This article introduces the paper ['DENDRITE REFINEMENT OF AL9C02 COMPOUND BY A CONTINUOUS INCREASE OF THE COOLING RATE DURING SOLIDIFICATION'] published by ['U.P.B. Sci. Bull., Series B, Vol. 74, Iss. 2'].
1. Overview:
- Title: DENDRITE REFINEMENT OF AL9C02 COMPOUND BY A CONTINUOUS INCREASE OF THE COOLING RATE DURING SOLIDIFICATION
- Author: Ana-Maria ADAM
- Publication Year: 2012
- Publishing Journal/Academic Society: U.P.B. Sci. Bull., Series B, Vol. 74, Iss. 2
- Keywords: Al9C02, wedge-shape mould/casting device, dendrite size refinement
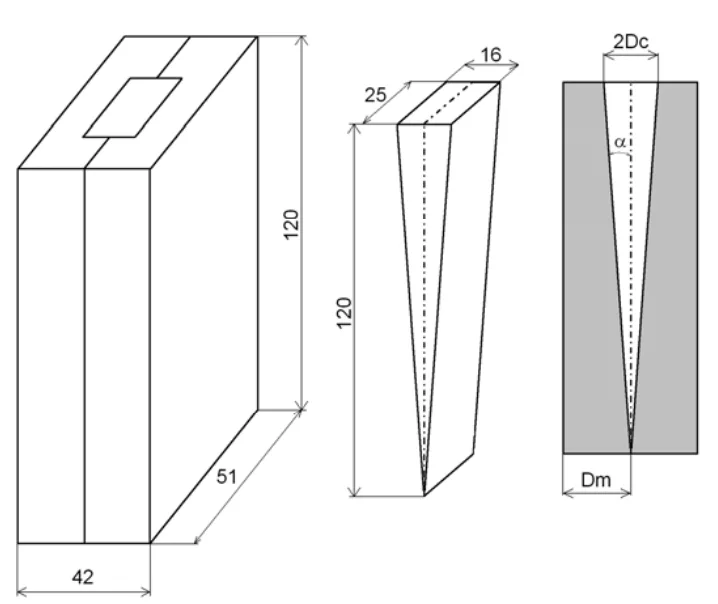
2. Abstracts or Introduction
Continuous modification of the cooling rate during solidification has been applied to a hypereutectic Al-9.71at.%Co alloy comprising Al9C02 primary dendrites that may be used as a precursor for making Raney-Co catalysts. A range of cooling rates of about five orders of magnitude have been achieved by means of a "wedge-shape copper mould device“. The extremely sharp edge of the wedge-shape casting (half apex angle a ~4°) has ensured a very thin half-thickness of the casting at its sharp edge (~50µm) and a cooling rate comparable to that achieved by rapid solidification techniques. The various optical micrographs recorded along the height of the wedge-shape castings have pointed to a decrease in size of the Al9C02 dendrites as the casting thickness decreased, that seemingly manifested a non-linear dependence. This non-linearity was rationalized by modeling the "wedge-shape mould and casting" device used in the experiment on the basis of a thermal-geometrical parameter H₁ = D 1.5 /Dm 0.15 that takes into account both the mould wall thickness (acting as a heat sink) and the liquid alloy thickness (acting as a heat source) in the heat transfer at the interface.
3. Research Background:
Background of the Research Topic:
In the realm of Al-Co alloys, various cobalt-aluminides such as Al9C02, Al13C04, Al5C02, and AlCo can emerge within the microstructure, contingent upon the alloy composition [1]. Notably, aluminides exhibiting a dendrite morphology, particularly when characterized by a diminutive dendrite size, hold promise as precursors in the fabrication of cobalt skeletal catalysts, commonly known as Raney-Co catalysts [2]. These Co-Raney catalysts, while exhibiting reduced activity compared to their Ni-skeletal counterparts, demonstrate enhanced selectivity.
