This article introduces the paper "Cooperation of Development and Manufacturing for Up-to-date Transmission Parts" presented at the ATZ
1. Overview:
- Title: Cooperation of Development and Manufacturing for Up-to-date Transmission Parts
- Author: Dipl.-Ing. (FH) Stefan Beinkämpen, MBM
- Publication Year: 2016
- Publishing Journal/Academic Society: ATZ
- Keywords: Simultaneous Engineering, Die Casting, Forming Technology, Transmission Parts, Electric Motor Housings, Automotive Industry, Lightweight Design, Manufacturing Process
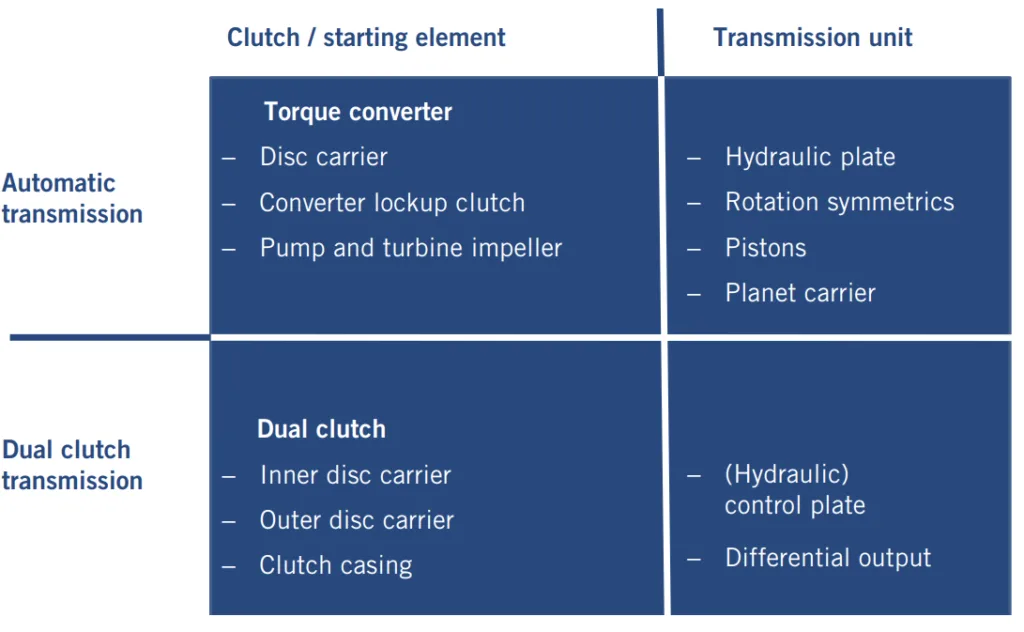
2. Research Background:
The automotive industry faces constant pressure to reduce development times. This necessitates a closer integration of construction and manufacturing processes within the die casting and forming industries. Historically, organizational structures have often led to a separation between product development and manufacturing process planning. This separation can result in suboptimal manufacturing solutions where planning is not fully optimized. Furthermore, the increasing complexity of lightweight design, moving beyond simple material substitution to holistic and systematic approaches, adds another layer of challenge. The traditional approach of late supplier involvement in projects, driven by purchasing structures, can also hinder the ability to correct manufacturing process risks due to tight schedules.
3. Research Purpose and Research Questions:
This paper aims to showcase how Voit Automotive leverages an extended simultaneous engineering approach to optimize the development and manufacturing of up-to-date transmission parts and electric motor housings. The core purpose is to demonstrate the benefits of early and close cooperation between component development and manufacturing process development. Key questions addressed implicitly in the paper include:
- How can simultaneous engineering effectively reduce development times for complex die cast components?
- What are the advantages of integrating manufacturing process considerations from the initial stages of component design?
- How can a supplier, through early involvement, offer added value in designing and operating secure and efficient manufacturing workflows for customers?
