This introduction paper is based on the paper "Development of Platinum-Base Superalloy Components via Powder Metallurgy" published by "Euro PM2009 – Non-Ferrous Materials - Processing".
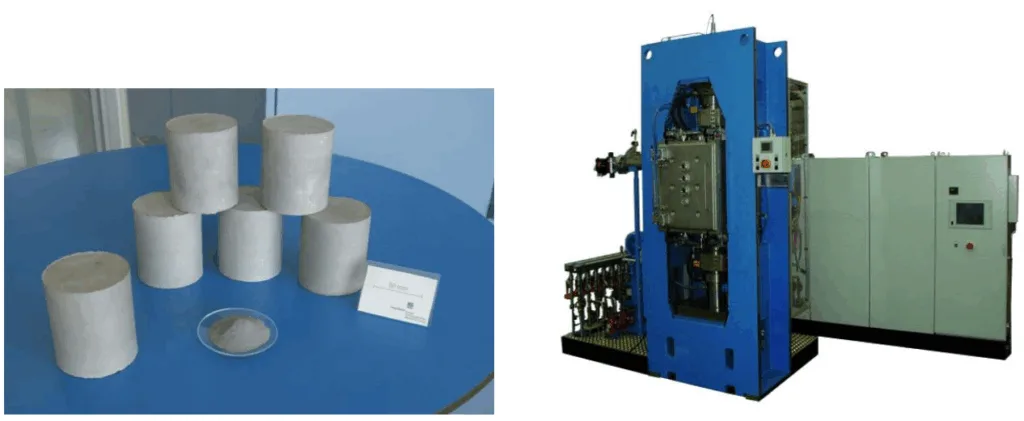
1. Overview:
- Title: Development of Platinum-Base Superalloy Components via Powder Metallurgy
- Author: A. Mwamba, L.H. Chown and R. Süss
- Year of publication: 2009
- Journal/academic society of publication: Euro PM2009 – Non-Ferrous Materials - Processing
- Keywords: Keywords not explicitly listed in the paper.
2. Abstract:
Platinum-base superalloys were developed by Mintek before but as these alloys are difficult to cast and have limited formability, powder metallurgy was a potential production route to be considered. In this work, two methods based on powder metallurgy were used to produce alloyed platinum powder to the atomic composition of Pt₈₄:Al₁₁:Cr₃Ru₂. In the first, elemental powders of aluminium, chromium, and ruthenium were melted together with platinum sponge to form a pre-alloy. The pre-alloy was then remelted and water-atomised to produce a pre-alloyed platinum powder. In the second, pure platinum produced by water atomisation was mixed with elemental powders of aluminium, chromium, and ruthenium and mechanically alloyed. The pre-alloyed and mechanically alloyed powders were characterised with reference to the morphology, size distribution and density of pure platinum powder, and uniaxially compressed. The compacts were sintered. Using a combination of optical microscopy, XRD, and EDX analysis, the sintered specimens were characterised with respect to the powder properties, the microstructure, and hardness and compared to those of a pure platinum compact and cast alloys of the same composition.
3. Introduction:
Platinum is well known for its use in autocatalytic and jewellery applications. However, similarities in properties with nickel in presence of certain alloying elements have drawn attention on the use of platinum alloys as high-temperature materials for structural applications. For many years, nickel-base superalloys have been the materials of choice for these applications. The use of NBSAs in turbine blades for aeronautic and land-based turbines is a typical example. However, because of new applications where higher operating temperatures are required, nickel as base metal is reaching its temperature limit. A replacement material is needed, and platinum group metals like iridium (1), rhodium (2) and platinum (3) were seen as good candidates because of similar behaviour to nickel with the added advantage of having higher melting points.
Mintek has developed platinum-base superalloys (PBSAs) with microstructures similar to those of NBSAs (4-6). The microstructure in the platinum superalloys is based on the Pt-Al system. This system is made of microstructures comprising γ' Pt₃Al particles in Pt-based γ matrix. Alloying this Pt-Al base system with Ni and Cr (7) or Ru and Cr (8) has successfully stabilized the L1₂ structure of Pt₃Al. A quaternary alloy was developed and optimised with Pt₈₄:Al₁₁:Ru₂:Cr₃ showing the best structure (7). Studies carried out on hot corrosion behaviour of platinum-based superalloys have shown good results, outperforming NBSAs (9). Investigations of creep properties of platinum-based superalloys have also shown that certain platinum-base alloys have high temperature stress-rupture strength as well as ductility making them potential high-temperature alloys (10). However, the poor castability and formability of PBSAs has made it difficult to make these alloys via traditional methods of casting and forming, raising the need to explore powder metallurgy routes (4).