The significance of a refined dendrite size within the aluminide compound of precursor Al-TM alloys (where TM denotes a transition metal such as Co, Ni, or Cu) is underscored by its direct correlation with the efficacy of skeletal TM catalysts. These catalysts are derived through an alkali leaching process applied to the precursor Al-TM alloy, facilitating the selective dissolution of Al and yielding a porous TM structure distinguished by a high specific surface area and elevated catalytic activity [3-5].
Raney-Co catalysts are produced via alkali leaching of Al-Co alloys, with Co content typically ranging from 35-40wt% or 49wt% (the latter being more prevalent). Such precursors encompass diverse Al-rich aluminide compounds (Al9C02, Al13C04, Al5C02) that undergo activation during the selective dissolution of Al. Prior investigations [6] have explored Al-Co alloys containing Al-richest aluminide, Al9C02, demonstrating a dendrite morphology with size dependent on the solidification cooling rate. Rapid solidification is now recognized as a novel approach for generating fine dendrites in Al-TM precursors intended for skeletal catalysts [7,8].
Status of Existing Research:
Previous research [6] has examined the dendrite size of the Al9C02 compound in a hypereutectic Al-Co alloy (9.71at%=15.82wt%) solidified at two extreme cooling rates: ~5 °C/s via die casting and ~5x10^6 °C/s via melt-spinning. Systematic studies on skeletal Ni catalysts (RQ Ni) produced from rapidly quenched Ni-Al alloys have focused on the impact of variable cooling rates during alloy preparation [9]. These studies revealed that the cooling rate of Ni–Al alloys influences the residual Al content, texture, structure, surface hydrogen species, and active sites of the Ni catalysts.
Necessity of the Research:
This paper extends the investigation to intermediate cooling rates, employing a wedge-shape copper mould to modify cooling rates continuously. While the wedge-shape mould method is commonly used for structural modifications in cast iron, its application to non-ferrous alloys, particularly for dendrite size refinement in Al-based alloys, remains limited. The wedge-shape mould method offers more reproducible local cooling rates compared to rapid solidification techniques (melt-spinning, melt extraction) and provides a broad spectrum of cooling rates at intermediate levels.
4. Research Purpose and Research Questions:
Research Purpose:
The primary objective of this research is to investigate the microstructures of a hypereutectic Al-9.71at.%Co alloy, specifically focusing on the dendrite refinement of the Al9C02 compound. This is achieved by applying a continuous variation of cooling rates during solidification using a wedge-shape copper mould device. The study aims to rationalize the observed non-linear relationship between dendrite size and casting thickness by employing a thermal-geometrical parameter.
Key Research:
- To apply a continuous modification of the cooling rate during solidification to a hypereutectic Al-9.71at.%Co alloy.
- To achieve dendrite refinement of the Al9C02 compound through controlled solidification.
- To utilize a wedge-shape copper mould/casting device to generate a range of cooling rates.
- To employ a thermal-geometrical parameter H₁ = D 1.5 /Dm 0.15 to rationalize the non-linear dependence of dendrite size on casting thickness.
Research Hypotheses:
- Continuous variation of cooling rates achieved through the wedge-shape mould will result in a gradient of microstructures with varying dendrite sizes within a single casting.
- Dendrite size of the Al9C02 phase will decrease with increasing cooling rate, corresponding to regions of reduced casting thickness in the wedge-shape mould.
- The relationship between dendrite size and casting thickness will exhibit non-linearity, which can be effectively described and rationalized by the thermal-geometrical parameter H₁, accounting for both casting and mould dimensions.
5. Research Methodology
Research Design:
This study employs an experimental research design centered around the utilization of a wedge-shape copper mould-casting device. The design facilitates the continuous modification of cooling rates during the solidification of a hypereutectic Al-9.71at.%Co alloy. Microstructural analysis, primarily through optical microscopy, is used to observe and characterize the dendrite refinement of the Al9C02 compound across varying cooling rates.
