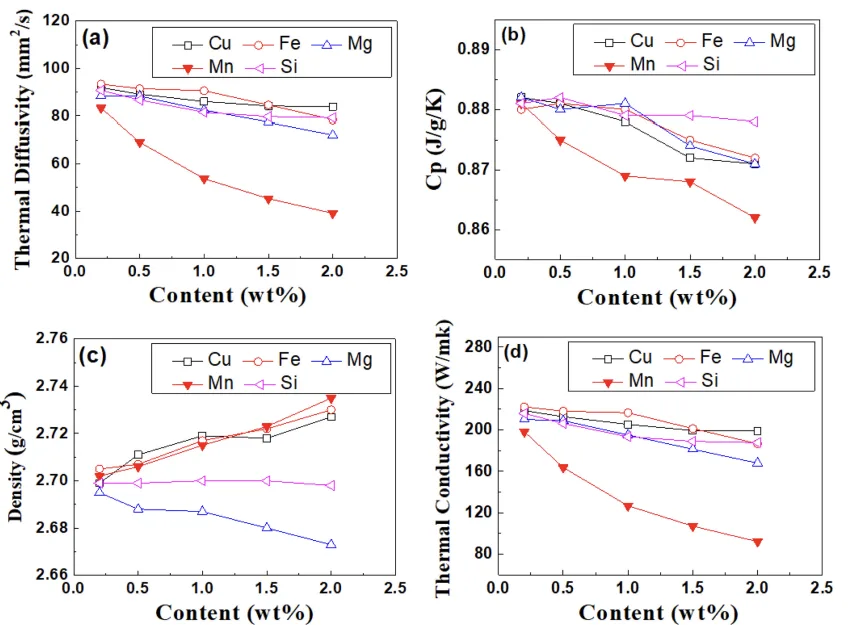
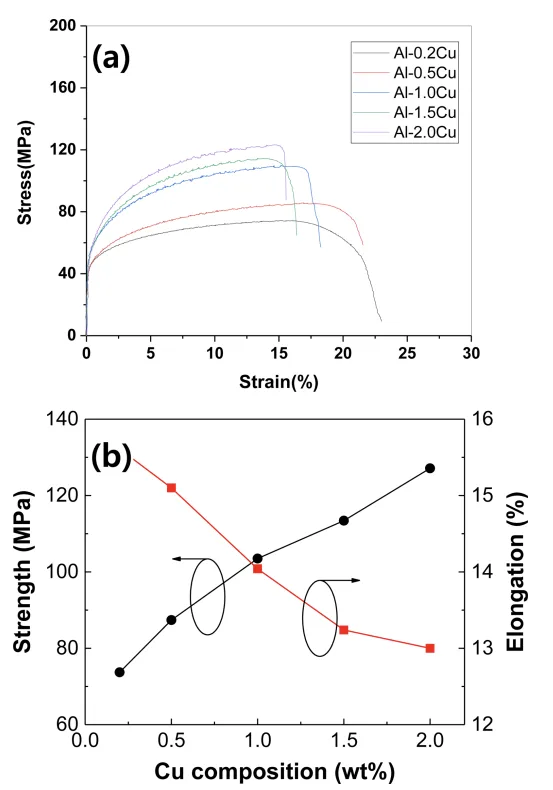
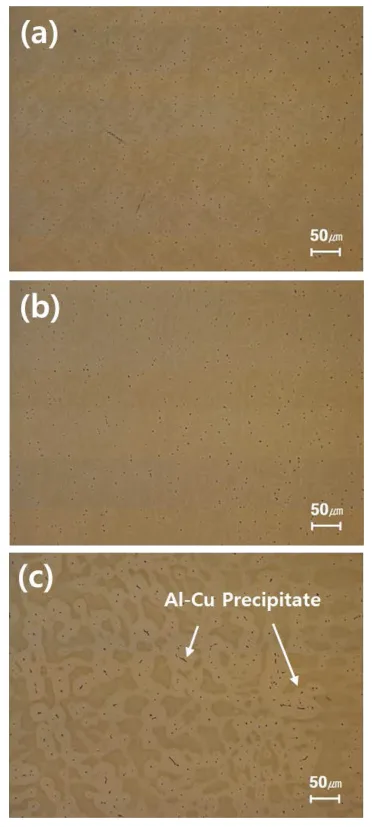
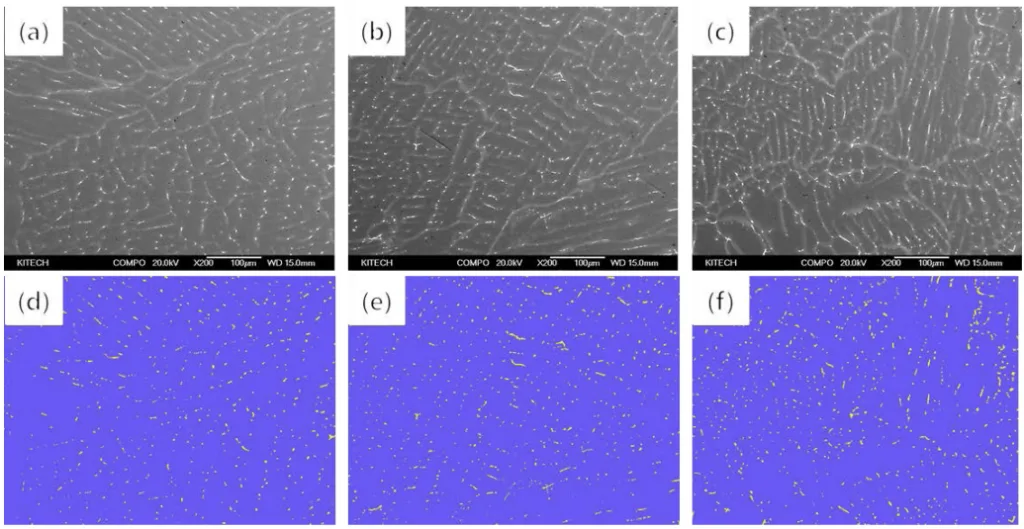
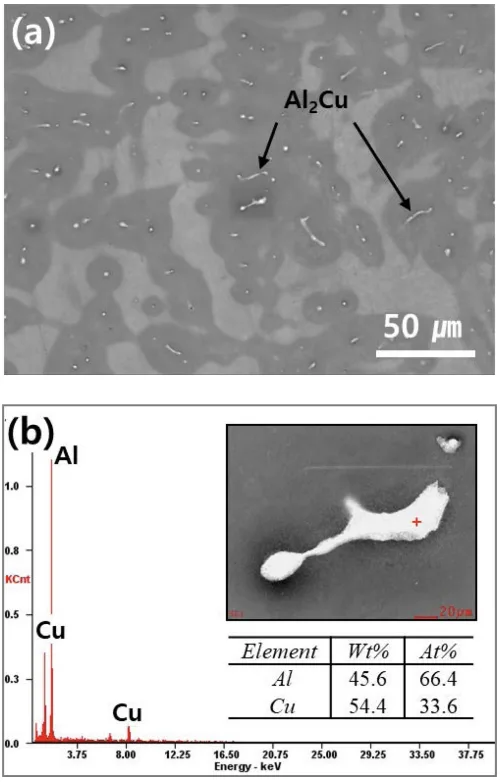
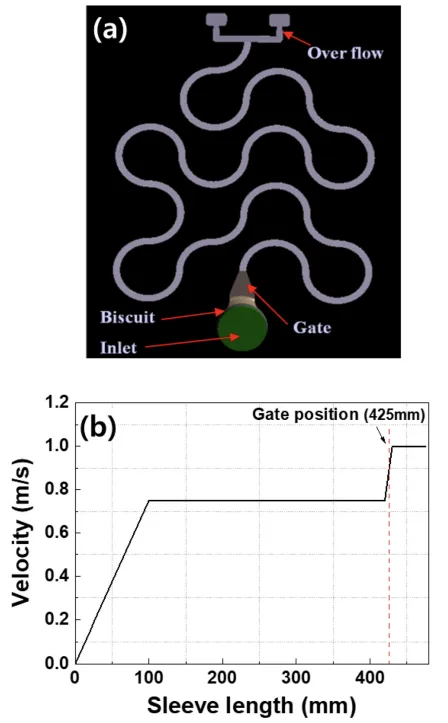
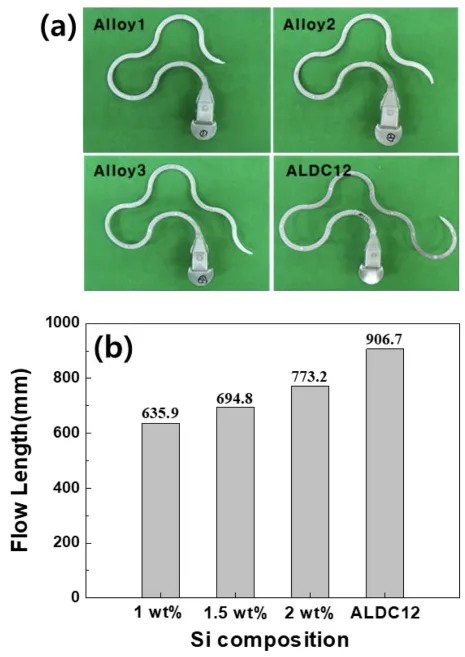
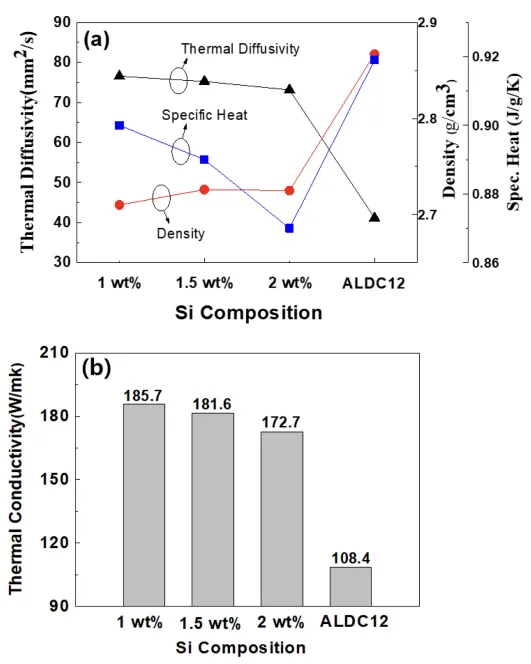
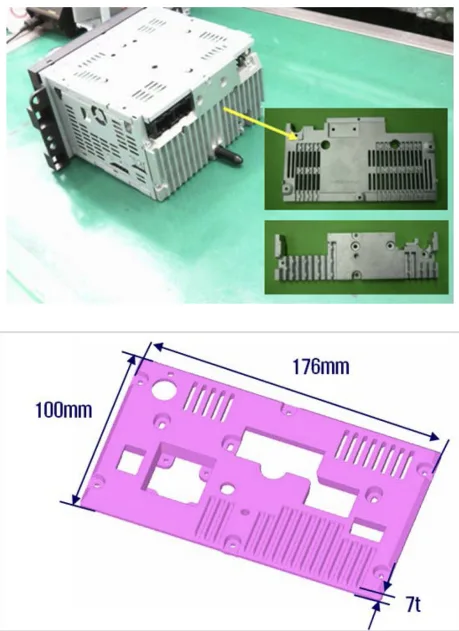