4. Summary of the study:
Background of the research topic:
Platinum-base superalloys (PBSAs) are being explored as alternatives to nickel-base superalloys (NBSAs) for high-temperature structural uses because platinum offers a higher melting point while exhibiting alloying characteristics similar to nickel. [Introduction]
Status of previous research:
Mintek has previously developed PBSAs based on the Pt-Al system, featuring γ' Pt₃Al precipitates in a Pt-based γ matrix, with stability enhanced by alloying elements such as Ni, Cr, and Ru. [Introduction] These PBSAs demonstrated favorable hot corrosion resistance and creep properties but were hindered by poor castability and formability. [Introduction]
Purpose of the study:
The study aimed to investigate powder metallurgy as a viable production pathway for PBSAs, specifically targeting the Pt₈₄:Al₁₁:Cr₃Ru₂ composition, to overcome the challenges associated with casting and forming these advanced alloys. [Abstract, Introduction]
Core study:
The research focused on two distinct powder metallurgy techniques: firstly, the water atomisation of a pre-formed alloy, and secondly, the mechanical alloying of elemental powders with water-atomised pure platinum. [Abstract] The characteristics of the powders produced by these methods, as well as their sintered compacts, were thoroughly evaluated and compared. [Abstract]
5. Research Methodology
Research Design:
The study was designed to produce alloyed platinum powders with the target composition Pt₈₄:Al₁₁:Cr₃Ru₂ through two powder metallurgy routes: (i) pre-alloying followed by water atomisation and (ii) mechanical alloying of pure Pt powder with elemental additions. [Experimental procedures] The powders were subsequently compacted and sintered, and the resultant materials were characterized to assess the efficacy of each route. [Experimental procedures]
Data Collection and Analysis Methods:
Powder production involved creating a pre-alloyed powder by melting elemental constituents with Pt sponge, followed by water atomisation (at 200 bars water pressure, 100 °C superheat) and sieving to <150 µm. [Experimental procedures] Mechanically alloyed powder was prepared by milling water-atomised pure Pt powder (<500 µm) with elemental Al, Cr, and Ru. [Experimental procedures]
Powder characterisation included determining apparent density using an Arnold meter, and evaluating particle shape, size, and distribution with a Malvern Mastersizer 2000, optical microscopy, SEM, XRD, and EDX. [Experimental procedures]
Powder compaction of pre-alloyed powder was performed using an 80-ton uniaxial press according to MPIF standard 41, while mechanically alloyed powder was pressed at moderate pressures ranging from 10 to 35 MPa (as detailed in Table 1) in a 17.50 mm die. [Experimental procedures, Table 1]