Data Collection Method:
The data collection process commenced with the fabrication of wedge-shape castings from a hypereutectic Al-9.71at.%Co alloy using a custom-designed copper mould. The wedge-shape casting method inherently provides a continuous gradient of casting thicknesses, thereby inducing a range of cooling rates during solidification. Following solidification and extraction of the casting from the mould, samples were sectioned at various heights along the wedge to represent different casting thicknesses and corresponding cooling rates. Optical micrographs were then recorded at specified locations along the height of the wedge-shape casting, systematically capturing microstructural variations as a function of casting thickness.
Analysis Method:
The analysis of collected data was primarily qualitative, focusing on the visual assessment of dendrite size variation in the optical micrographs. The micrographs, obtained from different thicknesses of the wedge-shape casting, were examined to observe the trend in Al9C02 dendrite size as a function of casting thickness. To rationalize the observed non-linear dependence of dendrite size on casting thickness, the thermal-geometrical parameter H₁ = D 1.5 /Dm 0.15 was employed. This parameter accounts for both the casting thickness (Dc) and the mould wall thickness (Dm), providing a more comprehensive characterization of the heat transfer conditions. H₁ values were calculated for different casting thicknesses, and the relationship between H₁, casting thickness (2Dc), and the observed dendrite size variations was analyzed to explain the non-linear behavior.
Research Subjects and Scope:
The research focused on a hypereutectic Al-9.71at.%Co alloy, specifically investigating the solidification behavior and dendrite refinement of the Al9C02 primary dendrites. The scope of the study is limited to the experimental investigation using a wedge-shape copper mould-casting device and qualitative microstructural analysis via optical microscopy. The thermal-geometrical parameter H₁ was applied as a tool to interpret and rationalize the observed experimental results within the context of heat transfer during solidification in the wedge-shape casting configuration.
6. Main Research Results:
Key Research Results:
The experimental results demonstrated a clear trend of dendrite refinement in the Al9C02 compound as the casting thickness decreased within the wedge-shape castings. Optical micrographs, recorded along the height of the wedge-shape castings, revealed a systematic reduction in the size of Al9C02 dendrites in regions corresponding to smaller casting thicknesses. This observation confirms that the continuous variation of casting thickness in the wedge-shape mould effectively induces a continuous modification of the cooling rate, leading to corresponding changes in the solidified microstructure.
Analysis of the micrographs indicated a non-linear dependence of the Al9C02 dendrite size on the casting thickness. The reduction in dendrite size was more pronounced at smaller casting thicknesses (near the sharp edge of the wedge) and became less sensitive to thickness changes at larger dimensions. This non-linear behavior was rationalized by considering the thermal-geometrical parameter H₁, which accounts for both the casting thickness and the mould wall thickness in characterizing the heat transfer conditions.
The wedge-shape mould device successfully provided a wide range of cooling rates, spanning approximately five orders of magnitude. At the sharp edge of the wedge, the cooling rates achieved were comparable to those obtained in rapid solidification techniques (≤10^6 °C/s), attributed to the extremely small half-thickness of the casting (~50µm) in this region. Conversely, at the thicker end of the wedge, the cooling rates were typical of die casting processes.
Analysis of presented data:
Figure 2 presents a series of optical micrographs that visually demonstrate the variation in microstructure along the wedge-shape casting. As the casting thickness (2Dc) increases from bottom to top, a gradual increase in the size of the Al9C02 dendrites is evident. The micrographs at smaller 2Dc values (e.g., 103µm, 338µm) exhibit finer dendrite structures, indicative of higher cooling rates, while micrographs at larger 2Dc values (e.g., 6000µm, 16000µm) show coarser dendrites, corresponding to lower cooling rates.
The non-linear relationship between dendrite size and casting thickness is further supported by the calculation and graphical representation of the thermal-geometrical parameter H₁. Table 1 lists the calculated H₁ values for different casting thicknesses (2Dc), and Figure 4 graphically illustrates the dependence of H₁ on 2Dc. The curve in Figure 4 shows a decreasing slope as 2Dc increases, indicating that the sensitivity of H₁ to changes in casting thickness diminishes at larger thicknesses. This non-linear behavior of H₁ correlates with the observed non-linear refinement of dendrite size, suggesting that H₁ effectively captures the changing heat transfer dynamics within the wedge-shape mould.