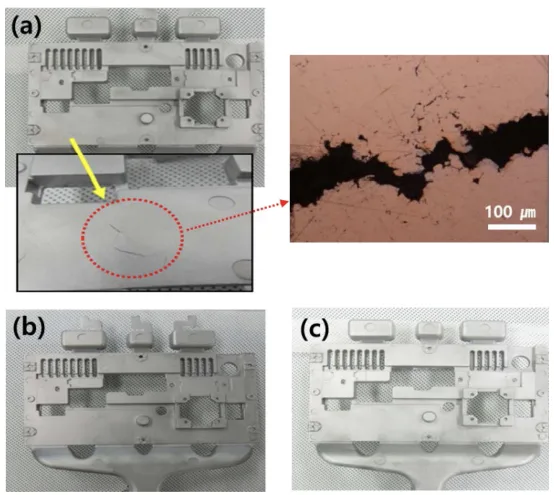
Figure Name List:
- Fig. 1. Thermal properties of alloys with different additive metals; (a) Thermal diffusivity, (b) Specific heat, (c) Density, (d) Thermal conductivity.
- Fig. 2. (a) Stress-strain curves and (b) change of tensile strength and elongation according to composition of Cu.
- Fig. 3. Microstructure of Al alloys with different Cu composition; (a) Al-1.0wt%Cu, (b) Al-1.5wt%Cu, (c) Al-2.0wt%.
- Fig. 4. SEM image of (a) Al-1wt%Cu, (b) Al-1.5wt%Cu and (c) Al-2wt%Cu (x200) and image analysis data of (d) Al-1wt%Cu, (e) Al-1.5wt%Cu and (f) Al-2wt%Cu (×200).
- Fig. 5. (a) SEM image and (b) EDS results of Al alloy with 2 wt% Cu.
- Fig. 6. (a) Schematic of metal mold and (b) injection speed profile for fluidity test.