Sintering and heat treatment were conducted in an argon atmosphere, with samples heated at a rate of 8°C/minute to 1450°C and held for 5 hours. [Experimental procedures] Post-sintering heat treatments involved reheating some pre-alloyed and mechanically alloyed compacts to 1450°C for 100 hours, and mechanically alloyed compacts to 1250°C for 100 hours. [Experimental procedures]
Characterisation of compacts involved evaluating green density relative to pure bulk platinum density. Sintered compacts were analysed for sintered density, microstructure (using optical microscopy and EDX), and hardness, with comparisons made to cast alloys of the same composition. [Experimental procedures]
Research Topics and Scope:
The research focused on the development of Pt-base superalloy components (Pt₈₄:Al₁₁:Cr₃Ru₂) via powder metallurgy, comparing the pre-alloyed versus mechanically alloyed powder production routes. [Abstract, Introduction] The scope included the evaluation of powder characteristics and the microstructural and mechanical properties of the sintered compacts. [Abstract, Introduction]
6. Key Results:
Key Results:
Powder Characteristics: The pre-alloyed powder exhibited a monomodal particle size distribution, with 50% of particles larger than 43.8 µm, as shown in Figure 1 and Table 2. In contrast, the mechanically alloyed powder was finer, with 50% of particles smaller than 6.7 µm, and its size distribution was between monomodal and bimodal (Figure 1, Table 2). Both powder types displayed a rounded irregular morphology (Figure 2). EDX analysis confirmed successful alloying for both powders (Table 3); however, oxygen was detected in the pre-alloyed powder, indicating oxidation during water atomisation, whereas the milled powder was oxygen-free. [Powder chemistry, Table 3] XRD patterns for both powders showed a distorted platinum lattice, and Pt₃Al peaks were also identified (Figure 3). [Phase identification]
Powder Compaction and Sintering: The pre-alloyed powder (<150 µm) demonstrated poorer compaction behavior, achieving a green density of approximately 15.0 g/cm³, compared to pure Pt powder (<500 µm) which reached about 17.5 g/cm³. [Powder response to compacting and sintering] The mechanically alloyed powder had a low apparent density (around 3.5 g/cm³) and consequently low green densities (approximately 10.0 g/cm³), as detailed in Table 5. [Powder response to compacting and sintering, Table 5] Sintering led to a density increase of about 7% for pre-alloyed compacts and around 5% for pure Pt compacts. [Powder response to compacting and sintering] For mechanically alloyed compacts pressed at 10-20 MPa, a more substantial density increase of 30-35% was observed after sintering. [After sintering…]