Figure Name List:
- Fig.1 Schematic depiction of the wedge-shape copper mould-casting device used to give a range of cooling rates during solidification (the dimensions are in millimetres); the two halves of the copper mould; the wedge-shape Al alloy casting; vertical cross section through the wedge-shape "mould-casting device'
- Fig. 2 represents a series of optical micrographs recorded from bottom to top of the wedge-shape casting at various locations specified by the value 2Dc
- Fig.3 Influence of the geometrical parameter H₁ on the solidification process of an Al-Cu-Si alloy (LM-21),, reproduced from [12]
- Fig.4. Graphical representation of eq.(3) showing the dependence between H₁ and 2D in the wedge-shape mould/casting device used in the experiment

![Fig.3 .Influence of the geometrical parameter Hi on the solidification process of an Al-Cu-Si alloy (LM-21),, reproduced from [12 ]](https://castman.co.kr/wp-content/uploads/image-933-png.webp)
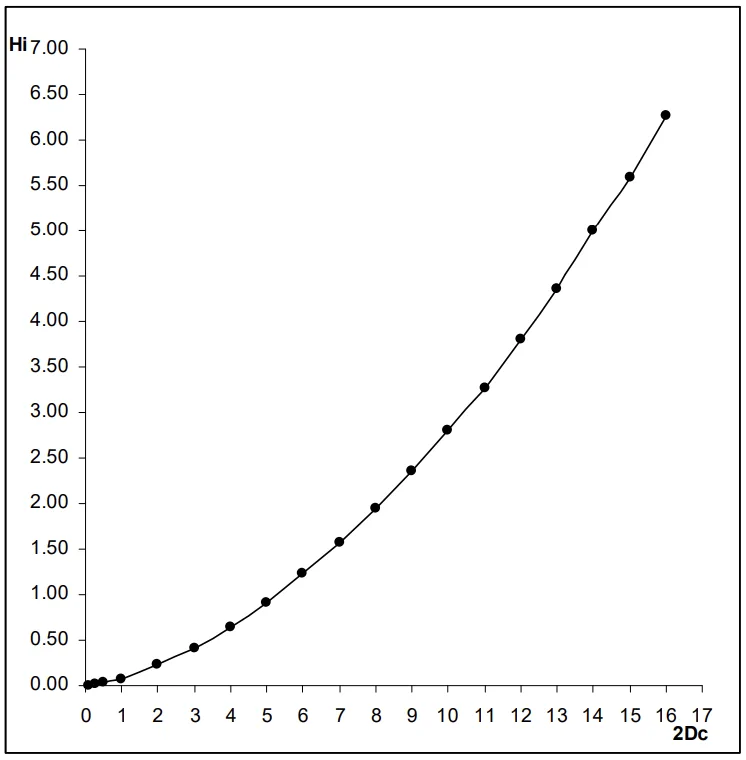
7. Conclusion:
Summary of Key Findings:
This study successfully demonstrated the application of a wedge-shape copper mould/casting device to achieve a continuous modification of cooling rates during the solidification of a hypereutectic Al-9.71at.%Co alloy. The wedge-shape mould effectively provided a wide range of cooling rates, from extremely high rates comparable to rapid solidification techniques at the thin edge to rates typical of die casting at the thicker end. A qualitative analysis of optical micrographs revealed that the dendrite size of the Al9C02 compound decreased non-linearly with decreasing casting thickness, indicating dendrite refinement at higher cooling rates. The non-linear dependence was rationalized by introducing and calculating the thermal-geometrical parameter H₁, which considers both casting and mould thicknesses, providing a more accurate representation of the heat transfer conditions.