- Fig. 7. Results of die casting fluidity test; (a) Schematic of die cast specimens, (b) flow length.
- Fig. 8. (a) Thermal properties and (b) Thermal conductivity of alloys with different additive metals.
- Fig. 9. Die cast heat sink component (car audio heat sink).
- Fig. 10. Diecast car audio heat sink component with various alloy compositions; (a) Al-1.0 wt%Cu-0.6 wt%Fe-1.5 wt%Si), (b) Al-1.0 wt%Cu-0.6 wt%Fe-2.0 wt%Si, (c) Al-2.5 wt%Cu-0.8 wt%Fe-11 wt%Si-0.2 wt%Mg-0.3 wt%Mn (ALDC12).
7. Conclusion:
Summary of Key Findings:
본 연구를 통해 고압 다이캐스팅용 Al 합금의 열전도성 및 주조성에 미치는 첨가 원소의 영향을 평가한 결과, 다음과 같은 결론을 얻었다. Mn은 Al 합금의 열전도도를 현저히 감소시키며, Cu는 인장 강도를 증가시키고, Si은 유동성을 향상시킨다. 최적 합금 조성으로 Al-1.0 wt%Cu-0.6 wt%Fe-2.0 wt%Si 합금이 도출되었으며, 이는 ALDC12 합금 대비 2배 이상의 높은 열전도도와 약 85% 수준의 유동성을 나타낸다.
Academic Significance of the Study:
본 연구는 고압 다이캐스팅용 Al 합금에서 첨가 원소가 열전도성 및 주조성에 미치는 영향에 대한 체계적인 데이터를 제공하며, 고열전도도 다이캐스팅 합금 설계에 대한 학문적 기반을 확장하였다.
Practical Implications:
본 연구에서 개발된 Al-1.0 wt%Cu-0.6 wt%Fe-2.0 wt%Si 합금은 자동차 음향기기용 방열 부품과 같이 고방열 성능이 요구되는 다이캐스팅 부품 제조에 활용될 수 있으며, 산업적으로 고효율 방열 부품 개발에 기여할 수 있다.
Limitations of the Study and Areas for Future Research:
본 연구는 특정 조성 범위 내에서 첨가 원소의 영향을 평가하였으며, 더욱 우수한 다이캐스팅 주조를 위해서는 첨가 원소 및 공정 조건에 대한 추가적인 최적화 연구가 필요하다. 또한, 개발된 합금의 신뢰성 및 내구성에 대한 추가 연구가 요구된다.
8. References:
- K. P. Keller, IEEE, 10.1109/ITHERM, 112 (1998).
- K. Keller, IEEE, 10.1109/IEMTE, 113 (1998).
- J. R. Davis, ASM, 10.1361/autb, 351 (2001).
- C. R. Loper, Jr., AFS Trans. 533 (1992).
- C. Mascre, Fonderie, 108, 4330 (1995).
- H. Y. Kim, S. W. Han, and H. M. Lee, Mater. Lett. 60, 1880 (2006).
- S. S. Sreeja Kumari, R. M. Pillai, T. P. D. Rajan, and B. C. Pai, Mater. Sci. & Eng. A 460-461, 561 (2007).
- L. A. Naraynan, F. H. Samuel, and J. E. Gruzleski, Metall. Mater. Trans. A 26A, 2161 (2004).
- W. J. Parker, R. J. Jenkins, C. P. Butler, and G. L. Abbott, J. Appl. Phys. 32, 1679 (1961).
- R. D. Cowan, J. Appl. Phys. 34, 926 (1963).
- R. A. Goncalves, Procedia Manuf. 1, 683 (2015).
- L. F. Mondolfo, “Aluminum Alloys: Structure and Properties", Butter Worths (1976).
- H. J. Kim, C. M. Cho, and C. Y. Jeong, J.KFS, 29, 169 (2009).
- D. K. Lews, "Silicon and Its Effect on Fluidity of Aluminum Alloys.", A.S.&R. Co., Inc, Data Sheet.
9. Copyright:
- This material is "김철우·김영찬·김정한·조재익·오민석"’s paper: Based on "고압 다이캐스팅용 알루미늄 합금의 열전도성 및 주조성에 미치는 첨가원소의 영향".
- Paper Source: DOI: 10.3365/KJMM.2018.56.11.805
This material was created to introduce the above paper, and unauthorized use for commercial purposes is prohibited.
Copyright © 2025 CASTMAN. All rights reserved.