Microstructure of Sintered Compacts: Sintered pre-alloyed platinum compacts featured a platinum solid solution matrix containing cuboidal Pt₃Al precipitates of approximately 500 nm in size, alongside very fine precipitates around 10-50 nm (Figure 4 (a) and (b)). [Microstructure of the sintered compacts] An interesting observation was the formation of liquid when mechanically alloyed compact samples were aged at 1450°C for 100 hours. [Microstructure of the sintered compacts] As-sintered mechanically alloyed compacts (Figure 4 (c)) and those subsequently heat-treated at 1250°C for 100 hours (Figure 4 (d)) displayed a greyish matrix with randomly distributed precipitates; precipitates smaller than 100 nm were visible after the 1250°C heat treatment. [Microstructure of the sintered compacts]
Sintering Issues: Evidence of poor sintering, such as particle pullout and craters (Figure 5), was observed. This was attributed to the presence of an aluminium oxide layer on the powder particles, which hindered inter-particle bonding. [Microstructure of the sintered compacts]
Hardness: The micro-hardness values for pre-alloyed sintered compacts (343±50 HV₀.₅ as-sintered, 369±37 HV₀.₅ aged, Table 8) were within the typical range reported for cast alloys of the same composition (300-400 HV₁₀). [Hardness of the sintered compacts] Similarly, the macro-hardness of these pre-alloyed compacts (336±11 HV₁₀ as-sintered, 365±23 HV₁₀ aged, Table 9) aligned with cast alloy values. [Hardness of the sintered compacts] Mechanically alloyed compacts exhibited lower macro-hardness (139±16 HV₁₀ as-sintered, 199±15 HV₁₀ aged, Table 9), though ageing resulted in a significant increase. [Hardness of the sintered compacts] Conversely, the micro-hardness of mechanically alloyed compacts decreased after ageing (from 316±25 to 240±22 HV₀.₅, Table 8), which was possibly due to stress relief and particle relaxation. [Hardness of the sintered compacts]
Figure Name List:
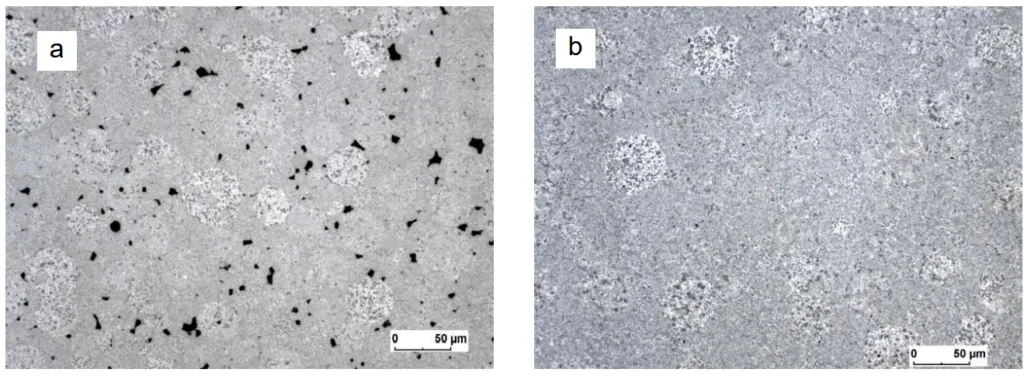
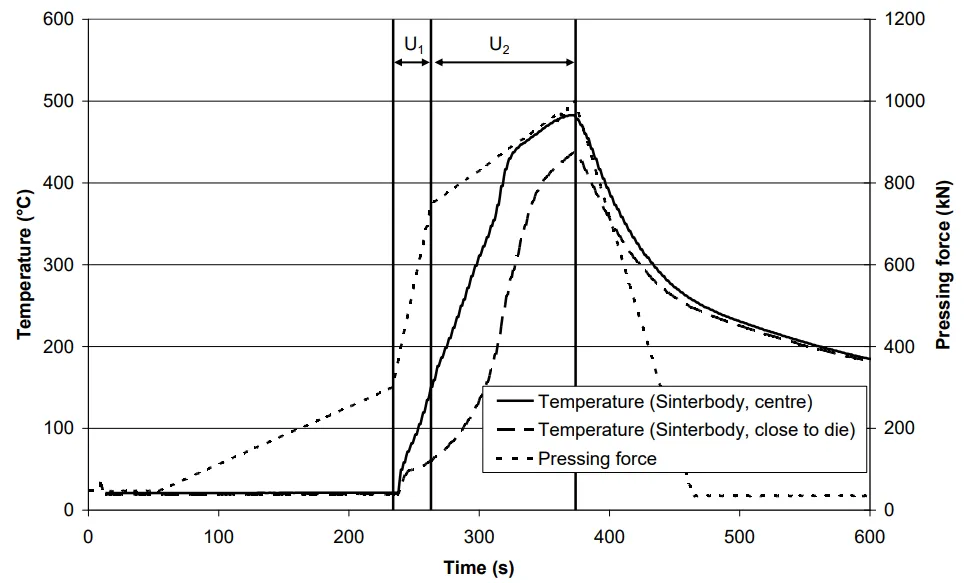
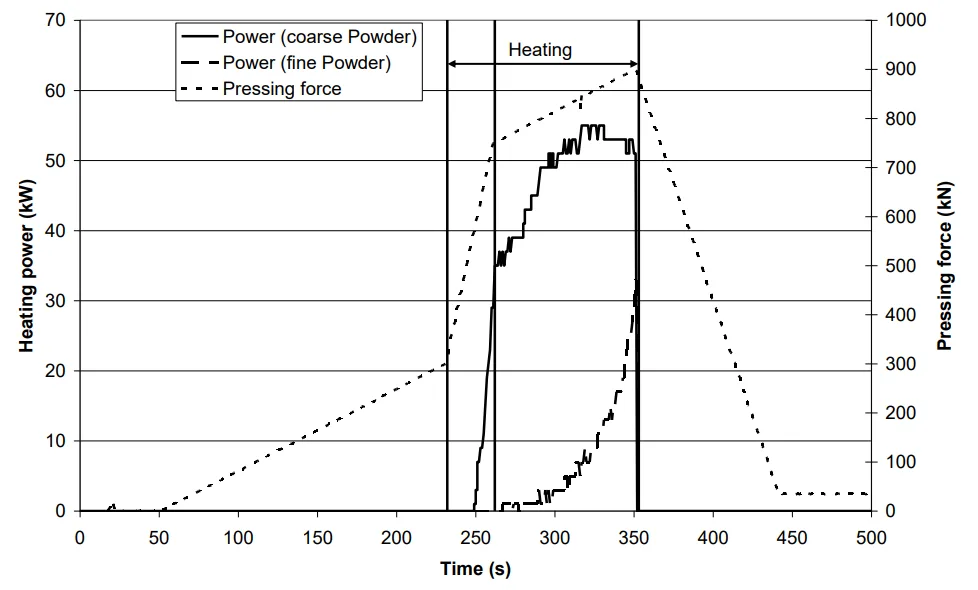
![Fig. 4. Microstructures of a consolidated MA sample (left) and a gas-atomized sample (right) with composition Mo–9Si–8B [10]. The Mo matrix is the brightest appearing phase, and the grey and dark grey appearing phases are Mo3Si and Mo5SiB2, respectively.](https://castman.co.kr/wp-content/uploads/image-2459-1024x378.webp)
![Fig. 6: Double-logarithmic plot of strain rate vs. applied stress for various Mo-9Si-8B alloys. Data for a single-crystalline Nickelbase superalloy CMSX-4 are shown for comparison [14].](https://castman.co.kr/wp-content/uploads/image-2454.webp)
- Figure 1. Particle size distribution for two powders.