4. Research Methodology:
The paper presents a case study approach, detailing Voit Automotive's methodology and experience in applying simultaneous engineering. It outlines their service offerings and target projects within transmission development. The methodology is illustrated through examples of component designs and manufacturing technology applications, supported by figures showcasing market trends and component matrices. The analysis is descriptive, focusing on the benefits and practical implications of their integrated approach. The scope is centered on automotive transmission components and electric motor housings, specifically within the context of aluminum pressure die casting and forming technologies.
5. Main Research Results:
The paper highlights that "development times are greatly reduced" through an extended simultaneous engineering approach where component and manufacturing concept development occur in parallel. Key results and observations include:
- Reduced Development Times: Simultaneous engineering significantly shortens development cycles by addressing manufacturing considerations concurrently with component design.
- Robust Manufacturing Processes: Early integration of manufacturing expertise ensures the development of reliable and efficient production processes, minimizing interface problems and potential errors.
- Target Project Identification: Analysis, as shown in FIGURE 1, identifies specific transmission components like "hydraulic plates, control plates, torque-transmitting rotationally symmetrical cup structures, axial pistons, disk carriers or planetary supports" as target projects suitable for manufacturing technologies such as "stamping and/or bending technology".
- Economic Considerations: Beyond technical feasibility, the paper emphasizes the importance of economic viability, considering factors like "positive projection of volume progression, FIGURE 2," and "regional attractiveness of a transmission technology."
- Material Mix Solutions: FIGURE 4 exemplifies material mix solutions, such as combining "an aluminium pressure die cast flange (yellow) and a deep drawn steel cup (grey)" for components like axial pistons in automatic transmissions.
- Component Matrix: FIGURE 3 illustrates a component matrix comparing "Aluminium die casting solution" with "Sheet metal forming, welded assembly" for components like "Rotationally symmetric structure" and "Planet carrier."
Figure Name List:
- FIGURE 1 Target components in a vehicle transmission which were chosen at Voit for defined manufacturing technologies (stamping and/or bending technology)
- FIGURE 2 Progression of production volumes of three selected technologies - European Union (left) compared to global (right), source: PwC Autofacts Q1/2016
- FIGURE 3 Component matrix with the alternative manufacturing technologies die casting and bending/welding
- FIGURE 4 Material mix of an aluminium pressure die cast flange (yellow) and a deep drawn steel cup (grey) for an axial piston in an automatic transmission with cut of the joining zone (top left)
- FIGURE 5 Pre-development project for the manufacture of a composite component (Patent pending ref. no. WO 2015/043580A1)
- FIGURE 6 Development project for a liquid-cooled electric motor housing
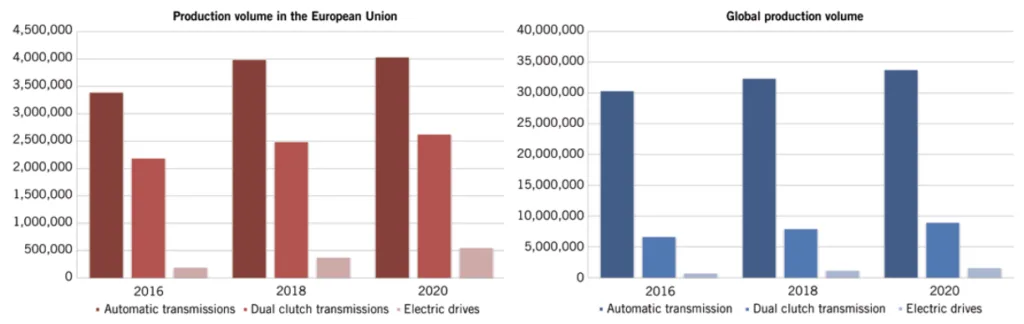