Academic Significance of the Study:
This research contributes to the understanding of solidification processes in metallic alloys, particularly in the context of continuous cooling rate variation. It highlights the effectiveness of the wedge-shape mould technique as a tool for systematically studying the influence of cooling rate on microstructure development in Al-based alloys. The study introduces the thermal-geometrical parameter H₁ as a valuable metric for characterizing heat transfer in wedge-shape castings, offering a means to predict and interpret microstructural variations in such configurations.
Practical Implications:
The findings of this study have practical implications for the production of Al-Co alloy precursors used in the manufacturing of Raney-Co catalysts. The wedge-shape casting method offers a viable approach to control and refine the dendrite size of the Al9C02 compound, which is crucial for enhancing the performance of these catalysts. The ability to achieve a wide range of cooling rates within a single casting process provides a versatile technique for optimizing alloy microstructures for specific applications.
Limitations of the Study and Areas for Future Research:
The primary limitation of this study is the qualitative nature of the dendrite size analysis, which relies on visual assessment of optical micrographs. Future research should focus on quantitative evaluation of dendrite arm spacing (DAS) through image analysis techniques to provide more precise and statistically robust data on the relationship between cooling rate, casting thickness, H₁, and dendrite size. Further investigations are also needed to quantitatively verify the influence of the thermal-geometrical parameter H₁ on dendrite size and to explore its applicability to other alloy systems and casting configurations.
8. References:
- [1] T.Massalsky, Binary alloys phase diagrams, 2nd edition, vol.1, ASM Publ., USA, 1992, p.136
- [2] A. Smith., L. Garciano II, T.Tran and M.S.Wainwright, Industrial & Engineering Chemistry Research, 47(5), 2008, p.1409-1415
- [3] A.J.Smith, T.Tran and M.S. Wainright, J. of Applied Electrochemistry, 29, 1999, p.1085-1094
- [4] I. Yamauchi, H.Kawamura, K.Nakan and T.Tanaka, Journal of Alloys and Compounds 387, 2005, р.187-192
- [5] A.D.Tomsett,H.E.Curry-Hyde, M.S.Wainright, D.J. Young and A.J.Bridgewatter, Applied Catalysts, 33, 1987, p. 119-127
- [6] A.M. Adam, Univ. Politehnica Buch. Sci. Bull., series B, 73 (3), 2011, p.215-228
- [7] I. Yamauchi and H. Kawamura, Journal of Alloys and Compounds 370, 2004, p.137-143
- [8] Z.Lou, X. Chen, L.Tian, M.Qiao, K.Fan, H.He, X.Zhan and B.Zong,Journal of Molecular Catalysis A: Chemical, 326, 2010, p.113–120
- [9] H.Hu, F.Xie, Y.Pei, M.Qiao, S.Yan, H.He, K.Fan, H.Li, B.Zang and X.Zhang, Journal of Catalysis, 237, 2006, p.143-151
- [10] T.Laoui and M.J. Kaufman, Metallurgical Trans. 73 A (Sept.), 1991, p.2141-2152]
- [11] M.C Flemings., T.Z.Kattami and B.P.Bardes, AFS Transactions, 99, 1991, p.501-506
- [12] K.N.Prabhu, S.A.Kumar and N.Venkataraman, AFS Transactions, 102, 1994, p.827-832
- [13] K.N.Prabhu, D.Madheswaran, T.S.P.Kumar and N.Venkataraman, AFS Transactions, 100, 1992, p.611-617
9. Copyright:
- This material is "Ana-Maria ADAM"'s paper: Based on "DENDRITE REFINEMENT OF AL9C02 COMPOUND BY A CONTINUOUS INCREASE OF THE COOLING RATE DURING SOLIDIFICATION".
- Paper Source: U.P.B. Sci. Bull., Series B, Vol. 74, Iss. 2, 2012, pp. 289-301.
This material was summarized based on the above paper, and unauthorized use for commercial purposes is prohibited.
Copyright © 2025 CASTMAN. All rights reserved.