- Figure 2: Particle shape in different powders.
- Figure 3. XRD pattern of pre-alloyed platinum powder showing (a) slightly shifted Pt peaks; (b) slightly shifted Pt₃Al peaks
- Figure 4: Typical microstructure of sintered pre-alloyed platinum compact.
- Figure 5: Typical features of poor-sintering area.
7. Conclusion:
- The particle size and size distribution in the pre-alloyed powder was narrow with a relatively small mean size. The pre-alloyed powder was surrounded by a discontinuous layer of aluminium oxide, which was the result of aluminium in the melt that reacted with oxygen from air and/or water. The compacts obtained from pre-alloyed powder were of poor sintering quality with a lot of unbound particles and porosity due to the presence of the aluminium oxide layer that prevented bonding during sintering. The microstructure in the sintered compacts was similar to the microstructure of cast alloys which consisted of a platinum solid solution matrix with Pt₃Al precipitates. The hardness of the sintered compacts was in the range of hardness found in the cast alloys of the same composition (300 -400 HV₁₀). Reheating and keeping the pre-alloyed alloy compact at the sintering temperature for 100 hours did not change the sintering quality or microstructure, and only resulted in a slight increase in hardness.
- It is possible to mechanically alloy platinum, aluminium, chromium and ruthenium elemental powders to the composition of the platinum-based superalloy. The powder produced by mechanical alloying was flake-like in shape, containing a lot of fine particles with a mean size below 5 µm, a high level of agglomeration and a particle size distribution lying between the monomodal and the bimodal distribution. The apparent density was very low. The mechanically alloyed powder showed a poor response to compaction but a good response to sintering. The microstructure of the compact consisted of a platinum solid solution matrix with a distribution of Pt₃Al precipitates of different sizes and morphologies. The hardness of the compacts was lower than in cast alloys, the reason being the low compacting pressure used to consolidate the powder. During ageing, a substantial change in the microstructure took place, giving rise to the formation of Pt₃Al precipitates < 100 nm in size. The change in microstructure after ageing resulted in a substantial increase of hardness.
8. References:
- . YAMABE-MITARAI, Y., KOIZUMI, Y., MURAKAMI, R, Y., MARUKO, T., and HARADA, H., Scripta Materialia, Vol. 35, No. 2, 1996, pp. 211-215.
- . YAMABE-MITARAI, Y., KOIZUMI, Y., MURAKAMI, Ro, Y., MARUKO, T., and HARADA, H., Scripta Materialia, Vol. 36, No. 4, 1997, pp. 393-398.
- . WOLFF, I.M., and HILL, P.J., Plat. Metals Rev., 44(4) (2000) 158-166.
- . CORNISH, L.A., SÜSS, R., CHOWN, L.H., DOUGLAS, A., and GLANER, L., Plat. Metals Rev. (2009), 53, pp 2-10.
- . WENDEROTH, M., CORNISH, L.A., SÜSS, R., VORBERG, S., FISCHER, B., GLATZEL, U., and VÖLK, R., Metal. And Mat. Transactions A, Vol. 36 A, pp 567-575.
- . DOUGLAS, A., HILL, P.J., MURAKUMO, T., CORNISH, L.A. and SÜSS, R., Plat. Metals Rev.2009, 53, pp 69-77.
- . VÖLK, R., WENDEROTH, M., PREUSSNER, J., VORBERG, S., FISCHER, B., YAMABE-MITARI, Y., HARADA, H., and GLATZEL, U., Mater. Sci. Eng. A 510, (2009), pp 328-331.
- . HILL, P.J., CORNISH, L.A., ELLIS, P., WITCOMB, M.J., J. Alloys Comp. 322 (2001) 166-17.