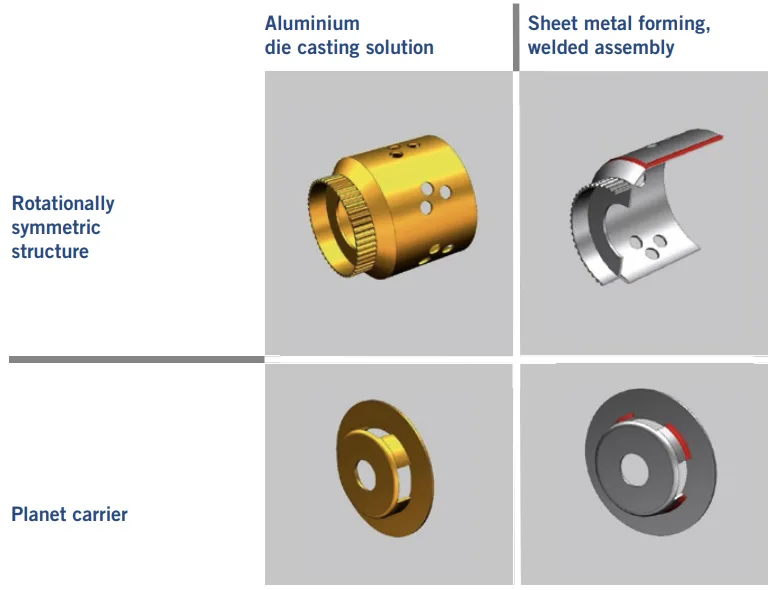
6. Conclusion and Discussion:
Summary of Main Results: The paper concludes that early cooperation and simultaneous engineering are essential for achieving savings and efficiencies in the development and manufacturing of automotive transmission parts. By integrating component development and process development from the outset, manufacturers can create reliable, cost-effective, and up-to-date solutions.
Academic Significance of the Research: This paper underscores the academic and practical importance of simultaneous engineering in the context of die casting and forming. It highlights the shift from sequential to parallel development approaches to meet the demands of the modern automotive industry.
Practical Implications: For die casting companies and automotive OEMs, the paper advocates for adopting simultaneous engineering methodologies and fostering early supplier involvement. This collaborative approach enables the creation of optimized manufacturing process chains, delivering "clean, ready-to-install components directly to the assembly stations of the customer."
Limitations of the Research: The paper primarily presents Voit Automotive's perspective and successful implementation of simultaneous engineering. It serves as a case example rather than a broad, statistically validated research study. The focus is limited to transmission parts and electric motor housings, and specifically to aluminum pressure die casting and forming technologies.
7. Future Follow-up Research:
Directions for Follow-up Research: Future research could explore the quantifiable benefits of simultaneous engineering in die casting through broader empirical studies. Further investigation into specific techniques for optimizing die casting processes within a simultaneous engineering framework would be valuable. Exploring the application of these principles to other automotive component areas and industries beyond automotive transmissions could also be beneficial.
Areas Requiring Further Exploration: Detailed cost-benefit analyses of simultaneous engineering implementation, advancements in digital tools and simulation for integrated design and manufacturing, and innovative material and design approaches for lightweight die cast components are areas warranting further exploration.
8. References:
[1] Friedrich, H. E.; Krishnamoorthy, S. K.: Triumphe durch Leichtgewicht. In: Friedrich, H. E. (ed.): Leichtbau in der Fahrzeugtechnik. ATZ/MTZ-Fachbuch. Wiesbaden: Springer Vieweg, 2013, p. 3 ff.
[2] Ellenrieder, G.; Friedrich, H. E.; Kienzle, S.: Potenzialerschließung durch Systemleichtbau auf Gesamtfahrzeugebene. In: Friedrich, H. E. (ed.): Leichtbau in der Fahrzeugtechnik. ATZ/MTZ-Fachbuch. Wiesbaden: Springer Vieweg, 2013, pp. 770 ff.
[3] Siebenpfeiffer, W. (ed.): Leichtbau-Technologien im Automobilbau. Werkstoffe - Fertigung - Konzepte. ATZ/MTZ-Fachbuch. Wiesbaden: Springer Vieweg, 2014, p. 174 ff.
9. Copyright:
*This material is Stefan Beinkämpen's paper: Based on Cooperation of Development and Manufacturing for Up-to-date Transmission Parts.
*Paper Source: ATZ magazine, 05/2016, Volume 118, pages 60-63.
This material was summarized based on the above paper, and unauthorized use for commercial purposes is prohibited.
Copyright © 2025 CASTMAN. All rights reserved.