- . MALEDI, N.B., POTGIETER, J.H., SEPHTON, M., CORNISH, L.A., CHOWN, L.H., and SÜSS, R., Int. Plat. Conf., The SAIMM 2006, pp 81-90.
- . SÜSS, R, FREUND, D., VÖLK, R., FISCHER, B., HILL, P.J., ELLIS, P., and WOLFF, I.M., Mat.Sc. Eng. A 338, 2002, pp 133-141.
- . SURYANARAYANA, C., Marcel Dekker, NY, USA (2004), ISBN 0-8247-4103-X, pp 269-315.
- . SHERIF EL-ESKANDARANY, M.,William Andrew Publishing, Norwich, NY, USA, (2001) ISBN 0-8155-1462-X.
- . MÖLLER, H.J., WELSCH, G., J. Am. Ceramic Society, Vol. 68-6, pp 320-325.
- . SERCOMBE, T.B., Mat. Science & Eng A 341, pp 163-168.
- . BONDYKE, K.J., and DUDAS, J.H. United States Patent 3,796,566, June 1972.
9. Copyright:
- This material is a paper by "A. Mwamba, L.H. Chown and R. Süss". Based on "Development of Platinum-Base Superalloy Components via Powder Metallurgy".
- Source of the paper: DOI not provided in the paper.
This material is summarized based on the above paper, and unauthorized use for commercial purposes is prohibited.
Copyright © 2025 CASTMAN. All rights reserved.
Paper Summarize:
Key questions and answers about the research:
This research aimed to develop platinum-base superalloys (Pt₈₄:Al₁₁:Cr₃Ru₂) using powder metallurgy, comparing pre-alloyed water-atomised powders with mechanically alloyed powders, due to the poor castability of these alloys. The study found that both methods could produce alloyed powders, but the pre-alloyed route suffered from oxide contamination leading to poor sintering, while the mechanically alloyed route showed better sintering response despite low green densities. Microstructures with Pt₃Al precipitates were achieved, and hardness values for pre-alloyed compacts were comparable to cast alloys, whereas mechanically alloyed compacts had lower hardness but showed significant improvement with ageing.
Q1. What were the two powder metallurgy methods investigated for producing Pt₈₄:Al₁₁:Cr₃Ru₂ alloy powder?
A1. The two methods were: 1) producing a pre-alloy by melting elemental powders with platinum sponge, followed by water atomisation, and 2) mechanical alloying of water-atomised pure platinum powder with elemental powders of aluminium, chromium, and ruthenium. [Abstract; Experimental procedures]
Q2. What was a major issue affecting the sintering quality of the pre-alloyed platinum powder?
A2. A major issue was the presence of a discontinuous layer of aluminium oxide on the pre-alloyed powder particles, resulting from aluminium in the melt reacting with oxygen from air and/or water during atomisation, which prevented good bonding during sintering. [Conclusion 1; Microstructure of the sintered compacts]
Q3. How did the mechanically alloyed powder respond to compaction and sintering compared to the pre-alloyed powder?
A3. The mechanically alloyed powder showed a poor response to compaction (low green density) due to low apparent density and strain hardening, but it exhibited a good response to sintering with a significant increase in density. [Powder response to compacting and sintering; Conclusion 2]
Q4. What was the typical microstructure observed in the sintered compacts from both powder routes?
A4. The sintered compacts from both routes generally consisted of a platinum solid solution matrix with Pt₃Al precipitates of various sizes and morphologies. [Microstructure of the sintered compacts; Conclusion 1, 2]
Q5. How did the hardness of the sintered powder metallurgy compacts compare to cast alloys of the same composition?
A5. The hardness of sintered pre-alloyed compacts was in the range of cast alloys (300-400 HV₁₀), while the hardness of mechanically alloyed compacts was lower, primarily due to the low compacting pressures used, though it increased substantially with ageing. [Hardness of the sintered compacts; Conclusion 1, 2]
Q6. What interesting phenomenon was observed when mechanically alloyed compact samples were aged at 1450°C for 100 hours?
A6. Ageing mechanically alloyed compact samples at 1450°C for 100 hours resulted in the formation of a liquid, indicating that liquid phase sintering could be possible at temperatures below the melting point of pure platinum. [Microstructure of the sintered compacts]